Uninsulated studs = cold sink = much worse R-value?

This is in Minnesota.
When insulating a 2×6 stud wall (16″oc) [with closed-cell spray foam], they will fill to about 3″ thick leaving about 2.5″ of air (photo below). One concern I have is that this also leaves 2.5″ of the side of each stud exposed.
One thought is that this reduces the r-value of the stud simply based on thickness so from an r-value standpoint we now have a 3″ stud (r=3.6) rather than 5.5″ (r=6) for the approx 30% of the wall that is framing.
A bigger concern is that the sides of these studs are now effectively cold sinks. Just as a heat sink sticking out of something transfers heat from inside to outside, it seems the sides of these studs would do the same and transfer heat from the air cavity between the spray foam and the sheetrock and thus massively reduce the whole wall r-value. Doing some very rough calcs I get a reduction from r=11 whole wall to r=7 whole wall.
Is there any truth to this? Any idea how much of an impact? Enough that it’d be worth it to make sure they also build up an inch or so on the sides of the studs?
(It’s a long and irritating story why we have standard stick framing rather than double-stud or exterior foam).
Thanks
GBA Detail Library
A collection of one thousand construction details organized by climate and house part
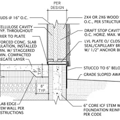
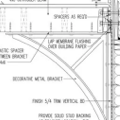
Replies
I’m going to assume that’s closed cell spray foam, so 3” of that at about R6/inch and a 30% framing fraction gives you about R 13.5 whole-wall performance. Using the more common 25% framing fraction gives about R 14.25 whole-wall performance. Thermal energy going through the wall still has to pass through the 3” of wood stud that is embedded within the foam, so it’s the cross sectional area of the enclosed part of the stud and foam itself that matters (think two dimensionally here). I think the additional exposed area of the stud beyond only the narrow face probably does act a bit like a collector fin, but I doubt it contributes to very much additional energy loss. There might be an issue with condensation in extreme conditions though. I like to have the installers flash the exposed sides of framing members like this with at least 1/2” or so of foam as extra insurance. Doing this does usually require a bit of trimming before drywall can go up though.
Bill
Thanks Bill. Yes, it's closed cell, should have mentioned that.
After it's done I'm tempted to stick a thermopen through in some inconspicuous places on some really cold days to see what the temp in the air pocket is.
Agree about the condensation potential. Does the 1/2" seem to fix it for you? That's effectively the stud becoming a cold sink I think.
A somewhat related problem that has cropped up in houses here the past few years is frost on interior of the sheetrock where there is a small gap between adjacent framing members (photo). This seems to be limited to about -15°f or below. They should probably be using something between them during framing as I think shooting something in later does not seem to be working. Exterior foam would fix this too.
The stub is a bit a of a heat sink fin, but the solution is to fill in the rest of the cavity with fiber insulation.
Exterior foam can do a lot, but it’s difficult to add as a retrofit after construction. Sill sealer gasket material would probably work in that gap you showed, but regular caulk should help too. The frost is probably from an air leak, so if you fill the gap enough to make a good air seal the problem will probably go away.
I agree with Dana too, adding “regular” insulation to the cavity will cover those studs, add some R value, and stop convective air movement in the gap. One simple solution to all three problems. In your case, I’d try the mineral wool “safe’n’sound” insulation because it’s a little thinner (3” instead of 3.5”), so it’s closer to your 2.5” gap. While this material isn’t rated for R value, that info is available from the manufacturer if you need it for approval. You could probably compress it to fit in the gap, although R11 fiberglass might be easier to squish.
Bill
Looks like thermal bridging is the name of the game.
https://www.greenbuildingadvisor.com/article/what-is-thermal-bridging
https://www.greenbuildingadvisor.com/article/the-thermal-bridge-to-nowhere
W. Ramsay,
I advise you to read this article on the topic: "Installing Closed-Cell Spray Foam Between Studs is a Waste."
Yes, you do get somewhat different R values when you do the proper 3D analysis (vs parallel-path approximation). Large differences where steel or concrete are involved.
