Low-Cost Wall for Coastal Location

Hi,
I am trying to develop a low cost 2×4 wall that meets code for Climate zone 6A (coastal Maine). I am thinking of the following to meet the energy code and some attention to extra strength since it is also a open higher altitude site with some pretty hefty winds:
Drywall–2×4 16″ OC filled with ccSPF (R-23)– 7/16 Advantec sheathing– 1″ XPS (R5)–Hydro Gap wrap— LP Smartside lap siding
I think this meets the insulation ratios of 0.2 minimum. I have also tried to look at vapor permeance for the assembly, but their a lot of confusing calculators and I am not sure my inputs are good to make sense of the outputs.
I am also considering hurricane strapping at top and bottom plates as well as the roof and increased nailing requirements.
Any thoughts if I am taking a good approach? Does my wall construction make sense?
GBA Detail Library
A collection of one thousand construction details organized by climate and house part
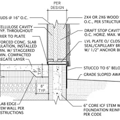
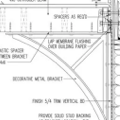
Replies
I don't associate closed cell spray foam with low cost.
Is there a reason the wall has to be 2x4? I think you'd be way ahead going with either a 2x6 or staggered 2x4 wall and a thicker, cheaper insulating material.
For windy coastal Maine, I would go with a good rain screen of plywood or lumber battens. And I would do a stagger stud 2x4 as above.
Some of your choices seems strange to me.
Why chouse a 2x4 wall? A 2x6 wall would be much stronger.
Why chouse 16 on center? 24” advance framing would lower the lumber cost with almost no reduction in strength.
Why chouse spray foam insulation? It is the most expensive and least green way to get an R of insulation.
Why 7/16 Advantec sheathing? I thought this product is only rated for horizontal use on floors.
Why (R5)–Hydro Gap wrap? I am not 100% sure but if this is bubble pack it has an R value of zero all claims to the contrary scams if not fraud.
Why LP Smartside lap siding? I throw up a little read the word Smartside. They had some bad runs of product a few years ago. They dragged out paying for years and did not pay enough to cover the costs.
Did you read this article?
https://www.greenbuildingadvisor.com/article/how-to-design-a-wall
Walta
All good points so let me clarify:
-ccSPF: Formulations now are much "greener" than those just a few years ago, so is not really an issue. Cost is higher, but adds strength and a lot of R for depth.
- Double stud 2x4 wall: Not much expertise for builders in my area. I need to build what can be built without being the guinea pig.
- Advantec: Common dense OSB product used for wall sheathing with a thicker product for floors.
- XPS is R5 foam board (also new Green formula without HFC). Hydro gap is WRB with 1mm chiclets for improved drying.
- LP siding: Old product from the 90's was bad. New product much denser and with fairly reasonable measures for install to avoid moisture issues. Hardie board not as strong and also many moisture issues. Natural wood has its own problems.
With tight labor in building trades I also need to come up with something that is affordable and within the realm of local builders.
You're not getting R23 using closed cell spray foam in a 2x4 framed wall. Period. No exceptions. There are two reasons for this: 1- close cell spray foam (ccSPF) is around R6/inch at best in reality, so a full 3.5" fill would get you R21. BUT -- you WON'T get a full fill. ccSPF is installed as a partial fill, to avoid the need to trim it flush with the surface of the studs, since it's difficult to trim. AT BEST, you'll get a 3" fill, which is R18. In reality, you get a slightly concave fill, so maybe 3" on the edges but quite possibly only 2-2.5" in the middle. That means you're getting an actual average R value of something under R15, maybe even all the way down to around R12 or so. One other thing that doesn't help you -- R values don't average out, so a little extra at the edges doesn't really help you if the middle is thin. Chances are that ccSPF wall is going to perform between R13-R15 or so, depending on the quality of the installation, and that's right around what you can do with high density fiberglass or mineral wool batts (the latter of which is a reliable R15). I would skip the spray foam in the wall here -- and I don't think of it as "structure", although it probably helps with racking, but that's not the only force a structure has to resist to deal with high winds.
