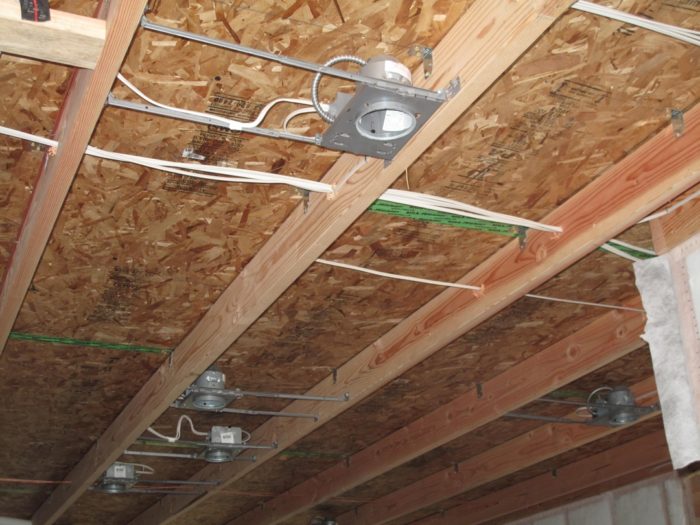
Image Credit: Image #1: Martin Holladay
Conventional wood-framed walls perform many functions. Exterior walls are supposed to support the roof load, resist racking, and provide insulation. They must also provide space for routing electrical cables and (in some cases) plumbing pipes or even ductwork. If the walls are built properly, they should also include an air barrier.
Timber-frame manufacturer Tedd Benson has criticized our conventional approach to building walls. He calls these multipurpose walls “entangled,” and he proposes a new approach to wall building — one that begins by disentangling the various functions of a wall.
According to Benson, “Wires and fixtures should be separated from high-performance wall and roof systems whenever possible. [At Bensonwood Homes,] we add a mechanical chase layer to our walls always, and to our roof panels when there is a heavy mechanical demand in that area. Otherwise, we have dedicated chases at the building peak, at the eave and other strategic locations when necessary. The point is that after sealing a building…, we need to also make changes and upgrades easy and provide a path other than one that violates the integrity of the envelope.”
There are many ways to disentangle utilities from the other functions of a wall. Approaches range from timber-framing, to PERSIST construction, to the use of Larsen trusses, to a variety of techniques adopted by Passivhaus builders in Europe. One element shared by many of these techniques is the service cavity.
What is a service cavity?
A service cavity (installationsebene in German) is a “wall-within-a-wall” — a secondary wall on the inside of an exterior wall. It can be framed conventionally, using vertical 2x4s or 2x3s, or it can be created by installing horizontal 2×2 or 2×3 strapping. The main purpose of a service cavity (also called a “service core”) is to provide room to run wiring, plumbing,…
Weekly Newsletter
Get building science and energy efficiency advice, plus special offers, in your inbox.
This article is only available to GBA Prime Members
Sign up for a free trial and get instant access to this article as well as GBA’s complete library of premium articles and construction details.
Start Free TrialAlready a member? Log in
84 Comments
PRESSURE Boundary
I agree with Thorsten and Lucas... we need something more durable than drywall for the continuous interior PRESSURE boundary.
I'm not so sure we need to give up interior space (or add footage) for a wall service cavity around the entire structure just for a few wall outlets. Of course plumbing walls should be isolated and be interior of the PRESSURE boundary.
No loss in space
When I lived and built homes back in Ireland I always used service cavities. If you use the finished internal dimensions as fixed, making the walls wider, then there is no loss of space. Internal wall board was Fermacell which stiffened up any walls a treat, Intello+ was the air/vapour barrier and, as your article states, not compromised in any way. Also, Fermacell was easy to patch if any electrical outlets etc were ever added at later dates.
Response to Ray Smith
Ray,
I understand your point, but thick walls have at least two possible disadvantages:
1. In a small lot with setback requirements, or in a remodel job, thick walls may indeed mean a loss of interior space.
2. In many parts of the U.S., property owners pay taxes based on the exterior measurements of their home -- and so homes with thick walls have higher taxes per square foot of interior space than homes with thin walls.
Martin, After having lived in Ontario and Manitoba, I now live in the Province of Quebec, where as you've correctly written elsewhere, builders almost always use 1x3 interior strapping (as custom, not code). I was about to arm myself with several sources to use in a friendly argument I'm having with my local building supply store's special projects professional that this strapping is not only not needed, but in sum, a net bad thing. At the same time, I'm rebuilding an exterior wall and need to make a decision on this locally-used strapping. I've paraphrased your words to him from a different GBA article you have written in which you specifically mention this quaint Quebec custom and took quite a stance against it. The problem is that no matter what search terms I use, I cannot find it. Can you -- or other readers here -- send me this GBA article that I'm sure was real?
CR2023,
I can't think of an article I wrote that has the discussion you're looking for. But I expressed an opinion on this issue in an old Q&A thread: "Does interior ceiling strapping defeat the effectiveness of fiberglass insulation?"
Thanks for the article Martin
It seems to be a quite comprehensive run-down of the options and design decisions that need to be made. I do confess, service cavities in domestic construction has always been an area I wondered about, and your article will provide me with an excellent first base, from which to think about this subject.
Thanks again for all the care in writing it, BOH.
Service Cavities
As I recall, the first houses that Katrin built in Urbana used 2x3s inside the insulating wall.
If framing for the service cavity is installed horizontally, how are the edges of the sheet rock nailed? Does it imply vertical blocking where the sheetrock will fall?
Pat
Response to Pat Murphy
Pat,
Gypsum drywall only has to be fastened every 16" or 24", so seams don't have to be fully supported.
Sheetrock corners
Regarding TFA in Passive Houses, you measure sheetrock to sheetrock - so no added TFA from a service cavity, Doesn't matter if you insulate the cavity or not. It is all about conditioning the space you can actually use.
Note on materials: it is much easier to put INTELLO Plus on a ceiling than mounting OSB overhead and then tape + fur out a service cavity - see picture. This can be done by one person instead of 3 and provides you drying potential as a bonus, which is especially important for flat or un-vented roofs.
An explanation of Floris Keverling Buisman's abbreviation
For those of us who haven't yet been invited to the inner circle, and are scratching our heads over "TFA" -- I think I figured it out.
Buisman is apparently referring to the "treated floor area" input for the Passive House Planning Package software.
Three questions
If you put up your OSB barrier, then add your horizontal strapping, then add your wiring and services, when does the building inspector inspect the framing of the exterior wall?
