Floor Trusses, OSB Sheathing, Rigid Foam, and Masonry Finish

Wow, I have spent countless hours reading your articles and blogs. Much to my husbands chagrin! We have already built a garage with an apartment above it in WNC, zone 4. We used certainteed cement board siding, tyvek, OSB, 2×6’s, 5.5″ open cell in walls. The roof deck was sprayed with 8″ of open cell and is unvented. (The Hvac is up there and from what I have read we should probably have supply and return ducts up there to keep moisture from becoming an issue… We are considering adding more insulation on the attic floor. But that will be another post .)
Now we are building the house. See photo for husbands mock-up. The basement is superior wall with a walk out on one side where the grade permitted (already in, decked, and back filled). After we ordered the houses floor trusses we decided to avoid the thermal bridging that is so evident on our garage by adding rigid foam to the exterior of our house. As a result of the last minute decision, the trusses were not designed to allow for OSB and foam to be applied without them being proud of the superior wall basement. The framer was able to gain 1/2″ of setback on three sides of the trusses by setting them closer together but one side is flush with the superior wall.
Upon consulting with our framer, we are considering using OSB to sheath the walls but not the first and second floor trusses. The walls would be set back 1/2″ from the trusses to allow OSB to sheath the walls but stop flush on top of the trusses. Then a continuous layer of rigid foam would be applied over OSB sheathed walls and bare trusses. This would leave the foam proud of the superior wall.
To further complicate things, we are applying cultured ledgestone to the first three feet of the first floor and continuing down the wall as the grade falls away to the walkout basement. Potentially, we can make up the difference by building up the superior wall with mortar before applying the stone.
Would that work?
I have read here that in zone 4 any exterior foam thickness is enough. Could we use as little as 1/2″ or 3/4″ EPS to minimize the problem but not cause issues with sorption (condensation)?
Boral specs applying two layers of wrb under the metal lath. They also say applying stone to rigid foam thicker than 1/2″ may require special fasteners. Any masons out there have suggestions?
After applying rigid foam and tyvek (both taped) we would fill the 2×6 walls with blown cellulose in the hopes of saving money, good moisture management on the interior side, and yet getting good r value. All at less cost to our health than using spray foam. Then drywall and latex paint.
I have tried finding an insulation contractor to speak with on these issues but it seems they are only able to promote their method of insulating.
Sorry for being so long winded but we are frustrated at this point.
.
GBA Detail Library
A collection of one thousand construction details organized by climate and house part
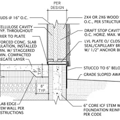
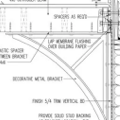
Replies
I'm not sure I understand the problem with the foam being proud of the foundation. Why not leave the wall and sheathing design as planned and have it hang over a bit? That's not uncommon.
As far as thin foam, it's reasonably accurate to estimate as follows: Your 2x6 wall with cellulose would a net R-value of R-14 or so, considering thermal bridging. You might hope that adding some foam would undo that degradation, but it doesn't really undo it. All it does is add a layer of insulation that isn't subject to the same problem. So if you have R-4/inch foam that is 3/4" thick, you add R-3. Your R-14 goes up to R-17. If you add 2" thick R-4/inch foam, you go up from R-14 to R-22. Adding foam doesn't solve bridging in the sense that you get more than you pay for--the benefit is more that you actually get what you pay for, unlike the cavity insulation where the performance is undermined by bridging. Roughly speaking.
Yes, insulation contractors are more likely to sell their product than give good advice.
The design of the building looks really nice, by the way.
The garage. If it is occupied right now, go in the attic and stick your hand into the insulation near the peak. If it is dry you are in great shape and should have no problems. I have used the same spray foam and have had no issues. The farther south you are the less problems. I am in zone 6 and have builds with no moisture issues.
You can easily and economically improve your garage apartment floor. The edges of the floor may need to have the insulation improved and the whole floor can have rigid foam added quite easily. You could also if carpeted, pull the carpet up, drill holes to blow in some insulation along edges if not done well, add insulation under the carpet we had a customer just put rigid foam down on the floor and cover it and it worked out well. Radiant cove heat shooting down from above would warm the floor. Insulate the garage and install a pellet stove in the garage, make it a play room, heat it for the worst winter months to help warm the floor above.
