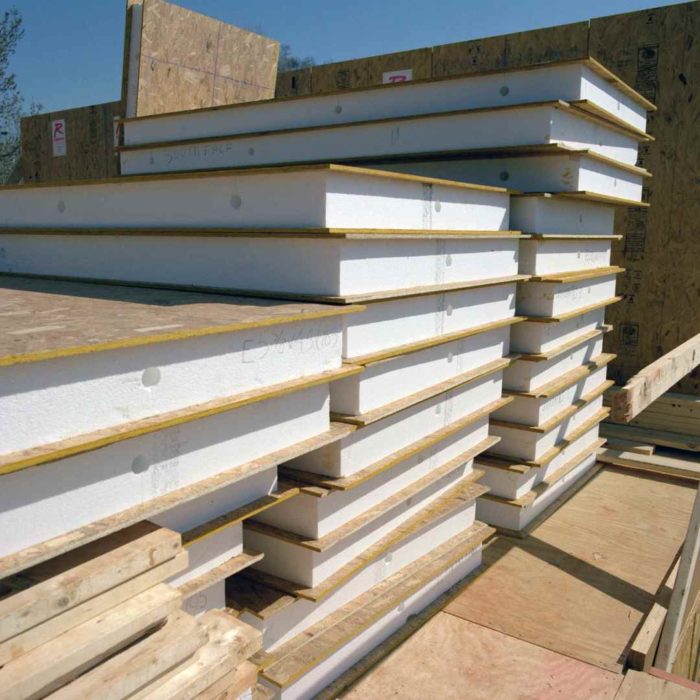
Matt Melton lives in central Washington state in a 3-year-old house with a roof made of structural insulated panels (SIPs) that are 12 1/4 inches thick. The pitch of the roof is very low, only 1/2 inch-in-12, and the metal roofing has been applied directly over the SIPs with no air channel beneath the roofing for ventilation.
When the house was built, Melton sealed the seams between roof panels with tape, applied on the bottom of the panels. The top of the roof was completely covered in a peel-and-stick membrane. In both cases, Melton now says, the seams of the tape and the roofing membrane didn’t seem to stick very well.
This year, there’s trouble. For the first time, Melton has noticed an ice dam on the roof. Worse, he reports water leaking through a seam between SIPs, although the leak appeared on a roof overhang and not in the interior of the house.
“Now, I’m wondering should I pull all the roofing off once it warms up and let the thing dry out and also to see if there is any mold,” he writes in a Q&A post at Green Building Advisor. “Then maybe replace with a better underlayment and a TPO roof?”
There’s one more complication: Melton has sold the house and is now renting it back from its new owners. They apparently plan to take possession in May.
How should Melton deal with this developing problem? That’s the question for this Q&A Spotlight.
A site visit is a good first step
GBA senior editor Martin Holladay makes five observations: installers used an interior tape with adhesion problems; there is evidence of air leakage at the seams between SIPs; it appears that melting snow on the roof caused by air leaks led…
Weekly Newsletter
Get building science and energy efficiency advice, plus special offers, in your inbox.
This article is only available to GBA Prime Members
Sign up for a free trial and get instant access to this article as well as GBA’s complete library of premium articles and construction details.
Start Free TrialAlready a member? Log in
One Comment
Good Article
Thank you again for this Spotlight article. A standard truss roof with an open attic (insulation at ceiling height - no spray foam) is the least problematic way to do a roof. No debating that. SIP roofs require special details, tapes and procedures to make sure that they will perform for a lifetime. These details were discussed in the above article. Skipping these steps and/or details, is a risky endeavor. Following these details will result in a sound and lifelong roof assembly.
MBCI makes standing seam metal roofs for pitches as low as 1/4:12 and they guarantee them against leakage. The standing seams are tall (usually 3") and they elevate the metal panels off of the deck by using clips and metal sub girts. The seams are clipped, locked and sealed in place. Steeper pitch roofs are the better way to go for drainage, especially in rainy climates, but in desert or low precipitation climates, low pitched roofs can use standing seams metal roofs but care and the right roof panel must be used.
Thanks again for the article! Hopefully it is read and utilized by those seeking to do a SIP roof.
Log in or become a member to post a comment.
Sign up Log in