Other than wiring and MAYBE one kitchen wall, what services are you guys putting in your exterior walls? I've always thought it best to put plumbing and mechanical in INTERIOR walls.
I understand using horizontal stapping as a thermal break and understand wanting 1.5 to 3.5 inches more insulation, but I do not understand creating this space and NOT insulating it.
Won't you lose some of the benefit of the thermal mass of the drywall if it has an uninsulated space behind it?
Response to Richard Patterman
Richard,
Q. "What services are you guys putting in your exterior walls? I've always thought it best to put plumbing and mechanical in INTERIOR walls."
A. If the service cavity is on the interior side of the wall insulation and the air barrier, there is no reason whatsoever why plumbing pipes can't be located in the service cavity. The service cavity is interior, heated space.
Q. "Won't you lose some of the benefit of the thermal mass of the drywall if it has an uninsulated space behind it?"
A. No. In either case, the drywall should experience interior conditions.
More detail for the simple-minded
Ok, say you are a layperson who reads GBA daily to help renovate your house and to plan building another house. And you've never built a house before. You guys have written about service cavities before and it makes sense that it is something to consider for a new house, but the details are pretty overwhelming.
Do you have more detailed drawings of what is entailed? I have to see stuff to understand it.
Does the wall cavity have to be about 3" deep for the electrical boxes? If you install a service cavity in the ceiling, do you still use insulated canned lights?
Thank you. Lucy
Response to Lucy Foxworth
Lucy,
Q. "Do you have more detailed drawings of what is entailed?"
A. The photos on this page should help you visualize several approaches to service cavities. In the first comment posted on this page, John Brooks included a detail of a ceiling service cavity. If you click some of the links in the article, you'll be able to read discussions on GBA pages; many GBA readers have posted details that include service cavities.
In the future, GBA hopes to develop and share more details that include service cavities.
Q. "Does the wall cavity have to be about 3 inches deep for the electrical boxes?"
A. Standard wall boxes are 3 inches deep, but shallower boxes are available. The electrical code has requirements on the minimum volume of electrical boxes; volume requirements vary depending on the number of wires entering the box and the number of receptacles or switches. It's certainly possible to use shallower 2 inch or 2.5 inch deep boxes for receptacles and switches.
Most ceiling boxes are about 2 inches deep, but (as with wall boxes), different depths are available, including shallow boxes that are merely 1/2 inch deep -- just deep enough for the Romex. Obviously, these 1/2-inch boxes can only be used for a limited number of applications.
Q. "If you install a service cavity in the ceiling, do you still use insulated canned lights?"
A. If you want to install recessed can lights in a service cavity, be sure that the cavity is deep enough. You'll probably need to frame the cavity with 2x6s or 2x8s if you intend to install recessed can lights.
If the service cavity has no insulation, you don't need to use recessed cans that are rated for insulation contact.
Two pressure boundaries...
JB,
No 3D airflow networks likely for that detail...
Very robust.
Assuming the interior wall is load bearing...
Maybe a vapour permeable fibreboard sheathing on the exterior would be better than plywood/OSB?
Struggling to think outside my "climate box"...
For hot/mixed humid climates maybe it would be better to make the exterior wall load bearing so that a more vapour permeable sheathing could be used on the interior side?
Edit to say:
John,
Never mind - sorry.
The thought behind my question about hot/mixed humid climates was less than half-baked.
The Alaskan study to me says
The Alaskan study to me says insulation in the cavity may promote mold.
depth of cavity and insulation of it
the depth of the cavity can be dictated by the fact that the electrical inspector/NEC requires wires to be > 1.25" from edge of the stud it is passing through. If it is less you need a metal plate to prevent shorting out these wires by nails/screws used for sheetrock, picture hanging etc. If you use a 2x2 and INTELLO Plus you can fish the wire behind it and comply with this code w/o metal plates or drilling through studs. Shallow 1.5" boxes would be needed in that case.
If you intend to insulate the service cavity it will probably mean the cavity will be deeper so you can use off the shelf batts and this also allows you to drill/run wire through the studs without needing metal plates. Please note that you would still want >2/3's of the insulation on the outside of the airtight layer to prevent vapor diffusion/condensation issues in winter.
An important topic
Martin,
Thanks very much for such an in-depth look at the service cavity. This is really great. I think GBA is showing itself as "far ahead of the curve" by treating this issue as one that is worthy of discussion by "all" of us, not just those who are living at the "bleeding edge".
Considering a service cavity represents a far bigger step for US designers & builders than one would think. It means that we are really thinking about the longterm overall health of the envelope and what forces affect it.
From a cold climate, dense packed fill insulation perspective: I look at this as a progression of increasing quality standards. It's my hope that all of the building industry becomes aware of, and considers it's relative position on the "quality progression". I think the path starts with airsealing.
Air-sealing the envelope by creating a pressure boundary at the sheathing is the first relatively simple step to separate conditioned space from the exterior. The focus is on an airtight envelope only. The line of the air-barrier may be a bit "squiggly" at first: Not following the exterior lines but just where you can initially reach the leaks to seal them.
Stepping up and adding the Air-tight Drywall Approach (ADA), means that now your moving the pressure boundary from the exterior to the interior. in addition to separating conditioned air from the exterior air, this will attempt to stop moisture laden air from entering the wall. An important step when the wall has become thicker and the exterior sheathing is now so far from the interior heat sources that it will not stay warm. Stopping moisture laden air at the drywall is taking the first step in preventing rot and decay.
If you typically build thick -super insulated- walls in mild to cold climates, then keeping that moist air out of the wall at the interior surface becomes a larger issue the more you become aware of it. More so with our typical North American assemblies that use OSB or plywood that is not vapor permeable on the exterior. Speaking for myself, when I really look at these assemblies I come to the conclusion that the long term health of the building, preventing rot and mold depends on the insulated cavities being protected from air and water on both sides. North American Builders got that "point" early and developed ADA. if you stay on that "path" and believe that these interior pressure boundaries are the key to long term health, then you have to "painfully acknowledge" that the finished wall will get punctured in many many places over what we hope will be a 200 year life span of this new structure.
So if your serious about the building and occupants health and life span, you have to protect the interior pressure boundary: Today that means placing it inside the wall and away from meddling hands. Once a builder takes this big step, a host of new choices open up: Both the builder and designer can start to entertain designs where the shear loads aren't picked up by the exterior sheeting. it's now possible to move the structural sheathing from the outside to the inside and build entirely new assemblies.
