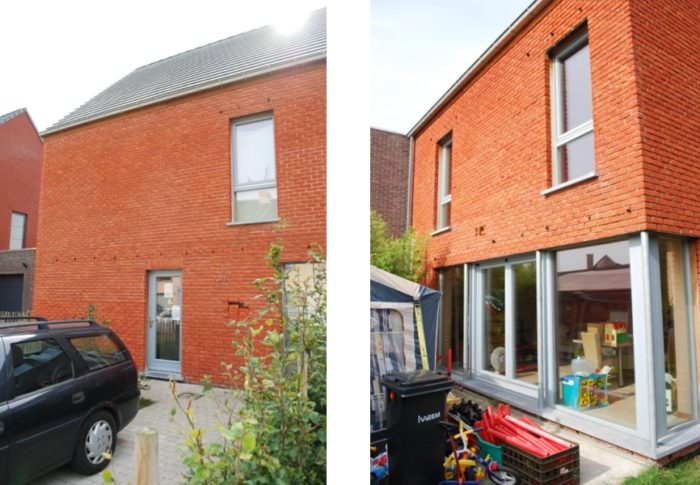
Image Credit: Hugo Hens
The first single-family Passivhaus in the U.S. was completed by Katrin Klingenberg in 2004. Klingenberg’s superinsulated home in Urbana, Illinois includes two unusual features: a ventilation system that pulls fresh outdoor air through a buried earth tube, and walls that include an interior layer of OSB. These details were not invented by Klingenberg; she adopted practices that were commonly used by European Passivhaus builders.
Although many North American designers have copied Klingenberg’s details, earth tubes are beginning to fall out of favor. Yet even in 2012, earth tubes are still being promoted by some Passivhaus builders.
By December 2007, when I first interviewed Dr. Wolfgang Feist, the director of the Passivhaus Institut, Feist was no longer recommending earth tubes. When I asked Feist whether earth tubes in Europe had experienced problems with condensation and mold, he answered, “There were problems in northern Europe, especially in Scandinavia. In Central Europe we haven’t had any hygienic problems so far. Actually, I’m not sure why we don’t have these problems in Central Europe. But I don’t advertise these systems any more, mainly because they are too expensive.”
The classic European wall
European Passivhaus builders (and Klingenberg) favor the use of a superinsulated wall system with three distinguishing characteristics:
- Vapor-permeable exterior sheathing made of fiberboard.
- Thick insulation — usually cellulose or blown-in fiberglass rather than spray foam or rigid foam.
- A layer of OSB on the interior side of the wall to act as an air barrier and vapor retarder.
Many American Passivhaus proponents (including Albert Rooks of Small Planet Workshop) endorse this type of wall assembly. They often claim that such a wall assembly is a better choice than one with thick exterior foam, arguing that it’s best to use vapor-permeable exterior sheathing so that a wall can dry to…
Weekly Newsletter
Get building science and energy efficiency advice, plus special offers, in your inbox.
This article is only available to GBA Prime Members
Sign up for a free trial and get instant access to this article as well as GBA’s complete library of premium articles and construction details.
Start Free TrialAlready a member? Log in
87 Comments
Response to Albert Rooks
Albert,
You're right that vapor-permeable sheathing is common in Europe.
As I've written many times, back in the 1970s, everyone worried about wintertime vapor diffusion from the interior to the exterior; that's why so many builders used to install interior polyethylene. In a way, the use of interior OSB follows a similar philosophy -- the idea being that OSB is a vapor retarder, and that's a good thing on the interior of the wall. (Fortunately, the permeance of OSB is variable, so it's able to act as a smart vapor retarder to some extent.)
Here's the problem with the old 1970s theory, however: there really aren't any diffusion-related disasters due to diffusion of interior moisture outward. On the other hand, there are an increasing number of diffusion-related disasters due to diffusion of exterior moisture inward.
During the summer, vapor-permeable exterior sheathing isn't such a good idea -- especially if you have brick or stucco cladding. That's why rigid exterior foam performs so well behind brick or stucco.
Good Discussion
Martin,
What a catastrophe. I'm glad that you brought this up. We need to have this discussion.
While I can't say anything about the earth tubes since it's out of my area of knowledge, I do feel strongly about permeable assemblies - in the right climate.
I wish we had the details for the rainscreen. This is a real stumbling block here in the US. When we talk about a rainscreen gap, to us 1/2" is a "big one". When you consider the major function in this case of the gap is to vent the driven moisture out of the cavity so it's not driven into the wall. For that reason we recommend a minimum gap of 3/4" with clear vent channels top and bottom. It's still worthy to note that the standard gap used on these applications is 40mm, or 1-5/8". We recommend this, but it's such a leap here to do that on a wall most builders and passive house designers balk at it.
Here we can see a failure of two systems (we think). Bad things happen on all continents.
I don't agree that our methods and habits of exterior foam is the right course. I think it's the wrong course. We've got a lot of "smarts" here in the US who have built permeable assemblies over the years successfully. Doug McEvers is one of them.
When East meets West and we try new things, we are going to have some failures. I'm very dedicated to seeing this through and pushing permeable assemblies here in the US -with the right details. They have a lot to offer. So far we are only talking about firbeboard as sheathing, the next step is low density fibre board that is a high perm sheathing and a thermal break.
Wood is good and these wood based permeable assemblies correctly built (like anything else) will last generations. However, we have no right to skimp on the details and do it wrong. No mater if it's wood, foam or putting away a wet camping tent, moisture is pretty unforgiving.
Btw... Martin. This type of assembly is not unique to passive house. It's the most widely used central european bu ild: OSB on the inside and high perm outside. (Floris K, please feel free to dis-agree if you do, but it sure is what I see most on a wall, but not roof).
Is the "Euro-Wall" really the problem ?
Most of the European walls and roofs that I have observed while websurfing seem to have claddings that are well ventilated.
I think this project may have many issues.
Did the "University Doctors" determine if the health threat was from the OSB off-gasing or from the Mold Spores?
Zero Roof Overhang and The Unshaded Summer Glazing probably didn't help.
Unshaded (high SHGC) glazing overheats living area in summer... OSB and (& plastic toys) cook.
It's warmer inside than outside (UninHabitable)
Air inside becomes less dense (more buoyant) than outside air
Occupants open attic windows...(a path)
The Atmosphere pushes uber air thru the 80% RH Earth Tubes (and mold factory filter).
Response to John Brooks
John,
The "Euro Wall" can certainly work if it is well detailed; however, as I noted in my concluding bullet list, I certainly wouldn't use vapor-permeable sheathing behind brick veneer.
As I noted in my article, many errors contributed to this failure. The fact that the air gap between the brick veneer and the sheathing wasn't ventilated certainly contributed to the problem. (However, it's worth noting that in the U.S., the weep holes at the base of brick veneer walls are often too small to provide an adequate inlet for ventilating air, and many brick veneer installations lack venting at the top.)
And I'm sure you know that it's very difficult for physicians to pinpoint the cause of symptoms like those of the Belgian family discussed in this article. The air in their home had a great many problems, ranging from high humidity to high formaldehyde levels to the presence of mold spores. Suffice it to say that the air was unhealthy.
Finally, you're right that opening second-floor windows could have increased the rate of air flow through the damp earth tubes.
Foam sheathing
In the late 1980's I built a house in the Twin Cities that had 2x6 walls specified and was to be brick on the front and the rest stucco. In my move to make the house more efficient I insisted we use foam exterior sheathing to increase the wall R-value. The stucco contractor installed felt and metal lath, then did the typical 2 coat stucco. This house performed well and adding the foam sheathing probably saved me a big headache. It has been my policy when using a single 2x6 wall to add foam sheathing to increase performance, every once in a while things work out.
This was before the discovery of interior polyethylene, exterior OSB and the disaster with stucco and brick cladding. In a cold, dry climate I do prefer a double wall with a high perm sheathing and rainscreen, sometimes space does not allow it.
Related Article
Another Article related to Inward Solar Vapor Drive
https://www.greenbuildingadvisor.com/blogs/dept/building-science/rain-control-energy-efficient-buildings-building-science-podcast
Response to John Brooks
John,
Thanks for the link. Here's a quote from Joe Lstiburek's podcast:
"So it rains on the brick, the brick gets wet, there is a lot of water stored on the surfaces of the brick. It is not drained because it is stored. It is like a sponge: You fill up the sponge with water, and then, once the sponge is filled, only then if you add more water does water drain out. In other words, if you add water to a brick wall, water doesn’t come out of the bottom; it keeps building up until you can’t store any more water, and then the water drains out. The reservoir is charged. Think of this as a water source.
