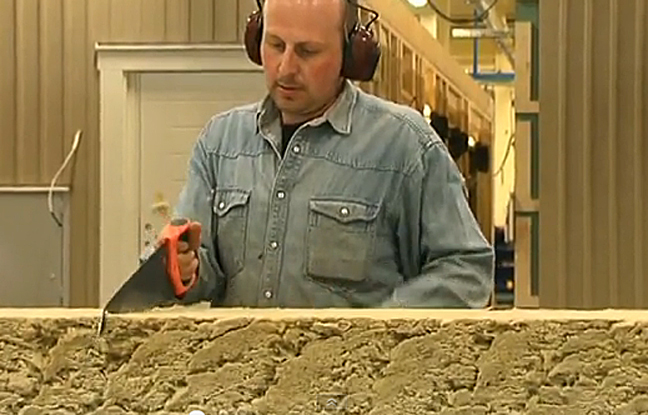
Image Credit: Smålandsvillan
Image Credit: Smålandsvillan A mineral wool batt has a shape and keeps its shape. It is much stiffer than a fiberglass batt. [Photo credit: Smålandsvillan]
Image Credit: Smålandsvillan Blocks of mineral wool insulation are stiff, so they need to be shoved into stud bays. [Photo credit: Smålandsvillan]
Image Credit: Smålandsvillan A mineral wool knife is a large serrated knife like a giant bread knife. [Photo credit: RepCon NW]
Image Credit: RepCon NW This simple table makes cutting batts to fit into easy work. We are working to bring them into the U.S. The first lot of tables marked in English units (inches, not centimeters) are coming to the U.S. If you would like one of these tables, contact us to arrange it. A worker uses a mineral wool cutting table to trim a mineral wool batt. [Photo credit: Randek AB]
Image Credit: Randek AB With the help of a cutting table, mineral wool batts can be trimmed precisely to fit narrow stud bays. [Photo credit: Randek AB]
Image Credit: Randek AB
If you are interested in green building, or call yourself a green building expert, then you should know about mineral wool insulation. If you have not seen mineral wool handled and installed, then you need to read this.
If you think that mineral wool batts are similar enough to fiberglass batts that you already know what you need to know about it, then you are a fool. And you still need to read this.
If you have already read some of my essays, you know that I am an advocate of using mineral wool insulation to improve the energy performance of the houses we build in the U.S. There are many reasons why I think that mineral wool is the best insulation for us here. Recently I find myself making my case for this repeatedly, so I thought it would be worthwhile to get it all down in one place and just point to it in the future.
Mineral wool is different from fiberglass
So why am I constantly explaining why I like mineral wool, and what’s good about mineral wool? And why am I constantly saying, “No, that’s not what mineral wool is like; rather, it is like this”?
It is because the green building community has almost universally decided that ol’ fiberglass batt insulation is bad. There are good reasons for this, and we’ll look at those, but the more obvious question is, What does this have to do with mineral wool?
The overwhelming assumption among those interested in green building is that mineral wool is just like fiberglass batts, at least in all the ways they feel fiberglass batts are bad. So if fiberglass insulation is bad, then they are convinced that mineral wool insulation will be bad, for all the same reasons. Its an easy conclusion to reach, but a lazy misunderstanding.
Not all batts are bad
The reality is that this is just not so. In fact this simply highlights the profound misunderstanding of what mineral wool insulation is like among green building advocates. The misunderstanding centers around the form of insulation: batts. The green building community has been very quick to condemn batts, when the problems that concern them actually revolve around fiberglass batts.
Let’s make this absolutely clear: There is nothing wrong with insulation in the form of batts. Batts are a convenient way to package insulation for transport, handling, and installation, which is why it is the predominant form for insulation in the U.S.
However, there are legitimate reasons to criticize fiberglass batt insulation, the status quo in U.S. house construction. It’s a brief list of reasons, so let’s look at them.
Fiberglass batts have low R-values
First, low insulation values. That’s right: fiberglass batts sold here in the U.S. don’t provide as much insulation as they could. It’s not that you can’t make fiberglass in higher performance levels; in fact it is made and sold in Canada at higher R-values.
But the big fiberglass insulation makers are not ready to bring that high-R-value fiberglass insulation here to the U.S. How do I know? I’ve called them, spoken to their people about it, and they’ve told me they won’t bring the high-R-value insulation to the States even though I said I wanted to spec it.
I say, shame on them. We should all take our business elsewhere.
Most fiberglass batt jobs are sloppy
Second: bad installations. Bad installations mean sloppy fitting of batts into stud cavities, over-compressing the insulation or leaving gaps that allow convection, sloppy trimming around obstructions, and any number of other installation sins that spoil the effectiveness of the insulation.
The installers are only partly to blame. The material is limp and fluffy, and because of this the handling, cutting, and placement requires more care to install well. It rarely gets that care; hence it is most often installed quickly and cheaply.
Where is the air barrier?
Third: bad air sealing and a bad vapor retarder. Well, what is that about anyway? Insulation is for insulating, not for air sealing — right?
Well, somewhere along the way, somebody had the bright idea to combine a vapor retarder with a fiberglass insulation batt. It turns two construction steps into one, and in theory saves labor and so saves money. The problem is that once you’ve had a bad installation as noted above, and cut the vapor retarder around electrical boxes, what you end up with does not seal well against air leaks or vapor diffusion.
Hell, you say — I don’t need my insulation to make an air seal, because I used that good ol’ housewrap on the outside. Nope, nothing wrong with housewrap — but it provides no help with the air sealing you need at your vapor retarder.
The air seal in this case wants to be on the warm side of the wall, to prevent interior moisture from entering the wall cavity and condensing during the winter heating season.
The problem is the fiberglass, not the batt
Let’s summarize the lesson here: What most green pundits blame on batt insulation is the fault of fiberglass insulation. While mineral wool also comes in batt form, it is a completely different product with different properties.
It does not suffer from any of the above problems of fiberglass, yet retains the best part: it’s easy to handle, easy to install, and best of all, your labor force already knows how to do it. That is no small point.
Roxul is going after the residential market
OK, let’s talk about mineral wool. I’m going to refer generally to “mineral wool,” but as of this writing I have in mind the products of one manufacturer: Roxul. This is the only mineral wool manufacturer taking the residential market seriously in the U.S. right now.
Roxul sells its mineral wool in consumer-friendly packages, just as you would expect in a big box home improvement outlet. They are making their batts in sizes made to fit stud walls, clearly aimed at the market for building houses of wood, the very same market that fiberglass is sold to. This is important. Same kind of packaging, same kind of expectations, same kind of product experience.
They are putting their products into long-standing material distribution streams that every builder in the U.S. understands. It’s available from the same sources, ready to be installed by the same people.
There are other mineral wool manufacturers out there, but they are not proactively pursuing the residential market. I’m not talking about them or their products. If your criticism of mineral wool revolves around your experience with some other product from some other time, then your concerns don’t apply here and now. You should catch up.
Mineral wool batts have a higher R-value
So let’s talk about insulation value first. In batts offered for 2×4 stud walls, mineral wool comes in R-15, while fiberglass comes in R-11 or R-13 (although it can be special ordered in R-15 in the U.S.). In batts offered for 2×6 walls, mineral wool comes in R-23, fiberglass comes in R-19 (and again, you can special order higher R-value, but only R-21).
Furthermore, mineral wool is available in batts that fit 2×8 framed walls, and these are R-30. Fiberglass is not offered in batts for 2×8 stud walls.
These are the products available now, today, in mineral wool. If you are interested in maximizing the energy performance of your walls, it’s a no-brainer. Even if you changed nothing else about the way you build, you can improve the performance of your walls by switching to mineral wool.
Mineral wool batts are easier to install
Second, installations. You might think, “How can mineral wool batts be easier to install than fiberglass batts?” It’s simple. Fiberglass batts are limp, soft blankets. They have to be hung and stapled into place or they will slump and leave gaps.
Mineral wool is dense and firm, and it friction fits into the stud space. People don’t generally understand this, and this is why I am including photos. Mineral wool has form; it has a shape. If you pick it up it does not drape or fold; it retains its shape. (See Image #2, below) It is a block. This block, when shoved into a wall cavity — and I say shoved because it literally must be pushed into place — when shoved into place, fills the entire wall cavity (see Image #3, below). No gaps, no sags, no spaces. More importantly, no convection, no drafts, and no stapling.
You still have to cut the batts to fit
There is one caveat here: Just as with fiberglass, mineral wool must be cut to fit odd-spaced studs and triangular corners that may exist between framing members. However, this is much easier to do with mineral wool.
With fiberglass batts, you are actually told by experts to use a 2×4 stud as a straightedge while you cut the fiberglass batts with a sheetrock knife. You are expected to compress the fiberglass enough to cut through it with the short blade of the razor knife. And if you are doing it correctly, you trim the batt and kraft paper to different widths, to leave a tab so you can staple it up. Good luck.
Mineral wool is different. You can actually measure and cut mineral wool to size, like cutting a big block of wood. In fact, for carpenters this comes as second nature, because as you might expect they are quite good at measuring, and then cutting something to fit, when that something has a shape and can be understood like a piece of wood.
The cuts are made with large serrated knives — imagine a giant bread knife. (See Image #4, below.) So there is no compressing the insulation flat so you can cut through it. The mineral wool retains its volume while you cut through it with the long knife.
You don’t cut against a 2×4, but rather you cut it on a purpose-made cutting table, which is just like a very large carpenter’s miter box (see Image #5). It adjusts for the thickness of the insulation, and allows you to set precise angles for cutting to fit those odd spaces. (Read more about the insulation table here.)
Insulation cutting tables
The mineral wool cutting table, for me, is the eye-opener: the cold water in the face that made me realize that we never took insulation very seriously here in the U.S. Here we pull a 2×4 out of the dumpster, and use a razor blade holder to cut it on the floor deck. That’s the best we can do.
Mineral wool is cut precisely to fill every void — quickly, accurately — providing complete fill of the wall cavity. Installations are easier, faster, and better than with fiberglass.
I’ll say with some confidence that no other insulation product can fill a stud space so completely. No spray, no blown-in product, no blanket can fill a wall void as well as a proper installation of mineral wool insulation.
Smart vapor retarders
And third, air sealing. Mineral wool only comes in unfaced batts. No foil or kraft paper vapor retarders are offered. This means an independent vapor retarder must be installed. Simply said, this is the best way to create an airtight envelope for the house.
My favorite product in this regard is a variable-permeability membrane, a so-called “smart” membrane, because the permeability self-adjusts to suit conditions. An example is the MemBrain vapor retarder from CertainTeed. This is their branding of the smart membrane product made by their European owner, Saint-Gobain.
Another high-quality variable-permeability membrane is Intello Plus and DB+ by ProClima. This vapor retarder membrane has a low permeability level in dry conditions, but if the humidity level within the wall gets high, the material will open up to allow the moisture to dry to the other side. The ProClima Intello membrane is notable because it is well reinforced. It will not tear or split from stapling, and this tolerance of handling makes it easier to work with.
Include a service chase
Now, if you wish to increase the likelihood that you won’t need to make any punctures in this airtight layer, then you should plan on a wall with an interior wiring chase, such as the U.S.A. New Wall that we’ve elaborated on here.
Your best chance for an airtight wall is if you don’t puncture your air barrier with electrical work, outlet boxes, and switches. If you’ve not studied it before, when you are done here go read the U.S.A. New Wall article, and the Swedish Platform Framing article to see how all these come together to make a simple but high-performance wall.
That covers insulation value, installation, and air sealing issues. Mineral wool goes on to excel in other ways that contribute to my preference for this material.
It won’t stay wet
Mineral wool is hydrophobic. From the dictionary: “Tending to repel or fail to mix with water.” If fiberglass insulation becomes wet, you end up with a wet lump of glass lint, with no insulation value to boot. Mineral wool, on the other hand, will not become wet.
In fact, water beads up and rolls off the surface of mineral wool. This promotes water draining and drying if the wall cavity becomes wet, rather than holding water like a sponge. Which would you rather have in your wall?
Addressing thermal bridging
One of the big issues with improving the performance of our walls is thermal bridging through the wall studs. The most popular way to overcome this has been to install insulation on the exterior of the wall, continuously, to insulate the studs from the cold.
The issue here is that rigid foam insulation has been the most common way to do this. The problem, however, is that the foam creates a vapor retarder, and the last thing you want is a wall with a vapor retarder on both faces.
So the practice has been to make walls with exterior foam insulation without interior vapor barriers. The foam must be thick enough to keep the dew point within the depth of the foam in order to prevent condensation within the wall cavity.
The problem here is that only the most general recommendations for these configurations can be made in the building code. Weather outside of the design limits can result in condensation. Highly humid interior conditions can cause condensation.
My opinion is that these walls are not resilient designs and are poor practice. A wall with a traditional configuration — with a vapor retarder on the interior — works in all conditions, even when the temperature or interior humidity goes beyond the design values.
My only caution is, if the home is to have air-conditioning, then it is very important to use a smart vapor control sheet, as mentioned above. These variable-permeability membranes will ensure the wall performs well during the cooling season when the vapor profile of the wall is reversed.
The good news in this story is that mineral wool comes in configurations that can be used as exterior insulation in place of foam. These are very dense fiber panels that are strong enough to support siding and cladding material mounted over them in a manner similar to foam. The difference: mineral wool is vapor permeable, which means you can insulate on the exterior without trapping moisture in the wall.
Furthermore, the insulation value of these dense mineral wool panels approaches the performance of foam. Typically for XPS foam you would get in the neighborhood of R-5 per inch. Mineral wool will provide R-4.6 per inch.