Consider putting some rigid foam between studs and drywall and using just enough between-studs spray foam to air seal (or none). Fill any remaining space with fiberglass or damp spray cellulose.
Thanks Martin (and all). I'm wondering if the penalty is much greater than your calcs though. If the sides of the studs are indeed acting as cold sinks then that will have a much greater negative reduction in whole wall r-value than simply reducing the stud depth with parallel-path? With that much extra cold surface are you effectively changing the percentage of the whole wall that is stud to something on the order of 50-60%?
BTW, we'd originally planned on exterior foam but midway through our architect, after previously agreeing, got cold feet with it and refused to do it. We looked at switching architects (to Racheal Wagner who was already acting as our energy architect) but the costs in money, time and stress would have been considerable.
You’d probably need to do lab setup to really accurately measure the amount of additional thermal losses from the exposed studs. Since your wall is already built that way, there isn’t much point in making the measurements — you really just need to deal with the problem. The easiest solution is to compress some batts in the gaps. You might be able to blow some cellulose into the void too.
Martin is right that spray foam in walls isn’t really cost effective. You would have gotten more bang for the buck using batts or cellulose in the walls and putting the savings towards exterior foam. I only ever spray foamed a wall one time, and the spray foam crew was already onsite doing the roof so it was cost effective to add a small portion of wall to the job. Since your wall is already built though, don’t worry about it. You’ll have excellent air sealing with the spray foam, and you can fill the empty space in the walls with inexpensive insulation.
Bill
I'm quite surprised that there are apparently no studies of this or solid knowledge. This seems like it could be a very significant reduction in R-value for walls that use closed cell yet it seems a total unknown?
Thermal bridging from studs reduces the effective whole-wall R value for any type of wall cavity insulation, not just spray foam. It’s a fairly well understood phenomenon, and is probably the biggest reason for using exterior rigid foam. Double stud walls also have thermal breaks.
Allison Bailes has a fairly detailed article about modeling stud thermal bridging. You can read his article here: https://www.energyvanguard.com/blog/77664/The-Layers-and-Pathways-of-Heat-Flow-in-Buildings
Bill
Thanks Bill, great article. It doesn't really address the cold sink issue from my OP though?
In this case the path would be through the sheetrock in to the air gap between the sheetrock and spray foam then in to the side of the stud, through the stud, sheathing, & siding. In effect rather than 2" of stud in the framing factor calculation you may have 6" (exposed surface area of stud) per 16" of wall.
This is the opposite of how an aluminum heatsink for electronic components (or various other items that need to be cooled) works. Aluminum is a very good transmitter of heat so with a heatsink what you need is a lot of surface area in a space cooler than the item you're trying to cool. Very roughly, if you double the size of a fin surface area you get about 78% more cooling (there is always some loss in transmission through the fin).
Aluminum heatsinks can similarly be used to warm very cold items - (such as a pipe of NO2 ?). When you attach an aluminum heatsink to this pipe the air around the heatsink becomes quite cold because the heat in that air is being transferred to the heatsink and in turn to the colder pipe. This would be similar to what is happening with a stud acting as a fin with 2 or 3" exposed in to the air cavity - it will, potentially, transfer heat from that air cavity to outside. The question perhaps is how much heat will it transfer? Enough to be concerned about?
Also, does spray foam perform less well when colder? Assuming outside is -10°f, If the air in the gap between the sheetrock and spray foam is 40°f (cooled by exposed sides of studs transferring heat from the cavity to outside) will this lessen the effective r-value of the spray foam vs if the air in the cavity is 68°f?
I see the concern about the stud acting as a connecting pathway between the interior and exterior surfaces with the interior surface acting as a sort of cold sink. I’m very familiar with heatsinks and heat spreaders as I’m an EE with a background in RF design. High power RF amplifiers use components with a very high thermal density (hundred+ watts per square cm), so we’d use copper heat spreaders sandwiched to aluminum heatsinks.
