Vapor Retarder for Ceiling Above Indoor Lap Pool

We bought a house in NY in climate zone 4A that had an indoor lap pool (50′ by 8′). Bottom line question is whether to install a vapor barrier inside the pool room before the ceiling boards are attached (so that the insulation is between the vapor barrier to the interior ceiling and the 3/4 inch plywood above that is the subfloor of the outdoor kitchen deck above)?
The pool was built as an addition on the side of the existing house so one wall to living space and nothing above for about 90% of the room. The far end of the room extends under a deck built off the kitchen. The folks who not long ago rebuilt the deck focused all their attention on keeping rain and snow from leaking into the house. That part is good. But, it appears now that they failed to account for the pretty humid room below even with a good dehumidification system because this part of the room is the back corner below grade and only about 10 feet wide, ceiling about 8 feet (ceiling is higher in balance of this 60 foot space with no living space above). I thought we had a leak in the deck but after two days of hose testing with no leak they started to take off a few of the ceiling tongue and groove boards inside this part of the pool room and the plywood is pretty well and uniformly soaked (some showing nails are rusted). They used 2 inch thick (not sure R rating) rigid and then R19 mineral wool insulation but no plastic vapor barrier before nailing up the tongue and groove ceiling boards. Seems like big mistake to me the homeowner. If the plywood is bad and has to be replaced the deck will have to be rebuilt, if the plywood is ok after drying (put aside potential mold issues for a minute), it seems like they need to put a plastic vapor barrier before re-attaching the ceiling boards. They are removing the rest of the ceiling boards tomorrow so will see how bad it looks. Appreciate thoughts on this basic question and type of vapor barrier and insulation to use and all i am no doubt missing. Thanks!
GBA Detail Library
A collection of one thousand construction details organized by climate and house part
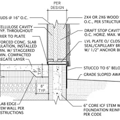
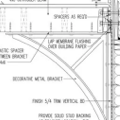
Replies
Hi Smf424.
Given that an indoor swimming pool is not a common situation and that there is more to consider here that the ceiling/roof assembly (for example, controlling humidity with mechanical systems), I'd highly recommend that you consult a local professional about this situation and not rely on the advice of an online forum. That said, you probably need some vapor control, and more importantly air control on the ceiling.
Typically, an assembly with 2 inches of rigid foam towards the exterior would need to be able to dry inward and if the foam's R-value was sufficient, you would use a class III vapor retarder (painted drywall) on the interior. However, in a space with high-humidity potential like an indoor pool room, I'd think variable-perm vapor retarder like MemBrain or Intello might be a good idea. These membranes control outward vapor drive in heating seasons and allow inward drying in warmer outdoor seasons.
No matter what you do, you must air seal the ceiling. If moisture-laden air is getting into the assembly, a vapor retarder is doing you no favors. If you do go with a membrane, you can detail it as an air barrier. If not, you need another air barrier behind the wood ceiling. That could be finished drywall. All recessed lights and other penetrations must be made airtight as well.
Hey Brian. Yes nice to have but been more of a headache at the end of the day so would not again own a home with an indoor pool. Contractor (who i don't think has much indoor pool experience) is thinking that after the plywood that is the roof of the deck above is dried out, he would paint that plywood with vapor barrier paint, use rigid insulation below that, then another layer of plywood or finished drywall, then plastic vapor barrier and then put back up the tongue and groove ceiling boards. The two bays of ceiling boards are each only 4 feet wide beam to beam and no recessed lighting. He thinks he can get to an airtight seal. We plan to direct more of the room heating toward that problem corner of the room as it has poor air flow now and have a powerful dehumidification set up.
Besides a vapor retarder/barrier and verified air sealing, also look into maintaining the room at a negative pressure to help contain moisture. Perfect air sealing is highly unlikely.
Thanks for these thoughts, much appreciated. Been having some trouble finding a local professional with experience in construction/renovation of an indoor pool.
They're not too common, but must be nice to have!
Indoor swimming pools are one of the most challenging and dangerous building enclosure problems that we deal with--the interior moisture levels are higher museums (70 F/50% RH year-round), which are also known to have problems.
