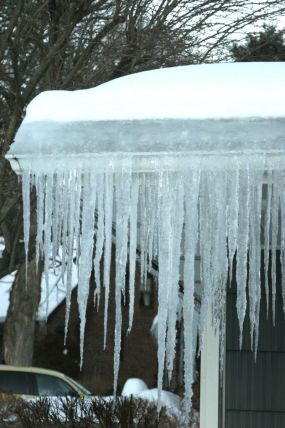
Image Credit: Image #1: Daniel Morrison
During snowy winters, many northern homes are plagued by ice dams. If your house suffers from wet ceilings during the winter, you may be ready to call up a contractor. Be careful, though: since most contractors don’t understand the causes of ice dams, they often suggest the wrong solution.
Ice dams form when a home’s escaping heat warms the roof sheathing and melts the underside of the snow layer on the roof. Water trickles down the roof until it reaches the cold roofing over the eaves, where it freezes. After a while, the ice at the eaves gets thicker and thicker, forming an ice dam. Eventually, water backs up behind the ice dam. If the water reservoir is large enough, it can back up under the roof shingles and damage ceilings. (Image #4, below, depicts the complicated shape of a typical ice dam more accurately than the simplified drawings in Images #2 and #3.)
The four possible solutions to ice damming are:
- Sealing air leaks between the warm interior and the attic or cathedral ceiling.
- Adding more ceiling insulation.
- Improving ventilation between the top of the insulation and the roof sheathing.
- Installing a rubberized membrane under the roofing.
While the first two of these solutions can reduce or eliminate the problem, the last two solutions are the equivalent of waving a white flag and admitting defeat.
Step one: seal the air leaks
Most ice dams are caused by flaws in a home’s air barrier. If escaping indoor air finds its way to the underside of the roof sheathing during the winter, the heated air raises the temperature of the sheathing. That’s bad.
One energy expert who made a career of correcting ice-dam problems was the late Tony Woods, a Canadian physicist and founder of CanAm Building Envelope Specialists in…
Weekly Newsletter
Get building science and energy efficiency advice, plus special offers, in your inbox.
This article is only available to GBA Prime Members
Sign up for a free trial and get instant access to this article as well as GBA’s complete library of premium articles and construction details.
Start Free TrialAlready a member? Log in
91 Comments
good job
Hi Martin,
A few items to add to your excellent post.
You repeat Tony Woods’ advice to go up in the attic. Better yet: find a morning a few days after a big snowfall when the outdoor temperature is around 20F. Call in sick at work, load the camera and drive around looking at icicles and ice dams. In looking at any roof, ask why is it melting here and not elsewhere.
The geometry of the roof plays a big part. Ice dams form in valleys. Providing waterproofing membrane at the valley is generally good practice..
There are other vagrant heat sources besides air leaks from below, including chimneys, equipment in the attic, leaky ducts, etc.
If you can imagine, or photograph, a catalogue of non-uniformities in attic and roof systems, then it’s good to sit back and imagine how a venting strategy could address the specifics of a particular building. How, for instance, would you vent just a valley when the rest of the roof doesn’t need venting? Or how do you target vent air to blow right at a brick chimney?
Your diagrams of ice dams are a bit cartoonish. Don Fugler and other Canadians have refined the picture. It includes formation of an ice layer at the bottom of the snow extending up the roof, and melted water gets beneath this ice. If you look at piles of snow on the ground a few days after a snow, it’s easy to see this ice layer, and to imagine water moving beneath it.
more refined image
Martin or Bill,
Do you have a link .....or could you post an illustration by Dan Fulger (or other Canadian)?
image for John
There is a good image and description in this link
http://www.cmhc-schl.gc.ca/en/co/maho/gemare/gemare_001.cfm
Thanks, Garth
Thanks to Garth Sproule (and CMHC) for the more accurate, less cartoonish drawing of an ice dam, which I have attached as Figure 3.
Another good article
This one by Dr Joe describes how they designed for extremely cold climates.
http://www.buildingscience.com/documents/insights/bsi-031-building-in-extreme-cold?topic=doctypes/insights
Note how they insulate the underside of the eaves and draw roof their ventilation air from the outside edge of the eaves.
There is always more.
Martin,
I think you forgot to mention a couple of things. I am from an extreme climate in central Idaho that receives 100+ inches of snowfall annually with 9000+ HDD. Ice dams here can rip a roof to pieces in no time. I will split up my observations into two systems: Attics and cathedral roof systems.
I will start with attics. First, using blown fiberglass or fiberglass batts in an attic space is a big mistake, especially in a cold climate. Don't be fooled by marketing gimmicks, even so called "next generation" fiberglass products are far too air permeable to stop convection and air leakage driven by stack effect in a cold climate. Even when laid down extra thick, the fiberglass simply does not perform. The next most common mistake is using the attic space as a mechanical room and HVAC chase. No furnaces, supply ducts, or returns should be installed in the attic. I always see folks wanting to add more insulation to the ducts to help remediate this design flaw, but give up. No amount of fiberglass wrap or shiny radiant barrier is going to solve the problem. The best solution is to remove the insulation at the ceiling line and cathedralize the attic space at the roof deck with low density spray foam insulation. Make sure you get a good seal to the top plate with the foam and don't go skimping on the r-value. Considering closed cell foam instead? I'd recommend taking a deep breath and then I'd forget that thought. Instead focus your thoughts on that nice deep 10-13 inches of water blown foam that is going to be waging war against old man winter. Trust me, if you stay away from the low bidder and stick with an experienced foam contractor you will be happy with the flawless roof performance and all the money that you saved over closed-cell (not to mentioned less embodied energy and green house gas emissions).
If you are one of the lucky ones with little or no ductwork in the attic, go ahead and remove all the fiberglass insulation from the attic. After the attic space is cleared out, go to town air-sealing penetrations. If the eave edge has cheesy styrofoam "chute" baffles, toss those in the garbage and install a high quality moisture resistant cardboard baffle. Make sure exhaust fans are routed out the gable ends and not dumping warm moist air in the soffit where it can end up right back in the attic. Next I would lay down a nice thick layer of R60+ cellulose insulation. The more the merrier, but without a raised heel truss the benefits of going super deep are diminished.
With cathedral roof systems, things can get tricky. I'll start with the simple things. First, just say no to fiberglass, especially batts. Secondly, resist the urge to lay down a coat of closed-cell spray foam and finish off the cavity with fiberglass. I'm a huge proponent of cellulose insulation, but in a cathedral application the best bet is low density spray foam.
Now things get a more complicated. To vent or not to vent, that is the question. I have seen perfectly sealed and insulated unvented roof systems perform flawlessly. I have also seen perform poorly. The same goes for vented roof systems. The deciding factor is the complexity of the roof geometry and the type of framing materials used. A simple unvented roof framed with engineered I-joists (TJI, BCI, etc) insulated to code levels with low density spray foam will perform like a champion. An engineered I-joist has only a fraction of the thermal conduction as dimensional lumber. This is why the product is so attractive for use in Passive House wall systems. Adding dormers, valleys, and other roof complexity usually leads to an increase in dimensional lumber, which leads to more structural conduction and heat loss. Additionally, complex roofs often funnel large areas of snow melt to concentrated drainage areas that grow to become impressive ice dams. The conventional wisdom is that adding cavity ventilation channels between the roof rafters will cool down the roof enough to offset structural conduction and heat loss, in practice this doesn't work so well. Typically, adding cavity ventilation to a complex roof loaded with valleys and dimensional framing will not completely prevent ice damming. Much of the time the complex roof design leads to deadhead cavities that don't interconnected to the ridge vent and soffit vent. Furthermore, it is not uncommon for the average ridegevent to be covered in a couple feet of snow in the dead of winter. This tends to put a damper on ventilation rates. To combat structural conduction on a complex roof I recommend upgrading from restrictive cavity ventilation schemes and adding horizontal strapping to elevate the roof diaphragm or a traditional cold roof system. Naturally foam board will also do the trick with the added benefit of adding more thermal resistance to the roof system.
There is no substitute for a simple, well insulated, and airtight roof system. No waterproof membrane will win the fight against the forces of glaciation.
Belt and Suspenders roof design
Just a few more suggestions if you're really paranoid about ice dams, and you should be in areas of high snowfall:
Simple roof design, (no valleys), no vents on the roof plane, steep pitch (6/12 or better), metal roof, no shingles of any sort. No gutters. No downspouts.
