Brick house insulation

All,
First of all, I wanted to wish everyone Happy and Prosperous New Year!
I would like to ask for an advice regarding a wall cavity composition. I am in Westchester County, 30 miles north of New York City, climate zone 4. I am about to acquire a brick house (tiny brick, maybe 2-3 inches thick). Single wythe, I believe. I think that brick is just decorative and is not load bearing at all. Only cinder blocks in the basement support the floor joists. Second floor ceiling joists are supported by wood framing.
I was trying to educate myself as much as possible on the subject. I have read https://www.greenbuildingadvisor.com/blogs/dept/musings/insulating-old-brick-buildings and other publications regarding the subject. I know that the best method is to insulate outside, but this does not seem to be an option as of now. As per inside, I understand that the best method is closed spray foam, but I would like to avoid that as well.
I think I will own a building with low risk factors, and may decide to go ahead without hiring a consultant. The building has no signs of exterior water damage, without any deteriorating bricks, and with flashings that do a good job of keeping rainwater off the building.
It will be total demolition inside only. After demo phase is completed, I would like to insulate as well as possible. I am not 100% sure, but as far as I was able to see walls are made of 2×6 studs. I think studs might be in direct contact with the brick, or there might be a very tiny space between (the house built around 1950). I know that according to recent research wood should not come into direct contact with brick, but it is a retrofit, and I will not be able to redo the framing, so whatever is there stays (if there is more space between studs and wall, I would slide insulation behind studs. I was planning to adhere 2 inch thick Polyisocyanurate (Thermax) R13 boards (due to all horror stories about respiratory problems, even when jobs were done professionally, I would prefer not to have spray foam in the walls, as far as I read Polyisocyanurate does not contain the same chemicals as spray foam, please correct me if I am wrong), cut them to snug fit, adhere them between 2×6 studs, tape them etc.. In case there are any cavities left, I would fill them with a canned spray foam (minimal quantities are ok). Then I was planning to use Roxul Comfortbatt R15 on the top of the board. Total R value (2 inch board, and 4 3.5 inch roxul) should be about 28, minus whatever I lose due to thermal bridging etc. I am fine with that. I plan to finish the wall cavity with a drywall.
Questions:
• Does my idea make sense? Would you plan the wall cavity differently? If so, how?
• Should I apply liquid-applied air barrier, on the inside, to the brick first? Like a brick sealant or so? I believe I read that GBA does not recommend this. Is this correct?
• Is Thermax Polyisocyanurate appropriate material for my application? If I look at “Calculating the Minimum Thickness of Rigid Foam Sheathing” it seems that its thickness is well enough for my climate zone, however in places where studs are, it may not be thick enough. Can this cause moisture problems? It seems that the wall would be water impermeable, perhaps except where the studs meet the bricks, or “almost meet”? I admit this is pretty confusing, and I understand why closed cell foam is the recommended solution here.
• Should Polyisocyanurate foil face be installed towards inside or outside of the wall? As far I was able to understand, it should be on the inside. Is this correct?
• What about the vapor barrier underneath the drywall? Would my Polyisocyanurate create a vapor barrier on the outside side of the wall? I read that it is not advisable to have two forms of vapor barrier (the rigid foam and the poly) with any kind of cavity or other material in between because condensation will build up between them. I was thinking about installing MemBrain Smart Vapor Retarder & Air Barrier Film underneath the drywall. Is this a good choice for my application? Would I create aforementioned problems? Perhaps I should skip it?
• What about the vapor barrier in the ceiling? Should the vapor barrier be installed on the ceiling too (ceiling will be insulated with R30 Roxul, and I may add cellulose on the top of it later, no boards here)? I guess in this case double vapor barrier problem would not exist so I could use MemBrain Smart Vapor Retarder & Air Barrier Film underneath the drywall without worries?
• Can I use the same wall cavity composition in the basement? 50% of basement walls are above the ground, so it is like a half basement, as the house is built on a slope. The basement walls are made of cinder blocks. I would be able to redo the farming here (on some walls it does not exist at all), and adhere boards to cinder blocks in continuous manner and thickens without any problems. Assuming correct board thickness, I see that vapor barrier is not recommended in basement applications, correct?
• Are there any special requirements when it comes to bathroom walls? There is about 5 feet wide outside bathroom wall. Should I insulate this part differently? If so, how?
• What material should be installed inside of internal bathroom walls? Some sort of faced insulation?
• If all else fails, and I have to go with spray foam, would 2 inches thick, complemented with 3.5 inches of roxul be sufficient?