I would go with mineral wool batts in the walls, which get you a reliable R value and are easily installed well. I would use polyiso on the exterior, which is better than XPS -- more R per inch -- and even if derated for "cold", it's still about the same R value as XPS so you don't really lose anything. I would put at least enough R worth of polyiso on the exterior to hit the recommended ration for your wall, whether you build with 2x4s or 2x6s.
Your wall will be great for racking resistance with Advantech sheathing. If you want more structure, up that to 3/4" CDX. After that, build "Florida Style", and use hurricane straps. Those tie the foundation to the wall, and the top plate to the rafters. Your structural sheathing should be put on to tie the studs together with the top and bottom plates, which means put it up VERTICALLY (which is pretty standard). Use the right nail schedule, and use ring shank nails. Now your roof is resistant to uplift forces. A 2x6 wall will be able to resist more force perpindicular to the surface compared to a 2x4 wall, but it needs to be able to transfer that force somewhere on the top side. That means you need some perpindicular shear panels on the interior on long spans of straight wall. I don't trust drywall for this if you expect high forces. There is some engineering that needs to be done to make sure everything ties together correctly. An engineer thinks of the forces as arrows (vectors, actually, but visualize them as arrows). Every time an arrow points towards something, it is "pushing" that something. Where does the "pushing force" transfer to? More arrows in everything connected to the first thing. ALL of those arrows have to have something bracing them, so that the forces they represent get transfered to something that will not move, which typically means the foundation.
BTW, I think a rain screen is a good idea here too, as mentioned by some of the other posters.
Bill
Despite what you may have heard, CCSPF and XPS, despite MODEST improvements, are still by far the worst foam insulations with respect to the environment. XPS and polyiso also lose a considerable amount of insulation value over time, approaching EPS in r/inch after 5-10 years. Polyiso also insulates less well as temperatures drop. EPS on the other hand actually insulates better at lower temperatures.
From the environmental standpoint EPS is best, and often the cheapest. As a designer it's all I specify.
2x4 studs @ 24" o.c. are perfectly adequate structurally, for a single story house with an attic. For 2 stories with an attic go with a 16" spacing. (IRC 2021 Table R6022.3(5) )
Typically things like studs aren't the weak links structurally. It's the connections that fail. So definitely you'll want very good strapping of roof to walls and walls to foundation. Study up the material put out by Simpson StrongTie on "continuous load paths".
https://www.strongtie.com/solutions/high-wind-resistant-connectors
My wall approach, starting from inside:
* 5/8" gyp. bd.
* 2x4 framing @ 24" o.c.
* R15 unfaced batt insulation (to encourage drying to the interior)
* 15/32" CD-X plywood sheathing (The installation cost of plywood is the same as OSB. Plywood provides a better air barrier and handles moisture better.)
* Tape all the exterior joints of the plywood for your air barrier.
* Outboard of the plywood apply 2 layers of EPS rigid insulation 1" thick each, staggering the joints vertically and horizontally. If you use a Type IX foam this has good density which makes a sturdy surface. It also gives you R-5 /inch (see Insulfoam for specs).
* Tape the joints of the outer layer of foam to act as your WRB (water resistant barrier). There's no need for Tyvek or building paper. But you need to know the right way to handle door and window openings. There are a number of solutions and you'll find articles here on GBA.
* Vertical furring 24" oc at each stud. 1x3 or strips cut from 3/4" work. The furring will need 5" long screws to penetrate the insulation and sheathing and get into the stud. Some people say 24" oc max is fine. But I'd go with a closer spacing though, 12". Once you're out there with a screw gun putting in screws it doesn't take that much longer.
* Cedar lap siding would be my first siding choice. Cedar shingles are great too but consider a panelized product. It will cost a bit more but makes the rainscreen detailing simpler. You can use the same vertical furring for both lap siding and shingles.
https://www.vintagewoodworks.com/cedpan.html
>"XPS and polyiso also lose a considerable amount of insulation value over time, approaching EPS in r/inch after 5-10 years. Polyiso also insulates less well as temperatures drop. EPS on the other hand actually insulates better at lower temperatures."
