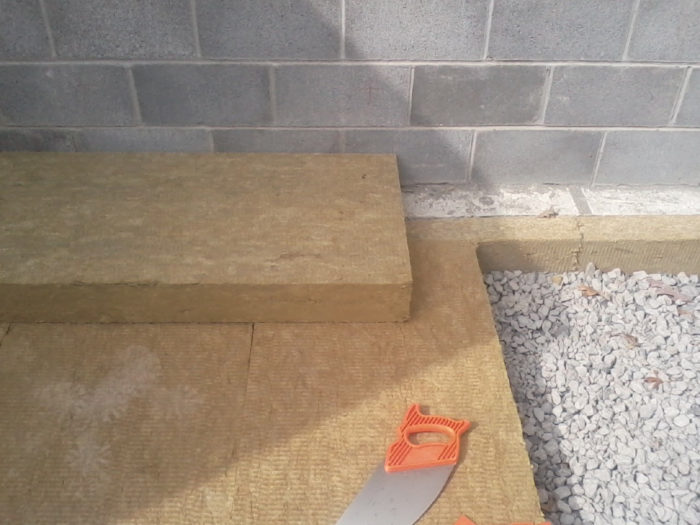
Image Credit: Image #1 and #2: Michael Hindle
UPDATED on April 5, 2016
Most green builders who need a layer of horizontal insulation under a concrete slab specify expanded polystyrene (EPS), an affordable product that performs well in this application. If a builder specifies high-density EPS rated for below-grade use, the product is very durable.
That said, many green builders don’t like EPS. Some object to the fact that polystyrene is made from petroleum, while others worry about possible health problems associated with the brominated flame retardants that polystyrene manufacturers add to EPS.
These builders have always wished there was a good, affordable way to insulate concrete slabs without the use of foam.
What about mineral wool?
Mineral wool insulation is available in several different forms. Some builders have looked at the densest available mineral wool panels and wondered, “Are these insulation panels dense enough to install under a slab?” When asked that question, mineral wool manufacturers have usually answered “no” — at least until the last few months.
A couple of years ago, I asked Iain Stuart, a technical solutions coordinator at Roxul, about using Roxul under concrete slabs. Stuart told me flatly that Roxul insulation products were “not for horizontal use under slabs.”
After several years of dithering, however, the engineers at Roxul, a manufacturer of mineral wool insulation, recently gave builders the OK to use horizontal mineral wool insulation under concrete slabs.
The announcement was oral
The first sign that Roxul was ready to change its public position came last fall. In the November 2014 issue of Environmental Building News, former editor Alex Wilson shared the news that a Roxul representative at a Passive House conference in Portland, Maine, announced that the company would “stand behind” the use of Roxul mineral wool insulation installed horizontally under slabs.
Ever since Wilson shared that news, I’ve been waiting to see…
Weekly Newsletter
Get building science and energy efficiency advice, plus special offers, in your inbox.
This article is only available to GBA Prime Members
Sign up for a free trial and get instant access to this article as well as GBA’s complete library of premium articles and construction details.
Start Free TrialAlready a member? Log in
19 Comments
Sub-Slab Roxul
Martin - Nice ,informative job. Does anyone have info. on prices for any of the 3 types of Roxul boards for Maine or New England area?
Response to Kevin Zorski
Kevin,
Contractors who contact local distributors and ask about the price of Roxul products get a wide variety of answers, depending on where they live in North America and whether other contractors in the area are requesting the material. In some areas, contractors are still being told that they must order an entire truckload of insulation; when that's the case, residential builders are in a quandary.
The bottom line: if you want to know about availability and prices for any building materials, you have to talk to distributors (lumberyards) in your area.