I haven’t seen anyone model or measure that particular thermal pathway. Allison’s article is the most detailed I’ve seen. My suspicion is that the additional energy loss from the drywall acting as a cold sink is negligeable, but I haven’t seen any actual measurements. The usual ways to provide a thermal break (exterior rigid foam or double stud wall) will stop this effect though.
Regarding close cell spray foam having reduced insulating value in low temperatures, I don’t think ccSPF has this property. As far as I know, polyiso is the only common insulating material that shows reduced R values in cold temperatures, and that is due to the blowing agents condensing in the cells within the foam. Dow Thermax doesn’t have this issue, and neither does very old polyiso, so it’s not the polyiso itself that is the problem, just the blowing agents used.
Bill
Thanks Bill. My concern is the sides of the studs acting as cold sinks, not the drywall. Even so your same thought that it may not be enough to worry about may apply.
When I look at those exposed studs though I'm having difficulty getting beyond my thoughts that they'll be sucking a good chunk of heat out of our house. Possibly a total irrational thought :-)
You can always fill any empty space with batts or blown-in insulation, either of which would serve to insulate the sides of those studs. Another possibility (one that I’ve used in the past), is to have the spray foam installed flash the exposed sides of the studs with maybe 1/2” or so of spray foam. You’d need to trim a bit to get a flat surface for the drywall if you go this route. Spray foam never goes entirely where you want it during installation...
Bill
Thanks Bill, these are my thoughts as well. Just trying to decide if they are worth the extra cost. Our builder much prefers to use closed cell and what he's bid is the standard 3" of closed cell that most upper end builders in MN have been doing. I'm waiting to hear back on any additional costs for flashing the sides of the studs or for going with thinner closed and then filling out with open.
And then to determine if it's worth it.
This is not exactly to the question but I did a wall check with my very inexpensive infrared thermometer. Outside in Minneapolis is 15.4F. Indoor air is 70F, drywall temp on the outside wall between studs is about 67F. The coldest spot I could find was a top plate at 63F. 1978 thermopane window with storm, 55F. This house is a 2 x4 wall with 1" of Dow Styrofoam for exterior sheathing built in 1978. This says to me the 1" of rigid foam has provided a fairly decent thermal break.
The wall system, 1/2" drywall, 4 mil polyethylene, R-11 fiberglass and 1" R-5 rigid does not comport with current thinking for cold climate walls. However, I have been inside these walls and they look like the day they were built, pristine. This R-16 (center of cavity) wall along with beefed up attic insulation (R-100), R-10 interior foundation insulation and rim joist air sealing performs very well. The tested ACH50 is 3 so it does have some air leakage but the house performs at about 2.3 Btu/sf/hdd, using about twice the energy for heating as my R-50 double wall homes that are more than twice as airtight.
Doug, interesting. Any idea what ACH50 for your house is? From my (very limited) understanding, with that wall you should have a dew point in the middle of your wall producing condensation problems. If so then your wall must be drying to the outside quite effectively?
When our architect started balking at the exterior insulation we brought up the thought of just doing around 1" and IIRC our energy architect said that if we did anything on the outside we needed to do at least 4" to avoid the condensation problem.
W Ramsay; ACH50 is 3 for this house and I do believe 1" of rigid foam does have drying potential if not poly faced. If ACH50 is 3 there is probably some drying inward as well. The walls mainly lie in the neutral pressure plane for this house so air movement may not be as great as 3 ACH50 would indicate.
I am not advocating this wall type in Minneapolis as energy modeling for this climate does call for much more exterior foam to keep the dewpoint out of the wall cavity. It has worked here however, the winter indoor humidity level right now is less than 25%. There is also some wall cavity moisture diffusion that can occur from cavity to cavity, through top and bottom plates. It would not cover major air leaks or bulk water intrusion but could keep humidity levels in the wall system somewhat consistent.
The goal for any wall system is to keep air movement through the assembly at a minimum to avoid R-value degradation. I suspect the 4 mil poly on the inside and the 1" rigid insulation on the outside is doing just that.
