Should I remove torn housewrap before installing polyiso foam and new housewrap?

Bare with my ignorance on the topic as I am new to this. I am in the process of an 1800 sq ft addition to my home. The existing home was roughly 1400 sq ft, brick home with cinder block walls. I am including that information in case it matters. The addition is wood framing and will be brick. I live in zone 4. The wall cavitys have r 13 batts, the crawlspace will be encapsulated and the attic will be blown in fiberglass (possibly 6″ of open cell foam if budget allows). My wife and I had a terrible experience with the builder and he never finished so now I am finishing the project. I am a furniture maker and I am very anal and overbuild everything. i am sharing that info in case if helps understand my viewpoint. Anyway, the builder used lumber yard house wrap and it has rips and holes all over it, far beyond repairing. I am thinking of installing 1/2″ polyiso foam board, taping the seems, and putting a drip edge where the wood sheathing and bottom plates meet the block foundation. Also putting plywood strips around windows to butt foam. Then i was going to install a new house wrap, either tyvek, typar or ordering some european housewrap if its worth it because i have read they are the best. the new house wrap is where i will be flashing the windows. Also, there will be 1/2″ space between back of brick and housewrap after foam. my questions are, is this approach acceptable and if so, will there be any significant benefit? Also, if it is acceptable and beneficial, do i need to remove the existing torn house wrap? I am sorry if there are threads on this, I feel like i have searched everywhere and havent found an answer to my questions, at least not that I am aware of anyway. i would really appreciate some input, i am open to suggestions because i am no expert (far far from it) and this is a site that seems like people are educated on this kind of topic. I am sorry to bother anyone and again apologize if the answer is all over this site. I am truly just becoming overwhelmed with all of the information and stressing on this matter too much.
GBA Detail Library
A collection of one thousand construction details organized by climate and house part
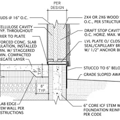
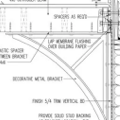
Replies
If you're using half-inch foil faced polyiso on the exterior side of the sheathing you might as well make the foil facer the WRB by taping the seams with a high-quality foil tape and don't bother with housewrap. Keep old housewrap in place, between the foam and the sheathing- it doesn't hurt, can only help.
Use EPDM flashing tape for the window flashing, not housewrap. EPDM flashing tape is much more rugged, and has a very aggressive adhesive for sealing the seams & overlaps air & water tight.
If you're insulating with fiberglass, caulk the framing to the sheathing inside every stud bay, making the sheathing the primary air barrier. If o.c. foam that step isn't really necessary. The thermal performance of 1.8 lb density fiberglass in a caulked stud bay is slightly higher than half-pound polyurethane, but not always cheaper. 1.0lb density fiberglass isn't very air retardent and suffers from convective loss.
With brick veneers weep holes at the bottom course and vent holes at the top course are important for keeping the whole thing dry, but with the foil facers on the foam there isn't much exterior moisture drive reaching the sheathing. The R2.5-R3-ish performance of the foam offers sufficient dew point margin on wintertime interior side moisture drives:
http://publicecodes.cyberregs.com/icod/irc/2012/icod_irc_2012_7_par028.htm
Mind you, R13 + R3 is still below IRC code min for zone 4:
http://publicecodes.cyberregs.com/icod/irc/2012/icod_irc_2012_11_sec002.htm
thank you for your response dana, i appreciate it more than i could put into words. the idea of using the foil facing the WRB is a good idea, thank you. would it be bad to put on another house wrap just to overkill? i am not rich by any means but plan to die in this home and dont mind spending the extra money for more peace of mind.
In regards to caulking the framing, it is too late because sheathing and drywall are both installed already. i am assuming o.c. stands for owens corning. if my assumption is correct, no it was not o.c. foam used in the walls. it was owens corning r 13 batts. I am almost certain the builder didnt caulk anything which is why I am trying to overkill with the foam and house wrap. is the lack of caulking something i should be concerned with?
i did not realize that r 13 wouldnt be sufficient for codes. i am hoping there are some things i can do to compensate for the poor quality of work from the builder. the inside of the house is almost finished so there isnt much i can do inside but we do not have brick up yet which is why im trying to find solutions on the exterior. again, any input or advice is greatly appreciated.
thank you so so much
William,
If you decide to install new housewrap, there is no need to remove the existing housewrap.
You can either use new housewrap as your water-resistive barrier (WRB), or you can use rigid foam as your WRB as Dana suggested. In either case, it's important to know where your WRB is, because the location of your WRB determines how the window flashing is integrated with the WRB.