Uncondtioned space behind kneewalls rafter level
In the picture at the end of the article from the University of Minnesota this appears to be typical Cape style house with kneewalls. Could you comment on how to properly detail the rafters in the unconditioned space behind the kneewall. It has been suggested in my research that properly air sealing a Cape style house is nearly impossible because of leakage at the top/bottom plates of the kneewall through the trim, micro-gaps in the attic room flooring & sub-flooring into the joist bays etc. Having a "balance of soffit vents and ridge vents" with ventilation chutes being the mechanism that gets air from the soffit to the ridge is essential. You go on to suggest an "in a cathedral ceiling, provide an air barrier between the top of the insulation and the ventilation channel" Typically in a true cathedral style ceiling drywall extends from sofit to ridge and this area needs to be airsealed with extreme detail as you alluded. However in a Cape style house, at least in our area, behind the kneewall is typically a non-conditioned space where the roof rafters are exposed with ventilation chutes between them. These ventilation chutes travel from the exposed rafters from behind the kneewall...... into the slant area (where the kneewall starts) which of course does have sheet rock in the interior side.
It has been suggested in the unconditioned area (behind the kneewalls) that in addition to adding ventilation chutes in the exposed rafters, the rafters be overlaid with a layer of XPS or something like Fanfold or even a layer of Tyvek to the move pressure-boundary of the house from the leaky kneewall & attic floors to the rafters, where getting a good seal is far easier to assure. This reduces stack affect and helps keeps the non-conditioned space under negative pressure.
However its also been suggested that if a decent job has been done air sealing below on the first floor trying to overlay the interior of the rafters behind the kneewalls with XPS is somewhat overkill. Not to mention extremely difficult because of the limited mobility in terms of trying to install it as you will be working on your back. Furthermore whether its realistic to be able to get full 4x8 sheets in there in the first place. In theory establishing the air barrier at the rafters makes sense but the practicality of trying to detail it in this way in a insulation upgrade scenario seems like a monumental undertaking because of logistics.
Lastly in many Cape Style houses you have valleys which means you DO NOT have a clear rafter run from soffit to ridge in some areas of the roof. If the interior of the rafters were overlaid with XPS the ventilation runs would dead-end in the valley areas
According to one insulation contractor that does work for the state sponsored Energy upgrade program in our area when dealing with a Cape style house indicated for the unconditioned space behind the kneewall they simply install ventilation chutes from soffit area to ridge and DO NOT attempt to create a secondary air barrier at the rafter level.
Are simply ventilation chutes between the rafters in the unconditioned space ok? Or should the unconditioned rafter space in addition to having the chutes be overlaid with say Fanfold or Tyvek. In all the diagrams of Capes that have valleys and have unconditioned space behind knewalls I have yet to see a diagram which address whether the air barrier should try to established at the rafter space by placing layer of rigid foam or something like Tyvek, Most write-ups simply spec the ventilation chutes in an open rafter which the travels up into the slant area. What is the opinion of the pro's here?
Response to Chris Sanders
Chris,
The opinion of energy experts for at least 20 years has been unanimous: the insulation belongs at the roof plane, not on the floor of the attic behind the kneewalls..
This sloped, insulated roof area needs to be detailed like any other sloped insulated roof. If ventilated, it needs ventilation chutes -- ideally site-built chutes using rigid material, carefully installed in an airtight manner. Once the insulation is installed, the bottom of the insulation should be protected with drywall, plywood, or foil-faced polyiso.
If space is tight, the sloped roof can be insulated with closed-cell spray polyurethane foam -- with or without ventilation chutes between the foam and the roof sheathing. Spray foam should always be protected by a thermal barrier (like 1/2-inch drywall) for fire protection.
Rafters
Martian says
"The opinion of energy experts for at least 20 years has been unanimous: the insulation belongs at the roof plane, not on the floor of the attic behind the kneewalls"
All the diagrams below for 1.5 story houses show the floor behind the kneewall with insulation on the floor. Irrespective of these link again I ask if the floor behind the kneewall IS insulated and considered a unconditioned space/side-attic, how should the rafter area be treated behind the kneewalls (NOT talking about the slant area @ the top of the knewall)
The area in question is clearly illustrated on the link below and explicitly shows no insulation in the rafters between the sofits and kneewall. My pointed question is Option 1 ventilation chutes be used in this area which then extend into the slant portion and up to the ridge or Option 2 ventilation chutes with cut-in rigid insulation interior to the chutes placed bewteen the rafters then extend into the slant portion and up to the ridge. Option 2 will essentially extend the air barrier already present in the slant area all the way down to the soffit area and prevent this unconditioned side attic space from being under negative pressure and sucking conditioned air out of the house as their is now an air barrier at the rafter level . Depending on code if rigid was used in the unconditioned area behind the kneewall I understand it may need to be covered with .50'' drywall or foil-faced polyiso.
http://www.oldhouseweb.com/blog/wp-content/uploads/2008/11/hq4179_weekly_mshea_ohwblogpic_finattic_bill1.jpg
This is a retrofit scenario. Perhaps this changes your comments as I dont see why anyone in their right mind would remove existing blowin cellouse on the floor behind the kneewalls. 1st links seems to indicate either way is acceptable..Second link seems to show Option 1
http://www.nrel.gov/docs/fy00osti/26450.pdf
Bottom of page
http://oee.nrcan.gc.ca/residential/personal/new-home-improvement/choosing/insulation-sealing/roofs-attics/khi-halfstorey-attics.cfm?attr=4
http://www.homeenergy.org/archive/hem.dis.anl.gov/eehem/picts/9503p31.gif
http://www.oldhouseweb.com/blog/wp-content/uploads/2008/11/hq4179_weekly_mshea_ohwblogpic_finattic_bill1.jpg
http://www.oldhouseweb.com/blog/how-to-insulate-a-finished-attic/
Second response to Chris
Chris,
The air barrier should always be aligned with the thermal barrier. If you want the thermal barrier to be at the kneewalls and the floor of the unconditioned area behind your kneewalls, then you need to establish an air barrier that follows your insulation.
This is tricky but not impossible. The most difficult area in a retrofit situation is the required blocking between the floor joists under the kneewall bottom plate. Each of these pieces of blocking needs to be caulked or foamed in place to establish an air barrier.
Air barrier continuity is also essential at the intersection of the insulated floor joists and the exterior wall, as well as the intersection of the top of the kneewall and the sloped ceiling.
These air barrier details can be quite tricky, which is why most energy experts recommend installing the insulation at the sloped ceiling, beginning at the soffit.
Thanks Martin your last
Thanks Martin your last response is alot more clear. You say "If you want the thermal barrier to be at the floor of the unconditioned area behind your kneewalls, then you need to establish an air barrier that follows your insulation.
So if the air barrier follows the thermal barrier and is established at the floor behind the kneewalls is it still advantageous to create a secondary air barrier in the rafter level over the ventilation chutes by using XPS or foil-faced polyiso. One Energy Consultant that we work with says yes for a myriad of reasons most importantly it will further reduce stack effect where the other energy consultant says that if decent job has been done air sealing in all the same areas you highlight in your article then trying to create a secondary air barrier on the rafter level is unnecessary.
So who is correct any why? Both are Energy Experts that are sanctioned by the state
Third response to Chris
Chris,
The answer to the question is, "It depends."
If there is reason to believe that the air barrier at the kneewall and on the floor of the attic behind the kneewall is imperfect -- as is often the case in a retrofit situation -- then installing airtight rigid material to create site-built ventilation chutes (or a continuous plane of rigid foam under the rafters) would make sense.
However, this work can be fussy and awkward in a tight, confined space. As you point out, the purpose is to prevent the depressurization effect of the ridge vent from sucking conditioned air through cracks in your ceiling.
If the area is cramped and difficult to work in, and if you feel confident that your primary air barrier is meticulously installed, then you are all set, and you don't need ventilation chutes in the attic behind the kneewall.
Response to Skylar Swinford
Skylar Swinford,
This morning I received an e-mail from Don Fugler (thanks, Don) questioning your suggested use of open-cell spray foam against roof sheathing in a cold climate like yours (Idaho).
I think he's got a point. Open-cell spray foam is very vapor-permeable, and I have reported on a case of rotten roof sheathing behind open-cell foam in Montana. It's possible to make open-cell foam work, but you have to be sure that your assembly includes a good vapor retarder on the interior side of the foam. Many contractors spray the cured foam with vapor-retarder paint.
You don't explain the reasons for your suspicion of closed-cell spray foam, but it's important to warn cold-climate builders that the use of open-cell spray foam against roof sheathing can be risky without a carefully applied vapor retarder.
Snow cover
Bill Rose is correct, a uniform snow cover on a roof means all is well with air sealing and attic insulation. I like a 12" energy heel at a minimum for a cold climate with an air chute for each rafter space with vented eaves and ridge. A continuous air barrier, windwash protection and a generous layer of attic insulation complete the assembly.
