Image Credit: Images #1, 2, and 3: Smith & Vansant Architects
Image Credit: Images #1, 2, and 3: Smith & Vansant Architects Wall envelope detail. The original builders of the 1928 building included two layers of roof sheathing. Each layer of sheathing was protected by a layer of asphalt felt. The two layers of sheathing were separated by a ventilated air gap.
Countless historic masonry buildings dot the American landscape, a large number of them falling under some form of aesthetic scrutiny prohibiting exterior insulation. The only option to make these buildings energy-efficient is to insulate them on the interior.
My company, 475 High Performance Building Supply, works with architects and builders who insulate these types of walls safely from the interior — considering moisture drive, bulk rain water issues, and insulation materials — while avoiding the dangers of freeze-thaw and mold. Using WUFI hygrothermal modeling, we show how effectively Intello, an airtight membrane with variable vapor permeance, provides the necessary drying reserve to keep newly insulated historic structures from falling apart. Using this approach, preservation and high performance can work together for a truly sustainable future.
College campuses have all manner of these types of historic masonry structures, from academic buildings to dormitories. It’s therefore not surprising that campuses have gigantic energy costs. Dartmouth College is one of New Hampshire’s biggest energy users. So there’s plenty of incentive to lower the heating and cooling load of campus buildings (without destroying them in the process).
Insulation on the interior with dense-packed cellulose
Smith & Vansant Architects, based in Norwich, Vermont, was hired to renovate an existing campus structure at 4 North Park Street in Hanover, New Hampshire. Built in 1928 as the Whitaker Apartments, it was designed by Jens Frederick Larson, famous for designing iconic Dartmouth landmarks such as Baker Library and Memorial Stadium. While the $3.6 million renovation pricetag for the LGBTQ living and learning program house could possibly have paid for a brand-new building, the school decided to keep the historic exterior. They also aimed to make it greener — more sustainable, energy efficient and comfortable. (Saving the structure from demolition was in itself one of the greenest strategies of the project!)
Like many building professionals, lead architect John Vansant expressed concerns about applying closed-cell spray foam insulation from the interior to bring the building to higher performance, and was interested in a different approach. Having worked with Dartmouth College on a number of retrofit projects, he invited members of the campus Buildings & Grounds department to attend 475′s “High Performance Historic Masonry Retrofits” presentation. They decided to specify the Intello Plus interior airtight system with dense-packed cellulose for both the existing masonry walls and the roof.
The existing walls were an unconventional hybrid of face brick over hollow terracotta tile (see Image #2 at the bottom of the page). In a case such as this where the moisture risks are even less well understood, Intello provides the drying reserve needed to overcome any unanticipated moisture stress.
For optimal airtight installations, 475 offers a comprehensive eBook guide with detail drawings, 3-D diagrams, and best practice recommendations. The general contractor, Estes & Gallup, did a great job tailoring 475 recommendations to the realities of a project on a tight budget and deadline. The project was a resounding success, and the Dartmouth community celebrated the “Triangle House” opening on Nov. 1, 2014 — delivered on time for the opening of the fall semester.
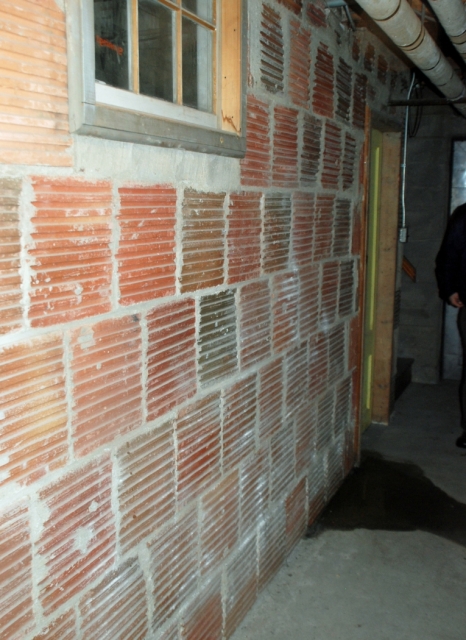
Simple steps to a continuous interior airtight layer
Step 1: The first step in any historic wall retrofit project is to evaluate and address bulk water issues. This includes assessing the quality of the brick, as well as restoring the traditional water shedding details to good working order. Fortunately, the brick exterior of this 86-year-old building was still in very good condition. The interior terracotta was also reasonably “windtight” — helping to ensure that wind-driven moisture would have minimal impact.
Step 2: In preparation for the interior airtight Intello Plus layer, 2×4 furred walls were offset a couple of inches from the masonry.
With no shortage of obstacles — from new and existing structural members to framed interior walls and existing floors — obtaining a perfectly continuous Intello layer was a challenge. (Note: our best practice recommendation is to cut back floors and interior walls to allow for optimal airtight taping and Intello continuity across such areas.)
At below-grade walls, rigid mineral wool board was first added to hedge against bulk water issues.
Then furred 2×4 walls were built over that.
Step 3: Without service cavities (another 475 best practice recommendation), Lessco airtight utility boxes were installed.
The boxes were later taped to the Intello membrane.
Step 4: Intello Plus membrane was stapled and taped with Tescon Vana across the inside face of the studs, with staples aligned vertically to resist tear-out when dense-packing. This differs from traditional installation of InsulWeb netting, which is often inset (lip stitch) stapled to the studs. Staples were also applied horizontally at top and bottom plates. Contega HF solid acrylic caulk was used to connect Intello securely and flexibly to subfloors and other rough/uneven areas for durable airtightness.
