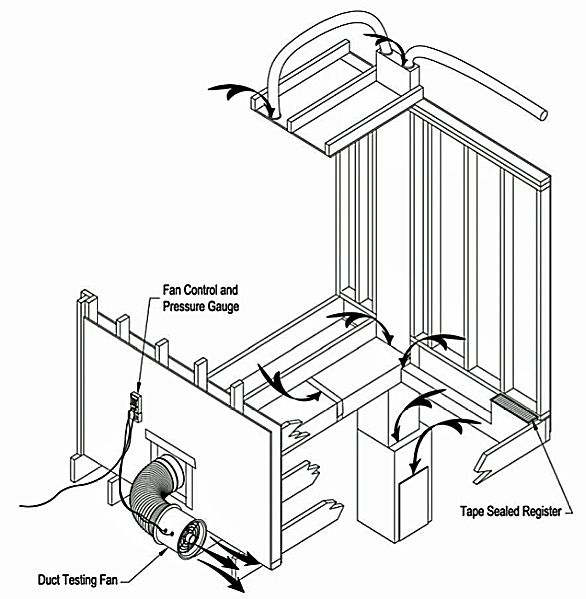
Image Credit: Residential Energy Builders Guide, University of Kentucky
For years, Americans who would never put up with leaky plumbing pipes have been willing to accept leaky ducts. While water damage is hard to ignore, the damage caused by leaky ducts is more subtle. Yet leaky ducts not only waste huge amounts of energy — they can also lead to comfort complaints, moisture problems, mold, and rot.
Most green certification programs require builders to pay attention to duct tightness. Now that duct testing requirements are starting to appear in some local building codes, more and more builders are asking questions about the ins and outs of duct leakage testing.
Duct basics
If you’ve never had to worry about duct tightness before, you may want to read the “Forced Air” section of the GBA Encyclopedia.
Most green builders already know their duct basics:
- Duct leaks are very common; in many homes, duct leaks are responsible for significant energy losses.
- For ducts located in an unconditioned attic, any leaks in the supply system tend to depressurize a house, while return-system leaks tend to pressurize a house. Either condition can cause problems.
- Duct leaks outside of a home’s thermal envelope waste more energy than duct leaks inside a home’s thermal envelope.
- Even if ducts are located inside of a home’s thermal envelope, duct leaks can still connect to the outdoors. For example, supply system leaks in a ceiling between the first and second floors of a two-story home can pressurize the joist bay, forcing conditioned air outdoors through cracks in the rim joist area.
- It’s much easier to seal duct seams during new construction than in an existing house.
Characteristics of a good duct system
A good duct system:
Weekly Newsletter
Get building science and energy efficiency advice, plus special offers, in your inbox.
This article is only available to GBA Prime Members
Sign up for a free trial and get instant access to this article as well as GBA’s complete library of premium articles and construction details.
Start Free TrialAlready a member? Log in
14 Comments
Wall Stud Cavity Returns--Retrofit
Hi Martin: many thanks for your thorough summary of the important issue of duct leakage. I've sealed (with mastic) and insulated the ducts in my circa-1988 (cold climate location) house. However the returns utilize interior wall stud cavities from the (high up on the walls) intake grills down into the basement where they connect to the return trunk duct. Result=leakage in the returns; worse, we periodically may be inhaling day old spider breath. Are you aware of any product/solution which can seal or retrofit a flexible "sleeve" or "lining" duct-equivalent into a vertical stud cavity inside an interior wall? I'm reluctant to tear out large sections of my house's interior walls to this end. Many thanks.
Wall stud cavities for returns
Jan,
For new construction (at least here in Vermont, where galvanized ductwork is the norm), we use 3 1/4 inch by 12 inch or 3 1/4 inch by 14 inch "wall stack" duct for 2x4 wall cavities. It's roughly equivalent in cross-sectional area to a 6-inch round duct, so it has limited capacity — equivalent to a single residential register.
I don't know of a retrofit solution. GBA readers -- anyone done this? Is there a solution?
You should calculate the necessary airflows for your return ducts -- it's certainly possible that your returns are undersized. If they're undersized, the solution is to bite the bullet and build new chases, properly sized, that enclose new ducts with sealed seams. That will make your rooms a little smaller, of course.
