Roofing leak near eave

Could a roofer possibly give an explanation as to what is occurring near my eave adjacent to a side wall. I have included pics. This has been about 8- 10 years in the making. There is currently a small depression (pic 1875) which is from deteriorating decking, but for 8-10 years there was dripping from underneath the soffitt below where this depression is pic 1871. The water also runs down alongside the house – pic 1869. (This water is not coming from the eave trough. At first that’s what I thought it was and patched what may have been any holes within it years ago ) It rained here today and the pics show where the water runs. The drip edge is a clean white down gradient of the bad decking (compare pics 1875 & 1877), but a few feet from that area the drip edge is black showing that the water is running over the drip edge rather than into the eave.
As can be seen in the pic the depression is down gradient of where a nail would have been driven at a break in the shingle tab.
GBA Detail Library
A collection of one thousand construction details organized by climate and house part
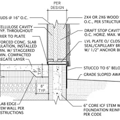
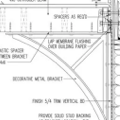
Replies
Get your home reroofed, include in the contract the water damage cause is to be remediated. If I were doing the job I would remove the roofing and the side wall siding. I flash and run ice and water shield 18" up side walls and up the corners of fake chimneys which love to leak... and rarely are flashed well or at all.
Make sure you don't have an AC unit that has a condensate drain goof up
Shouldn't be hard to find your problem when demoing your rotted structure just follow the rot and water.
I am going to have this area repaired. The rest of the roof is fine. It's just this one area. I would think that an ice and water membrane should be used. There is a valley above the corner of the house shown in the picture, and there is a lot of snow build up behind that corner in the winter, which drains slowly as it melts which I think is a contributing factor.
One roofer who gave an estimate said that I had bitumen there now that was just as good, and that I didn't need the membrane. But with this being a high drainage area I would think the membrane would help.
What do you mean by removing the siding? Removing it to place the membrane then covering it with the siding? I would think the house would look odd if it the siding was not replaced.
You need to remove the siding, replace the roof using correct flashing methods at the sidewall, and then replace the siding. It looks like they used caulk for flashing, which is guaranteed to eventually become a problem. If you're installing comp shingles again, you want step flashing, and you want a gap between the siding and the roof.
+1 on David's recommendation on re-working the kick-flashing at the dormer wall. Even if turns out that it's not the primary cause (though it's the prime suspect), it's surely a contributor.
And don't forget the kick-out flashing at the bottom of the dormer roof: http://www.nachi.org/kick-out-flashing.htm
David and Jesse further explained the solution most likely needed. I just thought I would add that if you look at the 3rd picture, the leak is starting beyond the picture and above. So if the poster adds a picture of the roof and sidewall farther up at some point we could see more of what is happening.
Still the bead of caulk running down the sidewall is a big no no. David shows the right way. And like I said, behind the step flashing first item to have is ice and water shield just like done in valleys.
Thanks for the input.
Attached are some more pics of the roof area above the damaged sheeting. The owner of the company that installed the roof came out to look at it and evidently bent back the lower siding corner piece, probably to see if there was step flashing behind the siding. Never told me about it. I had a friend who does roofing come out and he verified that there is no step flashing. I'm going to have him do the work because the company owner became upset with me and impatient when I asked him questions about how he was going to do the job. He never did answer whether he was going to wrap underlayment behind the flash siding as a protection against water intrusion. Just told me I would have to trust him. Like I said before he doesn't use ice and water shield. I had the original bid and told him it said that flashing would be used at all roof penetrations, so I would think he would have used flashing at the side wall too. When I told him that he said, "That was 19 damn years ago." But my friend said it was pretty common to use step flashing even back then. The thing is I had this owner out 4 years ago and explained the problem with the water coming out underneath the soffitt, but he never did anything.