Any question and suggestions are very welcome. Any help is greatly appreciated. If I got it all wrong, please tell me what would be a recommended wall cavity composition in my situation. I am trying to achieve the highest R value, as well as I prefer not to use a spray foam and cannot insulate from the outside. Big thank You!
I was following the below referenced document: Measure Guideline: Installing Rigid Foam Insulation on the Interior of Existing Brick Walls H. Natarajan, S. Klocke, and S. Puttagunta
GBA Detail Library
A collection of one thousand construction details organized by climate and house part
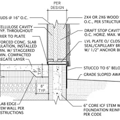
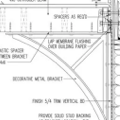
Replies
Sebastian,
You have posted a long thread with lots of questions. It will be necessary to answer your questions in chunks, a few at a time.
Your first misconception is that you have a brick house. Your second misconception is that my article ("Insulating Old Brick Buildings") has anything to do with your house. It does not.
You have a wood framed building. The brick veneer on your house is equivalent to siding. It is not structural. The guidelines in my article do not apply to houses like yours.
Sebastian,
Before we can advise you on the best way to insulate your walls, we need to know whether the existing 2x6 studs are touching the brick veneer, or whether there is a gap between the studs and the bricks. If there is a gap, we need to know the width of the gap.
(I'm assuming that your house has no sheathing.)
Thank you for your response.
I guess it is good news. Bad news is that the house is not mine yet, and it will take 6-8 weeks until it becomes mine. I just wanted to get ready to hit the ground running with renovations as soon as the transaction is completed.
There is a very small part of a wall exposed next to a pipe chase, and in there studs touch the brick. However, I cannot tell if this is the case for the entire house. If this detail significantly changes responses to my questions, I will wait and come back here when the house is mine and when I open the walls. If it is not a big deal we could analyze both variants. However, I do not want to stretch anyone’s generosity here, so probably the best option is to refresh the topic when details are known. Once again, thank you!
Sebastian,
If the studs are touching the brick, and the walls have no sheathing, I would proceed with one of the methods recommended in this article: Insulating Walls in an Old House With No Sheathing.
I looked through the article and comments. Seems that my approach with 2 inches polyiso (airtight) and the rest filled with Roxul should work. My idea with membrain product should be fine too, so if needed the wall may dry to the inside.
If studs do not touch the brick, would I follow the same guidelines with the exception that I would not have to install spacers crating the air gap? As putting polyiso flush with the back of studs would take care of it?
Thank You!
Sebastian,
You don't want the rigid foam to touch the bricks. So whether the studs touch the bricks or not, you will still need 1" x 1" sticks to provide an air space between the bricks and the rigid foam.
Using 1x1" sticks of cut up foam board for spacers is even better!
For foil facer to have any thermal benefit it must face an air space.
Building out 2x6 studs and cutting up foam to fit between them is a mistake. The performance of the high R/inch foam is severely undercut by the very low R/inch framing. A the same wall thickness it's significantly higher performance (and easier to build) to use 2" of continuous foam and a 2x4 wall.
In zone 4A you don't need a vapor barrier in any wall or ceiling assembly. But if you DO install a vapor barrier (such as foil-faced foam), take care to design the assembly so that the interior side of the assembly can dry toward the interior, and the exterior side to the exterior. (No interior side vapor barriers if there is exterior side foam.)
The foundation wall needs to be assessed for moisture before deciding how it needs to be insulated. Worst case it may need a dimple-mat between the CMU foundation and the foam layer, ideally draining into a perimeter drain cut into the slab, but that's a worst case- most don't need to go that far. Code minimum for foundations in zone 4A is R10 continuous insulation, which can be achieved with 1.5" of Thermax, or 2" of reclaimed roofing polyiso, at a fraction of the cost of Thermax. There are multiple vendors trading in used & factory seconds rigid foam. eg:
https://newyork.craigslist.org/search/sss?query=rigid+insulation
https://hudsonvalley.craigslist.org/search/sss?query=rigid+insulation
https://catskills.craigslist.org/search/sss?query=rigid+insulation
Keep the cut bottom edges of polyiso off the slab, since polyiso can wick moisture. An inch of EPS on the slab extending from the foundation wall under the wall foam and bottom plate of the finish studwall as a capillary and thermal break works pretty well. Give the EPS a 1/4" gap from the wall for drainage if there is no dimple mat.
Thank you all.
Yes Dana, you are right about building a wall of studs vs foam and studs. The problem is that the wall already exists. At this point I cannot insulate outside, so I am looking for whatever best I can do inside. If I had a comfort of building it from scratch, I would definitely follow all recommendations to insulate outside. In my situation, it seems like Cut-and-Cobble Insulation is my best option, despite its pretty significant disadvantages.