BSC's basic guidance on swimming pools is covered here:
BSI-055: In the Deep End
https://www.buildingscience.com/documents/insights/bsi-055-in-the-deep-end
First question: is the swimming pool roof intended as a vented or unvented assembly? Given that it is built on to an existing house, I'm guessing that there's no way to vent the roof? Overall, a ventilated assembly buys you a whole lot more forgiveness than an unvented assembly. See the comparison between the roof assembly options in BSI-055.
Arguing over vapor barriers is a lot less important than whether there is a continuous interior air barrier. Air leakage moves far more moisture than vapor flow (moisture passing through a solid material).
Agree with the previous poster recommending negative pressures in the pool--you can think of the air in a swimming pool as a harmful substance that you're trying to keep out of your assemblies.
Contractor (who i don't think has much indoor pool experience) is thinking that after the plywood that is the roof of the deck above is dried out, he would paint that plywood with vapor barrier paint, use rigid insulation below that, then another layer of plywood or finished drywall, then plastic vapor barrier and then put back up the tongue and groove ceiling boards.
If I'm understanding this layering correctly, putting a vapor barrier paint on the underside of the plywood roof deck is the wrong location--you're trying to keep pool moisture out of the rafter cavity insulation. It also sounds an awful lot like "cut and cobble insulation"--a dangerous approach in general, and incredibly risky in an environment like a swimming pool:
Cut-and-Cobble Insulation
Does it ever make sense to cut rigid foam into strips and insert the strips between your studs or rafters?
https://www.greenbuildingadvisor.com/article/cut-and-cobble-insulation
If you can post some pictures, that might be useful.
Thanks much for the thoughts Kohta. When the pool was built in the 80's there was no dehumidification system. A set up with vents to the outside exhausting and pulling in outside air. Those were not working when we bought the house and we installed a stand along dehumidifier that can pull 195 pints a day and can keep the humidity between 50-60%. We left in place one roof vent (not in this troublesome part with the condensation issue and drop ceiling) and on the opposite end of our problem we have a wall fan that pulls out air but is not an efficient set up as when not in use it allows outside air in (not ducted). For the most part no real problems until now, although it is starting to look like the large 12 year old skylights are starting to go, but that is another story. Will try to avoid cut and cobble. Contractor just was thinking in overkill mode to prevent potential ruining of the plywood by any future condensation issue by thinking maybe pain the inside room side with vapor barrier. Still contemplate vapor barrier directly above the ceiling boards. What is the best way to do an airtight seal? The ceiling height is about 8 feet, and there is only 7 inches of space between the ceiling boards and the plywood above. Here are a couple of photos if i did it correctly. thanks again.
not sure why that photo came out sideways. exposed wood is the ceiling.
here is more of the room
Hi there! First off--I think we might be talking past each other and confusing terms when we're talking about 'roof ventilation' or 'vented roof.' What I am specifically talking about is an open air channel above the roof/ceiling insulation, to allow for outdoor airflow from low to high through the roof assembly. For clarification, check out the article below--I'm referring to the figure at "Roof Venting 201: Vent the roof deck."
PA-1101: A Crash Course in Roof Venting
https://www.buildingscience.com/documents/published-articles/pa-crash-course-in-roof-venting/view
One thing that I suspect looking at your images is that this might be an "unvented" roof assembly--i.e., no outdoor air openings connected to all rafter bays. If this is a shed roof attached to the house, it is difficult to vent the top of the assembly.
So what would I recommend given these constraints? Here are three options:
(A) All exterior insulation (safest/best)
This is the safest option that we would recommend if were were building this assembly from scratch, putting all insulation outboard of the air-vapor barrier. I would adapt "Figure 3: Sloped Cathedralized Vented Compact Roof" from BSI-055 (linked earlier). It would involve stripping the exterior of the roof, installing a self-adhered membrane air-vapor barrier (Ice & Water Shield or equal), building up multiple layers of rigid foam on top of the roof deck, and then an airspace and new roofing. This is costly, and may run into dimensional problems if there are windows in the wall above the roof.
