HVAC Design for Cold-Climate New Home

Hi everyone, and sorry in advance for the long read. We’ve just broken ground on a new project in the White Mountains of New Hampshire (Thornton), and I’m looking for some input the mechanical systems. First of all, a little background on the project:
slab on grade
1600 sqft, 1 story, 3 BR, 2 BA with an open loft space, +372 sq ft on one end. Has a +400 sq ft conditioned mech rm on the other.
12 pitch cathedral ceiling in the open great room, loft, and scissor truss cathedral in the MBR, and std ceiling in the other BRs.
2×6 construction, R21 (cellulose) + Zip R9 spec’d
2×12 roof with cellulose (R42) and 1.5″ polyisio on the inside (R14 per plans?)
Windows/doors – lots of them, mostly fixed panels but a mix of triple (U-0.18) and dbl paned (U-0.27) Euroline tilt turns, so pretty good.
We’ll be using the place here and there year round, as we need a wheelchair accessible vacation home to ski, hike, etc., but the rest of the time it will be a short-term (hopefully income generating) rental year round.
My architect and build team have engaged a local plumbing/heating contractor (one they’re comfortable with), to design the system. I have asked the builder to apply for the energy star homes certification (offered through NH Saves Program), in hopes that will drive the proper sizing of the systems, but I still haven’t heard back from them on system design parameters. That’s not to say that it’s not happening, I’m just not privy yet to any specifics. The team knows I’m interested in right sizing the systems, and I hope that the concerns I hear about oversizing won’t apply to us. I did suggest that a 3rd party do the load calcs/system design (it was more reasonable than I expected), and I think there was some offense taken at that suggestion (any suggestions welcome on how to make those conversations go smoother?).
Anyway, we are about to start the footings and stem walls, and the panelized walls should come in the next month, so with that said, I have a couple of questions (finally, right?)
1. Given the slab on grade design, it has been recommended by our deign build firm to have hydronic, in-floor heat run by a HE boiler with an indirect water heater. I’m not opposed to it, but, from a short-term rental perspective, I’m concerned it will have a hard time reacting to different guest’s comfort needs. Of course, this means separate cooling/ventilation as well. So what about in-floor heat, running low temp (like 65 or so), with mini split heat pumps/AC, so the heat pumps could boost the heat if needed? We also have plans for a propane stove, ’cause it’s a cabin, and that thing throws 7-25k btu if desired.
2. I went against my team’s advice and had the manual J calcs done by a reputable engineering firm, just because I was curious. (It was cheap insurance?) The outdoor heating design temp used was (-18F) but that is for Mt. Washington, NH, and although that’s what the energy star guide uses as a minimum design temp, I think that data is taken from the Mt Wash. weather station, which seems a bit extreme.
3. DHW – indirect off a boiler, if I go that route, how do we size it? 2 standard showers (no tubs), typical kitchen with dishwasher. (Keep in mind for us, it’s just 3 people, but rental guests don’t seem to care how much water they use…)
4. Would a little 80K (or so) mod-con boiler be sufficient for the DWH and lower heating loads of in-floor heat?
If you’ve made it this far, thanks! Appreciate any input. I’m comfortable enough with my design/build firm, but since they haven’t really specified any specific system info yet, I prefer to have as much info up front as possible.
Thanks,
Jim
GBA Detail Library
A collection of one thousand construction details organized by climate and house part
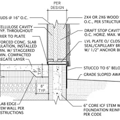
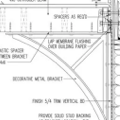
Replies
If you want AC and responsiveness, then you should use ductwork. In that case the in-floor heating is very expensive and rather inefficient compared to a central heat pump, while adding much complexity and trivial redundancy. You didn’t mention the sub-slab insulation, but assuming it’s adequate or better, the floor temp will be rather low. Manual Js typically run oversized, so a 50kbtu could easily be 40kbtu, which would be about 78 degree floors when it’s -18 out. An indirect for only two showers is pretty inefficient and expensive as well.
Thanks for the insight Paul. The slab is to be insulated 3" XPS under and 1" XPS at the edge. Could 2 smaller central ducted systems work? One on each end? The way the house is split by the great room doesn't leave much space to hide ducting. It would be an afterthought at this point, although...it could work.
Great underslab insulation.
Definitely! Two 24,000btu units would get you zoning and some redundancy. Adding backup heat strips, electric baseboard, or propane furnaces would help with the lowest temperatures. The propane stove would be good for power outages.
