Opinions on Swedish Building Techniques

Hello,
I recently came across Greg La Vardera’s website http://blog.lamidesign.com
Although I have read much on energy efficient wall types here, I haven’t noticed any comments on the USA New Wall. I am interested in other peoples opinion on this construction and how it compares to other energy efficient wall types. (I am thinking about the Building Science Corp s list of walls and how they score relative to each other -http://www.buildingscience.com/resources/high-r-value-wall-assemblies )
I would also like to hear opinions/cpmments about Swedish platform framing and mineral insulation.
Thanks in advance,
Mitch
GBA Detail Library
A collection of one thousand construction details organized by climate and house part
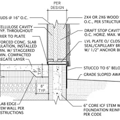
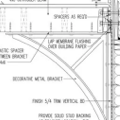
Replies
Mitchell,
Here are some links to GBA articles to get you started:
An Architect’s Take on Sweden’s Factory-Built Houses
Not-So-Foamy High Performance Construction Videos
FreeGreen’s Open-Source Floor Plan Adventure
If you enter "Vardera" into the GBA search box, you'll find a few more GBA pages with comments about (or from) Greg La Vardera.
It took me a while to find articles describing them on Verdera's site, so in case it helps others, here are two links and some short descriptions:
USA New Wall
From the outside going inward:
Weatherproof breathable cladding
1x3 furring to provide 3/4" air gap/drainage space
2" mineral wool insulation (R8, very breathable)
1/2" wood sheathing (OSB or Plywood)
2x8 stud with R28 mineral wool batts
Vapor retarder barrier (but no interior sheathing)
2x2 furring with mineral wool batts as wiring channel (R6)
Interior Gypsum Wallboard
Swedish Platform Framing
To minimize thermal breaks, the Swedish Platform system involves the stud walls stacked directly on the floor sheathing of the wall beneath, without an intervening platform. The floor sheathing 'caps' the wall below and extends flush to the exterior. Floor trusses are hung from the interior of the studs and supported underneath by a horizontal ledger running across the studs. The inner-floo volume between the trusses is insulated for the first few feet inward as additional thermal break. The bottom floor and roof have similar details that avoid thermal breaks.
It's probably just my current SIP focus, but the Swedish Platform system look a lot like the suggested modern SIP details:
Middle floor: http://www.sips.org/albums/11/sipafigs-colored-final-page-10.jpg
Bottom floor: http://www.sips.org/albums/11/sipafigs-colored-final-page-02.jpg
Thanks for posting those links:
USA New Wall
Swedish Platform Framing
There are also a series of videos introducing these assemblies:
part1 - intro
part2 - USA New Wall
part3 - Swedish Platform Framing
Clarifications to the description above:
- USA New Wall is incremental, meaning the assembly can be adopted in steps, easing builders into high performance.
- USA New Wall can be made with 2x6 or 2x8 stud walls.
- Mineral Wool for 2x8 studs is R30, not R28 (I need to go back and edit that...)
- Vapor control sheet recommended is variable permeability product such as ProClima's Intello.
Note these model wall systems deviate significantly from the test wall assemblies from BSC's above mentioned High R Value study. These Swedish based systems trade-off ultimate performance for familiar materials and trades (no spray, no blow). Although any performance trade-off would largely be made up in the better performance of the Swedish Platform framing. In short, conclusions reached in the BSC study regarding "strapped" walls really don't apply here.
Gregory,
I understand your reservations about the need for aligning the studs with the roof trusses in advance framing. But doesn’t the Swedish platform frame require that same type of alignment? If so, why would the need for alignment be objectionable in the Western platform frame, but not in the Swedish platform frame?
I don't have reservations about it. I believe aligning framing through stories as described in Advanced Framing is impractical. And this is evident by the failure of this technique to take hold even though it is decades old.
Swedish Platform Framing does align roof trusses with second floor wall studs, which is easy in practice, and does not impose on the planning of the rest of the structure. Beyond this, there is no need for alignment in Swedish Platform Framing. Check my diagrams - second and first floor walls meet with two plates, it does not require alignment as in Advanced Framing.
Nor is such alignment needed in traditional Western Platform Framing. This need for alignment is particular to Advanced Framing. If you want to understand why it is objectionable you need to speak to some of the thousands of builders who are not doing it. Perhaps try to convince them to try it.