With the structural sheathing now on the inside and doubling as the air and vapor pressure boundary, this means that you can build the classic european wall that has an increasing diffusion gradient to the exterior. The assembly that essentially will follow exterior relative humidity and can always dry since the exterior sheathing is replaced with something vapor permeable.
Using a membrane for the pressure boundary is equally attractive. it's a similar build to standard framing and probably assembles faster. There are two groups to work with: fixed or variable permeance membranes. The fixed permeance membranes work just like sheet goods: The vapor permeance is fixed.
Moving to a variable permeance membrane means (to me) you do need to be careful and really think about your climate and the rest of the layers of your wall. This really leads to another discussion. In short, variable membranes are variable because the permeance increases as the relative humidity increases. This means that the membrane can open up during periods of high indoor relative humidity. These levels change with macro and micro climates, occupation levels and activities. What needs to be carefully considered as you develop a wall assembly is the fact that the pressure boundary is there to limit air and water vapor from entering and accumulating in the insulated cavity. When the membrane becomes variable you lose the ability to rely on low permeance. if you're doing WUFI studies on an assembly with a variable permeance, you need to acknowledge that one case study possibly won't do it. WUFI can only model a single set of values. You might need to run a few cases that change both the indoor humidity as well as the membrane permeance. Having a variable permeance is a good tool when it's planned for and fits the application.
It may seem like this is over complicating things, but if the goal is to honestly maximize the health and longevity of super insulated energy efficient buildings, the ability to begin using these new assemblies starts to change dramatically when you introduce a service cavity; however you do it.
I really appreciate that you started this with Tedd Benson. His shop is the "Perfect Storm" for this kind of thinking: Timber frame folks (I'm one) are descended from a world-veiw that buildings last in the many many hundreds of years, not decades. Envelope quality is an entirely different conversation in that world -it's all about long term durability. Much like where Alex Wilson is going with the idea of Resilient Design, but deeper into the skin of the envelope. Add the fact that Tedd's shop has builders who are well versed in european assemblies where service cavities are the norm, and you've got a company with both the "knowledge" and the "guts" to take on the realities of what makes envelopes fail... And what you can do about it.
sorry for the long windedness. It's a passionate subject for me.
Albert.
The Alaskan study to me says
The Alaskan study to me says this wall design is a set up for mold.
The frame of the home here in the north needs to be fully in or fully out (of the insulation and vapor barriers) to best control mold. When OSB and drywall are are in between cold and or hot, they when moist grow mold.
So sandwiching OSB in a built up wall to allow for one wire to sm outlet is nuts. Put outlets in adjoining walls and in baseboards and floors. No plumbing or other items need to be in exterior walls.
Albert and others are right that for inside insulated and vapor barriered walls we need good permeable exterior components.
So if yaa like this chase idea be careful to think thru where mold and OSB may end up being its downfall.
Response to Albert Rooks
Albert,
You wrote, "There are two groups to work with: fixed or variable permeance membranes. The fixed permeance membranes work just like sheet goods: The vapor permeance is fixed."
I disagree. Plywood is a smart vapor retarder. According to John Straube, the vapor permeance of plywood sheathing varies from 0.5 perm when dry to 20 perms when wet.
Response to Martin
I forgot about this...
Thanks for reminding me.
Response to AJ
Did you read Martin's blog?
Did you see Thorsten Chlupp's comments towards the end?
I get conflicting reports on Plywood
Martin,
Yes I have been told that plywood permeance changes with saturation. The numbers I've heard about are more in the .5 to 1.4 - 2.0 perms. Not 20 perms. That's a new number to me. Can you refer me to where it's posted? I'd love to understand the conditions that it was measured.
Further... If the Plywood is used as an air and vapor pressure boundary at the interior of a super-insulated assembly, how does it get saturated enough to affect permeance that much? I'm not sure that this adds up when it's now inboard rather than at the sheathing layer.
Response to Albert
20 perms sounds high to me too...
Here is a snip from info-312 that shows wet cup permeance of 10 perms.
Although the thickness of the plywood isn't mentioned...
Wait a sec...
This snip from info-500.
More revealing...
Wet cup vs "saturation"...
Assuming that we don't include wetting from bulk water intrusion...
Isn't the wet cup value most appropriate for consideration under these circumstances?
Or (under the right conditions) can plywood act as a sort of reservoir that accumulates moisture through vapour transmission over time?
Conflicting permeance ratings??
Nice work Lucas,
I followed your links and found APA's Publication J450 (attached here). I also attached where I had gotten my original low perm rating for Plywood: NRCA Roofing & Waterproof Manual (the first 4 of 21 pages attached) See my highlights on this. It show a static 0.7 perms at .25". That number would decrease as the thickness increases to 0.5".
The two sets of data vary widely. Hmmm. Martin right (again)? Hmmm.
The number Martin was quoting varied so widely from what I read that I thought I must be misunderstanding something and that the permeance increase was measured when wetted by bulk water: A soaked board in an exterior application where the cells have expanded due to liquid saturation rather than RH. Hence my wondering about the position in the assembly...
In Publication J450, the even the OSB rating are higher than expected.
Response to Albert Rooks
Albert,
Thanks for attaching the APA document, “Water Vapor Permeance of Wood Structural Panels and Wood Wall Construction,” which confirms my statement. (The document even has a section with the heading, “Plywood and OSB are ‘smart vapor retarders.’”)
I never claimed that a plywood air barrier would get wet enough for it to have a permeance of 20 perms in an actual wall. Obviously, if your plywood is that wet, something is wrong with your wall assembly. I merely provided the measured values for the vapor permeance of plywood, to point out that I disagreed with your view that the permeance of plywood is "fixed."
Conceptual shift?
Albert, thanks for taking a step back and looking at the bigger picture. We definitely have a tendency to look at a newly completed home as a finished object which will never be messed with. Resilient building systems need to allow for a measure of less competent interventions further down the line.
Re: 'losing' floor space - this is not a sensible metric for evaluating a particular strategy. 40 sq. ft. may sound like a lot but in most rooms 2"-3" off the width or the length will make no practical difference whatsoever (the exceptions are the few tiny spaces like a compact bathroom). In many homes, bad planning wastes far more space than small increments in wall thickness.
Property taxes: any environmental upgrade has a cost - the marginal increase in property tax burden of a thicker wall will be a small part of that, to be measured in the normal way against the proposed benefit.