If you're under .4ACH any fuel burning source is a bad idea for particulate and potential backdraft if you don't' have a make up air system.
Jim,
Lots to think about. We've been in our house in Jackson, NH for almost 8 years now. We're at 1400', so possibly a bit colder/snowier depending on your location. We have a small and simple house that we built with energy efficiency in mind, some posts on GBA about it, start here: https://www.greenbuildingadvisor.com/article/building-a-small-house-in-the-white-mountains
Looks like your slab edge is actually 2" of xps, that's good. What is your ventilation plan? Hopefully an independently ducted HRV.
Some thoughts:
-We went through the Energy Star program. Well worth it for the advice, load calcs, and $4k rebate.
-Not sure if the outdoor heating design temp is actually the Mt Washington Observatory weather station (which would be crazy) or the Mt Washington regional airport in Whitefield. Check out some sites in NH, ME, and VT on this document (https://www.energystar.gov/sites/default/files/asset/document/Design%20Temperature%20Limit%20Reference%20Guide%20%282019%20Ed%29%20-%20ENERGY%20STAR%20SFNH%20Rev11_MFNC%20Rev02.pdf). Something around -10f might be more realistic.
-Your ACH is listed as 3, that is pretty leaky for an energy efficient home, should be pushing for 1.
-Your projected heating load of 50k seems excessive for a 2400 sq ft home. We are heating our 1500 sq ft house with a single 12k minisplit.
-Are you or can you plan for some solar PV?!
-We just rough it during power outages and our house isn't in danger of freezing, even in winter.
1. I would consider ditching the in floor heat, ditch the propane, and just go for air source heat pumps (mini splits). Either ducted or ductless or a combination. If designed/installed properly, they will handle all your heating and cooling needs. No need to add heat strips or electric baseboard, except maybe as a nice touch in bathrooms. And we do need cooling/dehumidification in NH summers.
2. I would have this redone with more accurate input on the weather station and confirm your target ACH with builder.
3. How about just a simple electric tank or heat pump HWH?
4. Go with the air source heat pumps.
Keep in mind I'm just a semi-knowledgeable homeowner, but we GC'd our house and learned a lot.
Brian
Hi Brian,
Not sure how I missed your reply, but thanks so much for sharing your experience. I'll check out your build. We're in the Thornton area, over by Waterville Valley.
We're just about to place footings, and I have yet to see an HVAC proposal, so this has me very nervous about what we will end up with for a system. I'm having a bit of a tough time getting the builder on board with using just the heat pumps. I'm also concerned the budget will be blown with basically 2 systems in place. Trying to get as much info up front so when the conversation happens, I'll be prepared.
Yes, the plan is for ERV, but again, no details yet. I've been trying to push these concerns at build team meetings, to ensure the architect considers space requirements, but haven't been very successful.
I was very surprised to see the -18F design temp as well. It seems that around -7F would be more appropriate. The Energy star manual does list that -18F, but I can't seem to find out why. That's quite a bit north from where I'm at. Is there any guidance on what a designer can do to alter those #s? As I read it, that's the minimum number that should be used, so should they just change to out for -7F and rerun the calc?
The leakage rates were just a guess, I guess, based on the plans. They only list "full air sealing" so who knows.
I went out and used a company known to the GBA community to perform the load calcs, mostly out of curiosity, as I'd played with loadcalc.net and a couple other online tools.
I'd definitely like to be able to add PV down the road. That'd be nice to offset the energy costs. South facing steel roof lends itself well to that I think.
We also have a Rais Viva 120L propane stove planned for the great room, more for ambiance, but it can throw some heat for sure (about 25K btu max) to cover any really cold spells.
Keep in mind, this is a short term rental as well, so we don't want guests calling us saying they need to bundle up either.
Also- I'm really nervous about being held hostage by a propane co... having never had to deal with a 1000 gal underground tank to rent.
Appreciate all the input.
Jim
Jim,
It can be tough to give advice on these forums because we all have different opinions and goals. We wanted a simple (but nice), small, affordable, and energy efficient house...and we made many significant choices with that in mind.
I would recommend checking out what some of the more well known energy efficient building companies are doing for systems:
https://unityhomes.com
https://www.gologic.us
https://garlandmill.com
Personally, I don't see the benefit of adding the expense and complication of propane to this build when electric systems (heat pumps, electric/induction stove, etc.) can meet the needs, but I understand that may be important to you.
