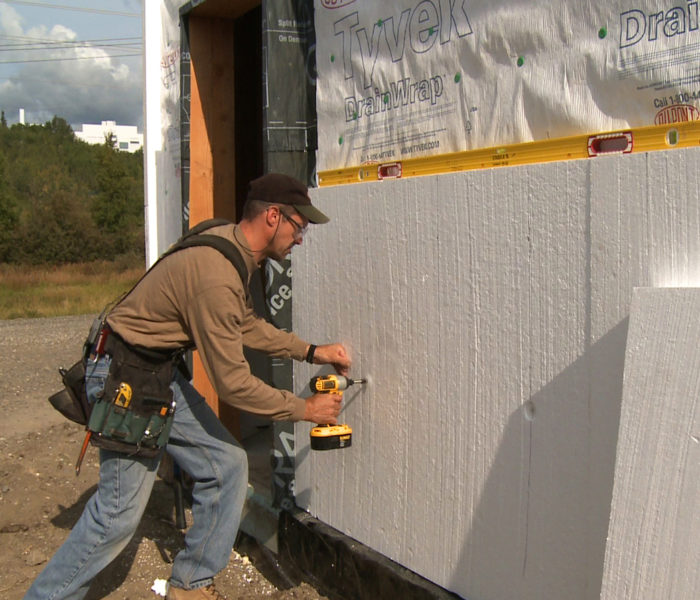
Image Credit: Image #1: Ty Keltner, Cold Climate Housing Research Center
UPDATED on February 26, 2016 with a new table (Image #3)
If you plan to install exterior rigid foam on the walls of your house, how thick should the foam be? Although GBA site has addressed this question several times in our Q&A forum and various posts, the question continues to perplex readers. New questions along these lines come our way regularly.
The last time I answered the question was at the end of a long, very technical blog. In this blog, I’ll cut to the chase.
Keeping walls dry
When it comes to rigid foam sheathing, thick foam is better than thin foam. Thin foam is dangerous, because it reduces the ability of the wall to dry to the exterior without warming the sheathing enough to prevent moisture accumulation (a phenomenon that is usually but incorrectly called “condensation”).
Fortunately, building scientists have calculated the minimum foam thickness required for different wall thicknesses and different climates. By following their recommendations, your wall sheathing (or the interior face of the rigid foam) will stay warm enough to prevent moisture accumulation during the winter.
Because foam sheathing reduces the ability of a wall to dry to the exterior, all foam-sheathed walls must be able to dry to the interior. That means you don’t want any materials with a very low permeance on the interior of a foam-sheathed wall or between the studs. If you are building this type of wall, you should not include interior polyethylene or vinyl wallpaper, nor should you install any closed-cell spray foam between the studs. It’s perfectly acceptable to fill the stud bays with open-cell spray foam, however, since open-cell foam is vapor-permeable.
Install thick foam and no interior poly
To sum up, there are two important points to remember about foam-sheathed walls:
Weekly Newsletter
Get building science and energy efficiency advice, plus special offers, in your inbox.
This article is only available to GBA Prime Members
Sign up for a free trial and get instant access to this article as well as GBA’s complete library of premium articles and construction details.
Start Free TrialAlready a member? Log in
213 Comments
up here in canada
Does anyone know if there is a similar section to IRC Table N1102.5.1 in the Canadian Residential Building Code.
Thank you for the great series of articles on this topic.
additional insulation in the stud cavities
Martin,
Does it matter with these numbers whether the stud cavities are insulated or not?
A project I was on in climate zone 6 went through a WUFI analysis and the results depended on whether there was insulation in the wall cavity.
I think in that case the concern with the insulation in the stud cavity was drying potential to the interior. But I recall from other contexts that the more you insulate the wall cavity the colder the sheathing. Isn't there the rule of thumb 2/3 R-value on the outside 1/3 on the inside?
Response to J Chesnut
J,
The IRC table assumes that the stud bays are insulated.
You're right that in order to keep the inside face of the sheathing warm enough to prevent "condensation," the ratio between the insulation outside of the sheathing and the insulation inside of the sheathing matters. The more insulation inside of the sheathing, the colder the sheathing.
If the stud bays are empty, you really don't have to worry about minimum foam thickness. There really is no minimum in that case -- other than the existing code requirement for wall insulation. That's the beauty of the PERSIST system.
The old rule about 2/3 and 1/3 was devised in the 1980s to address thick walls with a poly vapor barrier in the middle of the wall. People don't build walls like that anymore, and in any case it was just a rule of thumb. But the idea was the same -- builders wanted to keep the poly warm enough to avoid condensation problems.
What happened to section N1102.5 in 2009 IRC?
I have been putting foam exterior of the sheathing, the thickness more set by builder preference than dew point consideration. That said, most of my work is now done under a vigorously enforced IRC 2009, so I figured I better make sure I was familiar with the code. Section N1102.5 (concerning moisture control) seems to be completely removed from the 2009 IRC. Did the 2007 supplement not get rolled into the 2009 IRC or did the whole section move? I checked the IECC and did not see it there either.
eps interior and exterior
Would there be any caveats to installing 1"polystyrene on the interior and also the exterior? The stud cavities are dense packed cellulose and are built above a block masonry wall (raised ranch lower level). By installing 2" eps on the block it offered the opportunity to continue this thermal and air barrier for the remainder of the interior wall. Future plan is to install new siding with foam insulation. Do you think this assembly could trap mositure due to the low permenace of the foam board?
Response to Mike
Mike,
Most experts recommend against a "foam sandwich." It's best to choose which side of the wall you want to put your foam, and then add as much foam as you need or want -- all on one side of the wall. Then the wall can dry to the opposite direction.
Moisture Accumulation vs. Condensation
Martin,
Would you please elaborate on your early comment about moisture accumulation, which you say 'is usually but incorrectly called "condensation").'? Are you talking about moisture accumulation being more than condensation alone, or that the use of "condensation" is incorrect altogether?
Response to Gregory Behm
Gregory,
Condensation occurs when water vapor condenses on a cold, hard surface like glass or an aluminum beer can. Condensation generally does not occur on a hygroscopic material like wood framing, plywood sheathing, or cellulose. (However, frost can occur on these materials.)
If the material in question is below the dew point, it starts absorbing moisture: that is, its moisture content rises. This is a more accurate description of what happens -- more accurate than saying, "moisture condensed on the cold plywood."
For more information on this topic, see "Are Dew-Point Calculations Really Necessary?" (including the posted comments by Bill Rose).
Drying of walls
Martin, How do you get homeowners not to use low perm paints and wallcoverings? Does a disclaimer go with the house? This type of wall system is hardly robust in my opinion.
Response to Doug
Doug,
That's an excellent question. I wouldn't worry about paint, since most painted walls will dry to the interior adequately. But vinyl wallpaper is usually a bad idea.
Anyone have any suggestions for addressing the scourge of vinyl wallpaper?
Vinyl Wallpaper?
Does anyone with any taste still use the stuff? I know hotels and motels like it, but they have paid staff to evaluate things like that.
Martin, thanks for more helpful info about "condensation" on a hygroscopic material.
More on vinyl wallpaper
I agree that vinyl wallpaper is rare in residential applications -- fortunately.
Doug's question is similar to another question I hope to address in a future blog: If an existing cold-climate home built in the 1980s has interior polyethylene under the drywall, is it risky to install exterior foam sheathing during a re-siding job?
John Straube's answer is basically, the jury is still out, but all signs are, "Not so risky as most people think." Thousands of houses with interior poly in Ontario and Quebec (and northern New England, for that matter) have had retrofit exterior foam installed, and we are not seeing large numbers of failures associated with this retrofit work. Struabe says, "These homes will probably be fine."
Should tile and shower type surfaces be avoided?
Martin,
Should tiled or other types of shower walls also be avoided on the interior of foam sheathed walls? Should we be especially concerned with waterproof membranes such as kerdi underneath tile?
Response to Daniel Haedrich
Daniel Haedrich,
I have ordered a copy of the 2009 IRC but have not yet received it. I just got off the phone with Joe Lstiburek, who assures me that the table in question has been integrated into the 2009 IRC, but in a different location and with a different table number. As soon as possible, I will track down the reference and share that information here.
Code officials have decided to remove almost all requirements having to do with vapor retarders from the IECC, so you won't find this table there. All references to vapor retarders have been moved from the IECC and put into the IRC.
Response to Nelson Labbe
Nelson Labbe,
Any time that you have an impermeable membrane on the interior of your wall and foam sheathing on the exterior of the wall, you raise the stakes for the builder. In most cases these walls will work well, even in a cold climate, but you need to be meticulous about your details to stay out of trouble.
A rainscreen siding gap will go a long ways toward improving the chances that wind-driven rain won't enter the wall cavities.
Meticulous air sealing on the interior will go a long ways toward improving the chances that moisture-laden air won't enter the wall cavities from the interior.
Finally, be sure that your sheathing and studs are dry when you seal up the wall. If everything got soaked in a rainstorm, and then builders rush to install exterior foam and an interior waterproof membrane behind a tiled shower, you are trapping moisture in your stud bays right from the start.
So use your head, do a good job, and you should be fine.
Table Location
IRC '09 adresses vapor retarders and the allowance for class III vapor retarders over varying R-values of exterior rigid insulation (based upon wall cavity depth) in R601.3 and table R601.3.1. That is where the above information was integrated. Interestingly, IRC also recognizes the benefit of vented cladding in this section/table.
Response to T.C.
T.C.,
Thanks for the references!
table location
thanks for this info. I just finished enclosing a timberframe with 2x4 REMOTE walls. With 5.5" of foil faced polyiso and no cavity fill, even our PEng. had a hard time stamping the idea. This was over a year ago, glad to see IRC is finally catching up
2 x4 and 2 x 6 foam sheathing thickness
Martin
Thanks for the update on N1102.5.1. That table in CZ6 requires foam sheathing R7.5 for 2 x4 walls and foam sheathing R11.25 for 2 x 6 walls. Is the extra sheathing thickness and Rvalue required on the 2 x 6 wall due to the fact that higher R value is assumed to be installed in the cavities, requiring more Rvalue for the 1st condensing / moisture accumulation surface?
Response to Kevin Hanlon
Kevin,
Yes, you've got it. The extra insulation in a 2x6 wall (compared to a 2x4 wall) further separates the wall sheathing from the warm interior -- thereby keeping the sheathing colder. So 2x6 walls need thicker exterior foam than 2x4 walls.
Martin,
Thanks for the
Martin,
Thanks for the article! It's good to know that if I keep up with GBA, I'll get the information I need to know!
Other climate zones?
Martin,
So, based on this table, exterior insulation thickness is a moot point for climate zones 4A & 4B?
I realize there are other methods of calculating foam thickness (based on HDD, average wintertime temperatures, etc.), and designers should be informed before making a decision on this subject. BUT, from the IRC's perspective, people building in a zones 3, 4A, & 4B don't have to worry about winter time moisture accumulation?
I'd appreciate hearing your thoughts on this topic!
Response to Daniel Ernst
Daniel,
You're correct.
If you live in climate zones 1, 2, 3, or 4 (except 4 Marine), there is no danger of wintertime "condensation" (moisture accumulation) because your sheathing will never get cold enough to cause a problem, regardless of whether or not there is exterior foam, thick or thin.
Southern Paradigm
Every time I see this darn map and other DOE statistics I shake my head. It still seems to be calculated from the aspect of conserving "home heating oil". A typical residence in Central Texas runs the air conditioning (electricity) for ten months of the year. Additional insulation does allow for more comfort and less dependence on the cooling cycle. So I agree that we do not need the insulation for protection against cold, but we do need it for protection against heat.
Response to Anonymous
Anonymous,
So why do you shake your head? It's just a climate map. Surely you agree that the climate in Texas is different from the climate in Minnesota?
No one is saying that you don't need insulation in Texas. Of course you do. But the climate map tells you many things -- including the fact that in Texas, you don't need to worry much about wintertime condensation or moisture accumulation in your wall sheathing.
Interior Foam insulation
I have a building with a "stepped" ICF wall. Above the ICF I have a 2x6 studded wall on 24" centers with the studded wall flush with the outside of the ICF. I am considering using 4" of rigid foam on the inside to insulate and make the inside of the studded wall flush with the inside of the ICF. I have 1/2" plywood on the outside of the studs, with 30# building felt and board and batten siding. I plan to have the wall dry to the outside. I live in the Pacific Northwest. This building is a large shed and I will not likely be heating it over 60 degrees. What issues might I have with moisture content in the walls?
Response to Wayne
Wayne,
While many builders have had success with walls similar to the one you describe, building scientists are beginning to note that such walls are risky. You've got cold exterior sheathing; that sheathing is at risk of moisture accumulation.
So, you need to do one or two things to lower the risk. The most important thing you can do is to create an effective interior air barrier (for example, using the Airtight Drywall Approach). Don't forget to use airtight electrical boxes and to take measures to avoid air leaks at these boxes. These measures keep warm humid interior air out of your wall.
The second measure is optional, but it lowers your risk further: include a ventilated rainscreen gap between your sheathing and your siding. Such a gap will help your plywood to dry quickly if it ever gets damp.
IRC 2009 table N1102.1 and Online Codes for all
Martin--Two things.
First, I understand this pretty well and assume they factor in conservative estimates for moisture generated inside a tight house during the winter. But how do you reconcile table N1102.1 in the 2009 IRC that states zone 6 can have R13 batts in the wall and R5 foam sheathing on the exterior and footnote h. even goes on to say that you can have as little as R2 foam on the exterior? This seems to be in conflict with R603.3.1
Secondly, you mentioned you had ordered a new copy of the Code and were waiting for it. There are two websites with a lot of codes on line including many states and local municipalities--an invaluable resource. They are:
http://www.iccsafe.org/Store/Pages/FreeCodes.aspx
http://ftp.resource.org/codes.gov/
Response to Bob
Bob,
The code lists minimum performance requirements; however, it's perfectly possible to build a code-compliant house that doesn't perform well or fails quickly. There's nothing in the code to keep you from screwing up. The code doesn't necessarily keep you out of trouble. (For example, it still allows the use of interior poly in many situations when its use is ill-advised.)
So, "Table N1102.1 in the 2009 IRC that states zone 6 can have R13 batts in the wall and R5 foam sheathing on the exterior." That's the code minimum. I don't suggest you do that just because it is legal. You should do better.
Code conflict
Martin,
Maybe I wasn't clear. I totally understand the concept, agree with you and don't intend to put 1" foam on a 2x4 wall in zone 6. I was wanting to point out that it appeared to be a conflict within the code and wanted to see if you read it the same way. It appears to me that N1102.1 states you can do something that R603.3.1 says you can't. Is that how you read it?
Second response to Bob Ellenberg
Bob Ellenberg,
1. I agree with you that the code could be written better. You make a good point -- Table N1102.1.1 implies that it's OK to install R-5 foam over a 2x4 wall in zone 6. The table should be re-written or should include a footnote warning against the practice.
2. However, remember that minimum code requirements for insulation are NOT recommendations for best practice. These minimum requirements are simply a way of saying, "If you do anything less than this, you've broken the law."
Best Practice query
I understand that it is not necessary for exterior rigid foam in areas like mine (Zone 3) for walls. What about on unvented roofs? Or are roof questions ruled by a different table of commandments? And I'm interested in both walls and roofs as "best practices," not in terms of minimums for the minute.
My question comes from Dr. Joe's book on Mixed Humid climates where he designs an unvented roof for Dallas TX, also in a mixed humid climate w/HDD and climate similar to Atlanta's. He places R-5 rigid insulation on the exterior of the roof to avoid the potential for "condensation on the underside of the roof sheathing."
Is this a contradiction of the points made here, or am I (more likely) not understanding the difference between roofs and walls for rigid exterior foam?
TIA
Joe W
Response to Joe W
Joe W.,
Good question. Although I'm not a building scientist -- and I'll do my best to contact one to get more information on your question -- here's my understanding: unvented insulated roofs are particularly problematic if they aren't detailed carefully, since there are often few opportunities for damp roof sheathing over an unvented assembly to dry out.
Roof sheathing over an unconditioned attic dries readily to the interior. If the rafter bays are stuffed with insulation, however, the roof sheathing won't dry as quickly toward the interior. Since the roof sheathing is covered on the outside with underlayment and roofing, it doesn't dry much to the exterior, either.
Roof sheathing over an unvented insulated roof doesn't dry as well as wall sheathing. After all, wall sheathing is better able to dry to the exterior than roof sheathing.