Low-Density Foam, Not to be confused with cheesecloth
Martin,
The vast majority of spray foam failures are the result of air-leakage issues caused by installation flaws, not diffusion. This holds true for both low-density and closed-cell foam. Voids caused by installation errors that allow interior air to bypass the foam and condense on sheathing are the usual culprits. Another installation defect that can lead to moisture failures is coarse cellular structure. This issue is caused by a number factors that can be attributed to both manufacturers and installers. At any rate, low-density foam should have a very tight cellular structure with good interlaminary adhesion, and it should be soft to the touch. Coarse cell structure will lead to increased vapor and air permeability and potential moisture issues. Did you obtain core samples of the failed low-density foam in Montana that you reported on? I am concerned that an installer without the diligence to require mechanical ventilation in an air-tight home might not be best equipped to handle the responsibilities of maintaining a quality install. Unfortunately no insulation systems are idiot proof, especially spray foam. That much is certain.
I'd say that calling low-density foam "very vapor-permeable" is a bit hyperbole. For example Sealection 500, one of the most common low-density spray foams available today, has a perm rating of 2.3 at a thickness of 10". To achieve an R-38 @ 3.8 per inch we are looking at 10 inches minimum. To reach R-50 thicknesses we are closer to the 13”-14" range. True, it does not meet the code requirement of <1 perm, but its not exactly tyvek.
While low-density installers are sadly prone to skimping on r-value, I'd say closed-cell installers are king of the skimp. In retrofit applications, which are often not subject to the scrutiny of code officials, it is uncommon to find R-38 to R-50 installations with closed-cell foam. I usually see 4”-5” at best. This is most likely due to the high cost of the closed-cell foam, but it may also have something to do with the strong belief among many of its followers that it possess magic powers. In the end, closed-cell costs more, has a much higher embodied energy, and the GWP is off the charts. 2lb closed-cell foam is 4 times the density of .5lb foam, yet it doesn't even deliver twice the r-value.
All this being said, VR primer is dirt cheap. Installing it over low-density foam is extremely cheap insurance, and I wouldn't advise against it. However, the beauty of cathedralized attic spaces is that they are easily accessible for core sampling and moisture inspection. I have had the opportunity to personally inspect over a dozen crawlspaces and attics sprayed with VR free low-density foam (installed as early as 1995 in the same 9,000+HDD climate) and I couldn't find evidence of condensation at the rim or roof sheathing. I'm most concerned about my one-component foam patches causing problems than anything else.
Second response to Skylar Swinford
Skylar Swinford,
I agree with most of what you wrote. I especially agree with, "While low-density installers are sadly prone to skimping on R-value, I'd say closed-cell installers are king of the skimp. In retrofit applications, which are often not subject to the scrutiny of code officials, it is uncommon to find R-38 to R-50 installations with closed-cell foam. I usually see 4”-5” at best. This is most likely due to the high cost of the closed-cell foam."
You are also correct that once you install 10 inches of open-cell foam, the vapor permeability problem starts to be reduced.
Nevertheless, Joe Lstuburek and Armin Rudd have used their moisture meters to check roof sheathing at a lot of Icynene-insulated cathedralized attics in Massachusetts, and they've seen signs of moisture accumulation in the sheathing. No one needs the headache of worrying about sheathing rot.
So my advice is: in a cold climate, use closed-cell foam, or open-cell foam with a carefully installed layer of vapor-retarder paint.
Open Cell
The other big issue with low density foam is that it expands so quickly and vigorously that it often traps large voids inside the foam structure, especially at corners and geometry transitions. I've been hearing from the smart people that it's critical to thermally image a low density foam installation to find those voids and fix them, they aren't visible from the surface.
But that's a problem. If a material can have a significant installation error that isn't visible without expensive and specialized equipment, it's a situation ripe for abuse and problems.
Icynene Issues
Jesse,
"If a material can have a significant installation error that isn't visible without expensive and specialized equipment, it's a situation ripe for abuse and problems." If you want ensure a quality installation It is equally important to thermally image all insulation installations, especially in an extreme climate. Luckily, as Bill Rose and others have pointed out, flaws such as ice damming are quickly evident in snow country. That is why I recommend a foam contractor with a proven installation track record in an extreme climate. Do people even ask for referrals these days? Saving a few cents per SF going with the low bidder is never worth the risk, regardless of the insulation type. It is vital that the low-density foam is sprayed in layers rather than in super thick passes. You know those videos you see online of spray foam getting installed in one quick easy pass? Well if you see this technique on your jobsite, get real nervous and start taking core samples. It is also important to use a high quality foam with superior interlaminary adhesion. This allows the product to be effectively installed in multiple thinner passes. The installation characteristics of spray foams, especially low-density technologies, vary widely from manufacturer to manufacturer. Closed-cell foam, is just as prone to installation errors as low-density foam, especially when installing in an extremely cold climate.
Martin, Icynene has nearly twice the permeability as Sealection 500. There are many questions to ask about Rudd and Lstibureks investigations. Did moisture levels in the sheathing change with application thickness? Did elevated interior humidity play a role? Were elevated moisture levels consistent throughout the roof assembly? Despite all the snow, the inter-mountain west has an extremely dry climate compared to Massachusetts. Undoubtedly, this is a beneficial characteristic from a building science perspective.
Factors in houses with moisture accumulation in roof sheathing
Skylar,
Your questions are good ones: "There are many questions to ask about Rudd and Lstiburek's investigations. Did moisture levels in the sheathing change with application thickness? Did elevated interior humidity play a role? Were elevated moisture levels consistent throughout the roof assembly?"
Here's what I know: the thicker the foam, the lower the foam's permeability, and therefore the lower the chance of moisture accumulation. In some house, elevated moisture levels were observed on north roofs but not south roofs, a sign that some drying to the exterior is possible on south roofs.
Your point about elevated moisture levels is correct: the higher the indoor humidity level, the greater the chance that the roof sheathing will accumulate moisture.
But builders can't depend on homeowners to operate their houses according to best-practice recommendations. Owners do all kinds of crazy things. I always advise builders, "If you are depending on owners to maintain a certain level of indoor humidity to prevent your walls or roofs from failing, you are too close to the cliff. It's time to choose a more robust building assembly."
Dramatic Over-Simplification
Martin has a tendency toward over-simplification and one-dimensional thinking on many issues, and roof ventilation is one of these. Adequate, balanced and complete roof ventilation not only limits or prevents ice dam formation but also reduces summer radiant heat gain, extends the life of composite roofing materials, removes vagrant moisture, and dramatically increases the durability of the roof deck by creating a drying potential that simply doesn't exist in a hot roof.
To suggest that "In the world of ice-dam prevention, ventilation is capitulation" is to ignore the long history of the success of roof ventilation as a primary strategy for prevention or reduction of ice dams and the fact that almost all building scientists have promoted this strategy.
That one of those experts, Wayne Tobiasson, has now "backed off" a bit from his previous advice because of a trend toward increasing insulation levels does not negate the value of roof venting AS PART OF A TOTAL STRATEGY.
No one but a fool would suggest that roof venting can compensate entirely for woefully inadequate insulation or air sealing, though it would certainly improve an otherwise intolerable situation.
And to declare that an imbalanced exhaust-only or exhaust-dominated roof venting system can create negative pressure issues is simply to state that poor design and installation is a problem – an obvious and trite conclusion that applies to every facet of house construction.
The primary problem with roof venting as an ice dam control strategy is, as others have pointed out, that complex roof geometries undermine the continuity and integrity of venting. For this reason, an intelligent designer of cold- and snow-country homes will use the simplest roof geometries that allow complete and uninterrupted venting and easy shedding of excess snow.
Martin states that "No one needs the headache of worrying about sheathing rot", yet he fails to note that the most effective strategy to avoid roof rot is to create a viable drying potential at the roof plane. And the most effective way to accomplish that is to fully vent the roof. Roof venting has become more, not less, important now that vapor-impermeable roof membranes and highly vulnerable OSB sheathing have become commonplace.
Obvious and trite?
Robert,
I'm sorry if my summary of the causes and solutions to ice damming seems obvious and trite. To you, these observations may, in fact, be obvious and trite; to others, they may be useful.
We certainly agree on the advisability of including ventilation between the top of the insulation and the roof sheathing. That's why I wrote, "This type of roof ventilation often makes sense. It’s a kind of insurance."
I guess our main point of disagreement, if there is one, is that you see roof ventilation as "a primary strategy for prevention or reduction of ice dams," and I see it as a tertiary strategy. But really, Robert, I think we agree on most points.
Martin You Misrepresent
Martin,
I did not say that your entire argument was "obvious and trite", but used those terms only in reference to your statement that poor roof ventilation design can cause problems - since poor design or any sort can cause problems.
