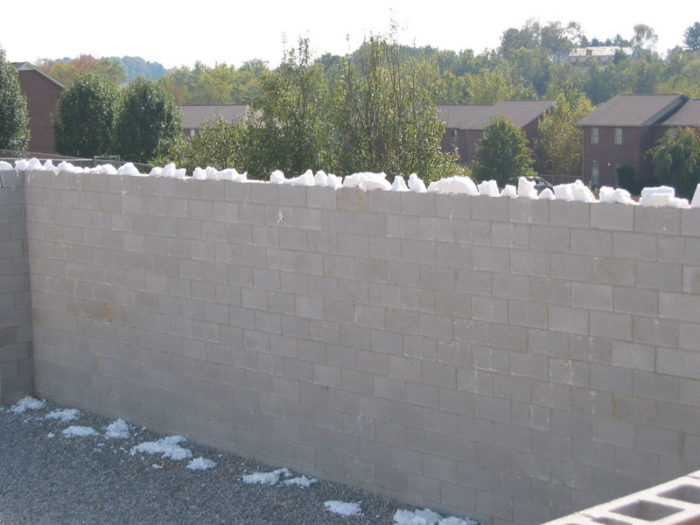
Image Credit: cfiFOAM
In working on a major revision to The BuildingGreen Guide to Insulation Products and Practices (available bundled with a webcast), we’ve had an opportunity to dig into some of the lesser-known insulation materials on the market. Some of what we’re found has been surprising.
Remember urea formaldehyde foam insulation (UFFI)? Back in the late 1970s and early 1980s it was the ultimate bad guy of the insulation world. Installed in hundreds of thousands of homes in the U.S. and Canada following the 1973 energy crisis, UFFI was found in some circumstances to emit high levels of formaldehyde and shrink considerably, resulting in performance problems.
The Canadian government spent millions of dollars insulating 80,000 to 100,000 homes with this insulation, then spent many more millions un-installing it when reports of problems emerged. Canada banned the product, as did the Consumer Products Safety Commission in 1982 in the U.S. — though the U.S. ban was reversed a year later.
The industry largely disappeared. While there had been 39 manufacturers of UFFI in 1977 and upwards of 1,500 installers, there were just a handful by the early ’80s. Most of us pretty much forgot about the product.
UFFI is still around
The UFFI industry shrank to just seven manufacturers by 1981, then two large producers, Borden and Ciba-Geigy, ceased production. But the remaining five companies have continued to produce UFFI, though under different names. Most of those companies have gone to significant effort to avoid any association with UFFI.
Among the five manufacturers of UFFI today, you will variously see the material referred to as “injection foam,” “amino foam,” “aminoplast foam,” “tri-polymer foam,” “dry-resin foam,” and various combinations thereof. The only reference you’re unlikely to see is “urea-formaldehyde,” and if you ask manufacturers what the stuff is most will go to great lengths to obfuscate their response.
Used for insulating concrete-block construction
The primary application for UFFI today is to insulate hollow concrete masonry units (CMUs) or concrete blocks — and I think it is a fairly good solution for such buildings. It can be also used as a retrofit insulation for wood-frame cavity walls, but there are better products for wood-frame construction.
What is it?
To really understand what UFFI is, one may need a degree in polymer chemistry. cfiFOAM, which is the most forthcoming of the manufacturers in production today, describes the material as being “part of the family of amine/furan resins consisting of phenol, urea, and melamine, coupled with an aldehyde.” The company explains in a fact sheet that “amino resins are thermosetting materials produced by reacting amine groups (NH3) with an aldehyde, such as formaldehyde.”
The reaction results in a blend of three different polymers — monomethylol, dimethylol, and trimethylol-substituted urea — which leads one manufacturer, C.P. Chemical, to refer to its insulation as TriPolymer foam. This resin is further reacted with an acid catalyst in a condensation process, and the resultant resin is dried (sometimes in a kiln) to produce a powdered, dry resin that can be stored and easily shipped.
Insulation contractors use specialized equipment to mix the powdered resin with water, surfactant, and catalyst to create the injectable foam. By carefully controlling the mix of these different components, the release of free formaldehyde — one of the main problems in the past — is greatly reduced.
Phosphoric acid is often used in this process, and that chemical imparts some fairly good fire retardant properties. To the best of my knowledge, there are no halogenated flame retardants used in any of the amino foams — which is a significant benefit of the material.
Consistency of shaving cream
Amino foams are fully expanded at the time of installation — unlike polyurethane foams, which expand as they are sprayed into a cavity or onto a surface.
The foams are very flowable, and, according to Bob Sullivan of cfiFOAM, can fill vertically as much as 18 feet, though he cautions that rapid setting can be problematic with rises above 12 feet. The flowability allows the insulation to fill concrete cores very effectively, including around hardened mortar protruding into the cores.
Misleading information on performance
Along with confusing information about what the amino foams are — and their history as UFFI — some manufacturers have made grossly misleading claims about performance. The material insulates to about R-4.6 per inch, which is quite good. You may see claims of performance as high as R-5.1 per inch, but if you read the fine print, you’ll find that the higher performance claim assumes measurement at 25°F instead of the more standard 75°F.
More significantly, you may see exaggerated claims about the resulting R-value of CMU walls insulated with amino foam. Tailored Chemical Products, the manufacturer of Core-Fill 500, continues to claim exaggerated R-values above R-14 for 8-inch CMU walls insulated with the company’s UFFI insulation.
