wall insulation on retrofit…

I’m thinking of residing my house (not sure yet what with), but my question is about how to add insulation. I’d like to do exterior rigid foam and have thought I would use 2″ of EPS (due to addl permeability over xps and better R stability over time). I’m in zone 6 and understand I would need R 7.5 (with having 3.5″ of fiberglass batt in the wall) of rigid foam, which the eps would give me barely. I would have to do window jam extensions and am thinking “innie” would work best.
The thought of adding blown in cellulose from the exterior has crossed my mind as well, but if I understand things correctly, adding that to my wall cavity in any amount then increases the exterior foam needed. Should I forget about the cellulose? Go with compacted cellulose and skip the foam? -which would undoubtedly be less headache overall as it would avoid most of the window jam extension needed. My wall cavity is 4″ wide (with the 3.5″ of fiberglass) due to having used non-dimension lumber, giving me room I guess for more cellulose. Any advice on options much appreciated.
Howard
GBA Detail Library
A collection of one thousand construction details organized by climate and house part
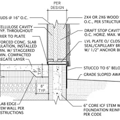
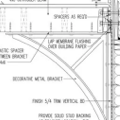
Replies
Been there done that!
With a 1960s 2x4 wall one story and hip roof, I can tell you "USE MORE". I did the 2" EPS exterior and sealed the attic, added 18" of cellulose up there and now after 7 years, I know I need way more. We're just south of Green Bay, WI and we've had 5 cold and snowy years. Although we never have ice dams or pipes freezing, I can tell you first hand the walls are still cold. All my PV and solar thermal works great and we are net zero but you can still feel the cold. I don't like that.
We had double pane argon windows put in 2001 and that helped but are nothing compared to what you can get now. I extended outward to meet the new insulation to make these "innies". The house had also been wrapped with a water/wind barrier at the time when the windows were inserted and then new vinyl siding (off went the aluminum). When I added insulation, I had to add leftover vinyl to make up the new width and length of the house.
This year I'm adding 6" more to the exterior but using Roxul Comfortboard IS for protecting against any close neighbor's house fire. I could get use EPS but want the protection as they are smokers. I'm also having closed cell foam blown in over the exterior wall plates, as the low roof does not allow enough room for proper insulation using anything else. Live and learn. I wished I had raised the roof heel before new roofing and PV was added back then. In zone 6 we really do need R40 walls and minimum R60 attics.
I did hand dig the whole foundation down to four and a half feet to add 2" EPS and also added a 2" XPS frost barrier out from the foundation just under the top layer of mulch. It does keep the basement MUCH warmer. A glutton for punishment. This spring will be as long as the last time, but after 7 years my memory allows for a "new adventure" in the retrofit.
Hopefully I can help your progress along with less mistakes.
Thanks Paul. You've done quite a bit and one can never have too much insulation. My house overall is really not bad to heat, perhaps due to open design, passive solar gain, etc. I use mostly wood that I cut myself, so that part is cheap, though I don't want to cut more than I have to. My questions were really more about how to do it in my situation, in particular with residing (I've done many other things as I went along over the years). I can't see adding much more than the 2" of rigid foam due to the issues in adding so much depth. That was the reason for my question about the blown in celllulose, which would add R but may be in conflict with the foam in terms of moisture migration and condensation on the interior sheathing. And I certainly don't want to/can't do much from the interior. I may add more blow in cellulose in the ceiling because it is easy, although I have about 15" now.
Howard
Howard
There are numerous detailed articles on exterior insulation retrofits.
Here is one video series, though part of it is free and part requires a subscription. https://www.greenbuildingadvisor.com/video-series-exterior-insulation-retrofit-introduction
Congrats to Paul with digging into the foundation to add insulation. I have thought about it and can't imagine doing it. I also have thought about adding exterior insulation. I have no prior experience and doing it by myself is daunting.