"Next, the sun comes out and beats down on the brick. What happens to the temperature of the water in the brick when the sun beats down on it? It gets higher. Now there is hot water on the outside of the wall. So moisture flow is going to go from where? Warm to cold. Think of the water as splitting—some of it is going to evaporate to the outside, and some of it is going to evaporate to the inside. The concentration of water in the brick is greater than the concentration of water in the outside air but also the water in the air behind the brick. Moisture is going to go from a higher concentration to a lower concentration."
John, I think I see external
John, I think I see external shades tucked behind the brick, though it's hard to tell from the photos.
Wow. Thoroughly disgusting. Did the article state if the pipes were plastic v. concrete? Was the system designed to drain? Doesn't sound like it.
Two things stand out...
One - 0.68ACH50, paired with insulation voids leads me to believe there were some large quality control issues on site. Construction dust in the ducts would seem to reinforce that.
Two - I've never seen this wall assembly paired w/ a brick fassade. And I read and/or own waaaay too many EU technical manuals.
In Hens previously published papers - it seems his nomenclature when describing PH projects has evolved from 'additional insulation' to 'extreme insulation'. In a fairly recent article, he seemingly slams balanced ventilation because during a blackout, you can't open the windows or else intruders will get in. This seems a rather odd statement to me, as the tilt/turn window allows just that (ventilation without intruders), and is commonplace throughout the EU.
Wow. This is a juicy one,
Wow. This is a juicy one, Martin!
First, a small point - if the air leakage rate you mentioned is correct (0.68 ACH50), then this can’t be a Passivhaus. A Passivhaus would have to be just a little bit tighter.
Next - to my knowledge, earth tubes have never held much favor with North American designers (Passive House designers or otherwise). Specifically regarding Passive House practitioners in North America - in PHIUS’ trainings going back to at least 2009 (PHIUS only started training consultants in 2008) earth tubes were and have since been presented as “risky” and were only to be attempted on consultants‘ own houses, if they felt like taking a chance.
Finally, linking this case with the Zaring Homes debacle is going too far. While it’s always good to remember when and why our buildings fail, the Zaring wall assemblies had three big differences to the Belgian assembly: 1) The Zaring brick was coupled to the fiberboard sheathing. No air gap. 2) The Zaring walls had an interior polyethylene vapor barrier. 3) The Zaring homes were cooled in the summer. 1+2+3 = building failure in lots of climates.
Response to John Semmelhack
John,
Of course their are differences between the Zaring Homes failures and this Belgian failure. Nevertheless, there were major similarities, including brick veneer, vapor-permeable sheathing, and enough inward solar vapor drive to contribute to serious problems leading to the abandonment of the affected homes.
Many North American Passivhaus builders are enamored of earth tubes. Among the Passivhaus projects that have included earth tubes are:
1. Katrin Klingenberg's house (also known as the Smith house);
2. The Waldsee Biohaus in Bemidji, Minn.;
3. Chad Ludeman’s passive house project in Philadelphia;
4. A passive house in Toronto; and
5. Jason Morosko’s passive house in Ohio.
Below are two photos of earth tubes. The top photo shows the earth tubes at Jason Morosko's house, while the bottom photo shows the earth tubes being installed at the Waldsee Biohaus.
If you want to enlarge one of the photos, just click on it.
I'm not overly sensitive
John & Mike,
This isn't an indictment of Passive House. It just one of many building failures. This one just happens to be a Passive House project.
We need to talk about failures in an open conversation. They happen no matter what the design goals are. The future is in High R envelops. No question. As such, we all benefit from a healthy debate and maintain that "fear of failure" in ourselves and the building culture.
To that end, Martin, I'll throw out a couple of points of discussion:
Btw... I'm in the Pacific Northwest. Brick facade is a minority, so I'm leaving that point with your or others experience.
You wrote: "Many American Passivhaus proponents (including Albert Rooks of Small Planet Workshop) endorse this type of wall assembly. They often claim that such a wall performs better than a wall with thick exterior foam, arguing that it’s best to use vapor-permeable exterior sheathing so that a wall can dry to the exterior."
Thanks, I'm happy to be the "poster child" for drying to the exterior in cold climates. Even if I take some "bruises" over it. You wrote" They often claim that such a wall performs better than a wall with thick exterior foam" Maybe it didn't come out as you intended, or maybe I don't express it right, but both you and I know that from the narrow U Value (or factor) point of view: It does not matter if you arrive at that low conductivity by foam or fibre... It's still the same value. So it's not that it will perform better in a cold climate, it's that I think it's a better choice.
I don't want us to build millions of homes with 4" of exterior foam. Frankly, while it may thermally isolate the occupants and not cause health problems, consider that the average US home has around 2500 square feet of wall area. At 6" depth that is 1250 cubic feet of foam per average house. As High R value envelopes exponentially increase over the next 20 years and we get towards a million units... we get 1.25 billion cubic feet of foam. Like nuclear waste, it going to be with us for a while.
I think that's a crazy self destructive idea. I don't even feel the need to go further and explain why I feel that way. However... It's my judgement call based on my personal values, It's not that I'm saying that they perform better, I'm saying it's a more rational environmental choice.
I'm choosing to voice alternatives to wrapping everything in pretty blue, pink, or shiny foil faced foam, As you know, I'm a big fan (as you are too:) ) of exterior mineral wool. But... my personal favorite is wood.
We can build really good high R value assemblies that deal with cold sheathing by drying to the exterior. We can also screw them up just like the unfortunate collisions that come from an inch or two of exterior foam with a layer of Polly behind the drywall in a cold climate. You recall the Q&A case a week or two ago where the Q&A community were advising against a near disaster.
How about that Stucco?
Martin,
Just to lob a little challenge your way :)...
You wrote: "During the summer, vapor-permeable exterior sheathing isn't such a good idea -- especially if you have brick or stucco cladding. That's why rigid exterior foam performs so well behind brick or stucco."
The hard part for me to square with this is: The Swiss, Germans, and Austrians have had such great success with Permeable sheathing topped with stucco. It's the predominant exterior finish. Typically it's on masonry construction, but over the last 20 years, on high perm wood too.
As you know, I import woodfirbe boards from Agepan in Germany. You were there the day my first samples arrived in Olympia:) I've toured job sites, toured the woodfibre plant in Meppen, and I see that they have systems that call for a direct application. They have been doing this long enough that the building are working fine.
Attached is a picture that I took a few weeks ago in Hannover of a Passivhaus, in a 300 unit Passivhaus development in the center of town. I talked to the builder quit a bit. It was tough as his English was not good. The house in the pic with the vertical red detail is: drywall+service cavity+OSB+2x6 (or so) stud cavity+about 8" of high perm wood fibre at around R 3 per inch. Just like the Agepan THD that I stock and bravely promote. The exterior finish is stucco. Blow up the picture and look how big the field is between expansion joints.
I think they've got a system that works. While I don't have it down yet, I'm enough of a stubborn "woodhead" that I'm going to learn it.
It's still early in our small companies experience, so I'm pretty conservative in how we treat the high perm assemblies. As you can see, we have not put up any propaganda on the Agepan wood fibre on our website yet. We will only deal with a specific project, in a specific location until we are a little further down the road with it.
Okay... I guess the only challenge I threw out was to "challenge the limitations" of what some "think" can't be done with wood. Just because we can't today, doesn't mean that we can't tomorrow.
So where is Phillip Gross when you need him!?!
Response to Albert Rooks
Albert,
First of all, thanks for being a good sport about my electing you to be the poster child for vapor-permeable exterior sheathing in the U.S. I'm well aware that my decision to elect you to that position is somewhat unfair.
Also, thanks for suggesting that it would be more accurate to report that you feel that vapor-permeable exterior sheathing "is a better choice" rather than "performs better." I have corrected the text of the article to reflect that point; I'm sorry if I was misrepresenting your position.
And yes, I remember standing with you outside of your garage in Washington as you opened the cardboard boxes containing samples of fiberboard sheathing shipped from Germany. If European-style fiberboard sheathing eventually becomes a common building product in the U.S., I'll be able to say that I was present at the birth of an industry.
Concerning building failures in general: I agree with you. While every building failure is a tragedy for the builder involved, it is an enormous opportunity and gift for the construction community in general. Builders should eagerly study failure stories; they are instructive. They help us all build better buildings.
Dramatic failures regularly occur in foam-sheathed buildings, of course, and also (apparently) in at least a few buildings sheathed with vapor-permeable sheathing. Each example of failure can provide a lesson.
You wrote, "I don't want us to build millions of homes with 4 inches of exterior foam. ... As high R-value envelopes exponentially increase over the next 20 years and we get towards a million units, we get 1.25 billion cubic feet of foam. Like nuclear waste, it going to be with us for a while."
