How to insulate steel beam cantilevers to exterior?

I am building a home with a large amount of steel beam cantilevers to the outside of the structure. I am worried about thermal bridges to the inside of the home, condensation, etc.
Directly against the web of the beam would be placed the sheathing, and then the siding (stucco). Directly below the flange would be a stucco board and then stucco.
Since both the web and flange are right next to the exterior, what is the best method of insulating? I was thinking of filing the web with rigid, foam, or wool, and then applying a Dow insulated sheathing (R-3 to R-5).
As for the flange, the only thing I could think of is using a 1/2″ thick foam insulating board, with a wire lath and then applying the stucco. That would maybe give it a R-2.5 below the flange. On the other side of the web we are stuffing the wood TGI’s. So likely it won’t be insulated or I could spray an 1″ of foam in there.
Recommendations? Products? Anyone have any better ideas?
GBA Detail Library
A collection of one thousand construction details organized by climate and house part
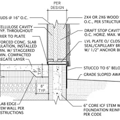
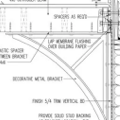
Replies
I'm not sure exactly how this beam is being used but you call it a cantilever and say you are considering only 1/2" of insulation at the flanges. Assuming you are somewhere in the great cold north, this is not going to be enough to provide any help. In addition to the thermal bridging, which will be significant, the possibility of condensation will be high. Even worse is that it sounds like you are covering it all up so that when things start rotting, and the steel starts corroding, you won't know until it is too late and you have to tear it all down. Again, without knowing the details, I would look at using a wood beam instead of steel. LVL or PSL engineered beams may end up being deeper than steel, for the same span an loading, but have far less thermal transfer and are much easier to apply normal finishes to. They are also easier to push up into traditional framing which may get a major portion up into whatever the floor system is that you are using.
Brandon,
I would talk to your architect about changing your design. You don't want steel beam cantilevers penetrating your thermal envelope. Back to the drawing board.
i disagree with martin - you can penetrate the envelope w/ structural members (even steel) and still hit passivhaus, so a redesign isn't needed.
in europe and canada (waaay ahead of us on the thermal bridging issue) there are products for this - though typically concrete over steel.
schoeck isokorb KST is designed for steel-steel connections through envelope. i think this may have even been used recently here in seattle but might be thinking of another product.
http://www.schoeck.co.uk/en_gb/new-construction/kst-36#category
images:
http://www.passivehouse-korea.com/assets/images/autogen/a_Massnahme_Isokorb_Typ_KST1.jpg
http://www.dako-pr.de/uploads/media/10-01_Isokorb_KST_Detail_02.JPG
I saw these products on display at the International Passive House conference in Innsbruck last week. There are a myriad of applications that will provide a thermal break in steel beam construction. With planning and new product choices you can hang most anything you want, where you want, and design it to be thermally broken from the steel or concrete structure within the conditioned space.
You gotta love "thermal progress"!
I'm not sure I'm properly visualizing this arrangement - are the beams sitting entirely below a properly insulated second floor platform or are they wholly or partly embedded in it? Are they an expressive design feature of the exterior? Obviously you cannot 'thermally break' the beams themselves without destroying their structural purpose, but if design parameters do not preclude this you can wrap the beams on the exterior so that they are effectively within the building enclosure. The most effective way to do this would be by furring down the cantilevered floor to a full stud depth below the steel and then insulating the whole assembly properly. However you don't seem to be going this route.
Just wrapping the bottom and sides of the beam as you seem to be planning would be a rather poor substitute, though in Seattle's mild climate you could probably get away with it. But why not use at least an inch of foam board? I wouldn't recommend the Dow SIS for this application, the hardboard backer of the SIS is intended for wind bracing of a stick frame, would serve no purpose here. You just need a secure fixing for your wire lath - 2X furring behind the foam will do it. I agree with Mike you don't need a full redesign as Martin suggests, however it is pitiful that this issue was not considered and fully resolved at an early stage in the design process rather than subjected to a last-minute kludge during construction. Par for the course I know, but still, just pitiful.
Well, you know those Seattle architects and their thing for steel cantilevers! Big cantilevers are the easiest way to win an award (speaking as a fellow member of the tribe...).
I'm with the others, either wrapping in foam board, or coating the exposed steel in adhering spray foam and then casing the steel in stucco is your best bet.
Make sure as well the penetrations through the envelope are very well airsealed before you add your insulation, hopefully with a flexible tape that can withstand differential thermal movement over time and not crack loose. Cantilevered beams are classic leak points on decks and overhangs in a marine climate, and very tricky to seal where they enter the building. They can wick water long distances if they get a chance.