Another perspective
Hi Martin,
Thanks for putting this out there. In some of your past articles you discus standards beyond code which as I am sure you would agree is a bare minimum standard. I agree that most are falling significantly short of meeting reasonable duct leakage standards. I think it's important to emphasize a couple of performance factors that don't recieve enough attention when we are talking about ducts and duct sealing. Some areas measure against a nominal air flow of 400 CFM per ton which rarely exists (in our test typical is 56% of nominal airflow), and like you sugest with the Colarado study the resulting ductleakage is significalty higher that what is reported. I think the IRC again shoots for too loose a standard by allowing additional leakage as square footage increases, are those larger buildings allowed to leak more from thier plumbing systems as well? We are trainging build performance contractors on the West Coast that the ducts are better off in the envelope, if they are outside the envelope the sytems should leak less than 5% measured air flow not to exceed 50 CFM25 regardless of system size. Most of our systems come in at less than 20 CFM25. Since our ducts are located in the attic this a target we achieve on all of our retrofit systems. I realize that ducts located in the conditioned space are bit of a differnent story, but there are still consequences to the pressure loss assocaited with those ducts being more leaky. The other piece that is too often ignored is that when we seal poorly designed ducts the result is an increas in static pressure, often to the point where variable speed fans are experiencing premature failure. I think that when ever duct test is completed a coresponding static pressure test should occur so that we are looking at the whole system. In the early adoptor states like California the duct sealing of existing systems has with airhanders designed to push 2000CFM and ducts only capable of distributing 1000CFM has led to static pressures in exess of 150% of the manufactures limits. On this forum I think we should describe where and how the code is a bare minimum, what it's shortcomings are, and some ideas for truely golds standards. What is cost effective tommorrow will not be the same as what is cost effective today. If this changes when will we go back to further tighten and inaccessible duct system. You did touch on these things, and I am not writting to correct you, instead merely adding a regional point of view. Keep up the exceptional work!
duct leakage based on sf conditioned area in weak
Great article, Martin. I don't know how many times I've heard HVAC contractors claim they build tight ducts, yet they don't own a Duct Blaster. I ask how do they know? Even the best crews sometimes make mistakes. You can't see air leakage. Of course, the only way to know for sure is to QA your installation crews by conducting leakage tests.
All mechanical contractors should conduct leakage and static pressure test-outs on every system they install. Unfortunately, it’s easier to sell high-SEER equipment than high efficiency *systems*, a distinction invariably lost in a competitive marketplace. I try to convince every builder I meet that they (and their clients) are better off paying a little extra for a quality duct system than paying a lot extra for high SEER equipment.
opps! wrong subject
The subject line of my previous comment obviously has nothing to do with the comment. I was going to comment on the validity of using percentage of floor area as the duct leakage standard. I guess I should finish that thought...
As the article points out, Energy Star and most other efficiency programs base duct leakage standards on conditioned floor area (Title 24 being the notable exception). That's a weak method. Leakage standards should be based on nominal fan flow. Otherwise the standard becomes a very low hurdle for efficient homes with right-sized HVAC equipment. It's not unusual to see homes exceeding 1500 sf per ton. At 6%, this translates to 90 CFM(25) per ton, or 23% of nominal fan flow -- a low hurdle indeed!
According to Mike Barcik, an early advocate for the floor area method, this method was selected for ease of calculation, as raters don't necessarily know tonnage of AC. If this rationale was ever valid, it certainly holds no water today. Since 2006, raters have been required to verify a proper load was done and equipment is sized to that load. For the purposes of this calculation, one can assume nominal fan flow is 400 CFM per ton. I've also heard the argument that using nominal fan flow encourages HVAC contractors to oversize the equipment. I won't even dignify that argument with a response.
Energy Star 2011's answer is to reduce requirement to 4% of floor area for outside leakage, but still allow 6% total leakage. I tried to get them to change, but I'm afraid the floor area method is here to stay.
David Butler
optimalbuilding.com
cfm25 to floor area
David, you're right that 6% duct leakage based on floor area represents a low bar for high performance homes with right-sized equipment. That doesn't mean, however, that using air handler flow as the measure is the way to go.
I work with Mike Barcik a lot, having taught 17 HERS classes with him over the past two years, and he's never said using floor area as the measure was for ease of calculation, as you say. The real reason is that when you use floor area, you have a valid comparison from one house to another. The amount of ductwork--and thus the amount of potential leakage sites--depends more on the size of the house than on the system.