Fitting into a tight lot: where the lot is reasonably generous Ray Smith's approach is correct - start with the required interior space and let the wall be as thick as it needs to be. If the lot is extremely restricted a balance will need to be struck, but I'd point out that in the UK where lots are tiny, exterior wall thicknesses for good reason are commonly 10" - 14".
OSB sandwiched between
OSB sandwiched between insulation equals mold. Worst idea ever dreamed up. Alaska study is your proof.
My conclusion, do not insulate in the proposed chase if for some wrong reason you build a chase. I think the idea is useless. Most homes will never have this.
Worried about a picture being Hung on the drywall, really???
Just sayin
Response to AJ Builder
AJ,
You wrote, "OSB sandwiched between insulation equals mold." That's not true, AJ.
To get mold, you need several conditions:
1. The OSB has to be cold; and
2. There has to be a source of humid air that introduces moisture to the cold surface, and
3. There must be limited drying ability.
There are many ways to prevent these problems, including:
1. Adding insulation on the exterior side of the OSB to keep it warm,
2. Installing an interior air barrier to limit the escape of warm, humid air, and
3. Ensuring that the materials on the interior side of the OSB are vapor-permeable, to facilitate drying.
Response to Martin Halladay
Martin,
Per your: "I never claimed that a plywood air barrier would get wet enough for it to have a permeance of 20 perms in an actual wall. " - "I merely provided the measured values for the vapor permeance of plywood, to point out that I disagreed with your view that the permeance of plywood is "fixed.""
I have to admit, The plywood seems "smarter" than I do at the moment. :)
Sure, things would be amiss if the inboard plywood was at 8o% RH for any length of time. While I was struggling to imagine what would set that up in a cold climate, I was more caught off guard about my own ignorance of the plywood being able to reach such high permeance. Even in the 45 to 60% RH range. It's a far more permeable than I was used to thinking. Interesting...
I have to admit, I'm certainly still a student (not a master) on this topic. I expect that I'll be one for a long time...
Thanks for the clarification.
The best and only way
The best and only way superinsulated walls should be constructed is with one insulation/air barrier layer. OSB is not a durable product in superinsulated assemblies.
Buildings should NOT be designed so exacting that merely hanging pictures is a concern as raised earlier. Real poor reason to build out a wall into a chase. And saving the time to drill for a piece of romex, really? Electricians can drill an entire house for wire in a couple hours.
This whole thread is not logical. Adding cost, time, material, mold trap, loss of square footage.
Not even a bad idea. Worse than that IMO.
Response to AJ
AJ,
Concerning your points:
1. "The best and only way superinsulated walls should be constructed is with one insulation/air barrier layer."
I'm sure you've seen moldy walls, but you are overgeneralizing from the failures you have seen. The mold was likely due to too few air barriers, not too many. And plenty of durable walls have more than one insulation layer. Each wall assembly has to be assessed on its merits.
"OSB is not a durable product in superinsulated assemblies."
That's a defensible statement. But when the OSB is on the warm side of the wall, it's likely to last a very long time.
"Buildings should NOT be designed so exacting that merely hanging pictures is a concern as raised earlier."
That sounds like an argument in favor of installing a service cavity.
Martin, sometimes you sound
Martin, sometimes you sound like you never owned a hammer and yet I know that's not true.
We will have to agree to disagree. The more you defend this chase idea the more I think it is down right silly.
Next idea.....
Rephrasing my answer
AJ,
OK, I'll say the same thing, this time holding a hammer in one hand.
AJ: Martin, I don't think that OSB is a good idea. It's gonna get moldy.
Martin: Naw -- it'll be fine.
AJ: I don't like it. Insulation on both sides.
Martin: Yeah, but there's more insulation on the outside, so it'll stay warm and dry. Don't worry so much. Who's getting donuts today?
Lol, good your holding that
Lol, good your holding that hammer otherwise I'd take a trip over to VT and take it away from you till you come to your senses.
Service chases aren't exactly new to energy efficiency
Thanks Martin for your article about service cavities.
It was interesting to read the responses and comments and somewhat differing viewpoints.
It got me thinking about what used to be one of the ways to build exterior walls in "superinsulated" homes in the 1980's. I built my family's home using this method. In those days, "double wall" construction enabled the inclusion of greater thicknesses of insulation since the interior stud wall could be offset from the exterior stud wall using plywood "plates" at the top and bottom. The total wall thickness was established by the width of the plywood plates tying the inner and outer stud walls together.
One of the construction "features" of this approach was the placement of the vapour barrier inside the wall construction (on the exterior side of the interior stud wall, usually protected by waferboard). In essence, the interior stud wall was the "service cavity". The poly was out of harm's way, and wiring and plumbing could occupy the interior stud space. Insulating the interior stud space was a "no brainer" and was done as a matter of course. The total cavity available for insulation in my walls was 14 inches.
That was then. Now my renovation of an old stone farm house has re-introduced the use of "service cavities".
Use of a service cavity makes sense when trying to achieve higher insulation levels and protect the integrity of vapour/air barriers. A service cavity also makes sense where it would be inadvisable to run services through construction members. In the case of my farm house renovation, the roof construction has been rebuilt and clay tile roofing installed by a local contractor.
The rafter dimensions and spacing are skimpy to say the least. Rafter cross-section is 2 3/4" x 6" and spacing 24". Clay tile is a very heavy roofing material - for this cottage total weight is over 10 tons. Thus, I certainly am not going to drill or notch any of the roof members for electrical or any other installations, to not reduce their bearing ability. Further, as the framing material for this project was fresh milled and not necessarily dry when installed (and also, no doubt, due to the weight of the clay tile), The rafters are not in one plane, due to sags and some twisting.
The solution here is to build the "service cavity", inside the living space, outside the bearing construction. Not only is there a place to put the electrical and plumbing, the inner wall and ceiling that will create the service cavity will be trued and in one plane. The space in the rafter cavities will be filled completely and covered with vapour barrier before proceeding with the "service cavity".
All the best,
Andris J. Auzins
Time has proven that high
Time has proven that high quality plywood is a great invention. Every existing home I have worked on has for too many reasons led me to the simple conclusion that OSB falls short of plywood and is not worthy of the tiny savings in overall project cost.
Even Advantech turns to mush if left too long in the weather. A 2000sqft unfinished deck here was totally shot in three years. Not a fair test true but.....
For me time has shown me that OSB is worthless.
Nobody owns me so, that's how I feel about OSB.
Response to Kevin Dickson
I agree that service cavities aren't an "ultimate solution" - they are a design compromise.