Aligning architectural aesthetics and technical performance is a huge issue in the profession right now, they're often strongly at odds. It's something we all need to be working on changing.
The solution is to move the steel further from the exterior. It probably needs nearly as much insulation outside of it as all other parts of the house. If it's currently positioned right at the exterior surface of the building, it's going to be hard to insulate it.
This is the part that would really concern me. How is this going to be detailed so that the beams don't get wet and possibly even draw moisture into the building? I'm a little north of Seattle and stucco is a tough choice in this climate. You are probably going for a modern look. And, it's not arctic cold here, but people tend to use at least some heat about 8 months of the year.
Jesse,
Thanks. Your observation -- "Cantilevered beams are classic leak points on decks and overhangs in a marine climate, and very tricky to seal where they enter the building. They can wick water long distances if they get a chance" -- is one of the reasons I advised a redesign without the cantilevered steel beams. When I see beams like that, I cringe.
The other commenters who believe I overreacted may have a point. It's possible to wrap a steel beam in foam insulation and make it work. But very often, these details are done sloppily, with insufficient insulation and bad air sealing -- so it's worth putting designers on notice that energy nerds like me think these beams that penetrate the thermal envelope are a terrible idea.
The home is already being built. We were planning on just adding a thermal break below the flange of the beam (R-0.6). What if I tell them to fur all the ceilings down 2" and put in 2" of R-7 spray insulation or rigid board. Giving us a R-14 there. Plus then use the R-2.5 stucco board. Thus I would have about an R-14 to R16 below the flange of the beams (W14). Seattle code says R-29 on exterior walls and they would all be super insulated in between the joists except for the flange of the beams. Do you think this would give it enough of a thermal protection from the elements and keep the moisture at bay. Still the outside corners of the web of the beam would likely be an R-4 to R-6, but the inner side of the web would be about a R-20.
The steel beams are fully encased by the siding. They are not exposed to the exterior air at all. But are right up against the sheating and air barrier, etc. The steel beams are stuffed (with wood) and then TGI's are running in between them. The area will not be vented. Spray foam will be sprayed all around the joists to air seal the area. Although the spray foam is not directly sorrounding the steel beam. Will I have to worry about future rot of the stuffed lumber and joists. Because of the beams sweating / dew points / condensation because the flanges are so close to the exterior. Would it have been better to place a weatherproofing material fully around the steel beams before stuffing them?
They are wholly embeded below the second floor. Then subfloor placed directly on top of the top of the flange (beams stuffed). No water proofing planned above the top of the flange. Although I could ask the GC to add some layer of tarp or something below the subfloor (warmboard) to keep the moisture (if any exists) below the subfloor. I could also ask them to take out all the stuffing and apply some type of water proofing material (around each steel beam on all sides). They said spray foam sorrounding each steel beam would not be good as it would provide an uneven surface for filing the webs. recommendations?
Brandon, your most recent written descriptions create a very different impression than has seemed the case before. I think you'll need to post a drawn detail of the existing setup - and maybe some photographs - to clear up the confusion and then you'll be more likely to get a clear response to your concerns.
Here is a picture of the ongoing framing. You can see toward the back of the picture some of the beams webs are stuffed - wood directly against steel. Those beams cantilever the foundation walls.
Its a 3 story home. the second floor cantilevers over the first, the third cantilevers over the second. The steel beams support the cantilevers. The steel beams are not directly exposed to the elements but are very close (1" off or so). There will have to be R-29 insulation under the cantilevered floor between the joists. However, the flange part of the beam would maybe have just an R-2.5 sourading it. The home is being built in Seattle WA. So we have a mild marine climate.
Here are some sketchup photos of the home. The steel is embeded beneath the siding. Its just that the steel is very close to the exterior and the bottom of those flanges are not sorrounded by much other than the siding and maybe a R-3 beneath them. We will be doing our best to seal all air out of the underside of the cantilevers using spray foam, taping to make it a air-tight space. I'm just worried about those beams getting cold in the winter, reaching the dew point, sweating and rotting the stuffed beams on my house, TGI's, and subfloor (warmboard). Plus them bringing in cold to the structure and subfloor which is directly on top of them and raising my heating bills. The rot, if it happens, Its something that would never be covered under my warranty with the GC because it would likely be something I deal with 10+ years down the line. should I have a concern or have him make any changes so that the wood is not against the steel (wrap beams in visqueen before stuffing and putting the subfloor on top to keep moisture if it happens off the wood, etc) ideas. ? Or do you think I'm worried for nothing because the beams will be fully encassed under the siding in an air tight environment and the likely hood of problems is very small.