Building Science has great details for detailing a build. Go read for a few days. They details anyone could follow, they are top notch.
http://www.buildingscience.com/index_html#
This link explains how I like to see a garage apartment above insulated during the new construction or if redone.
http://www.buildingscience.com/documents/insights/bsi-064-bobby-darin-thermal-performance?topic=resources/flooring-probs
See if you can't get all air sealed well.
Buy great windows and good doors,
Where to insulate. Insulate at this point where it is easy and economical and most effective. Doing the basement well and the attic well IMO would be all I would do. I would not mess with the walls at this late stage. My other items mentioned will do much much much more. Air seal, air seal, air seal.
Caulk or gasket the walls as they are set up during the framing. If not done then, you can caulk every seam of the frame after up. When interior partitions are drywalled they need to be caulked to the top plates. Many apply a bead of acoustic sealant or use log home log tape that you can buy from a log home supply company online.
Seal up the layers of the home as you build. Get a blower door test that includes time to look for the air leaks and seal up the leaks or at least mark them to do so at some point.
Buy the best windows you can afford. Much less cost to do so now on new construction.
Your home model is the best, you should be doing that for others. I hope any Western windows are super top performing. Which way is south on the model?
Condensation on walls and roof assemblies is a function of temperature and humidity differences between the inside and outside during the coldest months of the year; and how you manage both will affect your risk management level. Usually, dew-point analysis is made with interior temperature at 70°F and 40%RH. If the temperature and/or humidity goes up, the higher the risk for condensation. This dictates how much outsulation to use.
Let’s start with what you have right now. You are in Climate Zone 4. You are required to install R49 in the attic and R19 on the walls. See 2012 IECC Table R402.1.1. Installing 8” OC foam in an unvented attic only gives you R28-30. Open Cell foam is air-impermeable, but it’s not moisture-impermeable. Installing 60% of the insulation required for your climate zone is a bad idea (terrible sales job by the insulators, or lack of knowledge).
For your roof assembly, you need 2” closed cell above or below the roof decking minimum, plus 9”-10” open cell foam to reach a full R49. See 2012 IECC R806.5. Hopefully on the new house this issue is corrected, especially when I see in your model that you guys have vaulted ceilings. There are several articles in this website about insulating vaulted ceilings and conditioned attics.
The exterior 2x6 walls are well insulated with 5.5” of dense-packed cellulose for an R21, well above your minimum requirement. However, for condensation mitigation, you need 1” rigid foam R5-6.5 for outsulation minimum. To install siding, stucco and stone, I would recommend to use a rain screen, like Delta-Dry or Home Slicker. A rain screen is a three-dimensional thermal break material that allows moisture drainage. To install stone over 1” rigid foam, the manufacturer should have installation instructions specific to the stone you selected, or may be wise to hire an engineer. Again, there are plenty articles here at the GBA that talks about rain screens.
Do find contractors that have experience in high-performing houses and not give you the BS sales pitch just to get the job, otherwise you’ll be stuck with the problems later. Do thing right up front, or you’ll pay later.
Kristin,
If I understand correctly, you want to install "cultured ledgestone" (basically, little pieces of concrete that are formed to look like stone, and need to be adhered to the outside of your building) to parts of your Superior Walls foundation, and to extend the ledgestone so that it covers the lower sections of your framed walls. Is that correct?
If that is what you are trying to do, it is a tricky detail -- especially if you have framed walls that aren't co-planar with your foundation, and if you want to add rigid foam to the outside of everything.
If this detail hasn't been drawn up, and if you don't know how to do it, it's time to hire an architect and ask the architect to draw the detail. You have many issues: foam thickness issues, attachment issues, the need for a ventilated rainscreen gap behind the ledgestone, and risks of moisture entry into your wall. That's a long list of questions to try to answer in a Q&A column.
Thank you all for the quick advice!
My husband designed the house and built the model. I have trouble envisioning what my husband describes so he built the model to help me 'see it'. He even built some furniture so I could get perspective on the space. :-) I suggested he hire out his talent to local architects!
We are going to seal every where we can and are considering a blower door test as well, as you suggested AJ.
The front door faces south and the wall of windows you see is to our western view. The walk out basement is on the northwest corner but not built on the model.
We did make a design change after the model was built. We have collar tied the roof system for a ceiling height of 10'6" at its tallest. That meant removing the trapezoid windows and just going with the door wall. There will be a screened deck under the roof over hang on the south and two decks at the door walls on the west. They will help block some of the windows from the summer sun and a line of trees to the west will help. We are using Andersen's 400 series windows/doors with sun glass on the west.