That's not really accurate. XPS will gradually drop down to around EPS (~R4.2/inch), but it takes a fair bit longer than 5 years to get there. Even when XPS is fully aged, it's lost about 0.16% from it's RATED value (which already allows for some aging, but not all of it), and you end up no worse off than you would be if you started with EPS. XPS is worse in terms of blowing agents, but that's changing. I consider XPS to be something of a niche product, best for below grade (subslab, etc.), but not for other applications where there are better alternatives. Spray foam is similar, I only consider it for unvented roof assemblies and a few complex areas where the labor to do anything else is either very difficult or near impossible to do well.
Polyiso does NOT lose R value the way XPS does. It does degrade somewhat over time, but it's over decades, especially with foil faced polyiso. Polyiso also starts out a fair bit higher than the rated (aged) R value, so you aren't starting from the rated value with the derating. Polyiso, when derated for cold weather, is usually said to be about R5/inch, which is still better than EPS, and it's better than EPS all the rest of the time. Newer blowing agents aren't as affected when cold, either, and since the cold weather derating is due to blowing agents condensing, as those blowing agents diffuse out there will be less of an affect on the product's R value in cold weather (i.e. it will lose LESS R value over time). Polyiso is going to outperform EPS over the life of the product in nearly all applications, but it can't be used where it will get wet, which is the main downside to EPS.
I have nothing against EPS aside from it being the least durable of the three, but that's less of an issue with the denser EPS grades. EPS is the cheapest, but also less commonly available than XPS, unforunately. I really think the main reason XPS gets used so much is that all the box stores carry it -- and that doesn't mean it's a superior product. GPS is probably the best happy medium, with a bit more R per inch than "regular" EPS, and a bit more cost too, but not as much R or cost as polyiso.
Bill
Bill, have you worked with higher-density EPS, such as 25 psi or 40 psi grades? If not, I recommend giving it a try--I think you'll be surprised how similar it is to working with XPS.
I have looked extensively but have not found any published studies on how long it takes for air to displace the blowing agents in XPS or polyiso, aside from accelerated aging for polyiso's LTTR, which I know is 18 months of aging to approximate a 5-year service life. Have you found any?
EPS, like most types of insulation other than polyiso, does perform better the colder it is; R-value testing is done at mean 75°F, but when testing at lower temperatures, EPS approaches the equivalent of R-5/in. I'll attach a tech sheet from one manufacturer.
"XPS is worse in terms of blowing agents, but that's changing." I know that you know this, but for anyone else reading, the newer blowing agent for XPS is significantly better than the old one, but the total level of embodied carbon for XPS is still far higher than any other type of common insulation other than closed cell spray foam.
I admittedly have not worked with the higher density EPS variants outside of some formed pieces (like purpose-made corners). I actually do have mauybe 5 sheets of 2" 15 or 25 PSI EPS (I can't remember which) for an upcoming project. I wouldn't expect it to score and snap as nice as XPS, but I usually use my hotwire cutter on EPS so that's not really an issue for me.
My primary concern is with the EPS that is usually available at the box stores, which tends to be the crumbly low density stuff, usually with a plastic facer. I really wish the box stores would carry more than just XPS in a range of thicknesses, since I think a lot of XPS gets used where it's not the only or best option, simply becasue DIYers have the easiest access to it at the box stores. I'd love to see thicker polyiso stocked, and also some higher density EPS variants that are easier to work with. In my area, Menards stocks the higher density EPS in 2" thickness, but polyiso only up to 1". It's nice to at least have the higher density EPS as an option, but they have mostly XPS just like the others.
I'm usually looking at things from an energy efficiency standpoint and not embodied carbon. I do think of XPS as a niche product like spray foam though, and not a "use it anywhere" material. I think it's just the ease of availability that makes XPS so commonly used.
Bill
I totally agree on availability. With some planning ahead, I've found that ordering EPS in almost any size and thickness I want, delivered, costs the same or less than getting XPS locally. But there is a lead time and it's not readily available everywhere.
This is to Bill Wichers. The comment software is putting "zephyr7" instead.
Regarding the loss of insulation value over time. This is the study that comes to my fingertips fastest, but I've seen others more recent with similar results.