Anyway these 4 pics show the side view above the rotten sheeting. You'll see where I put some roofing tar on top of the shingles to try to divert the water away from what was a small depression where water did not drain off the shingle a couple of years ago. Didn't work. Like I said it had been running down the side off the house for at least the past 10 years when it rained.
Eric,
When I began working as a roofer in 1974 -- I guess that was 40 years ago -- we always used step flashing. Step flashing is not a new invention.
There appears to be a problem at the base of the valley. Does the valley have valley flashing? If so, how wide is it? Where does the valley flashing terminate -- against a wall or beyond the wall? How many inches of overlap is there where the valley flashing overlaps the shingles?
Then here are some pics of the top side wall and the valley. No step flashing there either. The one pic with my hand in it points to an area where there is no caulking near the bent siding. I'm sure there was caulk up there last year when I was up there, and the corner siding seems to show where there was caulking. I've put roof cement to seal the edging along this sidewall in the past, but maybe I missed this area. Going to have to seal it again as there are cracks in it. In the winter snow will accumulate up to and beyond the gable vents. The owner told me that snow will get up behind the siding as high as the snow is on the roof. That's why I asked him whether he was going to but some type of water barrier behind the step flashing. Is that true? I know from observations that the snow will melt away from the siding due to heat loss in the winter, leaving a gap between the siding and the snow. I just have a hard time believing that the snow will get behind the siding without melting as it enters. My side walls are not insulated.
Then one last thing. Although the bid called for placing flashing at all roof penetrations, according to my roofing friend none were placed around the standpipes. He thought it unusual that the old type of leaden, rather than plastic replacement, standpipes were still there on a re-roof job. There also was only one layer of shingling on the upper level of the house, but two on the area above the garage, where the rotten sheathing is. The contract states to re-roof the house with shingles. It doesn't specify that sheeting will be installed. Do you think $2000 in 1995 would be for just re-shingling the house, or a total re-roofing, with sheeting? My father was alive and living here when the work was done, but I was at work when the job was done so I didn't see it, but I do tend to remember being told to make sure I didn't drive over any nails in the driveway.
Eric,
Basically, you have a no-flashing roof installed by a know-nothing roofer.
Rip everything off and start from scratch. You need new roof sheathing, underlayment, drip edge, step flashing, valley flashing, kick-out flashing, Ice & Water Shield, and asphalt shingles. And you will need to remove the lower levels of siding near your roof to do the work properly.
Martin,
I don't know what valley flashing is. But I don't think there is any type of metal flashing at the base of the valley. When I looked behind the bent siding today all I saw was asphalt. My friend said there was no flashing behind the siding. I spoke with the contractor about the valley when I called him and he said there where two layers of 90 lb sheeting/felt in the valley. The valley is about 8 - 10 inches wide. And that the thicker black material at the base of the valley is commercial grade bitumen that is used on flat roofs. He said it was used at the base of my valley because the roof was flat there, which I do not really agree with. There is a slope, but maybe it is less that 1:4 or whatever specifications would denote a flat roof.
Eric,
When you hire a contractor to fix your roof, make sure that the contractor knows what valley flashing is.
Asphalt shingle roofs can have woven valleys (without visible valley flashing) or open valleys (with visible valley flashing). In either case, especially in a configuration like the one shown in your photos, this type of valley will need peel-and-stick flashing that will be invisible when the job is finished.
Martin,
Thanks for the input. Everything you recommended was going to be done save the valley flashing. I did go up into my attic and there does not appear to be any leaking or spotting of the sheathing beneath where the valley is. I thought the white streak might be dry rot, but it's just where the outer sheathing has fallen off. The actual problem may not be as severe as it appears as a couple of years ago I got the bright idea of putting roof cement near the drip edge where most of the water was coming out underneath the shingling, directly beneath the rotted sheathing. There was a small depression then and the water wasn't completely draining off the roof where the sheathing is rotted now, but I probably only exacerbated the problem by making the water back up more. I would just think that if the water was going behind the siding for 19 years that corner would have rotted awhile ago. But I can see how the valley definitely needs to corrected at the side wall.