For more information on these issues, see these articles:
All About Water-Resistive Barriers
Using Rigid Foam As a Water-Resistive Barrier
Flashing Brick Veneer
The "o.c." = "open cell", not Owens Corning, and was in reference to "...possibly 6" of open cell foam if budget allows...", thinking that it might be appropriate for walls too.
In the attic open cell foam isn't really called for- there are cheaper ways to air seal the attic floor, and blown cellulose (preferred) or blown fiberglass is also much cheaper. At 6" the o.c. foam would be nowhere near the R49 code minimum. It takes about 15" of cellulose or open cell foam to hit R49, slightly less with some fiberglass products. Cellulose is more air retardent than mid-density fiberglass, and is also more opaque to infra-red radiation, making it a performance edge at any given R-value over fiberglass. in my area open cell foam in my area runs anywhere from 8- 11 cents per R per square foot, compared to open blown cellulose at 4-6 cents/R-foot. Hopefully you have sufficient vertical space between the top plates of the exterior walls and the roof deck to blow 15" of fiber, with an inch or tow of clearance (?). (If not, how much clearance is available there?)
The R13 meets IRC 2015 if it has R5 continuous insulation over the sheathing. At 0.5" the polyiso is only R3. Local codes may be based on older versions of the IRC. As recently as IRC 2009 an R13 studwall without insulating sheathing was OK for climate zone 4. If it's possible put an inch of foil faced polyiso on the exterior instead of half inch and still maintain at least a half inch masonry cavity (a full inch would be better) it would meet IRC 2015 thermal performance, and would give you better dew point margin at the sheathing against wintertime moisture drives. That would also make up for potential deficiencies in the batt installation quality which is probably not very close to perfect, if the contractor was as sloppy as indicated.
Did they install a polyethylene vapor barrier under the wallboard? (Hopefully not...)
thank you martin and dana again for the help. "O.C.- open cell....hahaha, i told you all i may be slightly ignorant. I wish i had done o.c. foam in the walls. hindsight is always 20/20.
dana, thank you for recommendations on attic insulation. I would certainly like to save money especially if it makes more sense. i considered the open cell foam in the attic because i thought it would be more air tight. when you ask about the vertical space above top plates and roof deck, do you mean directly above the top plates or the whole attic in general? directly above the top plate is about 5" but its a gable roof so plenty of room in the attic. again sorry for the ignorance, just trying to be clear.
i also just read some stuff you wrote dana. "Instead, Dorsett recommends spraying 1 inch to 2 inches of foam against the roof deck and finishing with damp-spray cellulose or high-density fiberglass, a strategy that’s “the best of both worlds.” I think that is an awesome idea from what i have learned regaurding insulation. could that possibly work for me?
in regards to the walls, you are correct in assuming there are probably deficiencies in the batt installation. i would certainly have to agree that the install was very far from perfect (another reason i wanted to do foam board). there is not enough of a brick ledge to do 1" foam without sacrificing space between the brick and foam board.
No, there was no polyethylene vapor barrier used under drywall, just kraft faced batts. I cant say enough thanks for helping me through this process.
If it's only 5" of space between the top plates and the roof deck you would need R10/inch insulation to hit code minimum. Code requires a minimum 1" gap between the insulation and the roof deck, which means it's even worse- you onlyhave 4" there. I this situation as a DIY you may have to cut & stack rigid polyiso, sealed into place with can-foam up to where the clearance to the roof deck is at least 16" and fill in behind it with the blown cellulose. This can be real PITA work, especially on lower slow roofs.
Insulating at the roof deck can be much more expensive. The 2" of closed cell costs about $2 per square foot, and blown fiber in netting is 2-3x as expensive (sometimes more) as open blown cellulose on the attic floor. In zone 4C (marine zone, Pacific northwest) 2" of closed cell foam + 10" of cellulose is good enough to not need interior vapor retarders, but in 4B & 4C you would need 3" of foam + 8" of cellulose, or else figure out how to install an air tight interior side vapor retarder. This is easier to do with simpler roof lines, but it's never exactly "easy".
The kraft faced batts are fine, far better than poly vapor barriers in your stackup. The kraft facers are vapor retardent when dry, but become vapor open if the humidity in the stud bays rises to mold-inducing levels.
i am in zone 4a by the way. i am not planning to do the attic myself. i got a price from the most reputable company in my area to do the encapsulated crawlspace and the attic. They priced me on doing 6" of open cell foam on the roof deck and 3.5" on exterior gable wall. i realize it may be more money but would the company to do the closed cell on the roof deck and me doing open blown cellulose be a good route to go as far as energy efficiency and air tightness?
How would i know if humidity in the stud bays was at mold inducing levels?