Planning for solar PV would be great if you have a nice south facing roof.
Brian
It's tough - once you make the decision to add AC, most forms of hydronics become an expensive luxury with subjective benefits. Most American choose AC and forced air over AC and a separate forced water system.
Thanks guys. I offered to have to heating system designed by a 3rd party, but that idea was met with much disdain. One of the issues I see for ducting the systems (ERV included) is that the great room in the center has no real provision to supply and return from both ends. I suppose exposed ducting could work to solve it (although nor preferable from an aesthetic standpoint), or a dedicated wall mount unit could work, less desirable again. I'll pursue our options at the next meeting. Thanks for the support.
Jim,
Something is off on your man J. Even assuming the -18F design temp is right, 51000BTU for 1600sqft structure with your level of insulation is way too high. If you can post the full Man J, we can take a stab and figure out where the issues are. I would expect your place to come out at about one third that load.
Once the Man J is fixed, you can re-visit the equipment options again. A combination of ducted cold climate heat pumps or a combination of heat pump plus some resistance heat is all that will be needed. Anything hydronic is defiantly a giant waste of money if you also need cooling.
Also in zone 6 you need much more than 1.5" of polyiso for a hybrid roof. You can read more about the proper ratios here:
https://www.buildingscience.com/documents/building-science-insights-newsletters/bsi-100-hybrid-assemblies
In your case, it might be worth while to reduce the amount of insulation in the rafters, simplest is to use thinner batts pushed up against the roof deck and held in place with insulation wires, otherwise you will need a very thick (and costly) layer of exterior rigid.
Akos, I'm a bit bigger than 1600, and the Manual J was completed for 2400sqft, which includes about 1600sqft main floor and 360 of 2nd fl open loft and 450 of conditioned mechanical space on either side of the full height great room. I attached the full Man J, and I'd love to give the engineer a chance to fix it if you see something that looks off.
Also, I was JUST notified that we need to consider adding a full basement (we're days away from footings), based on grade issues/costs to continue with the slab on grade approaching that of a full basement. Not what I wanted to hear, and now I need to go back and read all those sections that I skipped about full basement construction :( . It does however, make it a little more attractive for ventilation/ductwork etc, as well as opening up space for a heatpump water heater, maybe.)
Lot of your losses are glazing, infiltration and slab loss. As Brian mentioned earlier, there is no reason why you can't hit 1ACH, that will take a huge chunk off.
Slab loss is moot now that you might need to go for a basement. With a well sealed and insulated basement, the loss should be still be less than the slab loss in the calculation.
There are some big losses form the 0.27 windows. I would look at upgrading the larger ones to triple pane, you can save some cost by making some of the smaller operable ones double pane to compensate. Watch when mixing triple/double on the same wall as they can be much darker. I would look at some mix and match coating options to get them to a closer shade if needed.
Nailing down your actual outdoor design temp will also help in getting your load right. -18F sound more like zone 7.
>"he outdoor heating design temp used was (-18F) but that is for Mt. Washington, NH, and although that’s what the energy star guide uses as a minimum design temp, I think that data is taken from the Mt Wash. weather station, which seems a bit extreme. "
A bit... Thornton is at ~600' of elevation, the Mt. Washington weather station is at ~6000'. Lebanon's design temp is -3F, Laconia is +1F, Concord is 0F. I suspect Thornton's 99% temperature bin is somewhere in that range- call it 0F. See:
https://higherlogicdownload.s3.amazonaws.com/ACCA/c6b38bda-2e04-4f93-bd51-7a80525ad936/UploadedImages/Outdoor-Design-Conditions-1.pdf
While the first page of the Man-J _SAYS_ they used the Lebanon airport for design condition criteria, they must have overridden the default 99% design temp for Lebanon (elevation ~600').
Starting out with a design temp 15-20F colder than reality is a pretty fat thumb on the scale, adding 20-25% to the heat load numbers. That's a pretty inane thing to do even with a code-minimum type house, let alone a tighter & better than code house. I'm sure there are other thumbs on the scale buried in there somewhere, but that's a pretty fat one- so fat it hits you right between the eyes on the very first page. Is the rest crap? I don't know, but the rest is at best suspect, given the starting point.
>"Also- I'm really nervous about being held hostage by a propane co... having never had to deal with a 1000 gal underground tank to rent."