Thank you for all suggestions regarding the basement, I will follow them, as well as I will try to use second hand materials. Vapor barrier situation has become clear as well. I will drop it entirely, or will use intelligent membrain products.
Going back to some of my original questions:
• As far as liquid-applied air barrier, like a brick sealant on the inside of the brick, I should not do it, correct?
• Are there any special requirements when it comes to bathroom walls? There is about 5 feet wide outside bathroom wall. Should I insulate this part differently? If so, how?
• What material should be installed inside of internal bathroom walls? Some sort of faced insulation?
Thank You,
Sebastian
It would be unusual for a house of this age at least in most parts of the US to be built with 2x6 walls, and brick veneer is usually around 4 - 41/2" thick. I think you may have been misled by a small area of plumbing wall built extra thick to accommodate a pipe chase. In any case you should wait until you take possession and can inspect the wall construction properly, and you should definitely seek professional input from a local consultant or contractor before potentially making expensive mistakes with your energy upgrade plans. There is a wealth of first rate information and advice to be found on GBA but remember it covers a vast geographical range of climate types and building practices and it should always be applied through the lens of local knowledge and experience.
James Morgan has it right- until you take possession and can do some exploratory demolition to assess the wall stack-up most of this is going to be mere speculation. Almost all brick veneer houses built in the 1950s had a 1" or greater cavity between the brick and the next layer, and the structural wall was a wood (shiplap plank or plywood), sometimes fiberboard sheathed milled lumber (1.5" x 3.5") 2x4 wall, sometimes with R11 rock wool or fiberglass but often empty. A 2x6 wall of that era would be rare- sometimes the sound of pounding hooves really is a zebra, but that's not what to expect.
The brick doesn't need to be an air barrier if it's facing a vent cavity, and adding sealants might even increase the risk of freeze/thaw spalling damage. The brick needs to be able to dry freely into the cavity to keep it's moisture content lower, reducing freeze damage risk. (I have seen freeze thaw spalling on a circa 1960-ish house in Westchester county, but that brick stayed wet primarily from excessive splash-back wetting at the eaves.)
Rather than cut'n'cobbled foam board, adding polyiso edge strips to the framing held in place with 1x furring sufficient to thickening up the cavity depth to 5.5" and using R23 rock wool or R21 fiberglass does more for performance than cut'n'cobbled foam between the studs. Most circa 1950 homes were framed with milled 3.5" x 1.5" 2x4s, so 1" thick polyiso edge strips (R6-ish) and 1x furring brings that out to 5.25".
An R23 compressed to 5.25" will still perform at R22, a compressed R21 would be still be at least R20. Alternatively, blown cellulose would deliver R19.5-R20, and would automatically have a near-perfect fit.
If it's full dimension rough 2x4s backing off to 3/4" polyiso edge strips.
This is pretty much the Bonfigilioni methodology:
http://www.finehomebuilding.com/membership/pdf/9750/021250059.pdf
Polyiso between the studs has the same performance problems as closed cell foam, and it's far more time consuming. Even with 3.5" of Thermax (R24 - R25-ish) packed in there only adds R2 to the "whole-wall-R". Adding even a half-inch of polyiso thermal break on the framing edges and (0.5" + 0.75" furring=)1.25" of fiber depth adds more performance than that. See:
http://www.finehomebuilding.com/membership/pdf/184243/021269086NRGnerd.pdf
There is probably a great chance that you are right regarding the walls thickness. They might be 2x4. Regardless what is there, I will bring it to 2x6. Either by simply adding 2x2 furring strips or by using Bonfigilioni methodology (thank you for that). What I am trying to achieve now is the best possible insulation in the 2x6 wall cavity. I planned to install 2 inch of polyiso board R13 (cut and cobble method) and 3.5 inches of Roxul R15, so total wall R would be 28, minus whatever (might be a lot) I lose due to thermal bridging, imperfectness of cut and cobble method etc.
I read the following document “The-Economic-Thickness-of-Thermal-Insulation-Dec08.pdf”. The document basically indicates, that the first inch of insulation represents 80% of the heat flow reduction in the system, the next inch 9%, the next inch 3%, the next inch 2%, the next two inches 1% each and the next four inches only 1%! So in the first 2″ you are getting 89% of the total performance realized in your insulation assembly. If the document is correct, then the key for success in insulation is to do a thorough job, sealing all the openings in your building envelope. Again the best done from the outside, no questions about it.
In my situation, I thought that first two inches done with polyiso, even keeping in mind its disadvantages and poor method, is still the best I can do in order to build as good as possible air barrier.
There is a VERY significant difference in thermal performance between adding wood furring v.s. Bonfiglioni style insulated strips. An inch of polyiso edge strip cuts the thermal losses of the framing by half compared to adding a 2x2.