My issue with your presentation is that you don't simply present roof ventilation as a "tertiary" strategy but as an example of a surrender of good building design. You have gone to considerable length to paint roof ventilation as a path of ignorance, and have completely ignored the many facets and functions of roof venting.
This kind of one-dimensional thinking and deliberate deprecation of a valuable part of good cold-climate roof design does nothing to improve the level of knowledge in the building community.
And more so...
An example of the disingenuousness and counterfactual nature of your entire presentation is your assertion that:
"Very deep snow acts like insulation. If your roof is covered with two feet of fluffy snow, the bottom of the snowpack is insulated from cold outdoor temperatures. That raises the chance that melting will occur."
All snow insulates, and the shallower the depth the greater the R-value per inch. Most new snow has a water content of 7% to 12%, a density of 4.4 pcf to 7.5 pcf, and an R/inch of 3.7 to 2.8. As snow ages and accumulates (and increases in density), it's R/inch decreases to 1.15 (@ 30% MC).
This means that a roof assembly insulated to R-38 will experience melting temperatures with as little as 4-5 inches of fresh snow or 11" of old snow when the outside temperature is 20°F. An R-49 roof assembly will begin to melt snow at the same outdoor temperature with as little as 5"-6" of new snow or 14" of old snow.
In other words, almost any hot roof in modest snow country will experience melting temperatures at the roof plane for much of the winter. This does not suggest that hot roofs are a sensible alternative to a well-vented roof.
There is simply no substitute to a cold roof to prevent ice dam formation, and the only way to achieve a cold roof is with roof venting.
Snow country
Robert,
Once again, Robert, we agree -- which is why I wrote, "if your climate is very snowy, you probably want to stick with a cold (ventilated) roof."
Deadhead Cavities and Open-Cell Under-Roof
From Skylar: "Typically, adding cavity ventilation to a complex roof loaded with valleys and dimensional framing will not completely prevent ice damming. Much of the time the complex roof design leads to deadhead cavities that don't interconnected to the ridge vent and soffit vent."
My home falls into this category -- partially finished attic space, complex roof with about 50% of the rafter cavities not reaching the ventilated space above. I have 2x8s rafters and I was planning to insulate with open-cell foam (my fear about closed-cell was that it's lack of water permeability would mask the inevitable roof leak).
This is a retrofit in Saint Louis, which I believe is zone 4 (almost 5). Assuming the choice of open-cell is the right one (and please tell me if it's not), I'm assuming I'll want some ventilation along the roof sheathing (proper vents?) whether the cavity reaches up to the ridge vent or not. Those cavities all connect to the soffit and should offer at least a little air flow to remove vapor moving outwards and dissipate heat that might cause a dam?
With that small an amount of foam, need I be more worried about moisture moving from the warm-in-winter inside to the roof sheathing? My assembly would be:
painted drywall > 7 inches of open-cell > vent (50%+ chance of poor flow) > roof sheathing
Any advice is greatly appreciated.
Arlington Superinsulation Retrofit Project
Hi Martin--very nice column.
In case it is of interest anyone, the owner of the Arlington Superinsulation Retrofit Project did a walk around town in January 2009, photographing various roofs (including his own) and their snow buildup. He is in a neighborhood with many identical houses marching up the street--so he could directly compare his roof to his neighbor's. The superinsulation retrofit job shows a hot roof working quite nicely--the assembly on his project is 6" of polyisocyanurate (2x 3" layers), with open-cell spray foam (2x8 rafter?) underneath.
http://superinsulating.blogspot.com/2009/01/snow-melt.html
Ventilation to prevent ice dams is a darn good idea when the snow loads get large. I believe that Wayne Tobaissen (and Joe) recommend it at ground snow loads of 50 pounds/square foot or greater (as per the IBC map).
no icicles is better than some
Kohta,
Those blog pictures brag about the few icicles on the superinsulated hot roof. In thirty years of building superinsulated homes with fully ventilated roofs, I've had no icicles form. There is no better method for mitigating ice dams than a tight, well-insulated and fully vented roof.
Martin is just plain wrong about this.
"hot roof"
Kohta,
How well does your ventilation perform when you have several feet of snow covering your ridge-vent? Are building a "cold-roof"? No matter how well the roof is vented or insulated, there are various climatic and solar exposure factors that can lead to small icicles forming on a roof.
Robert, Robert
Robert,
My blog said that ventilated roofs often make sense, and that hot roofs should be used only if you don't live in snow country. So I think we're agreeing!
Cold Roof in MT
I am a homeowner not a scientist.. I gather that the best option for a cold, snowy, low humidity place like Southwest Montana would be a cold roof.
And a good way to acheive this in a one story, 1930's bungalow remodel might be to spray foam the entire attic deck (especially the top plates of extrior walls and into the eaves) with 1" of foam to contain all warm air leaking from the interior, then blow in 20" deep cellulose and make sure that there is proper ventilation in the attic via gable end AND ridge vents?
Response to JP
JP,
Your plan has only one glitch: it's much better to provide balanced soffit vents and ridge vents than to use gable vents. You should probably fill in or block up your gable vents.
Be sure to install rigid site-built ventilation chutes (allowing for at least 1 inch of air flow) in each rafter bay at your soffit area before you install any spray foam. You want clear ventilation channels from your soffit vents to the ridge vents.
Response to Martins suggestion to me
Thanks Martin. For site-built "chutes" could I just nail 4x8 sheets of foam board to the underside of the rafters, beveled on the lower end so it can tuck right into where the back of the bird mouth on the rafter sits on the top plate? Then it would vent throuh holes in the friese blocks between rafters. Of course those will be drilled and screened for bugs.
Regarding your suggestion to cover up the gable vents, my ridge vents could be covered with 1 ft of snow.. .wouldn't that keep the air that is drawn through the friese block vents from exiting the ridge.
Thanks for the help.
Second response to JP
JP,
You can use foam board to create your ventilation chutes, but you still probably want to create a separate chute for each rafter bay. Otherwise you probably won't have enough room for thick insulation over the top plates of your exterior walls.
Many builders tack 1x1 sticks into the corners of the rafter bays, up against the roof sheathing. Insert the rigid foam against the 1x1s and caulk or foam the edges.
My ridge is also covered with snow during the winter. Fortunately, snow is not an air barrier, and some ventilation still occurs. Moreover, even if you don't have full ventilation during the coldest winter months, the soffit and ridge venting system is still useful during the milder periods of winter.
Buldling the chutes "insde"
Buldling the chutes "insde" the rafter bays with blocking makes sense. That framing/drywall interface from many years ago is surely a week link... however, FWIW all exterior walls have 3.5" of spray foam all the way up from Phase 1 of this project.
Thanks again.
ventilation
A white flag calling ventilation defeat. I'm a BPI energy auditor, a BPI building envelope specialist and a builder/remodeler in the western Colorado Rockies. Also, as I write this, I have a house that was featured yesterday for energy conservation, part of the 10/10. Yes, adding more insulation is important but equally important is getting the airflow from the soffit to the ridge. On the 40 year old house, I added soffit vents that never existed, I added a vented ridge that never existed and before my insulators pumped the insulation up to an R50, they added rafter baffles in every space between the the trusses.
It's interesting you are using Building Science Corp as a credit because they are all about insulation and ventilation. Seal it tight, ventilate it right.
I have to say Martin you need a bunch more education before you post articles such as this.
Shame on Fine Homebuilding for even linking to this article
Build Tight Insulate Right
As a certified Old Guy, I've been building in Northern Minnesota for...oh gawd let's not talk about that...and high levels of roof performance have always been a primary component of my work.
INSULATION - the world has shifted if the past few years since spray foam has come int its own. I usually end up doing vaulted roofs and have insulated with fiberglass for a long time. I've developed a method of building down the roof frame to allow just about any cavity depth you want. Myown roof is framed with 2x10 but has 14" of fiberglass and two inches of vent space above that. This works pretty well. But there is no doubt that the foam hi-density is good for some applications, lo-density better for most applications, will seal things up around every little cavity and wire and HipValJack. Be as fastidious as you might, you just can't cut fiberglass to fit like that.
TIGHTTIGHTTIGHT - I usually tell people that my goal would be that if the house was filled with water to the ridgeling, none would leak out. Well...OK that's not totally realistic, but it IS a goal. My clients would usually get pretty restless befor i was finished with the vapor barrier, caulking and taping the elec box es, sealing to the floor, going thru lots of boxes of caulk. Again, the foam has changed all that. You won't get airleakage around electrical boxes, for instance, because no air flows thru the foam.