I assume that Joe Lstiburek recommends the use of R-5 foam on top of an unvented insulated roof in Zone 3 to keep the roof sheathing warm (and therefore dry) during the winter. This foam isn't necessary for walls in Zone 3, because the wall sheathing is able to dry to the exterior during the summer.
Zone 3 roofs vs walls
Thanks Martin. That makes real sense. As always I appreciate the help. And yes, keeping the sheathing warm is his objective.
Joe W
I'm learning much from these
I'm learning much from these forums! Would it always be considered a best practice to have two layers of foam as opposed to one so the joints could be staggered then taped?
Response to Jeff W.
Jeff W.,
Most experts agree that two layers of rigid foam with staggered seams is better than one layer of the same total thickness.
Confusion by Clarification
Martin is finally differentiating between condensation and moisture accumulation in this blog and his "How To Avoid Condensation in Your Walls" blog, but I'm afraid the discussion is creating more fog than sunshine. I'm composing a Q&A thread, which will be posted very soon, to attempt to bring more light to this complex and highly misunderstood topic.
But my primary concern about this blog is that it seems to suggest that the best if not the only way to prevent condensation and moisture accumulation in sheathing (at least from the inside) is to keep it warm with exterior foam (which is Martin's oft-stated bias).
Though it's true that this blog is only about how thick a layer of exterior foam is necessary to keep the sheathing relatively safe, it's revealing that Martin abbreviated IRC Table N1102.5.1 (which he copied in its entirety on his other blog).
What the full table (https://www.greenbuildingadvisor.com/sites/default/files/Table%20N1192.5.1.jpg) reveals is that sheathing moisture problems can be avoided in one of two ways in almost all of the lower 48 states: either by keeping it mostly above the dew point temperature with exterior foam or by using permeable exterior sheathings and cladding assemblies.
It's heartening that the IRC, at least, is finally recognizing that exterior breatheability is as important as trying to keep sheathing warm, which can have the adverse effect of encouraging mold and decay growth (which cannot occur in cold or frozen sheathing).
Foam Sheathing
I have a small, cement block house in tbe wet Willamette Valley (Zone 4) of western Oregon. What thickness of exterior rigid foam sheathing should I use in that case?
Response to Catching Up
Catching Up,
According to the 2006 IRC, so-called "mass walls" in your climate zone should be insulated to at least R-13 (assuming continuous foam insulation rather than cavity insulation).
That means at least 2 inches of polyisocyanurate, or about 3 inches of XPS, or about 4 inches of EPS.
These are minimum code requirements. Many green builders prefer to exceed the minimum code requirements.
foam sandwhich
the minimum foam thickness charts don't seem right to me...experts recommend against foam on both sides of a wall, aka "foam sandwich" but does it really matter if you have poly and r22 bat insulation on one side of the wall sheathing and r15 foam insulation on the other side of the wall sheathing?? As this would be the case in a retrofit. Would it make sense on a 2x6 wall to use poly and r22 bat insulation on the inside of the wall sheathing and only 1" rigid insulation on the exterior as the 1" has enough perms to allow drying to the outside if necessary?? And there's no mention at all on this blog about tyvek or typar house wrap against the wall sheathing!
Response to Lyle Zimmer
Lyle,
I'll try to address the points you raise.
Q. "Does it really matter if you have poly and R-22 batt insulation on one side of the wall sheathing and R-15 foam insulation on the other side of the wall sheathing?"
A. I'm not quite sure what you mean by, "Does it matter?" I think your question concerns the presence of polyethylene, but I'm not sure. If that's your question, here's the answer: the polyethylene is less than ideal, because it slows down the wall assembly's ability to dry to the interior. However, the wall may still work, especially if there are no water intrusion issues from wind-driven rain, and if the indoor relative humidity is kept low.
Q. "Would it make sense on a 2x6 wall to use poly and R-22 batt insulation on the inside of the wall sheathing and only 1 inch of rigid insulation on the exterior as the 1 inch has enough perms to allow drying to the outside if necessary?"
A. First of all, if you plan to install exterior rigid foam on your wall, it never makes sense to install interior poly. So, if it's new construction, be sure to leave out the polyethylene. If it is a retrofit job, and the poly is already there, you may have to live the with poly -- not ideal, but not necessarily a deal-breaker. Concerning the permeance of 1-inch thick foam: EPS permeance is between 2 and 5.8; XPS permeance is between 0.4 and 1.6; and foil-faced polyiso permeance is 0.05. These are low numbers, so you won't see much drying, if any, to the exterior. It makes far more sense to keep the sheathing warm enough to avoid condensation or moisture accumulation than to deliberately leave the sheathing a little bit cold and hope that the cold, wet sheathing can dry through the foam. Trust me -- it won't dry through the foam. It's better to ensure that it never gets wet than to hope it finds a way to dry.
Q. "And there's no mention at all on this blog about Tyvek or Typar house wrap against the wall sheathing!"
A. True. So what? If you have a question about Tyvek or Typar, I would be glad to answer it. Briefly, Tyvek and Typar are water-resistant barriers (WRBs). Neither is thick enough to keep sheathing warm, so they don't enter into this calculation. Both materials are vapor-permeable. If you are interested in learning more about WRBs, I suggest you read All About Water-Resistive Barriers.
Do these minimum R-Values apply to SPF as well?
Being that I am in climate zone 4 here in Portland OR. Do I still need to achieve an R-15 minimum when encapsulating rafters with open cell foam?
Reply to Tyler Dotten
Tyler,
No, the guidelines presented here apply only to rigid foam sheathing installed on the exterior of walls.
If you are installing open-cell spray foam between your rafters, all you have to do is meet your minimum code requirements for R-value. According to the 2009 IRC -- which may or may not apply in your jurisdiction -- the minimum ceiling R-value for those following the prescriptive path in your climate zone is R-38.
That means that you need to install at least 10.25 inches of open-cell spray foam.
Above grade retro fit
Hello Martin and the Blog posters. I am interested in improving my energy insulation in a 2x4 studded walls with 40 y/o fiberglass R13 and Kraft faced insulation. I live in Zone 5 (Chicago).
After reading the great info on this site, I plan to re side and re pack the insulation with R15, then sheathing with OSB/Ply, rain/water barrier/proper flashing, then 2- 1 inch polyiso, seams taped and alternated, then furring strips, then fiber cememnt.
Does this sould appropriate? Do I need more than 2 inches of Polyiso (hard to come by for a DIYer).
Thanks in advance,
Bob
Response to Bob LeBeau
Bob,
As the blog on this page explains, all you need is a minimum of R-5 for a 2x4 wall in Zone 5, so your 2 inches of polyiso will work fine.
Is foam necessary?
Is foam on the exterior really needed? Wouldn't it be 'greener' to skip the foam on the exterior and do a double wall with cellulose using something like the zip system to seal up the outside. Thick foam seems to cause a lot of problems with exterior windows and detailing.
Am I missing something?
Response to Elizabeth Kormos
Elizabeth,
I don't know where you got the impression that foam is necessary; this article certainly never said that foam is necessary.
GBA includes a great many articles on double-stud walls, Larsen trusses, and the installation of mineral wool panel insulation on exterior walls. See, for example:
Double-Stud Walls
Is Double Stud-Wall Construction the Path to Efficiency on a Budget?
All About Larsen Trusses
How to Install Cellulose Insulation
Installing Mineral Wool Insulation Over Exterior Wall Sheathing
Sorry, just trying to figure it all out.
I've read all those articles and so far came to the conclusion that we didn't need foam on the outside. I am crazy or shouldn't there be a best practice (most energy efficient and affordable) way of constructing a wall per climate area?
Response to Elizabeth Kormos
Elizabeth,
Q. "Shouldn't there be a best practice (most energy efficient and affordable) way of constructing a wall per climate area?"
A. GBA tries to provide information to readers to help them determine energy-efficient and affordable ways of constructing a wall. However, the type of wall that is affordable in your area may be different from the type of wall that is affordable in others areas. Variables include the cost of labor, the availability of skilled cellulose installers, and the proximity of the nearest SIP manufacturing facility. All of these factors, and many more, affect the cost of a wall.
The building code sets minimum prescriptive R-values for wall assemblies. If you build a wall with a lower R-value than the code, you are breaking the law. Of course, building a wall with a higher R-value than the legal minimum is perfectly OK, and it's usually a good idea.
Green builders usually try to build a house that is better than the legal minimum. That's why there are a variety of green building programs with more stringent requirements than the building code. You might also be interested in the discussion around the idea of the "Pretty Good House" -- an attempt to establish what might be called best practices.
Martin
Hi Martin,
We are about to start design on our near passive house (or pretty good house) in zone 5. I've been an avid reader of all your blogs and articles. I think your recent discussions as to regionalization (which by the way LEEDS is now addressing too) is right on. Thank you for making all this information available to builders and homeowners.
If you were building my house (2,200 sf, 1,500 sf on first floor (universal design),triple windows, on a slab, vented roof, passive solar orientation) in upstate NY and had a limited budget what wall system would you use?
A high-R wall for upstate New York
Elizabeth,
It's hard to beat a 12-inch-thick double stud wall insulated with dense-packed cellulose for simplicity, relatively low cost, buildability, and energy performance. If you decide to build such a wall, I recommend that you use plywood sheathing rather than OSB sheathing.
High R wall for Upstate NY
That is pretty much the wall we are planning. I generally don't like OSB (I specified plywood on my current home). My husband does mold assessments and says that wet OSB is very susceptible to mold because the wood fibers are broken.
We are considering using the zip system since you can seal the seams easier than with plywood and it is sealed. Do you see any downside to using Zip?
Zip sheathing
Elizabeth,
Zip sheathing is a type of OSB. It's up to you to determine what type of sheathing you prefer.
Here's an article on the "cold OSB" debate: How Risky Is Cold OSB Wall Sheathing?
Worried
Now you have me worried. Do I run a risk of moisture collecting on the interior (not coated) side of the zip sheathing from interior moisture with the 12" walls?
If we use plywood, as you recommend, for the sheathing, how do we effectively seal the seams? I want a tight house.
Sealing plywood seams
Plywood seams can be effectively sealed. For more information on tapes, see Air-Sealing Tapes and Gaskets.
One product recommended for sealing plywood seams is 3M All Weather Flashing Tape (8067) . The two importers of European tapes, Small Planet Workshop and Four Seven Five, sell high quality tapes suitable for plywood seams.
What did you choose?
Elizabeth-
Which exterior wall system did you wind up choosing? I'm working on a project in Denver, CO, and am considering a wall similar to the one you described. I'm curious if you decided to use ZIP sheathing or not.
How strict are the climate zone requirements?
Hi Martin,
I'm in Bennington Co VT in the SW corner of the state. I'm technically in zone 6, but I'm a few miles away from zone 5. My builder designed 1.5" R9.8 foam board over 2x6 walls with fiberglass insulation. I see from the chart that zone 6 should have R11.25 and zone 5 should have R7.25 over 2x6 walls. It looks like I'm just on the edge. Do you foresee moisture problems with this setup?
Thanks for your help.
Response to Jon Lobo
Jon,
The recommendations in the building code (and in this article) result in a safe wall assembly that is relatively robust. These recommendations take into account variations in wall construction quality and variations in indoor humidity levels.
If your wall leaks air, the risk level rises. If your interior humidity level is high, your risk level rises.
If you build the wall you describe, you can lower your risk by (a) paying attention to airtightness when installing your drywall (in other words, following the Airtight Drywall Approach), and (b) maintaining a reasonable indoor humidity level in the winter (in other words, don't install a humidifier, and remember to use your exhaust fan when you take a shower).
interior walls
Thanks for the quick response Martin. So breathable interior wall is good because it facilitates drying, but big air gaps in interior wall are bad because they allow hot air to reach cold sheathing? I would think that a bit of convection in wall helps drying, but overall it's a net minus?
exposed floor - Climate Zone 7
I'm looking to insulate the underside of a porch and I wonder how these wall figures apply to an exposed floor.
The porch is conditioned space that's attached to the main house and sits on two concrete piers, so the underside of the floor is exposed. On the inside of the house, this floor area is very cold in the winter. I have enough foam from a previous project to apply 4" of continuous EPS (R 14) to the bottom of the porch joists and I'm unsure if I should add batt insulation between the joists, or if I should buy more foam? Is an exposed floor any different than an exterior wall?
Response to Jon Lobo
Jon,
Q. "So breathable interior wall is good because it facilitates drying, but big air gaps in interior wall are bad because they allow hot air to reach cold sheathing? I would think that a bit of convection in wall helps drying, but overall it's a net minus?"
A. What you call a "breathable" interior wall is more accurately called a wall that is vapor-permeable on the interior. This is very different from a wall with air leaks. It's possible (in fact, it's desirable) for a wall finish to be vapor permeable but also airtight.
You are correct that air leaks in your wall assembly are a "net minus." The energy waste and the potential for moisture buildup during the winter are much worse than any theoretical benefits.
The one part of your assembly where you can use air movement to your advantage is in the ventilated air gap between your siding and your sheathing. This type of air movement is not associated with energy losses or any problems from moisture buildup in your wall assembly.
Response to Mark Fredericks
Mark,
Q. "I'm looking to insulate the underside of a porch."
A. I suggest that you read the following article: How to Insulate a Cold Floor.
Q. "I wonder how these wall figures apply to an exposed floor."
A. The same principles apply, in theory. However, in practice, you are unlikely to have moisture problems in a floor, because the stack effect prevents air leaks from carrying interior moisture into your floor assembly. That's why the use of thinner foam than recommended in this article shouldn't lead to any floor moisture problems.
Q. "I have enough foam from a previous project to apply 4" of continuous EPS (R 14) to the bottom of the porch joists and I'm unsure if I should add batt insulation between the joists, or if I should buy more foam?"
A. Go ahead and install the batt insulation if you want; it will do no harm. If you want to buy more foam, that is also a good idea. In either case, the most important thing you can do is pay attention to air sealing.
Zip R Sheathing
does it create plywood drying issues?
should you put a tyvek type product over it?
would it work then with fiberglass batts or would that allow air to pass to the interior side of the foam and not dry out in the wall bays?
Response to Keith Miller
Keith,
Yes, many people have used it.
It isn't plywood. It's a type of engineered wood resembling OSB, sandwiched to a layer of foam.
The R-value isn't much. There are two versions -- one is R-3.6, and the other is R-6.6. Unless you choose a sheathing product that meets the minimum R-values recommended in this article, your wall could have moisture issues. In other words, Zip-R sheathing is a warm-climate product, not a cold-climate product.
Best Insulation for Climate Zone 4 - KS?
I am having a house built and trying to determine the best approach for exterior wall insulation. I'm in Kansas, climate zone 4, but about 60 miles from zone 5. We are using 2x6 walls. The three options I'm looking at are (1) flash & batt with 1/2" closed sprayed foam and R19 batt, (2) 1/2" exterior foam -- Dow SIS or Rmax Thermasheath SI -- and R19 batt inside wall, or (3) same as #2 but with 1" foam. I'm curious to know which method you think would be the best? According to your article, foam thickness doesn't matter in my climate, so would either of the 1/2" options be just fine and have no condensation concerns? Unfortunately very few builders and suppliers have used exterior foam so I can't find much good information locally. Thanks!
Response to Scott Rock
Scott,
Q. "Which method you think would be the best?"
A. Of the options listed, I would choose 1 inch of exterior rigid foam.
Be sure to pay attention to airtightness; I recommend the use of a blower door to track down air leaks.
Unvented roof
Martin,
At the end of this article you talked some about the code requirements for an unvented roof. I am a little confused about the way you defined the properties of insulation in the joist bays. You stated that code requires rigid foam above the sheathing, and "air-permeable" insulation in the joist bays. You went on to quote the IRC 2009 definition of "air-impermeable" insulation. Would you mind giving a little more clarification on that?
Which is the preferred method inside the joist bays, permeable or impermeable? Thanks for leading all of these helpful discussions.
LowR XPS sheathing error on garage
Martin,
I am in the process of converting a single detached garage into a workshop/storage venue, Winnipeg MB Canada, so Zone 7 I think (2 hrs north of Grand Forks ND). On one long wall adjacent to my neighbour's garage (2.5 foot separation between structures), I put building paper (i had 30 lb asphalt felt) over 5/8 ply, 1/2 in XPS (R3-5) to minimize thermal bridging, furring strips, then metal siding. The wall is 2x4 but with 2x horizontal bracing i had intended to put 1.5 in xps against the studs equal to the bracing but will just stick to bats now so it will be closer to 2x6 insulation (roxul or fibreglass pink -to be confirmed yet) covered by firestop drywall (fire code in wall next to neighbours garage as it is within 4 feet) then painted osb (to make shelf construction easier and so the drywall doesn't get too banged up). Thankfully I read your articles and blogs, and reread some of the building science.com stuff before doing the other 3 walls.
