Buffalo, NY wall system

I am looking to build an energy efficient house in Gasport, NY (just outside Buffalo, NY) – zone 5a.
Is a double stud wall my cheapest option and should I keep searching for a framing crew & architect willing to-do it?
I have been following http://rochesterpassivehouse.blogspot.com/ and have talked with the owner/builder & framer. I am not looking for full Passive House certification but want to do what makes scene vs code minimums. The local net-zero builder (Energy Star 3.0, herz <10) is using 2×4 with thermalstar lci-ss sheathing (http://atlaseps.com/wordpressfiles/wp-content/uploads/2015/09/LIT-1039-LCi-SS-Sell-Sheet-092915.pdf) R-20 wall (pdf says U 0.057), R-49 roof, superior foundation walls and an expensive geothermal system. I like the option of being able to heat/cool with a single (or double as backup) split air source heat pump (without geothermal I then have $15,000+ to put back into the shell) but do I need to do a 15.5″ thick wall to-do that or is getting down to <1ach with r-13+5 good enough (I know a Herz rater will have to do the math after the first blower door test)? I like the idea of no foam but have not found a builder locally that will talk to me about a double stud wall yet. The owner/builder of the Rochester house works for a cellulose installer but I am too far away for them to-do the insulation work. The framer in Rochester may be able to frame my house but he is 2hr away so that is going to cost me something. Should I stay away from SIP’s or because of the framing crew problems look to SIP’s to get greater than R-20 without on-site spray foam? Any advice would be appreciated.
GBA Detail Library
A collection of one thousand construction details organized by climate and house part
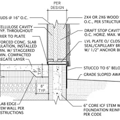
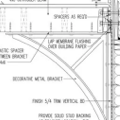
Replies
In Albany, NY- I am doing a 2x6 wall, 24"oc, with 2.5" of EPS foam on the outside, air sealing and 5.5" of dense pack cellulose in the walls. The difficulty is not with the framing as much as with the exterior window trim details as my windows will be "INNIES" but it lessens the issues with interior trim extension jambs, framing peculiar wall depths, and best of all- puts as much insulation on the outside as is reasonable. I may even go to three inches by adding a half in Polyiso under the EPS if I can procure some in reclaimed form. I will use 1x4 furring and 6" screws. You ought consider it.
I'd take a look at http://www.ecocor.us/
They are doing what you are looking for as factory-built wall panels. I have no direct experience or knowledge of the company but I really like the ideas behind it, and it might save you the trouble of trying to find a builder locally who is interested in learning.
Jeff,
The way to determine how an upgrade in the R-value of your walls will affect your home's energy performance is to model your home with energy modeling software.
If cost-effectiveness (rather than carbon reductions) is your chief concern, today's very low energy prices are likely to extend the payback period for energy-efficiency upgrades. Your assumptions about future energy prices will affect your decision. There are many unknowns in the equation.
GBA has published many articles on this topic. Here are links to a few of them to help you out:
Is Double-Stud Wall Construction the Path to Efficiency on a Budget?
Choosing a Cost-Effective Wall System
Choosing a High-Performance Wall Assembly
GBA Encyclopedia: Double-Stud Walls
GBA Encyclopedia: Exterior Walls
Calculating the Minimum Thickness of Rigid Foam Sheathing
The Klingenberg Wall
Jeff- my recently built pretty good house has double stud walls. It was a first for my contractor, but he had no trouble at all. Any smart framer can do it, with just a bit of planning.
Total framing thickness was about 12 inches, with two 24" o.c. 2x4 stud walls, resulting in a 5" space between them. Exterior wall was structural.
When you say you want to be able to use a single split air source heat pump (ASHP), are you thinking of a mini-split or the type that works with an air handler and whole house ductwork? There is an efficiency hierarchy of types of ASHPs. Ductless mini-splits have the highest efficiency, mini-duct mini-splits are next, and central ducted systems are least efficient (substantial range within each category). The effectiveness in distributing the heat goes in the opposite order. If you are thinking of a central ASHP, they are available with large enough capacity that it would not likely drive your wall design decision. If you are trying to get to a single ductless mini-split, then considerations of heat distribution are at least as important as total load. Reducing heat loss helps with heat distribution, but many other factors also come into play. How large is the planned house?