VENTILATE - Now here is where I take issue with the author. A home that is vented properly will not get ice dams [if there is any such thing - more on that later] . Of course you need enough insulation, that's obvious, but even with high levels of insulation the heat does migrate through the insulattion membrane. Those insidious little BTUs just have to get to where it's colder. If the little buggers get to a channel of air they are perfectly happy moving on out the ridgevent causing a minimum of problems. Otherwise the BTU will just lay there on the underside of the roof deck making it warmer and warmer and melting the snow and...yup, you got it. So you have to move out heat that gets to the roof deck. My roofs, I am proud to say, do not get ice dams if the client allows me to do it my way. Another factor you might consider is hot weather in the summer, a condition where the roof vent does you just as much good. Roofing can reach 150 degrees, but if you have cool soffit air floating below the roof deck, once again those delinquent BTUs are carried out the riudge vent. In a hot roof in those conditions you are cooking your shingles and that can radically reduce the life of the roof.
Whew!! I'd better let someone else talk.
Ventilation is a good idea
This is what I wrote: "Roof ventilation often makes sense. It’s a kind of insurance. ... Ventilation should always be the third, not the first, weapon in your arsenal."
I'm not against roof ventilation! Just be sure to address air sealing and insulation before you tackle ventilation.
Ice Dams
Oh yeah, forgot the semi-mythical ice dam. Well, since the 70's I've been seeing that same little drawing with the shingles, the mound of ice, and that pool of water. Thing is though, I've never seen that pool of water in real life. Some astounding ice formations, that's for sure. Up to twelve inches thick and weighting down the eaves with who knows how many hundreds of pounds. And I've seen the wet ceilings too, the work of those errant BTUs as described above.
But how does the water get thru the roof membrane then? My contention is that heat energy flows through the roof, melting the snow which then refreezes at night or when temps drop. As the ice forms it expands and forces itself between the shingles. When the temps rise and the heat continues to flow out of the building to the roof deck, the ice that has worked its way through the shingles melts, and the ceiling gets wet.
It's all about those pesky little BTUs, They are full of the same misguided energy you find in juvenile delinquents. And the solution is a nice straight ventilation channel sitting atop a substantial and exquisitely formed insulation membrane.
It's all much more likely to work right if you build it right.
Chimneys routed through attic space
I, too am not a scientist, but merely a conscientious home-owner, self educated owner-builder, but of all the dialogue here and within the multitude of tomes I've read in the past regarding homebuilding and insulation, nowhere have i seen the following issue addressed. How do you handle the problem of the heat generated from a properly constructed chimney of say a masonry furnace, passing through the attic and releasing heat, that thus affects the attic space, thus warming the roof envelope causing ice damming, etc. No amount of sealing or insulating is going to keep melting from occuring. My inspector made it a non-issue as long as my clearances to combustibles were adequate on the chimney. What do you guys think? Build an insulated chase around the chimney as it passes through the attic? or what?
Insulating a chimney stack
I have ice dams and I am convinced that the primary cause is the brick chimney stack is heating the attic space. I've vented like crazy and still I get the ice dams in valleys relatively close to the chimney and in valleys on the North side of the roof (no sun).
I've been fearful of insulating the chimney because I don't want to create a fire hazard. We use the fireplace insert to add heat to the home quite a bit. Is there a safe way to insulate the brick chimney?
I live in lower Michigan.
Insulating a chimney stack
EXACTLY! Let's hear from some of these experts...
Insulating a masonry chimney
Brian and John B.,
It's not only possible to insulate a masonry chimney in an unconditioned attic -- it's an excellent idea. A warm chimney means a warm flue; warm flues draw better than cold flues, and (if you are burning wood) are much less troubled by creosote formation. (Creosote begins as a liquid condensate that forms on the colder sections of the flue.)
You want to leave an airspace of 2 inches between your insulated wall and the chimney. You can build your wall as 4 panels; if enough room is available and the access is decent, you can build the panels on the attic floor. Install drywall on the side of the wall facing the chimney; in a tight attic, you may have to depend on adhesive to attach the drywall to the studs.
More insulation is better than less. After your new stud walls are in place -- drywall facing the chimney, fiberglass or mineral wool batts between the studs -- you can install a layer of foil-faced polyiso on the side facing the attic, and (if required by your local inspector) another layer of drywall.
Response to Rick Lawrence
Rick,
I'm sorry that you were disappointed by my article ("It's interesting you are using Building Science Corp as a credit because they are all about insulation and ventilation. ...I have to say Martin you need a bunch more education before you post articles such as this.")
However, your critical comments were balanced by those of Kohta Ueno, who posted a more favorable reaction: "Very nice column." Ueno has a master's degree in Building Science -- he studied with John Straube -- and is a project manager at Building Science Corporation.
preventing ice dams on top of vaulted ceiling
I am a cabin owner in central Utah, not a builder. My problem is that every year ice dams form on the roof in the valleys and against the chimney and I get spectacular icicles. Last year, some metal on the roof and the flashing around the chimney was torn away by ice getting underneath and by large chunks of ice falling off the roof in the early spring (my husband came off the roof with one of those large chunks-he was trying to break up the ice dams). As a result, we had a lot of water come down the chimney and into the fireplace. The roof is on top of a cathedral ceiling reaching 23' high and is metal. I have read some of the comments here and have not found any dealing with heat strips. We have a contractor who is recommending placing them on our roof to create tunnels to allow melted snow to escape. Does anyone have suggestions on how to prevent ice dams on a cathedral roof and does anyone have experience with the heat strips. No more getting on the roof to breat up the ice dams.
Response to Linda J.
Linda J.,
I'm afraid I can't recommend heat strips except as an emergency remedy to get you through the winter until weather improves in the spring, allowing a permanent solution.
Your ice dams are evidence that your roof is leaking a lot of heat. If you plug in some heat strips, you'll just be wasting more energy than ever.
My guess is that either:
(a) your cathedral ceiling includes air leaks, or
(b) the insulation in your cathedral ceiling is insufficient, or
(c) both.
The solution will not be cheap. First, you need to diagnose the problem, and that may require a blower door test. I suggest that you consult with a home performance contractor or energy rater, preferably one certified by RESNET or BPI.
You may need to do air sealing work or to re-insulate your cathedral ceiling.
Good luck.
More Vent Stories
I have also had some projects with blocked & no-way roof cavities that were....well, I can't say solved, but ameliorated. 1] A hot roof, mediocre vapor barrier, moisture in the cavity, no way to do soffit vents. We cut in a ridge vent and with only an outlet [no soffit vents] the cavity cleared of moisture. Gonna re-roof that one soon and we'll see how the solution worked in the long term. 2] vent chase blocked by look-outs going back to the first layout rafter. I drilled three [or was it four?] 3/4" holes in the lookouts. Not nearly enough airflow as required, but those cavities work well, no ice dams, no premature shingle curling. 3] Progress!!! There are several new vent systems for difficult places. Check out core-a-vent.com, but there are other manufacturers too. applications include a top vent where a roof meets a wall, a shingle-in vent for the soffit, and several others.
Response to Tom Bathelemy
Tom Bathelemy,
Your experience is typical. Builders know, from long experience, that improved ventilation can help solve an ice-dam problem.
I hope, however, that my analysis reminds readers that most of these problematic roofs probably have heat leaking through the ceiling. That's why there's an ice dam problem. While it may be possible to ventilate the heat away, it's always preferable, if possible, to try to find the heat leaks and plug them up. That means air sealing and insulation improvements should come first.
soffit retrofit
Perhaps I can entice some comments on my house: Bought 1960 ranch house 3 yrs ago. Roof pitch 6;12. Saw that the 2 x 6 clg joists were about 1/2 full of cellulose so I hired an insulator to add another 10". Next Spring I decided to remove my ugly 16" deep alum soffit panels. These were placed over orig 3/8 plywd soffit which had 6x 10 vent opngs @ 8' cc. Removed all plywd and saw that insulator had jambed FG batts tight to wall plate/roof deck and only vented every 4-5 bays w/ poly vent. I then removed all the stuffed batts from the exterior, cleaned out around top plate and gently pushed all the loose cellulose in toward house. Installed new poly vent in each bay, 4' long tight to roof deck. Infilled void above top plate and where cellulose was missing w/ loose batts. After all this I had the insulator back to replenish the eve condition and generally add a bit more everywhere. Finally, I installed new vented soffit, a composite wood type w/ continuous slots. Next winter I was only house on block without ice problems and I had full snow cover long after the neighbors. (is that a good thing?)
My point is I guess that there are millions of homes out there that need this type of intervention. It is very difficult to do without removing the soffit. The critical area is the top plate where most builders left us w/ precious little space to set things right. Worse are all the millions of homes like my nieghbors; hip roof w/gutter tight to brick; no soffit, no vent. How on earth are these roofs supposed to function?
