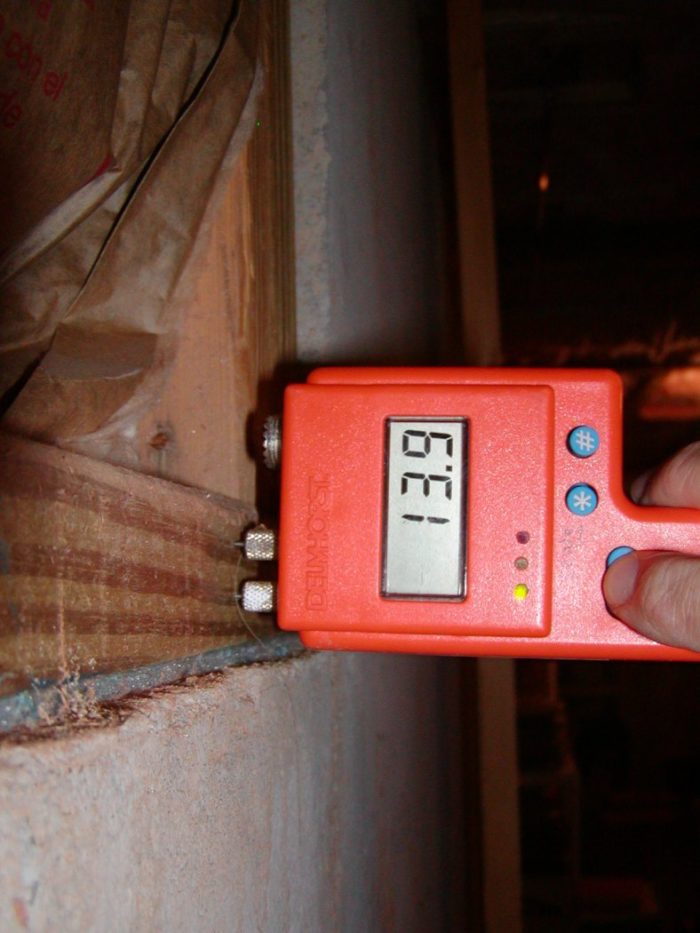
Image Credit: Peter Yost
Code requirements for wood-concrete contact treat the symptoms of rot, not the cause Last week we talked about moisture meters, and I asked readers why the wood in the picture was wet. As it turns out, that photo was taken in the same house on the same day as the two pictures at right. Why is one bottom plate sitting on concrete “dry,” and the other one “wet?” I admit that this week’s top photo was taken in the basement and last week’s and the bottom photo were taken in the crawl space, but the location is not the cause of the different moisture readings. The reason is simple: sill sealer. The light blue sill sealer installed between the bottom plate and concrete (most likely for air sealing) in the top photo is closed-cell foam. It’s meant to be an air-sealing gasket, but it also is working as a capillary break because it keeps water in the concrete from wicking up into the wood. Both wood and concrete wick water well because they are porous materials.
The real problem expressed in these photos: Building codes require wood that comes in contact with concrete to be pressure treated, rather than just saying that wood should not come in to direct contact with concrete. While the pressure-treated bottom plate won’t rot, it is still porous and can’t keep water from wicking through it and up into the end grain of the studs. In last week’s photo, we saw the moisture content at the bottom of the stud (not pressure treated) was above 17%. While we may not care if pressure-treated wood has high moisture content (it won’t rot), we certainly do care about the studs connected to the sill (they can). Pressure-treated bottom plates deal with the symptoms of the problem when a capillary break between wood and concrete deals with the cause. No direct contact, no need for pressure-treated bottom plates. A cautionary note about moisture meters and pressure-treated wood. Moisture meters use the electrical activity of the water in the wood to calculate moisture content. The salts used to treat lumber have a significant effect on this electrical activity; moisture readings for pressure-treated wood tend to run high, so take actual readings with a grain of salt (pardon the pun). The relative difference between the two readings in these two photos — both in pressure treated wood — is still useful. For more information on this effect, see “Effects of Wood Preservatives on Electric Moisture-Meter Readings” from the Forest Products Laboratory.