However, I think that if very low infiltration rates over long time scales is a goal, then a service cavity strategy has much to offer.
I think the total number of penetrations is largely influenced by where the pressure boundary is located in an assembly.
Some of the penetrations in your list (exterior boxes/fixtures for example) are not a concern if the pressure boundary is located far enough to the interior side of the assembly - cold climate bias.
As for sealing penetrations...
I think it depends on the components involved...
I am sealing penetrations to plywood and site-fabricating seals from a sheet of neoprene.
The neoprene seals very tightly around conduit, pipes and vents.
None of my electrical boxes/fixtures need to be sealed at all.
The "flange" part of the seal sits flush against the plywood and tapes easily.
The "flange" could probably also be glued down...
Running several wires through a piece of sealed conduit that penetrates the pressure boundary is easier that sealing individual wires.
Still working out the best way to seal the inside of the wire filled conduit...
Daniel Ernst...
Have you figured this one out yet?
Unavoidable Penetrations?
Before you run off thinking that service cavities are the ultimate solution, remember there are still many wall penetrations required:
1. Sillcocks
2. Exterior electrical outlets as required
3. Exterior lights at all entry doors and patio doors
4. Dryer vent
5. Range hood
6. Bath vents
7. Plumbing vents
8. Gas appliance vents
9. Main service panel/electric meter
10. Gas service
11. Telephone and cable service
12. Air conditioning lines and wires.
13. Doorbell
This seems like enough penetrations to eliminate most of the gains from a service cavity.
What to do? Just a bunch of tape and foam? Or can we eliminate some of these? (e.g. condensing dryer) Most of them are required by existing codes.
Back to the basic issue
AJ, Kevin and all of us thinking that the service cavity is not realistic...
Again, all that is going on here is that we are moving the air/vapor barrier back away from the finish layer. That's really the issue at hand. Not what the barrier is made of.
AJ: I don't know why your are caught up on the OSB concept so much. This air/vapopr barrier is just a barrier. What that barrier is being made of is up to you. I like OSB or a low perm membrane. Floris likes a variable membrane. Thorsten Chlupp likes plywood. All of those materials are one heck of a lot better than drywall. These just happen to be our preferences. I think you are in favor of air barriers. Right?
I spent some years as a motorcycle mechanic in a BSA/Triumph shop when I was young. Beautiful things these bike were. But geez, here comes an electronic ignition to replace the age old Lucas distributors and you'd think we were all on our way to heck. It was a suspicious change for many. However it stuck. We get better ideas. Things improve.
Kevin: All those penetrations on your list still have to happen no matter where you place the pressure boundary. No. Nothing is perfect. It's all an effort to make these assemblies a little better, step by meager step. The issue with the boundary is not sealing indoors to outdoors (perhaps I didn't follow your comment properly) it's sealing a cold climate wall from having warm humid air entering by infiltration. The assembly has to have penetrations and they should be sealed by however, and at best effort.
All of this pressure boundary issue is based on a wall that will manage it's moisture. If you're assembling a wall that won't dry and will rot the material... Don't do that!
There is no requirement that exterior sheeting has to be low perm OSB. Floris produced a good drawing that looks to dry well, Martin has reminded us about using exterior foam to "warm things up" (ext sheathing wise) and I'm a fan of high perm sheathing. And finally Herr Chlupp up in Alaska -makes me look like a ninny with his ultra high perm "membrane only" sheathing. His is most likely the most durable of all of them.
I think moving that pressure boundary back from the finish layer is a real step up. Sure it's more work, but I feel much better thinking about putting an emphasis on creating a more durable envelope than a few more interior ft2 or fancier finishes.
A few thoughts...
Good article and responses.
After building a Passive House without a service cavity (instead substituting a baseboard chase for outlets) but with the Air Barrier/ Vapor Retarder as OSB directly behind the sheetrock, now whenever someone inquires I always recommend not following my path. Unless necessary I wouldn't do it again for any wall. I spent the majority of the building phase biting my nails and micromanaging all the trades to ensure they didn't compromise the layer. Now it's time to constantly annoy the occupants... for years and years.
A thought on horizontal framing for the cavity: check with your sheetrocker first. Wallboard is usually hung horizontally also, necessitating 1) a good layout to catch the seams and 2) structurally strong enough fastening to keep the sheets from sagging.
Ceilings are a possible location to not use a service cavity (an added benefit of not having one there: getting rid of annoying can lights.) There's always a wall somewhere nearby.
Lastly, after sheathing another roof in plywood, I'm firmly a proponent of using OSB where appropriate. Sadly I imagine the Ply industry is working hard to meet the price point of OSB, but closely inspecting each & every sheet or having to remove sheets just installed because of defects is very costly and annoying. Yes it was only 4-ply 15/32", not the better 5-ply or 5/8" but that's even more expensive. No I won't use OSB for roofing applications, but for an interior air barrier/structural layer, absolutely. Also, in order to reach the air infiltration levels we're achieving, not being able to trust a plywood barrier to perform on account of imperfections just is a headache I don't want to fight.
Magic Plywood
Plywood is more than "smart" it is magical
snipit taken from "Mind the Gap"
http://www.buildingscience.com/documents/insights/bsi-038-mind-the-gap-eh/files/bsi-038_complex_mind_the_gap.pdf
Response to Albert
I'm not sure this is universally true.
In my case, the pressure boundary has holes for neither interior nor exterior boxes/fixtures.
Response to Lucas
Most of the penetrations on the list were venting or services: Dryer, range, bath, gas appliance, elect, gas cable, phones service... All of those would cross the envelope from inside to outside (or vice versa), and therefore cross the pressure boundary. My point was: Whether there was a service cavity and the pressure boundary was moved back from the finish layer has no affect on these either way (all joint sealing being equal). They still exist regardless of where you place the pressure barrier. -Generally speaking.
Dan, what would you do now?
You said that you wouldn't recommend anyone doing what you did. What would you recommend now? A full wall service chase - is that what you are saying?
Lucy
Dan? Seriously? This topic
Dan? Seriously? This topic had you biting your nails???
Martin, your hammer please..... Forget it, have four in the truck.
This thread has been the most entertaining since our last years building/religion/politics wars.
More posts .... Enjoying this. Why I may even chase something today.... Wish I had a tail right now.
(This post is meant to be completely in fun and not meant to be harmful to anyone!)
Nail biting
AJ, Dan is a conscientious builder. I'm glad he bites his nails.