Response to T.Gray
T. Gray:
Q: "Next winter I was only house on block without ice problems and I had full snow cover long after the neighbors. (is that a good thing?)"
A. Yes.
Q. "How on earth are these roofs supposed to function?"
A. Actually, in most parts of the country, unvented roofs can work fine. (See Kohta Ueno's Oct. 6 post on this page for a description of a Massachusetts home with a successful unvented roof.) However, they only work if (1) there is a good air barrier to prevent interior air from escaping through the ceiling, and (2) if the insulation is thick enough -- at least R-50 or R-60 in areas of the country plagued by ice dams.
Concerning your retrofit work: it's too bad that you didn't install a wind-wash dam above the top plates of your wall when you had your soffits open. Fiberglass batts are air-permeable, and they can't be used as a wind-wash dam. In this location, you need cardboard, rigid foam board, solid lumber, or spray polyurethane foam between the top plate and the bottom of your ventilation chute, to prevent outdoor air from filtering through your attic insulation and degrading its performance.
ventilation redux
Martin - as you say, venting will prevent ice dams but sometimes at the cost of energy efficiency. thing is, the roof where I drilled the pitifully inadequate holes thru the lookouts already had lots of insulation - done in the early 90's so it consisted of 14" of fiberglass, but that's not so slacky. Ice dams were not an issue there, but a couple other bays that were vent-blocked by skylites had premature shingle degradation.
My conclusion is that venting works for you in several ways. You were hasty to call it a white flag.
response to martin
Thanks. Yes I could have tacked up a wash dam carefully scribed to the profile of the 14" wide chute and then close all gaps w/ spray foam. With 120 lf of soffit I guess I just said it has to be good enough. My concern is if what I did was correct and recommended how on earth could I convince a normal homeowner or typical insulation contractor to do all this?
On the 2nd question about the hip roof you refrerred be to Kohta's post- but that is dramatically different- 6" polyiso above deck and spray in each rafter bay. I am talking about a basic builder home, hip roof, no soffit, batts @ ceiling plane, unconditioned attic with no intentional venting. You could never make that right without removing gutter, fascia, fix up eve condition (pinch point) reinstall gutter and fascia w/ venting. By your comments above you might recommend removal of all batts, air seal at ceiling plane then spray the deck and eves to R38 with no venting?
Second response to TGray
TGray,
Plenty of unconditioned attics work fine without perfect soffit-to-ridge venting. Some have gable vents, and some have no vents or incidental air leaks that function a little bit like venting.
If the ceiling is sealed against air leaks, so that humid indoor air can't enter the attic, such attics can perform well. If you want to prevent ice dams, though, you certainly need a well-sealed ceiling -- no air leaks! -- and very deep insulation. I'm partial to R-50 or R-60 cellulose.
Missed issue...
I have read (most) of the above comments, and still don't have an answer for my specific roof. I live in sunny Southern Colorado, in the mountains. We get a lot of sun, but a lot of snow. My house has a 5/12 pitch, but one side is southern oriented to get the maximum passive solar benefit. The drawback, is that half of my roof is northern oriented. With charcoal colored shingles, the south side melts off, heating the roof, and assumable the attic space, while the north face gets no sun, and is buried in up to 3' of snow. Combine that with a chimney running into the attic space, and you have 2 separate heat sources, that aren't mentioned above on how to best manage them. There was also no mention of ice melt cables anywhere. I understand the 4 basic steps to solve the ice dams, but if the logistics of the roof (orientation, color) and the physical aspects of the attic (chimney) all provide heat into the attic space, then what is my best option to resolve my north face ice dams? By the way, thank you for your assistance. As I've read above, there's a million "experts" out there, all claiming that they know the only way. I appreciate your objectivity and assistance.
R.
Response to Anonymous
Anonymous,
If your analysis is correct, and the only two significant heat sources for your attic are solar gain and a chimney, here are your options:
1. You can certainly insulate the section of your chimney that passes through your unconditioned attic. I described details in my October 12 comment.
2. If the solar gain through your south roof is still enough to melt snow on your north roof, then you can either experiment with improved ventilation, or you can install spray polyurethane foam insulation on the underside of your north-slope roof sheathing.
anonymous - ventventvent
If you have enough insulation, then the solution to your Colorado roof is to ventilate the cavity - preferably with a ridge vent, to get rid of the sun's heat. Ventilation, Insulation, tight construction - all three are parts of the package and it is real unwise to cherrypick one or two of them.
Thanks
Thanks, Martin for the concise response. This site is great help to alot of folks!
What do we do about flat roofs in the city that have ice dams?
Do flat roofs have the same causes for ice dams (insulations, lack of ventilation etc.)? What do we need to do to correct the leaking usually seen in one corner of the home? Do we also need to add insulation?
Response to Anonymous
Anonymous,
Seal air leaks in your ceiling plane and add insulation.
Most flat roofs aren't ventilated, and shouldn't be.
Who do you call
What type of person do I call to look at fixing the air leaks? Is this anyone who does insulation? I have a one and a half-storey - no attic, so should I wait until I'm going to replace the roof (due anyway) and then get a separate insulation person to come first and do step 1?
Thanks for any advice you can offer.
Anne
Response to Anne
Anne,
The type of contractor you are looking for is called a home-performance contractor, a home energy rater, an energy auditor, or a blower-door contractor. Whoever you hire should have (and use) a blower door.
You can ask your state energy office of your local utility's energy conservation office (if your utility has one) to identify a local contractor with a blower door. Or you can visit the Web sites of RESNETor BPI -- click the links -- and search their databases for a contractor near you.
Half-hot roof
I just had my cape-style home reinsulated. In the side attics we went with 7.5" open cell spray foam in the rafters from the soffits top the tops of the knee walls. Above the sloped and horizontal ceiling is 6"-8" of cellulose. Airsealing was performed. The top attic has a vent in each gable. So the top half of my roof is cold and vented (perhaps inadequately) and the bottom half is unvented. Roof pitch is 7/12.
This winter has brought near record snowfall to northern New Jersey and I've got a lot more snow accumulation my roof than most of my neighbors. But I've also got ice dams and most of my neighbors don't. Those houses aren't capes though, and my overhangs are wider. There's a lot of different factors involved I suppose.
I've been observing things daily and it appears the snow is melting from the top half slightly faster than the bottom half. I suppose this means I should try to increase ventilation in the top attic. If I'm right, how would you go about it? And if I'm wrong?
Response to Eldan
Eldan,
You don't need more ventilation; you need more insulation (and possibly air sealing work).
6 to 8 inches of cellulose isn't much -- that's about R-21. Much less than minimum code requirements.
Call back the cellulose truck! Your open-cell spray foam could have been thicker, too -- its only about R-26.
Response to Martin, #63
Martin,
I think the fact that there's still many inches of snow on my roof today while my neighbors' roofs are nearly bare or have the shingle pattern visible indicates that we've done a relatively good job air sealing and insulating. The ice dams may just be this year's anomaly but of course I'm seeing them as bitter irony.
I forgot to mention that the 8" of cellulose in the top attic is on top of the old fiberglass. I'm not sure what the total R-value is. In the sloped ceiling with 2x8 rafters the old fiberglass was removed and replaced with cellulose. Obviously there's no room for R-49 there no matter what I do. There will always be a band of minimum insulation in the middle of my roof. How does that impact the four solutions?
Another response to Eldan
Eldan,
It's hard to diagnose your problem over the Internet. Here are some possibilities:
1. It's possible that your ceiling still includes air leaks that are heating your roof sheathing.
2. It's possible that the band of R-26 insulation is allowing enough heat to reach your roof sheathing to cause problems.
If you can't afford to add more insulation to your roof (for example, by installing rigid foam insulation on top of your existing roof sheathing, followed by new roofing), you may have to live with the occasional ice dam. Installing wide Ice & Water Shield will minimize damage to you ceiling from roof leaks.
Flat roofs
It was not uncommon for flat roofs to be constructed with voids, or attic spaces, certainly those of a certain vintage. Drainage slopes were often constructed from separate framing on top of the primary structure, and these spaces were not always vented, as they probably should be. My own house, built around 1950, has this type construction. When the existing built up roof membrane is due for replacement my intent is to remove the slope framing and install sloped rigid insulation on top of the roof joists and install a two ply SBS membrane. This will eliminate the unvented void under the membrane, increase the insulation and create the slope to drain to the scupper location.
It is unclear to me if the person in post #58 is having leaking inside the home in that corner, or if there is water spilling over the edge of the roof, or at a scupper drain location. If it is leaking inside he house I would inspect the roof for obvious damage and soft spots. The junction with the parapet is always due for scrutiny. I currently have a location on my roof where it appears there is a hole in the membrane at the toe of the metal flash over the cant strip. I believe this is the source of the water infiltration I was seeing inside this fall.