In reality, the R-value of an 8-inch CMU wall insulated with amino foam is highly dependent of the density of the concrete. With very low-density blocks — 85 pounds per cubic foot (pcf) — two-core blocks insulated with this insulation provide a whole-wall R-value of 11.3. With heavier (more dense) concrete blocks the R-values drop. With medium-density blocks (105 pcf) the whole-wall insulating value drops to R-8.2, and with high-density block (125 pcf), the whole-wall R-value drops to R-6.0. The dramatic difference between the R-value of the foam insulation alone and insulated concrete blocks results from thermal bridging through the concrete webs in the blocks.
Formaldehyde offgassing
The major problem that led to the near destruction of the UFFI industry was the fact that the material can offgas formaldehyde. Back in 1982, when the Consumer Products Safety Commission temporarily banned the material, formaldehyde was considered a “probable human carcinogen,” but the hazard warning has been upgraded to “known carcinogen.”
MANUFACTURERS
C.P. Chemical Company (TriPolymer Foam)
www.tripolymer.com
cfiFOAM, Inc. (Core Foam Masonry Insulation, InsulSmart Interior Foam Insulation, and InsulSmart MH)
www.cfifoam.com
PolyMaster Insulating Foams (R-501 and RetroFoam)
www.polymaster.com
Tailored Chemical Products, Inc. (Core-Fill 500)
www.core-fill500.com
Thermal Corporation of America (Thermco Foam)
www.thermcofoam.com
Formaldehyde offgassing continues to be a concern with amino foams, but improvements in the chemistry by all of the manufacturers has significantly reduced offgassing. Amino foam insulation cannot be used in a buildings going through Living Building Challenge certification (because formaldehyde is a “red list” chemical that is banned in such buildings), but for a typical CMU building, the formaldehyde issue is not nearly as significant as it once was.
Shrinkage of foam
More significant than formaldehyde offgassing, I believe, is shrinkage that can occur with amino foams. Typical shrinkage after installation is 0.5%, but in some cases shrinkage can be as much as 2%, or even 4% according to some sources. According to cfiFOAM, the impact of shrinkage is accounted for in the reported whole-wall R-values by at least that company, but it’s still a big concern.
The bottom line
UFFI (a.k.a. injection-installed amino foam) has some quite attractive features, and I believe these to be a fairly good option for concrete masonry construction. Very significantly, it is the only foam-plastic insulation that does not contain halogenated flame retardants. Were it not for the shrinkage and the lack of clear information and transparency by most of the amino foam industry, I would feel even better about it.
— Alex is founder of BuildingGreen, Inc. and executive editor of Environmental Building News. In 2012 he founded the Resilient Design Institute. To keep up with Alex’s latest articles and musings, you can sign up for his Twitter feed.
Weekly Newsletter
Get building science and energy efficiency advice, plus special offers, in your inbox.
6 Comments
Awful
I have pulled it out of several houses. The shrinkage (and crumbling) in all cases was enough that I would guess it was somewhere between useless and counterproductive (in wood frame cavities). And I realize irritation and toxicity are not necessarily related, but each contact left me with a cough and irritated throat that took days to a week to go away.
Like anything there are the good, the bad...
...and downright ugly products & installers. With non-expanding injection foams it's important that it be properly mixed, and applied at the right temperature & pressure, to make sure "non-expanding" doesn't end up meaning "shrinking".
http://www.applegatefoam.com/images/custom/R-Foam-Forensic-4.jpg?&width=640&height=440
http://upload.wikimedia.org/wikipedia/commons/c/c5/Urea-formaldehyde_insulation.jpg
It's pretty easy to spot these defects with IR cameras & blower doors, but fixing them isn't nearly as easy as re-blowing an improperly packed cellulose or fiberglass installation.
In the UK it's becoming popular to fill masonry cavity-walls with the stuff, but the sticky-bead EPS solutions offer a better capillary break, and is probably more forgiving. (SFAIK the sticky-bead EPS isn't available in the US, but it would make a suitable core-fill on CMU walls.)
Isn't there a distinction
Isn't their a distinction between urea formaldehyde and phenol formaldehyde? I thought products like the currently used insulating foams are the latter and are less likely to offgass.
You say "It can be also used as a retrofit insulation for wood-frame cavity walls, but there are better products for wood-frame construction." I'm assuming the better product would be dense packed cellulose? Can you explain why this is a better product. Is dense packed cellulose basically just a lot cheaper and you achieve very similar performance? Would you recommend this product for brick homes?
Bryn,
It's unlikely you will receive an answer. The article is seven years old.
Bryn,
If you need to retrofit some insulation between the studs of an old house with wood-framed walls, then dense-packed cellulose is a better product than UFFI foam for the following reasons:
(a) It has a lower carbon footprint,
(b) Cellulose manufacturers are less likely than UFFI foam manufacturers to make exaggerated R-value claims,
(c) There are fewer off-gassing worries about cellulose than UFFI foam,
(d) If you ever sell the house, cellulose insulation will be less likely to freak out potential buyers than UFFI foam, and
(e) Cellulose is far more available than UFFI foam, meaning you'll have more contractors to choose from and you'll be more likely to get a competitive bid.
Log in or create an account to post a comment.
Sign up Log in