With 99% design temps warmer than -10F (which yours SURELY is, even atop the highest hill in Thornton) it's more reasonable to go with cold climate heat pumps (ducted or ductless) that with condensing propane equipment. Fossil-burners are rapidly becoming the past, and there is no good reason to go there (unless you own a gas well & local processing plant extracting the propane :-) ). The capital sunk into a 1000 gallon tank & buried installation is better applied to rooftop solar and an LFP battery (or a much smaller above ground tank + propane backup generator.)
Hi Dana, thanks for weighing in. Here's the thing, the Energy Star Design Temperature Guide actually lists that -18 and Mt Washington as the design temp for Grafton County, where Thornton is located. I can't fault the designer if that's what's listed can I? I am trying to apply for the Energy Star certification, so that seems odd to me. Could I ask that it be rerun using Lebanon's -3F?
So, met with the build team earlier today, and looks like we're going with the full basement. I'm told it includes insulation to code, but we'll see once we have a revised foundation detail. The window package is already on order, so my mix of triple/doubles will be what it is (We've already pushed harder than they'd like to get the Euro windows, so that will have to do).
The builder is NOT a fan of the heat pumps, basically saying: "It won't work. We've tried it. You need propane backup at least up here." I've asked them to take it to their HVAC contractor anyway to see what he says, but I'm not optimistic. More awkward discussions to follow, I'm sure.
If I can get some more clarification on my outdoor design temp issue, I'll go for a rerun of the load calcs and see where we're at.
If you have the ability to run ducting in the basement ceiling and use a single HVAC unit, adding a propane furnace as backup isn't the worst idea. Just because it's installed doesn't mean you'll need it! You could even disable it if you want. Avoiding the in-floor heating is the huge costs savings here, so a propane furnace, while probably unnecessary, is an easy concession.
Heat pumps were an issue in colder climate before hyper heat units become available. A number of current generation hyper heat units will deliver their nameplate capacity down to -5F and some can run down to -22F.
In my area (-2F design temp) I'm heating a house that is a mix of uninsulated double brick and new construction with a pair of ducted heat pumps without issues. The heat pumps carry the whole place without any resistance backup.
Up further north with -16F design temperature, I'm heating a 550sqft pretty basic 2x6 build cottage with a single one ton hyper heat unit.
If you look at the current price of propane, around me heat pump is about 2.5x cheaper to run. Since the cost of furnace+AC+propane tank is more than a cold climate heat pump it makes no financial sense to go for a fuel burner.
This is not some noble environmental goal but simple economics.
Get your man J dialed in and select a right sized heat pump. You'll end up with a much more comfortable place that is cheaper to run. Fuel burner backup is not needed and a waste of money, if you want a piece of mind install a resistance strip heater in the air handler.
There are threads on here for people using heat pumps in much colder place than you for example:
https://www.greenbuildingadvisor.com/question/heat-pump-hvac-systems-in-zone7-new-house-and-what-heat-system-for-backup
I spoke with the manual j designer, and he said they use the energy star reference when no other design temp is provided. He's happy to change it to whatever suits me. I couldn't find any data to support an actual 99% design temp for my exact location, but I feel like we're definitely a little colder than Laconia and Concord. I've asked them to update the manual J for a -3F design temp, and I'll report back with the new numbers. Thanks for all the coaching so far!
Attached is the updated summary, for a -3F design temp. It came in almost 10K BTU lower!
So, at a load like this, thoughts on using a single ducted hyper-heating unit like:
http://www.mylinkdrive.com/viewPdf?srcUrl=http://s3.amazonaws.com/enter.mehvac.com/DAMRoot/Original/10006\M_SUBMITTAL_PVA-A42AA7_PUZ-HA42NKA1_en.pdf
Or better to use 2 separate ducted units like a 24k and an 18K *(or another 24k?)?
Thanks,
Also, attached is what the PUZ-HA42NKA1 looks like on the NEEP tool (which is pretty neat BTW) according to the new load calcs.
Looks like it would handle most of my heating load (I'll have that euro-style propane stove as back-up, because it's pretty). It appears that it will have some low load cycling, and the modulation % looks lower than ideal. Am I reading that right? FYI - I plugged in the data for heating capacity at -13F from the data provided on the submittal sheet. Is that the way that's supposed to work? Should I keep looking?