Before I deconstruct the exterior to either add rigid XPS to an R15 or remove the too-thin layer I have (most likely option) would it be an acceptable risk to just leave this wall as is even with the non -desireble thin foam sheathing given that the structure will be only be heated to sweater temp no more than 16 hrs a week max during nov-feb as a workshop (ie I'm not living in it).
For the other walls, is it acceptable to just skip the external xps insulation and go with a more traditional, batt insulation in the 2x4 cavity, 1.5 in XPS, then poly (not sure if this is required other than the code says it is here)' then osb?
I know I am over- thinking this garage/man cave thing a bit much, but the idea that the cold sheathing will frost up if (when) heat/vapour moves through the wall and contact it makes absolute sense and I really wish I had figured this out before now.
Thanks
Mike
Response to Mike Gagne
Mike,
Q. "Would it be an acceptable risk to just leave this wall as is even with the non-desirable thin foam sheathing given that the structure will be only be heated to sweater temperature no more than 16 hours a week max during Nov-Feb as a workshop?"
A. Yes, that is acceptable.
Q. "For the other walls, is it acceptable to just skip the external XPS insulation and go with a more traditional, batt insulation in the 2x4 cavity, 1.5 in XPS, then poly (not sure if this is required other than the code says it is here), then OSB?"
A. Yes. As long as this is a garage, and it is not converted to living space, I think that would be fine.
Thanks
Martin,
Thanks. Your website is extremely helpful, informative, and practical. It contains a wealth of knowledge and people like me can learn a little from your experience and expertise. Firstly, just to be clear about the wall in the first Q with the inadequate r3 XPS - should I skip the 1.5 inch XPS and poly on the interior beneath the gypsum to allow in to dry inwards? And second, I confirm that it is definitely not to be living space.
Response to Mike Gagne
Mike,
Q. "Should I skip the 1.5 inch XPS and poly on the interior beneath the gypsum to allow in to dry inwards?"
A. Yes. But don't worry in either case -- if the room isn't generating a lot of moisture, everything should be fine.
Great White North
Martin,
Thanks for the great article! You may have saved me a significant amount of headache in the future.
I am replacing the siding on a house built in 1980 in Calgary Canada (I assume climate zone 6 or 7? It is very dry here). The house has poly on the inside of the wall behind the drywall.
I would like to install a cement fiber board over some rigid foam however the manufacture of the fiber board dictates a maximum foam thickness of 1”. Am I going to run into problems with only 1” (R6) of foam in my area?
Will installing a product like drain wrap between the OSB and the foam help mitigate any condensation problems?
Another option is to install 1.5” of foam with furring on the outside of the foam. The additional thickness may present some issues for installation however. Will 1.5” of foam be acceptable for my area?
Thanks again for all of your great advice.
Response to Shawn L
Shawn,
You should use the table on this page, and you should figure that you are in Climate Zone 7. I don't know whether your house has 2x4 walls or 2x6 walls.
In either case, you're clearly going to need more than 1 inch of foam. In order to install fiber cement siding, you will need to install furring strips.
More information here: How to Install Rigid Foam Sheathing.
The article includes many additional links that will help answer almost any question related to exterior foam sheathing.
Foam insulation to retrofit a cathedral roof
Hi
I live on Vancouver Island in British Columbia. My house was built in the 1980's and has a cathedral roof which suffers the problems you identify in your article "How to Build and Insulated Cathedral Ceiling'; it allows condensation to drip into the living room. It has 2x10 rafters. The vapour barrier, just above the drywall, is shot. The roof, also, has insufficient insulation which is fibreglass bats.
Will my roof work if I remove the fibreglass insulation, put blocking between the rafters over the walls (so no air movement from the soffits), put in 3 or 4 layers of rigid foam, put 2x4 strapping across the rafters, then cover the rigid foam with 2 inches of closed cell spray foam which will cover the rafters except where they intersect the 2x4 strapping, and then fasten steel roofing to the strapping?
I am not a builder or carpenter and have been reading and asking question until my head is spinning, so an answer will likely help both my roof and my head.
It has also been suggested that I put a radiant barrier (from Radiant Technologies) in with an air space on either side. I cannot find any support for this idea and so, unless you suggest otherwise, I will ignore this suggestion.
Response to Cliff Stainsby
Cliff,
It's unclear from your description whether you intend to install spray foam above the rigid foam or below. I'm going to guess that you will be opening up the roof from above, and that you intend to install the spray foam above the rigid foam.
Your plan will work, as long as the total R-value of the rigid foam plus the spray foam is adequate for you climate zone. I don't know the requirements of your local Canadian building code, but I would imagine that you want at least R-38.
Most roofers would feel more comfortable if you installed a plywood deck on top of your 2x4 strapping, and then a layer of asphalt felt on the plywood. Roofing underlayment (asphalt felt) is required by most building codes.
Your roof assembly does not need a radiant barrier.
Thanks
Hi again
Just a brief note to say thank-you. You guessed correctly about the approach I intend to use and you have made me feel much more comfortable about it.
Thanks
Foam insulation to retrofit a cathedral roof
Hi again
I don’t wish to overstay my welcome. However, the first idea I presented to you, which you thought would work fine, turns out to be considerably over my budget. I am retired on a partial pension.
I am trying to repair a cathedral ceiling/roof and I wonder whether you think the following approach would work.
The rafters are 2*10, so I have approximately a 9.5 inch cavity to work with; I am working toward an unvented roof.
I propose to:
1. place 2*10 blocking between the rafters over the outside walls
2. apply a 2 inch layer of spray foam between the rafters and up the inside of the blocking (to seal the lower ends), which apparently provides a complete vapor and air barrier as well as more than R12
3. put in 7.5 inches of high density fiberglass batts
4. cover the rafters with 1.5 inches of ISO board
5. cover that with ½ inch plywood, titanium 30 underlay (or something similar), and a steel roof.
This should give us an R50 (49.9) roof.
Do you think this will work? If the spray foam and blocking are applied properly is moisture likely to be an issue? Should I seal the ridge or leave a ridge vent? If a ridge vent, should it just be for the plywood and steel, or should it continue through the ISO board to allow moisture (if any) to escape from the fiberglass?
If these questions appear silly, please remember I am an amateur, not a roofer, not even a carpenter.
Thank you again.
Response to Cliff Stainsby
Cliff,
The most serious problem is your suggestion to install rigid foam above the rafters. That won't work. The rigid foam needs to bear on a continuous surface like plywood or OSB. If you put it on top of your rafters, it will compress.
However, your suggested solution will work as long as you reverse the order of the rigid foam and the plywood. So, once you have insulated your rafter bays, you install plywood on top of your rafters, followed by roofing underlayment (asphalt felt or synthetic underlayment). Then you install a layer of rigid foam. Then you install your purlins or furring strips (1x4s or 2x4s, parallel to the ridge -- usually 24 inches on center), and then your steel roofing.
Thanks
Thanks again Martin. Very helpful. I expect you saved me some grief.
Any comment on the question about a vent at the peak -
Should I seal the ridge or leave a ridge vent? If a ridge vent,r should it continue through the ISO board and plywood to allow moisture (if any) to escape from the fiberglass?
cliff
ps. I sure am glad I found your site as in it I find an endless series of interesting articles. I have spent much of my life fighting climate change and promoting energy efficiency, so your site is like manna from heaven for me.
Response to Cliff Stainsby
Cliff,
The roof assembly you have described is an unvented roof assembly, so you don't need a ridge vent. For more information on this type of roof assembly, see How to Build an Insulated Cathedral Ceiling.
Drywall, poly, 2x4, fiberglass batt, 3/8 sheathing, +2" iso ???
I've done some reading and it appears I'm in a bit of a spot. the poly is already in the wall.
1973 house, with the a fore mentioned wall construction, plus building paper over the 3/8 exterior sheathing, I want to put 2" polyiso board, strapped with 3/4 strapping and then Hardie siding. the Iso board I can get locally is for roof construction and has tiny wholes in the paper on both sides, No foil, and is supposed to breath (somewhat, not sure how much, but am looking into it) what are your thoughts on this for a north west, marine coast, Olympic peninsula, environment,
thank you
Response to Iain Matheson
Iain,
Many energy experts have worried whether it's a good idea to install exterior foam on a house with interior polyethylene. Although it would be better if the poly wasn't there, the fact is that tens of thousands of Canadian homes with interior poly have been retrofitted with exterior rigid foam, and there haven't been any reports of widespread problems. According to building scientist John Straube, all indications show that these retrofits are "not so risky as most people think. These homes will probably be fine."
That said, the installation of exterior foam is not advised on any home that has suffered wet-wall problems like leaking windows, condensation in stud cavities, or mold. If you plan to install exterior foam during a siding replacement job, keep an eye out for any signs of moisture problems when stripping the old siding from the walls. Investigate any water stains on housewrap or sheathing to determine whether the existing flashing was adequate.
If there is any sheathing rot, determine the cause -- the most common cause is a flashing problem, but condensation of interior moisture is not impossible -- and correct the problem if possible. If you are unsure of the source of the moisture, hire a home performance contractor to help you solve the mystery.
If your sheathing is dry and sound, I don't think you need to worry about adding exterior foam. Adding a rainscreen gap will certainly go a long way toward avoiding future moisture problems. Of course, it's important to be meticulous with your details when you are installing your new WRB and window flashing. It's also important to keep your interior relative humidity within reasonable levels during the winter. Never use a humidifier.
To summarize, here are four caveats:
1. Be sure that your foam is thick enough to keep the wall sheathing above the dew point in winter. Read more on this topic here: Calculating the Minimum Thickness of Rigid Foam Sheathing.
2. When the siding is being removed, inspect the existing sheathing carefully for any signs of water intrusion, and correct any flashing or housewrap problems.
3. Install rainscreen strapping so that there is a ventilated gap between the new exterior foam and the siding.
4. Keep your interior humidity under control during the winter; if the interior humidity gets too high, operate your ventilation fan more frequently.
exterior foam
I am in zone 5 2x6 walls batt insulation osb sheathing and housewrap. My budget is shot and I can only afford 1" extruded foam board instead of 1.5". Would it be better to use 1" or nothing at all. Vinyl siding on exterior. Certainteed voids the warranty if I use a rainscreen. Siding must have 100 percent contact with wall.
Thanks,
Aaron
Response to Aaron Whiteman
Aaron,
If you choose foil-faced polyiso instead of XPS, you'll get R-6 without an air space, or R-7.5 if you use furring strips on the exterior side of the polyiso. Either approach is pretty close to what you need, although it's best if you can go with the furring strips.
CertainTeed is nuts to void the warranty when furring strips are used. You might just go ahead anyway -- the warranty isn't worth much. More about vinyl siding and furring strips here: Can Vinyl Siding be Applied Over Furring Strips?
Response to Aaron Whiteman
Aaron,
Only you can make this decision.
The right answer is that the minimum R-value you need for your exterior rigid foam is R-7.5. That doesn't mean that your walls will rot if you decide to install R-5. It means that you have chosen a risky wall assembly.
If your indoor relative humidity stays low, your walls will probably be OK. But if you choose to build a wall assembly that is risky, you have to be willing to accept the risk that accompanies your decision.
Exterior Foam
If I am unable to find 1" polyiso in my budget would using the 1" xps be better or would it be safer to not use any foam. I am right in between Erie and Pittsburgh. I am not sure about siding on furring strips without filling in between. The Certainteed rep told me that the siding will become wavy when it starts to expand and contract as well as I will see "zebra lines", a term which they used to describe when there is dew on the outside of the house and is noticeably different on the siding where it lays on the furring strip as opposed to where there is no contact. Right now I am just worried about the foam.
Thanks again,
Aaron
values for 12" cellulose walls
This table is specific to 2x4 and 2x6 walls, but I'm wondering if it is possible to extrapolate an amount of exterior foam insulation necessary for 12" dense packed cellulose walls from the information here?
The recommended R values increase from 4" to 6" walls, so does it also increase for 12" walls, or does this not necessarily follow?
Response to Michael Pi
Michael,
It's usually a bad idea to try to put foam on the exterior of a double-stud wall filled with 12 inches of cellulose. As you guessed, the higher the R-value of the insulation between the studs, the thicker your foam has to be. By the time you get to 12 inches of cellulose, the foam gets ridiculously thick -- so thick that it is hard to attach.
If you want to do the necessary calculations to determine how thick your foam needs to be, this article explains how to do the calculations: Are Dew-Point Calculations Really Necessary?.
Soon, it becomes clear that if you are going to have very thick exterior foam, it makes sense to keep your stud bays empty -- that is, to put all of of your insulation on the exterior side of the wall sheathing. This is an excellent approach; it is called the PERSIST method. For more information on PERSIST, see Getting Insulation Out of Your Walls and Ceilings.
It's a little unclear to me why you want to put any insulation on the exterior of a 12-inch-thick wall insulated with cellulose. Do you just want more R-value? If that's the reason, why not just build a 14-inch-thick wall or a 16-inch-thick wall and fill it full of cellulose?
The idea with a thick cellulose-insulated wall (a classic double-stud wall) is to keep the exterior sheathing relatively vapor-permeable, to encourage drying to the exterior. So -- usually -- no exterior foam for this type of wall.
Response to Martin Holladay
Martin - Thanks, that's what I thought.
I don't want to put foam on my walls per se, but it was one strategy outlined in numerous of the great studies discussed here about how to deal with potential moisture migration issues. I thought this model wasn't recommended for thicker walls, and was validating that.
It's currently my understand that using plywood or fiberboard sheathing with a vented rainscreen gap along with airtight drywall looks like the best approach in this scenario (upstate NY zone 5 right on border of zone 6). I had read the Straube 2009 research which pointed to this.
More recently, I discovered and read the NREL Moisture Research - Optimizing Wall Assemblies paper. http://www.nrel.gov/docs/fy13osti/56709.pdf
There is a section for high R walls, including a double stud dense packed cellulose wall (evaluated in zones 5a and 7). They modeled with and without vented cladding. Without vented cladding, the wall I'm looking at increased in moisture over a 3 year period, but dried out with it. Then there is additional discussion of condensation potential which i don't entirely follow. And then section 4.2.4 including "all the high-R walls fail this criterion by a significant margin when the ASHRAE 160-2009 interior conditions with cooling are assumed. All the cases fail the 30 day running average." 4.2.5 - "For all high-R walls, the ASHRAE 160-2009 indoor conditions result in isopleths that indicate the potential for mold on both the interior surface of the drywall an the interior face of the first condensing surface."
They conclude by discussing vented cladding being essential, but i'm not clear on whether and in what conditions the concerns/failures above their concluding discussion continue to be relevant, versus in what cases they are solved by using vented cladding. This is undoubtedly just due to gaps in my subject matter expertise here. But some of this was concerning to me, and I intended to follow up with these study authors to gain some clarity.
Aside from clarifying some of the points in the study above, I suppose my overall concern is whether this wall is "high risk" - in the sense that it wouldn't react well to some sort of failure like a big leak, tape or caulk (or other "mechanical") failures, if the rainscreen gap somehow got plugged up or compromised, etc. At the end of the day though - not sure this matters because i don't know what a lower risk wall would be. All high insulation strategies seem to have potential for failure or risk if bad stuff happens. Not sure one has less than another or is in some way more adaptable to murphys law.
Response to Michael Pi
Michael,
As long as you choose plywood sheathing, board sheathing, or fiberboard sheathing, and as long as you include a ventilated gap between the sheathing and the siding, I don't think that cellulose-insulated double-stud walls are risky.
For further discussion of the issues you raise, see How Risky Is Cold OSB Wall Sheathing?
Further response to Michael Pi
Michael,
The issues you raise are discussed further in this article: Monitoring Moisture Levels in Double-Stud Walls.
IECC 2012 C402.2
My current project is in ASHRAE Zone 5. As I pulled up the table in reference from the code, I noticed the code also states that for 'wood framed or other' walls, R20 + R3.8ci is allowed. What is your experience with this portion of the code and moisture issues.
Response to Nathan Kipnis
Nathan,
Building code regulations provide the minimum specifications that you can build to without being arrested or sued. Building codes do not define best practices.
If you install exterior rigid foam on your walls, you should follow the guidelines provided in the table in this article. The only way you could get away with R-3.8 continuous insulation is if you made sure that the insulation is vapor-permeable (for example, by using R-3.8 of mineral wool insulation on the exterior).