Thank you for all your help.
I see lots of "issues"
some are more frightening than others.
Brandon,
Thanks for the further details. I now see that your beam problem is different from what I visualized. Nevertheless, you have a heap of problems to address.
It is unconscionable that the designer left the thermal insulation and air sealing details to such a late date -- after construction has already started! I just can't understand how it's possible for an architecture school to graduate these ignoramuses.
Well a picture's worth a thousand words they say and this demonstrates the point very well. From a quick glance I'd hazard a guess that condensation on your cantilever beams might be the least of your problems ten years or so down the road. Yes, this amount of steel will create excellent thermal conduits to/from the interior of the building unless they're covered with the equivalent of at least a couple of inches of foam on all exterior surfaces: I don't see why this would be difficult to achieve though from what you say it doesn't seem to be in the contractor's current plans. With this much glazing you can't afford to cut corners on the thermal performance of the other parts of the building enclosure. But also watch for failed parapet flashings, clogged roof drains and all the other well-documented performance problems of 'white modernist' buildings in rainy climates. Your framing is far more likely to rot from liquid water penetration resulting from these kinds of failings than from any amount of condensation on the steel. Get the drawings reviewed by a competent third-party engineer before it's too late. This kind of building is not fault-tolerant. Unless you're careful it's going to be a very high-maintenance home.
Just to be clear...
I would recommend an engineer look at the retaining wall near the property line
I am not familiar with your soil... This does not look "safe" to me
I looks like the windows a level above the garage door and down the left side in the center rendering would interfere with insulating under the beams. If those can slide down you can insulate to your hearts content
don't order the glass yet............
And yeah, what James said, ask you designer if he knows flat roofs aren't really flat....
I agree that there is something "not-so-good" about the Architecture Schools
And the Profession
Brandon,
As Keith said, at the least, dropping the cantilevered soffit down 3 - 4" would allow a real layer of rigid foam to be added to the underside of steel, which would do wonders to isolate that steel from the exterior vertically. The rear of the house will have issues with the window hard up against that soffit (would have to shrink), but you could end up with a consistent window to soffit detail around the house front to back in the end with this revision if you raise the front windows in tandem with rear lowering.
Width issues are difficult to judge without a wall section, but 2" minimum rigid would be a starting point to the outside face of packed out steel.
Brooks, you are absolutely brutal. I'll be sure never to post a pic of any of my projects!
pshaw!
architecture schools aren't the problem. neither is the profession. architects are responsible for less than 3% of single family homes.
but to respond to your "dwell" crits - i've seen all of those details successfully implemented on a passivhaus. granted - this house won't meet passivhaus - but you couldn't discern that from the rendering alone.
for example - your john portman (shudder) concrete thermal bridge could very well be a valerio olgiati paspels schule w/ concrete sandwich wall w/ ample insulation and an incredibly awesome structural feat of hanging the outer leaf on massive shear studs... stunner! bonus points for the corbusian scupper!
http://www.pratval.ch/assets/images/Oberstufe%20Paspels.JPG
additionally, you need more glass here in the NW - it's absurdly difficult to dwell comfortably in your home without it. Even with high VT glass - "normal" windows just don't let in enough of our overly limited daylight.
btw, the kundig-designed corten beaut jesse posted @8 comes with some really cool rental facilities - the herd:
http://www.rollinghuts.com/the_herd.htm
David,
You are right
I will accept the "nice lesson"
I did not intend to insult the owner or the Architect.
From what I have seen .....
the Architecture Schools and the Architecture Media seem to glorify Glass & Steel
and drop the ball on Low Energy and Durability.
Mike,
You wrote, "Architecture schools aren't the problem. Neither is the profession. Architects are responsible for less than 3% of single family homes."
I certainly agree that most residential designs don't involve an architect. But I never claimed they did.
1. I'll bet that an architect designed the house under discussion in this thread. If there is no architect on the project, I'll apologize for my slandering of architecture schools.
2. It appears to me to be a little late in the project for everyone on the job site to be scratching their heads and asking, "How do we insulate the exterior of all these steel beams?"
3. Such thermal bridges are sadly common on commercial buildings designed by architects, and I am not the first person to note the problem. Somehow, architecture schools are producing graduates who repeatedly ignore the fact that buildings need air barriers and thermal envelopes. This is astonishing to me.