Fair enough. But if your concern (and the concern of many builders who don't like exterior foam) is that foam is environmentally damaging, that doesn't mean we have to switch to vapor-permeable sheathing. We can also choose plywood, which might (for example) perform better than vapor-permeable sheathing behind brick and stucco.
Finally, you raise questions about the use of stucco over vapor-permeable sheathing in Europe. I'd love to know more about the details of these walls. Do European builders include a drainage gap between the stucco and the sheathing, for instance?
I know that in the U.S., tens of thousands of homes with stucco, OSB, and wood framing have experienced dramatic, expensive failures. I have reported extensively on these problems, both in Energy Design Update and in an article on GBA. According to many experts, inward solar vapor drive appears to be one element in these failures. That's enough of a concern that -- speaking personally -- I would never build a house with stucco siding over a wood-based sheathing unless the system included an air gap between the stucco and the sheathing.
Finally, here's a photo I took showing you with your newly delivered samples of vapor-permeable European fiberboard:
Where did the water in the earth tube come from?
This morning I just received an e-mail from Hugo Hens with an answer to my question about where the water in the earth tube came from. He wrote that the water in the earth tube was mainly due to the infiltration of rain water into the pipe, but that it is possible, even in "rainproof pipes, [that] relative humidity might touch such high values during late spring and summer that mold develops."
So -- it was liquid water intrusion. Obviously, the intake pipe did not drain to daylight; nor was there any provision for drainage on the house side of the system.
Ventilation the key problem? / No VB in vapor perm. walls?
Having more than one big problem does make sorting out the effects more difficult, and more difficult to draw conclusions. Obviously, in the Belgian case there are several problems especially the HRV with 'fresh' air from the earth tube and the bricks / poorly vented air gap / osb problems.
Surely the key causes are to due to inadequate ventilation design, both externally and internally, rather than in the use of vapor permeable insulation. Particularly if brick is used as a cladding, but ideally anytime, a very well ventilated air gap behind the cladding is essential, even with foam. Having a drainage plane moisture barrier (taped as an air barrier) to the outside of the fiberboard would also have been a good idea. As for the air from a mouldy earth tube, not good.
Do you think a vapor barrier in a thick, moisture-buffering (cellulose) wall/ wood fiberboard insulated wall is at all a good idea, especially in the non-extreme Belgian climate? How about getting rid of the OSB and using let-in 4x1 diagonal bracing for the racking. Then the wall is highly vapor permeable and breathes inward or outward depending on the season. Good ventilation on both sides takes care of the rest. There could be a vapor check to the inside, more as a second air barrier. Service cavity and breathable finish inside this.
Interested in how you think this plays and how resilient this build-up would be in different climates or with air conditioning?
Ah yes. what about that OSB?
Martin wisely states:
"Even with imperfect knowledge, I’m willing to stick my neck out and offer my own conclusions: - Most walls with vapor-permeable exterior sheathing and interior OSB perform well. However, it’s probably not a good idea to specify OSB with formaldehyde on the interior side of your walls."
I'm not too concerned about our American OSB in this application. They do contain UF along with all of the other engineered wood products (TJI's LVS, etc). These products are exempt from the the current bans on UF.
However, we are not seeing the failures and toxicity even though we have plenty of opportunities to see them besides this interior OSB design.
The concern that the Belgium case has brought up is: Inward solar vapor drive that results in such high humidity that the inner OSB starts reacting and creating these high levels of toxicity. The case is put that the vapor drives through the high perm sheathing and onto the OSB. It's worse than normal because the OSB is on the inside of the air and vapor barrier (pressure boundary). There is no further check for it to infiltrate the inhabited space.
However...
How is that different than an American code wall with a poorly vented reservoir material on the outside? In a code wall, you'd have the same drive hitting the OSB. The inner face of the OSB would off-gass into the stud bays and onto the imperfectly sealed drywall. The toxins would leak past the finish layer into the habitable space, just like it would leak through the smaller service cavity and past the imperfectly sealed finish layer in the diffusion open wall. In both of those cases the drywall is not the airbarrier.
To me it doesn't matter if the OSB is behind a 2.5" service cavity on the inside of a thick diffusion open wall, or on the outside of a 5.5" thick code wall. The point is to not create a situation where the drive wets the OSB. That is done by creating enough venting in the gap to accommodate venting the moisture drive. Theoretically you can place the brick veneer in the application provided the vent channel is big enough. However in practice, the vent channel requirement is not realistic to the realities of building, so no brick no matter whether the OSB is inside or outside.
I'd certainly rather not see any urea formaldehyde in the envelop at all. I was getting ready to check on the Belgium case study because I'm under the impression that these regions have regulated UF our of the products and they are now using PU. At least, the vendor I'm working sells it in Germany as a commodity. We should be demanding our mills to drop UF and supply us with non toxic materials.
When you wet OSB as much as the Belgium case, if it isn't the UF toxicity, it'll be the rot and mold that will make it uninhabitable. UF, or no UF, does not overcome improper layering.
Vent the cladding
I'm not sure if the earth tube will add much humidity in the summer, given that RH already averages over 70 percent outdoors, and the temperature is close to indoor temperature.
I like to check the math on these things, so here goes:
If somehow the house is getting an additional 20% RH at 22C/70F, that's about 22 grains of water per pound of air according to a table I found. Assuming 100 cfm ventilation, that's
(.075 lbs/cf air weight)*(100 cfm ventilation)*(.000143 lb/grain)*(22 grains/cf vapor fraction)*24 hr*60 min. =33.97 lbs/day H20 added to the air. That's either a very leaky pipe, or the vapor is coming from somewhere else.
For the vapor drive issue, isn't venting the cladding the most immediate solution?
USB as a vapour barrier
Interesting thread this thus far.
I work with German made wood-fibre products here in Ireland and the general consensus now is that OSB, even 18 mm ( almost 3/4") thick graded as exposure class 1 cannot be relied on as a reliable vapour barrier. Tests have shown that even within the same batch there is a hugh variability in permeability levels.
If the budget will take it then I use an intelligent membrane over the inner face of the OSB, else use a more normal VB.
Unless the OSB is required for racking then 1/2' can be used which reduces the cost somewhat.
In the case under review, the lack of ventilation in the cavity behind the brick facing did'nt help.
What is not clear is if there were any fixings from the brick through the external sheathing to the timber frame.
stucco over wood fiber
Martin,
In every holzfaser system i've seen, there is no gap for the stucco. they're all similar to this:
http://lh6.ggpht.com/-e_KEuOD8uX0/TslQaQFDsDI/AAAAAAAAlj0/pLGzECTwYGU/3-INTHERMO_Holzfaser-WDVS_mit_Putzsystem.JPG
i think it's a separating layer/reinforcing mesh, followed by a 2 part, diffusion-open stucco system.
Response to Paul Price
Paul,
You wrote, "Surely the key causes are to due to inadequate ventilation design, both externally and internally, rather than in the use of vapor permeable insulation."
I don't think so -- at least concerning the lack of ventilation of the gap between the brick veneer and the exterior sheathing. After all, most U.S. brick veneer installations are very poorly ventilated, and yet most such installations don't result in failures due to inward solar vapor drive. That's because OSB and plywood are vapor retarders -- unlike fiberboard sheathing. Foam sheathing is better still.
You asked, "Do you think a vapor barrier in a thick, moisture-buffering (cellulose) wall/ wood fiberboard insulated wall is at all a good idea, especially in the non-extreme Belgian climate?" Vapor barriers are generally not problematic if they are integral with an insulation product that has a high enough R-value to keep the cold side of the insulation above the dew point. Vapor barriers are only a problem when they have no R-value. In other words, thick rigid foam won't cause problems, but polyethylene often does.
You are certainly right that the bad design and installation of the mechanical ventilation system (the HRV system) played a decisive role in this failure.
European Stucco
I believe they typically use a mineral silicate paint over stucco in Europe. This is a breathable, integrated weather barrier that lasts a long time. Maybe that helps. The homes in Albert Rooks photo also have decent roof overhangs. I would certainly call for a properly installed, vented rain screen no matter what.
Response to Albert Rooks
Albert,
You wrote, "How is that [the Belgian case] different than an American code wall with a poorly vented reservoir material on the outside? In a code wall, you'd have the same drive hitting the OSB. The inner face of the OSB would off-gas into the stud bays and onto the imperfectly sealed drywall. "
There are two important differences:
1. In the U.S. case, there is an intervening layer of insulation -- ideally, 5.5 inches or more of cellulose (although more typically fiberglass) -- between the OSB and the interior drywall.
2. In the U.S. case, the damp OSB dries to the exterior. In the Belgian case, the OSB dried to the interior (meaning that evaporation was occurring -- including the evaporation of the formaldehyde -- on the interior side of the wall).