Also note, a 2x2 is only 1.5" in depth, and would only bring a milled 2x4 out to 5". not the nominal 5.5" of a milled 2x6. The IRC code minimum performance (= the lousiest wall that is legal to build) for zone 4A is R20 when the studs are all wood. Compressing an R21 to 5" won't even clear that bar, but compressing an R23 rock wool batt to 5" would. But at 5" the heat going through the framing fraction is ~9% higher than through a 5.5" stud. With an R6 polyiso 1.25" deep Buonfiglioni strip the heat through the framing fraction is cut in half, and a compressed R21 would still hit R20, making the assembly performance measurably higher than code minimum. Despite the lower center-cavity R, an R19 compressed to 5.25" (about R16-R17) would still hit code performance on a U-factor basis (with margin to spare) with R6 Bonfiglioni edge strips but a higher density, more air-retardent fiber is going to be more forgiving of any air leaks that develop over time.
If the existing structural sheathing of the studwall is plywood it's dead-easy to make the sheathing an air barrier. If it isn't, there are easier and more reliable methods than cut'n' cobbled foam board for air sealing. Before diving into the details, let's find out what you have first.
Typical hemlock, fir or high density pine species used for framing in your region run about R1.2/inch, so 5" thick framing would be ~R6. Typical framing fractions for 16" on center studwalls are 25% of the total wall area, after measuring up all the top & bottom plates, window framing, jack studs etc.. A compressed R21 will perform at about R19 @ 5.0" for the other 75% of the wall area. So at any arbitrary temperature difference dT the amount of heat moving through the framing fraction per square foot over the average area of wall is:
0.25 x dT/R6= 0.0417 x dT per square foot of average wall area.
The amount moving through the insulation fraction is:
0.75 x dT/ R19= 0.0395 x dT per square foot of average wall area.
Note slightly more than HALF the heat is being transferred through the framing fraction(!). That means even doubling the R value of the cavity insulation to R38 (say, with exotic & expensive stuff like aerogel) would still deliver less of a performance enhancement than doubling the R value of the framing fraction with edge strips.
And that is why it's better to spend the foam budget (and cut'n'cobble labor budget) on edge strips, rather than between the studs. It's only ~1/3 as much foam, far less cutting & cobbling, with maximal performance benefit. Cutting 1" foil faced polyiso is very quick and easy with a 4" steel wallboard tape knife sharpened on the edges, as demonstrated in this quick vidi;
http://www.finehomebuilding.com/2009/01/29/theres-a-better-way-cutting-rigid-insulation
Understood, so it seems that Bonfigilioni method is a must, otherwise loses are huge.
What about the rest of the wall if there is no sheeting? Do you do bats and let it dry to outside?
“If the existing structural sheathing of the stud wall is plywood it's dead-easy to make the sheathing an air barrier.” -- Do you mind listing some of the ways of crating the air barrier in this situation, without going into any details?
“If it isn't, there are easier and more reliable methods than cut'n' cobbled foam board for air sealing. Before diving into the details, let's find out what you have first.” Do you mind listing some of them, without going into any details?
It might be another misconception, but I am ‘locked’ into thinking that the only effective, externally facing air barrier is some type of rigid foam, so without the option of external installation I am back to cut'n' cobble. I believe that, even when I use Bonfigilioni to cut my loses, I still need foam. At the same time, if i can avoid this labor intensive process, and not lose much R value, I would be fully into it.
Assuming Bonfigilioni method to cut my loses, and 5.5 inch of insulation I can achieve R28 with Roxul and polyiso, and supposedly R23 with Roxul only. Question if R5 difference is worth the effort, and if there are any alternatives which can also achieve close to R28, like polyiso and Roxul combined.
"I am ‘locked’ into thinking that the only effective, externally facing air barrier is some type of rigid foam"
Unlock that thinking. Foam often shrinks over time opening up gaps over time. Even when foam is a continuous layer without seams with a dissimilar material such as wood it takes quite a bit of detailing to make it air tight even initially, let alone air tight after 50 years.
Using a sheet woody material such as plywood, OSB, or fiberboard sealed together with polyurethane caulk has a much better shot over time. The details of how to do that matter too.
Enough speculation. Nobody has enough time to go over every possibility in detail, whereas going of the details of how to deal with exactly what you have (still an unknown) is usually pretty straightforward.
Bumping the center cavity R from R20 to R28 has only a negligible effect on the whole-assembly R. Bridging expensive & difficult to install high R/inch foam with R1.2/inch wood is really a waste of time and money.
Understood, thank you, I will come back in a few weeks when I have more, and accurate information.