As a plug for energy efficiency I did seal and insulate my attic and put in new windows, new air conditioner, and a newer energy efficient furnace about 6 years ago and along with thermostat adjustments have reduced my natural gas usage from @1000 CF/year to @ 320 CF, and lowered my electricity usage from @ 6800 KwH/Yr to @ 2200 KwH/Yr.
There's a design issue there... the corner of the upper section of wall is directly in the path of the valley. It would be possible to waterproof that with roofing membrane, but a lot better to have a sheet metal mechanic make a custom piece. I would take a length of valley flashing and solder on a corner cap that covers the walls on both sides of the corner.
You should be prepared for some carpentry repair work when you strip that roof. You'll probably end up with a bunch of siding and sheathing off and getting replaced, possibly some framing, along with roof decking. Hopefully you can grab a week of good dry weather very soon to do this.
David/All,
Thanks for your input. Should have done this four years ago after my "contractor" failed to do anything after he came out.
David, I'm not in the construction field, but when I was taking the pictures and looking at the placement of the valley I came to the same conclusion that the valley shouldn't have been placed to run water up against the house.
With regard to the corner flashing I did find this method in Fine Home Building that might work also? http://www.finehomebuilding.com/how-to/departments/building-skills/bending-kick-out-flashing.aspx
Since we were supposed to get a lot of rain last night I made up a temporary flashing fix as shown in the pics. I couldn't get a good pic to show it but after the water left the "flashing" it went downhill right to where the depression is from the rotting sheathing. From past observations this is where the water has always tended to flow. I think the main problem is that this area gets too much concentrated rain water and snow melt due to the incorrect design of the valley and saturates the roofing near the drip edge. The drip edge also appears to be bent up a bit (pic), it is actually higher than the lower shingles and looks like it is forming a collection area (which may be from the shingles getting saturated and curling?)
My temporary fix stopped the water from flowing down along the siding, but water was still running back and dripping from under the soffitt- from the rotted saturated area above. We received 0.75 inches of rain in about four hours, at a rate at times of 0.50 inches/hr, but no water flowed along the siding for up to six hours (when I stopped looking) after the rain began. Water had always flowed down the siding after a rain before, as shown in the pic in the original post above.
So evidently water had been entering at the top of the side wall, and hopefully, flowing over some existing sheeting all the way to near the edge of the roof, contacting the siding and flowing down it. (My soffitt extends four feet, basically beginning underneath the sidewall corner.) I have never observed any water flowing down the siding directly underneath the sidewall corner where the valley ends, which would be the corner next to the front door, only beneath the gutter and about 20 inches in from the gutter. I did look behind the siding at the splice directly beneath the gutter at the third panel beneath the light (in between where the water would flow down the siding) and the sheathing looked to be the same as at splices at two separate walls of the house. This house was built in 1969, so there is no house wrap. Just hoping the problem was a combination of bad drip edge installation, felt installed short of the drip edge, and possibly an overdriven nail. Guess we'll find out when we remove the sheathing.
So now to prevent this problem from reoccurring I'm thinking about extending the valley by either 1) using metal roofing above the entire new sheathing adjacent to the sidewall, which would cover the main area of water flow from the valley above; 2) using a metal valley/run within the new shingles to over the drip edge to keep the sheathing from getting saturated (which might be hard to do as there is no valley below the side wall corner, or 3) metal over new shingles. Given my unique situation which do you think would be best? Or would a standard installation with step flashing, new drip edge, IWM work just as well?
Should an additional underlayment be placed between metal roofing and an ice and water membrane (IWM) to prevent it from exceeding 180 degrees, or will the metal just conduct the heat upwards away from the roof? I did find this article that indicates that even on an insulated roof (in Florida) the temperature of the shingles don't exceed 160 degrees. http://www.energyvanguard.com/blog-building-science-HERS-BPI/bid/31616/How-Hot-Is-Your-Roof-Insulated-Rooflines-and-Shingle-Temperature
Thanks again.