Mineral Wool sheathing
Martin,
Thank you for keeping this discussion thread alive.
I am considering using Mineral Wool insulation (Roxul Comfortboard IS) in a retrofit scenario rather than foam, as my walls were built using interior poly (Climate zone 7) and I want to maintain the ability to dry to the exterior.
I see that the header for Table N1102.5.1 in the article states that it pertains to foam sheathed walls. Is it the same if I were to use mineral wool insulation? As I understand it, the stated R value in the table is to try to minimize the moisture accumulation in the exterior structural sheathing and thus could be applied similarly to vapor open insulation that is applied exterior to the structural sheathing. I am aware that I would need to employ a rain screen for the siding installation. Sincere thanks in advance.
Response to Pete Marthaler
Pete,
The recommendations in my article and the requirements in Table N1102.5.1 refer to exterior rigid foam. They do not apply to mineral wool insulation.
If you want to install exterior mineral wool insulation, thick insulation is still better than thin insulation, since thick mineral wool will keep the sheathing above the dew point (and therefore dry). If you choose to install thin mineral wool, however, the mineral wool has one advantage that rigid foam does not: it's vapor permeable, so that when the sheathing gets wet during the winter, it will be able to dry out to the exterior in the spring and summer.
On the other hand, mineral wool doesn't stop inward solar vapor drive. So if your wall assembly is susceptible to problems associated with inward solar vapor drive, rigid foam is a better choice.
Aged Poly-Iso outboard + 'cold roof'
We are designing a three story house for Toronto. All insulation in the cathedral ceiling will be between the 12" , 24" o.c. rafters.. The roof will be built with a 1" vented airspace between the underside of the ply roof sheathing and 9" of poly-Iso foam topped with 1.5" of styrofoam. We were concerned about the ~1% (temp+time dependent?) shrinkage in new poly-Iso. However, we have access to perfect 12ft. x 4.5" poly-Iso slabs which are 11 years old. Can anyone direct us to information that quantifies shrinkage in this material vs. time? Has all of the time- dependent shrinkage already occured?
Lastly, where would you put the vapour barrier or air barrier?
Response to Theodore Chabane
Theodore,
It sounds like you are planning to insulate your cathedral ceiling with the cut-and-cobble method. I don't recommend this approach, because differential expansion and contraction between the rafters and the rigid foam can lead to air leaks.
For more information on the cut-and-cobble method, see Cut-and-Cobble Insulation.
For more information on foam shrinkage, see Using Rigid Foam As a Water-Resistive Barrier. (Look for the paragraph with the subhead "Do rigid foam panels shrink?" and read the sections that follow.)
The best way to use your rigid insulation is to install it as a continuous layer above the roof sheathing, rather than to cut it into strips and insert it between the rafters.
Styro sandwiched between 2x4 walls.
Hi all, I have posted this question/opinion in another thread. It also suits this thread and I would like all the feedback I can get.
I'm in zone 6a. I didn't include that in the original post.
Rob,
I have also been considering your design 3 option for my build. I live in Ottawa which often sees -20c through the winter. My wall section would consist of:
siding
house wrap (breathable drainage plane)
3/8 plywood
2x4 stud wall 16 oc with roxul batt. Framed to underside of floor decking.
1"-1-1/2" extruded styro with ship lap joints taped. Again to underside of floor decking. This will be my vapour barrier and thermal break.
2x4 stud wall 24" oc less joist height to support floor and run electrical. Will also insulate with fibreglass batt.
drywall and paint.
Note that I realize that the rule of thumb is 2/3 of the insulation should be to the cold side of the vapour barrier, and this design is close. I could easily achieve it by opting for 2x6 exterior, increased styro, or decreased batt to the inside. however I'm not to concerned as the design allows for drying to the warm side if or when condensation occurs.
My reasons for considering this design are:
-I will have quite a bit of exterior detail and I don't want the hassle of working over top and around insulation.
-I don't like the idea of a vapour barrier on the cold side of my wall for obvious moisture issues.
-I know that a continuous vapour barrier to the inside of a wall is virtually impossible after all the mechanical and fastening penetrations
-I like the fact that this design can dry to both the inside and outside.
With all the benefits that I see with this design I wonder why I can't find more about it. Is there something that I'm missing??? I realize that framing a second wall is more work but after factoring in the fact that you would have to strap over the entire outside of the house for something to fasten siding to (unless you plan to brick or stuco) I don't see that a second wall to the interior as such a big deal. In my opinion as a framer building walls is the fun part! If you have ever strapped and sided over styro you know that it's a pain in the a...
Maybe it's the r value that people are hung up on? But I would suggest that r means nothing if your walls leak... and something that I have encountered with these super tight wall systems is that the less leaks you have the greater concern they become. You can end up with a really high concentration of condensation where you have a small leak and most of these designs don't allow for the wall to dry in or out.
Does anyone have first hand knowledge of this design? or see an obvious flaw in my reasoning that I could be missing?
Response to Kevin Vesey (and others interested in the topic)
Kevin,
Posting questions twice is confusing. For the sake of GBA readers, it's best if all of the answers (and the back-and-forth communication) are on the same page.
Anyone interested in following the thread raised by Kevin Vesey should post any comments or reactions on the page where Kevin originally posted. Here is the link: Wall design questions.
Rigid Foam Sheathing
Martin
I will start building a new house near St. John’s Newfoundland this coming spring. I cannot find anything about a climate zone so I will go with the US zone # 7 to be on the safe side. The wall itself will be constructed using 2x8 studs on 2x8 plates. ½ plywood on outside of stud and 3/8 on inside stud, creating a sealed air space. Cavity will have spider insulation. 2x3 stud wall for electrics and such, not sure if I will insulate this wall probably not. I will cover the outside ½ plywood with building wrap. Then fit Rigid Foam to R-15 followed by 1x3 strapping for rain screen and add spruce clapboard stained both sides for siding. My question, is the R-15 going to be able to keep this wall warm since it is a 2x8 and not a 2x6, if not what R value should I use? There is going to be no poly or any kind of retarder on the inner wall.
Thanks.
Paul
[Editor's note: to read the answer to this question, advance to Page 3 by clicking on the "3" below.]
Response to Paul Fowler
Paul,
No, you can't use the same minimum exterior foam thickness for a 2x8 wall as you would for a 2x6 wall. If the R-value of the insulation between the studs goes up, then you have to also increase the minimum R-value of the rigid foam, to make sure that your exterior sheathing stays above the dew point.
Here is a rough, back-of-the-envelope calculation: you have increased the thickness of your between-the-studs insulation by 32%, so you also have to increase the minimum R-value of your exterior foam by 32% -- in other words, from R-15 to R-20.
For a more precise calculation, follow the method described in this article: Are Dew-Point Calculations Really Necessary?
Foam
Martain
Thanks for the reply. I went with zone 7 because I know that it is way colder their than where I live, bit over kill but that is okay. Spider is somewhere in between R 27 to 30 in a 2x8 cavity so that plus the R 20 foam should give me somewhere around R-48, is that right. Also how do you go about flashing the windows using foam? Plan on using one of those, not sure of the pronunciation, dudly box, windows are flange, nail on
Paul
Response to Paul Fowler
Paul,
Q. "How do you go about flashing the windows using foam? Plan on using one of those, not sure of the pronunciation, Dudley box."
A. For more information on how to flash a window in a wall with exterior rigid foam, see this article: How to Install Rigid Foam Sheathing.
For more information on the "Dudley box" method, see Window Installation Tips for a Deep Energy Retrofit.
Windows
Martin
Excellent. Really good information there. Think that about answers all my questions for now. Thanks for your help.
Paul
unvented cathedral ceilings - foam/batt ratio
With unvented cathedral ceilings I'm curious about the interior/exterior insulation ratios and if there's a rule of thumb for a safe, condensation free assembly. I understand this article, but often see homes being built with thin foam or thick batts. For example, in the BSC Habitat Prototype house (link below) they used 4" of polyiso over the roof deck and R40 fiberglass batts in the rafter bays. I'm sure this house is doing fine, but this insulation ratio seems more heavily weighted to the interior which should give the exterior foam a harder time keeping the roof deck above the dew point. Is there a safe ratio, or is 4" of foam enough, regardless of how deep your rafter bays or stud bays are?
http://www.buildingscience.com/documents/case-studies/cs-ma-westford-hfh?topic=doctypes/designs-that-work/dtw-case-studies
Response to Mark Fredericks
Mark,
Your question is addressed in the article on this page. The relevant section of my article can be found under the heading, "Is there a similar chart for unvented cathedral ceilings?"
In the U.S., building codes require that any unvented cathedral ceiling with some rigid foam above the roof sheathing and fluffy insulation between the rafters meet minimum requirements for the R-value of the rigid foam layer. These requirements are found in section R806.4 of the 2009 IRC, as I explain in the article.
These code requirements aim to minimize risk. Homes have been built, of course, that ignore these requirements and use thinner foam. As long as the interior relative humidity is relatively low during the winter, these homes are likely to avoid problems. In homes with high levels of indoor humidity, however, the risk of sheathing rot rises dramatically.
Was still unsure
Thanks Martin, I read that section in the original article but was still unsure if meeting the prescribed R value meant anything about the ratio of the two insulating layers. It seems like that table should be adaptable to increases with greater rafter depths.
I guess the take home message is that it's always safer to have more insulation outside the structure than inside! Thanks again Martin.
Second response to Mark Fredericks
Mark,
The code apparently assumes the use of 2x10 rafters or "typical" R-30 or R-38 batts. Since codes aim for simplicity, they don't account for all possibilities. Codes make assumptions and try to reduce risk.
Be aware of R-value
Be aware of R-value warranties on any insulation. XPS has an R-value warranty of 90%, isocyanate foam is less than that. A lot of foam thickness worries can go away by installing a smart vapor retarder on the inside of the wall along with rigorous airsealing and testing. If you don't test, you have no idea of what you have. A good alternative to foam is Roxul Comfortboard IS with ProClima products inside and out. ProClima also has some fantastic tapes for sealing things.
Rigid foam insulation over closed cell spray foam
House was built in 2008. I am told, by the builder, we have closed cell spray foam insulation with 2x4 construction. I like the idea of additional rigid foam insulation, plus rainscreen siding. Is there any types/brands of rigid foam insulation that could be used with this application?
Response to Eric Arey
Eric,
It's not a great idea to sandwich OSB or plywood sheathing between two layers of vapor-impermeable foam, but people do it. According to some authorities, the use of a wrinkled housewrap between the sheathing and the exterior foam allows for some "hygric redistribution" which can lower the risk.
EPS is the most vapor-permeable type of rigid foam, so that's probably the type of foam to use. Choose EPS without any foil facing.
zone 4 double stud
I'm designing a house in Virginia - in climate zone 4, but very close to zone 5. I am debating between
1) a 10" or 12" thick double stud wall packed with cellulose, sheathed with plywood or
2) a 2x6 wall packed with cellulose and sheathed with Zip R6 panels.
3) a 10" thick double stud wall packed with cellulose, sheathed with regular Zip or Zip R6 panels
In all three cases, the sheathing would be taped to create an air barrier and I'd install housewrap over the sheathing. I'd either install vinyl siding directly over the housewrap or lapped fiber cement siding over a rain screen.
In our climate zone, is there any reason for concern with wall assemblies #1 and #2? Am I correct that vinyl siding would provide adequate drying to the exterior?
I am more concerned about wall assembly #3. I like the ease of taping the zip system that I have read about in various GBA discussion threads. But it would be nice to have the R-value of a double stud wall. In our climate zone, would it be inadvisable to sheath a 10" thick double stud wall with Zip panels due to the poor drying of that material? Would using the Zip R6 panels add enough exterior insulation to keep the dew point outside of a 10" thick cellulose-insulated wall?
Response to Timothy Godshall
Timothy,
Q. "In our climate zone, is there any reason for concern with wall assemblies #1 and #2?"
A. No.
Q. "Am I correct that vinyl siding would provide adequate drying to the exterior?"
A. Yes.
Q. "In our climate zone, would it be inadvisable to sheath a 10-inch-thick double stud wall with Zip panels due to the poor drying of that material?"
A. In your climate zone, almost any type of sheathing should be fine, including plywood, OSB, or Zip sheathing -- especially if you include either a ventilated rainscreen or vinyl siding.
Q. "Would using the Zip R6 panels add enough exterior insulation to keep the dew point outside of a 10" thick cellulose-insulated wall?"
A. I don't think you have to worry about this issue, but if you want to perform the dew point calculation, here is a link to an article that tells you everything you need to know to perform the calculation: Are Dew-Point Calculations Really Necessary?
Roxul with Stucco
Any up date on the use of Roxul with a cementitious stucco finish.
In an article in 2011 Straube indicated more testing need to be done.
Response to Stephen Onstad
Stephen,
I haven't heard anything about recent testing of wall assemblies with mineral wool and stucco.
That said, it's worth pointing out that mineral wool insulation is vapor-permeable, so wall assemblies with exterior mineral wool can dry to the exterior. If you can come up with details for fastening the mineral wool to the wall, installing co-planar furring strips, and installing stucco, then there is no reason to believe that this type of wall would have any moisture issues.
2x6 wall with ZIP R6
Martin,
We are building high performance homes in Colorado, Zone 5, and your article was referenced regarding condensation point in walls. We are using ZIP R6 continuous sheathing over 2x6- 24" OC with dense pack fiberglass.
We added a 1" flash coat of closed cell foam in wall cavities on to meet the R 7.5 r value, and condensation concerns in the next house be built. There is a big debate here whether the flash coat is a necessary (big) cost. , These homes are very tight - around 1 air change per hour, have an ERV.
Any input would be appreciated. Thanks.
Response to David Phillips
David,
The recommendations in this article were developed to cover a range of indoor humidity levels. In theory, if there were any way to ensure the indoor humidity would always stay low, condensation (moisture accumulation) risks would drop. That would allow you to cheat on the foam thickness.
From a builder's perspective, however, the risk isn't worth it. Future indoor conditions can't be controlled by the builder. You want to build a robust wall, and you don't want any callbacks, headaches, or wet wall disasters that land you in court (or land your company's name in the newspaper). So follow the rules.
Flat Roof Issues
I am dealing with a 110 year old stucco single family with a flat roof. Insulation was modified about 20 years ago with blown in cellulose. Decking, and likely some roof joists, have failed. I suspect moisture and rock ballast may have played a role in the failure.
The roof configuration consists of a low pitch roof (probably 1:12) a parapet wall on three sides of the roof deck, and three structures rising above the roof deck (1) a chimney, (2) a doghouse (2’ x 2’) and (3) a hexagon shaped “turret” (approximately 4’ diameter).
Based upon your article I would like to close off the ventilation, leave or supplement the cellulose to pack it under the roof deck and install foam insulation board on the deck.
I was considering XPS on the roof deck because I read in a Fine Homebuilding article that it had superior vapor barrier properties and minimal moisture retention. But I have now read and considered some other issues, such as, polyiso has a higher R value per inch, and XPS requires a thermal barrier cover board such as high-density wood fiber when installed under a dark membrane.
Do you see a benefit either way?
Will polyisocyanate and XPS both act as a vapor barrier?
Can EPDM be direct glued to polyiso? Is there a preferred type of polyiso such as SecurShield or HP-H ? Is either of these suitable for direct glue? Is a thermal barrier cover board required?
If I were to use XPS, there are different varieties with different PSI ratings X= 15 psi, IV = 25 psi and V= 100 psi. Is there a preferred choice?
A roofer told me that using XPS would create a second vapor barrier, the EPDM being the first. This makes no sense, does it?
On the high side of the roof there may not be enough space to install 4.3 inches to achieve an R-25 (Minneapolis: Zone 6A). How much of a curb on the parapet wall would be required for EPDM? Perhaps we’ll need to raise the parapet wall to allow for a sufficient curb.
Is there suitable insulation board with a higher R rating to reduce the needed thickness?
If I install the R-25 board on the roof deck I assume I’ll need to open up the doghouse, turret and parapet wall and spray CC foam to create a continuous vapor barrier and R25 insulation.
Does the GBA have a list of roofers qualified to install flat residential roofs in Minneapolis?
Response to Barry Evan
Barry,
First of all, I'm surprised that you posted your questions here. There is a more relevant article that your probably want to read; here is the link: Insulating Low-Slope Residential Roofs.
Q. "I was considering XPS on the roof deck ...But I have now read and considered some other issues ...., polyiso ...Do you see a benefit either way?"