Finally got the house. And here is a surprise… so the wall is brick veneer, then air gap, then another layer of brick veneer, air gap, and plaster walls mounted without framing (not sure how, will demolish some tomorrow). Apparently there is currently no wood framing. Due to many reasons I would like to build framing. What would be the best approach here when it comes to insulation? As a reminder I do not want use foam, and would prefer roxul. Should the framing touch second layer of the brick? I have to say I got really surprised by this type of construction, but supposedly it was popular in 1950s. I appreciate your help.
Sebastian,
This isn't brick veneer. The wall you are describing is a structural brick wall -- "there is no wood framing."
Now that you know that fact, you'll have to abandon the plans that were based on the misconception that this was a brick veneer house.
Instead, you should follow the advice in this article: Insulating Old Brick Buildings.
This type of wall is tricky to insulate. The only safe way to proceed is to insulate with closed-cell spray foam -- and even that approach is sometimes contraindicated. Whether you can insulate this wall depends on the quality of the brick, the severity of the climate, and the amount of rain that reaches the brick.
As mentioned earlier I do own now a house build of double brick construction with plaster on the inside. There is air space between brick layers, which I assume, it is part of a design to air out and dry out the outer bricks. As far as I understand I have two options: insulate an inside, or outside, wall.
Outside option – ideally, Martin recommends 4 inches of polyiso and synthetic stucco.
• Does it have to be stucco, can I do siding over the rigid foam?
• Do I still care about rain management? I assume I have brick covered so I should not have to worry about it (I am in NYC, Westchester County)?
Inside option – I would not do a spray foam (afraid of potential health issues) so I can do a few layers of polyiso, the more the better, and then a framing for my wall. I understand this is not recommended by Martin, but I assume while not ideal, it is second best method to insulate from inside.
Are my assumptions correct? Do you see any red flags?
While I am here I will also throw a window question. I am considering windows of 0.19 U factor. Is this sufficient for my climate zone?
Thank You!
Sebastian,
Q. "Does it have to be stucco, can I do siding over the rigid foam?"
A. You can install any type of siding you want. For inspiration, see this article: Deep Dish Retrofits. See also the Building Science Corp. detail below. And here is a link to a GBA thread you might want to read: Rigid foam over brick exterior in Maryland.
Q. "Do I still care about rain management? I assume I have brick covered so I should not have to worry about it (I am in NYC, Westchester County)?"
A. You no longer have to worry about water on the bricks, of course, but any wall needs to have proper flashing, and siding installers always have to have a rain management plan. But you probably know that.
.
Is the light blue color representing a house wrap?
And how is first layer of foam attached to 2x4? Angled nails?
Sebastian,
The answers can be found in the article I linked to, Deep Dish Retrofits.
The WRB is a liquid-applied WRB: "Coat the exterior of the masonry with a fluid applied water control layer and air control layer."
The furring strips are described as "mechanically attached" -- in other words, fastened with TapCons.
Yes correct, sorry to be a pain, only thing which I did not fully understand after reading the article, apologies if I missed it, was how did they attached first layer of rigid foam to furring strips? Thank you
Sebastian,
The first layer of rigid foam can be attached with just enough adhesive to hold the rigid foam in place until the final layer of furring strips is installed. The last layer of furring strips secures all the layers.
Hello,
I just wanted to reassure myself, so even though there are two layers of brick, still internal layer should not be in contact in any fiberglass material like roxul etc., correct? And just to understand, there is a still risk that this layer of brick will get wet, not necessarily from rain, and cause potential mold problems, correct?
If I decide to insulate with 4 inches or so of foam on the outside, and half of the back of my house is basement, how should I approach insulating basement walls which are not covered with external foam (picture attached)? I planned to insulate it on the inside with polyiso, but if I do a rigid foam outside and polysio inside it is not a good composition, correct?
Reason why I am asking this is that doing everything on the outside will be very expensive, and I may not want to do it today, a breakeven point might be many years (I need to see my heating costs, but I assume they should be high with virtually no insulation in walls). On the inside I do not want to lose real estate upstairs, but I am ok doing so in half basement, but it seems I should not do anything until I decide on which side the rigid foam will go, as it can be installed on one side at the time.
Sebastian,
If you end up installing rigid foam on the exterior side of your walls, it makes sense to extend the rigid foam layer to cover the above-grade portion of your basement walls, too. To me, this is an aesthetic conclusion as much as a building science conclusion.
If this were my house, I would certainly extend the rigid foam to cover the above-grade portion of the foundation walls. But it's your house. If your budget is tight, there is no technical reason why you can't restrict the exterior wall insulation to just the upper floor.
