Proper crawl space encapsulation and also radon mitigation questions

Hello, I own a 1968 cape cod style home in East Stroudsburg in the Poconos, PA (region 5). It has a full basement with 7′ ceilings and concrete floor with probably little to no crushed stone underneath. At some point, there was a ditch cut out along 2 of the walls, with stone and probably a perforated pipe added, and concrete poured back except for a small channel along the block wall. This leads to a sump pit.
Adjacent to one of these 2 walls is a crawl space entrance where an addition was put in.
I am about to hire a radon mitigation contractor to mitigate an 11pciL radon level, and a spray foam contractor to encapsulate my crawl space.
I did some research and found this product which I like as a liner for the crawl space:
http://www.emecole.com/90mil-crawl-space-liner/
However, there are a lot of irregularities in the ground of the crawl space. It appears to be dirt, but is very hard, and even seems to have some patches of concrete. There’s also a perimeter drain dug along one or two of the walls in the crawl space. I intend to use this crawl space for storage, and I will also need to access it periodically when running wires and things. Also the radon mitigator may need to put a pipe into the ground here.
I want to make sure I protect the liner properly so it’s not damaged from crawling around in there and storing things. The radon mitigator suggested laying this on the ground prior to installation of the liner. Is this a good idea?
The liner I presume is only run up the wall about 6″ or so, and then covered with spray foam. We agreed on a 3″ minimum level of spray foam on the band joist and block wall of the 3 exterior walls of the crawl space. The wall adjacent to the full basement would only have a small bit of spray foam to cover the liner. The type of spray foam he will use is Lapolla 4G. Is this a good product and a sound plan?
He said it can be installed if it’s over 20F, which next Thursday will be. Is the formulation used for cold weather less effective than that used in warm weather or the same?
The other main question I have is how to handle the hatch/opening between the crawl space and the full basement. How do we finish the encapsulation under the hatch, and protect the liner in this area?
I can provide any pictures and measurements that are requested. I will have more questions regarding the radon mitigation later, but for now am mostly trying to nail down the encapsulation and only mentioned the radon mitigation for context.
GBA Detail Library
A collection of one thousand construction details organized by climate and house part
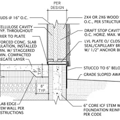
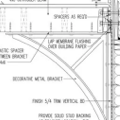
Replies
Ryan,
First of all, in case you haven't seen it yet -- here is a link to an article on this topic: Building an Unvented Crawl Space.
Q. "The radon mitigator suggested laying this [Foamular fanfold XPS insulation] on the ground prior to installation of the liner. Is this a good idea?"
A. Sure, that should work. It should provide some cushioning against sharp edges.
Q. "The type of spray foam he will use is Lapolla 4G. Is this a good product and a sound plan?"
A. Lapolla Foam-Lok 2000-4G is a closed-cell spray foam insulation. That's the type of insulation that you need in a crawl space. That said, the quality of a spray foam job has very little to do with the brand of insulation used; it has more to do with the skill of the installer. Here is a link to a data sheet with more information on this product: Lapolla Foam-Lok 2000-4G.
Q. "Is the formulation used for cold weather less effective than that used in warm weather?"
A. Not that I know of. However, applications in cold weather can be tricky. Again, the success of the job depends on the conscientiousness of the installer.
Q. "How do we handle the hatch/opening between the crawl space and the full basement? How do we finish the encapsulation under the hatch, and protect the liner in this area?"
A. You should lay down a few pieces of OSB above the vapor barrier membrane in this area, to protect the membrane. You should also lay down more pieces OSB to form a walkway (crawlway) in areas where maintenance workers will need access.
