How To Detail a Rainscreen

Hello all,
First, here are my details…
1) Prosoco fast flash & cat 5 liquid applied WRB
2) 2″ mineral wool
3) 3/4″ furring (1×4’s)
4) hardie lap siding
This project has been coming along on my house. I’m just this weekend going to apply the cat 5 membrane after temporarily self-supporting the deck to remove the old ledger board so that I can flash it properly.
I’m trying to look two steps ahead but it’s difficult. I’m a handy guy but I have no experience with these details aside from my numerous hours of research and reading.
My biggest complaint about most articles are the lack of calling out specific products. For example, although I see articles about rain screen all over the place and schematics/details on the final assembly, I have yet to find someone point to a specific product and step by step assembly of the bottom wall detail.
My questions…
1) Can someone point to an article or video (ideally) of a rain screen assembly being put together? I only ever see someone show the end but because there are many methods to handle this, I’m curious to see the full process.
2) See pic #2 – Which is best and can someone advise…
sometimes the rain screen assemblies show the mineral wool receiving a perforated J channel by itself…
or J channel that cups both wool + furring strip…
or stapled insect screen to sheathing around wool + furring strip…
or both or cor-a-vent…
or insect screen + cor-a-vent…
There seems to be no standard so someone like me who has one shot and doesn’t have multiple experiences to draw on, which is best? I’m in an with rodents, ants, wasps, with lots of winter snow. Planning to have mineral wool against exterior foundation wall if this matters.
3) What about top rain screen assembly? Does anyone have an article or video showing the process and not just the finished product?
Thanks!
Zach
GBA Detail Library
A collection of one thousand construction details organized by climate and house part
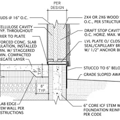
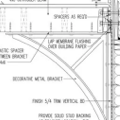
Replies
Mountaincabin,
We are in a time of intense change in the building community. The standard detailing that was used for decades doesn't work with high-performance assemblies. So right now there is a lot of experimentation going on, and an unsustainable amount of variation in how houses are built. Over time the details that work, both practically and economically will prevail, and one or two assemblies suitable for each climate zone will dominate. In the meantime I agree: It's hard to know what works best.
For your situation here is what I would suggest:
- Apply your WRB and flashing.
- Get a perforated metal base-flashing wide enough to cover both the mineral wool and furring. (Commonly called a J, but more accurately it should be a U with one leg extended enough to fasten to the wall.) This will stop all pests except the smallest ants and bugs which will find another way into the cavity anyway. The big advantage of the metal flashing is resilience against mechanical damage over time.
- Set the mineral wool into the base-flashing and tack with cap nails.
- Screw the furring though to the studs to form the cavity.
- Apply the siding according to the manufacturer's installation instructions. Remember that horizontal flashings for trim like belly-bands, or changes in cladding, sit on top of the furring.
- Do not vent the top of the rain-screen. You get the vast majority of the benefits from one with just a bottom opening.
Here is picture showing a perforated metal base-flashing, with the furring sitting in it (but not mineral wool batts):
Malcolm,
Don't vent the top?! This is the first I've heard of only creating an opening on the bottom but not the top. This would drastically reduce effort of the rainscreen detail based on your recommendation. Any further explanation of why not to vent top besides your short answer? When does venting the top matter, or does it not really in any environment/climate zone (I'm zone 5B).
I see some people say to make this metal J stainless, is this also your recommendation? Where would I go about finding this?
What about furring strips? I plan on using 1x4's but I see so much on material type. One contractor friends recommends pressure treated not necessarily due to resilience against water but because it won't so easily split as compared to other 1x4's like pine or fur.
Thanks,
Zach
Zach,
Rain-screens are mandated in our code, but aren't required to be vented at the top, and in general, top-vented ones are the outliers, not the norm.
The main functions of a rain-screen are:
-Providing a capillary break.
-Allowing the redistribution of moisture in materials.
- Providing a drainage plane for bulk-water intrusions.
- Ventilating the gap.
You get three out of four without venting the top. Is venting the top better? Maybe, but we know they work perfectly well without it.
My local lumberyard will custom bend perforated stock to any shape. There are suppliers like
https://www.menzies-metal.com/?post_type=product&product_cat=&s=rainscreen
I don't know if they only sell standard sizes, or will do custom orders. Any sheet metal supplier should be able to make them up.
Again because every house here has a rain-screen, our lumberyards stock 2" plywood strips in 5/8" and 3/4". Everyone uses them, but if they weren't available I don't think it would be worth ripping them yourself. Sorry I don't know much about which wood species makes the best furring having done very few walls with exterior insulation.
