Using a Double Stud Wall in Remodel

I’m remodeling a 1907 post & beam seasonal home in 5a or 6. It’s 2 stories with a wraparound covered porch on the 1st floor. The sheathing appears to consist of painted cedar shingles over beadboard. I think there may be some manner of building wrap under the shingles (if there at all, perhaps only on the 2nd story which overhangs the 1st story on 3 sides). The interior wall cavities are exposed to the beadboard sheathing. The exterior is in very good condition. There is no rain intrusion. There is no sign of condensation in the wall cavities but the home is not heated or used in the winter. I’m planning for a 4 seasons Pretty Good House.
My preference is to avoid the waste and expense of striping and replacing the shingles. We contemplate a double stud wall assembly. Our exterior wall layer strategy is: (i) seal the inside of the sheathing with Knauf Ecoseal, Owens Corning EnergyComplete or Aeroseal, (ii) dense pack cellulose insulation in the first stud cavity, (iii) Intello Plus, (iv) unfaced rock wool batt insulation in the second stud cavity (with the studs run horizontally) and (iv) drywall or other interior finish. We would do a blower test after the cavity is sealed and prior to insulation. Our thought is that the wall assembly will dry to the interior.
I’ve read a few of the articles from the last 20 years regarding double stud assemblies. The theory was that, without exterior insulation, mold and rot would result because the dew point would be at the sheathing. It appears from the later literature that field results may not always prove the theory depending upon the composition of the wall assembly.
If the shingles are well maintained (i.e., the paint is kept in good condition), should we expect that our strategy will avoid moisture damage inside the wall assembly and to our bead board and shingle sheathing?
GBA Detail Library
A collection of one thousand construction details organized by climate and house part
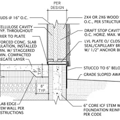
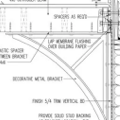
Replies
54fighting,
Unfortunately this is another one of those "it depends" situations.
The sheathing on double-stud walls relies primarily on three things to keep it safe.
- Cellulose as a moisture buffer
- A well sealed air-barrier.
- A rain-screen to remove moisture.
Which of those you can eliminate before the wall becomes risky is very situation dependent. Your shingles may allow some water intrusion, and at the same time block good outward drying. They may also be in good shape because they have relied on the heat loss from the house for drying, which will be greatly reduced.
Or conversely everything might be just fine. I'm just not sure how you predict the outcome?
Thanks.
In this instance, I believe I am lacking the rain screen. I don’t believe there is any current drying of the shingles from heat loss as there is no heat source in the building.
I am anticipating that the assembly, other than the shingles and the sheathing, will dry to the interior. So, I think the question is whether the sheathing and shingles can dry to the exterior without a rain screen and/or air leakage from the wall assembly.
54fighting,
That's the million dollar question.
Assemblies dry in the direction of lower temperature and humidity. In heating-dominated climates, that is the exterior. If there is significant moisture accumulation in the wall and it can't dry to the exterior, it will dry toward the interior, but you can't fight physics--the majority of the time in CZ5 and 6, indoor air and moisture will be trying as hard as it can to get outdoors, and anything that prevents that is at risk of moisture-related damage.
When you have highly insulated walls, such as with a double-stud wall, there is little energy to push that moisture through, so it's even more important than with thin walls to allow moisture to push through. I would never design a double-stud wall without some sort of rain screen.
The last time I consulted on a project like yours, where the owner and architect refused to strip the siding, I advised that at least 30% of the wall's R-value needed to be closed cell spray foam. The insulator was there for two weeks and charged $80,000. It was a big house, and maybe that was less than replacing the siding, but it's not how I would have spent my money.
Michael,
Thanks. That is the clear explanation I wish I could have written.
I appreciate your response, and I hope you will entertain a question or two. I’m with you; that’s not how I would spend my money in the situation you described.
Did you recommend that the closed cell foam be applied against the interior sheathing and if so was the intent for it to serve as an air/vapor barrier?
I think I have a very basic understanding of the mechanics of vapor transmission; i.e., that moisture during the winter would seek to move to the exterior. But wouldn’t the reverse be applicable during the summer; that any moisture that accumulated in the wall during the winter would seek to dry to the interior? If so, is it your belief that this drying would be insufficient?
P.S. I bought and read the PGH book; it was great.
Yes it was closed cell foam, applied to the interior of the existing sheathing. I don't recall now what the sheathing was but the foam would help with air-sealing and greatly slow vapor movement.
When you are running an air conditioner vapor drive is usually toward the interior. That's usually only a few weeks a year in climate zones 5 and 6 so it's not something you should rely on for drying out your walls, in my opinion. If you're not running an air conditioner the interior and exterior are likely at similar vapor pressures and the walls will dry in either direction.
Here's an article I wrote a long time ago about how flash-and-batt systems work: https://www.greenbuildingadvisor.com/app/uploads/sites/default/files/Why%20Flash%20and%20Batt%20Makes%20Sense.pdf.
I link to this article by Martin Holladay roughly weekly here:
https://www.greenbuildingadvisor.com/article/calculating-the-minimum-thickness-of-rigid-foam-sheathing
I'm glad you enjoyed our book!
I wonder what the roi on that is…..
Impossibly long. I disagreed with the decision but they didn't want to pay for a hygro-thermal analysis and the only safe approach I know of is to follow IRC/BSC guidelines.
It’s interesting where people are willing to spend in the build process and how proper design is often relegated.