Hi Martin,
Thanks for the reply. Yes I've read the article a few times to absorb all the information. At the moment there has been no discussion for the addition of mechanical exhaust ventilation. We don't have a furnace. We presently heat the home using a coal stove with backup electrical resistance baseboard heating used sparingly. We don't presently cool the home except for a couple of window A/C units. We do have plans to possibly install a multi-split system, but I am still performing research on this before deciding. Our heating this winter has been very inexpensive with coal at $160 per ton so it's hard to justify the investment. Would this type of mechanical ventilation still make sense in our case? Should I just cut out a passive floor vent between the crawl space and the living space above? The crawl space can always be open to the full basement through an entry hatch which does not need to be kept closed.
Your article also suggests bringing the liner a minimum of 6" up the wall, and then later mentioned bringing it all the way up the wall to within 3" of the top. But since the walls will be covered by closed cell foam, is there any amount of length that they really must come up the wall? Or just a few inches, enough to be covered by the spray foam.
I assume the channels cut along the walls are for moisture collection. And as I mentioned, the sump pit is in the full basement, but in a corner adjacent to a corner of the crawl space where one of these channels also ends. Is there anything I need to be concerned about with my process that will interfere with their function of passing along any moisture to the sump pit?
Can you provide any additional guidelines I can use to help ensure a quality installation on the spray foam? The one thing I specified in advance was that a 3" minimum be applied as opposed to an "average" which was the original language of the contract proposal. I did read the datasheet on the Lapolla 4G and noticed a few things there, such as not applying more than 3" at a time, which is interesting since my contract calls for a 3" minimum - they will either have to get it exactly right on one pass, do it in 2 smaller passes, or else they will slightly overspray and cause some slight risk of fire and/or odors that do not dissipate with time.
Also we don't have any plans to cover or coat the spray foam in this room (for fire protection). There are no local codes requiring such, but I wanted to know if it's a good idea to do something just in case.
OK, so I will obviously not fasten the OSB in any way, as I don't want to puncture the liner. I will just lay it down directly over the liner at the entrance and in any areas I expect myself or others to be crawling around to. I also see in your article a suggestion of pouring a 2-3" rat slab over the liner. So alternatively, I could do this with self leveling concrete after the encapsulation is finished and just cover the entire thing?
Also, I'm not sure why the radon mitigator wants to puncture a pipe into this room, since it will be encapsulated, I cannot see how any radon gases can come up through this area? But I see your article suggests installing a passive radon collection system. His system though is going to be an interconnected series of pvc pipes connected to a continuous fan which gets vented above the roofline. I did notice your article states unvented crawl spaces can have radon levels 10 times higher than vented crawl spaces, though I'm not sure I understand how the radon would enter if it's encapsulated. If there is a solid reason for him to add a collection point in here, and he must puncture through the liner, what is the proper way to seal around his pipe to not lose the benefit of encapsulating? The encapsulation will be done before the radon mitigation.
Thanks again,
Ryan
Lapolla 2000-4G! That's terrific! That's the one product on the market that doesn't have a high global warming impact blow agent!
Ryan,
Concerning ventilation for your crawl space: I advise what is called "watchful waiting." If the crawl space doesn't seem damp or smelly without any ventilation, then you don't need any ventilation. If the crawl space develops some type of moisture problem after the encapsulation work has been completed, describe the problem here on the GBA site, and we'll give you some advice on what to do next.
By the way, even though coal is cheap, it's not very good for the environment to burn coal. Just saying. After all, this is a green building site. You might want to come up with a transition plan to move to a more environmentally friendly heating fuel.
If you are installing closed-cell spray foam on the walls, it really doesn't matter how far up the walls the floor membrane extends. Six inches is fine.
Concerning your sump and the open drainage trenches: it's hard to visualize what you are talking about, but this is probably a question for your radon mitigation contractor. Here is a link to an article on radon mitigation: All About Radon.
If your floor isn't too uneven, then a rat slab is an excellent idea. There are no down sides (other than cost) to installing a rat slab.
It's normal for a radon mitigation contractor to install a vertical pipe that penetrates the vapor barrier. Don't worry; your radon mitigation contractor will know how to seal this penetration in an airtight manner.
Thank you for all the helpful advice.
I am not sure about this, but is it possible that some of the radon is coming from the coal or coal ash?