Armando, they may have put a little more than 8" on our roof deck since they said it was R 30.6. Code at that time was R38 and they said the inspectors would pass us due to the fact that open cell also offers greater insulation due to the air tightness. Was I gullible? That was before I discovered you all at GBA!
Any advice on how to increase the garage attic insulation? I assume no blown cellulose with the furnace up there?
Thanks Martin. I had pretty much arrived at the same conclusion but needed to see if anyone had a magic wand.
So, at this point we are very frustrated. My husband wants to ignore the thermal bridging and just sheath with OSB and forget the rigid foam on the exterior. That would leave us mostly flush with the superior wall which would make it easy to apply the cultured stone. Would that be committing hari-kari on our sheathing? we are not considered a cold climate after all.
With no exterior foam would open cell in the wall cavities be advisable?
This is not a complicated issue, and I would not give up on outsulation, it is a critical component for high-performing buildings, plus gives you lots of protection in the long road, but at the end of the day, it’s all about what you are comfortable with.
I would maintain continuity with the wall sheathing from top to bottom, install the WRBs and Rain Screens, then 1” rigid foam on top, with capped nails. Hardie Siding and Boral have free, downloadable installation instructions on their products. They should also provide “Best Installation Instructions” for applications using outsulation and rain screens.
Please check with an experienced Architect, Engineer or HERS Rater or Provider for detailing. It should not be that expensive, and it can save you a lot of money down the road.
FWIW, you were not gullible, it happens most of the time. Unfortunately, most insulating contractors do not have a clue about building science, exposing the homeowner to higher risks, and they try to make their bids more competitive by bidding less of the amount required, also because the code allows to install less R-value under the “Performance” code verification process, which you most demonstrate a minimum HERS score to be achieved and verified.
I just had an additional thought: Just because the code ALLOWS something to be done, it doesn’t mean it’s the right approach. A “Code” house is the minimum allowable house it can be built!!! All physics laws still apply and when bad things happen, you, the homeowner, get stuck with the fix-up costs.
Thanks. One issue still being the superior wall basement will not be on the same plane as the rest of the structure since it will not get OSB or foam. The stick built walls would be proud of the basement walls by about 1.5". That's a lot of space to make up with mortar. I'm afraid I thought of using outsulation too late in the game.
We consulted with an engineer on our roof structure. It took him weeks to get us the approved plans. Now the framer is ready to start tipping up the walls. Don't know if my husband will wait for the engineer to get back to us on this. Ugh!
We really appreciate your advice
What about covering up the exposed basement walls with even more stone veneer? That should make up the 1.5" gap and look prettier than exposed concrete anyway. It'll be an extra cost, but it sounds like you don't have a gigantic amount of exposed wall to cover.
Now that I understand that the stone is going to extend above the foundation wall, what about adding 1.5" EPS foam to the outside of the foundation wall to make it flush with the foam added above? Then you have the same material sticking out the same distance all the way up and down.
Well, the idea is to cover the exposed basement wall with stone and continue up the structure to roughly three feet above the first floor deck. The problem being the basement and structure above are not co-planer, to use Martin's term. So we need to figure out how to have the stone flush over the area. Extending the rigid foam down the superior wall makes up the gap but it also makes an issue of installing doors and windows on the walkout elevation. Not sure if SW recommends that. Am waiting to hear back from our rep. Also, boral does not recommend applying stone over foam more than 1/2" thick without getting an engineer to certify the install method.
Kristin,
There are lots of problems with your plan. You need a ventilated air gap between the fake stone and your OSB or plywood wall sheathing -- and this air gap needs air inlets and air outlets. The air inlets can't be below grade. If the fake stone doesn't extend below grade, it looks like glued-on fake stones instead of a stone foundation.
Lots of walls with manufactured stone veneer over wood-framed walls are rotting, so it's essential to get the details right.
I have been reading the Boral Stone install directions and they recommend the stone ending 4" above grade. I agree that looks bad. Was not aware of that fact. It is not above grade on our garage. Hmm
They only mention using an air gap if required by local code but I understand that it is good building science whether required by code or not.
And I assume waterproof OSB is not an adequate precaution.
What did you end up doing? I was interested to hear that 1/2" foam could be enough for WNC as I'm similar area in TN.