Icynene roof deck, peel and stick membrane, climate zone 4
I am building an unvented attic/cathedralized 2nd floor with icynene on the roof deck. Inspector insists upon the "peel and stick" membrane from the eave up several feet up the roof--that is, enough to cover a portion of my insulated roof deck. This seems to be both unnecessary--the entire roof will be cold and won't create a melt/refreeze condition--and dangerous--won't the roof "want" to dry to cold/low RH exterior in the winter but be stopped by the membrane?
Roof has a 14/12 slope, which would seem to further mitigate ice damming. Should I continue to push back with the inspector.
Thanks for any advice.
Response to Jon
Jon,
Just because you are insulating with Icynene doesn't mean you can't have ice dams. How much Icynene will you install? What's the R-value?
Also, what's your climate?
You wrote that you plan to install "Icynene on the roof deck." That's unusual; are you sure you didn't mean to write UNDER the roof deck?
Icynene-insulated roof decks usually dry to the interior, because Icynene is vapor-permeable, and because most types of roofing are not very vapor-permeable.
Roof Insulation Retrofit
I am insulating a roof under a laundry room which has had extreme ice dam formation. I live in far NE PA. My roof is metal with snow brakes. I am installing 4 inches of XPS spay can foamed in place with a 1.5 inch air gap below the deck. There are roof vents cut in below the ridge. Also will have 2 inches of polyiso strapped across the bottom of the rafters. The XPS extends over the top plate and sealed with foam. This will make the attic space a unheated storage area. Will this be sufficient to stop the ice dams from forming? I had to replace the gutters twice before and then I added the snow brakes. I still have my gutters but I have 4 foot icicles too. Any comments and insights would be appreciated.
Response to Charles Scarborough
Charles,
It's impossible to be sure from your descriptions whether the work you propose will prevent all future ice dams. A few comments:
1. XPS is different from "spray can foam." XPS is extruded polystyrene, a type of rigid foam that comes in sheets.
2. It's hard to determine what your final roof assembly R-value will be, because you haven't identified the foam you are using. Two inches of polyiso has an R-value of about R-13. You are in NE Pennsylvania, which is either climate zone 5 or climate zone 6. If you are in climate zone 6, then the 2006 IRC requires a minimum of R-49 in your ceiling. That means that after installing the 2 inches of polyiso, you still need an additional R-36.
3. Your plan to install 4 inches of "spray can foam" won't meet R-36, since that would require your "spray can foam" to have an R-value of R-9 per inch -- an impossible value. It sounds like you need to increase the R-value of the insulation you plan to install.
4. Your plan will only work if you succeed in installing an effective air barrier at your ceiling plane. I suggest you do what it takes to add R-49 to your ceiling.
Roof Insulation
Martin. Thank You for responding. I apologize for not being clearer. What I meant to say was that there will be 4 inches of XPS cut to fit between the rafters and that they will be spray foamed in place from a can at the edges. I looked at the map and I believe I'm Zone 6. Will the Polyiso be enough of an air barrier across the rafters? I could possibly add additional layers to up the R-value as there is room to fit it. With 4 inches of XPS and 2 inches of Polyiso I believe that is R33. Another 2 inches will bring it to R46. Close but not to code. Will I gain any extra R value with the reflective side down towards the attic? The information mentions an additional R value gain. Thanks for your time and I am sorry for my poor description previously.
Response to Charles Scarborough
Charles,
Upon re-reading your original question, I now understand what you have in mind.
Yes, your plan will work -- and the polyiso will make a good air barrier, as long as the seams are taped. If you install 4 inches of XPS and 4 inches of polyiso, you will be close to code requirements, and you should greatly reduce your chance of ice dams.
Is there any reason you don't want to use polyiso between the rafters instead of XPS?
Insulation
Martin, I am concerned that if a roof leak ever occurred that the polyiso would absorb water and possibly be a problem especially if it happened during the cold months where it could refreeze in the insulation. Maybe this scenario isn't possible. Since this assembly will make it difficult to determine when a leak occurs I thought XPS would send the water down the rafter bay without absorbing any. I realize that I would possibly see any leak at the soffits but how long the leak existed before I noticed it concerned me. I appreciate all your knowledge and advice that you freely share with the rest of us. It is much appreciated.
Knowledge About Roofs & Ice Dams
I'm amazed by the depth of the discussion here ... and now I know I need to learn more & find some experts from Canada/Midwest to help my readers understand these problems where they're VERY important as NH isn't anything like what most of you are talking about.
I totally get that you start with sealing, then insulation plus ventilation or you'll end up with moisture problems in the attic. What I don't understand is why there's no discussion about roof ice melt solutions like the one offered by Bylin Engineered Systems (described at http://icemeltne.com/ice-dam-prevention-technology/).
In my mind, you first want to prevent the heat loss but knowing you can't stop (except cold roof) all the heat loss, you next want to prevent ice dams so beyond removing snow, there are ice melt solutions or metal roofs.
PS My readership is homeowners, so in lay terms I've written a series of articles and welcome comments (or send me an article to add to the series) ... http://www.hometips4women.com/ice-dams-why-they-happen-why-you-dont-want-them
No, Tina -- no!
Tina,
In my article, I described why ventilation and rubber membranes are a form of capitulation, chosen by contractors who have given up any hope of stopping heat from escaping from your home. But I failed to explain the obvious: even worse are contractors who solve the problem by INCREASING the heat escaping from your home.
You have provided a link to a company promoting "heating panels delivering 36 watts per square foot" for installation on top of your roof. As I often write -- run, don't walk, away from such contractors.
If a homeowner installs just 40 square feet of these advertised heating panels, they'll be wasting the same amount of electricity as would be required to provide all of the space heat for a Passivhaus building.
It's hard enough these days to convince builders that we need to make our buildings well insulated and tight. I don't think I have the strength to battle the idiots who want to attach electric heating panels on top of our roof shingles.
Great article. I agree that
Great article. I agree that too many people address the symptoms of ice dams and not the cause; however I disagree with the "ventilation and rubberized membranes should be the last weapons in your arsenal." statement. Proper ventilation and an ice dam protection membrane are required by the model building codes and most local building codes. They should not be considered "the last weapons in your arsenal". They should be included into the design from the very beginning. What I am trying to say is; they are just as important as air sealing and insulation to the prevention of ice dams (ventilation) and roof leaks (ice dam protection membrane).
Again, great article. It is one of the best articles I have read about preventing the formations of ice dams.
Michael H. Lichy
RC Lichy & Associates, Inc.
Response to Michael Lichy
Michael,
Residential building codes do not require ventilation for all roofs. In the 2006 International Residential Code, for example, the steps necessary for unvented roofs are set out in Section R806.4.
Retro 1964 hip with dropped soffit
In 2006 I did all the painful sealing of top plates on a 4:1 single level ranch (mine). This took considerable effort to reach with a hoe and vacuum and my longest 36" foam gun just to catch edge of holes in plate. Then I stripped off the vinyl siding and added 2" EPS not knowing at the time (life w/o Utube) that I should have gone with 3-4 more inches of insulation. Walls are 2x4 and hip rafters are 2x6 with old standard notch to bring the soffit down below the plate.
That means I had very little space to add insulation when I blew in 18" of cellulose over the old crappy fiberglass between the ceiling joists. I have a new recycled rubber slate roof with lots of solar thermal collectors and PV so I can't do much with that. I'd love to raise the roof to add higher heel but that would be an engineering feet tipping the roof one side at a time. Yikes!
The big question>>> can I add (if I remove the aluminum vented soffit again, cut off the upper section of my EPS to expose top plate & push back the old fiberglass or new cellulose) enough spray foam (what would be the best?) to stop heat loss at the upper room edges. That's really the biggest heat loss shown on the gun and I see a little mold growing in two North wall corners inside.
I will be taking off the siding again to add at least 3 more inches of EPS and furring strips. Rebuilding the window boxes (again) to warm up the walls. Blower door showed I got us to 1.2 and would love to add some of the new Lunos HRVs in a few walls (no room for regular duct work). My solar thermal runs floor heat.
Oh yah, one more biggy. I'd cut the tail ends of the rafters and support the roof overhang like on the hot roof (Alaska style) and the new EPS would cover the rafter ends. Basically everything covered but the plastic vent tubes I installed in every rafter bay (except hip corners where NOTHING can fit).
Let me have it Martin, another PK adventure with spouse looking for a way out...
Thanks
Response to Paul Kuenn
Paul,
If you have a ventilated unconditioned attic with limited space between the top plates of your perimeter walls and the roof sheathing, the obvious choice for insulation in this area is closed-cell spray foam. Remove all the existing insulation back from the soffit to a location where there's room for 16 inches of insulation, and install spray foam.