We could use more conscientious builders like Dan who care about the details and worry over getting things right.
My two cents
Just to further Kevin's point about penetrations...(btw he might also include the two large pipes necessary for a HRV on his list) All these penetrations have to be sealed...permanently. Rather than fuss with neoprene or expensive tapes to seal behind a service cavity, where it is not inspectable, I personally would rather deal with all penetrations at the drywall layer, where I can seal it with cheap caulking if I want and inspect and repair as necessary. Simpler, faster, less costly, inspectable, and repairable.
Sure, someone can kick a hole through the drywall and ruin the barrier. Sorry, but I have no sympathy for someone who would do that and not repair it.
The main benefit to a service cavity, as Lucas points out, is that the electrical boxes themselves do not have to be sealed.
Question for Doug
What are you using for an air barrier in the homes you describe...drywall or poly?
Response to Albert...
I understand your point.
And I agree whole-heartedly with your point of view.
I just think that one big advantage of using the service cavity strategy is that there is an opportunity to dramaticaly reduce the number of electrical penetrations in the pressure boundary...
Which tend to be many under ordinary circumstances...
I really like the idea of using a short piece of conduit as a single point penetration for many wires...
Including phone/network, signal wire, cable/satellite etc.
Response to Garth
I agree with you (and apparently Doug as well) that there is nothing wrong with building a good envelope without a service cavity.
In my opinion though, if PH levels of air-tightness are what a builder is aiming for, and they want to maintain that level of air-tightness over many, many years then a service cavity strategy has a lot of potential...
I still think that the "extra cost argument" is a little over-blown.
Yes, it costs more to buy the lumber and install it...
But it also takes extra labour to properly do ADA and seal all the outlets, switches and fixtures...
Also, the neoprene isn't too difficult to work with...
I bought a 4'x4' sheet for $4 from a local industrial supply warehouse.
If you consolidate enough of the electrical penetrations then there is relatively little sealing work to do.
In the end I think service cavities are like any other strategy, there are pluses and minuses...
It just depends on what you're trying to do.
plywood air barrier
Lucas, you have not sold me on the wall service cavity yet.. but I really do like your Interior Plywood Pressure Boundary and the neoprene interface detail you described.
I think the plywood even without service cavity will make a much more buildable & durable Pressure Boundary than ADA.
If the occupants hang pictures..at least they won't need to use mollies,butterflies,etc.
And if there is an air barrier failure caused by occupants behaving badly....It's not like they will have to tear the whole house down to repair it.
I vote no on service cavities
I am glad I was on vacation, reading this has given me a headache. Production builders will not be doing service cavities soon, it is expensive and not needed. We have been building superinsulated homes for over 30 years in a cold climate with a warm side air barrier and they are doing just fine. These homes test in the 1 ach50 to 1.5 ach50 range with comprehensive air sealing details. A thick wall has a lot of diffusion capability for the very minute amount of air and moisture passing through. Too many people are relying on what they hear or read as to the durablity and performance of walls. The proof is in the results, revisit some built homes to learn about what works.
We might not all be building superinsulated homes in the near future but they are proven to be durable and are quite easy to build.
Garth and Lucas
Garth, poly
Lucas, I agree with you that if Passive House performance is what you are after, a service cavity should be a consideration. The main point I was making was my experience, and I have been inside a lot of cold climate walls, you do not need a service cavity for building longevity reasons. Now, most every house built in MN, new or old will have some type of warm side air barrier and will dry to the cold side. If you are using airtight exterior sheathing, I have no experience with that.
Risky?
Doug
I am familiar with the poly air/vapor barrier approach as it is the standard here. I have also tried to do wall repairs, renos etc where I have found it virtually impossible to cut out a section of drywall without totally destroying the poly behind it. There is no good way that I know of to fix it.
Homes with poly on the interior and OSB on the exterior have very little drying potential in either direction. Yes, they have worked so far, but add a few breaks in the air barrier due to repairs etc, and then add a humidifier (quite common up here) and the risk of problems goes up a lot. Any leak from the exterior (inevitable) could result in big problems.
My personal choice of wall system would be 2X6 wall with lots of exterior polyiso and cavitties filled with blown insulation...ADA as air barrier...latex paint as vapor retarder. No poly.
Garth
The risk in the wall you first describe is the OSB, low perm exterior sheathing, I would not use poly either. OSB as an exterior sheathing in a single stud wall in cold climate does not make sense. If I use poly, the exterior sheathing will be fiberboard with a housewrap layer allowing drying to the cold side, with the flow of heat.
If one must use a hard exterior sheathing for a single stud wall in a cold climate, exterior plywood is the proper material choice. ADA should also be considered with this wall in my opinion.
The builders I work with in the Twin Cities metro are using continuous poly, 2x6 walls with fiberboard and housewrap.
Location, location, location...
One odd beauty of this continent we call home is the variety we work to mesh into one whole. For some reason I live and build in a place (Puget Sound) where for a large portion of the year it is very wet. It's fun to venture into the unmaintained areas of the region and observe the buildings being consumed by rot and vegetation. Not very forgiving. Not an enormous amount of bulk water all at once but a lot of it everywhere, especially suspended in the air and puddling in your boots. Occasionally it turns solid. I can see lots of you grinning at the recent emergency caused by, Gasp!, 6 inches of snow and 1/2" of ice. It also happens to be a place where earthquakes are a given. Not a 5 point one either. The Marine coastal regions of the Pacific Northwest are on the same level of expected seismic activity as California, or Chile, or New Zealand, or Japan.
So... Fiberboard in a structural situation? nope. Exterior OSB on a super-insulated wall? Better detail it precisely (and maintain it) or have a very good insurance policy. Throw in some air leakage (carrying moisture) and ouch, better have a VERY good insurance policy. Plywood instead of OSB? Maybe if I was only planning on a 50 or 75 year building, just buying time. Interior poly... scary. All very established and good options for many places but I've seen way too much moisture damage in this climate. Maybe I'm paranoid but if I'm going to build a structure that is designed for a century or more, I want to limit the known dangers. Which means bringing the shear panels and their poorer perm ratings inside and ideally stopping short of all the way to the interior plane of the wall.
But this was about service cavities, I just think they are a very good solution for giving a place for the various trades to do their dirty work, and doing it quickly, without affecting that substantial, air-tight, continuous, warm blanket we're wrapping our buildings in.
Lucy - What would I recommend? For MY CLIMATE, a service cavity on the interior (2x2, 2x3, 2x4... your choice) then a structural air barrier with the majority of the insulation outboard. High perm product on the exterior side of the wall. Yep it's a bit more complicated, but I also get to build 'em... Where are you building?