I have torn apart the inside attic and added rigid foam. It is much easier for me and less stressful to work from the inside, though living space is reduced.
You'll be much better off with 3.5" of dense packed cellulose than 3.5" of old R11 fiberglass, due to the much higher air-retardency of the cellulose.
Your perception about retrofitting cellulose requiring an uptick in exterior R is mistake. It does NOT change the prescriptive level of exterior R necessary for dew point control. The prescriptive values presume up to R15 of center-cavity fiber, and with 3.5lbs cellulose (or cellulose blown over R11 batts) the total fiber R is only going to be in the R12-R13 range. Only if you make the studs deeper to accommodate higher R would you need to upgrade the foam-R.
With 2" of EPS and R13 of fiber your average sheathing temp will be in the 40F range, and an average mid-depth-foam temp of 25-30F. At a center foam temp of 40F 2" of Type-II EPS will be performing at about R9.0, and at 25F mid-foam temp it'll be running over R9.5. You'll have PLENTY of dew point margin in a zone 6 climate with that stackup, despite the seemingly marginal R8.2 ASTM C 518 tested R ( tested at a mid-foam temp of 75F.)
So, go with the cellulose AND the foam. Of course more foam is always better, but as a retrofit going more than 2" can get complicated at windows & doors- be prepared to do a lot of window & door flashing detailing to get it right if you double up.
Not to hijack the thread but Paul: how difficult was it to dig the exterior foundation? I would love to do this on my 42" deep daylight basement foundation but have been deterred by the cost of a mini-ex (and access). Just seems like a bridge too far. But if one crazy person has done it, perhaps this crazy person could do it...
Dana:
Thanks for your response and for clearing up my misconception about the amount of foam. Wondering about your mention of the 3.5" of dense cellulose (did you mean 3.5 lbs?). Were you thinking I could/should remove the old fiberglass, or were you saying that dense pack added to cavity would be 3.5" (which would mean compressing the fiberglass to one half inch, seemingly unlikely) or was that just a general example?
When I've considered digging down outside the foundation it has seemed like an unreasonable nightmare, but that probably depends on the house involved. I have lots of plantings and numerous underground stuff, like well water line, electric line, septic pipe exits, etc to watch out for, as well as a deck. But if those kinds of obstructions are not a particular issue, the digging would not be unreasonable with a machine. There are very narrow buckets, and there are backhoes that can go on relatively small tractors if one wanted to minimize the machinery impact. But I never considered hand digging to that depth, so kudos to Paul.
Howard
Thanks for the thoughts!
Crazy... well I do bike to work everyday even when it's -17F and I'm in my mid 50s. I am lucky that we only have clay soil from the glaciers and not rock mixed in (like to our south). It WAS A LOT of work and folks walking past on the sidewalk just turned their heads and whispered to one another as they saw my shovel full thrown above the pile. I do keep a very sharp spade. We went to drought by April in 2006 and the clay went rock hard half way around our 1200 sq. ft. house so I was forced to use the pick axe half the dig. Ouch!
I did have to cut long 12" strips of concrete out, four feet from the foundation where the patio met the foundation wall. I recycled that on the low end of the house to raise up the frost line to within 8" of the sill band. I turned them over to expose the "rock look" and made them into a terrace five feet away from the wall then filled it in with the dirt my extra insulation left behind. That forced my neighbors water back into their yard.
I did this because our whole yard is a garden and I couldn't stand the thought of excavation equipment damaging it all. I moved any bushes (after drastic pruning) into a huge bark mulch pile during the hot month of June. I also had the time when work was slow with solar installations. Money was very tight as well for the same reason.
Now with new work and long OT hours, it will be a chore to dig again but I am going to add 3" of Roxul drain board or EPS two feet deep to protect the upper wall of the basement even more. I'll put the horizontal 2" XPS back over it for more frost protection. It made a huge difference the first time around and I think this will help even more. The basement walls stay dry and warm to the touch until November and I'd like to see them last into early December. I'd love to dig down to the base but that would be a huge cost and mess. Seven feet down seems to be a happy 40-50F during the winter vs the near freezing at the surface.