(B) Vented Assembly
This is trying to make the cathedral roof bays into a vented assembly, with a bombproof interior air-vapor retarder. From exterior to interior:
- Roof shingles, underlayment, plywood (existing)
- Ventilated airspace ~2" between roof sheathing and insulation, bottom and top openings
- Batt insulation in remainder of rafter cavity
- 1 inch foil faced polyisocyanurate insulation, all seams taped. No penetrations for lighting or mechanicals
- 1x3 or similar strapping
- Roof finish boards
To make this work, you will need ventilation openings low (at the soffit) and at where the roof hits the wall. This might be difficult, but here's an example product: http://www.roof-2-wall.com/
(C) Closed Cell Spray Foam Assembly
This is the highest risk option, but it is what I pull out when I'm backed into a design corner. I would make sure the plywood roof sheathing is dry (using heat and dehumidification indoors), using a wood moisture content meter to check MC. Then apply closed cell spray foam in the rafter bays, followed by a fluid-applied air- and vapor barrier membrane (Class I, 0.1 perms or less) directly to the surface of the spray foam. Do not attempt to use polyethylene plastic or something else to cheap out: putting the vapor barrier directly on the foam ensures that air leakage will not bypass the air/vapor control layer. An example product is Henry Air-Bloc® 16MR Low-Temp Liquid Emulsion Vapor Impermeable Air Barrier Membrane. The key thing is finding a product that is compatible with the spray foam (many manufacturers will not warrant this application) and one that does not have excess odors for an indoor use.
With option 3 do you spray the spray foam and ceiling rafter/joists with the liquid vapor barrier then just leave exposed so covering
It seems to me we have ventured into a very specialized area of expertise.
My guess is the correct answers varies by region and have been learned at great cost and will not be shared on the internet for free. I think the smart move would be to find a local expert with indoor pool references you can contact.
You may want to look for a Indoor swimming pool consultants.
http://www.omegapoolstructures.com/residential-outdoor-and-indoor-pool-designer.html
Walta
Well BSC, who I believe Kohta Ueno works for, is one of the groups to consider hiring. And he is giving advice for free here. Admittedly, this design work really would benefit from an onsite review and engineering plan.
On the layman's building science side of things, do you keep the pool covered when not in use? A cover should have a huge impact on the ability to control moisture in the space. I imagine the pool is not used for more than a few hours a day. Motorized covers are available.
Thanks so much for the helpful suggestions. We dont want to take off the roof and outdoor deck above it at this stage. This one annoying corner of the pool room with drop ceiling is a real pain. No real way to ventilate the drop ceiling bays but will double check (most is below grade in this corner). Might have to go with option 3. Also have to do better to keep room humidity lower and get some airflow to this one corner. I do believe there is Ice Water Shield installed as part of the roof assembly. There was clearly no air barrier installed just above the ceiling. Boards and the rigid foam boards were not sealed. It has been surprisingly hard to find locally a pool design engineer despite being just 30 minutes from NYC.
No real way to ventilate the drop ceiling bays but will double check (most is below grade in this corner). Might have to go with option 3.
As a warning, Option 3 is the highest-risk in terms of moisture. We have applied a Class I vapor barrier to the underside of the spray foam, shutting off any inward drying. And the underlayment on the roof plywood is also a Class I vapor barrier. The preferred approach is to have a ventilated cavity over the roof's structural sheathing, allowing outward drying--see the cathedral assembly in BSI-055 as an example.
I do believe there is Ice Water Shield installed as part of the roof assembly.
To clarify--this material is an air and vapor barrier, but it is on the wrong side of the assembly for a pool in a cold climate. The idea behind the air and vapor barrier is to keep the source of moisture (pool air) from coming in contact with cold surfaces.
Thanks Kohta. At this point we are thinking about putting right above the tongue and groove ceiling boards 1/2 inch plywood and making an airtight barrier using a vapor permeable membrane called Adhero from 475 building supply (it is peel and stick on the side of the plywood facing down into the room) and using a tape product they sell to seal all seams and where plywood meets the beams. Above the plywood we are thinking about unfaced mineral wool insulation. The roofer is nowhere to be found but i think he used Ice Water Shield and do not want to rip up the roof under an outdoor deck at this stage. Others have said could use a 6 mil poly just above the ceiling boards. We are sort of stuck between a rock and a hard place thinking about the 3 options you suggested at this point, but when the weather gets better here in NY we may just have to start from scratch as a last resort. Not a good situation.