And because of mineral wool’s hydrophobic properties, it will not absorb moisture in this location, and in fact will promote the drainage and drying of rainscreen siding cavities.
Foam insulation brings other problems, such as dilemmas in flashing practices, and the dubious reliance on adhesive tape as a long term weather barrier.
Fire safety
Mineral wool simply makes wood stud construction safer. This is the same material that is used to fireproof steel members in commercial construction. Mineral wool will stand up to temperatures that will reduce fiberglass to a puddle of molten glass.
Mineral wool will increase the length of time that a wood-framed house will stand during a fire. It gives the occupants more time to exit safely, and firefighters a safer window of time to enter a burning home.
Summing up
Let’s just go over some broad conclusions now. Mineral wool is a completely different material from fiberglass. They both just happen to fall in the broad classification of batts.
Mineral wool is available in higher insulation values than fiberglass. Mineral wool’s rigid shape and ability to be measured and cut accurately enables it to fill stud voids more completely than any other insulation product, with less effort, and more speed.
Mineral wool fits into the building practices of 99.9% of America’s builders with no need for new processes, extensive retraining, or changes to new subcontractors, new suppliers, and new business relationships.
Mineral wool is the easiest way for the vast majority of builders to step up their game and start building better.
Appendix 1: Concerns of green builders
Those focused on green building often immediately point to the presence of formaldehyde in binders used in mineral wool. Formaldehyde-based resins have long been used in the “glues” that prevent fibrous insulation from coming apart. It’s long been used in fiberglass, and is still used in many fiberglass products today. But it is clearly on the way out. Fiberglass batts from Knauf and Owens Corning are now available with alternate binders.
Mineral wool still contains a very small amount of formaldehyde-based binders. The wall insulation products from Roxul meet the GreenGuard Gold certification standard (formerly known as GreenGuard Children and School certification), which means they are consistent with products that are used in schools, day-care centers, or other environments where children spend significant periods of time. What this means is if you are a builder shifting from traditional fiberglass batts, this mineral wool will likely have lower formaldehyde emissions than what you used before.
If you are a green builder seeking to eliminate any formaldehyde, then you have other options.
On the matter of embodied energy, the Roxul products now use from 75% to 93% recycled content, depending on the availability of the raw materials, and their facilities are “zero waste to landfill.”
If you are a green builder who can get the same performance from a material with less embodied energy, then great. If you are a builder considering shifting from fiberglass, the energy savings from the lifetime performance of the mineral wool will greatly exceed any difference in manufacturing energy of the fiberglass you use now.
Appendix 2: Predictions
Higher R-value insulation will eventually own the market here. CertainTeed, one of the biggest U.S. makers of fiberglass, is now owned by Saint-Gobain, a large producer of mineral wool in Europe. CertainTeed now has access to mineral wool, and could begin to sell it in North America as it gains market share.
Owens Corning, the other large American insulation maker which is highly vested in fiberglass, has purchased an American mineral wool manufacturer, Thermafiber, widening its offerings to include both mineral wool and fiberglass.
The third large American manufacturer of fiberglass insulation is Johns Manville, which has recently acquired an American mineral wool manufacturer, IIG (Industrial Insulation Group).
Not all of these companies are actively promoting mineral wool for residential building insulation, but it is remarkable that we find all of the major American insulation manufacturers vested in mineral wool.
Fiberglass has also been dogged by health questions. In 1984, fiberglass was classified as a “reasonably anticipated” carcinogen. This did not proceed to the next level, “known carcinogen,” and in 2011, following more research, it was removed from this list.
Currently fiberglass is classified similarly to mineral wool, which is considered what is called “biosoluble.” This means that these mineral fibers dissolve in contact with tissues, leaving no fibers to trigger disease. Whether fiberglass can shed its unhealthy reputation, or if it will be overtaken by mineral wool with its higher performance levels, has yet to be determined.
Editor’s note: This article was adapted from a blog written by Greg La Vardera in 2012.
Greg La Vardera is an architect practicing in Merchantville, New Jersey, just outside of Philadelphia. His work has included the development of several off-site building methods and progressive design in catalog house plan publishing. He is now focusing on creating energy-efficient prototypes for production building based on Swedish precedents, as well as posting blog entries on his website.
Weekly Newsletter
Get building science and energy efficiency advice, plus special offers, in your inbox.
104 Comments
Compression
Great article. Sounds like a really good product for Wildland Urban interface zones.
"You still have to cut the batts to fit
There is one caveat here: Just as with fiberglass, mineral wool must be cut to fit odd-spaced studs and triangular corners that may exist between framing members. However, this is much easier to do with mineral wool."
When used in a stud bay, does mineral wool compress to take up different widths due to bent or warped studs. In other words, if one stud is bent to the left 1/8" or more and the other stud is bent to the right 1/8" or more would one then cut the batt to the largest width? If so, what it the tolerance?
not a hand saw
BTW the "hand saw" in the picture at the top of the article is not a saw, but rather has a serrated blade like a bread knife, just in a large format like a hand saw. It is a Bahco ProCut insulation saw. Bahco is distributed in the US by Snap-On Tools.
@ Debra
Its not rigid/stiff, but rigid/resilient. It relies on being slightly oversize for a snug fit.
Exactly how much - you should follow the manufacturer's lead - you can determine from measuring the uncut batt from out of the bag. It comes in standard widths for 16 & 24"oc, and is sized to fit snug in that spacing.
Response to Gregory La Vardera
Greg,
I'm sorry if my caption to the photo was inaccurate. One might argue that a hand-held insulation saw is a type of handsaw. (On the manufacturer's website, Bahco calls this tool a "handsaw.")
But I agree with you that it is more accurate to describe this tool as an "insulation saw."
Debra
I have to ask: Why is this a good product for "Wildland Urban interface zones"?
@Martin
No problem Martin - it was not identified in my original post. I just thought it was a worthwhile clarification. Its part of the theme here - they use special tools to make insulation installs better. We use 2x4s and sheetrock knives...
Response to Malcolm Taylor
It does not burn and we have a chance of building a fire safe ventilated rain-screen using Roxul comfort board. I realize this article is geared towards Roxul batts but I think using the batts in combination with out-board Roxul comfort board appears to solve some of the issues that may be caused by exterior foam and other cavity insulation products.
Don't over-sell the higher R value.
R23 rock wool in a typical 25% framing fraction allowing R1 for gypsum and siding comes in at R15.2 whole-wall.
R20 (code minimum for US climate zone 5 under the widely adopted IRC 2009) would come in at a whole-wall R of 14.3, less than an R1 difference, about a 6% difference in heat flow.
R21 fiberglass is widely available at box stores (at about 2/3-3/4 the cost of R23 rock wool in my neighborhood) and comes in at R14.6 whole-wall. R21 fiberglass isn't dramatically floppier/squisher than R23 rock wool.
Everybody's favorite straw-man the R19 fiberglass isn't even code legal without another insulating layer. In a 2x6 cavity it performs at R18, with a whole-wall R of R13.6, but a 1/4" XPS fan-fold siding underlayment would bring it up to code performance.
If batts, rock wool is my first choice too, but the marginally higher R is the least of it.
Also:
"The foam must be thick enough to keep the dew point within the depth of the foam in order to prevent condensation within the wall cavity"
There is never condensation inside the wall cavity from interior moisture drives until the wood is actually saturated. The dew point of the entrained air in the cavity will never be higher than the temperature of the wood. When the wood falls in temperature it takes on moisture as adsorb (not liquid)and liquid water never form as on either the fiber or the wood until the wood is saturated, which takes more than just a few weeks of abnormally cold weather if the house is built with the IRC prescriptive minimums for exterior R for the climate zone. Those prescriptives should be considered minimums, but it doesn't take a whole lot more than the prescriptive minimums to make the assembly HIGHLY resilient (recommended), the air-sealing benefits of smart membrane vapor retarders notwithstanding.
Nice article
I've always been a fan of mineral wool, now even more so. Good article!
Skärbord
Gregory,
I checked out Skärbord.
Looks like a great tool - I only wish I'd known about it sooner.
Debra
Good point!
What I still do not know about mineral wool
Even after reading this very informative post, I still do not know the most important fact to all home builders - the cost difference between mineral wool and fiberglass. (Mineral wool has always been more costly than fiberglass)
I would also like to hear your commentary or opinion on the labor factor that would be added by a single company who had trained professionals doing the work on each material.
I do not agree that the same tradesmen who install fiberglass batts have the right kind of experience or training to graduate from using a utility knife to using both a tape measure and a hand saw. I have never had an insulation company offer me both products.
In the case of insulation contractors who do fiberglass batts, my experience is that their cavalier "anything goes" approach to quality control leaves their installers at a profound disadvantage to anyone who has ever been properly trained to install mineral wool.
Also, the insulation companies that I am familiar with pay their workers on a piece rate. If they paid the same per batt for mineral wool as they do for a fiberglass batt job, then the outcome will surely be less effective than the manufacturers say it should be because I expect that properly installed mineral wool would take longer to install than a comparable job done with fiberglass. But the installers will do BOTH jobs equally badly in order to make their quotas.
Answer to John Hansen #12
At recent local box store pricing the cost of R23 rock wool came in about 25% more than R21 HD fiberglass, both designed for 5.5" deep 2x6 cavities. On a small project I did about 15 months ago R15 rock wool was at cost-parity with R15 HD fiberglass.
It's not a hand saw, it's a serrated knife with a saw-type handle. There are no rocket scientists wasting their careers doing intensive training on how to use them. If anything it's EASIER to get a square-ish end cut with a purpose-made insulation knife than with a utility knife, and is recommended for use with fiberglass as well. I've personally found it easier & quicker to trim & split rock wool batts with a tight fit than mid-density fiberglass, but I can't say I have massive experience with either. It's slightly easier to deal with than HD fiberglass too, again from a fairly amateur perspective, with less than 10,000 square feet of lifetime installation experience with batts of any kind.
While the industry "typical" or "average" installation is pretty sloppy, there are batt installers capable of doing it right with either material, but the notion that it's more difficult or takes longer to do it right with rock wool is counter to experience.
Rely to John Hansen
It's too bad that, from your and others comments, it appears fiberglass installation in some areas is very poor. It isn't here. With all the time and diligence in the world i couldn't do as good a job as my installer does.
Extending your question as to whether installers will do as poor a job with mineral wool, I'd have to ask whether it is the material that causes the poor work or some other factor. If it isn't inherent to the material, which my installer shows is nor the case, then what is to stop any contractor from doing a sloppy job with spray foam or dense pack cellulose? The consequences of poor installs with those material are much more severe too.
Mineral wool - great solution for fire breaks too!
Thanks Gregory for the excellent article -- which should help dispel common misconceptions about mineral wool vs fiberglass. A few suggestions:
> Fire breaks: Mineral wool is a great solution for the firebreaks required at the top of stud walls, and for the linear breaks required every 10' along a basement wall. If you follow Martin Holliday's excellent advice and run foam board along your basement wall, for example, you will need to include a firebreak that runs from the floor to the ceiling, every 10 feet. (Foam board cannot run continuously along the concrete basement wall.) Mineral wool is a great solution; just leave a gap in the foam board behind one of the studs, and pack it full. Similarly, mineral wool is easy to pack into the gap at the top of your stud bays, around pipes and wires, etc. -- to meet that firebreak requirement. Make sure you ask your inspector first, however. Some inspectors will only approve solid fireblocking with 2x lumber and 3/4" OSB.
> Unlike fiberglass, mineral wool acts like clay when you pack it into gaps and holes. You can shape it with your hands, and it stays put. You can pack it into the end of a ceiling joist bay to insulate the rim joist, for example, or around HVAC ducts.
> Wear gloves! Like fiberglass, the fibers in mineral wool can make your hands and arms itch.
In short, great stuff! It cost a bit more than fiberglass at my local HD -- and was worth every penny.
Twice as hard to work with than Fiberglass
Even when I was still in the "dark ages" and using combinations of fiberglass and rigid insulation, I tried upgrading to mineral wool and found it twice as hard to work with than fiberglass. As a builder I still insisted on doing all my own insulation installation trying to be a meticulous as possible. Mineral wool is very difficult to work with, trying to cut around boxes, working around wire. Fiberglass you could at least cut a little tight around receptacles and the fiberglass would hug the boxes. Unless you were literally ready to spend a week scribing outlets your install would have gaps.
There's a better way its called cellulose. Fill all the voids. Anyone who has handled a lot of this product knows that it still falls short and is still just a batt insulation.
Don't fall for the hype.
Sound attenuation
One more property of mineral wool is that it is a very good at sound insulation. We used dense packed cellulose for the exterior walls but did double stud walls and Roxul for soundproofing between our home offices and TV room.
Mineral Wool & Fiberglass Options
I am interested in doing much of my own construction work in order to achieve the highest possible quality. This would include installing the insulation. Because of my inability to install spray foam, plus a variety of other reasons, I have ruled out that type of insulation. I would consider cellulose, but hesitate because of probably needing to hire that work.
So, my preference has been fiberglass batts. I know all the complaints about that product, but I can overcome those drawbacks with 100% success, including a perfect installation. I will not use paper faced batts, but rather, rely on a separate vapor barrier. I find that fiberglass batts friction fit and hold themselves in place with no problem. I prefer to revert to double studs and a relatively low R-value insulation rather than maximizing stud width by using 2 X 8s and using the highest R-value insulation possible.