Back to the original thread. If I had not already covered the exterior walls with EPS, I would put holes in it and force cellulose into the walls just for the sake of stopping air flow and increasing R value. Taking a circular saw to a half inch depth, you could easily take out the top few inches of exterior sheathing and pull out the fiberglass if the cellulose folks think it will create havoc. Just a thought.
PK (more time than brains)
Paul: I've done a few labor intensive things myself that others consider nutty or pig headed, so I understand where you are coming from. The memory of the pain fades quickly and the good parts, of which there are usually several, last.
Good idea about how to remove the fiberglass if that seems wise or necessary. I could certainly cut strips out as you mention, probably two in each bay since there is a mid-way horizontal 2x4 (or maybe one that extends enough inches above and below the lateral). The fiberglass is held in/on by only the bit of glue to the back of the kraft paper, now quite old and surely not offering much resistance and could be pulled out with a hoe or other tool. I just like to use stuff already there unless, as you say, it is a problem or a negative. It would add to the cost I assume as more cellulose would need to be used.
"Wondering about your mention of the 3.5" of dense cellulose (did you mean 3.5 lbs?). Were you thinking I could/should remove the old fiberglass, or were you saying that dense pack added to cavity would be 3.5" (which would mean compressing the fiberglass to one half inch, seemingly unlikely) or was that just a general example? "
The nominal dimensions of a 2x4 is 1.5" x 3.5", thus the maximum amount of fiber (cellulose, fiberglass, or a combination) is 3.5". (I had inexplicitly missed the detail about it being a full-dimension lumber.) The amount of compression you get out of the batt when blowing fiberglass into the cavity depends on the density of the batt and the target density of the cellulose. While 3.5lbs density is fine, 3lbs would also be fine.
At those installation densities R13s might only compress to about 2.5", R11s would compress to something like 1.5", and the performance of the fiberglass will run about R4/inch at it's compressed density, to about R3.6/inch for the cellulose layer. Assuming you end up with R10 of fiberglass and 1.5" of R3.6 cellulose you're still pretty much at the R15 mark, which means it won't change the foam-R requirements. You'd potentially go over if you went with 1.8lbs density Optima or Spider, which would deliver about R17, but even that only raises the foam-R requirement to (R7.5 x R17/R15= ) R8.5.
The rated- tested performance of 2" of Type-II EPS is R8.4 at center-foam temp of 75F, but it rises to R9.0 at a center-foam temp of 40F, and continues to rise as the average temp through the foam falls. Since the WARM side of the EPS is going to be averaging about 40F and the cold side is your +15F or whatever mean winter temp the EPS will have an even higher R during the outdoor temperatures that matter from a dew point control point of view, which means you'd have dew point margin with 2" of EPS even if you yanked the batts and dense-packed high-performance fiberglass in there, and PLENTY of margin for cellulose or a cellulose/compressed batt do-over.
The fact that you currently don't have an air barrier up snug up against the itchy & fuzzy on both sides, and instead have a half-inch air gap means that the batt convects freely into the gap, and losing some of it's performance at the temperature extremes. When the cavity is filled completely without that thermal bypass/convection zone the performance of the cavity fill will increase somewhat during the extreme chill, but not by more than the EPS.
Some batts yank out easier than others, but you can still hit ~2.8-3lbs average density without snaking in a dense-packing hose if you drill every couple of feet. (Normal dense-packing methods involves one hole, and inserting a hose to the end of the stud bay.) But it's also possible to run the blower "air only" to ease getting a narrower dense packing hose into the cavity. Every installer has their own bag of tricks, and while it can be a PITA to blow over batts in wall cavities, it's do-able. If you end up with a balled up a wad of shredded batt while trying haul it out it becomes an obstacle, and HAS to come out.