A. From an environmental and performance standpoint, your best bet is EPS. Choose one of the denser types of EPS that will hold up to foot traffic. Polyiso performs poorly in cold weather, and XPS is manufactured with a blowing agent that has a very high global warming potential.
Q. "Will polyisocyanate and XPS both act as a vapor barrier?"
A. Yes.
Q. "Can EPDM be direct glued to polyiso?"
A. The best way to answer that question is to ask the manufacturer of the EPDM roofing product that you intend to use.
Q. "Is there a preferred type of polyiso such as SecurShield or HP-H?"
A. I don't recommend the use of polyiso in Minneapolis, which is a cold climate.
Q. "If I were to use XPS, there are different varieties with different PSI ratings X= 15 psi, IV = 25 psi and V= 100 psi. Is there a preferred choice?"
A. As far as I know, any of those would work. But check with the roofing manufacturer about the need for a cover board.
Q. "A roofer told me that using XPS would create a second vapor barrier, the EPDM being the first. This makes no sense, does it?"
A. The roofer is right. But having two vapor barriers won't cause any problems.
Q. "On the high side of the roof there may not be enough space to install 4.3 inches to achieve an R-25 (Minneapolis: Zone 6A). How much of a curb on the parapet wall would be required for EPDM? Perhaps we’ll need to raise the parapet wall to allow for a sufficient curb."
A. Perhaps you will.
Q. "Is there suitable insulation board with a higher R rating to reduce the needed thickness?"
A. Assume R-4 per inch for EPS, R-5 per inch for XPS, and something like R-4.5 to R-5.5 for polyiso, depending on the temperature.
Q. "If I install the R-25 board on the roof deck I assume I’ll need to open up the doghouse, turret and parapet wall and spray CC foam to create a continuous vapor barrier and R25 insulation."
A. I don't follow you. Where do you want a vapor barrier, and why?
Q. "Does the GBA have a list of roofers qualified to install flat residential roofs in Minneapolis?"
A. No.
Foam Board on Roof Deck
Thank you Martin for your fast response. Correct, I meant to enter my comments on your article: Insulating Low-Slope Residential Roofs. Can my comment be moved?
Regarding the roof penetrations:
Since the doghouse, turret and parapet walls are not covered by the insulating boards each would allow moist vapor to rise through them and moisture to accumulate on the cold surface at the top of the parapet wall, doghouse and metal capped hexagonal turret. I thought I would need to open up each of these structures and spray closed cell foam to at least R25 to be continuous with the R25 of the roof deck.
What is the required minimum number of inches of curb for an EPDM installation?
Thanks
Response to Barry Evan
Barry,
I don't know the purpose of the structures you describe as a "doghouse" and "turret." If these structures are intended to vent the roof, you don't need them for an unvented roof. The structures should be removed if they are unnecessary.
To achieve continuity of your insulation layer at the parapets is tricky; each building is different. Suffice it to say that you want a continuous, unbroken thermal barrier (insulation barrier) around the building. The wall insulation must be connected to the roof insulation, without any gaps or thermal bridges. Where necessary, spray foam or rigid foam boards can be used to maintain the continuity of the thermal barrier.
Q. "What is the required minimum number of inches of curb for an EPDM installation?"
A. The manufacturer of the EPDM roofing that you intend to use, or your roofing contractor, should be able to provide requirements for the roofing installation.
Foam Board
Hi Martin, I haven't found EPS or XPS in thicknesses above 4.5. To achieve 6 inches Is there any problem using a double layer of 3" and staggering the seams?
Should EPS or XPS seams be taped? With what?
Response to Barry Evan
Barry,
Q. "To achieve 6 inches, is there any problem using a double layer of 3 in. and staggering the seams?"
A. No, there is no problem. In fact, two layers of 3 inch foam with staggered seams is preferable to one layer of 6-inch foam. For more information, see this article: How to Install Rigid Foam On Top of Roof Sheathing.
Q. "Should EPS or XPS seams be taped?"
A. Ideally, yes -- although some builders skip this step. It's a good idea to tape at least one of the two layers of rigid foam.
Q. "With what?"
A. Three tapes to consider are Siga Sicrall, Siga Wigluv, and 3M All Weather Flashing tape. For more information, see Return to the Backyard Tape Test.
exterior rigid foam- should i or shouldn't I
Hello Martin,
we are building a new house in north Ontario- zone 6 and have triple glazed windows. we want a tight house and very well insulated as we have extremely cold winters. our thoughts were to use a 2x6 wall filled with open cell spray foam insulation and plywood exterior sheathing. then we were going to use 3 or 4 inches of rigid EPS covered by Typar and then 1-1/2" drainage/ventilation space and wood siding. After reading your comments, I wonder if this could be a big mistake. should we move the wall sheathing to the outside of the rigid foam or possibly consider a type of structural rigid insulation like Tuff R. or maybe we should just eliminate the exterior rigid foam?
we really appreciate your help.
mike
Response to Michael Miller
Michael,
I think that you need to be a little big more specific. I'm not sure why you are worried that you might be making "a big mistake."
In your climate zone (Zone 6), if you install 3 or 4 inches of EPS on the exterior side of your wall sheathing, you'll end up with between R-12 and R-16 of rigid foam. That's plenty of foam for a 2x6 wall; the interior face of your plywood sheathing will stay warm enough all winter that it won't accumulate moisture. Moreover, because you are specifying open-cell spray foam (which is vapor-permeable) between the studs, your wall sheathing will be able to dry to the interior if it every gets wet.
So, exactly why are you worried?
Response to Michael Miller
:Leave the structural sheathing where it is. The sheathing is a class-II vapor retarder, but the sheathing is also susceptible to moisture, which is the problem you're trying to solve.
As long as the average temp of the sheathing over the winter is above the average dew point of the interior air (about 4C), it won't adsorb much moisture via vapor diffusion through the open cell foam cavity fill. Putting the EPS on the exterior keeps it warm enough, as long as the ratio of the exterior foam's R value to the total center-cavity R-value is high enough. In zone 6 about 35% of the total R needs to be on the exterior to have any margin.
With 2x6 framing and open cell in the cavity, the cavity R is about R20, and with 3" of exterior EPS you'd have R12.5 on the exterior, for total of R32.5. The ratio R12.5/R32.5 is 38%, it's definitely enough.
At 4" of EPS you'd have about R16.8 on the exterior, for a center cavity total of R36.8. R16.8/R36.8 is 46%, which would be HUGE margin over the minimum necessary to protect the sheathing.
If you move the sheathing to the exterior side of the EPS it'll run colder, and it would dry toward the exterior into the ventilation gap. The amount of interior moisture arriving at the sheathing would be very small through 3-4" of EPS, which would have vapor permeance of about 1, maybe a bit less, so it won't load up over the winter. You could do that, but it would require using something else to provide the structural rigidity against racking forces, since the moment-arm of 6" fasteners for the sheathing-to-studs would be too great.
What WOULD be a big mistake is to install 6-mil polyethylene on the interior side of the assembly, since that would create something of a moisture trap between the low permeance EPS & plywood exterior, and the ultra-low permeance polyethylene.
exterior rigid foam
Martin,
This information is what I was hoping to hear, in terms of keeping the wall sheathing dry and avoiding future dew point concerns. From what Dana has indicated, 3" rigid will work well. And I can keep the sheathing against the wood framed wall assembly! I have decided on using the "outies" windows to help minimize any water infiltration potential and give us some decent size window sills for the cats to sit on. The windows will be needing fasteners that penetrate the 3/4" plywood window box, the 3" rigid insul, the 1/2" sheathing and anchor about 1-1/2" into the studs. Do you see any problems using long screws or will they compress the rigid insulation?
thank you for your help.
Response to Michael Miller
Michael,
I'm glad you are reassured, but I'm surprised that the article on this page wasn't enough to reassure you. The information in the article (and the table that is the heart of the article) should have put your concerns to rest.
For the answers to your questions about window installation, I recommend that you read this article: Installing Windows In a Foam-Sheathed Wall.
"Value engineering" wall insulation options
We are in the Boston area, Zone 5, I believe. The exterior wall section we designed for the renovation of our one-story house, built in 1950, was for existing and new 2x4 walls filled with dense-packed cellulose insulation in the stud cavities, 1/2" plywood sheathing, a fully adhered W. R. Grace Vycor enV-S weather restrictive barrier, covered by 2" of polyisocyanurate board insulation, furring strips, 3/4" wood siding, and "outie" fiberglass windows. The interior will have 1/2" GWB with veneer plaster and latex paint, no other vapor retarder or vapor barrier. We recently received final pricing updated from the preliminary pricing of a year ago, and the overall price has gone into the stratosphere. Apparently, this is fairly common these days in the Boston area where the construction industry is very hot. We are looking at ways to reduce costs in all aspects of the house design, the exterior walls included.
I would like opinions on making the new exterior walls (approx. 112 linear feet) of 2x6 studs with dense-packed cellulose, 1/2" plywood sheathing, a fully adhered W. R. Grace Vycor enV-S weather restrictive barrier, covered by 1.5" of XPS board insulation (R-7.5), furring strips, and 3/4" wood siding. Some have recommended the new walls of 2x6 studs with dense-packed cellulose, Huber Zip System R-Sheathing 1.5" panels (R-6.6), furring strips, and 3/4" wood siding. I am concerned that this Zip system is not suited for our Zone 5 because: the R-value is below 7.5 for a 2x6 wall, the polyisocyanurate insulation layer would be on the interior side of sheathing instead of the exterior side, and that sheathing is just impregnated OSB that would be screwed through 56 times times in every 4x8 panel, compromising its effectiveness as an air and water barrier. To economize on the existing 2x4 walls (approx. 77 linear feet), I am thinking of filling the stud cavities (which have 2-cell Infra radiant barrier aluminum foil insulation) with dense-packed cellulose or open-cell spray foam insulation, installed from the inside and not replacing the existing windows or adding the recommended R-5 sheathing for 2x4 stud walls and then needing to replace the siding. We also have approximately 62 linear feet of insulated window walls facing south, and approximately 58 linear feet of an 8" CMU wall facing east. Your thoughts? Can you recommend any other cost effective wall sections to achieve a similar R value (approx. R-26) in the exterior stud walls? Thanks for your input.
Response to Timothy Oldfield
Timothy,
First of all, you will get more answers to your questions (including answers from the many intelligent members of the GBA community) if you post your question on GBA's Q&A page. Here is the link:
https://www.greenbuildingadvisor.com/qa
Second: If you want to lower the cost of your planned construction project, the best person to talk to is your builder. Your builder will have a much better idea of ways to lower the cost of the project than we will.
Third: Your wall contains some unusual features, including a radiant barrier (something that makes me go "Hunh?") and a fully-adhered WRB (a feature that probably performs very well, but which undoubtedly costs more than most WRBs).
Response to Martin Holladay
Martin,
Thank you for your quick response. As you recommended, I posted my questions on the Q & A page. We are working with the builder on lowering costs, and at the same time I wanted to get the advice of the broader GBA community. The Infra radiant barriers were installed in the walls and rafter bays in 1950! It's interesting to read about Infra and its rise in popularity in the '50's, and then its demise. I decided to use a fully adhered WRB after reading Joe Lstiburek's essay on its benefits. Thanks again for your ongoing work on this website.
Exterior Wall for Small House in Main
Martin:
I need to ask for your help. ASAP. I'm building (together with a professional residential contractor) a cabin (small house) for myself in MidCoast Maine (04553). Climate Zone 6.
The cabin is 24' x 20', will be a single story with a 12/12 gable roof..
We've already:
1. Built an ICF Foundation.
2. Installed sill plates, floor joists, and floor sheathing (Advantec).
3. The sill plates were setback 1.5” from the outside of the ICF to accommodate 1.5” of PolyIso that was going to be installed outside of the exterior sheathing, to which the cladding (with spacer) was going to be attached.
We're now ready to build the walls.
4. Until two days ago, we were planning on installing from interior to exterior:
a. 5/8 gypsum
b. 2" x 6" studs filled with cellulose or such
c. Zip Sheathing with Taped Seams on outside of studs.
c. 1.5” of PolyIso per #3 above.
e. Some sort of product to create air space
f. Cladding (likely cedar shingles
5. But in reading your blog, we realize what we were planning to do is INADVISABLE.
Can you give us advice, asap, as to what wall system you'd recommend we use. We were to start framing the exterior walls at 9AM tomorrow (Monday) morning. But we are going to try and hold off and wait to first try and receive word back from you.
Thanks in advance for your help.
Response to Glen Berkowitz
Glen,
The answer is provided in this article: in your climate zone, the minimum R-value for exterior rigid foam over 2x6 walls is R-11.25. Because polyiso doesn't perform well in cold weather, it's best to consider the R-value of polyiso in this location as R-4.5 or R-5 per inch. So 1.5 inch of polyiso should be considered to have an R-value of R-6.75 to R-7.5. That's not enough.
If you want to use polyiso, you need at least 2.5 inches of polyiso for this wall. Thicker rigid foam would also work.
R-3 foam board
Hi Martin,
I am considering hardie board siding on my house in Colorado. It currently has wood siding and is being eaten by woodpeckers and generally not in good shape. A contractor today said he could add foam board insulation under the siding but that it can't be very thick otherwise the screws won't go in enough to meet hardie board standards. So he said he could use a "thin" foam board that has an R-3 rating which sounded very low to me. Plus I knew there were moisture risks associated with the use of foam board under siding. I found your article and from what I understand this guy is really steering me wrong? It seems like just using very long screws with thicker foam board that meets your criteria would be what is needed here? But it also sounds like we shouldn't use foam board at all if there are any moisture issues happening under the current siding. Since I have holes in my current siding I'm concerned about this. Other solutions to the insulation need?
Thanks so much for the article!
Shara
Response to Shara Howie
Shara,
The answers to your questions are in the article on this page.
You didn't tell us your climate zone. Colorado has four climate zones, so you will have to check the climate zone map if you haven't done that yet. Here is the link:
https://www.greenbuildingadvisor.com/sites/all/assets/htzones_with_cities_abc.jpg
Then you have to check whether you have 2x4 or 2x6 studs. If you aren't sure how to do this, you should ask a builder to help you determine your stud size.
One you have determined your climate zone and the details of your wall framing, you can calculate the minimum thickness of any exterior rigid foam. If you live in the warmest corner of Colorado (zone 4A), your contractor's plan would work.
If it turns out that you need thicker rigid foam, your contractor can install vertical furring strips (1x4s) on the exterior side of the rigid foam, and can attach the new siding to the furring strips.
Edmonton Canada
This is very timely for me.
We do a lot of 1.5" EPS over StoGuard waterproof air barrier with closed cell spray foam in a 2x6 wall. The HRV is standard equipment in these buildings and we will be putting vinyl wallpaper in a couple of places on one on-going project.
We're normally pretty dry up here; should I wave the client off the vinyl?
Response to Quinn Parrott
Quinn,
Your methods raise a lot of red flags.
Edmonton, Alberta is on the border of Climate Zone 6 and Climate Zone 7. (Here is a link to a climate zone map for Canada.)
1.5 inch of EPS has an R-value of R-6. That is nowhere near enough rigid foam to keep your sheathing above the dew point during the winter. If you are building 2x6 walls in your climate zone, the exterior rigid foam needs to have an R-value of R-15 or more. If you are using EPS, that means that you need at least 4 inches of EPS, not 1.5 inch.
If your walls have exterior rigid foam, it's essential that the walls be able to dry to the interior. That means that you can't install any interior polyethylene or vinyl wallpaper.
Thanks for this - the timing
Thanks for this - the timing has been perfect.
Not a problem, exactly...
He's insulating the cavities '...with closed cell spray foam in a 2x6 wall...".
If there's at lease 2" of closed cell foam on the interior side of the sheathing there isn't a dew-point control rationale for more exterior EPS, since the closed cell foam is a class-II vapor retarder (and qualifies as a "vapour barrier" per Canadian code definitions.) There's probably more like 4-5" of closed cell foam, at abotu 0.2-0.25 perms, WELL into class-II vapor retardency. The sheathing dries toward the exterior, through 1.5" of EPS (about 1-1.5 perms.)
Bumping the EPS to 4" would make it less than 1 perm but still over 0.5 perms, which would be fine if it's all dry when assembled. It still dries toward the exterior, but very slowly.
Vinyl wallpaper has some potential for creating a moisture trap, since the drying rates through the 0.2 perm closed cell foam are glacial at best.
Response to Dana Dorsett and Quinn Parrott
Dana,
Thanks for your comment. You're right, of course, about the closed-cell spray foam.