Also, if a house has a 2 ton cooling load, for example, and a 4 ton AC, it ends up with half the duct leakage (when expressed as a ratio of cfm25 to air handler flow) that it should have, merely because of the oversized AC. I don't know that any HVAC contractors out there are oversizing just for that reason, but the fact that the ratio changes just by changing equipment--even when the ducts aren't touched at all--means that it's not the best way to talk about duct leakage.
I think ENERGY STAR has it right in going with the cfm25 to conditioned floor area ratio. Getting that number as low as possible is the goal. Really, though, the best way to eliminate duct leakage is to bring them into the conditioned space.
Allison A. Bailes III, PhD
energyvanguard.com
I don't buy it
Many factors affect leakage - in particular, the number of duct connections and terminations. However, if the run-outs are flex, the overall duct length is almost irrelevant from a leakage perspective. All other things being equal, a 4 ton system can be expected to leak roughly twice as much as a 2 ton system. For a given house, an oversized 4 ton system compared to a right-sized 2 ton system will have larger cabinet and plenums, and larger (and/or more) collars, boots and other fittings. This means a reasonably tight standard pegged to floor area will require little or no effort for high performance homes with right-sized HVAC.
For a mastic-sealed system, 10% of fan flow is considered a low hurdle (see below). Now consider a well insulated 3000 SF home with a 2 ton heat pump. Using the floor area method, even 2% is a low hurdle in terms of the impact on overall HVAC performance (7.5% of system capacity lost to leakage, depending on location of leaks). But if we apply that same standard to a 3000 SF home with a typically oversized system, say 4 tons, even a conscientious HVAC crew would have trouble complying. And we haven't even talked about how the floor area method necessarily creates a climate zone bias.
In the commercial market, duct leakage standards (established by SMACNA) are based on duct surface area rather than fan flow. But here there are two important differences: 1) the SMACNA standard was developed for fabricated ducts, which are far more prevalent in the commercial sector, and 2) with commercial, there's a separate leakage standard for cabinets.
I submitted a comment on the duct leakage metric to Energy Star (e: 2011 draft program requirements). In its response, Energy Star said it previously followed the fan flow method (prior to 2006) and argued that it "...promoted increases in fan size and associated airflow, which minimized savings." Whoever wrote this obviously doesn't understand that "nominal" fan flow is based on condenser tonnage, not blower capacity. No contractor would ever select a larger fan to 'game the system' since 1) it would not change the prescribed leakage limit, and 2) a larger fan would actually *increase* duct leakage. This response was nothing more than 'arm waving'. Considering this response, and the "ease of calculation" explanation (conveyed to me by Barcik in 2006), I've yet to see a rational justification for the floor area method.
Consider this: Prior to RESNET's about-face (in the lead-up to Energy Star 2006), virtually every residential duct leakage standard was based on nominal or design fan flow. Other notable examples include:
* Energy Star's Advanced New Homes Construction BOP
(3% of fan flow, ducts inside conditioned space)
* California Title 24
(6% of fan flow, performance method for new construction)
* Building America - Performance Analysis Procedures
(referencing 1998 IECC definition of tight duct system as < 5% of rated fan flow)
* ACCA Standard 5 - HVAC Quality Installation Specification
(10% of fan flow, total leakage)
* Texas Residential Standard Offer Program (electric utilities)
(10% of fan flow, total leakage)
Finally, I have been involved in or have reviewed a number of utility-driven residential "AC tune up" programs over the years and all of those that included duct testing used nominal fan flow as the reference. When selecting a quality assurance metric, it's important that it correlate with the level of effort or skill required to achieve the desired result. Residential duct leakage correlates far better with fan flow than with floor area. This makes it a more appropriate metric for doing "QA" on HVAC installation crews.
Energy Star's decision to switch to the floor area method has led to many other standards and programs adopting following suit (including the 2009 IECC), so it's apparently here to stay. Nevertheless, I recommend we hold installers to the fan-flow metric whenever possible, especially for homes with exceptionally small HVAC systems. A leakage target of 5% (to the outside) of nominal fan flow would be reasonable.
Regarding your last point -- just because ducts are inside the envelope doesn't eliminate concerns over duct leakage. But I know that you know that. In any case, I certainly agree with the sentiment of your comment.
David Butler
optimalbuilding.com
Do you need transfer grilles in bathrooms or laundry rooms?