Correct, but this is either or situation, right? If I extend the external foam to the above-grade portion of the foundation walls, then I do not do polysio inside, correct? If so, what do I do with the covered side of my foundation walls? Do I insulate only this part from the inside?
Sebastian,
Q. "If I extend the external foam to the above-grade portion of the foundation walls, then I do not do polysio inside, correct? If so, what do I do with the covered side of my foundation walls? Do I insulate only this part from the inside?"
A. It's really your house, and it's your decision. It you are having a tough time making decisions, you may want to hire an architect or a general contractor to help guide you in this process.
How much insulation do you want on your basement walls? Do you care if you meet code? Do you want to exceed minimum code requirements? Most of these decisions are up to you, although you need to comply with local regulations.
It sounds like you are in Climate Zone 5, where building codes generally require at least R-15 basement insulation for new homes. The requirement may not apply to a retrofit project.
If you install R-10 of continuous exterior insulation, for example, you might want to install R-5 on the interior side of your basement wall. Or you might not want to.
Or you might want to install R-15 of exterior insulation, with no insulation on the interior of your basement wall.
Westchester County NY is zone 4A, not 5A, and R10 continuous insulation on the basement walls would meet IRC 2015 code minimum.
The house in the picture appears to have a hipped roof with 20"+ overhangs as well as gutters. The amount of direct wetting of the brick is pretty minimal, but the white painted foundation will be getting some. The cricket and flashing details around the chimney are pretty important to get right though.
It's probably going to be easier/better to insulate the basement from the interior or exterior only, not a hybrid. Any errors in the flashing details over exterior foam could raise the moisture content of the foundation considerably, putting any wood that's in contact with it at risk, and increase the moisture content of the lower courses of brick, increasing the freeze/thaw spalling risk.
The type of brick wall with a gap between wythes is a "cavity wall". The gap provides a capillary break to keep exterior moisture from finding it's way to the interior finish surface. The gap also adds another ~R1 to the stackup. If insulating on the exterior-only air sealing the gap at the top prevents it from becoming a thermal bypass channel.
Insulating the exterior with 3" of reclaimed roofing (R17-ish) polyiso for the above grade portion and 3" of EPS (R12-ish) for the below grade down to 2' below grade would work just fine. Installing Z-flashing at the transition from polyiso to EPS would direct any bulk moisture that got behind the polyiso to the brick to the exterior. With R12 of EPS on the exterior you'd then be able to use an insulated 2x4 non-structural studwall on the interior to boost performance.
To meet IRC 2015 code for the above grade walls on a U-factor basis means taking it to less than U0.060, which is R16.7 "whole wall", that includes the R -value of the brick, the siding, the air gap/cavity, the interior & exterior air films, etc, so you'd have PLENTY of margin with just 3" of polyiso on the exterior.
To meet IRC 2015 code for the basement walls requires R10 continuous insulation all the way down to the floor, or R0.059 max (
R17, curiously slightly higher performance than what's required for the above grade walls.) An insulated 2x4/R13 studwall with half-inch wallboard has about another R11 "whole wall" performance where there are no door / window framing, land only single top plates (allowed, since it's not structural), and will meet code. Adding a half-inch of unfaced XPS between the stud edges and foundation as a capillary & thermal break and ground-moisture vapor retarder on the walls that extend below grade would be prudent, adding another R2+ to the stackup.
On the walk out basement wall the additional framing reduces the whole-wall R of the 2x5/R13 to about R9.5-R10, and it doesn't need the vapor retardency or capillary break of the XPS, but with R12 of exterior EPS it would also have plenty of margin beyond code minimums.
https://up.codes/viewer/utah/irc-2015/chapter/11/re-energy-efficiency#N1102.1.4
https://up.codes/viewer/utah/irc-2015/chapter/11/re-energy-efficiency#N1102.1.2
As usually, great comments, which make my head spinning. I would rather try to achieve about R26 if possible, in my walls.
The house in the picture appears to have a hipped roof with 20"+ overhangs as well as gutters.
Would installing 4 inch of foam plus siding, so essentially shrinking overhangs to down to 15 inches, be still ok?
Any errors in the flashing details over exterior foam could raise the moisture content of the foundation considerably.
Is stucco a bad idea here? Would siding be better, or does not matter as long as it is done properly?
If insulating on the exterior-only air sealing the gap at the top prevents it from becoming a thermal bypass channel.
Would this have to be done in the attic, at the top of the brick? Any recommendation for a material and technique?
Reclaimed roofing
Why did you call it roofing if this will go on the wall?
