Insulating a “pole building” / garage using nail base insulation panels

Greetings,
I’m planning to enclose a pole building at a vacation property located in central British Columbia. PoIes are apparently 6 feet in the ground and, as far as I can work out, appear to be telephone poles. They are at least 12 inches in diameter at ground level. Dimensions are approximately 36 ‘ wide X 26 ‘ deep X 12’ high. I want to insulate the building and will eventually want to add an insulated slab. Siding material will be metal. The front aspect (36 feet wide) will provide for two garage bays and one entry door on the left. The three other sides will have two windows each, and one side will have an entry door as well.
Im tossing around options for framing out the structure in as-cost effective a manner as possible and in a way that will allow for a sensible insulation strategy. I’d like to heat the thing eventually. It gets cold in the winter, and there is power to the property but no gas.
I was planning on running 2X6 girts around the perimeter 24″ OC, then sheeting, then WRB, then insulation, then tin on top. This strategy avoids having to mess around with framing and insulating around round poles and the various problems I’ve imagined they would create. While thinking this through, I stumbled across GAF nail base insulation panels (apparently not structural), which are faced with 7/16 OSB and they seem to be a reasonable option. In this case, the WRB would be on top of these, followed by the metal siding.
Finally to the question – anyone have experience using these in a similar application? Pros and cons?
Many thanks, and love the site!
GBA Detail Library
A collection of one thousand construction details organized by climate and house part
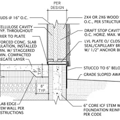
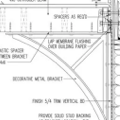
Replies
Marco,
Your approach will work. As with any type of wall construction, the key is paying attention to airtightness.
You might also want to work through all of the steps needed to pour an insulated slab once the walls are up -- to make sure that (a) there are no "buildability" issues, and (b) you have a good plan to air seal the crack between the slab and the walls, and (c) there isn't any below-grade wood.
For more information on using nailbase panels for walls, see this article: Nailbase Panels for Walls.
One more point: Your telephone poles will end up on the interior side of your thermal envelope. In the old days, telephone poles were treated with creosote, which is nasty stuff (and a health hazard). Before you decide to live with telephone poles in your living room, you might want to investigate what type of preservative these poles are impregnated with.
[P.S. I'm not sure whether the building is intended as living space or just a garage. It's possible that you might be willing to tolerate creosote in a garage, even if you wouldn't tolerate it in a house. Your decision, of course.]
-- Martin Holladay
Thank you very much, Martin. I will definitely think through whether the poles are suitable for indoor spaces. They may be borate treated but will confirm this. I know nothing about concrete and will engage a contractor for the slab pour, but was considering installing a 2 X 10 pressure treated nailer on the exterior of the posts. This would be appropriately braced and serve as the exterior of the form for the pour. Poly (6 mil?) would then be installed to cover the floor and run up the sides of the PT nailer. On top of the poly would be the insulation and rebar. I imagine I need some sort of isolation strip (ideas for the appropriate product would be great!) between the concrete and both the posts and the 2X10 nailer to allow movement of the slab. I could then frame the wall directly on the concrete slab, thus avoiding gaps, although I am somewhat concerned that if the slab moves, it could take the wall with it. Perhaps this is not a concern?
Does this plan make sense?
Thanks Martin.