No, not at any level that is affecting my indoor air measurement.
Guys, I need some quick advice if possible. My crawl space is actually scheduled to be encapsulated tomorrow morning. I was going through, vacuuming up any dust and bagging up the old insulation. My intention was to lay down that 1/4" foam board tonight so it's ready for them in the morning. They are laying down a 90 mil Emecole liner and closed cell foam on the walls.
However, it's raining pretty hard, and I just noticed a small leak in one part of the block wall, and one section of the footer is very wet. There is a channel cut in next to the footer going around about half of the perimeter. There was old wood rotted inside this channel that I pulled out. It's apparent that they put the wood in on purpose to keep this water channel of sorts. The crawl space itself actually already has a very thin liner laid over it, and then a very thin rocky layer of cement was poured over that. I didn't even realize it until I went in and started vacuuming. The concrete is broken in places and the liner has lots of punctures. Please note the pictures to see the small part of the block where the water is coming through, and also the damp footer along the channel.
My question is, what do I need to do to fix this problem? I don't want to cancel the encapsulation job, we jumped through lots of hoops to make sure it could get scheduled for tomorrow (as did the contractor). Is this something that I can wait until the spring, dig down and patch some holes and apply a coating to the exterior of the block wall? Or must it be dealt with urgently prior to the encapsulation? How can I protect the 1/4" foam board in that area that I was going to lay over the ground? Should I have them lay a strip of the Emecole liner along this corner, under the foam board. Then the foam board, Then the actual liner. Then spray foam the walls? So that any water that comes in, just drizzles straight down into that channel, and only touches the liner?
Thanks.
Well, I asked them to lay a piece of poly along the width of the footer, from 2-3 blocks up in height, down to the footer, crossing over the channel, and a foot or two over the crawl space slab. So any water that comes in should hit that and fall into the channel and not affect the foam board or spray foam, or get onto the crawl space slab.
I'll have to wait until the spring to dig down outside to the footer. What should I do at this point? Patch the block with mortar, and paint some kind of tar mixture over the block and refill? The grading is already good - grades away from the house. So not sure why this one section is getting infiltration. There are gutter pipes that run along here, so that may need inspecting.
The job is complete and I'm pretty satisifed with it. There were a few spots under 3" but they went back in and topped them off. The only thing I wasn't thrilled about, but might not matter, is that they only brought the liner up 6" on the block wall on the 3 exterior walls of the crawl space. They only brought it to the edge of the floor where the block begins on the interior wall, and then foamed over it perhaps 6" up the wall to seal it. Is this a non-issue?
Any comments on my previous issue and my chosen resolution?
I was thinking instead of laying OSB over it, I would actually just lay some more rigid foam board on top and tape them together. This way it's softer on my knees when crawling around in there. Any suggestions on thickness and type of foam for durability with storing stuff on top? I was thinking either 1/2" or 1". Can I use PolyISO or would XPS be better?
Actually, now I'm thinking I'll just lay a roll of indoor/outdoor carpet. It's 12' wide and there will just be a few inches on each side of liner exposed. This is the most inexpensive one I found and seems like it will do:
http://www.homedepot.com/p/TrafficMASTER-Elevations-Color-Sky-Grey-Ribbed-Indoor-Outdoor-12-ft-Carpet-7PD5N660144H/203240740
There doesn't seem to be anybody around the last couple of days but I'd appreciate any comments from my last few posts. Thanks!
Kind of surprised this series of questions didn't receive any responses in 4 days. Wondering if it was just too lengthy or if I should have started a new thread with the questions?
Ryan,
Lots of questions. I was on vacation last week, and I guess no other GBA reader volunteered any advice.
If you want to excavate on the exterior next spring, go ahead. You'll learn something. You may be able to figure out why water is entering at that point. If there are any underground conductor pipes carrying roof water from your gutters, make sure that these pipes aren't perforated. Depending on how much excavation you do, you may want to install some asphaltic dampproofing compound on the exterior of your foundation. Backfill carefully, and use clay-rich soil for the top 6 inches.