In his 2013 article on the topic, Alex Wilson shared what he learned about the price of Roxul insulation in southern Vermont:
"I was pleasantly surprised recently when I asked Leader Home Center in Brattleboro, Vermont, to price a number of insulation materials for a BuildingGreen report we’re revising. The contractor pricing for ComfortBoard IS came to $0.64 per board foot, compared to $0.48 per board foot for standard polyiso, $0.75 for fire-rated polyiso (Thermax), and $1.07 for XPS. While pricing will doubtless differ in other regions and for different quantities, the fact that ComfortBoard is in the same ballpark as these other materials is great. Even after correcting for the lower insulating value (you need more thickness of ComfortBoard to achieve R-10 than with the foam plastics), Comfortboard IS locally was more affordable than XPS: roughly $1.59 per square foot at R-10 for ComfortBoard vs. $2.14/sf @ R-10 for XPS."
Basement walls
For those of us who are a bit foam-wary this is very good news.
Martin, any comment on the basement detail Roxul provides for wall insulation?
Response to Malcolm Taylor
Malcolm,
As some GBA readers know, I usually don't recommend the use of air-permeable insulation materials like fiberglass or mineral wool to insulate the interior side of a basement wall, because of the likelihood that condensation will form between the concrete and the insulation.
In its detail, Roxul appears to be admitting that condensation is indeed possible. The text in the illustration notes that the mineral wool layer on the interior side of the basement wall is a "drainage layer to footing." Since a layer of mineral wool connects the wall insulation with the crushed stone layer (which is drained by a perforated pipe), anticipated condensation can flow downward to the crushed stone relatively harmlessly.
It's an interesting solution to the condensation problem.
Martin
I bet there will be a lot of condensation on the poly.
Response to Malcolm Taylor
Malcolm,
The Roxul detail shows just 12 inches of polyethylene at the bottom of the wall -- not a wide enough strip of poly to cause problems, in my viewpoint. There is a "vapour control layer" on the interior side of the wall -- presumably this could be gypsum wallboard painted with vapor-retarder paint, I suppose, although the vagueness of the text isn't helpful.
Strangely, the layer of material directly under the concrete slab is also called a "vapour control layer," not polyethylene, even though the words "6 mil poly" appear elsewhere (describing the 12-inch-wide strip of material at the base of the wall).
So the detail raises several questions. Remember, it's a draft detail.
10" of RockBoard 80 seems risky with just a 4" slab
Martin,
Assuming a linear compression coefficients (of the RockBoard 80), given the code min live loads of 40-50 psf, and the 10" of sub-slab insulation, that would imply a dynamic +/- 0.1" + of compression and de-compression of the insulation from changing the live loads around on the finished slab (unless i am calculating something wrong). In my basement, i definately have a few loads much closer to the 300 psf under the shelves in my basement which get cycled moving from summer to winter seasons (which would be close to 1" of compression movement...
Granted concrete has rigidity, but I think you would need to add significant amounts of steel to reinforce the slab to prevent cracking and floor settling -- especially if a future home owner would decide to repurpose a room.
Response to Jonathan Rupp
Jonathan,
First of all, this article recommends that anyone interested in trying this technique should use Roxul IS or Roxul CIS, not Rockboard 80.
Second, if this approach to insulating under a slab seems risky to you, I would never urge you to go this route. Just use EPS.
Jonathan
Another way to look at it might be that 10" of any type of sub-slab insulation is a bit nuts.
Price and results
Kevin, In my pricing I have found that mineral wool is less than XPS and competing with Poly-iso. It is a bit higher than high density EPS though.
Martin, thanks for writing on this and shedding more light on this product. I want to be clear that our experience with the RockBoard 80 was really very good. I would and in fact am using it again on another Passive House project. I am using CIS on yet another project and will have comparative experience to report on. My expressions of caution stem in part from my experience on affordable housing job sites. So, while the guys at Gosnell Buildiers handled the Rock Board 80 extremely well and got terrific results, I am always looking to find the design solution that will be applicable whether working with high end craftsmen like Gosnell, or crews on my affordable housing projects. Hence my excess of caution, and if you can get a little more margin of confidence, why not?
I am delighted that Roxul will release their technical Bulletin and bring this product more into the mainstream.
Response to Michael Hindle
Michael,
Thanks for your comments. I'm glad to hear that you are using mineral wool under slabs, because job-site experience is essential to understanding how this technique works. I look forward to any future reports comparing Rockboard 80 to Roxul CIS.