This is an excellent explanation, the only thing I can think to add is to look at where that moisture is coming from. It can come from the exterior in the form of rainwater intrusion, that's kind of a building flaw and something that should be dealt with by the weather resistant layer rather than counting on vapor drive to clean it up. But it's true that if it's there, a level of intrusion that wasn't a problem can turn into a problem when the insulation level is increased.
The other source of moisture is vapor from the interior, that is introduced by occupant behaviors like bathing, cooking and breathing. Each occupant produces about five pints a day of moisture. Even if the wall is capable of drying to the exterior you want to keep that moisture out of the wall in the first place, with a vapor barrier or retarder on the interior.
If the wall isn't capable of drying to the exterior, then you have to keep the moisture from condensing, which is where the impermeable insulation comes in. To the extent the wall dries, it's going to be to the interior, which means either a variable permeability barrier, or none at all.
DC,
Excellent addendum.
I understand, but in my assembly I am air sealing the sheathing from the interior with one of the 3 products mentioned. Also I am using Intello Plus on the interior to reduce moisture intrusion from the interior and allow drying to the interior.
It’s seems to be an unfortunate predicament in a remodel; i.e., either avoid a robustly insulated wall or strip the exterior siding (unless Michael’s flash and batt method is economically feasible).
Air sealing is not the same as vapor sealing.
I think with Intello on the interior you're fine unless rain water is getting in.
I couldn’t reply to the post below, but thank you for the cite to those two articles.
I was looking back at the literature on GBA on double stud and saw Joe Lstiburek’s article from 2011 (I think) predicting moisture issues because the dew point would be against the sheathing and recommending exterior insulation.
But then I saw the 2015 article, “Monitoring Double-Stud Wall Moisture Conditions in the Northeast” by Kohta Ueno, which I think (I don’t want to mistake their conclusions) suggests that the results were not necessarily consistent with the theory regarding moisture issues.
54fighting,
For what it's worth, this is my take.
Your proposed assembly isn't in the category of those we always consider safe, or those we know almost always fail. It's in the group in-between that have some risk associated with them. I suspect it is much closer to the safe end of that group, but it isn't one you can guarantee will not experience problems - and I'm not sure you can accurately quantify how risky it is.
I don't intentionally choose assemblies with any risk associated with them, but many people are comfortable doing so.
That is correct, the study that Kohta was involved with did not show the anticipated moisture issues. He attributed the cause mainly to the borate additive in cellulose insulation which prevents microbial growth of anything it touches. Other insulation types don't have that benefit. Systems without borate-treated insulation may not have moisture issues either but you are increasing the risk of problems if you don't use borates.
My friend and frequent collaborator Dan Kolbert wrote this good overview of double-stud walls: https://www.greenbuildingadvisor.com/article/a-case-for-double-stud-walls. My only disagreement is that in addition to including a rain screen, a relatively permeable sheathing and borate-treated insulation, I also include a variable permeance membrane on the interior. Together, those elements have proved to be safe from problems. Eliminate any of them and the risk increases. I don't like taking risks with my building assemblies.
With a thick double stud wall assembly, an air gap between the sheathing and siding is important. I would not build such an assembly without a rain screen. You are introducing a modern problem set to an old assembly that has worked because moisture can dry to the inside. That'll change with your proposed wall.
Further, without removing the siding, it will be extremely difficult to air seal tongue and groove sheathing. I assume, too, that you'll be installing new construction windows and rearranging some architectural detailing. You could unintentionally open a good portion of the exterior.
A Bonfiglioli wall is a better option for a retrofit if you are not opening the exterior. A service cavity will help you detail an air barrier. I have used interior ISO in certain circumstances too.
One more note-
You have an old house- likely for it's character and historical nature. Often times, compromises are required. That is, you can not fit a round peg through a round hole. If that's what you'd like to do, strip the exterior.
Thanks for the responses. I learned much. I appreciate that the assembly I am proposing is not risk free. I know that I have to judge the likelihood and extent of the risk against the cost to eliminate that risk. If the cost were not significant or the risk were, I would eliminate the risk. But the costs would include hundreds of pounds of waste in a landfill and, because budgets are a reality, may include an asphalt roof rather than a metal roof, a lesser HVAC system, etc. I can figure out the cost; the risk is more difficult to quantify. At the end of the day, I suppose it’s about being put to the test. We would all agree on risk free. The more interesting question may be what is the answer when the charge against the budget, a charge that represents a reduction in scope, is $X.
There is no charge against budget- you're way off the mark. Not every tactic works on every house- simply not a good application for a double stud assembly here. Why humor a risky assembly or completely trashing out an exterior in reasonable condition? Figure a path forward that better suits your home, or sell it and move on to a new build- that is the compromise.
If the exterior were in need of replacing, then a double stud assembly would be sensible. But that isn't the case. You'd be better off starting from scratch to reach the performance standards you seek. There is immense value in repurposing an old home- a new house has much more embedded carbon, and old houses often have character detailing that's cost prohibitive in a new home.
I have had great success with older homes, they're well worth the effort and extremely satisfying to reinvent. I've created some amazing spaces that I'd never design into a new home. I will concede that the exterior or interior (except a grandfathered stair system) will need to be removed entirely in order to achieve a good performance standard. In some instances, where both interior and exterior finishes are pristine, envelope considerations are less important: do what's feasible.
Deleted
I respect your opinion, but we will have to agree to disagree.