Response to Kendall Willets
Kendall,
You wrote, "I'm not sure if the earth tube will add much humidity in the summer, given that RH already averages over 70 percent outdoors, and the temperature is close to indoor temperature. "
I haven't reviewed your math, but intuitively, it can't be a good idea to pull your fresh ventilation air through a duct with standing water in it.
You wrote, "For the vapor drive issue, isn't venting the cladding the most immediate solution?"
It would certainly help -- although job-site conditions often conspire to keep the weep holes at the base of brick veneer walls small. Moreover, masons often clog air gaps with mortar droppings, and masons have been known to screw up the ventilation at the top of a wall. These details require supervision and inspection, which adds cost to the job.
So, I'm not sure that ventilation is "the most immediate solution," since a layer of rigid foam is easier and (because it requires less supervision and inspection) probably cheaper.
Response to Colm O hAonghusa
Colm,
You seem to be concerned about the fact that when OSB is used as an interior vapor "barrier" (I would probably use the phrase "vapor retarder" here), it doesn't stop the vapor well enough. You think that an additional product is needed to be sure that the OSB is better at resisting vapor flow.
But I don't think that there is any evidence that the house in Belgium needed a better INTERIOR vapor retarder. What this house needed was a better EXTERIOR vapor retarder.
Response to Mike Eliason
Mike,
Thanks for the link to the photo.
To GBA readers who (like me) were momentarily puzzled by Mike's German vocabulary, "holzfaser" means wood fiber. Mike is referring to European systems that use stucco applied on top of vapor-permeable sheathing.
It's interesting that there is no gap. I wonder if any research labs have tested these systems for inward solar vapor drive.
Response to Steven Konstantino
Steven,
It's possible that, as you suggest, the paint is protecting these European walls. But if your guess is correct, that means that failure of the paint could be enough to change the performance of the wall and put the wall at risk.
I certainly wouldn't want to select a wall system that depended on the integrity of a layer of exterior paint to keep moisture out of the wall.
OSB and European external render systems
The tests on the OSB to which I refer were to tape a a layer of a barrier on the inner face of the OSB and then apply the blower test with negative pressure. The layer bubbled as soon as there was a very small negative pressure. This to me is an air barrier failure.
This would suggest that in the case under review, the lack of air resistance on the inner face, ie the OSB meant that the solar vapor pressure build up had somewhere to go, line of least resistance so to speak.
The European renders on the external wood fibre materials, typically used in EWI projects, differ from a brick layer in so far as they dont have the mass or the specific heat capacity to heat up in such a concentrated way as brick. Neither do they aborb as much water in such a concentrated area.
They are, by design, water resistant but vapour permeable and work well in tandem with the natural materials used as insulation.
I cannot comment on the performance of foam/PU/PI/etc rigid insulation behind European type EWI renders. There is a lot of it being used in retro work for the housing stock in UK and Ireland but I think the jury is still out on the longer term performance issues
I cannot comment on the paint issue and its role in the EWI buildup, in any projects I have done the colour is in the render and no further painting is required. However it does point to the need to tell the home owner that if painting, it needs to be chosen carefully.
Micky mouse weep holes are never going to perform. Just consider the code requirements for ventilated eaves...
Response to Colm O hAonghusa
Colm,
I was confused when you wrote (in your first post) that "OSB, even 18 mm ( almost 3/4") thick graded as exposure class 1 cannot be relied on as a reliable vapour barrier." The statement in your second post -- referring to "an air barrier failure" -- makes more sense. It sounds like the OSB needed better tape at the seams.
You wrote, "Mickey Mouse weep holes are never going to perform." Depending on your definition of "Mickey Mouse" -- not a technical term as far as I know -- I disagree. Properly detailed brick veneer installations can work well. The weep holes don't necessarily need to allow for significant ventilation -- although it wouldn't hurt, of course, if they did -- but they do need the following characteristics:
1. They need to be above grade.
2. They need to be integrated with durable flashing at the bottom of the air gap, and the flashing needs to be integrated with the WRB.
3. The flashing needs to extend to the exterior. In other words, the lip of the flashing should be visible below the weep holes.
4. The air gap above the weep holes must not be clogged with mortar.
Such systems work quite well -- especially if the brick veneer is installed on a building with exterior rigid foam sheathing.
OSB
Rooks and all
OSB is inexpensive and that is why it is used. But it when subjected to moisture can be the most expensive mistake in picking a sheathing material to utilize. It is not my favorite material.
QAQC is critical to success
...with skillful design by a trained professional, a pre-certification design check and rigorous PH specialized onsite third party QAQC (such as in PHIUS+ RESNET QAQC) the problems that led to the downfall of the Belgian project would have all been caught during construction. Without rigorous quality assurance we might see failures of this kind here in the not too distant future also.
... 10 years later, the 8 projects in Urbana are doing exceptionally well, with and without earth tube! John is correct, we have never promoted earth tubes as PH solutions in NA, only for those who know how to handle them correctly. They can be an appropriate choice. All depends.
Response to Katrin Klingnberg
Katrin,
I agree with both your points. Clearly, the construction quality on this job in Belgium left a lot to be desired, and no one was looking over the builder's shoulder.
And it's good to hear that the homes in Urbana are doing well.
Response to Martin re: Response to Colm O hAonghusa
Martin,
I'm pretty sure that Colm was describing a different test:
"The tests on the OSB to which I refer were to tape a a layer of a barrier on the inner face of the OSB and then apply the blower test with negative pressure. The layer bubbled as soon as there was a very small negative pressure."
Meaning that he was testing the OSB itself for air leakage. Place the AB at center of the OSB barrier, de-pressurize the envelop and watch for air passing through the OSB at panel center, not the taped seams.
This is not the first European builder that I've had discussions with that has tested the air leakage of OSB. It's seems like it becomes more common as builders work below 1 ACH50 as a matter of practice. -When you work on the "frontier" of building, you meet the darndest people...
Response to Albert Rooks
Albert,
If I understand the test correctly, there is an installed piece of OSB on the interior side of a wall. Let's assume that the OSB measures 4 feet by 8 feet. Then a builder tapes a piece of membrane to the center of the OSB; this membrane measures less than 4 feet by 8 feet. Let's assume it measures 2 feet by 3 feet.
After the membrane is taped in the center of the OSB, the house is depressurized. The builder observes a bubble of air that appears between the OSB and the membrane. Do I have it right?
If that's what's going on, why do you conclude that the air is leaking through the OSB? It seems far more likely to me that the air is leaking through the taped seams (that is, the tape used at the perimeter of the membrane).
Response to Martin Holladay
Martin,
Re:
"There are two important differences:
1. In the U.S. case, there is an intervening layer of insulation -- ideally, 5.5 inches or more of cellulose (although more typically fiberglass) -- between the OSB and the interior drywall.
2. In the U.S. case, the damp OSB dries to the exterior. In the Belgian case, the OSB dried to the interior (meaning that evaporation was occurring -- including the evaporation of the formaldehyde -- on the interior side of the wall)."
To try and be a little more detailed in my example:
1. In the U.S. case, there is an intervening layer of insulation -- ideally, 5.5 inches or more of cellulose (although more typically fiberglass) -- between the OSB and the interior drywall. [AR]: For my example, lets make it a code minimum wall which to me means it's probably a fiberglass batt (and not perfectly installed).
2. In the U.S. case, the damp OSB dries to the exterior. In the Belgian case, the OSB dried to the interior (meaning that evaporation was occurring -- including the evaporation of the formaldehyde -- on the interior side of the wall)." [AR in both cases the brick was not properly installed. That means that the US case cannot dry to the exterior. Solar Vapor Drive floods the system and it forces the same toxic behavior that can only seek balance to the interior. The batt insulation and drywall would not put up much resistance to the OSB drying and off-gassing to the habitable space, much like a lesser depth service cavity + drywall appears to have "passed gas" in Belgium.
I was only trying to suggest that the OSB's reaction to an improperly vented brick veneer would be similar regardless of it being "diffusion open to the exterior in Belgium", or an "American code wall in Minnesota". In both cases, the OSB is flooded with high humidity and must release the humidity, along with the toxins, to the interior as the system tries to balance itself.
My point was that in an extreme failure like this, the added 3" in cavity depth and batt insulation of the US wall would not be much resistance. The interior space would be equality uninhabitable.
The take away is that interior OSB is no more dangerous than exterior OSB to the effects of an unvented solar vapor drive.
Response to Martin Holladay
OK, maybe it's me who is misunderstanding... - Not you!
You've got the test right as I was describing it. As far as the why's, I don't know. I've only heard about these tests and have never done one.