Gregory,
Okay, I see your point now. The alignment between first and second floor is the issue because of the differing door and window patterns. I can see why it would be impractical, and understand why builders would not want to do it. Thanks for your explanation and for offering the information on this type of framing.
You are quite welcome - your questions help me figure out where I am explaining this well and where I am not.
The Swedes have some other interesting techniques that are not incorporated into my framing model as they don't fit our common practices, but are interesting none the less. For instance they use stronger trusses than we do, and space them further apart. This brings greater point loads on the wall at their bearing. Instead of aligning, they introduce a horizontal ribbon member directly under the top plate that amounts to a continuous header. They let it into the outside of the stud which leaves plenty of insulation to the inside in their 200mm studs. And this resolves any need for alignment. Done in the factory with very little extra effort or expense.
I came across the USA New wall as well as I was trying to figure out the best way to insulate my home for a second floor addition. I had come up with a similar thought to the "Best" and "better" wall, but what I could not quite figure out is:
1.) how can you put more insulation on the warm(inside) side of the vapour barrier on the inside of the house. Wouldnt the inspectors have a problem with this. I live in Alberta, Canada
2) the wiring chase is 2x2 from the looks of it, but most electrical boxes are more than 1.5" deep. Do these boxes then "push" into the vapour barrier, hopefully without breaking it?
3. I do not see a vapour barrier in between the floor trusses, just on the outside. There is then some insulation stuffed there, and no insulation to cover the gap with thin the truss structure (1.5" thick, with varied triangular shapes. wouldnt the 2' of stuffed insualtion be defeated by the air simply going around it? And once again this is on the warm side of the vapour barrier. isnt this a no-no
My though to eliminate 3. is to normally platform frame with rim joist and close cell spray foam this area. This would provide the required vapour barrier(and it would be "good" as opposed to trying to poly around some stuck out insulation) and insulation value, and I could do it myself.
My other thouught to eliminate 3. in the attic (I have vaulted trusses) is to build little triangle shaped styrofoam insulation to fit inside the triangle parts of the trusses.
Foam may not be green but in this very limited quantity, I see it as the only viable options, unless someone has some other ideas(other than changing the framing, (which I cannot because it is an addition)?
1: IIRC in Canada as long as the vapor barrier is sufficiently inside the insulation layer that it's average temp in winter is above a presumptive 4C dew point tempearture in the local climate it's fine to put it somewhere other than the interior side of all the insulation. The depth within the insulation where that occurs is of course varies by local climate.
2: Show me the picture- I can't quite follow the 1000 words.
3: Again, without the picture it's hard to tell exactly what you're referring to. Blown insulation can fill any shape, and is preferable to batts as a general rule, especially with framing that doesn't fit standard cut insulation (such as open web trusses). Cut'n cobbled chunks of rigid foam aren't really a great solution, but blown cellulose or dense packed fiberglass can be.
In a vented attic or crawlspace in the warmer parts of Alberta (say, Calgary) a vapor barrier would not be needed on floors or attics, as long as it's air tight, code verbiage notwithstanding. North of Edmonton it's potentially issue.
BTW: The whole discussion about Swedish methods needs to be understood in the context that 5 out of 6 homes in Sweden are built in factories under controlled conditions, not site-built in the way the vast majority of homes in N. America are built. The precision and quality control aspects of site building is nearly impossible to match that of a factory assembled building. Also, in Sweden energy codes are performance based, not prescriptive R values or U-factors etc. the way it's traditionally been done on this side of the puddle. Those codes are also enforced- if the house doesn't perform well it's up to the builder or designer to fix it, which can be expensive if they screw up.
I was looking at new usa "better" wall
For 2, in the new usa wall design, it goes from the inside: drywall, 2x2 wall(for wiring chase) with roxul in between the 2x2, then vapour barrier.... The problem is here in alberta, electrical boxes are more than 1.5 in deep, which is the depth of the 2x2. This means if I have a 2.5" deep electrical box, 1" would push onto the vapour barrier. Is this the plan, or can I only ever use 1.5" electrical boxes? Or do i use one of those vapour barrier things to go around the electrical box, or simply let the electrical box push the vapour barrier into the 1.5" of roxul.
For 3, i cant find the rim board detail now, but the question remains, how exactly is the rim board insulated and vapour barriered? New homes here typically spray foam the rim board in between the floor I joists.