When I originally read Quinn's comment, several alarm bells went off -- which is why I responded, "Your methods raise a lot of red flags." I meant to get around to the issue of using closed-cell spray foam between the studs -- but by the time I addressed the other issues, I managed to forget about the problems raised by the use of closed-cell spray foam.
Quinn: In my article, I wrote, "This type of wall must be able to dry inward, so it's important to avoid low-permeance layers like polyethylene, vinyl wallpaper, or closed-cell spray foam on the interior." So my vote is to stop using closed-cell spray foam between the studs.
Better choices include cellulose, mineral wool, or carefully installed fiberglass. If you insist on using spray foam, make sure that it is open-cell spray foam, which is vapor-permeable -- not closed-cell spray foam.
Noted. Thanks to you both.
Noted. Thanks to you both.
Cut-and-Cobble and Moisture
Hello! I am new here - not a builder, but generally interested in energy saving solutions that make sense.
I have a two-story house in Zone 4-A with a first floor that now has 2x6 studs (2x4 plus a 2x2 addition). For various reasons, doing cut-and-cobble will be the least time and money consuming method to increase the insulation of this first floor. Currently, there is 2x4 fiberglass between the studs, against the outside wall, and I would like to add some rigid foam on top before installing dry-wall. I have searched this and various other articles, but cannot find a clear confirmation that my method will work well. Can I use 1 inch rigid foam? (To clarify: Outside - fiberglass - rigid foam - drywall.) Should or should I not use some additional vapor barrier?
Thanks so much!
Miriam
Response to Miriam Kraatz
Miriam,
It's possible to insulate walls with interior rigid foam. Here is a link to an article on the topic: Walls With Interior Rigid Foam.
However, your situation sounds unusual. I'm not exactly sure what you mean when you write that you have a house with "a first floor that now has 2x6 studs (2x4 plus a 2x2 addition)." Did you extend the existing 2x4 studs with 2x2 strips (measuring 1.5" x 1.5") and nail those strips to the 2x4s so that the studs resemble 2x6s? If so, that was a mistake.
If you want to install interior rigid foam, the foam should be installed in a continuous layer, so that the rigid foam interrupts the thermal bridging through the studs. It's always a bad idea to cut rigid foam into narrow strips and to insert the narrow strips of rigid foam between the studs.
So, to give you the best advice, you should describe your current situation, and how you got there.
Response to Miriam Kraatz
Miriam, I'll suggest you go ahead and submit your question as a new question is the Q&A section. That will probably help more people see it and make it easier to keep track of.
How I got to where I am
Hello Martin,
thank you so much for your reply! I know it is convoluted, and there is thermal bridging, and it's time consuming and messy, but yes, I added 2x2 (1.5x1.5) extensions to my 2x4 studs. Here is the reason: The original studs are sturdy, but all over the place, both in parallel to the wall (i.e., they have all kids of weird angles), and when considering the direction into the room (i.e., some parts stick out a little, other parts have indentations etc.). The original wall covering was some horrible cheap ugly veneer.
The builders agreed that the studs as they were would be a little annoying to attach drywall to and possibly even problematic (this is the same reason why installing rigid foam over the original studs was not considered). A very, very handy woodworker installed the 2.x. extensions so that they create a good base for drywall. Now I have the two (1.5) inch deep cavities between fiberglass and where the drywall will be. I have had extremely pleasant experiences with air/draft sealing in another house that I live in.
Even if it takes an extra second and is not the best possible solution (which would have been tearing out the studs and old insulation, but that was not an option), I feel confident that this will lead to improvement and just want to make sure that I am not going to create a moisture risk for the house.
Also, don't scold me too harshly! I am new to this stuff, just trying my best, and someone is waiting to move into that room on the first floor now. Lol. First house. I will keep learning from mistakes!
@Charlie: I'll put it in there later tonight. Thanks for the suggestion!
Miriam
Wall with interior rigid foam
Hello Martin, I read the article you mentioned, and it seems like my scenario will not create the moisture issues I am worried about. Would you also like me to repost my question as a new Q&A?
Miriam
Response to Miriam Kraatz
Miriam,
It sounds like you are all set. Good luck.
With 2 in Polyiso in Zone 6 Should I reduce interior insulation?
I finished installing 2" Polyiso foam board on the exterior of my new house in Maine in zone 6. The stud walls are 2x6. I just found the articles that say the polyiso is not really going to give me r 13 at cold temps but more like r 10 or even less. If i account for the decrease in the rating of the polyiso I no longer have enough exterior insulation. Should I consider using 2x4 sized r 13 fiber glass or r 15 mineral wool over r 19 or 21 2x6 insulation to prevent condensation?
Response to Michael Prisco
Michael,
As the table accompanying this article shows, if you want to install exterior rigid foam on a house with 2x6 walls in Climate Zone 6, the rigid foam needs to have a minimum R-value of R-11.25. Now that building scientists understand that polyiso performs poorly at cold temperatures, builders in your zone should really be installing 3 inches of polyiso, not 2 inches of polyiso, over 2x6 walls.
There are three ways you can reduce the risk of damp sheathing:
1. As you propose, you can downgrade the fluffy insulation to R-13.
2. You can keep an eye on your indoor relative humidity during the winter, and aim to keep it at 30% or lower. That will reduce your risk compared to homes with 35% or 40% interior RH. However, if you ever sell the house, the next homeowner may not be as conscientious as your are, so this isn't really a long-term solution.
3. You can use full-depth fluffy insulation, but cover the studs on the interior with a smart vapor retarder like MemBrain. The smart retarder will reduce outward vapor flow during the winter, helping to keep the sheathing dry. That should keep your walls safe enough to allow you to sleep at night.
Response to Martin Holladay
Martin,
Thank you for the quick and detailed response. Glad to know I have options. If I went the R-13 route would you have a recommendation on the placement of the batt? ie pushed back in to the sheathing of pulled out to the face of the stud with a gap between the insulation and the sheathing?
[Editor's note: To read the answer to this question (and to continue reading other comments), click the number "4" below to proceed to page 4.]
Response to Michael Prisco
Michael,
The batts should be in direct contact with the exterior sheathing. You might want to install some steel insulation supports (like these) to keep the batts in place and prevent them from slumping.
Response to Martin Holladay
Thank you. This website and community is such an incredible resource. I learn so much every time i visit.
Follow up question to Martin Holladay
Martian,
I wanted to follow up with your response from this morning. I would really like to get the highest R value I can out of the walls. I had originally planned on using mineral wool in the 2x6 walls which is more like r-23. Using r-23 I would likely put the dew point somewhere in the mineral wool. Has the MemBrain proved effective in a case like this? Or would it be safer to go with the R-15?
Response to Michael Prisco
Michael,
It's hard to gauge the risk, frankly. I know what building scientists recommend -- and I tend to be conservative. I also know that people sometimes break the rules, and that many rule-breakers don't suffer problems.
The families that have problems with sheathing rot are probably the families that maintain high indoor humidity levels. Interior MemBrain will probably keep your wall safe, but nothing is guaranteed. If you install R-23 mineral wool and MemBrain, it wouldn't hurt to keep an eye on your interior humidity. Whatever you do, don't install a humidifier.
I'm sorry that my answer can't be more definitive.
Another question for Martin Holladay
Thanks again for you quick responses. They are very helpful. I keep going back and forth on a decision. I like the idea of being conservative. If I went with r15 insulation in a 2x6 wall what would the effect of the 2" air gap between the drywall and the fluffy insulation? Would it create a place for convection and greatly reduce the r 15 value or does the air gap add R value?
Response to Michael Prisco
Michael,
Q. "Would it create a place for convection and greatly reduce the R-15 value or does the air gap add R-value?"
A. It would potentially create a place for convection, but the reduction in the R-value of the insulation would probably be minor. You're going to have to let that worry go, Michael, because what you are doing is deliberately making sure that the stud bays are poorly insulated. The reason you are doing that is because you didn't install enough exterior foam. You've boxed yourself into a corner, frankly -- so stop trying to improve the R-value between the studs. You want the R-value to be low.
Response to Martin Holladay
Thank you for your frankness. I did box myself into a corner and know what I have to do. Cheers.
New Building Wall Section
Hello Martin-
Great article and blog! We are trying to finalize a wall section for a new project. We are in zone 5 (Chicago). We have 2 x 6 metal frame walls 24" on center. We are considering the following section outside to inside:
-4 inch face brick
- 1.5 inches Rmax / EcomaxCI with a stated R value of 10.
- 5/8 Dense Glass Gold
- R13 fiberglass batt insulation
- 5/8 interior drywall
Do you see any issues with this section? Should we use faced or unfaced batt insulation? Do the aluminum facers on both sides of the EcomaxCI present any problems? If we went to R-19 batt insulation do you think we should increase the EcomaxCI to 2 inches?
Thank you
Response to John McFarland
John,
Steel-stud walls don't perform like wood-frame walls. Thermal bridging through the steel studs completely dominates the thermal performance of the stud wall; for all intents and purposes, and insulation installed between steel studs is a waste. It's money down the drain.
With a steel stud wall, all of the insulation has to be installed on the exterior side of the steel studs. In Climate Zone 5, the code calls for a minimum of R-20 wall insulation. If you want to use polyiso, remember to de-rate the polyiso R-value because polyiso performs poorly at cold temperatures.
I'd say that your wall needs at least 4 inches of polyiso -- and 5 inches would be better.
Thanks for the reply Martin.
Thanks for the reply Martin. We thought about four to five inches of exterior insulation but were concerned about window installation and how masonry ties could be adhered by having to go through that much insulation. Any thoughts on that? Thanks again
Response to John McFarland
John,
This question has come up on GBA a few times before. One GBA reader recommended Simpson Heli-Tie Helical Wall Ties. Contact Simpson for more information.
Another company you might want to contact is Rodenhouse. This video shows one of their fastening and brick tie systems. I'm not sure of the maximum thickness of rigid foam that this system can accommodate, but it might be what you are looking for.
.
Is the DensGlass structural?
Positioned between the foam and the steel studs what function is the exterior side gypsum serving?
Code min for residential construction is 2x6/R20 between wood studs or 2x4/R13+ R5 continuous insulation, either of which performs about the same as R15 continuous insulation. The maximum U-factor is U0.057, which R17.5 whole wall, after adding in the performance of the brick, the interior gypsum and the air films, etc.
http://publicecodes.cyberregs.com/icod/irc/2012/icod_irc_2012_11_sec002.htm
The R10c.i. + R13 between steel studs with the brick and both gypsum layers meets that performance level but only barely. At a typical 15% framing fraction R13 in steel studs delivers about the same performance as R5 continuous insulation:
http://web.ornl.gov/sci/roofs+walls/research/detailed_papers/thermal_frame/
So, from a thermal performance point of view, at the very same wall thickness you'd be better off replacing the 5/8" of gypsum with more polyiso and using steel bracing for structural rigidity, but keeping the R13s in steel, which would add another ~R3 to the whole wall R (after subtracting the performance of 5/8" gypsum and adding in the performance of 5/8" polyiso.) Without the R13s in steel studs you'd have to go with at least 3" polyiso to hit code min performance, when properly derated for temperature/climate.
Do the math on whether R13s in studs is more expensive than another inch of polyiso, or whether it's cheaper or better to go with gypsum vs. cut in bracing if wall thickness is a concern.
27%
Is the 27% of the wall value the real wall value including the framing factor or just simply adding R values?
What is the percentage for cathedral ceilings? Zone 5 specifies R20 that would mean a total of 20/27x100=R74. That looks a bit high.
Response to Tony Tibbar
Tony,
The answer to your questions can be found in this article: Combining Exterior Rigid Foam With Fluffy Insulation.
Concerning your question about the "27%" figure in my table on walls, the explanation in my article notes, "The tables are based on the nominal value of the insulation layers, without taking into account the effects of thermal bridging through the studs. The tables show the minimum percentage of the total R-value of the assembly that needs to come from the rigid foam layer."
The same article also discusses cathedral ceilings. In Zone 5, 41% of the roof assembly's total R-value needs to come from the rigid foam layer (assuming we are talking about a roof with a combination of exterior rigid foam and interior fluffy insulation).
More information on cathedral ceilings can be found in these two articles:
How to Build an Insulated Cathedral Ceiling
How to Install Rigid Foam On Top of Roof Sheathing
Below is the table with information on walls.
.
Thanks Martin
Totally clear now. I overlooked the 41%
Will 2 inches of Polyiso be adequate in Zone 6
I've been pouring through this website but I can't seem to find an answer to this. Looking at the chart, I need a minimum of R 11.5 for exterior rigid foam sheathing. A lot of the 2" Polyiso foam board I see advertised is R 13. But I've read you have to degrade the R factor in colder temperatures. So will 2" Polyiso be OK? I am building in North Idaho and will be right on the border between Zone 5 and 6, but am in Zone 6. I ask as the cost of sheets of 2" Polyiso appear to be 60% of the cost of going with 2.5 inch XPS.
Response to Steve Wolfe
Steve,
The answer can be found in the article on this page, which states, "GBA recommends that cold-climate builders use caution when choosing a rigid foam designed to keep wall sheathing above the dew point during the winter. Either EPS or XPS is probably a safer choice for this purpose than polyiso, unless you derate the performance of the outermost layer of polyiso to about R-4 or R-5 per inch."
So, if you feel safe assuming that polyiso has a value of R-5 per inch in cold weather (rather than R-4 per inch, which is more conservative), then 2 inches of polyiso (R-10) is insufficient. You should go with 2.5 or 3 inches, or switch to a different type of rigid foam.
Adding exterior rigid foam to a wall with interior polyethylene
Many energy experts worry that it may not be a good idea to install exterior foam on a house with an interior vapor retarder. Although it would be better if the vapor retarder weren't there, the fact is that tens of thousands of Canadian homes with interior polyethylene have been retrofitted with exterior rigid foam, and there haven't been any reports of widespread problems. According to building scientist John Straube, all indications show that these retrofits are "not so risky as most people think. These homes will probably be fine."
That said, the installation of exterior foam is not advised on any home that has suffered wet-wall problems like leaking windows or condensation in stud cavities. If you plan to install exterior foam during a siding replacement job, keep an eye out for any signs of moisture problems when stripping the old siding from the walls. Investigate any water stains on housewrap or sheathing to determine whether the existing flashing was adequate.
If there is any sheathing rot, determine the cause -- the most common cause is a flashing problem, but condensation of interior moisture is not impossible -- and correct the problem if possible. If you are unsure of the source of the moisture, hire a home performance contractor to help you solve the mystery.
If your sheathing is dry and sound, I don't think you need to worry about adding exterior foam. Adding a rainscreen gap will certainly go a long way toward avoiding future moisture problems. Of course, it's important to be meticulous with your details when you are installing your new WRB and window flashing. It's also important to keep your interior relative humidity within reasonable levels during the winter. Never use a humidifier.
To summarize, here are four caveats:
1. Be sure that your foam is thick enough to keep the wall sheathing above the dew point in winter. Read more on this topic here: Calculating the Minimum Thickness of Rigid Foam Sheathing.
2. When the siding is being removed, inspect the existing sheathing carefully for any signs of water intrusion, and correct any flashing or housewrap problems.
3. Install rainscreen strapping so that there is a ventilated gap between the new exterior foam and the siding.
4. Keep your interior humidity under control during the winter; if the interior humidity gets too high, operate your ventilation fan more frequently.
-- Martin Holladay
Residing Project
Our home in Maine was built in the late 80s, has 2x4 construction and was poorly insulated, probably R10 unfaced. We are replacing the roofing and siding (cedar shakes) and would like to add exterior rigid foam to the walls. I have read exhaustively through this website and others and it seems we need a minimum of R7.5 so I'm thinking of 1.5 inches of XPS followed by another layer of 1/2 sheathing, draining housewrap, then the shakes. Unfortunately, the interior walls do have a layer of poly behind the drywall. I have read that is a potential issue as it would impead drying to the inside. Would we be making a big mistake to proceed with the foam anyway? Wondering if the risk is just too much and we should give up on the foam.
XPS
I would also advise using something other than XPS, because the R-value of XPS decays over time as the gas it's made with diffuses out. That gas also is a potent greenhouse gas. EPS or neopor does not have that problem, and is also more vapor permeable so you can have at least a tiny bit of drying to the outside. And 2" of EPS is probably cheaper than 1.5" of XPS.
See https://www.greenbuildingadvisor.com/articles/dept/musings/thermal-drift-polyiso-and-xps
What Charlie said.