It's been a while since I've fired up Therm, but this would be fairly easy to simulate right? https://windows.lbl.gov/software/therm
Just model and compare these cases:
- 5.5" stud with 3" sprayfoam (the potential heat sink situation)
- 3" stud with 3" sprayfoam (this removes both the heat sink, and also the small amount of R-value contributed by the airspace)
5.5" stud with 3" spray foam + 2.5" fluff (aka "flash and batt")
I'm not sure Therm knows to think about the cold sink element? I think it is a parallel path analysis only?
There are both 2D and 3D versions of THERM, both of which use finite element analysis
not simple-arithmetic parallel path, and newer versions even factor in surface emissivity. But in the case of a flat studwall it's really academic- the difference in whole wall performance modeled 3D THERM is and a simple parallel path is less than 10%. To paraphrase from a '90s era campaign mantra:
"It's the thermal bridging, stupid!"
With 3" of closed cell foam in a 5.5" deep studs there is no excuse for leaving the remaining 2.5" unfilled. Any fiber will do. Filling the 2.5" with cheap fiber insulation will cut the center-cavity heat transfer by about a third, and will cut the framing fraction heat transfer by nearly half. With something like 2/3 of the total R on the exterior of the fiber insulation there is effectively zero risk in any US climate zone of wintertime moisture accumulation inside the wall cavity, even without using vapor retarders.
Thanks.
Well, one excuse is cost. :-)
It sounds like in our case the insulator will try to hit the sides with closed cell as best he can without having to do a lot of trimming. To do 1/2" on all stud sides was $7k extra. He was supposed to have provided cost estimates for; 1) filling out with open cell, 2) reducing closed to 1" and filling out with open, and 3) filling out with fiber but has not yet provided those costs.
Cost is the excuse for not filling the cavity?
That's a pathetic excuse! First consider the ridiculously high cost (environmental and financial) of the 3" of closed cell foam!
Consider that 2" of closed cell with the other 3.5" filled with R15 batts would be just as air tight, cheaper, and higher performance. With R12-R14 foam on the exterior of R15 fiber there is effectively zero chance of condensation accumulating at the foam/fiber interface, the center cavity R would be R27 or higher, and the thermal bridging lower.
Some interesting data points. The EU spec for CO2 (2014 code) is no more than 350-500 ppm above outside background levels (assumed to be between 250-350 ppm) and never greater than 1000 ppm at any time. Sweden and others state 350 ppm above outside. These requirements are expected to be tightened up in the next 2 years.
Mechanical Air exchange rates for most countries in Europe are .35 l/s/m2 - .49 l/s/m2 which I think is 2-3 times our current U.S. rate. Many also include a provision that air may not pass from a more polluted space to a less polluted space so they require some specific continuous exhaust from bathrooms, wc's, kitchens, laundries, and mechanical rooms. All ventilation may be turned off when windows are open. Some are now requiring CO2 detectors and demand ventilation capability of 2-4x standard rates to insure levels remain below 1000 ppm at all times.
There are also a variety of requirements for maximum VOC levels, particularly CO, NO2, Formaldehyde, Benzene and Trichloroethylene.
U.S. OSHA states:
250-350 ppm: background (normal) outdoor air level
350-1,000 ppm: typical level found in occupied spaces with good air exchange
1,000-2,000 ppm: level associated with complaints of drowsiness and poor air
2,000-5,000 ppm: level associated with headaches, sleepiness, and stagnant, stale, stuffy air; poor concentration, loss of attention, increased heart rate and slight nausea may also be present.
I think CO2 background levels now are a bit over 400 ppm. Once you get over 1000, you supposedly get stupider.
Actually, based on a couple of studies, once you get over 500 ppm you get stupider. :-)
@Dana, I agree ("Consider that 2" of closed cell with the other 3.5" filled with R15 batts would be just as air tight, cheaper, and higher performance." I can't seem to reply directly to your post).