Now... I have to try it :)
I can take care of the edge issue by priming the tape with SIGA Dockskin. OSB + Dockskin + 1" of tape. That will create a perfect air seal. The remaining 1" of the 2" wide tape is on the membrane or poly. Darn I just missed a blower door test last week. I'll have to wait for the next project where we can replace a door with an OSB panel.
Recently, Dr. Joe made this
Recently, Dr. Joe made this statement regarding formaldehyde and ventilation rates...
"What’s amazing is formaldehyde in houses doesn’t respond to ventilation rate changes. So if you’re ventilating at 0.1 versus 0.2 versus 0.3, the formaldehyde concentration remains constant. The reason is the more you ventilate the more it emits. You ventilate less it emits less. Don’t put it in the building, that’s a phenomenally successful way of dealing with the problem."
So wouldn't this be an issue that's beyond whatever convoluted QAQC program anyone wishes to develop?
Regarding the leakiness of OSB - this came up on a couple of EU discussion boards lately, as well as a linkedin group. There was also a report titled, "Air Permeability Requirements for Air Barrier Materials in Passive Houses" that discussed the wide variability in leakiness through OSB. How's your Flemish?
http://www.ecobati.be/nl/producten/afwerkings-panelen/osb-plaat/het-afdichten-van-de-osb.html
http://www.boomerbvba.be/index.php/nieuws/luchtdichtheid_in_passieve_en_laag-energie-gebouwen/
I've seen some speculation that the EU OSB is leakier due to composition (less formaldehyde/more wax?) but I haven't seen anything remotely conclusive.
Response to Mike Eliason
Mike,
My Flemish is weak. My family lived in Holland for three years (1955-1958), but I since I was born in 1955, I don't really remember my time there ... or the Dutch I learned as a toddler.
There's always Google Translate: "[We] checked with manufacturers [who] taught us that some people claim that their [OSB] panels [are] airtight and they have never received any complaints regarding such a phenomenon. Others admit that their OSB panels are indeed not completely airtight."
[Later edit: Here is a link to the paper in English: "Air permeability requirements for air barrier materials in passive houses."]
OSB inside vs. outside
In a summer vapor drive scenario, wouldn't exterior OSB be warm, nearly the temperature of the brick veneer (or the cavity air anyway)? Therefore well above the dew point?
OSB on the interior side of the insulation, on the other hand, will be much cooler, often below the dew point behind the solar-heated, rain-saturated veneer. (Particularly if air conditioning is in use.)
The one time I saw this in real life, the exterior OSB sheathing looked and measured dry, with no biological growth; but the interior drywall was saturated and moldy.
Also, Martin I think there would be no pressure difference between the back of the OSB and the plastic in this test scenario, so no reason for air to enter through the tape. For depressurizing the house to push the plastic toward the interior, there must be connections through the OSB to the outside.
While I haven't seen much about this issue in North America, I did hear about a house where the air leakage went up after the roofers nailed down the shingles. The contractor believes it was all the little holes!
earth tubes and K Klingenberg
For the record. I took the PHIUS Passive House training summer of 2009 at Parsons in NYC and Katrin did not encourage eath tubes. She was quite clear that earth tubes were not appropriate for most US climates, and required maintenance similar to a "pet", her dry humor for discuraging their use.
Response to Laura Blau
Laura,
I'm glad to hear that there is a general consensus on the fact that earth tubes are usually ill-advised. It's too bad that the Belgian designer and builder didn't get good advice before they finalized their plans.
Response to Mike Eliason
Mike,
Regarding quality assurance and quality control - why would the elimination of urea-formaldehyde in certain materials be beyond the potential scope of a QAQC program (internal or 3rd-party)? It seems to me that eliminating the source of the problem would be something a project team would wish to assure.
Unbuilt houses often work well
Martin said, "If only Zaring Homes had specified rigid foam sheathing instead of fiberboard sheathing, these walls would have been fine." It's easy to claim great performance in a house that was never built. This kind of "spec" housing always performs well. But in an article focused on real, as-built houses, and their problems, I think it out of place to offer such predictions of how a group of homes would have performed with one change. It's misleading at best to compare a possible design change of one wall-assembly element to complex in-the-field failures of the Belgian house. After all, just like your hypothetical modified Zaring Homes, the Belgian house performed perfectly, up until construction began.
I have a similar objection to the statement, "Vapor barriers are only a problem when they have no R-value." This is an overly broad assertion, to which many counter-examples have been described in actually built houses using foam. I'm not saying that foam was the sole source of the problems, just that having an R-value in your vapor barrier doesn't guarantee anything.
Brick airgap with (now) unvented attic
Hi, I live in a 1953 house outside of Washington DC with exterior walls of the following construction and zero roof overhang:
Brick
airgap
cinderblock
fiberglass batts
drywall/plaster/wood paneling (depending on the room)
We recently insulated the roof with 3.5" of CC polyurethane spray foam because the attic had too many protrusions to seal tightly and the duct work is all exposed there as well. My concern is that by retrro-fitting an unvented attic, there is now no place for the brick-to-block-to-drywall cavity(s) to vent their moisture trappings to.
We have been monitoring the attic temp and humidity levels and have thus far seen nothing out of the ordinary but wonder if we should do some forced ventilation or dehumidification as a precautionary measure?
Response to Martin comment #33
Martin said, "It seems far more likely to me that the air is leaking through the taped seams (that is, the tape used at the perimeter of the membrane)."
It seems to me that Martin's explanation means that air is leaking from the reduced pressure airspace in the room to the increased pressure airspace between the membrane and the OSB. Leaks in the tape could neither create nor maintain airflow from low pressure to high.
Response to Derek Roff's comments on Zaring Homes
Derek,
I'm not sure why you are scoffing at my suggested change to the sheathing that was used in the failed Zaring Homes. According to many building experts who looked into this disaster, the cause was clearly inward solar vapor drive from the damp bricks through the fiberboard sheathing that led to the moisture entering the wall cavity. Clearly the fiberboard sheathing was the weak link in the system. Of course, you could change other aspects of the wall assembly if you preferred -- for example, substituting vinyl siding for brick veneer would also have prevented problems.
The other sentence you object to -- "Vapor barriers are only a problem when they have no R-value" -- was stated in the context of a longer paragraph. If a vapor barrier has a high enough R-value to keep the cold side of the material above the dew point, you're not going to get condensation. As long as a wall assembly can dry in either direction from such a vapor barrier, the wall will perform well. This is in stark contrast to a vapor barrier like polyethylene, which has no R-value and can lead to all kinds of problems.
Response to Josh Wimpey
Josh,
You don't have to worry about the performance of your wall assembly. Brick veneer over a concrete-masonry unit wall is a very robust system. Especially since you note that you "have seen nothing out of the ordinary," I don't think you have any reason to worry.
Response to Derek Roff's comment about leaks through tape
Derek,
I'll admit that I don't know what's going on with the OSB air leakage test that Albert Rooks described. All I know is that I find it hard to imagine that much air leaks through the field of an OSB panel.
Importance of vapor-permeability, Sydney Australia
A very informative post. Here in Sydney Australia we enjoy a warm temperate climate, build in brick-veneer and have only in the last few years started to require insulation in walls and, as a result, experience condensation problems.
Typical wall construction - inside to outside: drywall + 2x4 studs (now with 3 inches fibreglass batts) + building wrap + 2 inch cavity + brick veneer. The building wrap has typically been vapor impermeable but the emergence of winter condensation problems in houses built in the last few years has led to recommendations for permeable building wrap and the installation of impermeable membranes such as polythene or aluminium foil on the interior side.
Since Sydney has warm summers (warmer than LA) and summer rainstorms and air conditioning is the norm, I'm wondering if solar vapor drive could become a problem. I note that the first Passivhaus now being built in Auckland New Zealand - which has a similar climate to Sydney - is using a variable permeability air tightness system (Pro Clima Intello) at the interior. Does anyone have any experience with such products?
Thanks also for bringing up the issue of earth tubes. There has been some experimentation here with them but not enough discussion about the possible health issues.
More information from Hugo Hens
A few days ago, I sent an e-mail to Hugo Hens asking whether this wall assembly included a water-resistant barrier (WRB) like Tyvek or asphalt felt on the exterior side of the fiberboard sheathing.
The answer was surprising, to say the least: there is no WRB at all -- no membrane to address liquid water that gets past the brick veneer.
In other words, this house had a whole basket of problems.
HRV intake
At the risk of getting completely buried under a long thread...
.
In various thinking about my own pending retrofit and HRV
installation, it's occurred to me that the fresh-air intake
of one that isn't an ERV should have a humidity sensor in the
stream, so that if it's about to shovel stupidly humid air into
the building it can either shut down, or go to a really
minimal flow rate -- something that the HVAC will be able
to easily deal with, rather than forcing it to handle extra
latent load. Once my system is installed I might experiment
with this. Such a rig might have saved the earth-tube situation,
or at least alerted someone that the air from them wasn't
acceptable to bring inside.