Step 5. Intello Plus was folded and taped into window openings with Tescon Profil for full airtight integration. With the airtight layer complete up to the top plates, cellulose was blown through temporary holes that were then patched with acrylic tape. Airtight and foam-free rim joists could have been achieved with a combination of Intello and tape, but due to time constraints closed-cell foam was used in those areas. A very small fraction of the insulation in this retrofit was foam!
A code-compliant vented roof with cellulose and mineral wool
Roof insulation retrofits can be challenging: insulation code requirements, airtightness, vapor control, fire resistance and other needs have to be met. For cathedral roofs that don’t resort to closed cell foam, venting outboard of the roof decking is always desirable. However, in this project there were no plans to touch the existing slate roofing. Fortunately, the designers of the original gambrel roof presented the architects with a gift — in the form of a “double roof” with a vented gap in between (see Image #3 at the bottom of the page). With venting already built in, it would be code compliant to dense pack cellulose in the existing rafter bays. (Note: by keeping moisture levels low, Intello would have been safe to use even without venting.)
As with the walls, Intello Plus provided the airtightness, intelligent vapor control and reinforced membrane for a practical, cost-effective and safe way to insulate the dormitory roof with dense-packed cellulose. An additional layer of Roxul ComfortBoard was added inboard to provide a thermal break along with fire rating for the attic.
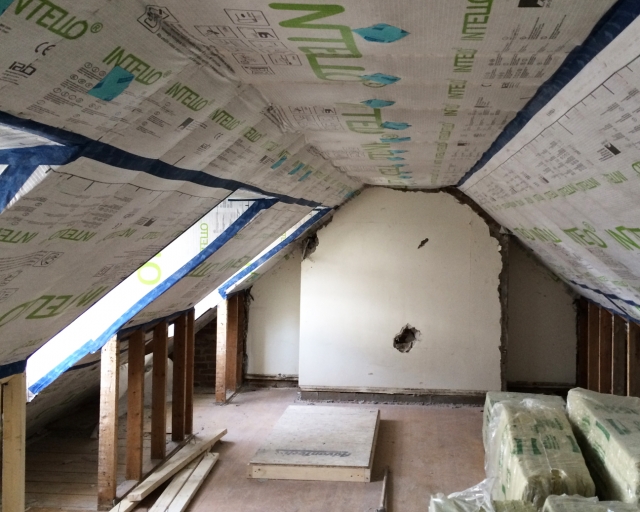
Step 1: After taping/caulking surfaces were swept clean (see “Dust is not airtight, so don’t tape to it“), Intello Plus was stapled to rafters and caulked to the floor, and then the seams were taped. Structural and service penetrations were diligently taped.
Step 2: A number of brick interior and end walls interrupted the roof. Brick work is pretty leaky — the mortar joints are air transfer paths. It has been reported by the Passivhaus Institut that plastering the brick for 3′ 6″ (1 meter) will make the brick/mortar joints sufficiently airtight. There are several options to connect this plaster in an airtight manner to the roof Intello.
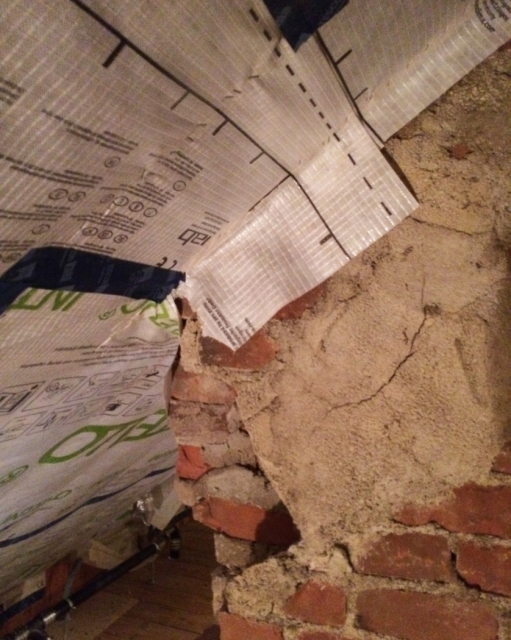
For this project, Intello was taped to the brick with Tescon Vana and Tescon Primer RP.
Then the fleece side of the Vana was plastered over.
Step 3: After dense-packing behind the Intello Plus and taping the blow holes, the slight bulges were rolled flat.
Then the 2-inch-thick rigid mineral wool boards were secured through to the rafters.
Mineral wool boards were also added at end walls.
The renovation work is reversible
While no blower door tests were done to verify the final airtightness, Jon Haehnel from Zero by Degrees issued a comprehensive report of pressurized fog tests. He commented that the “air barrier system is performing well and that there has been careful attention to detail when making transitions in the air barrier”. The architects also praised the foam-free interior, noting that it “felt different” from spray foam projects.
Historic buildings cannot take a pass on addressing climate change mitigation. We can — and should — safely make our historic masonry walls more energy efficient (using WUFI as a guide). And historic roofs can also be brought to high performance — and done reversibly, with sustainable fibrous insulations such as cellulose and mineral wool.
Oliver Klein is the New England product consultant for 475 High Performance Building Supply. He is a LEED AP, Certified Passive House Consultant and registered architect in Massachusetts. Oliver has a Masters degree in Materials Science from Dartmouth College and a Masters in Architecture from Boston Architectural College.
Weekly Newsletter
Get building science and energy efficiency advice, plus special offers, in your inbox.
0 Comments
Log in or create an account to post a comment.
Sign up Log in