Looks better. The ACH @50PA is still at 3. With minimal effort you should be able to half that and 1ACH is not really a stretch for a ZipR build with some attention to detail. That would knock about 3/4 ton of heat load off which would put you into the range of a SVZ-KP36NA SUZ-KA36NAHZ which has better modulation range and much cheaper than the P series. The data for this is not in the NEEP database, you'll have to pull the engineering manual for it from:
https://mylinkdrive.com/USA/M_Series/R410A_Systems-1/Outdoor_Equipment/R410A_Outdoor/SUZ_KA36NAHZ?product&categoryName=R410A_Outdoor
With a lot of glazing, two zones might make sense if parts of the house get significantly more solar gain. This can be an issue as those areas tend to overheat whereas the rest the of the house will run colder. Unshaded large west facing windows are typically the worst for this. Your hvac designer can take a look and advise on how to split it up. This will add a bit of cost to your mechanical budget. In case of two units, make sure that each one is on its own outdoor unit, don't go for a multi split. Multi splits have much lower modulation range and tend to be less efficient for about the same BOM cost as two one-to-one units.
It is also possible to zone a large SVZ/PVA. The simple setup (thermostat module + Honeywell zoning controls) is not the best as you loose some modulation, the expensive one (Airzone) might be a challenge for your HVAC installer to configure properly.
Hi all, just a status on my heat pump design woes...
HVAC contractor just provided details on the system design. I may be missing something, but I feel like there are many better options. (As reminder that I went out for a 3rd party man J (rough) of about 42K heating at -3, and 23K cooling at 86, Climate zone 6. I also ended up about there with the tool at hvac.betterbuiltnw.com (41K heating). I have not shared this with contractor yet, as I was waiting for more info).
Here's what they've spec'd:
International Comfort Products R4H448GPK (seems like a generic heat pump, might be a Carrier, or other, but searched of the model mostly turn up "out of production") with Tempstar FXM4X4800AL air handler. They've also specified a 20KW backup heat kit. For ventilation, an integrated HRV with separate Panasonic bath fans.
Keep in mind this conversation is happening through the GC, so some things may be lost in translation. When I asked whether we should be considering one of the cold climate options like the Fujitsu AOUH36LMAH/AMUG36LMAS and comparable Mitsubishi Hyper-Heat units, the response from the HVAC contractor was:
"No, and we have the job spec for electric back up. The Fujitsu A/H does have an option for electric back up. Where just shy of what we need.
80,000 input 57,000 output BTU for heat The Fujitsu A/H is 55,000 BTU Max.
4 Tons of air conditioning. 48,000 BTU, the Fujitsu 45,500 BTU."
I'm honestly not sure what that quoted text is supposed to mean (I'll ask for clarification), but it makes me feel like load calcs were certainly not done. I also feel it's not great to start out with a design that requires resistance heat for most of the winter, even if the costs could be offset down the line with roof mounted solar.
When I compare the annual cost of resistance heat for the suggested 4 ton unit and the 3 ton Fujitsu, it looks like the Fujitsu would save about $800/yr, in heating costs alone (I haven't evaluated cooling yet, but the 3 ton seems much closer to my estimated cooling load (Still 1.5x oversized).
I'm hoping that I won't have to chock this up to one more example of "Implementing Energy-Saving Advice Isn’t Always Easy". I appreciate all the input.
20kW backup heat is about 70000BTU. That is silly. You need to upgrade your service just to be able to run it.
You want a properly sized cold climate unit, the one they suggest is not it by a long shot. It would be fine for zone 3/4, but it will simply not work in zone 6. The properly sized hyper heat unit is about the same cost as what they suggest, so there is no reason to get one that falls flat in cold weather, needs a silly large heat strip and costs you more to run.
If they want Carrier, there are better spec units that are essentially re-baded Midea cold climate heat pumps ie:
https://ashp.neep.org/#!/product/65359/7/25000///0
Thanks Akos. Not sure about the brand, as the spec sheet they sent seems to have no brand info other than ICP in the file fine print.
Looks exactly like this unit here, even has the exact same data sheet:
https://hvacdirect.com/4-ton-14-seer-airquest-heat-pump-with-air-handler-id82757.html
My thought is that they've spec'd the absolute cheapest unit they can find, and are backing it with the heat strip. I will try to convince them to take another stab, but their first effort seems to show they have little experience sizing for cold climate heat pumps. After that, it might be time for another HVAC guy, if we can find one.