.
My system is also going to vent the cathedralized attic -- not
in an extreme way, but enough to matter. This seems to be
something that's completely ignored -- what happens in the attic
under a tight envelope if it's basically sealed off with no
air passage other than a few ceiling leaks??
.
_H*
[Editor's note: To continue reading comments, click on Page 2]
Response to Hobbit
Hobbit,
Your question has been studied by researchers. The answer is, cathedralized attics do not need mechanical ventilation, HVAC supply registers, or HVAC return grilles. The conditions in a cathedralized attic should be close to the interior conditions elsewhere in the house, so there is no need to worry.
WRB
Martin,
you seemed very surprised to find out that the Belgian House did not have an American Style WRB (Tyvek or Felt)
from what I have observed...there are several "systems" that do not incorporate a "membrane"...
This Pavatex System is one example
http://www.natural-building.co.uk/PDF/Pavatex/090216_Technical_Manual_PASSIVHAUS.pdf
No WRB is "no problem"
Martin,
Yes.... It doesn't matter if it's Gutex, Pavatex (thanks JB) Agepan or other Euro style fibre board. The boards contents are: woodfibre, PU Adhesive and wax. The wax does allow the WRB to be omitted because it is now redundant. It's a standard course with that material and has performed well since the early 90"s. I talked to plenty of builders and designers who have had good results and have not found any with bad results.
It's also one of the reasons that I was reporting my frustration with the "how big of a gap is big enough" discussion in the US. The bigger the gap, the better the ventilation. The vendor I work with requires a minimum of 3/4" gap at the rainscreen regardless of the facade material.
I'm not sure if I qualify as a Yankee as I hail from the Pacific Northwest. I see it as more of a Nor'easter thing... However, I think I share some of the same skeptic traits as a Yankee and decided to start my own test. It's highly un-scientific but reliable.
The Small Planet Workshop is located at the bottom 1/4 mile of the very bottom of a large ocean inlet know as the Puget Sound. It is the reason that the State of Washington has a funny shape and looks like it missing a piece out of the middle. The shop itself is less than 50' from of the salt water marsh that is the stagnant end of this large body of water. I'm not sure how the developer got away with it, but our septic tanks and field is between the shop and the water.
My test for this "purported" wax impregnated sheathing that makes a WRB redundant is that I placed a 12"x14" piece of the 16mm Agepan DWD on a stake over our septic tanks that are around 40 feet from the salt-waters edge back in march 2012. You really could not find a wetter place in the State than over our septic tank at the bottom of Puget Sound.
You may have heard rumors that Seattle gets some rainfall. The only place in the State of Washington that gets more rainfall than Seattle... is Olympia!
As you can see in the pictures, I planted the test sample on March 8. Since then we've had unseasonably wet late winter and spring. I occasionally test the sample for expansion and so far it has not gained a millimeter when I check it wet or dry. The water seems to just roll off and not saturate.
The Olympia "Septic Test" is not meant to replace controlled independent testing. I'm just doing it to see what happens. However I do think this system works based on the builders I've talked to.
Response to Brooks & Rooks
John and Albert,
OK, I learned something. These products are basically the Zip Sheathings of Europe -- the WRB is integrated with the product. I assume that all you do is tape the seams and you are good to go.
A Joe Lstiburek quote
I spent all day Wednesday at a building science seminar offered by Joe Lstiburek. During a discussion of the use of sacrificial lime plasters to address problems from efflorescence and spalling on masonry foundations that lack a capillary break, Joe said something that could have just as easily referred to the Belgian house under discussion here.
Joe said, "I’ve done more than my share of work in Europe, where they know a lot about stuff that we don’t know about. But we also know a lot that they don’t know about. You are kind of surprised by how much they know, but also how much they don’t know. Europe is filled with lots of really, really, smart people as well as lots of really stupid people. Europeans aren’t all smart and Americans aren’t all stupid."
I thought the BSC/GBA was this week...
And wondered if the subject failure of this post would come up during the day?
I think that's really the opportunity here. Each building culture gets to exchange new idea's and practices. On a good days it the "world music" of building. On a bad day it's competitiveness, doubt, and stubborn regional protectionism.
Re #54: Tape the seams and you're good. Ja!
Response to Albert Rooks
Albert,
During a break in Wednesday's workshop, I had a chance to chat with Joe about the house in Belgium. He made two comments: “If a wall is at risk for inward solar vapor drive, you have to have ventilation behind the cladding. And stucco over fiberboard sheathing without an air gap is nuts.”
Belgian Passivhaus
Martin - great piece as always. I shared on my blog: http://riles-files.blogspot.com/2012/06/belgian-passivhaus-piece-from-gba.html
It made me think of the supply side of market transformation to a greener world. Thanks again.
Even when done perfectly, earth tubes are fatally flawed
I was bemused by this passive house failure story. Been there -- screwed it up myself decades ago, and got the T-shirt. I did a bunch of houses in 1979 and 1980 with earth tubes as a pre-conditioning system for my HRVs. I have pictures somewhere. I think the statue of limitations has run out by now. Horrible mistake.
Earth tubes cannot be made to work except in a desert climate, and even then you have to be nervous. The psychometric chart shows why. So I have to respectfully disagree with you about them ever working even when done perfectly, because even perfectly done they are fundamentally flawed.
Response to Joe Lstiburek
Joe,
Thanks for your comments -- and your valuable warning.
Those who are ignorant of history are doomed to repeat it. So, GBA readers: if you don't want to collect the same T-shirt that Joe's talking about, stay away from earth tubes.
Window detail
Martin,
Btw... Look at the window details on 3.3 and notice the "over insulation" of the exterior window frames as well as the rest of the "innie details". You know those things will perform so much better than hanging outside of the envelope on a nailing flange.
Response to Albert Rooks
Albert,
Thanks for tracking down more details on these systems, Albert.
For some reason, the link to the first pdf document that you attached isn't working for me.
I'm always willing to learn something new, and eventually we'll find out more how these systems work in a variety of climates. I must say that the entire idea of stucco over vapor-permeable wood-fiber sheathing without an air gap strikes me as highly undesirable and risky. However, I've been wrong before.
I don't read German, but it's fun to say "Oberputz."
Stucco systems were developed for the exterior of masonry buildings. For thousands of years, stucco systems have worked well over brick, stone, and concrete walls. All of the stucco failure stories I know about have arisen when builders used stucco on wood-framed buildings.
At risk of being nuts: Stucco without a gap.
Martin,
Back in post # 13: [MH] "Finally, you raise questions about the use of stucco over vapor-permeable sheathing in Europe. I'd love to know more about the details of these walls. Do European builders include a drainage gap between the stucco and the sheathing, for instance?
It took me a bit of time to gather some details, and I did not get a chance to translate them since the days are going by too darn fast but here is some system data and details.
These details are for a jointly developed system specific to Knuaf and Agepan. I say specific because they are tested and come with a warranty for the system. It can't be sold over here in the US since it's a specific contract based in the EU. The key to it seems to be that the Agepan THD is thick (2"+ depending on your choice), and is tongue and groove. These two characteristics along with a specific fasteners schedule create a solid base to receive the stucco.
Further to it's stability is that these thick woodfibre boards have a higher mass and heat storage capability. I know the heat storage capacity in other aspects, but not very well as it relates to the stucco. What I "think" it means is that it moves less than plywood when subjected to heat.
In any case, the stucco going over it is directly applied and highly permeable. The theory goes that the inner layers can absorb and release moisture as needed. The stucco layer is not so thick that it's going to store the large amount of moisture that a brick would store and drive into the wall when hit by the sun.
So... Small water storage + high perm and the ability to absorb and release + a stable base that's thick, heat tolerant, low in density for thermal isolation and causes less dimensional change... Means that the system "hangs together" well.
I do know that these systems continue to perform well, and that the other fibre board makers have their "partnering systems" too. It's not just Agepan. We do have permeable stucco systems here so I'm confident that it will work here with the right stucco product, but I'd caution anyone thinking of doing this with the statement of DO NOT TRY THIS WITHOUT FACTORY SUPPORT! At this stage we are at the Geeewizz let's learn more about this stage, rather than lets start covering projects.
I've got the right board and can try a sample wall this summer, but it sure would be interesting to do this in an "skeptical lab" like BSC. If it worked, it would be a pretty serious breakthrough for US Builders.
Take a look at the attachments. The written doc is just a coupe of pages out of the German Approval Document. The second page shows the layering of the stucco. The detail sheet is in German but pretty easy to see the idea.