AJ - I appreciate the peanut gallery, hammers... nails... biting thereof... better than spitting them.
Response to John Brooks
Well, I never was a very good salesman... ;-)
Response to Dan Whitmore
Dan,
It sounds like you are building envelopes similar to the way I am building my own home...
I have details posted at my blog here:
http://ourhouseuponmoosehill.blogspot.com/p/details.html
I wonder how your envelope details differ from mine?
OSB instead of plywood?
Do you use "airtight sheathing"?
Do you airseal your sheathing with tape?
How do you "build out" your wall?
Sorry for the many questions...
Just curious.
Same Thoughts
Lucas, Dan's description reminded me of your project ....
I'm sure he will comment ... but meanwhile....you can see some of the differences at this link
http://www.passivehouse.us/passiveHouse/2010_Passive_House_Conference_Presentations,_November_5_files/2010%20Conference-Courtland%20Place-Dan%20Whitmore.pdf
Airtight Electrical Boxes
Doug, I noticed that you never promote your product at GBA
So I will..... It looks pretty clever and useful to me
http://www.airfoilinc.com/products/products.html
Furthermore
If you are using a service cavity for extra airtightness, I found it makes little difference with a double wall system. I tried poly on the outside of the inner double wall on my first super house, the 1/3 and 2/3 gig. Was a pain to do and from then on went to poly right under the drywall. There was no improvement in ACH50 by creating a service cavity by putting the air barrier outside of the electrical wiring.
Actually I had 1/4 of the insulation in front of the poly and 3/4 on the cold side of the poly now that I think about it. The 2 homes I compared above averaged right about 1.25 ACH50 but then I did not have airtight electrical boxes back then (John Brooks take note).
Double Wall Construction
I built our house in 1982, with 12" double walls. The OS 2x4 is the bearing wall, the IS wall is 2x3 with the 6mill VB on the bach side, covered with 1/2" fibreboard. The top and bottom plates are 12" wide, 3/4" exterior grade plywood. Exterior finish is stucco over 5/8" fibreboard sheathing.
All poly seams are caulked with Acoustic sealent. The windows are set plush with the IS wall. The wall has an "R" of 40.
The ceiling apour barrier and drywal was installed prior to the walls. All wiring, except for 2 lite fixtures, runs in the insulated servvice space or the basement. These 2 wires were brought thru poly boxes and caulked with acoustic.
The poured concrete foundation has 2" SM on the outside and R20 framed walls inside. The concrete bsmt floor was poured over 1 1/2' styrofoam and 6 mill poly.
Heating is 10 kw electric furnace and HRV (no gas). Central AC for summer
We are in Winnipeg, Manitoba, Canada, just 3 hours north of Grand Forks, ND .Hydro budget is $135. 00 per month.
Have had no problems in 29 years
USA New Wall
Do the ideas presented elsewhere by Greg Lavardera at
http://blog.lamidesign.com/p/usa-new-wall.html
address the issues that some of the posters here have with service cavities ?
Peter, thank you for posting
Peter, thank you for posting Greg's blog. My kind of architect. Details of how to build structurally as much as what to build artistically.
Thanks Peter
Thanks Peter for pointing out Greg's blog.
It's another case of "seeing it as a quality progression". And... a really well illustrated one at that. No one is forcing these walls on us. It's an option that I think delivers real quality improvements that are self evident.
John Brooks posts in support of Airfoil
Yes John,
I also notice that Doug McEvers posts regularly, but never mentions Airfoil. I started taking a clue from him awhile ago and am less engaged with talking about my specific products here. This virtual space is much more valuable when you get to talk concepts and exchange "how to's" than "hawk the wares".
However... Here's airfoil from a reasonably well mannered distributor: http://www.smallplanetworkshopstore.com/airtight-electrical-boxes/
Doug's boxes are not cheap, but according to many many builders, including my passive house guru & friend Dan Whitmore (posted above), are the best airtight boxes on the planet today. The boxes themselves are made here in the US and Airfoil is a testament that American small businesses can bring good innovations. The good answers don't always come from big business.
We are even looking at trimming the rear webs for SIPS builders on request to allow face mount in a simple shape cut-out.. I think it would be a great device for those guy's and pretty easy for us to do.
I've been continually aware that my enthusiasm about service cavities are in one sense counter productive for me: I like OSB for the job rather than membrane. To make matters worse, I don't sell OSB but I do have the low perm membrane. Go figure.
Regardless of what goes into it. I can't back away from the standpoint that OSB makes a great low cost pressure boundary. It sets up the possiblity for a highly permeable exterior sheathing where a membrane won't, except for diagonal boards.. It's a good assembly, but to many, it's still excessive. It's probably in good company: I think that superinsulation had the same greeting in the 80's... And the 90's... And 2000... And... today.
GBA's review of the Airfoil box
GBA reviewed the Airfoil box two years ago, in issue No. 7 of Insider (the print companion magazine that used to be sent to GBA subscribers back in the old days).
If you want, you can download the issue here: Insider No. 7.
The page with the review is attached below.
Albert, the idea of loving
Albert, the idea of loving OSB... for you is to do with high tech passive house builds. My last decades of dealing with 99% of what is built proved to me the stuff is junk and is sold at the right price for how much worse it is to plywood.
So my general warning here is to anyone trying to whip up there own creation of a cute wall... to know that IF the wall fails to stay dry, they just may pay a lot higher price for choosing OSB verses something more durable.
That all said... if people like Greg Lavardera are accessed for a COMPLETE SET OF DETAILED PLANS ALONG WITH WHATEVER ASSISTANCE NEEDED TO GET THROUGH THE LEARNING CURVE... then I can see OSB in use if it is truly known that it is to stay dry.
Anyway... taking the price of an entire project, add the cost of upgrading to plywood or Membrain or your products... I think the difference is worth waiting a year after building for the hot tub or granite countertops.
Fire Safety
I realize that this thread may be stale by now, but what are the fire safety / fire spread implications of these service cavities? I googled and found this:
"In my opinion, the major risk in timber framed buildings arises from open, but concealed, cavities containing combustible materials. Connected clear voids within internal and external walls allow any fire which has penetrated the cavity to burn and spread. Alternatively, if the voids were fully filled, the fire would tend to be stifled" http://www.probyn-miers.com/news/2011/06/fire-safety-in-timber-buildings-fire-spread-in-cavities-2/
Airtight electrical boxes and service chase
I know this is an old thread, but I know some people go back and read old posts (i.e. John Brooks). I just bought a couple of Airfoil boxes to see how they look and to show them to construction people to see what they think since the concept is kind of alien around here (zone 3 Upstate SC).