Coravent works well !
Zach, I'm surprised to hear Malcolm suggest venting at the top isn't necessary. I would think that not having it would interrupt the stack effect that you're looking for behind the siding material. Maybe he'll come back and elaborate on his reasons for this.
I would echo his thoughts regarding the current status of 'green' building techniques, adding that the variety of possible solutions does complicate things for those trying to replicate such projects. It's not always clear-cut on the best way to proceed, especially when it comes to the finer details.
On our project, we mostly copied Hammer and Hand details for our wall assembly, including the rainscreen set-up: https://hammerandhand.com/best-practices/manual/4-rain-screens/4-6-horizontal-rain-screen-battens-vertical-siding/
Steve Baczek had a slightly different idea for this area, with the Cor-A-Vent installed between the top of the siding and the frieze board (if my memory is correct). I did a quick online search, but I couldn't find the detail. I'm pretty sure it showed up here on GBA or in Fine Homebuilding magazine.
Although we haven't had any issues (I keep looking), with our assembly insects could (at least in theory) set-up a nest on the blocking behind our frieze board. With the Baczek detail you completely deny insects any entry point to this top of the wall area. Either way, there should be ample air flow behind the siding.
On our blog I note the details, including the products we used, of our rainscreen assembly:
https://kimchiandkraut.net/2019/07/11/siding-1-of-2-continuous-insulation-with-a-rainscreen/
https://kimchiandkraut.net/2019/09/21/siding-part-2-charred-cedar-shou-sugi-ban/
It's also worth doing a mock wall assembly, including all the components that will be involved, so you can work through any trouble spots before doing it for real on the job site. I realize you're far along in your project, but it still may be worth doing --- it could save you a lot of headaches later.
In addition to their Best Practices Manual, you may find the Hammer and Hand collection of YouTube videos helpful as well: https://youtu.be/2452EmtQhys
Hey Eric, thanks for your details here. I've come across your site before and but go through in more detail now. Questions:
1) what type of furring strip do you use? size, wood? People say pressure treated so it doesn't split or others say pine. Thoughts? Plywood seems like it would be too wavy but wouldn't probably split.
2) now i'm not sure what to do in regards of top venting of rain screen. I have looked over hammer and hand before in detail. One thing they don't detail is an assembly over mineral wool. I'm doing 2" and had questions if i had to use cor-a-vent product, how to attach it. Looks like you used long nails. Gunned or hand driven? I was planning to not use cor-a-vent and have perforated J flashing bent and have the furring strips go to the base all the way.
3) for gable ends, how do i take care of venting? I am also running a continuous vent on the sides but not sure how to do gable ends. This also has to do with stack effect but unsure if i run a continuous vent how it would vent outside wall assembly once hot air gets to top, thoughts? (see pic)
We used 2x4's on our house for our first layer of furring strips (vertical). The siding guys said the 2x4's were easier to work with in order to avoid compressing the Rockwool.
The second layer of furring strips (horizontal) were 1x4's. We chose 1x4's over 1x3's for the second layer because I had read (probably here on GBA) that splitting can be an issue with 1x3's.
I've consistently read (again, here on GBA and elsewhere) that pressure treated wood isn't typically necessary since the furring strips are unlikely to get and stay wet for very long (oceanfront exposure, or extensive annual rainfall may be the exception to the rule). Plywood, I would think, would be a pain to cut into the strips required for furring, although I think Malcolm mentioned a while back that in his area it's common to see plywood pre-cut in local lumberyards for this very purpose.
I would include ventilation at the top of the wall, but I'm only basing this on what I've read and our direct experience with our house. For little more in time and materials it seems to me that you can maximize the ability of the ventilated rainscreen assembly to dry out your cladding.
The siding guys attached the cor-a-vent with a nail gun, sizing the nails so they were just long enough to get through the Rockwool and bite into the sheathing. The cor-a-vent also ended up being squeezed to the Rockwool and the sheathing by the second layer of 1x4 furring strips, which does help.
Metal screening should work just as well as the cor-a-vent (the Maibec products look really nice), but, again, this is an example where doing a mock wall assembly could help you solve these kinds of issues before you buy all of the individual components and start installing them on your house. It wouldn't cost much, or take a lot of time to make. Even one that was 6' wide and 4' tall with a window opening would allow you to install all of the individual elements and help you figure out sequencing.
You can also see if compressing the Rockwool will be a problem for you (we used FastenMaster Headlok screws, but Heco-Topix are said to work even better in this regard: https://youtu.be/JocIoRFw-h4 ).
The mock wall assembly will also give you a chance to work through all of the air sealing, insulation, and flashing details, particularly for around windows and doors.