One other question if I may. how does one "know" what this is:
"1: IIRC in Canada as long as the vapor barrier is sufficiently inside the insulation layer that it's average temp in winter is above a presumptive 4C dew point tempearture in the local climate it's fine to put it somewhere other than the interior side of all the insulation. The depth within the insulation where that occurs is of course varies by local climate."
i.e. is this 4" from the outside in? 6", 2", how do I know if a 2x6 wall with poly on it is okay enough to put 1.5" of roxul on the inside of the poly? Will I be trying to convince the inspector where the 4degC dewpoint is on the cross section of my wall?
If you give us your location with a little better precision than "Alberta", it would be easier to estimate the R-ration that keeps the vapor barrier above 4C. It's a big province, with dramatically different climates at different locations due to differences in both latitude & altitude
Calgary, Alberta, thanks
Has anyone explored how to fit electrical wiring into the 1.5" wiring channel between interior fur strips?
also, where does one source 1.5" mineral wool batt ? I could saw a 3.5" in half but this would cause quite the mess
We did our electrical wiring in a 1.7" service channel (2x4 ripped in half). I really wouldn't want to go any shallower than that, and 2" would have made it easier. Code requires you have a minimum of 1.25" between the face of the stud or furring strip and the wire, otherwise you need protective plates. I came pretty close to the limits of box fill in some locations. If you don't plan on having dimmers or other specialty devices that tend to be on the larger side, it might not be an issue.
Don't get me wrong, 1.5" is certainly possible. It's just more limiting in what options you have.
Rockwool Comfortboard comes in 1.5" thickness. Fitting that over top of wiring might be a challenge in a 1.5" channel, as it's not very compressible. That's another reason to consider making the service channel a little deeper. Or just forgo the insulation in the channel, and add an inch to the outside. More bang for the buck there anyway.
Patrik,
As long as the separation between the stud-wall and the cavity is something flexible like a membrane, as opposed to plywood or OSB, you should be able to use regular electrical boxes.
I don't know where you could get batts to fit a 1 1/2" cavity to how easy it would be to hold them in place if you did. Most builders using the similar Mooney-wall use blown cellulose, but that moves the air-barrier right to the interior, or they leave the service cavity uninsulated.
Returning to this post after many years –– singular question about the wiring in the 1.5" utility space. Since the original post I have written a blog post to address this specifically:
http://blog.lamidesign.com/2018/05/usa-new-wall-never-ending-question-of.html
The short answer is 4x4x1.5 electrical box with a single or double gang reducer/plaster cover. Typically these have more cu in than a corresponding conventional single gang box, and allow you to put your boxes flush with the furring. Total depth with reducer is 2" with 1/2" drywalls, enough to accommodate most fat devices like GFI.
And no, it won't be that simple, because you will get incorrect push-back alleging that running wire in the chase violates the requirement for 1 1/4" of cover for wires. This is an incorrect misunderstanding held by most electricians and electrical inspectors. The 1 1/4" dimension is correct, but it only applies where wires pass through or behind framing where fasteners will be used, like along studs where drywall is fastened. Its also a good caution when tacking wires to the side of studs running vertical as its easy to miss a stud with a fastener. But there is no prohibition on running wire between framing at a distance less than 1 1/4". And in fact this is common practice where wires enter and exit electrical boxes and other fixtures.
Since this post I've had the good fortune of clashing with an electrician and inspector over this which enabled me to elevate the question to the State Code Officials who supported my position. I have an informal opinion letter from NJ to this regard and would happily share it with others that clash over the same.
Thanks for the follow-up!
Greg,
If the wiring runs in the cavity without passing through the framing, how is it secured at the code mandated intervals? In particular how is it fastened within 12" of the electrical boxes?
It is very easy to fasten horizontal runs to the face of the wall studs - you just staple them through the vapor control sheet. When approaching a box you just need to fasten the wire to the nearest vertical stud to the box. If the box is between studs one will be within 12". If the box is on a stud you can fasten the wire above or below, and the make your loop of extra wire then enter the box.
Vertical runs of wire slip behind the furring for cover, and can be secured with the same black clips that are used for pex piping. All off the shelf.
https://mobileimages.lowes.com/product/converted/697285/697285500266.jpg
Thanks Greg. That makes sense.
I've used the 4"x4"x1.5" boxes with single mud plates. They are a lot easier to fit wires into than the regular deep single boxes.