Eric, my opinion is still that you should get someone with sheet metal skills to make a custom corner/valley flashing piece for you, or at least skillfully adapt stock flashings to work. That's a tough situation, the roof planes are what they are, and you can't really change that, but you can do a lot better as far as protecting that corner from the valley water, and trying to push it out away from the corner so that it doesn't all follow the lower roof/wall intersection to the bottom. The kickout flashing shown in Andy's piece would only apply at the very bottom, at the gutter, and it is essential in this application.
You might be able to get a good roofer recommendation by calling some of the better remodeling contractors in the area and asking who they would use for a tough re-roofing job.
Sorry, wrong link for the corner piece flashing. I mixed them up I meant the one below. http://www.finehomebuilding.com/how-to/departments/building-skills/installing-step-and-corner-flashing-on-a-roof.aspx
Since my house was built in 1969, it would seem that this has been a problem 45 years in the making, or more like 35 since it started at least ten years ago. Lived here since 1982 and I really can't believe that the plywood has lasted this long on the house. It was shingled in 1995, but this is the first work involving replacing sheathing.
Installed OSB sheathing, water and ice membrane, step flashing, new drip edge, asphalt shingles, and a little kick out flashing. Also installed new fascia board as part of the existing one near the sidewall was rotted. The wall fiberboard was OK.
It appeared there were four (4) main contributing factors: 1) There was no final step flashing piece at the base of the roof near the gutter, which allowed the water that had been flowing down the step flashing from above and along the side wall to spread out above the gutter, instead of flowing into it; 2) the existing step flashing, which must have been installed in 1969 as it was found under the first set of shingles, was rusted in places; 3) the existing initial felt underlayment was minimally installed OVER the drip edge, so that the water leaving the last step flashing piece and the rest of the roof area could flow along the drip edge away and wick back up under the felt; and 4) the quantity of water flow from the valley above. You can see from the pics it looks like there was a lot of flow from the final flashing piece away from the sidewall along the drip edge. It was also apparent, and shows in the pics, that the plywood was wet. Only the lower portion was rotted.
The thick modified bitumen at the base of the valley was found to extend up behind the aluminum siding and two pieces of the temporary steel flashing were placed beneath and behind it, with the downhill piece extending a little past the corner. This new flashing extended up behind the siding by at least 4 inches and out into the valley about 8 inches.
Good news for you not much damage, takes a lot to rot plywood. Hope you are checking out the blog on kick out flashing. Also extend your shingles over the eave drip edge 3/4" as that helps get water into the gutter verses adhering to the fascia and going places you don't want it to go.
Completed the work in about six hours, which included the time required to pick up the materials. I had someone I know who has 30 years of roofing experience do the job. The first company that built the house didn't install the flashing correctly, maybe due to a beginner's error, since the first piece was forgotten. Then the contractor who did the re-shingling didn't install new flashing. I also have a friend that is doing work on a drywall/painting work on an historical home that is being refurbished. The contractor for that job installed step flashing as part of a roofing job, but as the house as the old wood shake siding they didn't install the flashing behind the siding. In places there was a 1/2 inch gap between the top of the step flashing and the wall, inviting water to flow behind the flashing. So I figured I'd be better to have an individual I know with experience do the job then hiring some unknown firm, who is going to send out individuals. This was the first time I'd seen a roof being installed, and like I told my friend if I would have hired the contractor that did the re-roof, who owns a company that has been around since 1905, he probably would have walked off the job because of all the questions I was asking. He agreed.
AJ,
Yes, I was glad there wasn't as much damage as I was anticipating. I think it helped that I had four foot wide ventilated metal soffitts so that the water dripping into them could drip through them.
I think he did a good job extending the shingles, although the kick out is more like a drip edge extension. The drip edge is much better than the previous one. Going to have to get some plastic aluminum and repair the corrosion of the siding too.