However, in a superinsulated, extra-thick wall, fiberglass batts do raise some strategy questions about combining batt thicknesses to fill the cavity, the density to use and its availability in various batt thicknesses, and the option of compressing it to raise its density.
My approach is to incorporate a service cavity as Mr. La Vardera mentions, which eliminates the need to pierce the vapor barrier with electrical boxes or to fit insulation around them. I also would have no piping or other obstructions within the insulation cavity in order to reduce the fitting of batts as much as possible.
So, within this overall approach, I welcome the addition of mineral wool as another batt insulation option. I have never used it, but I will certainly consider it going forward. Generally, I see it as a maximum-performance batt option. I too have wondered and inquired with insulation manufacturers about why they don’t come out with higher density fiberglass. Until they do, I see the mineral wool option moving in the direction I want to go. I have used a very high density fiberglass board, but have heard little about its application to building insulation. I have understood that it is intended for industrial applications. I don’t see why this could not be the future direction of high density fiberglass.
I had not known about the mineral wool batt cutting table shown by Mr. La Vardera, but I have been thinking about such a device for cutting fiberglass bats. I agree that the utility knife and straightedge used for cutting fiberglass is problematic, but the problem is in the very short length of a utility knife blade. To penetrate the batt with the utility knife blade, the knife body drags into the batt and pulls out chunks of insulation. A longer blade kitchen knife works much better. The ideal cutting table could cut miters, but this is a major challenge with fiberglass batts because they are cut in a state of compression. So the miter angle for a finished cut has to be modified for the cutting process in the compressed state of batt thickness.
I understand Mr. La Vardera’s point about the need to cut and fit mineral wool with the measuring and cutting mindset of a carpenter. I apply the same standards to cutting and fitting fiberglass batts, and believe that this is an essential requirement for a good installation job. Ignoring this requirement is the main reason why fiberglass batts are often considered to be poorly installed. However, I see no reason why careless installers will not achieve the same poor fit with mineral wool that they do with fiberglass.
Response to Ron Keagle
Ron,
You wrote, "The utility knife and straightedge used for cutting fiberglass is problematic, but the problem is in the very short length of a utility knife blade."
You may be interested in reading an article I wrote for the May 2003 issue of Energy Design Update, in which I review long-bladed insulation knives. I will post the article below as two jpg files.
[Click on the image below to enlarge it. The two images below look like one image, but they are really two images. If you click near the top, you'll get the first image. Then click near the bottom to get the second image.]
.
An 8" serrated bread knife works pretty well
... for cutting & trimming rock wool (& fiberglass) batts you can't find the purpose-designed tools. Insulation knives are available at box stores in my neighborhood.
Using utility knifes to cut fiberglass (especially HD fiberglass) is a bit of a hack, only to be done in a pinch, though still a commonly used method for low-density goods. Insulation knives work better though, on any density of batt.
Response to Malcolm Taylor's comment #14
You have a good way of addressing the question of what factors contribute to the poor quality that I see. I think there are a few issues.
1) The piece rate paid to the installers may work for simple walls and flat ceilings, but complex structures reduce the ability to achieve quality work at the same $/batt that the men would get paid. The need for speed that is created by paying piece rate results in batts simply being TORN rather than cut. Even the mineral wool that is stuffed around the drains under showers and tubs is seldom cut but just shredded by hand.
2) Insulation companies generally do not have a supervisor in the field checking quality. Rare is the company who has anything more than a dispatcher in contact with the installers. If there is a field supervisor, he is mostly concerned with whether there is enough material to finish the job, and when will the crew get to the next assignment.
3) Builders would NOT do QC inspections of insulation if it were not code required. Lazy builders cause many of their own problems when they think they can simply buy the job at the lowest price. And builders typically want the draft stopping done for "free" by the mechanical trades who drilled the holes, and then they leave that task out of the contract for the insulator.
4) Until recently, carpenters were seldom tasked with any responsibility for building a tight envelope, and they felt that it was all supposed to be done by the insulators. Many carpenters still do not "get it."
5) While the builder specifications might call for electrical boxes not be placed back to back on outside walls, negligence by the electrician and several other players make the task next to impossible for the insulators to make it any better than it already is. I have NEVER had any insulator bring up any issues that prevent them from doing a quality job. They just do not have the time to ask the builder to do any rework at this stage and the builders may have already had the drywall stocked. Here again, the attitude of the builders is as much at fault as the insulators. Builders do not want anything to slow them down, and that attitude sets the stage for all of the trades.
Swedish Platform Framming
Did anyone else read or notice the Swedish Platform Framing Gregory posted. Insulation is just a part of our issues. I didn't quite get the split lower sill? How many pieces are there and that is the only thermal bridge but a weak one? 3, 2 outer and a center "tongue and groove" So the center one is being used as an alignment tool for a prefabbed wall? If you don't run a chase you just strap the joist with a ribbon metal strap and you have a rim joist I didn't get that?
"Attached to the wall is a plywood plate, with the rest of the sill plate. This is like a tongue and groove joint, which allows our anchoring, and the sole plate of the wall above to be one in the same. It also permits the wall to be positioned precisely on the foundation when the sill plate is installed, not when a wall panel is dangling from a crane. The wall keys into the sill plate and its in the right position. If you were site building this you would use a solid sill. Inboard of this is a sill plate for the floor joists. Walls using an interior wiring chase tie the joists to the studs using the first 2x2 furring member(5). Walls without the interior wire chase use a rim joist, or ribbon tie let into the joists tops as is common with plate nailed floor trusses. Ok. Did we follow that? One sill plate. No sole plate. No rim joist insulation space. Wall batts continue all the way to the sill plate uninterrupted. The vapor retarder/barrier(6) also continues all the way to the wall sill uninterrupted. This is huge when you are trying to create a continuous vapor retarder, and huge that we can make a consistent insulation cavity all the way to the sill. And we are keeping count of thermal bridges, right -1 "
I wish I could read the first 3d picture text?
http://blog.lamidesign.com/p/swedish-platform-framing-info.html
Safety?
The workers in the photographs have sound protection equipment, but where are the safety glasses and mask to prevent inhalation of particles. The shirt on the worker in the lead photo isn't clean - he's obviously having stuff come off onto the clothing while cutting and handling the batts.
Cutting insulation batts and boards
Martin,
Thanks for posting those insulation knives. They look like the right tool for cutting fiberglass. I have never cut mineral wool, so I wonder how a serrated knife works for doing that. For cutting XPS, I like to use a hand saw because it removes material so the blade can’t drag from the friction. I also use a hand held circle saw or table saw at times. That insulation cutting table appears to just be a guide for a hand saw or knife.
@John Hansen
John, I've seen fiberglass crews take to mineral wool without loosing a step. I've handed them my Bahco knife and seen it immediately change their work flow, and the quality of their work. The contractor reported they finished the job with greater speed. I don't think my experiences are unique.
@Ron Keagle
The service cavity takes very little additional effort to install, and greatly speeds the main stud cavity installation, since it is now free of wires and pipes. Quality and speed goes up, and with another layer of insulation in the service cavity a thermal break is introduced.
You can build these assemblies with fiberglass, but I'd still stay away from the faced batts. The separate smart vapor sheet makes it so easy to establish your primary air-tightness layer between the service cavity and studs, and the Swedish Platform Framing shows the way to extend that all the way around the interior. So much easier than taping sheathing, and trying to make that air tightness transition from outside wall to interior ceiling.
@ Terry Lee
If you are not clear on any details of the Swedish Platform Frame contact me direct and I'll try to help. You might watch the associated video as it looks at the assembly in 3d and in some ways shows this better.
@Ron Keagle
That Bahco knife is also good for foam, and they claim it makes a lot less crumbs than toothed saws. There is a good video showing this on the Bahco web site. Seek it out.
@Dana
I disagree with your dismissal of the higher density and r-value as an oversell. You can not get higher r-values without going to a foam product which then has undesirable impact on the vapor performance of the wall system. Its a no-brainer to use the higher value mineral wool. The additional cost is off-set easily by the better performance, and for the installer it is off-set by faster better quality installs.
Thank you for your account of adsorption, but not so much for your dismissal of the risks: "…which takes more than just a few weeks of abnormally cold weather …". You know well that the wood in the cavity will always be colder than the average temperate section through the assembly, and the studs may be experiencing adsorption to some degree during normal temperature ranges, and in a pre-or partially saturated state before entering an abnormally cold snap. That means it is more prone to moisture problems, mold growth, and decay. This is compounded in places like bathrooms that also experience out of range humidity. I maintain that this kind of assembly is not resilient.
The point is it really takes some analysis to get it correct when you do a wall system that relies on exterior foam insulation to control for condensation, or adsorption if you have to speak building science. Here lies the problem. The vast majority of houses built in the US never see an architect, never mind a building scientist. Advocating for these reverse vapor profile walls, whether you call them perfect walls or remote walls, or whatever is a recipe for failure when handed off to an industry that builds from model wall assemblies or prescriptions in the code. Assemblies with interior side vapor control in heating climates are simply more resilient.
Response to Gregory La Vardera
Gregory,
You wrote, "Advocating for these reverse vapor profile walls, whether you call them 'perfect walls' or REMOTE walls, or whatever, is a recipe for failure."
I'm sorry, Gregory, but I disagree. I'm not sure whether your broad statement is based on exaggeration or ignorance, but there is absolutely no evidence of problems with REMOTE walls -- while there are countless examples of problems with walls insulated with batts. It's all fine and good to describe the advantages of mineral wool insulation -- I tend to agree with you on most of your points -- but there is absolutely no evidence to support the idea that advocating the REMOTE approach is "recipe for failure."
We will agree to disagree then (response to #25)
Sure, R23 is R3 better than code-min, but translates into R1 improvement in thermal performance. It's not the fault of the material, but needs to be clear to whomever is buying it that an R23 studwall is not a 15% improvement in thermal performance over a code-min R20 studwall. It's less than half the performance gain that the center-cavity R might imply.
I'm shocked and dismayed when people put R30+ closed cell foam in a 2x6 16" o.c. studwall, for a gain of about R2 in whole-wall performance over an R20 code min fiber solution. Yes, it's higher-R, but there is both cheaper & better performance enhancements. The upcharge for R23 rock wool over R21 HD fiberglass at recent pricing is nowhere near as egregious as the closed cell foam example. But it's still significant, while the thermal performance improvement isn't, which is why that uptick in R value isn't a good selling point. (I'm saying this as someone who would pay that upcharge every time, but not for the R-value, for other attributes of rock wool.)
It doesn't take a lot of analysis to come up with dew point calculations for exterior foam, in fact it doesn't take any calculation at all. IRC 2012 prescriptive minimums (spelled out in chapter 7: http://publicecodes.cyberregs.com/icod/irc/2012/icod_irc_2012_7_sec002_par025.htm ) are sufficient. In US climate zone 5 at the same thermal performance, an R13 + 5 code min wall (or an R15 +5 of slightly better thermal performance) with no interior side vapor retarder other than standard latex paint is more resilient than an R23 2x6 wall with an interior vapor retarder- the sheathing stays warmer, and there is more drying capacity, despite the potentially lower vapor permeance of the exterior layers.
At 3-5 perms interior latex is still a pretty good vapor retarder for riding out the cold weather extremes- enough so that it's only the averages that count. The increased adsorption rates during a 1-week cold snap isn't going to materially affect the peak moisture content of the wood, and even a mid winter month averaging 5F colder than normal isn't going to cause a problem. Five consecutive winters where all 13 winter weeks averaged 5F colder than normal might, if you were dead-at the IRC prescriptive minimums, and on the cold edge of your climate zone. Exterior insulation works, and works BETTER than smart vapor retarders (WUFI, anyone?).
But more exterior-R is of course better, since it bumps the wintertime mean sheathing temp a bit further, and code-minimums is the crummiest assembly that you are legally allowed to build. The upcharge for another R4 of exterior insulation above the prescriptive minimums is on the order of 40-50 cents per square foot, and buys a HUGE amount of dew point margin, as well as an improvement in thermal performance uptick that is still cost effective in almost all utility markets. In a green-building blog discussion code minimum building assemblies are not the defaults, even if code-min is buildable using crummy/so-so/good/better/best-resilience methods.
@Martin
There are countless problems with walls insulated with batts because they were built with kraft faced fiberglass which provides neither an air barrier or vapor control, or barely if installed well.
I am talking about wall assemblies installed with a continuous vapor control layer also serving as the air barrier. That is an assembly that can be batts, or other materials as well. This is not a batts vs exterior foam question, its interior vs exterior vapor control.
The other reason there are countless problems with walls insulated with batts is because of the huge installed base. There is no where near the installed base of Remote based wall assemblies in the US. I think you are making an apples to oranges comparison.
That fact is that Canadian building science went one way, Swedish building science went the other. The Canadians never had a good solution for the rim joist space, hence insulating outside it. The Swedes solved this, without adopting the counter intuitive move of vapor control to the outside. That is it in a nut shell. My opinion is one is a solution, the other is a hack.
@Dana
I don't find your comparisons fair, nor apples to apples.
An assembly with vapor control at the interior can also have exterior insulation, which improves the sheathing temp and bequeaths all of the resilient qualities you ascribe to exterior foam/vapor control.
OR you have the option to create a service cavity at the interior, which makes it so much easier to keep the vapor control layer free of holes, and hence the temperature of the sheathing is not really a concern.
And you can do both the exterior insulation and service cavity if you want the Best performance.
But I don't put much stock in the vapor control of latex paint when every outlet box and switch box makes it irrelevant. And time spend on air-tight drywall practices would easily pay for the service cavity which is a much more resilient approach, something that wont be compromised by casual remodeling in the future the way air-tight drywall (jumbo shrimp?) can be.