Often you’ll have to prescribe the solution yourself. If the load is 41kbtu, then plenty of cold climate options fit that and if you do slightly undersize it, adding 3-5kw of resistance backup is easy enough. If you sign off on a “undersized” Fujitsu, that might be good enough. 4 tons of AC is embarrassing to suggest in your climate.
The confusing part is that while they’re suggesting an inadequate heat pump, it’s not exactly a well known inadequate heat pump, so what exactly is the point?
Being in zone 6 one of the things to keep in mind is that the efficiency of air source heat pumps decreases as the outdoors air temperature lowers. Also, the colder it gets the more often the pump has to go through a defrost cycle, and that uses a lot of energy.
One option would be to use a preheater like the Comfofond-L from Zehnder.
https://www.international.zehnder-systems.com/comfofond-sub-soil-heat-exchanger
Another option would be the Tempeff Dual Core, which also doesn't need a defrost cycle.
https://www.tempeff.com/dual-core-difference/
3 ton Fujitsu airstage full vrf with your choice of indoor air handling units. Keep it simple.
No need for backup.
Based on some very preliminary comments I'm getting from my GC, I'll be going down this very same frustrating road with him and the HVAC contractor soon. I am already feeling your pain Jim, having to negotiate heat and cooling loads, and then the actual units, with the professionals. Argh.
Decided to reach out on my own for an HVAC contractor near my build area. Spoke with a "Fujitsu Elite" installer, providing my original Manual J, research on NEEP and my tentatively preferred system ( AOUH36LMAH1/AMUG36LMAS) and here's what I received. Just another oversized manual J and ridiculously sized system. This time it came in at a 4 ton LG PLUS a 2 ton LG (wait didn't I ask for Fujitsu?). Design temps for Lebanon, NH used were -9F and 94F. Looks fishy right off the bat.
I've spoken with the build team and the next step is to reach out to a "system designer" (not sure who this is yet), who will supposedly respect the calc's done by a HERS rater for the Energy Star program, and try to regroup. We're starting to frame this week so I have to get on the ball.
Jim & Nick
Your experiences are not unique. It seems the HVAC industry has an overwhelming level of incompetence. The code and inspection officials are not going to take on fixing this. The only hope is that the mfg of the equipment will take it on, but my hopes have been dimmed by two supposed Mitsu "Diamond Elite" dealers whose field techs know less than I do, and I have never installed an HVAC unit - everything I learned is by reading on this site and Energy Vanguard.
The mfg need to figure out some sort of way to make if financially better for HVAC companies to be knowledgeable and implement that knowledge. So far none of their efforts have worked to any impactful level. It is very discouraging that this is always an uphill battle, because with this industry, the consumer educating themselves results in the consumer often being more knowledgeable than the "professional."
When looking for ducted mini split installers, I had the best luck with a company that also did commercial work. I still ended up installing it myself due to cost, but they respected a third party Manual J and didn’t try to sell me an oversized system.
I’m not sure if you will find anyone in your area, but it might be worth looking.
Thanks Kyle, that's a good idea, I'll check around. And, if I have EV (or someone) design the system, I'll have what I need for a commercial installer.
It may add some delay, but have you considered enlisting a third-party firm such as Energy Vanguard to design your HVAC system?
I have actually begun that conversation already. Just need to confirm with the build team this week, and understand impacts, etc. Although without it, I feel we're no closer to a system, so shouldn't be a real showstopper. Thanks,
You could try consulting Corbett Lunsford. He has a Youtube channel called Home Performance TV and does consulting.
https://www.youtube.com/@HomePerformance
I'll be following this thread with great interest. For the original design of our new home, I enlisted HVAC Design Pros to design the entire HVAC system, which they did very well. But then the builder said that his HVAC contractor did not agree with the proposed system. And as in your case, I could not really talk to the HVAC contractor, so that was $4000 wasted (other than me learning how the system SHOULD have been designed).
Fast forward one year, we have a new design team and a new house design. The builder gave us a quote for the HVAC, but all he said so far about the details is that it's a "heat pump with two zones, and a separate ductless mini split for the ADU". I'm planning to ask him for more details, but I really worry that I won't get much more, certainly not load calcs.
So I'm again pondering using a consultant to generate the load calcs, but I don't know what to do if the builder does not divulge the HVAC system details, or does not want my involvement in HVAC at all.
So I'm curious to see how your situation works out, and whether you are able to prevail in this endeavor.