Using 2" of unfaced 1.5lbs density "Type-II" EPS delivers more dew point control, but also allows a higher drying rate toward the exterior, since it's vapor permeance is about twice that of 1.5" XPS.
XPS performance eventually decays to that of EPS of similar density, whereas the thermal performance of EPS is stable over decades.
Using reclaimed EPS from salvage companies or foam reclaimers is cheaper still. EPS is a popular roof insulation in flat commercial roofs, and 2-4" thick reclaimed EPS is usually pretty easy to find at 1/4- 1/3 the cost of virgin stock goods. In southern ME you're in reasonable trucking distance from some of the larger recliamers in MA (Green Insulation Group in Worcester, or Nationwide Foam in Framingham), and even with freight going with 2-3" EPS is going to be quite a bit cheaper than virgin stock 1.5" XPS at building materials distributors.
EPS
Thank you Martin, Charlie, and Dana. After getting some quotes for adding 1.5 to 2 inches of either XPS or EPS followed by another layer of 1/2 plywood sheathing, I found the labor of the additional layer of sheathing stresses our budget too far. However, I'd still like to add some insulation value, thermal break, and air sealing during our siding project. We are going to side with cedar shakes. Would 1/2" EPS be permeable enough to avoid moisture due to condensation? The plan would be to apply the EPS to the existing sheathing, followed by drainable housewrap, then the shakes.
1/2-inch EPS?
You should contact the manufacturer of the rigid foam to find out the vapor permeance of the EPS in question -- some brands of EPS have a vapor-impermeable facing. If there is no facing on the EPS, its vapor permeance may be as high as 4 perms or 5 perms.
If I were you, I wouldn't install a product like EPS that slows outward drying of the wall sheathing. You really want damp wall sheathing to dry quickly, not slowly.
According to my article, if you install rigid foam on the exterior side of 2x4 walls in Maine (Zone 6),the rigid foam needs to have a minimum R-value of R-7.5. I stand by that advice.
-- Martin Holladay
Shake installation tool and mineral wool
I agree with Martin--even though EPS can have some vapor permeability, I'd be disinclined to do anything less than the recommended thickness.
Here are some other suggestions that might help:
1) There's no minimum thickness requirement for mineral wood insulation boards, because they have high vapor permeability. You could install whatever thickness you can afford.
2) To reduce labor cost on your project, and have some spare change to put into insulation, consider this installation tool for the shakes.
http://sbccedar.com/en/05_products/02_siding-roofing-shingles-09.html
I'm not sure how many installers are already using those, but the carpenter who installed our shingles hadn't seen one before and though it was a big improvement.
3/8" fan-fold perforated siding underlayment would be OK
The fan-fold XPS siding underlayment runs about 5 perms and has a reasonable history in retrofits. It's only about R1.9 when new, dropping to ~R1.5 slowly over time. On typical 2x4 wall that would be about a 13% improvement in wall performance on a U-factor basis.
Half inch Type-I EPS would be about R1.9 on day 1, and on day 100,001, but the facers create a moisture trap.
I've never seen half inch EPS of any density/type without facers. Maybe it exists (and maybe the tooth fairy gets around on a unicorn too.) It would be too fragile to survive much handling without knocking off corners, unless it's of a sufficiently high density to reduce
3/4" asphalted fiberboard is about 15 perms when the humidity is high- that's more vapor open than Typar housewrap, and it would add about R2 to the stackup. Half inch asphalted fiberboard runs about R1.3. Fiberboard has reasonable fastener retention for siding, and would add structural rigidity to the stackup. Whether it's "worth it" for that marginal improvement is up to you, but it's a better choice than way-too-thin foam. Half inch fiberboard is easier to find than 3/4", and under $10/sheet for 4'x 8' if you can find a local distributor stocking it.
http://commerce.bluelinxco.com/wcsstore/ExtendedSitesCatalogAssetStore/images/documents/105805448.pdf
http://www.homedepot.com/catalog/pdfImages/95/958dd23e-8bdf-4340-a701-61b855d9c5df.pdf
A single layer of half-inch fiberboard would deliver about a 11.5% improvement in U-factor for a typical 2x4 wall.
For about the same material cost as a layer of half-inch fiberboard, single layer of 2" reclaimed polyiso would deliver a 55% improvement in U-factor. That's less than half the heat loss of the "before" picture, or more than double the whole-wall R value.
See BSI-092 for discussion
See BSI-092 (How Come Double Vapor Barriers Work?) for a discussion about less-than-condensing amounts of somewhat vapor permeable foam and an interior-side vapor barrier working well. With 2x4 walls, 3/4" foam would have even better moisture performance.
Adding poly-iso in climate zone 3 to 2x4 wall
Hi Martin, as part of my remodel to improve earthquake resistance (and support some larger window openings) most of my 2 story 2x4 wall has been updated with PSL beams and hardy frames. They fill the complete wall depth so I will loose insulation and I was thinking to add 1" poly iso. House in Woodside, CA (Climate zone 3).
Can I have the following setup from exterior to interior:
1. 5/8" cedar shiplap (vertical install)
2. BENJAMIN OBDYKE HOME SLICKER HOUSEWRAP w/ INTEGRATED RAIN SCREEN
3. 1" poly iso
4.OSB wall board with every gap sealed with siga-tape (OSB nailed to create needed shearing)
5. 2x4" wall with blown in cellulosa or cotton batt insulation
6. Interior shearing if needed, f not this is the final drywall.
7. If shearing also needed from the inside OSB in step 6 and drywall as step 7.
Any problem with this setup?
Also how to keep the poly iso in place? Can you use 1.5" nails to nail the house wrap and through the poly iso and into the OSB?
How to then hold the rain screen until you have the siding in place? Nail again into just the poly-iso (just lightweight plastic mesh)?
Finally the cedar with shiplap can be nailed through and into to the OSB?
Thanks,
Response to Mats Lundgren
Mats,
Q. "Any problem with this setup?"
A. No.
Q. "How to keep the polyiso in place?"
A. Polyiso is installed with cap nails. For more information on this issue, see How to Install Rigid Foam Sheathing.
Q. "Can you use 1.5 inch nails to nail the housewrap and through the polyiso and into the OSB?"
A. Housewrap is also installed with cap nails. As the article which I linked to explains, cap nails are available in a wide variety of lengths. You are correct: you need the nails to reach the OSB. Be sure to follow the installation instructions of the housewrap manufacturer.
Q. "How to then hold the rainscreen until you have the siding in place?"
A. Again, cap nails will work (as far as I know -- but it never hurts to read the installation instructions -- in this case, the instructions provided by Benjamin Obdyke). All you need for each of these layers is minimal attachment until the next layer is secured. You just need to prevent everything from being stripped away by the wind until the job is done.
Q. "Finally the cedar with shiplap can be nailed through and into to the OSB?"
A. In most cases, siding is fastened to the studs, not to the sheathing. That's why horizontal siding is easier to install than vertical siding. Many types of siding, including vertical shiplap, are best attached to horizontal blocking between the studs. If you haven't anticipated this problem by installing horizontal blocking, you need to either (a) switch to horizontal siding, or (b) attach your siding with screws rather than nails, and talk to an engineer (or the siding manufacturer) to verify that attaching to the sheathing is sufficient.
Foam thickness zone 6a
Hi Martin, we are residing a 1950 something ranch house. The inside walls are 3/8 drywall with plaster on top. Wall cavity is 2x4 with Rock Wool Batts (paper on both sides). Appears to be Shiplap sheathing.
I would like to put 2" Type 2 EPS foam on the sheathing and then vinyl siding. Could I put #30 felt on the sheathing followed by the foam and then use Tyvek? or should I skip the felt? Just foam and Tyvek. FYI new windows will be installed with the siding so they will be outies. How thick can the foam be before a Dudley is needed? Thank you!
Response to Zone 6
Zone,
Q. "Could I put #30 felt on the sheathing followed by the foam and then use Tyvek?"
A. Yes.
Q. "Or should I skip the felt? Just foam and Tyvek?"
A. It's your choice. Every wall needs a water-resistive barrier (WRB). If you decide to install both asphalt felt and Tyvek, you need to decide which of these two layers will perform as your WRB. If you skip the asphalt felt, then clearly the Tyvek should be your WRB.
Q. "How thick can the foam be before a Dudley box is needed?"
A. The question has no easy answer, because there are so many variables when it comes to window installation. A lot of the relevant discussion and recommendations can be found in this article: Installing Windows In a Foam-Sheathed Wall.
Follow up questions
Hi Martin!
Thank you for the quick reply, however now it seems we have more questions. Our window installer will not install windows over foam thicker then 1 1/2". He suggests a wooden picture frame around the windows (like you did in the 80's) if we want 2" foam. Here is his suggestion for our Wisconsin home.
"As far as the comments on the foam thickness, its acknowledged in the building science community that 1.5" XPS foam will be sufficient to control the dew point to mitigate condensation. Frost is simply "flash" frozen condensation, so the same would apply. That thought more commonly is when there is no other substrate existing, so the fact that you have wood sheathing that you are going over only serves to add to that. The type and qty of insulation in the wall cavities, presence (or lack thereof) of a plastic vapor barrier on the interior side factor into that as well. If I recall, you have a plaster over sheetrock interior wall, so no plastic exists. If this were my home, I would use XPS foam of between 3/4 and 1 1/2" thickness. If additional insulation was desired, dense pack the wall cavities with cellulose. I have concerns about the siding installation over 2" of foam without any furring as well. That's a pretty large gap for those nails to bridge. Lastly, I'd also recommend a having a blower door test after these installs as you will be tightening the home up quite a bit in terms of air exchange. You will want to ensure that the ACH is sufficient to maintain good indoor air quality."
Would the picture frame (maybe 4' wide) be a source of Thermal bridging?
Would a 2" thick frame made with a 1" thick board and 1" of foam solve the Thermal bridging problem?
Should we just give up and use 1 1/2" XPS?
If so
We would put the 1 1/2" XPS foam on the sheathing leave the joint untaped and use Tyvek as the WRB.
Do you think this method be good for our zone 6A home?
FYI- Not sure how many walls have the Rock Wool, I have found some places that have paper backed fiberglass.
Thank you!
It's hard to parse some of those comments... @ Zone 6
Even with mental filters wide open I have a hard time figuring out what your contractor really means.
But here is is in an nutshell:
In US climate zone 6 a 2x4 wall with cellulose / rock wool / fiberglass cavity fill and at least R7.5 on the exterior meets the code prescriptive for dew point control:
https://up.codes/viewer/general/int_residential_code_2015/chapter/7/wall-covering#R702.7.1
The labeled R value of 1.5" XPS is R7.5, but it will eventually drop to about R6.3 as it's climate damaging HFC blowing agents leak out over a few decades. If XPS, use at least 2".
Leaving the foam seams untaped does next to nothing for improving drying, but it does reduce performance. Tape it.
Polyisocyanurate at 1.5" will underperform it's R9-R10 (~ R6/inch) labeled R during the coldest days of winter, but in your stackup you can count on at least an R5/inch average over a winter. If you're really stuck at 1.5", use polyisocyanurate. Polyisocyanurate is also greener, blown primarily with (low environmental impact) pentane, and it's very long term performance won't take the hit that XPS does.
Long-nailing through even 1.5" foam isn't a great way to hang vinyl siding, and may violate the siding manufacturer's specs.
Response to Zone 6 (Comment #182)
According to Joe Lstiburek, it's possible to install vinyl siding through rigid foam as thick as 1.5 inch with long nails. I have never tried this approach, but Lstiburek says it works. If you try it, remember that you can't nail everything snug -- the vinyl siding still has to be able to slide right and left in the nailing slots.
If the rigid foam is any thicker than 1.5 inch, or if you are nervous about the "long nails" approach, the solution is to install the siding on vertical furring strips. There is only one catch: most vinyl siding manufacturers prohibit the installation of their siding on furring strips. Does this make sense? Probably not, but that's what the manufacturers say. For more information on this controversy, see Can Vinyl Siding be Applied Over Furring Strips?
One way out of this box is to switch to a different type of siding -- for example, fiber-cement lap siding.
Not all "picture frame" methods of window installation involve thermal bridging. You should read this article: Installing Windows In a Foam-Sheathed Wall. In that article, I describe a type of picture frame that is separated from the sheathing by a layer of rigid foam: "Install a picture frame of 1x4 lumber, installed on the flat, on the exterior surface of the rigid foam. The 1x4 picture frame is screwed through the rigid foam to the sheathing and framing."
type of foam zone 6A
Hi Martin,
What Dana said about using Polyisocyanurate sounds good but I am no expert on the mean Temp.
Our cooling cost is high but our heating cost is not bad, so the Polyisocyanurate would be good that way as well.
The Polyisocyanurate will be ok uncovered while siding, another plus.
Does Neopor® GPS need to be covered quickly (Tyvek) to prevent damage from the sun?
If I can find 1.5 inch Neopor and assuming the cost is equal to1.5 inch Polyisocyanurate, which would you recommend?
Thank You!
Neopor protection
Zone,
Q. "Does Neopor GPS need to be covered quickly (Tyvek) to prevent damage from the sun?"
A. The Neopor instructions read as follows: "Care should be taken to keep exposed foam protected from reflected sunlight or prolonged solar exposure. If deformation of the insulation product occurs due to excessive heat transferred from reflected and concentrated sunlight, remove the reflective surface or shield the insulation product. A secondary method to protect the foam from direct sunlight and heat is to install sunscreen or tarp on the outside of the scaffolding, much the same that is used on building construction that protects the public when it is necessary for them to pass by construction site underneath the scaffolding."
I'll admit that this information is a little vague. For more detailed information, you might want to contact BASF (973-245-6000 or 800-526-1072).
Neopor
Martin,
I called BASF tech support, They don't actually make the Neopor and can't answer any questions or ever tell me where to buy it. If I can't find any Neopor should I just use 1.5 inch Polyisocyanurate? The charts still confuse me but I believe our mean temp would be ok even on the -15 days (2 weeks or so) and definantly ok on the 15-20 degree days. It seems Dana similarly interprets the charts. And I can buy the Polyisocyanurate at my local Menards.
Thank you
Response to Zone 6
Zone,
Yes, you can use 1 1/2 inch of polyiso (as Dana explained to you in Comment #183).
Vapor Retarded Required
There's all this talk about eliminating the interior vapor retarder, but what to do when you live in an area where one is required by code? See: https://docs.legis.wisconsin.gov/code/admin_code/sps/safety_and_buildings_and_environment/320_325/322/IV/38.
If I'm required to use a vapor retarder on the warm side of the wall, how do I utilize foam sheathing without creating a second vapor retarder? Or is that no concern as long as the foam has a minimum level of vapor permeability to allow drying?
Dew Point Chart
Martin states, "If you are building a house in one of the warmer climate zones — zone 1, 2, 3, or 4 (except for 4 Marine) — you don't have to worry about the thickness of your foam. Any foam thickness will work, because your sheathing will never get cold enough for “condensation” (moisture accumulation) to be a problem."
Officially, I'm Zone 4, but right on the border of Zone 5 (27%+ foam), so I go with Zone 4.5. I'm looking at using Zip-R6 1" polyiso / 7/16" OSB. Based on the BSC study, I'm de-rating it to R5 in the cold. Maybe a few days here and there, the temps drop to around zero F. I suppose it could de-rate to R4.3 at 15 degrees occasionally and below R4 at zero rarely.
Based on the Zone 5, 27%+ foam, most of the house then will be 2x4 R-13 wall fill with some 2x6. I suppose the 2x6 should also be kept at R-13 to keep the dew point in check. Do you think the Zip-R6 is sufficient for Zone 4.5? Should I stick with R-13 batts or could I up them to R-15? Thanks.
It's the seasonal averages that matter (not the peak)
Having the occasional cold snap where the sheathing takes on some moisture via vapor diffusion isn't a problem, as long as it dries before temperatures rise high enough to support rapid mold & fungus growth. It's really about the average.
Being in the cold edge of zone 4, near the warm edge of zone 5 isn't really a concern here. If the IRC prescriptives are good enough for the cold edge of zone 5 they're overkill for the cold edge of zone 4. ANY amount of insulating sheathing (or none at all) is sufficient for keeping the average temperature at the foam/fiber boundary of a ZIP-R wall sufficiently warm to limit the peak and average moisture levels in a 2x6 cavity (at any fiber-R) to tolerable level. Even R23 rock wool is fine.
If you're the type who would always worry about it, use cellulose instead of fiberglass or rock wool. Cellulose can take on a fairly large amount of moisture without damage or loss of function, and redistributes any moisture within the fiber.