XPS: https://www.greenbuildingadvisor.com/article/thermal-drift-of-polyiso-and-xps
Here is an article about polyiso.
https://www.greenbuildingadvisor.com/article/cold-weather-performance-of-polyisocyanurate
As you can see from the graph in the first article, most of the loss happens in the first 5-10 years. Sorry that I did not include a reference in my original comment but I usually do check these things before I write them even if I don't include the reference.
Honest insulation manufacturers are stating the "long term" values more often now. However most use 5 years as their "long term" while the losses between 5-10 years are not insignificant. But I find that many people, including consumers are still quoting values fresh out of the factory. So the misconception that XPS and Polyiso are significantly higher in R value per inch still persists. Once you factor in aging and in the case of polyiso, reduced efficacy at colder temperatures, the difference with EPS becomes very small.
As I wrote carefully in my original comment, I was comparing to Type IX EPS, (not just any old EPS), which is denser and consequently more suitable in exterior applications. It also gives a slightly better R value for thickness compared to other EPS types.
I don't know what your basis is for describing EPS as the least durable of the 3. As an exterior rigid insulation on walls and roofs I'd like to see some studies that define that more accurately. Of course, EPS is also routinely used in below grade applications where it sees quite challenging conditions. So durability isn't a problem if good quality material is installed correctly (as should be the case with every building material).
Regarding R-5 per inch for Type IX EPS, I'm referring to its performance at the coldest temperatures, when we typically need our insulation the most.
https://www.insulfoam.com/wp-content/uploads/2014/04/InsulGrade-IX-TDS.pdf
"Polyiso, when derated for cold weather, is usually said to be about R5/inch, which is still better than EPS"
That name changing stuff is from the GBA software change. Supposedly things will get fixed one day, but it is what it is for now. That is not my doing :-)
Polyiso was famous for inflated R values in the late 70s and into the 80s, before they were using the LTTR values. The manufacturers liked to use "right off the line" R value numbers (R9-10 per inch or so), which were good for maybe a year or two at best. Now they use aged values, which are much more realistic for an average R value over time. In the beginning, when the material is new, it will perform better than rated. At the end it will be less than rated, but the general idea is that the average over time will be somewhat close to rated. That's the theory anyway. I don't think any manufacturers of polyiso have been stating anything other than LTTR values for decades now. Typical material is rated at about R2.7 for 1/2", R6 for 1", and R13 for 2", using the normal density foil faced stuff commonly used. I actually have some old (late 70s vintage) 1/2" stuff rated R5, which I don't believe at all. The one advantage to the older stuff is that it didn't have the "derate in the cold" issue due to the blowing agents used back then.
My basis for the durability comment is regarding the typical low-density stuff usually found in box stores that DIYers are most likely to have easy access too. There is no question the denser varients are far superior here, they just aren't as readily available to DIYers. I very much wish that wasn't the case, as I don't think XPS is deserving of the placement it gets in the box stores (typical box stores carry 1/2" through 2" thick XPS, sometimes in two different densities, but only a little bit of faced low density EPS if any at all, and only 1" or thinner polyiso). This isn't an issue on commerical projects that can order what they need, but it's an issue for many smaller renovation projects, unfortunately.
To accurately compare materials, you need to hold ALL variables constant. That means comparing material R values at similar temperatures. EPS is typically listed as R4.2/inch under standard test conditions, XPS at R5/inch, and polyiso at R6 per inch. XPS will eventually fall down to EPS, but not below. Polyiso is actually a little better in R/inch at thicker thicknesses (R13 at 2" for example). It's true that EPS will come up a bit in colder temperatures where polyiso goes down, but that would mean derated polyiso would be close to "cold improved" EPS. All the rest of the time, polyiso will outperform EPS, so if you look at energy savings over a season, and not just on the coldest of cold nights, polyiso will do a little better overall. Dana Dorsett pointed this out to me several years ago, and he had a good point: the coldest nights are only a relatively small percentage of the overall heating season, so a little better over a small period of time (EPS in the cold) is not enough to make up for the "little better over a long period of time" (polyiso over the entire season) in terms of total energy savings with the materials.
I'm aware of the "polyiso in the cold" paper, and note that the different manufacturers all did differently. People like to latch onto the one worst one (which Dana had referred to as "world's crummiest polyiso"). Manufacturers have also improved their products since that was written. The issue is that there isn't much actual info out there showing test data for cold polyiso. I keep thinking to build a test rig to do some work in this regard to publish, but I haven't had the time -- although I did put a design together and even order parts.