I got a few emails off-line from a few folks who have had non US experience with woodfibre and stucco and were pretty enthusiastic about the blog posts. Too bad they didn't post themselves :( It's interesting to see how widely GBA is read outside of the US and these readers have some pretty valuable experience.
One of the emails offered to help with translation :) I'll pass the detail sheet on and see if he'll translate the few layers shown.
It might be me, but I find the stuff that we don't know far more interesting than the stuff we do know...
Response to Albert Rooks
Albert,
This link still isn't working for me.
Oberputz! Oberputz!
Martin,
It's just as well the first link did not work. It was a condensed version. I've attached the full version here. What I found most interesting was on pages 9 & 10: The call-out for fastening the boards and then the stucco layers.
I've sent the detail sheet to someone who offered to do the odd translation based on their interest in the subject of woodfirbe insulation boards (and works at NHBA). Let's see what comes back.
Not sure of the issue.
Martin,
The link is not working for me also. I've converted it a few times to new types and still it won't show. I'll try scanning it from scratch later today... Sorry for the run around.
European certification processes
I like to point out that to this day rigorous onsite QAQC is a missing component in current European PH certification processes.
For that reason PHIUS was inspired to create the PHIUS+ certification program to do as best as we can in our efforts to all but eliminate problems caused during the construction phase of a PH project.
Basic wall construction detail
See the attached detail from Albert with my translation.
In some cases the fiberboard sheathing acts as the WRB. I'm not sure if that is the case when stucco is applied. When there's an air gap (drainage plane) behind the siding, bitumen-impregnated fiberboard is sometimes used. Beyond the tongue-and-groove, no seam treatment is called for. (That bitumen probably wouldn't allow the stucco to adhere very well.)
Response to Dan Buuck
Dan,
Thanks for the translation.
It's hard to imagine any reason why this wall assembly wouldn't load up with water on a sunny day in the summer, after a rainstorm. Of course, the wet wall may eventually dry out in both directions -- but it still seems odd to design a wall that seems to invite moisture loading during the summer.
Response to Martin Holladay
In my architecture classes in Germany, we would do a rough calculation of how much moisture would permeate (and condense) in a given wall construction. It was said that a certain amount was okay as long as it would eventually find its way back out.
The stucco on EIFS is so thin, I don't think there is much bulk water storage there at all. If the sun does drives some moisture into the wall, it will only be for a while (until the sun goes down or they get another long period of cloudy weather). Then it will find its way out of the wall again, finding the path of least resistance is to the exterior. (That's the theory anyways.)
Since EIFS has been used for decades in Germany without it falling out of favor, they must not be experiencing too many moisture problems. Could it have something to do with their specific climate and level of detailing? (Windows are located in the middle of the wall construction!) It might be interesting to note that you have to have at least a 4-year degree to design a single-family home in the state of Bavaria, and I'd assume it's the same for the rest of the country.
Approval docs
The document I was trying to upload was 13 pages. I bet that was the issue. Here are just the first two pages.
I think the reason that this works is that the system doesn't restrict the flow of moisture or vapor. Like cellulose, I think that the "big woodfibre boards" can take on a lot of moisture and that the stucco's capacity to store and release, is well within the range that the rest of the system can handle.
[edit] I just tested the link after posting. It's working for me.
a.
Oh brother... For years, long
Oh brother... For years, long before the PHI said Sayonara, PHIUS sang the praises of the PHI certification route as being 'quality assurance' enough. That it was the PHPP that did the vetting - along with the blower door test to ensure a high quality of construction. It's only upon formation of a certification that many view as lacking legitimacy that the traditional certification route (which ain't exactly a walk in the park) isn't good enough? Hilarious...
PHIUS, 2008: "Passive House Planning Package software is the basis for quality insurance. It was
specifically developed for this task... Its calculations have been proven"
PHIUS, 2010: "Passive House air-tightness standard [is] a quality-assurance feature."
PHIUS, 2011: PHI certification is, "an issue. It is an issue of quality assurance and Dr. Feist is entirely in agreement that that is a very important aspect of Passive House implementation."
I'd like to point out that construction practices in Europe are far more advanced than here in North America. CADCAM technologies and prefabrication ensuring ultratight tolerances are the norm for high performance housing. I'd also like to point out that few, if any, of the 'certified' projects on the PHIUS website have been through 'rigorous onsite QAQC'.
Furthermore, outside the plethora of issues on this project, it never was a Passivhaus. It didn't meet the blower door test. It probably didn't meet the specific space heating demand. It certainly was never vetted through one of the many certification agencies approved by the PHI. This project lies squarely in the category of buildings calling themselves 'Passive House inspired' or other nonsensical terms.
Not really a Passivhaus ?
Mike E.,
John Semmelhack brought this up back at post #9
Is this project really a "Passivhaus"?
Who gave this house the Passivhaus Label?
Was it Hens?
If this is NOT a Passivhaus....
Is the title of this blog fair?
Response to John Brooks
John,
As the article indicates, my source is an academic paper by Hugo Hens. His paper was presented at this year's ASHRAE Winter Conference.
1. The title of Hens's paper is "Passive houses: what may happen when energy efficiency becomes the only paradigm?"
2. Hens states, "In the paper the case of a passive house is discussed that was declared inhabitable less than 2 years after the inhabitants, a family of five, moved in. ... The concept was introduced by Feist (Feist, 1988, Feist, 1996). Basic performance is a net energy demand 15 kWh/(m².yr) (317 Btu/ft²). ... A blower door test is mandatory while n50 measured should not pass 0.6 ach. .... The one house was erected using traditional brickwork and the other constructed according to the passive standard. ... Measurement of the n50-value gave 0.68 ach, which is slightly higher than the 0.6 ach imposed for passive dwellings."
3. A few commenters on this page have concluded, perhaps correctly, that since the measured air leakage rate of the Belgian house slightly exceeded the Passivhaus standard, it is not a Passivhaus.
4. Most Passivhaus buildings in Europe are not certified; nevertheless Dr. Feist and the Passivhaus Institut count these uncertified Passivhaus buildings when tallying the success of Passivhaus construction practices in Europe. It's certainly possible for a builder to aim for the Passivhaus standard without going through the headaches of certification, and it's certainly possible for a builder to decide that 0.68 ach50 is close enough.
5. This building failed because of damp ventilation tubes and inward solar vapor drive, not because of any problems due to the fact that its air leakage rate was 0.68 ach50 instead of 0.60 ach50.
Lost in Translation
Martin,
Thanks for the additional info.
I certainly don't believe that 0.60 ach50 would have "saved" this house.
I was just curious if Hens actually called the house a "Passivhaus"
Do you have a link... or can you post the Hens Paper?
Response to John Brooks
John,
I think ASHRAE is controlling release of this paper; I got a copy direct from Hugo Hens, and I don't think I can publish it without seeking permission from Hens and ASHRAE.
Cause of Excess Humidity
I can see the advantage of earth tubes for drawing fresh air into a house while using the cool mass of the earth to cool the incoming air for the purpose of cooling the house. But I can also see a problem with the cool earth tubes condensing moisture out of incoming air if it is high in humidity as summertime air often is. That might leave condensed water standing in the tubes where it might grow mold, and the mold would then be drawn into the house with the incoming air.
However, in the case of the house under discussion, it sounds like water entered the tubes as rainwater. That strikes me as a major careless defect in the design and/or construction. Keeping rainwater out of the earth tubes seems like it would be an absolute requirement. Moreover, it seems like it would not be a difficult challenge to do so.
Considering this major defect in the earth tubes, I am wondering how it was concluded that the cause of the humidity problem in the house was contributed to by both the earth tubes and the inward vapor drive. I can see that the conditions favoring inward vapor drive exit, but how do we actually know that was occurring and contributing to the humidity problem?
Response to Ron Keagle
Ron,
The conclusion that the OSB was humidified by inward solar vapor drive was made by Hugo Hens.
Hens wrote, "As reported above, the enclosing cavity walls consist of a highly insulated timber framed inside leaf, lined inside with an air-tightened OSB sheathing and finished at the cavity side with a very vapor-permeable wood fiber board. A 3 cm. wide unvented cavity separates that inside leaf from a capillary active, 9 cm. thick brick veneer. At the wind side – in Belgium the South over South-West to West orientation – that veneer acts as a rain buffer with the potential to store up to 14 liters per m² (0.18 USgal/ft²) and more. During warmer weather after a rainy period, part of that moisture diffuses across the inside leaf to the inside where it humidifies the OSB, a phenomenon called solar driven vapor flow (ASHRAE, 2009).