Martin, your blog says that a good duct system "includes ducts or air paths that allow return air to flow back to the air handler from every room with a supply register"---sounds right to me. However, my HVAC sub says he never puts transfer grilles in bathrooms or laundry rooms (even though they have supply ducts) because they have vent fans. I think his philosophy is that any overpressure would flow through the vent fan duct to the outside---doesn't sound very efficient to me. My plan is to insist on transfer grilles. I would like your opinion. Note that this is in a HH climate (central Texas) with a GSHP and foam insulation (including roof rafters). The AHU, heat pump, and most of the ducts are in the semi-conditoned attic. This brings up another question---should I have transfer grilles to the attic (no supply or return currently planned for that space)?
Response to John Walls
John,
1. Many people omit the transfer grilles for bathrooms and laundry rooms because these small rooms have lower cfm requirements than bedrooms. Usually a door undercut is sufficient to avoid problems. However, if you want to install a transfer grille — assuming you have considered the noise transmission issue — go right ahead.
2. A semi-conditioned attic that is within the home's thermal envelope does not require a supply register or a return grille.
no transfer grills for attics!
All great questions, John!
I don't recommend a transfer grill for encapsulated attics, as this would be wasteful. In fact, I recommend reasonable efforts to air seal the ceiling (although many foam installers recommend not to air seal). Several years ago, I asked Ed Reeves at Icynene about this issue. He said when they sought recognition in the IRC for encapsulated attics (Sect 806.4), their models only considered *conducted* heat flow through the ceiling. My philosophy is that if direct conditioning or infiltration is needed to maintain non-condensing temperature, then there's not enough insulation on the roof. In any case, in a HH climate, winter condensation is a non-issue.
I agree with Martin regarding baths and laundries. Your contractor may be extrapolating from a rule that no direct returns be installed in baths, kitchens or laundries. You are correct in your efficiency concern. Here's some useful information that can help you decide how to handle:
According to Manual D 3rd Edition (Table A1-2), door undercuts can handle 2.1 CFM per square inch. So a 24" door with 1" undercut can handle 50 CFM, more than enough for a standard sized bath in a high performance home. The design load for a high performance home in central Texas is likely less than one ton per 1000 square feet, which equates to 0.4 CFM per square foot. Many of the loads I've done for high performance homes in similar climates are closer to 0.25 CFM per SF. A bath or laundry may be more or less than the house average, depending mostly on windows.
A transfer grill (or jumper duct) may be required in the following circumstances:
1) a large master bath and/or a bath with large window(s)
2) the HVAC system is oversized, pushing more air to room than undercut can handle
3) the Bath or laundry ducts are oversized relative to their load (but this can be fixed with damper or adjustable grill)
You can tell if you need a transfer grill by observing whether the vent flapper opens when HVAC blower is operating. If no flapper, as in the case of a down-facing outlet, attach a piece of confetti or similar on the grill.
David Butler
optimalbuilding.com
Attic moisture control with jump ducts---foamed house
Martin and Dave, thanks for the good advice. I do have one further concern regarding HVAC air flow to the attic. For foamed houses with semi-conditioned attics in a HH climate, don't you need some type of HVAC circulation in the attic to maintain a reasonable relative humidity (say 50%). If you have a leaky ceiling or put in a jump duct, you would get some circulation. If you have a well-sealed ceiling and only conducted heat transfer occurs between ceiling and attic (see Ed Reeves comment), then the attic temperature may be ok, but what about moisture control? It seems that in the hot and very humid summer, the attic would reach a steady state of high humdity if it doesn't get a little help from the HVAC system. Note that I have 2x6 rafters and knee walls with full thickness open cell foam insulation.
Semi-conditioned attics
John,
Researchers have looked into the question of whether there are any advantages to supplying conditioned air to (or having return air grilles in) semi-conditioned attics. The answer is no.
There are no advantages to supplying conditioned air. There are no downsides or problems in semi-conditioned attics without supply registers or return grilles. If you have a good air barrier that prevents exterior air from leaking into your attic, you won't have any humidity problems. Remember, the humidity is outside -- so seal it out.
Moreover, energy costs are higher in attics with supply registers.
Hi, just a quick note that the first link to "Forced Air" in the Green Basics Enc. is broken and should be replaced with: https://www.greenbuildingadvisor.com/green-basics/forced-air-hvac-systems
Thanks!
Eric S
Eric,
Thanks for alerting us. I have corrected the broken link. I appreciate your help.
Log in or become a member to post a comment.
Sign up Log in