BTW, I'm not against EPS at all. It's advantages are that it's the cheapest of the three, and it's R value is stable over time. It just doesn't have a performance edge over polyiso in terms of total energy savings over a season, although polyiso will cost significantly more than EPS which does partially offeset the seasonal energy savings. Each material has pros and cons that make each more or less suitable for different applications. My own usual preference is polyiso in most above grade walls/ceilings, and interior foundation walls where moisture isn't an issue, XPS underground where it will be wet, EPS on wetter basement walls, areas that need some vapor permability (EPS is the most vapor open of three unless you include vapor permeable faced polyiso, which is less commonly available), and in other areas where cost is a concern. I insulated my dog's doghouse with EPS, and my rim joists. It has areas it's best suited too.
Bill
When lumber price went through the roof, this was low cost high R value wall I used:
-gyp
-2x4 16OC with R14 HD batts
-CDX taped
-2" fiberfaced roofing polyiso
-WRB
-1x4 strapping
-siding
The windows were on small 2" bucks so the WRB was a simple plane like a regular wall. This wall is also exactly the same thickness as a 2x6 so you can use off the shelf windows and doors but you get roughly an R25-R26 assembly.
At the current prices, you are better off with a 2x6+R5 rigid wall. This simpler to build as lot of siding can be nailed directly through the foam or even a rain screen can be nailed up with a framing nailer. In zone 6 this does require a warm side vapor retarder (faced batts or variable perm membrane).
This assumes your local trades are used to working with exterior rigid. This might not be the case at which point your best bet is a 2x8 24" OC wall with HD batts without any exterior rigid.
All these are roughly the same assembly R value and near the sweep spot in terms of energy savings and build cost in colder climate.
I had similar pushback from contractors on building what they are used to, so I let them build what theyre used to, and added 3" of XPS to the exterior. Other than putting up the XPS (which is very easy), it adds making boxes for the windows, and adding strapping to create the rainscreen. It also allowed use of fiberglass batts in the studs and eliminated use of a separate interior vapor barrier.
“ccSPF: Formulations now are much greener” Call me skeptical sounds like green washing to my ear. Don’t discount the risk of having a bad batch we get posts often how to fix my stinky gummy ccSPF.
Consider a 2x6 walls filled with damp spray cellulose insulation. My guess is it would cost less and deliver more Rs even on 16 inch centers.
Seems to me thicker “was wood”/OSB offer little or no strength advantage against wind loads. If you want to stop fling 2x4s you need plywood.
The bad LP product was talking about was installed in 2008.
Walta
The new HFO blowing agents really are much greener. There is also supposedly a "water blown" variant (maybe only open cell though), although I haven't seen that one myself. That's a completely different issue from the "bad mix" problem that is still possible, regardless of the blowing agents used. They are two different things.
If you're going with dense pack cellulose, I'd go with staggered studs to get rid of the thermal bridges. Once you go with cellulose, the entire "make it fit between stuff" problem isn't an issue anymore, so the framing can be done in different ways without worries about insulating what you end up with. I'm not sure how a staggered 2x4 studwall would compare to a 2x6 studwall though in terms of wind resistance -- my guess would be if the concern was for strength alone, the 2x6 wall would have a big advantage. It would be possible to build a staggerd stud wall with 2x6s for the exterior and 2x4s for the interior though, on a 2x8 (or deeper) plate, to get the benefits of strength AND reduced thermal briding though.
Bill
The newer, HFO blowing agent is far better than the old HFC blowing agent; the GWP (global warming potential) of HFO is about 1000 times less than that of HFC. But that's not the whole story; the other materials used in manufacturing still pack a potent climate punch. I'll attach the results of studies of both products, commissioned by the spray foam industry.
The old LP siding that had a lot of failures has not been on the market since the late 1990s. I have not heard of any problems with LP Smartside, and I know a lot of builders who have been using it for 10+ years.
All good comments and feedback. I will try to digest and take into account as we move forward in our planning of the house. Thanks to all.