"At the rain side, the brick veneer/cavity interface stays at 100% relative humidity year round. In fact, even a very moderate moisture content of 14 kg/m3 (0.87 lb/ft3) stands for a relative humidity beyond 99% in bricks, see figure 8. As a result, the relative humidity in the OSB inside lining shows an annual fluctuation close to the one calculated in figure 9. Superimposed is a daily oscillation with relative humidity peaks at the cavity side of the OSB nearing and passing 90% in summer. In fact, temperature at the cavity side of a wet west over south-west to south looking brick veneer wall may pass 35°C (95 °F) during warm summer days, giving water vapor saturation pressures up to 5260 Pa (109.5 lbf/ft²), high enough to create an additional daily vapor flow to the inside, which further increases humidification of the OSB."
Earth Tubes
Martin: Many comments in this thread have mentioned that "earth tubes don't work" (including one by Saint Lstiburek). But no discussion of the failure mechanism was provided. Ponding water should not be a disqualifying characteristic, since that can be easily prevented by sloping the pipes to drain away from the dwelling. In fact, any condensation that does form on the pipe walls (and then drains away with the properly sloped pipe) should result in humidity level in the air being LOWER than that in the outside air and therefore the condensation process should be considered a positive attribute of the tube idea.
The real problem with with earth tubes (that we found after trying them in several houses in the mid 80's) is that the heat transfer is poor. Their cooling effectiveness relies on the conductivity of the thin layer of earth directly around the pipe. We found that our pipes did provide some cooling for the first two weeks or so after installation, and then the earth around the tubes heated up so that there was no longer any measurable cooling going on because the conductive heat flow through the earth layer was relatively low. The extent of this problem depends, of course, on the moisture content and conductivity of the soil around the pipes. Typically, tube installations that we have seen set the tubes relatively near the ground surface where the soil is dryer and less conductive than in deeper strata. Dry soil is a poor heat conductor so little heat transfer occurs.
The second reason they do not work well is that there is relatively little surface area for heat exchange. Only the air in contact with the wall of the pipe will undergo any cooling effect. Compared to, say, a finned heating or cooling coil, the contact area between the pipe wall and the air is vanishingly small, and little heat transfer occurs, even with a cool pipe wall. Most of the air travels down the center of the pipe and never touches the pipe wall.
Response to Carl Mezoff
Carl,
Thanks for your comments.
I am aware of the problems you describe -- limited heat transfer and problems resulting from the soil surrounding the pipe heating up in summer and cooling off in winter -- which is why I wrote, "earth tubes ... provide limited energy savings."
Great!
Article and thread.
I live in Calgary, AB, and we have more humid and cooler summers lately to contend with, and still cold winters. From +22 d C and 70% humidity commonly in summer, to -30 d C and 7%. Winter Chinook winds also drive the temperature + or - 40 d C in both directions in 12 hours or less, 5 or 6 times a year. So you can go from -20 C to plus 10 C (0 d C = 32 d F) and from 10% H to 80% H, mid-day, in as little as 6 hours. We are thus REALLY cautious about new wall assemblies.
Pity the fact that we stick to drywall/poly/2X6 and fiberglass/OSB/whatever outside, including poorly vented EIFS, despite the issues with this assembly. With our climate, which usually DRIES out every summer and even in winter, we have been extraordinarily lax about vapour transmission. Currently popular is 6 mil poly vapour barrier on the interior, and EIFS on the exterior, a recipe for disaster in a cold climate, in my opinion. I am also leery about sandwiching biology between layers of impermeable plastic.
I share the caution about poly. I have seen too many disasters based on the mistaken assumption that because we call it a vapour barrier, it is. Like, it works. Talk about "working on paper..."
I would share the same concern about depending on foam, taped, to act as a air barrier on the exterior.
Both systems depend on actually stopping any air flow in order to remain effective, emphasis on "remain." This is, if not impossible, at least unlikely.
Despite my caution about rushing out and advising folks about installing permeable wall assemblies right away, I see it as the only way to solve the issues surrounding the use of impermeable plastic in a wall assembly.
Key, though, is Martin's note in one of the comments: use an impermeable barrier, so long as it can dry both ways.
Key, also, is the importance of a difference in climate and the need to test assemblies as they relate to conditions.
The key failure so far as I can see in the Belgian case is the lack of proper vent space between the brick and the house, the failure of venting there, and the drive of moisture within the home as a result. Certainly the water in the earth tubes didn't help, but in our climate, that brick would have been frost damaged and would have fallen apart the first winter or two.
We told you so...
For 40 years many of us Old Timers have been trying to tell you, "you are building em too tight..." Now millions of dollars of litigation later and examples like this Belgium house, is anyone listening? Get back to fundamentals, and the basics. If you can't feel a slight draft when the wind is blowing around a receptacle, your house isn't breathing. Mold loves it when your house doesn't breath. Fire codes love to cut off ventilation. So the incredibly small chance of having a fire, and the resulting oxygen starvation to retard that, fuels the incredibly high chance of growing mold with the lost ventilation. The Apollo 13 crew almost killed themselves in a vehicle that doesn't breath by, well, breathing. Don't make the same mistake, you have a choice on earth. Listen to Gramps, let em' breath. Fine tune conditioning of the air, not 'tightening' of the structure. Bill Kastrinos, Tortoise Shell Home LLC
Response to Kevin Brown
Kevin,
You wrote, "I share the caution about poly. I have seen too many disasters based on the mistaken assumption that because we call it a vapor barrier, it is. ... I would share the same concern about depending on foam, taped, to act as a air barrier on the exterior. Both systems depend on actually stopping any air flow in order to remain effective."
Actually, interior polyethylene is an effective vapor barrier (or vapor retarder) -- so your skepticism about whether or not "it works" as a vapor retarder is unfounded. It works all too well, which is a problem.
Although interior poly works very well to stop vapor diffusion, it usually makes a lousy air barrier, because a great deal of air leaks through seams, penetrations, and electrical outlets.
Response to William Kastrinos
William,
It sounds as if you believe that the problems in the Belgian house occurred because it wasn't leaky enough. I disagree. I think that the problems were due to a poorly designed wall assembly that allowed inward solar vapor drive, coupled with a faulty ventilation system that introduced humid air into the house.
You wrote, "If you can't feel a slight draft when the wind is blowing around a receptacle, your house isn't breathing. Mold loves it when your house doesn't breathe."
Actually, I think it's unwise to deliberately build a leaky wall, as you apparently advise. The flow of air through a leaky wall isn't always inward -- it can also be outward. When warm, moist indoor air escapes out of the air leaks around the electrical outlet of your leaky walls, the moisture piggybacking on the air can condense on cold wall sheathing. That's where the mold comes from.
Poly as vapour retarder
Much better nomenclature, because it clarifies.
A flat sheet of 6 mil. poly sheet does indeed act as a vapour barrier - in the lab. But when it fails, it fails disastrously. It is precisely because of the concentration of air leaks around common points - seams, penetrations and electrical outlets - that helps it fail in its purpose: vapour transmission is focused on those points of failure, providing amazing amounts of moisture to the building assembly, ripe for condensation in our cold winters, and thus mould growth.
The leaky nature of poly as a vapour retarder is precisely the problem. That is why I am pursuing vapour diffuse building assemblies. These systems allow you to manage vapour flow, rather than depending on a system that is guaranteed to provide plenty of opportunity for focused failure.
Still, it is the industry standard, and with very careful control of the details, and with some improvements such as the installation of an installation stud wall, interior to the poly layer, many of the issues can be dealt with. Many Net Zero homes in Canada are still using poly, and achieving very good air tightness. Seems to me that this is your point in much of your discussion on the issue...
Like you say, it works as a vapour retarder all too well, except when it doesn't!
Thanks for the discussion!
And furthermore!
Martin's comment about caution with the installation of any vapour management layer in relation to the dew point is an essential but often ignored point...
Response to Kevin Brown
Kevin,
It may appear that I am insisting too much on this point, but it's an important point: it is essential that we understand the difference between a vapor barrier and an air barrier. Only when we understand that difference will we be able to design good walls.
That's why I must insist that you are wrong again when you write, "The leaky nature of poly as a vapor retarder is precisely the problem." Polyethylene (as usually installed) is a leaky air barrier, but it performs extremely well as a vapor retarder.
The effectiveness of a vapor retarder is not significantly diminished by a few flaws. If you put lots of holes in a sheet of poly, so that the sheet is now 5% holes and 95% poly, you have destroyed its effectiveness as an air barrier, but you haven't significantly hurt its performance as a vapor retarder. This damaged poly still limits vapor diffusion, performing with 95% of the effectiveness of a brand-new sheet of poly without any holes.
For more information on this distinction, see:
Vapor Retarders and Vapor Barriers
Forget Vapor Diffusion — Stop the Air Leaks!
Log in or become a member to post a comment.
Sign up Log in