Insulating the exterior with 3" of reclaimed roofing (R17-ish) polyiso for the above grade portion and 3" of EPS (R12-ish) for the below grade down to 2' below grade would work just fine. Installing Z-flashing at the transition from polyiso to EPS would direct any bulk moisture that got behind the polyiso to the brick to the exterior. With R12 of EPS on the exterior you'd then be able to use an insulated 2x4 non-structural studwall on the interior to boost performance.
Do you mean here to insulate the above grade portion from the outside, and below grade from the outside as well? Why different thickness?
The below grade down to 2' below grade would work just fine”
What 2’ below grade mean here?
With R12 of EPS on the exterior you'd then be able to use an insulated 2x4 non-structural studwall on the interior to boost performance.
What material would use her so I do not trap moisture. Can Roxul get in touch with internal brick assuming there is a rigid foam on the outside of the wall (outside layer of the brick wall)?
If I do top with 4 inches of foam, plus siding or whatever, what do you recommended to use at the bottom to make the surface almost flat before applying siding, stucco or something else?
It was mentioned here that it is possible to hire consultants. Are phone consultations possible? If so, what is the process? Thank You!
Sebastian,
I'm guessing you're a homeowner, not a contractor.
Every time that we answer a question, you come back with 4 or 6 followup questions. That's good, because it demonstrates your thirst for knowledge. Perhaps a GBA reader with lots of time will start chipping away at your questions and provide answers.
But it's also possible that the next round of answers will generate more questions. Sometimes this exercise resembles cutting off the head of Hydra.
My guess is that you need to sit down with an experienced residential architect or general contractor.
You are right Martin, I am a homeowner. The problem is that I have not met more experienced people as you all responding here to my questions. Contractors I talk to, they are supposedly reputable (number of review at angie's list etc. references), have often no clue when I talk about things discussed here and explained in your articles. I should not generalize, but it is the case many times. Reason why I am trying to understand this stuff is to get a contractor and tell him how I want to get the job done. And I understand that I am probably annoying coming back with tons of questions over and over again. That is why at the end of my last post I asked if there is an option to have a phone consultation with you guys, and pay for it. Is this possible? I get that I have somewhat exhausted free help. I know that a site visit is better, but this probably out of budget.
OK, GBA readers, here is the challenge: Are there any GBA-reading builders or GBA-reading architects in Westchester County, New York -- someone who Sebastian can call?
I apologize for some of the screwy grammar and botched sentences in some of the prior posts. (I need an editor, or maybe just spending less time watching Hindi, Korean, & scandinavian media would help! :-) )
If you install 4" of foam on the top section, install 4" of foam on the bottom section too.
Reducing the roof overhangs to 15" (or even 5") would be just fine for the "after" picture, since there will no longer be direct wetting of masonry, with capillary breaks between the siding and masonry.
Polyiso designed for roofing insulation is higher density than that marketed as insulating sheathing, and usually has asphalted paper or fiberglass facers (instead of foil, which is usually on wall sheathing polyiso) but it can still be mounted on walls. Reclaimed roofing polyiso is FAR cheaper per R than new insulating wall sheathing polyiso, and re-use is far greener than any new insulation.
Installing any fiber insulation in direct contact with a masonry wall that could potentially wick ground moisture from the footing is not a good idea, since it can raise the moisture content of the susceptible wood, or finish wall. Even a thin sheet of polystyrene insulation breaks the capillary draw, yet is still reasonably vapor open, allowing the masonry to dry, and not compromise susceptible wood that may be in contact with the masonry. Only un-faced polystyrene should be used here. Half-inch 1.5lb XPS is about 3 perms, comparable vapor permeance to interior latex paint on drywall, as is 1" unfaced Type-II EPS. For the fully above grade portion (walk-out basement wall) it's probably going to be fine to have the fiber insulation touching the wall, but at the very least applying masonry sealer and painting it with a latex primer to limit ground water moisture wicking into the fiber would be prudent.
2' below grade means extending the exterior foam down to at least 24 inches below the adjacent ground level, which in your case is sloped on two sides of the house. You don't have to dig all the way down to the footing. It's not clear if that would be easy or hard to dig down 2' in the covered stone clad patio/porch area, and may not be fully worthwhile in that section if it's too difficult/expensive to cut the patio slab to accommodate the foam. I suspect it's not going to be that bad. A diamond blade on a circular saw can cut through the finish stone and concrete down to 1.5-2" inches below the top surface, and a heavier-duty hammerdrill with a chisel bit can take out the rest, as long as that slab isn't super-thick.
Thanks for your detailed answer, Dana.
Gents,
Hope you are well, I am coming with another quick question, hopefully getting to the end... So I, most likely, decided to remove my plaster, and expose the brick on the inside. Then I plan to run continuous foam board on the inside, no more than 2 inches thick, and then frame it as thin as possible so it is enough to install electrical boxes.