The solution isn't perfect, but it's the best you can do under the circumstances.
If you want to gain room for another inch or two of insulation, you can remove the ventilation chutes, and convert your attic into an unvented attic. If you did a good job air-sealing your ceiling, this solution may work fine with no further modifications. If there are signs of moisture problems after you do this, you might need to install insulation under all of the attic roof sheathing, converting your attic into a conditioned unvented attic. That costs money, of course.
Minimal top plate insulation
Thanks!
You not only fixed my problems getting to this Web site but also gave me a good solid approach - all on a Sunday! Great thought going to full depth at change from closed cell to cellulose at 16" depth. I had thought of an unvented attic but hate the thought of spending a summer's worth of afterwork evenings again up there. I think once was enough. However, it's still better than raising the whole roof.
On that note: In our cold and snowy area Appleton (near Green Bay), WI, do you think that more than 2" sealed EPS/XPS would be needed under the rafters for an unvented attic? I have more than 18" of cellulose ontop of the old fiberglass for ceiling insulation. If treated like a wall with 2/3 insulation on the outside... is the attic like the wall interior in that situation?
FYI - we've never had any ice dams even with two feet of snow on the roof for months. I was more worried about the load on those 50 year old 2x6s.
Your advise is always appreciated. PK
Response to Paul Kuenn
Paul,
If you want to be sure that you won't have any condensation problems in an unvented conditioned attic in your climate, I have to give you the conservative, cautious response: follow the building code.
You are in climate zone 6. In your climate zone, you need a minimum of R-25 of closed-cell spray foam under your roof sheathing to create an unvented conditioned attic, according to the 2009 IRC (Section R806.4). More information here: Creating a Conditioned Attic.
I'm not saying that less insulation wouldn't work. I'm just saying that the code requires a conservative approach.
Minimal top plate insulation
Thanks for the link!
Very good article that I've missed in searches. I like the idea and knowing codes are worthless for real world scenarios, would think overspraying to cover rafter bottoms would be a good control on frosting in below zero temps if there was (isn't there always?) some moisture. I'll have to get a quote as that sounds like a big job (but worth investigating). I'll see how doing the outer edges works first. PK
EPA Graphic
This is the most comprehensive article and ensuing conversation I've ever seen about ice dams! Good points all around. I thought that this graphic I found might add to the conversation...the US EPA actually posted an infographic about common air leaks in a home to educate homeowners about it. I thought it was helpful.
.
Reply to Joe Skowan
Joe,
Thanks for the feedback. For more information on sealing these air leaks, see Air Sealing an Attic.
Lots of good advice, but...
I see there are some proponents of cellulose insulation. Good stuff, but you have to understand mice and other rodents love the stuff too. Non-irritating and easy to tunnel through.
I didn't read all the experts' opinions, but was the effect of sunlight addressed? I noticed in our area the severity of ice dams seem to correspond to the amount of sunshine we get, especially in late winter.
Response to Horst Fiedler
Horst,
I've done a lot of remodeling, and I've found far more evidence of mice in fiberglass batts than in cellulose. I think that the borates added to the cellulose make cellulose insulation less attractive to mice.
You're right that sunlight can contribute to snow melt and ice dams. This is the only cause of ice dams or icicles on unheated buildings like garages and sheds. Of course, ice dams on unheated buildings are minor and rare compared to ice dams on heated buildings, which is one sign that sunlight is only a minor contributor to ice dams.
One more important solution: heat cable to clear gutters
Thanks Martin for this very helpful post on ice dams. Based on a number of articles on GBA and Fine Homebuilding, we sprayed the underside of our roof deck with 10" of foam. This sealed the air leaks, significantly reduced our heating costs and eliminated most of the ice dams and huge icicles that grew on our roof in the winter.
But not all. On a sunny but cold day, our well-insulated and dark roof warms up. Snow melts and runs down to the white gutter that is hanging in the cold air. Voila -- an ice dam that blocks the gutter and builds up until it pushes water up under the shingles.
This problem is 80% better than before we foamed the roof deck, but until we replace the roof and add more membrane protection, the only solution is a heat cable clipped to the gutter. I connected it to a switch, and the cable clears the iced up gutters in a couple of hours.
As you noted, one blog post cannot cover all of the details. GBA readers need to know, however, that the best insulation, venting and membranes often will not stop all of the ice dams on a roof with gutters -- and heat cable is the only option.
Thanks!
Fiberglass batts as filler under rafter vents
My attic has rafter vents but the space between the vent and the top plate of the exterior walls is stuffed with what seems like folded fiberglass batts.Is this typical and acceptable or should I have them replaced with polyisocyanurate boards (cut to form and properly air sealed with foam all around) as shown in the videos on this page?
I have fiberglass blown in insulation in the attic about 14 inches (Climate Zone 5a) and I have had condensation around the ceiling edges this past winter.
Thanks in advance.
Response to Venkat Y
Venkat,
If you have seen evidence of condensation at the perimeter of your ceiling, there is clearly a problem. Windwashing of the fibrous insulation at this location is the most likely explanation. So, yes: the work you describe will help.
Step one is to create an air barrier and insulation dam as you describe. This should be located as far as possible toward the exterior of your wall, at the exterior edge of your top plate.
The next question is whether there is enough vertical room between the top plates of your walls and the underside of your roof sheathing to get an adequate thickness of insulation. You're aiming for at least R-38 (that means at least 11 inches of blown-in fiberglass) to meet code. If you don't have 11 inches of space available, you might want to use spray foam (or stacks of carefully installed rigid polyiso, with air-sealed edges) at the perimeter of your attic.
Solving Cape ice dam; unconditioned to conditioned living area.
Thank you, I have learned much from this article, the discussions, and am hoping I can get some advice.
The house is a cape in western NY that has an ice dam problem on the southwest windward side. The cape has no overhang. The attic is sloped front and back, unconditioned, and has a single layer of original 4” fiberglass batt between the 8” attic floor rafters. There is a plywood floor which does not extend to the last three feet towards where the roof rafters meet the outer walls. There are two gable vents and the attic is presently used for storage.
We will be doing the work by ourselves. We want to have the present attic become living space with storage behind the newly constructed kneewalls. The center ceiling would not be cathedral. There are no dormers and I will not be constructing any.
Unless convinced otherwise, I was not going to foam due to possibly a chemical mistake vs. temperature and such. I have researched diy with Froth-Pac spray foam. I have taken in your information on having no venting and spraying foam direct to the sheathing. I am not counting out spray foam as the final decision.
For venting, I have researched the Smart Vent and Air Vent products where a cut away is made in the roof sheathing 6” from the roof ends. This have favorable reviews but I do wonder if the first six inches without having direct venting underneath it makes for a not complete solution. I would build the venting channel with the 1 x 1’s as you suggest. This seems like the only venting fix or construct a short three or four inch overhang. I could use some input on this.
Above the wall plate, the roof/wall junction starts with 2 inches of space with 7 ½” space below the plate in the ceiling rafter channel. So I cannot get R50 at the roof/wall with rigid board. Your recommendation here is to foam spray as first choice with rigid board wind dam second. So I am not sure which way to go here.
For the lower slope behind the kneewall and the upper slope above the flat center ceiling, I can go R50. It’s the loss of usable room footage in the living area of trying to get R50 with rigid board which leads me to two thoughts. How much depth of foam spray would it take to get to R50? Or get this section of slope roof to R27.5 in the channel and one layer of 1 1/2” board over the rafters, giving a total of R35. Is this section of slope with the lower R going to cause snow to melt into water at this section, possibly moving an ice dam further up the slope instead of near the gutter?
I have not priced a company coming it to foam spray yet versus the cost of myself installing with foam board or myself doing the spray foam.
Thank you for your time I appreciate some insight.
Response to Tony Matuszak
Tony,
Q. "How much depth of foam spray would it take to get to R-50?"
A. If you install closed-cell spray foam, you would need between 7 3/4 inches and 8 1/2 inches of spray foam, depending on the brand. If you install open-cell spray foam, you would need about 13 1/2 inches of spray foam.
Q. "Is this section of slope with the lower R going to cause snow to melt into water at this section, possibly moving an ice dam further up the slope instead of near the gutter?"
A. That's a hard question to answer, but the answer is "maybe." It depends on the circumstances. The higher the R-value you can achieve, the better.
It never hurts to repeat the obvious: the best solution to your problem is to install one or more layers of thick rigid foam above your roof sheathing, followed by new roofing. Here are links to two relevant articles that may help you:
Insulating a Cape Cod House
How to Install Rigid Foam On Top of Roof Sheathing
Log in or become a member to post a comment.
Sign up Log in