Ventilated rainscreen details for the gable ends are basically the same as the rest of the house, you're just following the angle of the roof. I'll attach a couple of pictures from our project showing a gable end before blocking/frieze board are installed and after.
Eric,
Thanks for your thoughtful response. Based on your opinion, I'm actually going to be using 2x4's for the furring strips instead of 1x4's. Luckily I had enough wall depth to do this.
Questions:
1) how did you attach your mineral wool to the foundation? I see rodenhouse has plastic fasteners that you drill into foundation wall and secure in place with compression. It looks like this is what you did, would you recommend this or another method?
2) how did you attach your metal that surrounds your mineral wool and foundation so that it doesn't bow out? Is this just held in place by the backfill or did you do some sort of mechanical fastening? (see attached photo for reference of my wall assembly with metal skirt and hardie siding.
3) any recommendations on how I attach my deck ledger board and awning ledger board to the wall while accommodating the exterior insulation? I was looking at the maine deck bracket for the deck but I don't think it'll work for the awning since there's only studs and not a continuous 2x6 to tie into.
I would definitely recommend using the PMF fasteners from Rodenhouse. With a decent hammer drill and the proper drill bit, once you've established a hole through the rockwool and into the concrete foundation it's easy to gently hammer the plastic fasteners into place.
For the metal flashing that covers the rockwool on our foundation we just had the siding guys treat it like a traditional Z-flashing, only they just carried it down over the face of the insulation on the foundation --- about 4" lower than where we knew the level of our gravel border would end up. In other words, if you were to pull back the gravel in the border a few inches you would see where the metal flashing terminates on the face of the rockwool.
To keep the metal flashing pieces together as each piece overlapped the next (the black metal flashing was coil stock on rolls that were 2' wide) we used a simple pop rivet gun to keep the vertical seams together (https://youtu.be/WPwNsQMnx88).
So far, it's all staying together nicely, apart from one seam that needed a little sealant to close an unsightly gap that developed over time. The gravel border also adds some weight up against the flashing to help keep it in place and tight against the Rockwool. It's not perfect, but it does the job.
If you don't have a roofer or siding company who can bend the flashing for you, and if your dimensions are consistent around the perimeter of your house, you might be able to order the Z-flashing pre-made and shipped to you by a company like this one: http://www.trimbender.com/z-flashing
This article by Mike Guertin details the 'how-to' for using different products with continuous exterior insulation to install a deck ledger:
https://www.deckmagazine.com/design-construction/framing/installing-deck-ledgers-over-exterior-insulation_o
For establishing a ledger for your awning while avoiding thermal bridging, someone here on GBA might offer a solution, or you might want to consult with a structural engineer to see what your options are. My guess is you might have to open up drywall on the interior to add blocking between the studs that your Maine Deck Bracket can bolt/screw into, but maybe there's a more straightforward (and more structurally sound) solution.
You might find this video helpful regarding ledger install details/options: https://youtu.be/5HaYmbXASCs
Hi again Eric,
Had a couple more questions for you as I get further in my project.
How do you attach the cor-a-vent to the house and to each other? I am also needing to double up on the vent bc I also went with a 2x4 rain screen on top of my 2” mineral wool.
Thanks!
Hi Zach,
The cor-a-vent was attached with nails that were just long enough to bite into the Zip sheathing. Individual pieces were installed tightly together next to one another (basically a friction fit).
We also combined the cor-a-vent with window screening in a 'belt and suspenders' approach. It didn't seem like either one on its own would completely deny insects entry behind or under the siding.
Having said that, there are plenty of projects that use only the screening or only the cor-a-vent. Since it was my home I was willing to pay a little more in terms of labor/materials to double up the protection.
Maibec sells specialized ventilated strips just for that purpose but don't know how easy they are to get in the US (https://www.maibec.com/en/resistech/products).
The past 10 years I've just folded SS or aluminum bug screen up onto the furring strips (I use 3/4" ply as it's actually cheaper than pine if you rip 4x8' sheets into 4" pieces). Screen needs to be about 16" wide as I like it to end high behind the siding. I start by tacking it onto the sheathing above the bottom flashing before I put up the exterior insulation but after the flashing pan. I have some nice HVAC guys bend my flashing stock as I put 4-6" of exterior insulation on. I allow a 2" bend against the sheathing for nailing, then whatever width for insulation with a return down angled drip flange. The section under the insulation is ever so slightly angled down for runoff and allows air to get under the insulation and up through the bug screen. Close enough to 90 so I can just lay the insulation on before fastening. I'll try to find a photo.