Q1.
The only foam I would agree to put inside of my house would be a faced polyiso (facing the brick), unless you know other “green” options. I would go with 2 inches thick continuous layer, taped on seams. Then a stud wall with something in between studs, can I use roxul here, on the top of the polyiso? I guess it should be ok now, correct?
Q2.
2 inch thick polyiso will not be water preamble. If the house, during winter, turns out to be still cold, I still want to have an option to insulate it with 3-4 inches of a foam board on the outside. Is there a foam board with not bad R but still water preamble at 2-4 inch thickness. Hope this will not be necessary, but whatever I install later should be water preamble so the wall can dry to the outside. Is this feasible? Just in case of any issues, I really hope that I will be ok after insulating it inside.
As always, your help is greatly appreciated. I am hopping to execute my plan very soon, and not to come back with 10 more questions.
Sebastian,
If you are talking about insulating an above-grade wall that is a structural (multi-wythe) brick wall, you are breaking the rules. Here is a link to an article with recommendations for insulating this kind of wall: Insulating Old Brick Buildings.
If you don't want to accept the advice of building science experts, you are risking moisture problems and freeze/thaw damage.
One more question to add to my saga. Please assume that my house is a good candidate for insulating using rigid foam on the inside. Freeze/thaw risk is minimal, brick is in good shape, it is protected from the rain, plus there are two layers of it (cavity wall). I also understand what is the best in this case, and understand that I what I want to do is not ideal.
I would like to follow guidelines included in https://www1.eere.energy.gov/buildings/publications/pdfs/building_america/measure_guide_rigid_foam.pdf . Furthermore, I wanted to follow the following chapter of the aforementioned article - 1.1.3 Rigid Extruded Polystyrene (XPS) Board Insulation. "This method is relatively easy to implement and consists of rigid foam insulation board directly adhered to the masonry wall, finished off by studs and drywall. When installed correctly, the taped and sealed foam is an effective air barrier. Two-inch XPS that is rated for moist or below grade applications is recommended in colder climates (Climate Zone 4 and higher), as it is a more durable product. If additional insulation is required, the cavities in the stud wall may be filled with fibrous insulation. The application of a liquid-applied air barrier to the inside of the masonry before the installation of insulation can be an advantageous back-up measure."
1. Can I do 1 inch of Polyiso (as stated before I will not do EPS, XPS or spray foam due to questionable chemicals included) and fill the rest with Roxul between 2x4? It will meet code requirements, but I also wanted to make sure that thinner layer of the board will not cause any moisture issues (I do not want to lose too much of real estate, hence thinner polyiso. I am open to suggestions in terms of the wall composition, I can do up to 6 inches all in, including framing, and sheetrock)
2. Do I need any air gaps here between polyiso and roxul?
3. Would mem-brain smart vapor retarder, before sheetrock, be suitable here or should I skip it completely?
4. Assuming all prerequisites are fulfilled, is there anything concerning with this approach?
As always, I appreciate your time and help!
Sebastian,
In Climate Zone 4, an inch of polyiso is enough to avoid the problem of condensation on the interior side of the rigid foam.
That said, there are still a few risks here. The biggest risk is that hidden air channels (which are hard to prevent) will allow warm, moist interior air to find a way to the tiny gaps (inevitable gaps) between the bricks and the polyiso. Since the insulation makes the interior surface of the bricks colder than ever, you can get moisture accumulation on the interior side of the bricks if these air pathways exist.
That's why closed-cell spray foam is the best insulation to use.
I understand the risk. Is there anything I can do, referring to my questions #2 and #3, to minimize the risk? Would vapor retararder on walls and ceiling help in keeping warm and moist air inside of the house?
"2. Do I need any air gaps here between polyiso and roxul?"
Absolutely NOT!! An air gap would be a potential thermal bypass channel. The insulation layers need to be snug up against each other for optimal performance.
"3. Would mem-brain smart vapor retarder, before sheetrock, be suitable here or should I skip it completely?"
It doesn't hurt, but if the stackup includes an inch of foil faced polyiso for dew point control MemBrain does not buy you anything. The fiber insulation will be warm enough to not accumulate wintertime moisture, and the foil facers block exterior moisture drives from the brick from reaching the wallboard.
The work has started! Turns out there is no air gap, between the bricks. Just two layer of the bricks. The bricks are water proofed on the inside. Wood was attached to the brick, and plaster walls attached to it. Wood and brick has no mold or moisture signs at all. Continuing with the plan of gluing foil faced polyiso to the bricks (foil facing the bricks), and framing afterwards.