In Marine zone 4C (which has a much longer heating season and a shorter drying season than zones 4A & 4B) the IRC prescribes R3.75 for 2x6 framing. Even with derating the ZIP-R to a presumptive R5 it would have margin. But in zones 4A & 4B it's not really necessary, since the outdoor temps rise well above the indoor dew point temperatures much earlier in the spring season than in 4C.
@ Bryanw511, I believe
@ Bryanw511, I believe Wisconsin requires a class 1 vapor retarder. Variable-permeance membranes like Pro Clima Intello, Siga Majrex and Certainteed Membrain meet that requirement, but if moisture accumulates within the wall their permeance increases to allow drying to the interior. (Technically with Majrex the permeance is different depending on which direction it's facing, but the effect is similar.)
I am building a small house in region 6. Walls are 2x6 on 16" layout. I have OSB sheathing, house-wrap, 2" of polyiso, vertical batten boards and hardi-plank lap siding. Roof is 2x10 cathedral ceiling (collar ties) on 24" layout. I have OSB sheathing, ice and water shield, 5" of polyiso, another layer of sheathing, tar paper and then standing seam metal. Going unvented and drywall will be carefully sealed. Disappointing to learn that the R-value of polyiso drops at low temps! We don't need cooling in the summer, so cold weather is the entire point. My question is about the R-value of fiberglass batts I'm putting in the walls and ceiling. Code calls for R-11.25 rigid foam on the exterior then R-13 in the wall cavities, which would presumably to keep sheathing above dewpoint. Planning to stick with code but tempted to add more fiberglass. Would it be OK to go with R19 in the walls? Any reason to prefer unfaced vs paper-faced fiberglass? Thanks in advance! This is by far the most useful website I've found for efficient building practices!
Alan,
The code recommendations for 2×6 walls assume (in Climate Zone 6) that any exterior rigid foam has a minimum R-value of R-11.25 — your polyiso will perform at R-9 or R-10 in cold weather, so it’s not quite thick enough — and fluffy insulation between the studs rated at R-19 or R-20. Installing thin fiberglass batts is theoretically possible, and that would lower the risk of the assembly, but then you have a new problem — keeping the thin fiberglass batts in contact with the wall sheathing.
If I were you, I would fill the 2×6 studs of with R-19 or R-20 insulation, and add an interior “smart” vapor retarder to reduce the risk somewhat. More information is available in the following two articles:
"Rethinking the Rules on Minimum Foam Thickness"
“The Exterior Rigid Foam is Too Thin!”
“[Deleted]”
> The code recommendations for 2x6 walls assume (in Climate Zone 6) that any exterior rigid foam has a minimum R-value of R-11.25
For the general case of a Z6, 2x6 wall with some exterior rigid foam, code requires one of a variety of options, only one of which is ≥ R-11.25 of foam.
Agreed, a class II vapor retarder is one of the code compliant options.
Thanks for the responses Jon and Martin. I feel defrauded with regard to the polyiso insulation. Who cares what the R-value is at 75 degrees? Wish I'd read more here before installing it!
My new plan for the walls is R-20 kraft-faced fiberglass to provide the class II vapor retarder and keep the fluff in contact with the sheeting. In addition I'll be carefully sealing the drywall. Should this work to avoid moisture issues? I've got a similar situation over 1/2 of the roof with 5" of polyiso and 2x10 rafters. My plan there is R-30 kraft-faced fiberglass in addition to the R-20/30 rigid foam. The other half of the roof is flat with a TPO membrane on top of 2" to 5" tapered polyiso foam and 2x10 TJI rafters. Most of this roof is over the garage but there is 12' by 12' section over the kitchen. Would the same kraft-faced R-30 fiberglass and good sealing be adequate? I've found that R-19 fiberglass will sit on the flanges of the rafters to fill those cavities well as it sits on the flanges of the rafters but I'd prefer the greater R-value.
On a side note I work with temperature data at my job so just for kicks I calculated HDD from 1950 to present. If the current trend continues we'll be in zone 5 by 2020!
Alan,
Q. "My new plan for the walls is R-20 kraft-faced fiberglass to provide the class II vapor retarder and keep the fluff in contact with the sheathing. In addition I'll be carefully sealing the drywall. Should this work to avoid moisture issues?"
A. The answer can be found in the two articles I linked to earlier:
"Rethinking the Rules on Minimum Foam Thickness"
"The Exterior Rigid Foam is Too Thin!"
The lower the indoor relative humidity in winter, the lower the risk of moisture problems in your wall sheathing.
Q. "I've got a similar situation over 1/2 of the roof with 5" of polyiso and 2x10 rafters."
A. For more information on roofs, see "Combining Exterior Rigid Foam With Fluffy Insulation." In Zone 6, the code calls for rigid foam in this type of assembly to have a minimum R-value of R-25. I think that your 5 inches of polyiso will work, as long as you limit the R-value of the fluffy insulation to a maximum of R-24. Don't use R-30 fiberglass. You'll have to figure out a way to keep the R-24 fiberglass in contact with the underside of the roof sheathing.
With the air space between the board & batten the foil facer adds another ~R1 of performance to the stackup. It's close enough to not really sweat this one too much, especially when using a "smart" vapor retarder on the interior like asphalted kraft facers.
Just be sure to detail the interior to be as AIR tight as possible. Convecting air leaks from the interior into& through the cavity insulation can move a lot more moisture than vapor diffusion through kraft facers.
Strange...the NYS seems to have only R 5 for continuous insulation and R 20 for the fluffy stuff. From what I read here I should be advising clients that code is inadequate?
Tim,
I'm not sure what "the NYS" means, but I'm guessing that you're referring to a local code. Whether or not R20+R5 is risky depends on your climate zone. If you live in zones 5, 6, 7, or 8, the combination is risky -- even though it is code-compliant.
For a full discussion of the "20+5" problem, see this article: "The 2012 Code Encourages Risky Wall Strategies."
NYS...code speak for New York State...VERY UPSTATE basically Canada. Meaning its even riskier. thanks Martin!
New York codes are based on the IRC 2015. In chapter 7 of the New York code they adopted the exterior insulation requirements when using Class III vapor retarders from the IRC 2015 without amendment. See Table R702.7.1:
https://codes.iccsafe.org/content/IRC2015NY-2/chapter-7-wall-covering?site_type=public
thanks Dana!
Great article. I see some possible contradiction about closed cell foam in the stud cavity though. You state "...nor should you install any closed-cell spray foam between the studs. " But further in the article essentially you are saying a flash & batt, using some closed cell is ok. I'm presuming the latter (less thickness) does not impede drying to the inside? Whereas the full depth foam (e. 2x6) would not?
But here's my situation: I'm building a home in zone 6 with 2x6 with 2" rigid foam directly applied to outside stud, then tyvek, opdyke rain screen, then LP Smartside vertical siding. I'm not using sheathing between 2x6 and rigid foam. For the interior, I was planning on using closed cell in the stud cavity (nominally about 5"), with drywall, then 3/4" shiplap. Does this system allow for drying to the interior? Will my system work in managing the dew point and perform properly? Do you see any risk in this assembly?
>" For the interior, I was planning on using closed cell in the stud cavity (nominally about 5"), with drywall, then 3/4" shiplap. Does this system allow for drying to the interior? "
At 5" most closed cell foam will be less than 0.3 perms, possibly only 0.2 perms, which ain't much drying capacity toward the interior.
It's also going to perform about as well (or may even slightly underperform) a 1" flash (necessary for dew point control in zone 6 with only 2" of rigid foam on the exterior) and filling the remainder with cellulose, due to the 5" thermal bridge through the insulation compared to 5.5" with a full cavity fill. Do the math:
https://www.finehomebuilding.com/2017/07/10/closed-cell-foam-studs-waste
With 1" closed cell foam on the cavity side of your 2" rigid foam there won't be significant wintertime moisture accumulation at the foam/fiber boundary, and the drying path for the framing will be pretty good. Even the outermost stud edge can dry toward the interior, since it has at most 1" of wood or foam to pass though, which is on the order of 1 perm (or a bit more, depending on the species of wood and brand of closed cell foam.) With ship-lap (and no wallboard) on the interior it will need some other air barrier- a "smart" vapor retarder such as Intello Plus detailed as an air barrier would be more rugged over time than 2-mil nylon (Certainteed MemBrain) that is also variable permeance. But no membrane type air barrier/vapor retarder is as rugged as half-inch wallboard with a coat of latex primer as the interior side air and vapor barrier.
Spending the flash-foam money on slightly thicker (or higher performance) exterior foam sufficient for dew point control would probably be cheaper and greener. The IRC prescribes a minimum of R11.25 for dew point control on the exterior of a 2x6/R20 wall. While typical brand-X foil polyiso is labeled R12 at that thickness it would have to be derated to R9-R10 at temperatures that matter in your climate, so 2.5" would be the minimum for R20 cellulose. But 2" of Dow Thermax polyiso needs no derating for temperature.
Using 2.5" of Type-II EPS (1.5lbs per cubic foot nominal density) would be labeled R10.5, but would perform at R11.25+ at outdoor temperatures that mattered for dew point control, and would be just fine to up-rate to R11.25 @ 2.5".
XPS would be labeled R10 @ 2", but is only warranteed to R9. This is because it's performance degrades over time as it loses it's climate-damaging HFC blowing agents (a mix of predominantly HFC134a, with a 100 global warming potenial about 1400x CO2.). Eventually it will degrade to the same performance of EPS of similar density.
Both EPS and polyiso are blown with comparatively benign hydrocarbon blowing agents, predominantly a variant of pentane, with a 100 year GWP of ~ 7x CO2. In the EPS case almost all of the blowing agent leaves the foam while it's still at the factory, and is recovered, not released, and it's performance doesn't change over time. The facers on polyiso retain some of it for a decade or more, but very little (if any) 0f it's R/inch performance is dependent upon the blowing agent- indeed the blowing agent retention is responsible for the necessary derating at colder temps.
Clearly not all foams the same environmental impact. On strictly a global warming potential basis polyiso is roughly between EPS and rock wool on this chart:
https://materialspalette.org/wp-content/uploads/2018/08/CSMP-Insulation_090919-01.png
But there are other impacts that mere carbon in the polymer lifecycle, putting polyiso even a bit further to the green.
Compared to cellulose (which is 85% recycled/reclaimed material, and becomes sequestered carbon for the lifecycle of the building) they're all bad. Cellulose has a net-negative carbon footprint, and the other impacts from the fire retardents etc are extremely low compared to any polymer insulation.
Even with sufficient exterior foam for dew point control on R20 fiber insulation the assembly would still need a robust interior side air barrier and vapor retarder.
Question on Aesthetics: Let's say you are doing a retrofit and add 4" of EPS. Does anyone have any tips on how to make your existing windows not look sunken in, and also how to flash these new window openings?
Matt,
If you look at older buildings, you'll see that many are designed with "innie" windows -- what you call "windows that look sunken in." This approach protects the windows from rain exposure. Moreover, in a hot climate, this approach provides some shading, reducing solar gain.
Whether or not you like this aesthetic is an entirely personal matter.
The flashing question is more pertinent to this site than the aesthetic question. It is absolutely essential to get the flashing details right, or you can rot your walls. Proper flashing details are certainly easier if you install new windows than if you keep the existing windows.
Ideally, you want to flash the rough opening. The sill flashing needs to be under the window, and needs to extend to the water-resistive barrier (WRB). If you can't flash the rough opening, you end up with an imperfect flashing job -- and the suitability of your site-built solutions become a series of judgment calls, in which you weigh factors like exposure to the elements, annual rainfall, and the robustness of your finish materials.
There is no simple way to describe what you need to do, but think like a roofer, and strive to keep rain out of your walls. Durable materials include solid PVC trim like Azek, or durable metal flashing like copper. Think about seams. Remember, caulk won't save a bad detail.
Hi Martin,
We just bought a 1 1/2 story 1930 house with a gable roof (2x4 rafters) and a large dormer on each corner of the house for the stairs and two upstairs bedrooms. There is what looks to be an unvented roof assembly for the dormers, and unvented, conditioned attic kneewalls on each side that are insulated against the sloped ceiling. The smaller kneewall is insualted with R11 fiberglass with sheetrock, while the larger one is R15 mineral wool with a layer of 2" XPS over it to help with thermal bridging. I assume the dormer ceilings are just R11 bats, but perhaps I would be pleasantly surprised if I removed the sheetrock.
The roof needs to be replaced, so I'm quoting for a hidden fasteners standing steam metal roof for the dormers (1-2/12 pitch) to help with the early failure the previous owner had experienced with asphalt shingle, and the rest of the roof with asphalt.
So long as we have the roof off, I wanted to add some exterior rigid insulation. I had hoped to add 3" of XPS, but if I am understanding this article correctly, that would mean I could only have ~R9 insulation under the sheathing, plus the 2" XPS would need to be ripped out of the larger attic kneewall area. Is that right?
Can our roofer go up to 3.5" easily on the roof to bring us to R10.675 on the interior (and only barely violate your 61% rule)? That would still meaning ripping out the 2" XPS though, right?
Is there some other option that you would recommend? Sell the house? Thank you!
C.E.,
I can't answer your question unless you tell me your climate zone or geographic location. The colder the climate, the thicker the rigid foam has to be.
My advice: don't violate the minimum thickness rules for exterior rigid foam.
For more information on this issue, see these articles:
"How to Install Rigid Foam On Top of Roof Sheathing"
"Combining Exterior Rigid Foam With Fluffy Insulation"
Hi Martin,
Thanks for the reply. Sorry, I somehow edited out the zone amidst all this. We're zone 7.
I have read those, but I just wanted to make certain I was understanding this correctly, plus see if there was some other approach you would recommend in this case.
I also saw this article and hoped we could find a "harm reduction" approach perhaps: https://www.greenbuildingadvisor.com/article/the-exterior-rigid-foam-is-too-thin
C.E.,
In Zone 7, with the type of roof assembly you are describing, at least 61% of the total R-value of the roof assembly must come from the layer of exterior rigid foam.
Most green builders avoid the use of XPS, which is manufactured with a blowing agent that has a high global warming potential. (For more information on this issue, see "Choosing Rigid Foam.") But if you ignore the advice of GBA and install 3 inches of XPS, that layer will have an R-value of R-15 (at least when the foam is new), meaning that your total assembly R-value will be no higher than R-24.6. That means a maximum of R-9.6 for your fluffy insulation.
If you want more total R-value, you need to increase the thickness of the rigid foam layer beyond 3 inches. One option is nailbase, a product that is available in R-values higher than R-15.
Hi everyone - perhaps my question has already been answer and relatively basic.........
We are in NJ - Zone 5A
Existing House with existing R13 batt insulation (2x4 walls) on the interior and 1" rigid foam (foil face) on the exterior - not sure what type. The interior has been gutted and the interior insulation is being replaced - we are considering 3 options and wanted some advice:
Option A - interior spray foam
please confirm interior spray foam is not recommended in this situation as the sheathing would be between two layers of foam and will not be able to dry to the exterior or interior - very risky
Option B - Upgrade from R13 batt insulation to R15 batt insulation - would this have a possible negative effect and we would end up with even more R-value on the inside vs outside or is R2 negligible - some risk
Options C - New R13 batt insulation to match the existing - from the areas that have been opened up the sheathing appears to be in good shape
Thanks in advance.
John
I am slowly working on insulating and finishing my daylight basement in climate zone 6B (concrete was poured in 2016). My approach has been to adhere a 1.5" continuous layer of rigid faced EPS with an R-value of 7.5 to the poured concrete wall and fill between the seams with canned spray foam, then frame a 2x4 wall in front of it with rockwool comfortbatt r-15 cavity insulation. I have the EPS and framing installed and am working on the electrical. I have some areas where there will be no cables filled where I have installed the rockwool batts in the cavities. This winter I am finding that there is moisture accumulating on the face of the EPS behind the rockwool batts, at least where the concrete walls are above grade on the exterior. This is only occurring in the areas where I have the batts installed. Where I haven't yet installed the batts, the face of the EPS is dry. My thought at this point is that the EPS is not thick enough and is getting cooled through to the point of vapor condensing, but from all the conversations I see regarding this topic, and the ratio tables, it should be thick enough. I also am not currently heating the basement space as I am installing hydronic baseboard heat as part of the project. Do I need the increase the thickness of the EPS where the concrete is above grade on the exterior, or could this just be a result of my not yet heating the interior? I obviously don't want moisture accumulating in the wall cavity or between the EPS and stud wall once finished. Any advice would be much appreciated.
-Tim
Log in or become a member to post a comment.
Sign up Log in