I like how solid they feel and the fact that they are made in the US. I also like the fact that they will be anchored better in the wall. You know how you pull out a plug in most homes and the whole box moves, I hate that feeling. I'm afraid I am making the electrical connections loosen.
My question is are they redundant if you have a service chase? If you've already got a effective air barrier behind the service chase, are they really needed?
I am thinking of using them anyway for the reasons listed above, but I wanted to ask.
Also I wanted to comment on Andy Parkinson's post about the service cavities. Won't most people put insulation in that area? My plan is to use mineral wool which would help prevent flame spread.
Thanks again. Lucy
Response to Lucy Foxworth
Lucy,
Q. "Are airtight electrical boxes redundant if you have a service chase?"
A. Yes. One of the main reasons to have a service chase is to be able to run all of your wiring on the inside of your air barrier.
Q. "Won't most people put insulation in that area?"
A. That is a survey question, not a building-science question. The answer is, it's hard to say. There are plenty of builders who prefer to keep service cavities free of insulation.
Cellulose in double stud wall
I am building a double stud wall that will use osb on the inside for sealing and then a service cavitie. My question, how to hold the celluulose in place till i get the osb in place. Would a fly screen work or what do most people use?
Response to Paul Fowler
Paul,
Most people use an air-permeable membrane designed for that specific purpose. The best-known brand is InsulWeb.
For more information, see How to Install Cellulose Insulation.
Mixed solution service chase
Ok, this is a stale thread so if there is no reply, no sweat.
But I wonder why I didn't hear any mixed insulation solution advocacy?
Why not build your service chase with horizontal straps but insulate most of it? For a wall without plumbing etc, the service chase is mostly overkill. Leaving one horizontal cavity free of insulation and for electrical work makes sense but why leave the whole thing open?
I'm planning to build a service chase on some recently modified walls and know why I will leave them insulation free. I want that stuff outside my respiratory envelope and don't know anyone who has successfully remodeled in my area with airtight electrical penetrations. If a customer or builder didn't care about exposure to insulation byproducts, then why not at least insulate portions of the service chase that overlapped headers or other areas of heavy thermal bridging? The situation also begs the question of what to use. A 1.5" or 2" cavity horizontal cavity seems like a bad choice for most products, except perhaps foam board cut to fit.
Another interesting thought that comes up is whether service cavities offer an opportunity to enable 3 ply headers in older 2x4 homes. I did some window work on my previous house (92" ceilings, 2x4 walls). In some cases on the first floor, I simply could not obtain the header strength needed for a desired large window design with only 2x4 framing. In other cases, greater wall depth would have allowed me to use a 3 ply insulated header. Obviously you'd have to carry the load down to the foundation and need to involve an engineer, but a service cavity could enable some header retrofitting that otherwise wouldn't be possible. Obviously you could just fir the wall in this situation but I think in terms of remodel synergy. It seems like there is an application here.
I'm just a DIYer so if the answer is obvious, well, it won't be the first time.
Response to Keith H
Keith,
Q. "Why not build your service chase with horizontal straps but insulate most of it?"
A. As my article explained, many people do just that. I wrote, "If you are a purist on the issue of disentanglement, you won’t fill your service cavity with insulation. Rather, the service cavity will remain empty of insulation for the life of the building, to facilitate the work of electricians when the home is remodeled. On the other hand, some builders go ahead and insulate the service cavity once electrical and plumbing rough-in work is complete."
You are correct that thicker walls allow more room for thick window headers.
Insulweb behind stud for wiring cavity
I am building in Pa, thinking of a double stud wall with dense pack cellulose. Would there be anything wrong with attaching the insulweb behind the interior studs to create a wiring cavity?
Insulweb isn't an air barrier.
You should have a real airtight barrier between the insulated cavity and the service cavity. Insulweb is designed to be highly air permeable--the opposite of what you want. You could consider a membrane such as Intello.
Reducing Insulation to Create Service Cavity
Hello.
I'm undertaking a newbuild that will have 2x6 walls and I'm planning R6 of insulation (Roxol comfortboard) exterior of the sheathing, My wall U-Value code is only R16 (which we hope to exceed) so I am wondering if there are any downsides to reducing my stud wall insulation to say 4.5-5" by stapling the vapour barrier (likely Intello Plus) slightly inboard on the studs so create a 1-1.5" service void in certain stud bays (only ones with electrical outlets). I don't necessary mind the R Value sacrifice as the building isn't occupied full-time in Winter, but are there are considerations I should be aware of? Convection loops behind the dryway perhaps? I could tape over the staple locations so ensure the integrity of the vapour barrier.
Clearly separate straps on top of the studs for a full service cavity is better, but that may not be feasible for this build. Thanks!
Response to Quinn Sievewright
Quinn,
As long as you pay attention to airtightness when installing the Intello Plus membrane -- and by the way, I think that taping over the staples is unnecessary; just tape the Intello seams -- your plan will work fine.
-- Martin Holladay
In a deep energy retrofit two storey balloon framed home (1904) I have installed 1.5” GPS insulation with a perforated foil facer on the interior side (the exterra insulation is rated at about 1 perm). Flooring was cut and stairs removed so the insulation is continuous from foundation to roof. My intention is for the air and vapour control to be at the taped and sealed GPS. I’m strapping the wall out to build a service cavity over the GPS, but for flexibility I am thinking on doing a mat of 3/4” plywood strapping horizontally and vertically (1.5” total) for ease of electrical wiring and even out the wall waviness. With the craziness of lumber pricing this is actually cheaper than 2x3s. I have two concerns: 1. Fire spread risk. 2. Increased convection looping. Anyone have any insight on this?
Grant,
According to my understanding of code requirements, you'll need fire blocking between floors:
https://codes.iccsafe.org/content/IRC2018/chapter-3-building-planning#IRC2018_Pt03_Ch03_SecR302.11
To the best of my knowledge, you'll also need vertical fire blocking every 10 feet along the wall. If you have any doubts about fire blocking requirements, talk to your local code official.
You should be able to use solid lumber that is 1.5 inch thick as fire blocking. If you run wiring through the fire blocking, you'll need to use an approved caulk at these locations.
Log in or become a member to post a comment.
Sign up Log in