Does that interior trench lead to a sump? If so, how is the sump drained -- with a sump pump or a drain to daylight?
It's fine to install indoor/outdoor carpet above the floor liner to create a surface to crawl on.
Hi Martin,
Thanks for the reply! There is a pipe that traverses that side of the house which carries water from the gutters. I've never inspected this pipe so it could be blocked up or broken. I'll definitely follow your suggestions come spring.
The interior trench stops at the interior block wall, but directly on the other side of this block wall (and down another 3-4 feet) is my sump pit. There doesn't seem to be any connection created between the end of the trench and the sump pit, though. The sump pit has a pedestal sump pump (and I just purchased a submersible pump to swap that out with) which empties into a gutter (which empties into the same pipe described above).
I have 2 more questions now regarding this space.
1) I'm concerned about a fire barrier. Not so much for code purposes, but rather for safety. I don't think my local code requires one in the crawl space, if I keep the hatch door closed between the full basement and the crawl space, but I don't particularly want to keep a hatch door in place here. I've read several articles of yours on crawl spaces, basements, and spray foam, and my 3 main options seem to be 1/4" hardboard, 3/8" particleboard, or 3/8" drywall. Due to the size of the hatch, a 4'x8' piece of material is impractical, so
Seems 3/8" drywall would be the cheapest. I could use this ripped into 8'x2' pieces, to fit through the hatch:
http://www.homedepot.com/p/Sheetrock-3-8-in-x-4-ft-x-8-ft-Gypsum-Board-14109012208/100321594
Alternatively this ripped into 8'x2' strips, at about double the price:
http://www.lowes.com/pd_49156-99899-49156___
So perhaps this ripped to 8'x2' abd doubled up in thickness, also more expensive:
http://www.lowes.com/pd_15483-46498-SS1254825_1z0ufgy__?productId=3014304&pl=1
The question though is this - I did not think to frame a stud wall prior to spraying. And the bottom of the spray really creeps into the room quite a bit so that I would lose a lot of space if I were to frame walls around this crawl space. Is there any way to apply a fire barrier against this spray foam without framing a stud wall in front of the foam?
2) From time to time, I will need to drill holes through the foam to run new wires into my garage or some other area. If I do this, is there a preferable way to patch the closed cell foam around the wires? So far, this is the product that seems to make the most sense to me. However, since it is a one-time use product, it seems there would be a lot of waste if I just wanted to patch a small hole or 2:
https://www.sprayfoamkit.com/products/spray-foam-kits/foam-it-12-patch-a-repair-kit-detail?gclid=Cj0KEQiA89u1BRDz8enExq7rvN0BEiQAaFCHmwnuy1q1Nu4yFmowq8srua7-LO6SeOJ9zY0-AMapFFQaAmQe8P8HAQ
Ryan,
You are correct: if you don't have any studs, you can't use drywall as an ignition barrier over cured spray foam.
The standard solution is to install an intumescent coating. Because of code requirements for approving these products, you must use a brand of intumescent coating that has been tested with your brand of spray foam. You'll have to contact the manufacturer of the spray foam that was installed on your crawl space walls to determine which intumescent coatings, if any, will work in your case. For more information on intumescent coatings, see Thermal Barriers and Ignition Barriers for Spray Foam.
Concerning your second question -- sealing the leaks around holes drilled through cured spray foam for wiring penetrations -- you should just pick up a small can of spray foam at any hardware store -- something like Great Stuff. The cost is $5 a can.
Thank you! I called Lapolla and asked which intumescent coatings were approved over Foam-Lok 2000-4G and they were supposed to get back to me but haven't yet. In the mean time, I found this article:
http://www.lapolla.com/wp-content/uploads/2014/11/lapolla-ccrr-1025.pdf
which suggests that DC 315 is suitable, so I will pick up 5 gallons of that. Much appreciated!