Hi all,
Believe it or not, I've still not come all the way though this HVAC design issue, but have engaged a new contractor, who recommends Mitsubishi (model TBD), but will install whatever I want. My full system design from EV is still a month out, and I need to lock down the new HVAC contactor ASAP (we're ready to start mechanicals now). So, I've come really close to pulling the trigger and going with the Fujitsu Airstage 3 tonner (AOUH36LMAH/AMUG36LMAS), based almost solely on the NEEP performance charts (and brand quality assumptions). When comparing performance of different models within the NEEP application, I just want to be sure I'm comparing the same data points. Can anyone tell me if:
1. In the NEEP application, there's the option to "Manually Set Low Temperature Capacity Rating". The field to fill in says "Maximum Capacity (BTU)". I expect I use the "total capacity" listed in the MFR design specs? I attached the "heating capacity" table from the Fujitsu design manual, which states:
"NOTE: Values mentioned in the table are calculated based on the maximum capacity."
Does that mean it excludes defrost cycles? And if so, is that even realistic to use to compare low temp performance?
2. I'm back and forth on the 3 ton vs 4 ton. As a part-time short term rental, I'm very concerned about meeting heating capacity if defrost cycles affect the design temp (and lower) performance. No one wants to be cold...
3. In the Mitsubishi world, a similar option is the SUZ/SVA line, but NEEP doesn't have that combo. The data at mylinkdrive.com is similarly confusing, as the rated and max capacity is vastly different. which #'s shoul I be looking at to ensure coverage at my design temp (-3f)?
Thanks again for any knowledgeable eyes on this. Hopefully we'll be installing soon!
Rated output is only used for peroformance testing to get SEER and HSPF number. It has no use in the real world, you always size these by max output.
As for defrost, look at P810 here for the correction factor for your outdoor temperature:
https://mylinkdrive.com/viewPdf?srcUrl=http://s3.amazonaws.com/enter.mehvac.com/DAMRoot/Original/10006/M-Series_Technical%20Data%20Book_01-2021.pdf
You mostly loose capacity near freezing.
Hi Jim,
I read though your messages and these are the time wasters I'm trying to avoid. Looks like you are 6 months in and still trying to figure it out. I'm rebuilding/renovating an 1877 6000sq/ft mixed use building in Bethlehem, NH with retail on the 1st floor and a 3bd apartment on the 2nd floor. The HVAC is my biggest fear out of everything. My wife and I are going to live and work here so I want to nail the HVAC design.
I've invited some local HVAC contractors over to do a walk through and look at my 2D floor plans, etc. I've come to the conclusion that the scope is beyond what most of the contractors here are used to doing and that I need to pay someone to do a total design and spec all the equipment. I just don't think there is enough experience with heat pumps and ERVs up here. For a house, it's crazy that so many contractors are still 10+ years behind in technology, but I guess they install what they know and most people don't know any better.
I've emailed back and forth with these guys and plan to have a call next week. I hope the call goes well and I can move forward - https://www.heatloadusa.com/ There is also a Diamond Mitsubishi dealer near me. I had him come over with his regional rep and do a walk through. I sent him my floor plans and asked him to engage the Mitsubishi performance dept directly to properly design the system and do load calculations. This stuff isn't cheap and you are the one that has to live with it so don't compromise. Let us know what you end up doing!
@Poindexter77
@jimgove30
did you ever find any competent HVAC contractors in New Hampshire?
I'm in southern New Hampshire so a bit of a drive from the White Mountains, but hoping you have some leads for me to avoid time wasting
email me twdATgmail.com if you have any tips to share
Ok guys, so next week we start the mechanical install. I should have my 1st draft of the full system design tomorrow from EV, and will hand it over to the HVAC contractor. Just when I was feeling really good today, my HVAC contractor sent me an email which basically said, "My normal load calc guy says your load calcs are way off, partly because of those "hinged windows" (Dbl and trip pane Euroline, fixed and tilt turns) and the load is more like 100k BTU! (spec'd a 100k and a 40K furnace)! Wow, are these guys not getting it? Pull me off the ledge, and tell me my Fujitsu Airstage 3 tonner I'm about to install next week is gonna be fine! EV's design seems to think so...
The good part about having and HVAC engineer design your system is that they certify it. If it doesn't work as designed they are responsible. I doubt EV would take that lightly so the system they speced will work.
As a reference, a while back I did a fuel use based heat loss for a slightly larger uninsualted double brick and it came in at 39000BTU in zone 5. A 100k furnace for a new build 1600sqft is beyond silly.