The fact is that the natural pressure in the housing industry is to put up as little of an expensive material like foam as possible - not to put up a little extra because it will perform that much better. The vast majority is code minimum, that's it, and less if they can get away with it. And at the scale of the climate zones which is how the code dictates foam thickness, there are plenty of opportunities for local climate, not to mention recent wild weather variations, to push an assembly beyond what the code has anticipated.
It seems there are many fans of this exterior foam approach on GBA, so I apologize for being so contrary. I see it as poor practice, and its discouraging to see it so highly recommended by such a popular source.
Response to Gregory La Vardera
Gregory,
You wrote, "There is nowhere near the installed base of REMOTE-based wall assemblies in the US. I think you are making an apples to oranges comparison. That fact is that Canadian building science went one way, Swedish building science went the other. The Canadians never had a good solution for the rim joist space, hence insulating outside it."
I agree that there are many more walls in North America that are insulated with batts than there are insulated with the REMOTE system. But we have lots of data on how exterior insulation affects sheathing. Researchers have found that exterior foam insulation makes wall sheathing warmer and dryer. (For example, see the data from the Coquitlam test hut.)
I am not saying, of course, that there are failures in Sweden. The Swedish wall system works fine. But there is no need to make unwarranted aspersions about the REMOTE system, which is extremely robust. It's ironic (and clearly untrue) that you wrote, "The Canadians never had a good solution for the rim joist space," in light of the fact that the Canadians invented PERSIST, and that exterior rigid foam is an excellent way to insulate rim joists.
@Martin
Martin - I am not making unwarranted aspersions - I am expressing my opinion in the comment section.
And my opinion is that piling foam on the outside of the wall is not an "excellent way to insulate the rim joist". It is an expensive way, and it then triggers a whole host of flashing complications, that again I feel American builders will be unprepared for, and unwilling to invest the time and cos to execute correctly.
Also the performance of Remote style walls in Canada, where very cold temperature ranges are common, and the thickness of foam has to be sized to anticipate this, is a different situation than introducing it in the US where the temperatures are higher, extreme cold spells are becoming more common, and there will be resistance to building beyond code.
That is simply my opinion, that is what I am calling a recipe for failure.
The Swedes invested a great deal in building science and rejected this approach. They did not reject it because their housing industry wants to spend more on walls than they need to. They rejected it because they had better solutions. Today they have a housing industry where every house is built to high performance levels. What do we have in North America?
Response to Gregory La Vardera
Gregory,
You are entitled to your opinions, of course. But the data don't support your opinions.
You wrote, "Also the performance of REMOTE-style walls in Canada, where very cold temperature ranges are common, and the thickness of foam has to be sized to anticipate this, is a different situation than introducing it in the US where the temperatures are higher."
If you are worried that the spread of the REMOTE system from cold climates (Alaska and Canada) to the lower 48 states will leak to an increase in problems, then you have the situation backwards. Designing walls with exterior foam is easier, not harder, in warm climates than in cold climates, because less foam is required to keep the wall sheathing above the dew point in winter.
It looks like I'm in the same boat as Dana (on a different issue). We're just going to have to agree to disagree on this point.
@Martin
I think I've made myself very clear, but I'll try one more time, and I'll try not to insult you nor suggest you are ignorant. You keep returning to the same claim regarding the performance data which leads me to believe you do not follow what I am saying despite its simplicity, or less generously you are choosing to respond to what you want to and ignore the rest.
First, I know that a Remote wall system will perform fine within its design parameters. And I am aware they can be made more resilient by adding more foam. And I am aware that if BSC builds a test assembly perfectly it will live up to its premise. And yes, they have lots of data supporting that. That is not my point.
My contention is that these wall systems will not be built in the ideal context of a test, they will be built in market place by real people, not scientists, and that best laid plans being what they are they will fail. The data supports my assertion that there is a point at which these Remote walls will fail to perform. You may not agree that these conditions will come about, but it is the simply physics of the matter is that this is true. You know this to be true, and continuously stating that the data does not support my opinion is a deliberate misinterpretation, and disingenuous.
Building Errors: If Remote style walls become widespread contractors will make mistakes when they build these walls. You know this to be true, you are well familiar with the track record of the American housing industry.
Out of range conditions: Changing climate has not and will likely not continue to cooperate with our longstanding categorization of climate zones. We are clearly experiencing wider variations and divergent conditions. You say that warmer climates are easier to design for Remote wall systems. I say that is wrong. In fact current design standards make these walls more vulnerable with the out of range weather conditions we are experiencing. But it does not take climate disaster to experience out of range conditions. All it takes is a teenager who takes 1/2 hour showers.
Economics: The economic incentive for builders is not to build in margins that make these walls more resilient. You know this to be true. The industry has a long history of cutting corners, and in the case of large merchant builder so value engineering home models to extract as much value from assemblies as possible.
These factors combine to create pressures that make these Remote style wall assemblies risky. They are already fragile, and it is my opinion that they will not stand up to the rigor of adoption in the wider housing industry. We have better options.
Gregory is making some valid points'
And Gregory I too have voiced exactly your concerns as my own. I have remodeled homes where rigid foam thoughtfully employed over OSB on the exterior caused the worst rot possible. Three times I have found framing that was so far gone as to have become soil no wood left period. Meanwhile the finish layers were there so the customers are standing there so disbelieving that even looking at the damage they think I am somehow involved subterfuge.
We builders should build assemblies that do not fail easily from almost assembling all correctly.
Martin and Dana by the way I also respect the knowledge you both convey here... but Gregory is making some valid points. To me at least.
I also respect Martin and
I also respect Martin and Dana's position. But I believe I am making valid criticisms. If my expression seems exaggerated, its because I see no critical stance with regards to these assemblies.
@aj I think the kind of failures you see are due to exactly the kind of application I am wary of. This was no strict application of the Remote Wall premise. The Remote Wall approach recommends 2/3 of your insulation value outside the sheathing. The stipulations for exterior foam applications without interior vapor control in our code in no way approach this. You can have 2" of foam - R10 over even the worst possible wall assembly - 2x4 w/R11, and you are still not even close to their recommendations.
In the US it is not in the least bit uncommon for a remodeling contractor to apply 1-2" of foam over an existing wall assembly with kraft faced batts. This is all kinds of bad, but many of them think they are following best practices for energy efficiency.
Gregory, every contractor in
Gregory, every contractor in my area is making the same "too little foam" mistake over glass filled walls of old.
GBA seems to not understand the realities of the actual majority of the building and remodeling market.
foam on the outside
I do not understand the benefit of demanding our walls dry to the inside by putting foam on the outside. Not even considering moisture loading of the sheathing in the winter, it would seam if there was a leak from the outside due to inclement weather, the foam wall will be at risk. There will be leaks over the 100 year life of the building. Seems like we will need a fast way to dump water behind the foam. I know there are products for this but why create a problem then have to fix it. I also wonder what the effects of 100 years of paint maintenance will have on the drying to the interior for moisture loading in the winter. Seems like a vapor open system in the form of rockwool board on the exterior combined with a rain screen ventilation channel would be more resilient than a load of foam sheathing on the outside. I just don't understand peoples attraction to exterior foam. Rockwool will warm the sheathing, everything dries, what's not to like.
Debra, good points, you may
Debra, good points, you may be predicting where many start to go..... May take decades, people are very very adverse to new and change...
Debra,
I agree, but there is a large jump that Mr. La Vardera makes from championing mineral wool to his reductionist claim that only his wall works. The variants are numerous: a conventional stud wall with rigid mineral wool batts on the exterior in place of foam, his quickly dismissed double wall with the outer one balloon framed to eliminate thermal bridging. There is more than one way to skin a cat - although I'm reluctant to enter this debate after seeing the abrasive way Mr. La Vardera deals with anyone who disagrees with him.
Response to Gregory La Vardera (Comment #37)
Gregory,
I'll try to find some points of agreement.
You wrote, "First, I know that a REMOTE wall system will perform fine within its design parameters." Good. So we agree on that point.
You wrote, "My contention is that these wall systems will not be built in the ideal context of a test, they will be built in market place by real people, not scientists, and that best laid plans being what they are they will fail."
I think we agree on this point as well: namely, that if a wall system is built right, it will work well, but if errors are made, then it can fail.
Here's the main point, though: if a builder is sloppy, or if a builder doesn't understand water management issues, or if a builder doesn't know how to flash a wall, or if a builder doesn't pay attention to airtightness, almost any type of wall can fail. The need for good workmanship is universal. It applies to REMOTE walls, but it also applies to Swedish walls.
You ask for an apples-to-apples comparison. Fine. Let's compare a well built REMOTE wall to a well built Swedish wall. Fair enough? Both work.
If you want to talk about sloppy practices, we can also compare a poorly built REMOTE wall -- say, one with bad flashing -- to a poorly built Swedish wall -- also with bad flashing. Fair enough? Either wall can fail, of course.
You hypothesize that we should be building well-flashed walls with mineral wool insulation, a carefully installed smart vapor retarder (installed with attention to airtightness), and an interior service cavity. That's a nice wall. Do American framers and insulation contractors know how to put that wall together? Not really, but they can learn. There are ways to teach builders what matters, and how not to screw it up. That takes education. You are trying to educate builders; so am I.
I don't think that I have ever bad-mouthed the Swedish wall. There is no need to bad-mouth REMOTE walls.
Exterior insulation makes sheathing warmer and dryer, and makes a wall assembly less risky. And by the way, exterior insulation doesn't have to be foam. It can be mineral wool -- a fact that GBA has highlighted in many articles.
Itchiness
I like working with mineral wool because, unlike fiberglass, it doesn't leave me itchy and scratchy.
Unfortunately, I have been unable to find it since moving to central Florida.
Question
Martin,
If the various wall designs all work if built without defects, why does a wall with exterior insulation make sheathing warmer and dryer, and make the wall assembly less risky?
Response to Ron Keagle
Ron,
Q. "Why does a wall with exterior insulation make sheathing warmer and dryer, and make the wall assembly less risky?"
A. The short answer is "physics."
The longer answer is that the relationship between the temperature of sheathing and its moisture content is a matter of physics, and that researchers have confirmed that sheathing that is protected with exterior insulation (a) stays warmer than sheathing without any exterior insulation and (b) stays dryer than sheathing without any exterior insulation. The method used by the researchers is to insert moisture probes into sheathing and monitor the sheathing moisture content during the winter.
FACTS
I’ve read A LOT of opinions here but little ‘fact’. Is it a ‘fact’ that REMOTE walls with foam are doing fine or, is the fact that they are growing in popularity in the north the “fact” and whether they are ‘doing fine’ or growing in popularity an unknown? If they are doing fine and growing someone please point to the data that shows a life cycle, mean time to failure? Also, please tell me how besides a bunch of hype and theory how I can design a wall and set the dew point to some depth or distance away? Show me air seal data? What thickness what lap joint, what stagger, let’s see some design guides that show the actual dew point location? If this is the answer lest see some ‘facts”? I’m not looking for a bunch of pretty words here and theory, how wood will absorb faster or slower, some code that do not directly apply. I’m looking for some REAL field data or test that shows humidistats and/or other temperature thermocouples, blower door test at build and 30 years later, and a fungi resistance value of foam stacked up in a common wall assemble in all climate zones? I could care less about theory keep it to yourself. I can show that peel and stick at the seams does not have a long thermal life, no adhesive at room temp cure does, try at least 75 psi and 400F clean room cures to get 30 years at best. I’ll give it 10 years at best providing no voids or debri in the bond lines which is VERY unlikely.
Wood is highly unpredictable that is a very well known fact. If someone invented it today it never be approved as a building material. It’s strength properties depend on its orientation, no two pieces are alike, cruelly of all it expands and contracts based on relative humidity, it expands differently based on orientation, when in shrinks it expands, it shrinks and expands along the grain differently than perpendicular, shrinks and expands more at a right angle to the grain than along the grain, studs get shorter or longer, do not get thinner or thicker. It burns, rots, it can’t get worse but, after years of testing and use we understand it to some degree but not entirely. That’s why this industry designs with such high safety margins that fight themselves in weight and dead loads. There are far better material choices, better strength-to-weight ratios, and combinations that work well together, that resist moisture and fungi so get over it.
We know some other facts about manufactured foam, they are Halogenated Flame Retardants (HFRs) - Chlorine and bromine fire retardants(C or BFRs) base produce dioxins, are highly carcinogenic human health hazards when exposed to fire. They are also created in the formulation of PVC and found as chlorinated or brominated fire retardants or (BFRs) to a host of products. There is no required labeling or legislation for quantity of HFRs. OEMs need to be pressured to produce less toxic materials. There are alternative non-flammable materials vs foam and halogen-clad wiring. I’m surprised a ‘green’ site promotes their use. Take a look at what it has done to our ocean and toxic environment. Let’s hope there is ban on its use soon! Don’t use this if you are building air tight, and want a “Indoor Airplus” or pass an IAQ test for Energy Star Certification.
We know some facts about mineral wool, mineral wool forms naturally when strong winds blow through molten lava to create the thin, gold-colored strands that volcanologists call Pele’s hair. Today’s mineral wool insulation is made in a less dramatic process using basalt and iron-ore slag (pre-consumer recycled slag from iron manufacturing) that is melted, spun into fibers, and held together with a phenolic resin. It’s a natural fire resistant. which melts at around 1300°F (704°C). Unfaced mineral wool can withstand temperatures in excess of 2000°F (1093°C) for over five hours with zero smoke developed. Knauf ECOSE technology has Roxul beat since it is formaldehyde free and lower embodied energy.