RockBoard 80 approval history
Just a little history of why we selected RockBoard 80...in July of 2014, prior to the Technical Bulletin release and after much pursuing, Roxul provided us with an official letter and multiple emails from their technical department stating that RockBoard 80 was among their products approved for sub-slab installation. The material was then approved by our structural engineer and installed a month later. The recent Technical Bulletin does not, however, list RockBoard 80. When you are a pioneer of something you tend to be overly cautious and critical of small issues and maybe want to change something the next go around, but there has been no problem in overall performance with the RockBoard 80 and we appreciate the support of Roxul in this endeavor.
Response to Malcolm Taylor
"Another way to look at it might be that 10" of any type of sub-slab insulation is a bit nuts."
We likely live in different climates so this is possibly and apples vs oranges thing, but where we built the Ecohome house in Canada, the 8 inches of insulation we installed under our slab was arrived at after lengthy consideration. Air and ground temperatures, the cost of insulation, the cost of heating along with the type of ground we were building on were all factored. So the 'optimum' amount of insulation will vary depending on where you build and even the ground on which you build (rock conducts heat much quicker than soil for example).
When you separate concrete from the ground with enough insulation, it stops acting as a conductor and instead assumes the temperature of the conditioned space. This will for sure reduce and possibly eliminate all together the need to heat a concrete floor.
So if you direct your design and budget more towards heat retention rather than heat generation, you are then comparing the price of insulation against the price of heating infrastructure. If I add a couple of thousand to my sub-slab insulation budget and in turn I save even more than that on heating infrastructure (meaning if I no longer need a radiant floor but can get by with a heat pump and still have warm feet), I may save money on the initial build, I'll definitely save monthly on heating and I'll be paying off what effectively amounts to being a lifetime supply of heat.
In a super-insulated house like this you are effectively 'purchasing' heat at the bank through your mortgage, rather than 'renting' it monthly from utility companies, so a bigger bill is offset by a smaller one. The actual cost you have to put out monthly can be surprisingly similar, until the mortgage is paid off then it will be much different, in a good way.
Mike
With ten inches of Comfortboard IS you are looking at R-40 sub slab insulation. Surely you are well beyond the point of diminishing returns where the increase over, say, half that amount makes no appreciable difference.
While I agree entirely with your characterization of purchasing heat through the increase in efficiency of the building envelope as being a good thing, there is a point where more makes no difference, and I think R-40 well exceeds that point.
Word - not sure thsi makes sense even in climate zone 2. I would love to see a WUFI etc modeling showing relative energy loss in that house. I would strongly suspect dollars a could be much better spent on superior windows , let alone skylights (!) and perhaps even spending on zip “2.0” (ie liquid flash seams rather than tape).While I do advocate you never can spend too much to keep a basement dry up to and including backfilling entire foundation with gravel , i see all too often really unbalanced insulation (R60 roofs, R30 walls and now R20 plus basement) specs on houses with double pane, or generic American triple pane windows ….Huh ?!and in many araes where radon is an issue, you need a robust sub slab evacuation system anyway and that shoudl assuage all the foam phobes re sub slab foam (tho I wouldn’t advocate spraying in the field!)
Malcolm
Ours was 8 inches of Comfortboard CIS, so somewhere in the R32-R33 area. Where are you located Malcolm? I could see how it would seem like overkill for someone in a more hospitable region. Our engineer figures under most circumstances in this climate at least R20 -25 would be justified under slabs, more in cases of building on rock. Using 2 inch sheets our options were either R24 or 32, so we preferred being slightly over instead of slightly under. Finding the true 'sweet spot' of insulation is at best guess work anyway, and impossible to pin down stretched over different climate zones. Along with climate and ground considerations you would also have to factor the estimated and useful lifespan of a building to be accurate, another impossible feat. I would say though, that under-insulated slabs are more common that over-insulated ones.
So there was no cracking in monolithic slab where it transitions from roxul to foam?
Tim,
At the time this article was written, none of the slabs had unusual cracking. Nor have I heard any reports to that effect since the article was published.
“[Deleted]”
Log in or become a member to post a comment.
Sign up Log in