Weekly Newsletter
Get building science and energy efficiency advice, plus special offers, in your inbox.
9 Comments
Sill-Seal...3 functions
Peter,
Don't you think that the gasket is actually doing 3 good things?
Air sealing, capillary break AND thermal break.
The wood is warmer and therefore drier.
Crawl space photos
Peter,
It looks to me like the crawl space photo was taken in exactly the same location as the crawl space photo in the previous blog...and you say they were taken on the same day...yet very different
readings.
Why so different? What climate is this?
What were the outside conditions?
warmer basement
It also looks like the basement is conditioned or semi-conditioned space(kraft faced batts)....What was the temperature of the basement compared to the crawl space?
Oh I see now
On crawl space photo was taken on the stud and the other was taken on the treated plate...maybe it is the salt.
Pressure treated on concrete slab for an EXTERIOR wall
Hi Folks,
I have a concrete slab on my car port that I want to frame off into a garage. The slab is thin and has a crack from previous settling. I was considering pouring a very small footer on the slab and tying it to the new concrete with all thread bolts and rebar. A fair amount of water runs near this side of the slab and I thought this would get the exterior wall off of the ground to prevent rotting siding, sheathing, and studs. I was advised by a general contractor not to do this because "concrete on concrete is a bad idea."
Now I am considering laying the bottom plate using a 6X6 treated lumber. Would a the method used above (blue sealer beneath treated lumber) work for this purpose? Is this a fairly standard practice? My concerns are 1) avoiding rot or other damage from moisture; 2) complying with Seattle building codes (I know I have to check these out); and 3) not raising eyebrows during a future inspection if we decide to sell the house.
Thanks for your thoughts on this.
Glass fortified wood product
I have come across a product called TimberSIL that is 100% non toxic and is warranted against termites and fungus. It is also ignition resistant. My investigation of the product indicates that the wood fibers are covered in glass. This helps Reduce capillary action, the termites won't eat it and it is incredibly strong. This the only material that I will use in moist to wet locations like bottoms of exterior columns deck ledgers and back basement walls where the permanence of the wall system is low. Has any one else had experiences with TimberSIL in California? I feel like I have discovered gold with TimberSIL.
Treated Lumber in Home
I was planning on building on using treated lumber for support. The CCA-A treated16 foot 4x6 would be covered with drywall. Would there be any danger of fumes or anything else?
TimberSil and dangers of CCA-treated lumber
TimberSil is a great alternative to more traditional wood treatments; it's listed in the GBA Product Guide (https://www.greenbuildingadvisor.com/product-guide/prod/timbersil-nontoxic-pressure-treated-wood) and has been a Top Ten product in BuildingGreen's GreenSpec.It's main challenge is price; it is currently significantly more expensive than other conventional treated wood products.
While CCA-treated wood products contain toxic substances (heavy metals and arsenic), it won't offgas in place. It's mainly the dust and sawdust associated with cutting, planing or sanding. And then disposal issues when its service life is up.
@Peter, thank you for this article. What is the reading on a moisture meter on the wood building materials (studs, bottom plate) that would deem it unfit for closing up and the need for the materials to dry out first? Also, what would you recommend that we can do to avoid mold and mildew growth on our wood studs while framing in this climate zone 2 humid environment (Houston)? One of the things we are going to do is not have lumber deliveries just sit on the dirt and also to cover them with tarp when it rains but allow it to breathe from the sides (so leave sides of tarp open). We are about to do framing and I am cramming for information so we can do this right as we are building to help a family member who needs a fresh start to be able to heal from health issues caused by mold. Thank you so much and appreciate all the knowledge you share in the building community!
Log in or create an account to post a comment.
Sign up Log in