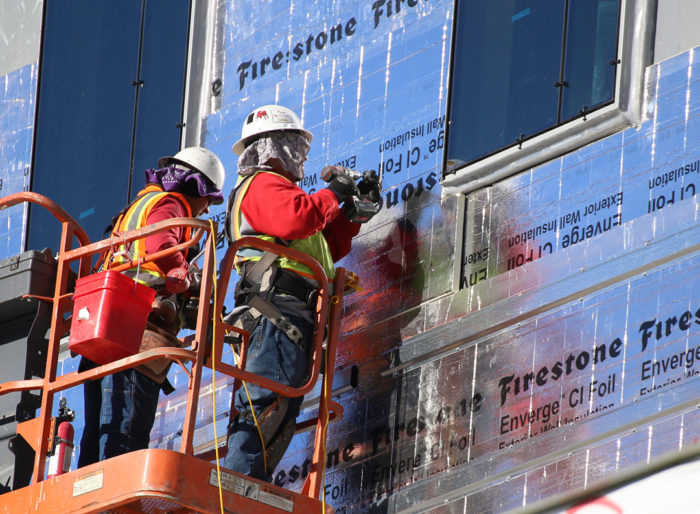
Image Credit: Image #1: L&W Supply
R-value tests by the National Roofing Contractors Association and the Building Science Corporation have revealed that the thermal performance of polyisocyanurate is greatly reduced at cold temperatures. While the R-value of polyiso at a mean temperature of 75°F might be about R-5.7 per inch, the effective R-value of the polyiso drops to about R-4.8 per inch at a mean temperature of 25°F.
Over the past three years, GBA has published several articles on this problem. (See, for example, In Cold Climates, R-5 Foam Beats R-6 and Cold-Weather Performance of Polyisocyanurate.) As builders have learned that polyiso wasn’t doing as good an insulating job at cold temperatures as they had thought, they’ve started to ask questions, including:
- How long have polyiso manufacturers known about this problem?
- Are polyiso manufacturers doing anything to try to solve the problem?
In response to such questions, it’s fair to say that polyiso manufacturers have been tight-lipped. John Straube, a professor of Building Envelope Science at the University of Waterloo in Ontario, has had several conversations with representatives of polyiso manufacturers. In a 2015 interview, Straube told me, “Maybe the manufacturers … are not telling us the truth. But in apparently honest conversations with several polyiso manufacturers, they’ve told me that they do not fully understand why this is happening. PIMA [the Polyisocyanurate Insulation Manufacturers Association] doesn’t even believe the phenomenon is real. Some of their members … say, ‘I am not 100% sure it is a real effect.’ Well, it is real. … Here’s the thing about polyiso manufacturers: They do not share their proprietary formulations. Manufacturer A may not know what is in Manufacturer B’s foam. So now, when we discuss cold weather performance, they are kind of going, ‘I’m really surprised.’ But it’s possible that they are…
Weekly Newsletter
Get building science and energy efficiency advice, plus special offers, in your inbox.
This article is only available to GBA Prime Members
Sign up for a free trial and get instant access to this article as well as GBA’s complete library of premium articles and construction details.
Start Free TrialAlready a member? Log in
5 Comments
Is the GWP really unknown?
It's astounding to think Letts wouldn't know the GWP of the secret ingredient. Perhaps it's some newly proposed gas that hasn't been analyzed for GWP, but would they really invest in studying the performance vs. temperature before figuring that out? More likely he is bluffing, knowing that if he said a number, someone could cross reference it and find out what they are using. Or perhaps they made him undergo a selective memory purge procedure before allowing him to give this talk.
Thanks for the good reporting and the appropriate emphasis on the fact that 25 F is a bigger problem than 40 F. In the paper, there's a nod to the fact that the location of the insulation in the assembly matters, but the paper still concludes that looking a colder temperatures is not necessary. That's seems like a contradiction.
Another point I'd like to see better addressed by the manufactures is how this settles out after 10 to 50 years of aging. Maybe we can simply design based on that eventual settled performance and consider any short-term improved performance a bonus.
The discussion of how the different blowing agents interact with the cells walls is very interesting.
Small correction: I believe the date was Dec. 2016.
Still better than EPS?
It seems that despite the problem, the R-value per inch at 25 deg F is still significantly better than EPS. So if I want to maximize the benefit of 2" of rigid non-permiable insulation, and it rarely goes below 20 deg F, then Polyiso would still be the most effective of the low GWP choices. Correct?
More R-values
Maybe, manufacturers should provide a chart with REAL temperature R-values that Designers and Builders can rely on... start at 0°F to 100°F in 10°F or 20°F intervals, in that way, folks in AK and CAN can use those values that are appropriate for them, as well as folks in AZ or TX to use theirs, and everyone in between.
I'm sure providing truthful and open information would be helpful for most of us.
EPS is better at 25 F
Adam, the thermal conductivity of EPS varies with temperature too, and in fact it become a better insulator at low temperature. You can see that this plot of thermal conductivity (lower values = more thermal resistance)
https://www.greenbuildingadvisor.com/sites/default/files/Karagiozis%20-%20thermal%20conductivity%20of%20a%20variety%20of%20insulations%20as%20a%20function%20of%20mean%20temperature.jpg
Below about 7.5 C (45 F) the EPS beats the sample of polyiso shown in that chart. By the time you get down to 25 F, the EPS has twice the thermal resistance of the polyiso!
The sample shown there may be a particularly bad one, so that may be a little pessimistic. But they key point is that as polyiso is getting worse at low temperatures, EPS is getting better.
That's 25F MEAN temperature through the foam. @ Charlie Sullivan
Those performance tests are done with at least a 50F temperature difference between the warm & cold sides of the foam. So in an insulating sheathing option with other insulation on the interior, that would be 0F outdoors, 50F on the interior side of the foam to achieve a 25F mean temp. When it's 25F outdoors, the mean temp through foam sheathing would be significantly warmer.
The mean temp through the foam layer depends on the stackup of other materials (including insulation layers), the indoor temp, and the outdoor temp, and in some assemblies, the thermal mass in each layer if it's enough to induce a significant time delay.
It's silly to look at the performance at the 99.6th percentile temperature bin- most of the time you're more interested in the average seasonal performance, or the average performance during the coldest 5-10 weeks of a typical year. If your January binned hourly mean outdoor temperature is 25F, (a typical US climate zone 5 location, like Chicago: https://weatherspark.com/averages/31158/Chicago-Illinois-United-States ) estimate the mean temp through the foam layer based on the proportional R values for when it's 25F outside. Even though the foam performance may crash (or rise) at lower temperatures, the total number of hours in the heating season that it's lower performance are small compared to the total heating season, or the fraction of heating degree-days.
Log in or become a member to post a comment.
Sign up Log in