Condensation Risk With Split-Wall Assembly

Hi all,
Am very grateful for this website and all the great information. Just hoping to get some feedback on the plan we have for insulation. We are in climate zone 6 and retrofitting an existing house using passive house principles.
Our plan for insulation is as follows:
-Above grade walls will be 9 inches (R-37+) of Comfortboard 80 on the exterior (strapped and fastened with long stainless steel screws) and comfortbatts in the 2 x6 stud wall (r-22; total nominal R-value of 49).
-Below grade – 2 x8 framing set 1-2 inches away from concrete foundation with ccSPF of 8 inches (R-48)
-Roof will be same as the walls with 9 inches of Comfortboard exterior and then R-22 batts in the rafters (total R-value of 49).
We will be doing unvented roof assemblies and bringing the attics into the conditioned space as one of our ceilings is cathedral. Also the entire house, including up over the roof will be air sealed with a WRB/air membrane. The exact membrane is still to be determined, so we’re open to recommendations.
Anyone have concerns re condensation risk of the split-wall assembly or have any suggestions for how we might effectively increase R-value without dramatically increasing cost?
Thanks in advance,
Jackie
GBA Detail Library
A collection of one thousand construction details organized by climate and house part
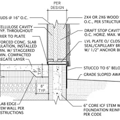
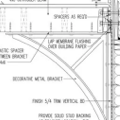
Replies
9" of exterior rigid insulation is going to be very challenging to work with. I think you'd be better off with a double stud wall here an dense pack cellulose instead -- it will probably be cheaper to build, and it will certainly be easier to work with. Even with a retrofit, you can convert the wall to a double stud wall, and if you're plan was 9" of exterior insulation, you're going to be doing some construction work either way.
I would use rigid foam below grade instead of ccSPF. Rigid foam has the advantage of being flat here, and may well be cheaper too. I would use polyiso here. Rigid foam can be set directly against the foundation wall (assuming you don't have an irregular foundation like stone), then you can frame right over the foam. Spray foam is only really needed if you have a foundation wall with a very irregular surface.
I don't see an issue with the roof as long as you maintain the right ratios of exterior to interior insulation for your climate zone.
Bill
You could likely reduce both cost and environmental impact in the basement. 8 inches of closed cell foam will be both very expensive and unlikely to ever "pay back" it's global warming potential debt. You're already using mineral wool products extensively, why not use mineral wool boards or batts in the basement over a thinner layer of either spray foam or rigid foam boards? I believe an inch or two of foam is sufficient from a vapor control perspective, though I'm not sure if there's a ratio to consider here like there is with roofs and walls. Mineral wool would be relatively insensitive to any moisture / wetting that did occur. Or, just use multiple layers of rigid foam.
On the walls, you may need to consider some form of additional support for that much exterior rockwool -- that's a lot of weight. Check out this article for some details on the bottom edge supports for just 6" of mineral wool. On the roof, you may also need to look carefully at the structure -- older buildings can have roof structure that's already undersized by modern standards, and you'd be adding another 6psf dead load worth of fluffy rocks. Again, the article I linked provides one possible solution -- an additional structure of engineered I-joists -- but if you're going to the trouble of that, it'd be more cost effective and environmentally friendly to just do a vented assembly with dense pack cellulose.
Thanks very much for your comments. We opted not to do dense-packed cellulose in the walls simply because, to achieve our desired R-value, we would need to lose too much interior space and given that we are dealing with an existing floor plan, some rooms just didn't have the space to lose.
For the basement, I do like the idea of just doing a thinner layer of sprayfoam and then using the comfortbatts. To be honest, I had to be convinced to do sprayfoam at all because I am trying to avoid all foams in an effort to be environmentally-conscious, but it is hard to argue with below-grade performance of ccSPF in our climate - particularly given the lack of exterior insulation and our reluctance to spend the money to dig down and add it. We avoided polysio because of the degraded performance at colder temperatures - we are on the east coast of Canada so winters are long and can be cold. https://nnca.ca/sites/default/files/Optimal%20Wall%20Design%20for%20North%20Feb%2017-2016.pdf
The roof and attic have been a matter of much debate - vented/unvented, and which product. We landed on this arrangement simply because we felt it allowed us to make the exterior air barrier as continuous as possible - as we could run it directly over existing soffit and fascia and onto the roof. We have been given feedback by other passive homeowners to prioritize air tightness. While we were originally planning to do dense pack cellulose, we have concerns about the ventilation and insulation thickness at the edges of one of our roofs and our ability to achieve our desired R-value. It would certainly be more economical to take this route if we could airtight the ceiling and achieve our desired R-value. To complicate matters, one of our ceilings is cathedral with only 12-14 inches of space for insulation so we knew that we would need at least some exterior insulation for that one.
In terms of structure, two of the roofs are being replaced so trusses are new and being engineered to account for the additional load. The third roof is existing and I will certainly raise this question to our contractor. I also like the idea of creating a bit of a shelf for the insulation. Thanks for sharing the link. This study helped me feel a lot more comfortable about the screws being able to bear the load: https://www.rdh.com/wp-content/uploads/2017/11/CCBST-2017-Structural-Testing-Screws-through-Thick-Exterior-Insulation.pdf
Yeah, there's certainly a lot of options and tradeoffs (I haven't firmed up all of my design choices even as my project is already underway -_-). Some of your decisions may be influenced by materials availability, too -- I was just quoted leadtimes of over 100 days for Comfortboard 80.
Continuous exterior insulation does have advantages, and allows unvented roof assemblies, but if you're going to the expense of replacing roof structure with new trusses, that seems to me like prime opportunity to just design the trusses to allow for sufficient depth of loose fill cellulose in a vented attic. Is that an option or are you limited by other factors? With replacing roof structure entirely, you have a lot of options that less invasive retrofits don't allow (also think about things like designing trusses that provide a plenum or service cavity within the conditioned space to make air sealing easier and keep all HVAC inside the envelope).
On the walls, what Bill may have been suggesting would be to build out rather than in, but still use cellulose. You can use I-joists or field fabricated "Larsen trusses" to increase the thickness of your wall to the exterior, adding new sheathing (or I think there's ways to just use a WRB membrane by itself) and dense-pack the cavities.
Yes, there are long waits for comfortboard and other rockwool products. I spoke with them today and they told me that they are effectively sold out and building a 4th new plant that is due to open in June! Lots of people renovating at the moment. Hopefully, we will get right around the time that we need it.
Unfortunately we have three roofs that meet each other and due to space available where they meet and not wanting to decrease our roof pitch beyond 3:12, we don't have the space to design the trusses to allow for significant interior insulation (and as I mentioned, our cathedral attic space is only 12-14 inches - not enough to achieve a high r-value with cellulose alone. The one roof that we are not replacing is my biggest concern - getting good insulation at the edges - I have not been able to think of how to do that except to add exterior insulation.
Oh yes! That makes more sense. Thanks for clarifying.
Jackie,
Have you priced out the Comfortboard yet? I suspect it will be 2x to 3x more expensive than Type II EPS or Polyiso with a similar or lower R value. You need not worry about Polyiso's R value decrease with that much foam. Even if you live in Nunavut, the total R value of a 9" thick layer of Polyiso would still average out to more than R-4/inch (the R value of 4#-8# density Comfortboad.) Sure, the outer inch or so of the polyiso's R-Value may fall but the inner layers should maintain a 4+ R- Value.
Personally, I would opt for re-claimed polyiso or Type I EPS over Comfortboad. Although it is a petrol-chemical based product, Type I EPS has less embodied energy than even the lower density Mineral Wool 'boards'. If you live in Quebec, then I would load up on Sonoclimate Eco-4 boards as my exterior insulation. Regardless of what insulation you choose, I would probably opt for a self adhered WRB if you live in a place like Newfoundland or Sydney, NS where the weather/wind can be brutal.
Consider performing some simple heat loss calculations to determine how much energy you are actually saving with your walls/roof as described. Surface area will matter a lot here. If your house is 30' wide and 80' long with a 16/12 pitch, then I would want more than an R-49 Roof. That's an extreme example, but you get the idea. :-)
Thanks for this. We are definitely going to opt for a fully adhered membrane because yes, we get lots of wind! We are in PEI and up on a hill so it can blow. ;)
I checked into the Eco4 boards, but it appears they only come in 1.5 thickness. I am sure my contractor will kill me if I make him add that many layers. Love the environmental aspect though. We are also considering Gutex Multitherm. I am waiting on a price. It comes in up to 8 inches, but the water and insect properties are not as attractive as Rockwool - although it has other redeeming features.
Forgive my ignorance, but what kind of calculations would you recommend? We haven't done energy modelling.
Polyiso below grade doesn't see the outdoor temperature -- temperatures underground are warmer, so this is actually an ideal place to use polyiso since it WON'T be subjected to the very low temperatures where derating becomes an issue. I would try to use reclaimed polyiso here, since you'll be concealing it. I did the same in my own house (except it's mostly in a crawl space, so it wasn't visible for a different reason).
Even derated, polyiso will typically perform as well as EPS, and it will perform better at all times except the very coldest times. This is something to consider -- better performance over 49 of 50 days and worse performance during 1 day will likely still result in lower energy losses over the entirety of the 50 day period, for example. ccSPF doesn't really have an advantage here over any of the rigid foams, especially underground where the temperature delta will be less with comparison to what would be seen above grade on a cold winter day.
Regarding the dense pack cellulose, I was thinking of building out. you're going to be building something to handle 9" of exterior rigid foam, so why not use something like Larsen trusses and use dense pack cellulose instead? Martin wrote an article about this some time ago here:
https://www.greenbuildingadvisor.com/article/all-about-larsen-trusses
Bill
Okay. That is really good to know. Maybe I will revisit the polysio for the basement.
Believe it or not, until this point I thought that a Larsen truss would require an additional foundation to be poured, which is what was daunting to us. I think I got that wrong. My concern though is about cold sheathing and condensation risk? How does this system address that? Plus, the usual issues with dense-pack including settling, gaps and potential for mold if it were to get wet.
Jackie help me understand what parts of the original house are you saving?
My guess is you could build new and better for less money than it will cost to work around the old house and it will never be exactly what you want because you are working with the old foundation.
Walta
If I had a dollar for every time I wished I had built new instead of starting a renovation, I'd be able to afford to tear everything down and start over!
But, from an environmental perspective, what's better -- building a new structure or improving the performance of an existing structure? I don't know the answer, just something I ponder.
Walta, you are probably right! And it makes me want to both laugh and cry. :) We are saving the entire foundation and exterior wall structure (i.e. framing and sheathing) for the full 5500 sq ft house. The foundations are in great shape and dry and the foundation lay-out works for us so we went with it. Partly in the interest of attempting to reuse some of those materials and save money. We are adding a slab garage and one area of the foundation was only below grade (it was a pool in the basement) so we are adding a main floor addition to that foundation. We are also saving the roof over one part of the house. Does that clarify?