I'm still waiting on the costs to come back from the insulation guy. Then we'll see how much of an excuse it is. :-)
I do wonder if a 2x6 wall w/ 3.5" closed cell and exposed sides of studs would actually be a lower overall r-value than a 2x4 wall with the same 3.5" of closed cell. Those 2x6's sticking out beyond the 3.5" of closed cell are acting like radiator fins that are sucking heat out at a far greater rate than the 2x4 studs that are only exposed on one face. The question is how much?
Thanks,
>"I do wonder if a 2x6 wall w/ 3.5" closed cell and exposed sides of studs would actually be a lower overall r-value than a 2x4 wall with the same 3.5" of closed cell. Those 2x6's sticking out beyond the 3.5" of closed cell are acting like radiator fins that are sucking heat out at a far greater rate than the 2x4 studs that are only exposed on one face. The question is how much?"
The additional air films in that 2" deep cavity would most likely more than counteract the heat sink effect of the 2" of stud exposure, making the 2x6 wall with 3.5" of foam plus the still -air cavity slightly higher performance than a 2x4 wall with just the 3.5" of foam.
A still air film next to a vertical plane is good for R0.68, and with a 2" cavity with a miniscule temperature difference between the surface of the foam and the surface of the wallboard there isn't much of a convective drive- you can count on two of them, for a total of about R1.35 or so. The first inch of exposed stud is worth a comparable amount, more when counting the R0.68 air film next to the stud.
While there is a bit of convection drive due to the temperature difference of the stud, it's still less than what's normally seen for convective drive on the conditioned space side of the wallboard, where the R value of the air film is nominally modeled at R0.68.
Having been through this, I guarantee the most cost effective ccSPF option will be to dropping to 2" closed cell and filling the rest with R15 fiber.
If you are only doing walls, open cell foam makes more sense. Closed cell only makes sense for roofs. Air sealing will be just as good. 5.5" of the product linked below will get you a bit below 5 perm. I forget the perm thresholds, but depending on climate you may need an interior vapor barrier.
https://www.demilec.com/documents/Tech-Library/Agribalance/Update/Agribalance-TDS.PDF
Beyond the thermal bridging, the open bay will have convection loops, further increasing the heat transfer. This will be a much bigger deal than the "radiator fin".
With spray foam, you still need to plan on caulking or using single part foam to get all the little gaps they can't spray.
>"Beyond the thermal bridging, the open bay will have convection loops, further increasing the heat transfer. This will be a much bigger deal than the "radiator fin"."
That would be true if the surface of the foam was a lot colder than the wallboard, but it isn't. It's not the same as having cold sheathing on one side, warm wallboard on the other. The temperature of the wallboard will be very close to the temperature of the foam, and the temperature of the exposed side of the stud only a very few degrees cooler. There isn't much convective drive here until it's getting close to absolute zero outdoors.
Thanks Matt. Would convection loops still be a problem in a closed wall cavity? Each cavity is bounded by a studs, top & bottom plate, sheathing+foam, and sheetrock?
"With spray foam, you still need to plan on caulking or using single part foam to get all the little gaps they can't spray."
Yep. Even so a lot of builders in the upper midwest have been having problems with frost lines on the interior of sheetrock. What they're finding is that nothing seems to expand with the gap enough to keep them sealed. The insulation guy on our project recommended some 3M tape over these to fix the problem but I'm not sure if that will fix it or not as it seems the cold would still penetrate the relatively thin tape.
External foam would solve this too... But unfortunately we're not doing external foam.
Convection requires a temperature difference. Convection big enough to overcome the insulating properties of the adjacent air films requires a substantial temperature difference.
With as little as R5 of closed cell foam between the cold sheathing and the cavity air the temperature difference between the warm side of the foam and the wallboard a few inches away is negligible, even when it's -20F outside, +70F inside. Glacially slow convection currents (even through air-retardent batt insulation) can still move a lot of moisture, but not a lot of heat. But you're at most about R1.5 for the cavity air + air films, which isn't enough to support a big temperature difference between the R5 foam and R0.5 wallboard.