Closed-Cell Spray Foam in Unconditioned Attic

My home was built in circa 2005, Zone 4A (WV). 2x story colonial. My Trane Air Handler is in the attic, which is unconditioned. After routine HVAC maintenance, the tech said that I should consider adding some more insulation to the attic as it’s just shy of R30 (blown in fibreglass). Tech also said they don’t install air handlers in unconditioned attics anymore because of issues they’ve seen in the field with equipment failing at a higher rate. I have noticed over the years that certain rooms upstairs are warmer/colder than the others (summer and winter, respectively). Here comes the rabbit hole discussion: First place I found via searching was a company that marketed their proprietary foam solution (USA Insulation). I got handed a ‘datasheet’ which looked more like advertising than anything with limited data and some strange R-value claims. I asked for an MSDS/SDS. They said they’d get back to me (it’s been 3 months now). Some reviews were unimpressive. Next up, I had another indy contractor come over and want to spray the attic ceiling down to near the floor with closed cell spray foam, and then top off the attic floor with some more insulation to bring it up to about R-49 to R-60, plus air sealing. It was a few thousand for this. So the question is – Is closed cell spray foam for an unconditioned attic recommended, or is it open spray foam? Are there caveats to be aware of? I’m kind of nervous to proceed with spray foam at all because I’ve seen some horror stories from roofing colleagues having to fix roofs because of rotting due to spray foam. (Just today, I went up in the attic and the air temperature was 129F at 2pm. Pulled out the thermal imager and noticed some of the non-buried ducts were about 70F, and I noticed *some* leakage on the camera.)
GBA Detail Library
A collection of one thousand construction details organized by climate and house part
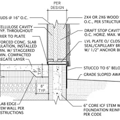
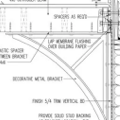
Replies
I'm dealing with one of the horror stories, so I am jaded to the subject.
But one thing that I have learned, is that closed cell should be put against roof sheathing, not open cell. One bid that I had gotten was for a mix of closed cell and EPS boards.
Would you care to elaborate on your horror story?
My story isn't much different than others. No ventilation or containment, and improper application technique. I had open cell installed against a roof line. We went back to the house 3 days after the install, and a lingering odor was the first sign. Then people started to get reactions after being in the house for a short period. Good luck once you are at that point.
With so many other options, I wish I had picked something that has less of a chance of causing permanent damage.
Open cell is much easier to remove than closed cell foam, but any remediation job will be disruptive and expensive. It's why finding a good installer is critical whether you are paying for closed or open cell foam.
If the open cell foam is still in place, I would install a few humidity sensors next to the sheathing and monitor the levels. Something like this: https://www.amazon.com/gp/product/B07R586J37/ref=ox_sc_saved_title_1?smid=A2KZ7X05DCDJDL&psc=1. You may be able to reduce your risk by sending conditioned air into the attic and/or installing a dehumidifier.
What was the type of foam installed?
A minimum R-49 attic should be your target in CZ6B. You can add more fluffy insulation or convert the attic to a sealed space with some amount of new supply air.
While you can combine closed cell foam with air permeable insulation (fiberglass or cellulose), you want to avoid installing open cell foam on the underside of the sheathing. Open cell (or any other air permeable insulation) increases the risk of moisture accumulation in the sheathing, which can eventually lead to rot.
Another option is to move the HVAC equipment out of the attic. If your equipment is 17 years old, this may be the most cost effective solution.
In other words, you have some options for increasing comfort. If it were my house, I would consider moving the equipment and then add additional blown-in or batt insulation. I wouldn't rely on HVAC contractors as trust advisors for making this upgrade since they all have their own agendas. Instead, I would hire an independent HVAC engineer to size and design the new system. (See https://www.greenbuildingadvisor.com/article/who-can-perform-my-load-calculations for more on this topic.) I'd also consider hiring a local HERS rater to do a blower door test and help me map out a plan for making the home more air tight and comfortable.
HVAC equipment is about 5 years old - replaced older, broken HVAC system that only lasted about 10 years before the coils leaked.
I just looked and I do not have any free room for the air handler on the 2nd story, *Unless* I moved the washer and dryer to the ground level in the mudroom. Another option is to get the stackable washer/dryer combos to move them into the same space, then move the air handler to where the washing machine would have been, which, is /very/ close to where the air handler is.
How can I locate a HERS rater?
Look here for a Resnet person: https://www.resnet.us/raters/hers-raters/. It's best to establish a baseline (how leaky your house is currently) and then develop a plan for improving performance.