As for wall designs, there are many options between R13+5 and passive house. BEOpt is a useful tool for assessing some of the trade-offs.
There are a lot of wall types that can get you to Net Zero Energy type levels, some without going crazy on complexity.
Download a copy of BA-1005, read the first chaper, and take a peek at Table 2, p10.
http://buildingscience.com/documents/bareports/ba-1005-building-america-high-r-value-high-performance-residential-buildings-all-climate-zones/view
In zone 5 using 2011 vintage photovolatic (PV) system efficiency and cost it's possible to hit Net Zero Energy with an R30 whole-wall cost-effectively. Much beyond that you may be better off spending the money on the rooftop solar. The cost of solar has fallen by more than half since then, and the efficiency (read, "amount of roof area needed") improved incrementally, as has the efficiency of best-in-class air source heat pumps.
Then, download a copy of BA-0903, and take a peek at Table 3, p13:
http://buildingscience.com/documents/bareports/ba-0903-building-america-special-research-project-high-r-walls/view
Of the wall systems discussed, that exceed R30:
Case 2b: R34.5 whole-wall, 2x6 AF wall w/ R19 cavity fill and 4" exterior foam.
Case 4: R30.1 w-w, double studwall w/ 9.5" of cellulose
Case 5: R36.6 w-w, Larsen Truss wall w/ 12" of cellulose
Case 6b: R35.2 w-w, SIP w/11.25" of EPS
Case 10: R32.4 w-w, double studwall w/2" closed cell polyurethane + 7.5" of cellulose
Case 11: R37.1 w-w, Offset studwall w/ exterior spray foam
Case 12: R30.1 w-w, 2x6 advanced framing w/ EIFS finish on 4" EPS.
There are pages of discussion on each technique about ease of build, moisture resilience, cost, etc.
It's possible to replace exterior foam with rigid rock wool in most stackups (not the EIFS) which dramatically improves the moisture resilience, since it has more than an order of magnitude higher vapor permeance for exterior drying. Thermal performance is comparable to EPS of equal thickness. It's more expensive, but it's fireproof, and will never shrink over time opening up gaps, as can happen with EPS after a decade or three. A variation on case 10, with 3" rock wool instead of 2" polyurethane would be more resilient. In zone 5 you would normally need at least 25% of the total center-cavity R value to be on the exterior of the sheathing for dew point control to be able to use a class-III interior vapor retarder (= standard latex paint) in an drying-toward interior stackup, or vented siding for the high drying toward exterior capacity. Using rock wool instead of low-permeance foam gives you both, and if you wanted to limit the exterior rock wool to 2" (~R28.5 whole wall, for a Case 10 type stackup) it would be fine without interior vapor retarders, despite not having quite enough exterior R for dew point control.
But it might be simpler & cheaper to build a Case 2b type stackup, using R20 cellulose instead of crappy R19 batts (that really perform at only R18 in a 2x6 cavity), and 3" of exterior rock wool, which would also be in the mid-high R20s whole-wall, and a good enough wall to hit Net Zero reasonably in climate zone 5 with current technology PV and heat pumps. This is pretty much the wall that Joe Suhrada did (response #1), only with rock wool instead of EPS.
And my plan (2x6 walls with foam outside) basically is a way to save gobs on interior trim work (extension jambs) by doing the innie windows. However, the exterior "extension jambs" are needed but if you plan your window and doors in such a way as to minimize the number f sizes and configurations, you can build your exterior trim in the shop and set them in place. INNIES are also better performing and protected from the wind and rain. Also With six inch screws and 1x4 furring strips, the level of foam can be increased to 3" total before you need to go up a size on screws to 7" and if you do want to use 7" screws then you may build her with 4" foam or Roxul boards stacked up. I am thinking that at 3" of foam I am at the sweet spot, for cost effectiveness, particularly if I can overlap reclaimed EPS over reclaimed polyiso.