There is no comparing mineral wool to foam and fiberglass, it wins hands down by material properties not opinion. The Swedish have the answer on configuration, that is a no brainer. If you want some general data look at all the sites with failing western framing and foam on the internet. Many issues with foam, many, many environmental and health related law suits especially lately.
I must say I think Gregory has done a great job here. Even after being referred to as ‘ignorant’ by Marin, & Dana whom ignore his main valid points with a bunch of washed down theory, he held his cool and responded well.
I watched the 4 video series on the Swedish builds, all three walls are better than western. I think we turned for the worse back post industrial revolution when some nit wits decided it was a good idea to integrate studs and utilities with insulation and it has been a failing battle ever since as seen by the ‘ignorant’ trying to make sense and justify a bad design and configuration with foam band aides, simple as the problem is on its face, still some just don’t get it. I think it is great they don’t since it leaves the doors open in this country for the smarter builders to surpass them. Only place for foam is trapped in a sandwich construction where it’s properties can be combined in a monolithic design and toxins or high particles per billion trapped permanently. Even then a bio-based product is better, or better yet a natural product since when it gets down to it you just cannot trust factory manufacturing.
Gregory, the video and pics don’t really detail the lower sill installation well so I will try and get a hold of you. I sent you an email through your site. Thanks, Terry
Response to Terry Lee
Terry,
Like you, many green builders prefer to avoid the use of rigid foam. GBA has solicited articles for years from builders who have installed mineral wool on the exterior of wall sheathing, and have published several articles on the topic, including the following:
Mineral Wool Boardstock Insulation Gains Ground
Installing Mineral Wool Insulation Over Exterior Wall Sheathing
Installing Roxul Mineral Wool on Exterior Walls
Wrapping an Older House with Rock Wool Insulation
You wrote, "I’m looking for some REAL field data or test that shows humidistats and/or other temperature thermocouples, blower door test at build and 30 years later, and a fungi resistance value of foam stacked up in a common wall assemble in all climate zones?"
Like you, I love research -- especially long-term research. In my opinion, there haven't been enough studies of wall durability spanning 30 years. Such research is expensive, but I welcome it. We've done our best to report on relevant research on these issues.
There has been research on air barrier durability by Canadian researchers. GBA has also reported on several studies of sheathing moisture content; see, for example, this article: Monitoring Moisture Levels in Double-Stud Walls. While this article deals with only one type of wall, GBA looks forward to publishing more research results as they become available.
You wrote, "Please tell me how besides a bunch of hype and theory how I can design a wall and set the dew point to some depth or distance away? ...Let’s see some design guides that show the actual dew point location?"
I suggest that you start with these two GBA articles:
Are Dew-Point Calculations Really Necessary?
Calculating the Minimum Thickness of Rigid Foam Sheathing
Cycle Testing
Here is an example of factual test lab data on a seal I am testing that did not make it far. Let's see some similar lab or field data on REMOTE walls? Seals and adhesives any design that relies on them don't last long, better if high pressure and temp and the adhesive is designed for it. You would need to qualify the bond line by ultra-sonic and x-ray test since a void or delamination is an a breading ground for fungui. We do fungi testing too lets see some fungi resistance test of these assemblies too? Say over 30 years?
" Test Facility Comments: Test article started leaking about 68 cycles into the 2nd section of testing at -40 deg. F. Sample leaked about 15 mL in first 10 minutes, then the leakage rate increased to where the leakage had exceeded 75 mL in 20 minutes. See data sheet"
Ventilated Facades
I would agree that rock wool is an excellent product in terms of its relatively high R Value/inch, permeability (30perm for most exterior double density), non-combustibility and hydrophobic nature. One of its limitations in my opinion is that it is difficult to install in commercial construction - i.e. steel stud with glass faced gypsum sheathing. Keeping it in place without horizontal z-girts (thermal bridge) can be tricky and stick pins are unreliable at best. There is also the issue of dealing with the joints b/w the sheets but here in Canada we are seeing several projects calling for 2 layers of 3" staggered on the outside walls. What are your thoughts on this?
Comparing REMOTE wall to other wall types
Martin,
So, when you say that both wall types will work well if properly built, you do not mean that they will perform equally well, but rather both types will meet an acceptable level of performance. However, the REMOTE wall’s performance will be better that the alternative wall because the sheathing will be warmer in the REMOTE wall.
However, if your build the two wall types properly, the non-REMOTE wall will have an effective air barrier on the warm side that will prevent vapor from reaching the cold sheathing. So then why does it matter if the sheathing is colder than it would be in a REMOTE wall?
Response to Ron Keagle
Ron,
You're correct that I believe that both of these types of walls work well. The Swedish wall dries outward, so that if the sheathing takes on moisture during the winter -- and studies lead me to believe that it will -- the moisture dries to the exterior in April and May.
My hope is that those who like the Swedish approach will will continue to build the type of walls they prefer, while those who like the REMOTE approach do so too. My further hope is that we can praise the advantages of the wall systems we like without denigrating other approaches.
Designing to dew point is flawed!!!
Martin, I read a bit of the dew point blog and stopped. It is a waste of my time. I’d like to see one exterior foam case where it was calculated and validated to be accurate? Can you imagine putting this in the hands of the average builder? The theory of “moving the dew point” outward is flawed! Unreliable on its face, especially in the hands of a non-Engineer or professional as Gregory clearly pointed out.
Besides, it’s not the dew point that does damage it is fungi. We test with a series of conditions that vary with pressure, temp, RE humidity, material properties, salt content, dew point is just one parameter.
insulation around stovepipe roof penetration?
Is mineral wool an acceptable insulation to pack around the roof penetration for a woodstove pipe? In my super-insulated house, having a 12"x12" hole to accomodate the stovepipe transition box (from black pipe to double wall insulated) in the foam roof panels with no insulation seems like a big miss. I would like to pack the box with mineral insulation, does that comply with code and common sense safety? thanks in advance for your thoughts!
Response to Charles Young
Charles,
I hope that you are talking about a metal chimney, not a stovepipe. A stovepipe is single-walled; a metal chimney is double-walled.
Building codes and the installation instructions provided by manufacturers of metal chimneys require that there be a minimum air space of 2 inches between a chimney and any combustible materials like framing lumber. This space should not be filled with insulation of any kind.
A question for Gregory La Vardera #37
When making statements such as:
"My contention is that these wall systems will not be built in the ideal context of a test, they will be built in market place by real people, not scientists, and that best laid plans being what they are they will fail. The data supports my assertion that there is a point at which these Remote walls will fail to perform. You may not agree that these conditions will come about, but it is the simply physics of the matter is that this is true. You know this to be true, and continuously stating that the data does not support my opinion is a deliberate misinterpretation, and disingenuous."
...is it too much to ask to actually SEE the data supporting that assertion? I like data- don't tell me, show me.
It's not rocket science (or a building scientist_ to design REMOTE wall stackups that work for any given climate, (and a few weeks of climate perturbations don't make a relevant difference, even when designing at the limits.)
And just as it's possible to screw it up, REMOTE stackups are less sensitive to issues like minor air leaks at the interior side as compared to systems that rely on variable permeance membranes as the interior air barrier. I'd argue that in the real world building with membrane air barriers that leak is also quite likely, but potentially more consequential if there is no insulating sheathing.
And regarding said insulating sheathing:
"The issue here is that rigid foam insulation has been the most common way to do this. The problem, however, is that the foam creates a vapor retarder, and the last thing you want is a wall with a vapor retarder on both faces."
Sure you do, just not an ultra-tight vapor retarder on both faces. OSB sheathing is almost a class-II vapor retarder at about 1-perm, which is part of the the problem- let it run cold and it can adsorb moisture more quickly than it can it can be rid of it on the exterior. And no matter how vapor-open MemBrain etc becomes in the presence of elevated humidity, the 3-5 perm interior latex paint will be limiting factor for drying rates toward the interior. To be sure there is good/better/best approaches to the permeance of the insulating sheathing- rigid rock wool is extremely vapor permeable, but Type-I and Type-II EPS is still at least as permeable as the OSB at R12, which is sufficient for dew point control on 2x6 framing in US climate zone 6, and on 2x4 framing in zones 7 & 8, and would allow the OSB to dry toward the exterior as well as the interior. In very tight homes the interior humidity can easily rise in winter to levels that would make MemBrain vapor open, something that needs to be managed (usually via ventilation) when relying on the smart vapor retarder for protection.
I guess my problem with the blog article has to do with tone- the overstatements & mis-statements of fact.
In the real world the converse of "Most fiberglass batt jobs are sloppy" is not: "Most mineral wool batt jobs are awesome.", so why even go there? There are hacks and pros installing all types of goods, which says little about the nature of the goods.
The statement that " ....fiberglass comes in R-11 or R-13 (although it can be special ordered in R-15 ..." or " fiberglass comes in R-19 (and again, you can special order higher R-value, but only R-21 " is simply not true. Sure- you COULD special order R15 batts, or you can go to ANY of the local box stores or distributors and buy it off the rack- a convenience that has been true in my US climate zone 5 mid-sized city for at least 15-20 years. Unlike rock wool, I can pick up HD fiberglass goods from multiple manufacturers and multiple box stores without having to leave the city limits. (Hopefully the availability of rock wool will improve as anticipated.) While I don't presume my local experience to be universally the case, it's certainly not rare (and easy to verify on box store websites.)
I'm not a fan of fiberglass in general, or HD batts in particular (though I acknowledge how HD batts are an improvement over the lower density goods.) But neither am I a fan of unsupported assertions regarding alternative materials & methods masquerading as facts. If you're going to commit it to writing, it's advisable to have something better than yet more unsupported knocks on competing methods or materials to back it up.
Risk from cold sheathing
Martin,
This gets to a point that we have discussed before. I understand that cold sheathing can hold more water than warm sheathing, and it is better for sheathing to be dry than wet. So one obvious remedy is to keep the sheathing warm, which a REMOTE wall does. However there is another remedy, and that is to deprive the sheathing from a source of water.
I see two different sources of water. One comes from the interior living space and the other comes from the outdoors. A proper air barrier and diffusion limiting will prevent the source of water from the living space. Proper flashing and bulk water barrier will prevent one part of the source of water from the outdoors. So the only source of water that is left is the part of outdoor water that exists as airborne outdoor moisture which will have free access to the sheathing. That component of the overall water source will exist even with perfect workmanship that stops all other water sources.
How much of an issue is that one unstoppable source of outdoor water vapor when it comes to producing the detrimental effects such as disintegration of sheathing and wetting of the insulation? I suspect that the airborne outdoor water vapor is practically irrelevant in causing those ill effects.
Therefore, I conclude that if REMOTE walls and non-REMOTE walls are built properly, there is no difference in riskiness.
DATA VS. REMOTE VS. SWEDISH VS. "GREEN"
Just amazing how people want to debate over a simple concept of less thermal bridges the Swedish Design has on GBA, anyway you look at it less is more regardless of insulation methods.
http://www.cchrc.org/docs/best_practices/REMOTE_Manual.pdf
Take a look at the figures 1-3 REMOTE then look at Swedish, once the REMOTE sealants and adhesives fail, “cutting strips of self-adhering waterproofing membrane that are wide enough to cover the double top plate and extend down both sides of the wall several inches” the air and moisture seal is compromised in time due to thermal cycles. REMOTE looks more labor intensive, especially around doors/windows, with a lot of emphasis on detailing, especially at the raised heal/wall to keep the insulation and vapor retardant continuous and intact for a long life cycle.
When it comes to ‘data’ this industry really has limited: lab test funding, collecting, storage, and a shortage of empirical data that can be used in all climates and configurations to design with. With that said, less labor and relying on skilled labor is better.
Let’s talk “green” Hay bale outer insulation, clay plaster and stucco lime washed, with beam and post let in, local resources, still standing in Nebraska after 100+ years perform better than both, unskilled labor, manufactured on site, builder controlled manufacturing and Quality. :)
Dana, I am just beating a
Dana, I am just beating a dead horse with you, but if you insist..
"...is it too much to ask to actually SEE the data supporting that assertion?"
Must I really present a study to prove a principal of the science you know to be true? With vapor control and insulation to the outside there will always be some point at which interior moisture will cause a problem to the wall. Period. You want me to show you what you already know?
The argument here is the possibility of these conditions emerging. Martin and I have reconciled that this is where we differ, I'm sure we can do the same.
You say:
"And just as it's possible to screw it up, REMOTE stackups are less sensitive to issues like minor air leaks at the interior side as compared to systems that rely on variable permeance membranes as the interior air barrier. "
This is not true because what we have being built and guided to by the code is not a Remote Wall, but what I've been calling a Remote Style wall. There is not nearly the amount of exterior insulation in the assemblies permitted by code to ensure the resilience you attribute to a Remote Wall. This is my point - once the builders of America screw it up as you say, its not going to be less sensitive, certainly not less sensitive than a wall system with a variable permeance membrane.
A wall assembly with a service cavity makes it very easy to have a very airtight assembly. No electrical penetrations, continuous sheet from floor to floor, less taping. Also much harder to screw up.
" And no matter how vapor-open MemBrain etc becomes in the presence of elevated humidity, the 3-5 perm interior latex paint will be limiting factor for drying rates toward the interior. "
No, because the drywall will be full of holes from light switches and outlets, so it does not matter much the perm rating of the latex paint.
"I guess my problem with the blog article has to do with tone- the overstatements & mis-statements of fact."
I don't dispute the tone of this piece - it was written as a rant on my own blog 2 years ago. Martin was interested in it, and I welcomed him republishing it. There may be some blustering, but mis-statment of fact is not true.
"In the real world the converse of "Most fiberglass batt jobs are sloppy" is not: "Most mineral wool batt jobs are awesome.", so why even go there? There are hacks and pros installing all types of goods, which says little about the nature of the goods."
No, this is in fact the most important part of the issue here. Bad craftsman and good craftsman aside, it is easier to do a good job with mineral wool. And that will result in better installations. Wall systems that get the wires out of the cavities will result in better installations no matter exterior foam or not.
At the time I wrote this piece I was still getting push-back from local builders about using R15 or R21 insulation. I was always told, truthful or not, that it was a special order from their supplier. I wrote it as I live it.
And Dana, if you don't like my writing, I invite you to read elsewhere, thanks.
Reply to Gregory La Vardera
Your whole tone of being the One Just Man is silly among fellow professionals. The blog is a polemic which doesn't brook any discussion. If it irritates you when people disagree with you then don't publish on a discussion board, and as a guest don't tell long time regular contributors to go elsewhere.
OK- I'm good with that. ;-) But still...
"And Dana, if you don't like my writing, I invite you to read elsewhere, thanks."
More charm offensive? On a bit o' bloggery that launched with:
"If you think that mineral wool batts are similar enough to fiberglass batts that you already know what you need to know about it, then you are a fool. And you still need to read this."
OK, the history that it start as a rant on your own blog makes the tone SOMEWHAT more comprehensible.
That's not to say that you really have hard data to back up your opinion.
We will simply disagree on the relative resilience of IRC-prescriptive-minimums for exterior-R vs. smart vapor retarders to air tightness error. WUFI simulations of the former do not indicate imminent disaster. Manufacturers of the latter warn against use in higher humidity environments. I trust my physical intuition on this far more than I trust yours (an artifact of having studied physics, I s'pose, not that my work in physics ever had a direct bearing on anything building-science.) When you claim the data supports something, then when I ask to see it you whine " Must I really present a study to prove a principal of the science you know to be true? ". Well, yeah- if you claim there is data, let's see it. To paraphrase recent statements by , David Crane (CEO of NRG, the largest independent power generation company in the US) regarding nukes & coal: I'm not anti-REMOTE, or anti-rock wool, but I am anti-bullshit. (Even when the bullshit is mine. ;-) )
"Bad craftsman and good craftsman aside, it is easier to do a good job with mineral wool."
Anybody who can screw up a "remote-like" assembly can just a easily screw up the air tightness of a membrane, or a rock wool batt job- count on it. The more fool-proof you make something, the more creative the fools become. To claim that installing rock wool is any easier than HD fiberglass is an opinion not universally shared. I personally find HD fg & rock wool fairly comparable on the ease of installation part, neither harder nor easier to get right. Even if perfect on day 1, membrane air tightness in wall assemblies will almost always get compromised in short years, at every picture-hanging or retrofit electrical/plumbing modifications.
"There may be some blustering, but mis-statement of fact is not true."
In my experience the notion that R15s and R21s have to be special ordered is a mis-statement of fact. R15s and R21s are widely available even in a random selections of NJ box stores, spot checked yesterday. Perhaps that wasn't the case 2 years ago when you wrote the initial blog, but sure is now.
Dana, about box store
Dana, about box store insulation.
In the past I have done some small remodels where I priced the fiberglass batt insulation against having the project done for me. The price at the big box was about the same as the installed price. What I am saying is no one should be buying at a store when one can get the same price installed.
Lastly please all of you stick to building.
I believe the discussion to
I believe the discussion to be very good, if we stick to building issues.
One of my concerns with exterior rigid foam is that it raises the sheathing temperature to mold growth temperatures for more time. Cold sheathing stops mold. Warm starts it. Frozen sheathing is not rotting, warm and damp sheathing is. No science behind this just speculating... A theory to be tested.
Fungi
Man, rough crowd out here lets show some LOVE shall we :) I’ve been around this country a lot most of what I see is crappy homes falling apart, very energy inefficient with poor IAQ only getting worse as we build tighter envelopes.
http://www.epa.gov/indoorairplus/pdfs/consumer_brochure.pdf
“EPA studies show that levels of many indoor air pollutants can be two to five times higher than outdoor levels. And since most people spend close to 90% of their time indoors, keeping indoor pollution levels as low as possible is the right thing to do for you and your family. “
From what I read the average home has a 40 year life cycle, less than half pre-industrial revolution. There are earth walls/homes still standing after a millennium. I have to agree with Greg something is wrong in this country and it is up to many of you experienced senior professionals that this generation listens to straighten it out.
The problem with moving moisture or a dew point out to rigid foam insulation sheathing (eg: REMOTE WALL) is it was not designed for that service condition unless it has an anti-fungi or anti micro-phobia additive which most do not, nor is OSB, plywood, etc. The additive only takes care of “most” spores and the products MSDS should still show a “Fungi Resistance” test per standard ASTM, RTCA, or better ISO by a third party.
Owens Corning uses the additive in the inner duct insulation but not their FOAMULAR board.
http://www.foamular.com/assets/0/144/172/174/d21ec081-65c8-417a-bc33-2e630e57e426.pdf
http://en.wikipedia.org/wiki/Natamycin
There are many spores that do not need a lot of moisture or heat to grow and their development and type will be specific to material properties, moisture levels, temp and other environmental factors. Some are exempt from testing since they are known through a series of test to be fungi resistant however, foam is not one unless it is stated in the MSDS. Mineral Wool is hydrophobic tending to repel or fails to mix with water. Water in fact beads up and rolls off the surface of Mineral Wool. This promotes water draining and drying if the wall cavity becomes wet, rather than holding water like a sponge. Clay has the same property and ability to breath moisture up to seven times better than cement stucco. Both have a better chance of warding off fungi especially in the Swedish Platform design.
There are two major fungi in wood, dry or brown rot, that only needs 28-30% relative humidity to initiate an attack.
http://en.wikipedia.org/wiki/Dry_rot
Some of you I see pushing foam when you do not fully understand fungi as evidence by a lack of acknowledgment in your post. Many think they can design to it using ‘perm’ rating’s which is false.
DIY Install experience
My gosh, REMOTE this, swedish that. It's all over my head.
To the couple of folks wondering about DIY and substituting mineral wool for fb batts and install experiences, here's my recent experience with Roxul:
- Much less irritating than fb on the lungs
- Varies by individual in terms of skin irritation
- N95 is adequate whereas I've taken to wearing an N100 if I'm touching old fb
- Installs VERY VERY fast for a DIY. I have no idea how fast a crew can install fb well but I can install Roxul very fast alone.
- A bread knife works fine
- Yes, you have to measure but not like a carpenter. Once you get skilled, you can actually cut to fit without a tape easily. Hold batt one side in the bay, make a small incision mid-way through the next stud, place on the floor and 'saw', inset. Same thing for notches for electrical boxes.
- You do have to learn to make straight cuts without the straight edge. It's not tough.
- I've introduced three laborers to the product: two experienced DIYers, one pro contractor. All of them prefer it and plan to use it. My father took one look at my install and spec'd it to his contractor for his laundry/garage wall reconfiguration.
- I cannot emphasize the difference in sound absorption. I know the A/V soundproofing geeks poo poo MW for fancy stuff like resilient channel and double 5/8" with decoupling glue, but the difference in sound absorption is easily detected by the human ear.
- Mice seem to be just fine with nesting in FB. I don't have empirical evidence yet but they aren't supposed to like MW. Since I know they don't like steel wool, I have hope. If you have an older building in a mouse prone location that you are having trouble sealing, this could be a small but tangible benefit.
- Contrary to what some individual said above, Roxul is awesome for odd spaces. You can make really nice finding truss end blocks etc. To those who find it 'shreds', you are doing it wrong. Cut multiple pieces and squish them together. Don't try to tear and wrap like you do with fb.
Fiberglass board
I am wondering why the fiberglass industry does not make fiberglass board in a density and R-value identical to mineral wool. They do make this type of product, but it seems to be intended for, and only used in industrial applications. How does the price of that industrial fiberglass board compare to mineral wool?
Why does mineral wool have those voids and crevices running through it?
Keith
I agree. The discussion has been muddied by conflating the properties of mineral wool and the Swedish wall assembly, which don't have a lot to do with one another.
Mineral wool is nice to work with and performs very well in sound attenuation assemblies. It works significantly better than fiberglass, but using it or res bars and layers of drywall isn't really the choice as they all perform different functions. Mineral wool is just a better cavity fill.
I've read about rodent's aversion to it here in GBA but unfortunately I've got a mouse nest in an unused batt left in my shop which seems to belie that claim.
Ron
I wonder if it has to do with the hydroscopic characteristics of fiberglass. Roxol's Comfortboard can be left in fairly exposed situations without any damage. Would a similarly dense fiberglass board become a sodden mess?
Fiberglass & Mineral Wool
Aside from the difference in reaction to water, I would think that the two types of insulation could compete with each other on an even basis. For the most part, everyone is trying to keep moisture out of their insulation cavities.
Since mineral wool competes with fiberglass, I wonder why the fiberglass industry does not introduce a fiberglass product that has the same characteristics as mineral wool.
If the two products were priced the same per R-value inch, I am not sure which one I would use.
mineral wool and fiberglass
@Ron Keagle
Fiberglass manufacturers do make higher R-value batts, but they don't offer them in the US. For instance, in 5.5" batts in Canada you can purchase R-24 batts. These are rated by Canadian standards, and might very well be R-25 in the US. You can see this on the Canadian web sites of manufacturers such as Certainteed, Owens Corning, or on the web sites of building supply vendors in Canada.
Its true that fiberglass can be made in these higher R-values, but its not quite right that there is no connection between the properties of mineral wool. The Swedish Platform framing model relies on the fire resistive properties of the insulation to eliminate the need for wood fireblocking. Fiberglass can not stand in for mineral wool in this case, nor can cellulose. Fireblocking would break the wall cavities down into smaller cells adding work to the installation. Fireblocking also adds thermal bridges to the wall assembly compromising performance. So I would say the Swedish techniques and performance advantages are well tied to the material.
Comment #68, Malcolm Taylor
you wrote: I agree. The discussion has been muddied by conflating the properties of mineral wool and the Swedish wall assembly, which don't have a lot to do with one another.
Wrong! First off anytime you put insulation in a wall frame assembly they have EVERYTHING to do with one another. Failure to understand that is one of the underlying reason we have such bad wall assemblies out there such as the REMOTE fungi trap. The Swedish have obviously established a good relationship between mineral wool and their frame configuration. Greg did an excellent job in explaining and you obviously misunderstood.
This is not ‘physics’ 101 either, it is ‘design-build’ where even the build operations and cost is considered and accounted for in the design, again Greg did a good job integrating and explaining in his blog.
Response to Terry Lee
Terry,
I have stated my position on the performance of REMOTE walls already, and I have no intention of responding to every comment posted in this debate. Many of these comments consist of reiterations of strongly held opinions.
Every now and then, however, I feel that GBA readers deserve some balance.
I am confident that there is no evidence to support the idea that REMOTE walls are "bad wall assemblies." Nor am I aware of any reputable building scientist who is has heard of something called "the REMOTE fungi trap."
We have lots of data on actual temperatures and moisture levels in wall sheathing with exterior insulation. The data show that this type of sheathing stays significantly warmer and dryer than sheathing without exterior insulation.
While REMOTE wall studies are limited, they all show that these walls are performing well. Here is a link to one such study: REMOTE wall study.
Response to Martin
Martin, let’s not mistaken a lack of understanding of rot and fungi damage and empirical evidence with “opinion”. This is not a popularity contest by vote of Swedish vs Remote, opinions do not change facts.
The facts are seen by the design there are less Swedish thermal bridges for one, that integrate well to a continuous interior air barrier and uninterrupted insulation's wall/roof planes. It does not take a Manufacturing or Quality Engineer to see that there are less design gaps to qualify and/or seal/insulate with easier access. The Bill of Materials listing of the Swedish design is less meaning there are less assemblies and things to go wrong, more consolidation, equals lower manufacturing cost and higher quality. The Swedish design allows the insulation to diffuse moisture drive to exterior air reducing the risk of growing fungi and rot, not trap it to a material such as foam that is not fungi resistant or proven to be, or, have any manufactured recommended applications as such, as a place to collect dew point as I show in my last response, or where the material property absorption rate (approx. 10%) saturates and promotes fungi growth. It’s pretty simply really, material technology and in service processing.
Here is what I wrote this morning on Allison Bailes attic foam/OSB blog below same lack of understanding.
The core issues causing ‘rot’ here is fungi growth, not moisture, air, and temp. There are a lot of spores out there that need different environment’s/conditions to grow starting with material properties and testing to identify them. Wood only needs low levels and has mainly two spores, some theory claim none for ‘dry rot’. Moist air and permeable materials can transport spores, absorption rate is more of an indicator not perm. MSDS will specify if a fungi resistant additive has been added. Most OSB and oc foam no!.... It was never designed for prolonged potential exposure to moisture absorption or diffusion. Seems to be a large misunderstanding of chemistry and Material Technology design here. WUFI and these other cheap modeling software’s are only as good as the user, trash in trash out.
In a case like this, despite the lack of manufacture fungi and testing I have seen rare, limited, builders and/or scientist go back and tear all the foam out after 10-30 years to be able to say ‘everything is fine’ or establish design guides and/or develop empirical data for good modeling, especially in all climate zones to some file or depository or model? If there is such a database please show me since as I said fungi and rot have A LOT of variables and testing to understanding them is VERY expensive. Some materials are known not be anti-micro-phobic, OSB and foam are not in that category. The material composition varies so much it has to be stated in the MSDS to a third party test and ASTM, RTCA, or ISO.
http://www.energyvanguard.com/blog-building-science-HERS-BPI/bid/75042/Will-Open-Cell-Spray-Foam-Insulation-Really-Rot-Your-Roof
OSB properties
It would be nice to have at least some consensus come out of this.
What would you all think of a concerted effort among the green building and performance building community to call for a change to the properties of OSB? Would everybody agree that an OSB panel that freely transpired moisture would be helpful to all these assemblies? With foam at the exterior this would allow the OSB to dry faster, and in assemblies with interior vapor control it would make more drying potential from the wall cavity. I'm suggesting that the properties of OSB could be made more in line with Plywood.
How could they do that? Different adhesives? Drill small perforations across the entire panel? No, perhaps drilling a pattern of small holes that stop just short of the opposite face - 1/16" of wood instead of the full OSB panel.
Can we brainstorm around this?
Consensus
Let me suggest:
- Mineral wool is an excellent batt insulation but the price difference may mean that depending on the wall assembly being proposed, at present it doesn't always make sense to upgrade from HD fiberglass. A discussion as to the comparative attributes of Mineral Wool and HD cellulose would have been useful.
- There are a number of promising wall assemblies which increase the performance of North American residential buildings. Among them are the Swedish and Remote methods. Each have their merits and deficiencies. There is no clear comprehensive advantage to either of them or over other alternatives.
- There are a number of materials that can be used to sheath the exterior walls, including no sheathing at all. OSB is generally a poor choice, although some manufacturers have higher end versions such as Zip Sheathing which perform very well.
Feel fee to add more.
Response to Malcolm Taylor
Malcolm,
I'm happy to subscribe to your three points of consensus.
osb
I suggest adding boron to osb and plywood in the factory not in the field as deep penetration is difficult to achieve in the field . This will reduce the chance of rot in the sheathing but to the best of my knowledge it will not inhibit the growth of mold.
Add a 1/8'' permeable drainage mat behind the foam such as http://www.mtidry.com/hyperspecs/ . Detail the drainage plane to get bulk water out fast- short runs to dump moisture.
Use a liquid applied wrb to simplify the drainage plane and seal fasteners penetrating the wrb.
OSB and plywood are
OSB and plywood are manufactured by the same hard steel caul plate tooling and processes. High temp adhesive in the range of 200-400 F and 75-150 PSI. A phenolic resign is the moisture retardant and adhesive plus a catalyst, wood filler or veneer. OSB has multi-directional structural properties based on chip size and orientation, plywood extruded grain direction. Plywood generally can take moisture better and is stronger due it’s large lap shear and tension bond lines, it is also manufactured more consistently. You have to go back and seal the edges, if there were holes that were dry or resign shy it would cost a lot to inspect and disposition them. The resign could be stubborn to flow into hole edges and the holes would compromise strength. The trick with both is temp and pressure to avoid de-laminations and voids, or squeeze out of the resign. You can imagine the variations in quality based on the manufactures quality control and understanding of material integration.
The best answer coming to a store near you is graphite in a phenolic resign that is moisture and fungi proof, outer shell of some aircraft like the new Boeing Dreamliner 787 come to mind. Bond some skins to a phenolic or romex honeycomb core and you have a wall assemble you do not play perm and absorption per volume games with based on a lack of understanding of mateing materials and how they behave in relation to one another, that is optimized for weight-to-strength, easy to build on site, semi-monolithic. A scaled down lower cost version is concrete/earth foam core sandwich construction.
Just because something is not clear and you know what you don’t, don’t assume the technology to be better or worse. If you are only looking at initial cost of wool vs HD FG that should tell you don’t know what you are doing. If you want a comparison of HD FG vs Mineral wool for design purposes the ONLY place to get that is the MSDS, not here! How they fit in wall assemblies requires extensive expertise knowledge of a Materials Technology Engineer and field/lab data per climate zone, not opinion or general statements like “Each have their merits and deficiencies. There is no clear comprehensive advantage to either of them or over other alternatives.” The only thing clear about those statements is you can't list the "merits and/or deficiencies" nor understand them. If you think a discussion along this line would be useful then by all means?
The thing I like most about foam and Engineered wood applications in America is my restoration company will be employed for decades taking it down.
Zip has not proven it has not been out long enough.
@ Debra
Debra, you wrote: I suggest adding boron to osb and plywood in the factory not in the field as deep penetration is difficult to achieve in the field . This will reduce the chance of rot in the sheathing but to the best of my knowledge it will not inhibit the growth of mold.
Add a 1/8'' permeable drainage mat behind the foam such ashttp://www.mtidry.com/hyperspecs/ . Detail the drainage plane to get bulk water out fast- short runs to dump moisture.
Use a liquid applied wrb to simplify the drainage plane and seal fasteners penetrating the wrb.
____________________________________________________________________________
Ideal anti-fungi foam or product: Pure synthetic polymers are usually fungus-resistant because they offer no carbon source for growth of fungi. Unfortunately, foams popular in construction, polymer additives such as plasticizers, cellulosics, lubricants, stabilizers, and colorants often permit fungal attack of plastic materials. PVDC contains no plasticizers or other process additives, is inherently very pure, hydrophobic, and resist microbial attack, even under conditions favorable for such attack, namely, temperatures from 35-100F, and relative humidity from 60-100%.
Polyvinylidene fluoride (PVDF) is fungi and fire resistant : http://asia.kynar.com/export/sites/kynar-asia/.content/medias/downloads/literature/fungal-chemical-fire-resistant-pvdf-foams-and-polymers.pdf
Vs,
Polystyrene (EPS, XPS) chemical family or Polyiso HCFC gases. The Bromine “hazardous component” is listed in the MSDS: IE: http://www.insulfoam.com/images/stories/docs/MSDS.pdf
Chlorine and Bromine fire retardants (C or BFR’s) produce dioxins, are highly carcinogenic human health hazards when exposed to fire. Bromine is not an anti-fungi additive.
Boron you mentioned is concentrated on Earth by the water-solubility of its more common naturally occurring compounds, the borate minerals. Boarate a relatively non-toxic natural occurring mineral used for fire, pest, insect, and microbiological resistance (anti-fungi) used in the formation of cellulose is what gives it’s fire resistance, as opposed to halogenated fire retardants. Cellulose has little to no rating on smoke development rating index (SDI) (An ASTM rated test that values amount of smoke). FG=50, spray foams = 300-450, foams are also very flammable once code-mandated fire barriers have been compromised.
http://www.epa.gov/oppad001/reregistration/cca/borates.htm
A drainage plane between foam and OSB would set up a convective loop that will encourage diffusion and evaporation from the surface of the OSB wall further enhancing the drying potential. This cavity does not act as an anti-fungi additive or alter the material properties but, helps prevent fungi from initiating an attack that would be decomposed to air, not another material growth potential by vapor diffusion. If you are in a windy climate zone with high velocity’s of wind heating the boundary layer (OSB, foam) it may keep the dew point off the surface. It would defeat the intent of the REMOTE wall to keep the dew point off sheathing and provide an insulated air sealed envelope, foam dew point collector. Having the drainage plane outboard vs inboard of insulation as shown in the Swedish Platform make more sense.
OSB realities
The only change we need to make to OSB is to stop adding toxic formaldehyde to it. Boron & graphite, really?
If I make a coffee table out of OSB and sit it in the middle of my living room it doesn't grow fungi, rot out or need to transpire moisture. Could we come to consensus on this one, please?
The OSB and stud wall on the interior of a REMOTE wall is essentially the same as that OSB coffee table. It's 100% inside the building, and no water or fungi is acting on it any differently than any other wood object inside the building. 100% of the insulation is on the outside of the OSB, as well as 100% of water and moisture the outside of the house will see.
Why the confusion over this simple concept?
Terry Lee
Strange as it may seem to you I don't employ a Materials Technology Engineer. I instead follow the advice of The CMHC, NRC, Building Science and others who do to try and make informed decisions about how to build.
"You don't know what you are doing"
Any chance you could dial back your rhetoric a bit? The scattergun insults which are being thrown around in this discussion really don't sway anyone's point off view.
Jesse
Exactly. If your wall assembly allows enough moisture to accumulate on the exterior sheathing that it can cause the OSB to rot, the assembly needs modifying, not the sheathing material.
In that regard I'm surprised there isn't a variant on the Swedish framing that places the sheathing on the interior of the 2"x8"s.
Response to Jesse Thompson
Jesse,
Thanks very much. I agree completely with your comments, which are entirely accurate and aligned with the understanding of building scientists.
Your comments should help to clear the air of several obfuscations that are piling up on this page.
Plywood/OSB Manufacturing
I just got off the phone with Georgia Pacific OSB/Plywood lab Engineer. We had a good conversation since we both do the same thing but mine is metal and composites. I'll try and write up the conversation in simple terms over the weekend. I learned a few things about the manufacture of plywood and OSB I did not know.
They do not add a fire retardant btw.
Martin Clearing things up
Why is the wrb between the insulation and the sheathing?
Response to Debra Glauz
Debra,
If you want to build a wall with exterior insulation, you don't have to put the WRB between the insulation and the sheathing if you don't want to.
For more information on this topic, see Where Does the Housewrap Go?
@Jesse & Martin
Jesse said:
"The OSB and stud wall on the interior of a REMOTE wall is essentially the same as that OSB coffee table. It's 100% inside the building, and no water or fungi is acting on it any differently than any other wood object inside the building. 100% of the insulation is on the outside of the OSB, as well as 100% of water and moisture the outside of the house will see."
That would be fine, but that was not the discussion, and is not the practice in the field.
First of all the Remote wall recommendation is 2/3 of your insulation value outside the sheathing, not 100%.
Second, the IRC code allowable exterior foam and elimination of interior vapor control is much less than the 2/3 recommended by Remote wall practices. Depending on the zone this is only a few inches, and perhaps 1/3 of the insulation value depending on what is put into the stud cavity. This is what is happening in the industry, not 100% of insulation outside the studs.
As far as formaldehyde in OSB, true, although I thought we had already started to see OSB made with alternate resins without formaldehyde, no? However I Don't think they are any different terms of passing vapor.
Gregory
Can I ask you about your comparison of Swedish Framing with that of Conventional Construction as it appears to have entered this discussion.
Starting from the bottom:
- Why are both foundations shown as being 12" wide? I understand this is necessary for the Swedish framing but it represents a substantial increase in costs and is almost never done in conventional construction.
- Using two plates in conventional construction is at best a regional practice and not integral to the framing. Should this increase really be counted as an additional thermal break? Should any of the sill plates be counted as they are routinely insulated on the interior?
- You show an open web truss floor system for both examples, but in conventional construction it is a distant third choice to dimensional lumber and I joists. I ask because they both require a rim joist for lateral stability and that doesn't appear possible with the Swedish framing.
- The floor trusses constitute a thermal bridge which you say is mitigated by insulation at the perimeter of the floor. Doesn't conventional construction also include insulation there too? How does this differ?
- What are the logistics of installing a continuous air/vapour barrier on the first floor walls before the second floor framing is complete?
- The conventional wall is shown with two plates at the roof trusses for bearing. You say it can be eliminated using Advanced Framing, but that it isn't practical to do so. How does this same single top plate support the trusses in the Swedish example?
@ Malcolm
I am happy to
@ Malcolm
I am happy to respond and I apologize to others for straying from the topic. I'll be brief but if you contact me directly I'm happy to discuss it more.
- I am going on my own practice here for basement walls of CMU. Any basement deep enough for an 8ft ceiling I always use 12" CMU. My structural engineer concurs. This is somewhat tied to our local soils, but its good practice.
- Two plates is typical of good quality construction in my region which is why I used this as a point of comparison. That said most construction is one sill plate and is not quality construction!
- I think you are right about the popularity of TJIs, although I don't see that much solid wood anymore unless in custom work or additions. Solid wood joists can be notched for a ribbon strip similar to the plate nailed trusses, or you can rely on the first furring strip to tie them back to the studs. TJIs can be stabilized with 1/2" of sheathing rather than a the thickness of a rim joist. Once tied to the wall with the first furring strip they will be stable.
- What I am referring to is about 24" of insulation in the joist space around the exterior. This offsets the tendency of the joists to loose heat through the bearing and through the ribbon strip which both are solidly connected to studs. It prevents the creation of a convective loop off these surfaces in the joist space.
- Installing the vapor control sheet behind the joist bearing requires you to put in place strips of the vapor sheet material while you are framing. Takes some forethought and coordination, but its not difficult. When these walls are built in a Swedish factory on the flat the entire wall is sheeted at once from a roll next to the work station, very rapidly with very easy handling.
- Yes, again I show two plates because this is what is common for Western Platform Framing. It can be much easier to align just your roof members with studs to use one plate even if you elect to not attempt to align everything as in "Advanced" framing. And depending on the spans and loads there may be instances where a single 2x8 top plate is sufficient. The Swedes never add a second plate - when needed the put a second stud oriented vertically, under the plate, notched into the top of the wall. This leaves plenty of insulation inboard, and is much stronger than a conventional double plate. They often have a machine in the factory that does nothing but notch stud ends for this purpose.
So in general Swedish Platform Framing can be and is as diverse as Western Platform Framing. I've just tried to show an example that explains the differences as clearly as I could. But variations are natural and encouraged.
Gregory
Thanks. The Swedish framing is very interesting. My questions are an attempt to clarify what are the essential elements and which are preference, but also how I can integrate some of its best attributes into the way I design and build now.
At first glance the most promising areas for improvement over convention framing are at the two floors. They also represent the biggest problem I can see. We typically pour an 8" concrete foundation wall and it would take a bit of creative manipulation to get both the wall and floor to bear on it. The problem I see with the second floor is that I work in a high seismic area where more restraint of the floor system is probably necessary than is provided by the ledger connection.
Perhaps the solution to both is to attach a rim joist to the interior of the 2"x8" wall and use hangers for the floor joists or TJI's?
All good food for thought. As you say the interesting variations look endless!
@Malcolm
You could do a ledger, or half a ledger with notches on the end of the joists would perform better thermally.
You will have to engage an engineer for a seismic evaluation but my sensibility is that the ledger does not matter much. Having the deck continuous from the joists to the wall is what will tie the assembly together and allow the deck to brace the house. You might want to add metal ties at the bearing of the joist ends to resist being pulled off the ledger.
Foundation-Wall Integration:
Foundation-Wall Integration: The closer the aspect ratio (width-to-height) the better the load transfer, lower buckling. It's simple statics, Pressure = Force/Area. Look what happens to pressure (compression-lbs. /ft2) when area increases, it goes down. Weight increase over a larger area and distributes better. This in part explains why massive 24” walls last for centuries and lite western framing 40 years on average. The way that load gets distributed to soil depends on the Geo mechanical and thermal properties of the soil which can vary by region drastically. Code minimum here is 12” x 24” since our frost lines is 18”. Many do not understand that standard min code has little to do with reacting actual loads that can vary drastically. We have a lot of foundation issues in this country.
If foam were the core with stressed skins such as SIP vs REMOTE outer wall, the skins, as part of this structural system, took a lot of shear load, the ductility of the core would provide shock and vibration resistance to buckling the wall and foundation and/or failing the shear/compression strength of the soil.
Below: The structural issues I have with the Swedish design is the broken sill and lack of continuity to the foundation through the wall studs by way of 2 x 2 sole plates. The structural system is an inner and center sectional, and the two are not tied together via 2 x 2 straps/nails as well as the western design 2x 4’s. Swedish provides a good pre-fabed installation methodology but, can create bending if it sees out of plane loads resulting in a moment from wind or seismic. Anytime you can pass load through solid major structure with less detail parts and/or larger interfaces the joint and moment transfer is better. The western design load transfer is better since the studs and joist are fastened with more contract area, the larger sole plate and sill have a better joint to the joist, and the rim joist further prevents buckling and aids load transfer to the foundation. IF the Swedish inner section, floor joist and panels, transfer load through the anchored 2 x 2 sill and keep it away from the sill-foundation connection, transferring it to the massive foundation is the question. Same applies to the center section and its anchor. I can see increasing the sheathing shear thickness and floor thickness in high wind/seismic loads.
Above” Two upper sole plates are not there for “bearing” area that are there for buckling between stud supports that depends on span width to supports (2/4 studs/plates vs 2x 8 studs/plates) and how much joist live-dead load those spans can take at the studs and between the studs. Notching is not a good idea unless the cross-sectional can still transfer load.
Feel free to check me with your Structural Engineer.
Greg: I’d suggest you refer to contact area when trying to convey thermal bridges since it is part of the heat transfer coefficient for materials in contact. It’s clear if you look at the pictures in that respect.
Malcolm: You seem to struggle with cost. Initial material cost is only part or one color of money. If it takes extensive labor to install a material choice or design it adds to the builders cost. For example, if you are trying to obtain an Energy Star rating, RESNET Grade 1(CL 11 with a continuous air impermeable insulation > R3) requires a uniform fill without substantial gaps, or voids around blocking or bridging, fitted tight around wiring and other utilities, nested to sheathing; Rater checked by probe. It should be clear that labor cost will be lower in a chase and passing inspecting easier without a lot of costly rework and inspections. One might take a look at different types of insulation based on their labor skill set and weigh it into the material acquisition cost.
If the products design requires a lot of future maintenance, it adds to the owners cost which could affect the builders reputation and cost by a reduction of future business. There are other types of money to consider but, I will stop there. I know I will spell out my design-build-maintenance cost selections in detail to my clients to give myself an competitive edge to my competition, no doubt!
Jessie you wrote: The OSB and stud wall on the interior of a REMOTE wall is essentially the same as that OSB coffee table. It's 100% inside the building, and no water or fungi is acting on it any differently than any other wood object inside the building. 100% of the insulation is on the outside of the OSB, as well as 100% of water and moisture the outside of the house will see.
Why the confusion over this simple concept?
If your wall assembly allows enough moisture to accumulate on the exterior sheathing that it can cause the OSB to rot, the assembly needs modifying, not the sheathing material. In that regard I'm surprised there isn't a variant on the Swedish framing that places the sheathing on the interior of the 2"x8"s.
___________________________________________________________________________________
As Greg pointed out there is no way to assure and inspect the dew point location in the REMOTE design. More than likely it resides at the sheathing-foam interface where foam additives that are known to promote fungi residence, and are feed. You correct that fungi concept is very simple and proven, there is no debate.
An example I can think of lately where millions in maintenance cost of corrosion prevention spray of aircraft was reduced by 2/3 (5 year inspection cycle vs 15) by a change to graphite composites vs aluminum. The build cost is drastically reduced to by automated machinery like the Swedish use. There are MANY more examples but I will stop here there is no debate.
Inner sheathing in the Swedish design would be highly ineffective since there is no direct load transfer to the foundation. The 2 x 2 outer non-structural strap they fasten it to needs a rain and pest screen so, it is not that effective either but, takes shear load out and stabilizes the studs from buckling. How effective the wall assemble is at transferring load to the foundation without an anchor is questionable.
The most interesting aspect here to me is going back to nature and getting away from manufacturing processes with material selections causing the least problems (eg: mineral wool, cellulose, borate, pure foam, etc). One thing Georgia Pacific and I agreed on regardless of the “Exposure” rating(i.e.: Class 1, Exterior) these manufacture’s give to their ‘engineered wood’ products they still contain wood that is unpredictable and does not do well when exposed to high humidity and heat. As far as fungi resistance the foams with the additives are more of an issue.
Cutting batts in half (thickness)
In planning to replace our exterior siding I wanted to look into additional insulation while the walls are exposed and realizing that rigid foam might cause problems with the pre-existing vapour barrier I came across this mineral wool info. It sounds like the perfect choice for the exterior, I've seen both the Insulated sheathing board and the comfortbatts for sale here. Originally I was just going to do furring strips and a rainscreen to attach the new cedar siding. My question; is there a problem with cutting the Comfortbatts in half (thickness) and installing them between the furring strips? My main reason for wanting this is price, the sq ft coverage of the Insulated sheathing board is more than three times the cost of the batt approach. Also, the house has 20 year old Tyvek building wrap (WRB) that I was planning on replacing, based on what I've read here it makes the most sense to keep the WRB where it is now against the exterior sheathing or should it go to the outside of the furring strips/mineral wool? FYI it's southern BC, Canada I believe that's a zone 5/6, and the exterior sheathing is OSB. Thanks, great article by the way!
@Hardy
You will have to consult with Roxul to determine the wisdom of using cavity batts as an exterior insulation layer. You seem to acknowledge that the batts are not dense enough to support any weight in this kind of application because you say between the furring strips. That would avoid bearing the fastening of siding on the insulation. But of course that strategy creates more thermal bridges.
I would not slice batts in half thickness because the effort for labor would be ridiculous. Look into their commercial product lines and you'll find you can get thinner batts easily.
And finally, yes - I would keep the WRB at the sheathing.
@Gregory La Vardera
Thanks for the input! I'm sure that Roxul would recommend their Comfortboard Insulation sheathing, that what it's designed for. I'm not too worried about all the effort, I have a summer to accomplish the task and reducing cost is paramount. The siding needs replacement so it's coming off regardless, I was thinking that applying insulation during that time would be ideal. I can either fill the rainscreen voids with insulation or I can leave them open, if it isn't worth the $800 or so in batts then I probably won't do it. Based on some numbers in the Nachi forums the reduced batt thickness would provide somewhere around an R5, would that be beneficial at all? Thanks again!
Availability of Roxul
Gregory & others,
Roxul Comfortbatt ( 3 1/2" & 5 1/2") is readily available in my area (central Texas).
Comfortboard FS or IS is not available here.
I need some 1", 4pcf, board.
What is your opinion of / experience with Thermafiber SAFB? I can get that locally.
In general, for all manufacturers, is there any concern of contaminants from the high percentage use of slag in the manufacture of mineral wool insulation? Like any compounds left over from the steel making process---sulfur or whatever?
Best tool for cutting Roxul Batts
FYI
Buy a 15 dollar black and decker electric serrated knife. Cuts Roxul like butter.
Wool vs Foam - basement insulation
Thanks for your article. There are lots of different and contradicting articles on this website about using wool or roxul to insulate basement walls on this site. It seems to promote using 2" rigid foam against concrete walls, building a frame on the inside of that, and then either filling or leaving the frame open and dry walling.
On the other hand I've seen places and contractors ( my own) recommending using 3" roxul afb pinned directly to the concrete wall, framing directly in front of it, and then drywall with a good primer and paint to act as the vapor barrier. What is your tought on the two scenarios? A company like Dr. Energy proposed the roxul method, and for the unfinished portions of my basement like the mechanical room to just pin the same 3" roxul against the concrete and leave it as is without a barrier or drywall (unconditioned space) I'm totally confused what the right approach is for me? I live in Westchester NY, I don't have any water issues at all, but it does get humid in the summer. My Santa fe dehumidifier does the trick.
The first assertion, that if I don't agree with your thesis I'm a fool, is a sad way to commence a presentation. I immediately scrolled to the bottom to see who butters your bread.
Batt insulation, whether it is derived from glass, rock, cotton, or carbon fibers is only as good as the installation. Roxul batts suffer from the same challenges as fiberglass batts when installed in non-uniform spaces and around plumbing and wiring. Batt installers are in the lowest caste of construction workers and therefore there is high turnover and little skill other than speed. Being fastidious is a liability in this occupation because it only lowers your daily earnings. If you have money you might find boutique batt installers with science degrees who will produce wonderful results.
For 15 years I would come in the day after installers finished the batts and spend four hours checking and remedying bone-headed batt installation mistakes. A dozen ten years ago I switched to blown-in-batt fiberglass insulation in the walls to avoid the zillion voids that batts create.
Boutique batt installers would cost a little less that BIBs but every batt installer you talk to is the best—just ask 'em. I'm weary and wary. I'm jaded. I don't get fooled again. I'm not sold on batts between conventional framing w/o supplementary insulation. I don't believe I'm a fool, but I'm open to argument.
Stephen- you realize this blog piece is more than 5 years old, right?
Gregory La Vardera may have been sorely in need of remedial charm-school (or mayhaps a Dale Carnegie refresher course? :-) ) , but if I had to guess I would assume he won' t be reading this in a timely fashion, if ever.
My old roof needs replaced. It sits above an unfinished, uninsulated second floor with a cathedral ceiling. I want to maintain the cathedral ceiling. Following excellent articles on this website, I planned to remove the current shingles and replace them with an unvented, above-deck rigid insulation assembly. I have stamped engineering plans to reinforce the rafters and footers to deal with the extra roof weight, but I can't find a roofer in Indiana to install such an assembly affordably.* It's 12/12 pitch with many hips, valleys, and dormers, and with a neighboring roof preposterously nearby. The few affordable quotes I have received are from large roofing firms that do not inspire confidence.
As such, I may be stuck dropping my rafters (a combination of 2x6s and 2x4, both true and nominal) to accommodate R-49 worth of insulation below deck. The house is ancient by US standards (150+ years old) so the rafters are something like 19" +/- OC.
Is mineral wool a viable path forward? The fact that it is semi-rigid, but with some give makes me believe I could cut it to size and wedge it between the cathedral rafters such that it would stay unaided; but does compressing it enough to hold at that angle lessen its R-value?
Are there any specific mineral wool products I should consider well suited to a cathedral ceiling? Are there alternatives to mineral wool I should be looking into?
Do you have any recommendations for what the final assembly should look like? I assume the roof will have to be vented, and with a 1 1/2" channel between the mineral wool and the roof decking. Anything in the way of air barrier, etc to include?
We installed R-23 batts in our roof rafters. It was a beast of a job, because our rafter bays are not evenly spaced, and very few are perfectly sized for the standard width of batts (16 on center and 24 on center, if memory serves). We furred out our rafters (which were mostly 2 X 6) just to be able to accomodate R-23. We did not vent our roof, instead paid for foam insulation at the underside of the decking.
If the rafters are long enough, mineral wool will stay up without any wires or drywall holding it up, even on the angles. But what I don't know is whether *two* batts would stay up stacked over each other, because we didn't try that. Some of our batts bow out considerably, so I wonder. I think I did see a video of a guy who put up mineral wool in his barn rafters and layered them, but I think it was a new barn -- he did not have to cut any of the batts to fit the width of the rafters.
It is easy to cut the mineral wool with a bread knife. But with all the angles of rafters meeting each other, sometimes it wasn't easy to cut to fit lengthwise. (And I didn't always cut a perfect line width wise either, but you may be more skilled at DIYing than I am..)
> alternatives to mineral wool
Consider blown in cellulose, especially with unusual rafter spacing. Do use an interior side air barrier.
Log in or create an account to post a comment.
Sign up Log in