It's possible you could installed a minisplit system (a one-to-one or multisplit), keep the attic vented, and also move the HVAC into the conditioned space. That said, if the current system is only five years old, converting the attic to conditioned space might be the better option. The HERS rater should be able to help you weigh the pros and cons.
I just recieved a quote from the installers of the HVAC system. To completely move the Air Handler and run new linesets, drip pan, tie into the drain system is going to be more expensive as just adding more blown in insulation to the attic to get R-49+. This does not include the ~=$2k for replacing the washer/dryer with stackables.
It seems moving the air handler to the living space would incur /more/ cost.
tneicna,
When you create an unvented attic it needs to be conditioned to avoid moisture issues. The problem is if you add insulation to the underside of the roof, but also rely on the blown insulation which is in place in the floor, that attic space becomes a hybrid in-between space, that is not fully conditioned, which can have unpredictable results.
My own feeling it's an either or choice. You commit to moving the insulation and air-barrier to the roof plan, or move the HVAC out of the attic and add more insulation to the floor. https://www.greenbuildingadvisor.com/article/three-reasons-to-remove-attic-floor-insulation-in-a-sealed-attic
Does removing the attic floor insulation apply if my attic has Vented Soffits for the sides and a Ridge vent?
If you are continuing to vent the attic then there is no point in adding insulation at the roof level.
Well, I'm a tad bit confused - why would insulation contractors offer me to spray foam the entire attic, even after they noticed I have vented soffits at the attic floor level and a ridge vent in the same space? Do they mean spray foam everything - including the ridge vent and soffit area?
Should I just blow in some insulation over the HVAC ducts / the rest of the attic to get R-49+ and just be done with it?
Yes. The spray foam seals the existing vents. It covers from the top plate to the roof peak.
Ah, that makes sense. I bet if I do that, it would solve numerous temperature problems and prolong the life of my HVAC equipment.
NO location in WV is in IECC climate zone 6B- it's either 5A or 4A, and it makes a difference. Find yourself on this map, then report back:
https://s3.amazonaws.com/greenbuildingadvisor.s3.tauntoncloud.com/app/uploads/2018/07/25030613/H-T%20Zones%20-%20legend-700x928.jpg
The IRC 2021 code minimum for both zones 4A & 5A is now R60 (up from R49 in recent prior versions- either R30 or R38 back when the house was built, depending on your actual zone). See Table N1102.1.3:
https://codes.iccsafe.org/content/IRC2021P1/chapter-11-re-energy-efficiency#IRC2021P1_Pt04_Ch11_SecN1102
But putting the air handler ABOVE the R60 would be silly.
Bringing it to R60 with closed cell foam would be both expensive and counterproductive, given the higher environment cost of closed cell foam (even HFO blown closed cell foam.) Given the R30 on the attic floor I suspect you're in zone 4A. Sealing the roof & gable ends with an all-foam R30 would already be more than what makes financial or lifecycle carbon sense. But R18-R24 (3-4" of foam) plus R30 of fiber (or 6-8
half-pound open cell foam applied directly to the closed cell) can still work safely in zone 4A.
In most cases you can also safely keep the R30 on the attic floor, but any floor-R would not count toward code compliance. (R30 on the roof + R30 on the floor does not equal R60- only the roof-R would count.)
The first and most important thing is to get the air handler & ducts fully inside the pressure envelope of the house- which means air-sealing the attic from the outdoors. That's followed by bringing it all inside the thermal boundary (insulation) of the house. Sealing & insulating the underside of the roof deck and the gables with closed cell foam to air seal it might be "worth it", but not the attic floor.
The R-amount of closed cell foam then constrains you as to how much cheap fiber insulation could be added to the interior side of the foam to pad out the total R without running into moisture problems, but it's not going to be financially rationale to hit the current code. The optimal R-value ratio of foam/fiber or foam/total that works is very much climate dependent- you can get away with a heluva lot less foam in zone 4A than in 5A, but in no way should you be treating it as zone 6B.
How deep are the rafters?(or are they trusses?)
How about the stud depth on the gable ends?
I do apologize, being a turfgrass biologist, we use the USDA Plant Hardiness Zone Map so I ended not thinking that's what was asked. (sorry for the confusion).
I'm in zone 4A, according to that map.
I attached 2 images of the attic, as it's very hot up there I'll have to wait until it cools down until I can take some measurements. (i took it from looking up from the hatch)
Deleted
Image #1 is the rafter depth:
Image #2 stud depth on the gable end:
Image #3 is the view facing south:
Image #4 is the view facing north: