Wall Assembly to Limit Mold Risk

IECC Climate 6/7 need help with shell design
We are nearing the end of our home design and the thing we continue to get stuck on is the shell design.
Our son has been in the hospital more times than we can count due to allergic responses so building a home that avoids water damage and condensation that leads to mold is incredibly important. We know there are many ways to do this, but some materials and selection price points are well beyond what we can afford.
My question is: does anyone know of a good system that wouldn’t break the bank using materials that most contractors would be familiar with? Or maybe even a referral someone can share to contact a building science expert and help us make selections?
Currently we are considering…
1. Metal siding
2. rain screen
3. Insulation layer of either: 2” foam board, 2 layers of 1” foam board with seams taped and alternating, or comfortboard (unsure on which insulation rating is best)
4. Tyvek
5. plywood, seams taped with Siga tape
6. Framed walls with comfortboard insulation
7. membrane vapor retarder
8. drywall
9. paint
Is there a better way to do this? Anything I’m missing?
Thank you for you help. We are also working through the roof decisions but I will make that a different post and question.
GBA Detail Library
A collection of one thousand construction details organized by climate and house part
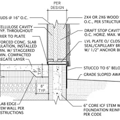
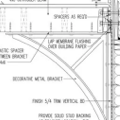
Replies
The key to avoiding mold is to understand how your building manages water and water vapor. Using mold-resistant materials is usually an ineffective bandaid approach.
In your climate zone, I would use a high-quality variable permeance membrane on the interior, vapor-open insulation (specifically, borate-treated cellulose as it keeps all microbial action at bay) and a vapor-open exterior with a robust rain screen to promote drying. Exterior foam insulation can be a good thing but it has to be thick enough to prevent condensation; 2" XPS is not enough in CZ6 or 7 unless the framed walls are 2x4.
The roof should have large overhangs to keep water away from the building; it's possible to build a durable house without overhangs but it requires specific knowledge and attention to detail, whereas overhangs are pretty simple and effective.
Make the house airtight so you infiltration through random cracks is not your source of fresh air.
High-quality triple glazed windows to minimize condensation that leads to mold.
An air source heat pumps to help keep humidity under control and provide efficient heating and cooling and to keep indoor air quality high.
An ERV with a MERV13 filter to keep outdoor pollutants to a minimum.
Build on a slab; basements tend to be damp and moldy. But make sure the siding and framing are a bare minimum of 6" above grade, and preferably 8-12".
Those are a few ideas to get you started, anyway.
Thank you Michael! This is really helpful.
For a heat pump, we had heard that they don’t work well in areas with very cold winters. Was there a certain one you know where this isn’t the case?
The interior insulation we were considering was Rockwool in 2x6 exterior walls. Would this work?
And, for the exterior insulation, are you saying we wouldn’t really need the exterior insulation? I’m wondering, if it’s just as effective, to skip it. But if we did use it, if 2” isn’t enough, what would we need and wouldn’t that stop the shell from being vapor-open? I think this piece (the exterior construction) is one of our biggest hang ups.
Also, do you have any thoughts on radiant in floor heat if we do a slab on grade? Biggest concern there is the water pipes and condensation.
Mitsubishi has mini-splits that recently operated down to -20°F here in Maine. Some systems I know of were not able to keep up, but most of those were in poorly-performing homes where the units simply had to work too hard to keep up. The two units I know of in high-performance homes that weren't able to keep up were multi-splits, with a single outdoor unit feeding multiple indoor units. That arrangement is never as efficient as having an outdoor unit for each indoor unit, and my tiny sample of anecdotal evidence indicates that there may be a low-temperature penalty as well.
With heat pumps, you aren't limited to units mounted high on the wall; there are ceiling-mount and low-wall options, there are units that can handle short sections of ductwork and others that can supply an entire house using ductwork.
This is an older but still relevant article regarding how much exterior insulation you need: https://www.greenbuildingadvisor.com/article/calculating-the-minimum-thickness-of-rigid-foam-sheathing. The short version is that your proposed insulation ratio is at moderately high risk of condensation and mold growth. If you can afford it, one easy solution is rigid wood fiber insulation. TimberHP manufactured here in Maine will be available soon, and in the meantime, Gutex and Steico are available as European imports.
In-floor heat doesn't work well in homes that have good levels of air sealing and insulation. It does provide evenly distributed heat and makes the floors slightly warmer than the air temperature, but not much, so you don't get the "warm floor" effect most of the time, response times are very slow and homes are prone to overheating. More info here: https://www.greenbuildingadvisor.com/collection/radiant-floors
It looks like your URL at bottom has doubled and is leading to a 404 error.
Thank you, fixed now.
After reading all the links and your response again, I’m wondering… is exterior insulation needed? For example, if we did all the steps I listed above, skipping the external insulation, but choosing a breathable internal insulation like cellulose, rockwool or fiberglass, with a smart membrane barrier, would I need the exterior insulation? Would the wall be able to dry inward and outward enough to not have issues with condensation?
There are many ways to build a good wall: https://www.greenbuildingadvisor.com/article/walls-that-work. Any "good wall" will be nearly immune to moisture accumulation, which is what allows mold to grow.
The system I usually use is a double stud wall: https://www.greenbuildingadvisor.com/article/a-case-for-double-stud-walls. In theory it's at some risk of moisture accumulation and mold, but Dan Kolbert, the author of the article and a friend and collaborator of mine, has never seen problems with his approach. I add a variable permeance membrane on the interior to make it even more resilient and resistant to moisture accumulation.
Another approach I like is a Larson Truss (or Swinburne Truss: https://www.greenbuildingadvisor.com/article/alaska-builder-faces-an-insulating-dilemma.) It's a way to get continuous exterior insulation without having to use foam; you can use a vapor-open product instead.
Soon to be my favorite approach, once production starts here in Maine, is exterior wood fiber insulation. Here's an article I wrote about it: https://www.greenbuildingadvisor.com/article/in-favor-of-wood-fiber-insulation, and an upcoming project with Dan Kolbert, the double-stud fan, will have exterior wood fiber insulation.
Thank you! I read through the articles and if I’m understanding them correctly, using r-24 interior insulation with a vapor smart membrane would work with the exterior 2” rockwool Comfort Board that is R-8.4.
Does this sound correct? It looks like this would meet the 35% exterior required ratio for zone 6 and still provide a vapor open assembly so things can dry inwardly and outwardly.
Before everyone starts offering product ideas, what specifically is your son allergic to? If it's mold then moisture is the primary thing to avoid, if it's VOC's then certain types of foams, solvents and glues are the problem.
For healthy indoor air, what are you planning on doing for dehumidification and fresh air? An ERV or an HRV? Some ERV's and HRV's offer dehumidifying within the unit but a stand alone dehumidifier may be a better choice.
Thank you for asking, he’s allergic to environmental things like mold, pollens, dust, ect. We do try to keep our toxins low just because his body is already on overdrive but yes, moisture is the number one issue.
We were planning to do an ERV but hoping to find one that did not include dehumidifying as we would probably get specific units for that we’re thinking.
No conventional ERVs provide dehumidification. They maintain the interior humidity levels better than other systems; in cold weather, they keep more humidity in the house than an HRV or exhaust fan, and when you're running air conditioning or a dehumidifier in warm weather, an ERV keeps the interior drier than an HRV or exhaust fan would.
There are specialized units that do more than that; you might look into a CERV or Minotair unit to combine ventilation with humidity control. But a plain old ERV will work fine if you have another source for humidity control.
Mr. Maines, Please tell me what the C in CERV stands for. I've googled and failed to see any explanation. This is the first time I've heard of it. Thanks.
I found on my house in zone 5, that two layers of 1-1/2" rigid insulation had advantages; it exceeded code minimum, it greatly reduced any chance of condensation on the interior of the sheathing ever, it allowed construction to continue into winter without needing the stud cavity filled, one layer can be replaced with 2x framing for detailing purposes, and the labor for 2 layers of 1-1/2 is the same as 2 layers of thinner insulation.