Double Staggered-Stud Wall vs. 2×3 + Foam Strip + 2×4 Wall

My new house will be in a part of climate zone 2B in Arizona where the winter nights often dip into the 30s and the summer days often rise to 100 with around 45 days of “monsoon season” mostly in August when we’ll get an hour of thunderstorms once or twice a week. We have moderate to severe termites.
I like the idea of a double stud wall, but two 2×4 walls with a 4-inch gap between them all filled with insulation is more thickness than I want in a small 20×40 house and probably more insulation than is cost-effective in this climate. To save some floor space and extra cost, I have two ideas for eliminating the 4″ gap between the walls while still preventing thermal bridging through the wall studs.
The first idea would be two 2×4 walls 24″oc with the studs staggered, but each on their own bottom plate or their own half of a 2×8 bottom plate so that the wall will be as thick as it would be if the studs weren’t staggered.
The second idea would have a 2×4, 24″ oc outer, structural wall and an inner wall made of 2x3s 24″ oc aligned with the 2x4s, but separated from them by 1″ thick, 1.5″ wide strips of polyiso attached to the 2x3s and sandwiched between the 2x3s and the 2x4s. This construction would seem to be easier, as I wouldn’t have to reconcile a staggered pattern whenever I came to a window or door, and I could use the strips of polyiso to interrupt thermal bridging around those openings and throughout most of the wall.
For either idea, I would use R15, 3.5″ Roxul batts between the studs in both walls so that most of the wall area would have an R30. I know cellulose is more often used in double-stud walls, but I prefer the Roxul, and it’s pretty affordable, around 88 cents per square foot for the 3.5″ thickness. The interior would be finished with drywall, the exterior with a sheathing/siding like HardiePanel, SmartSide, or possibly painted steel.
Is there any drawback to my second idea other than the minor trouble of attaching strips of polyiso to the 2x3s?
GBA Detail Library
A collection of one thousand construction details organized by climate and house part
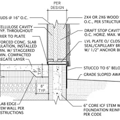
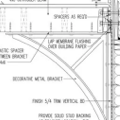
Replies
Jeff,
Your idea will work, but you will get better thermal performance if you simply build a 2x4 wall and install a continuous layer of rigid foam -- as thick a layer as you can afford -- on the exterior side of the wall sheathing.
In your part of the desert southwest, with heat and termites and lots of contractors with masonry experience, I would advocate doing block walls with several inches of rigid foam or mineral wool on the outside. The block walls will be immune to termites, more more comfortable in the heat, and the interior mass should moderate peak loads.
Jeff, Stay away from 2"x3" walls. They will only cause you grief.
Thank you, Martin, Nathaniel, and Malcolm.
Martin, I just read several of your excellent articles about exterior foam, and I understand its advantages, but would it preclude using 4'x8' panels like SmartSide or HardiePanel as the outermost layer of the wall? I understand that I would not need another layer of sheathing, but the extra cost and labor of plank-type siding is a consideration, and I gather that vinyl siding doesn't survive well in the extreme UV here.
Nathaniel, I originally planned to build block walls, but I'll be doing virtually everything myself, and the labor seems too much greater.
Malcolm, Why would the 2x3 wall I propose cause me grief?
Jeff, 2"x3"s can be hard to source, provide a flimsy substrate for drywall especially at 24"oc and under our code at least are too narrow to be used for wiring. You don't see them used in house construction for a reason.
Thanks for the explanation, Malcolm. I don't know about the flimsiness, but 2x3s are easy to get here, and I was planning to run the wiring behind the 2x3s by just leaving small gaps in the strips of foam.
Jeff,
Q. "Would the use of exterior rigid foam preclude using 4'x8' panels like SmartSide or HardiePanel as the outermost layer of the wall?"
A. No. The panel siding could be fastened to furring strips; the furring strips would be screwed through the rigid foam to the studs. For more information, see How to Install Rigid Foam Sheathing. The article includes many links to other articles if you need in-depth information.
Jeff, the more I think about it the more I like you design. Attaching the foam to the 2"x3"s may be finicky but if you are doing it yourself why not? As the walls line up, if you did find the inner one flimsy you could always install plywood gussets at mid span. It sounds like a really build-able wall.
Reply to Malcolm and Jeff: my new house has double stud walls, about a foot thick. Some of the walls are 14' high. I wish we had used the plywood gussets at midpoint. A few of the tall studs bowed out when dense pack cellulose was installed.
Martin, Thank you for the link to your article about installing rigid foam sheathing. I had read it and several of the articles to which it links before my previous reply. The only type of siding they seemed to mention or illustrate was lap siding, so I wasn't sure if screws would be strong enough to hold the weight of heavier siding across a largely unsupported span through foam, but I did find in the manual you link to, " Incorporating Thick Layers of Exterior Rigid Insulation on Walls," a little table that indicates that any siding will be okay up to 5 pounds per square foot. Apparently, HardiePanel is too heavy, as its manual requires nothing but wood encasing its fasteners, but in the SmartSide panel manual, I found the following:
"LP SmartSide Sidings may be installed over low-compression rigid foam or exterior gypsum. The following precautions must be followed:
a) Adequate bracing of the wall in accordance with the International Codes or other ruling building code is required.
b) For rigid foam sheathing up to 1" (25.4 mm) thick, siding may be nailed directly to the foam sheathing unless a drainage plane is required by the local building code. Nail length must be in-creased to ensure a minimum 1-1/2” (38.1 mm) fastener penetration into the structural framing.
c) For rigid foam sheathing greater than 1 in. (25.4 mm), a minimum 1-1/2 in. (38.1 mm) thick by 3-1/2 in. (88.9 mm) wide vertical strapping or furring strip must be installed over the sheathing to provide a solid, level nailing base for the siding. The strapping must be securely fastened to structural framing spaced no greater than 16 in. O.C. (406 mm) with a minimum nail penetration of 1-1/2 in. (38.1 mm) and a maximum nail spacing no greater than the width of the siding.
Louisiana-Pacific will assume no responsibility for any damage or condition arising from the use of rigid foam or exterior gypsum."
Assuming that polyiso qualifies as a "low-compression rigid foam," the main question becomes how much benefit in thermal performance I would gain with sheathing + exterior polyiso at R6.5/inch + furring (if foam over 1 inch) + SmartSide at what difference in cost compared to one of my double-stud walls.
Malcolm and Stephen, Thank you for suggesting and seconding the idea of plywood gussets in case I need them.
Your polyiso strip idea is nice, but you don't actually need it. As long as you have an inch gap between the inside and outside wall studs, the thermal bridging is not bad. And if I am doing the math right, with 2x4 + 2x3 on a 2x8 plate (all nominal sizes), you actually have a 1.5" gap.
Here's the analysis:
http://www.swinter.com/Collateral/Documents/English-US/CNAugust2009.pdf
Charlie, The advantage as I see it from Jeff's plan is that the foam strips leave him cavities exactly the right size to fit standard batts. The foam isn't so much for thermal bridging, as to eliminate voids at the studs and plates so there are no convective air currents in the wall. He is able to insulate in two layers, rather than monkey with another one for the gap.
Thank you, Charlie. That CN analysis is extremely interesting, especially because, unless two studs in contact with each other create much less thermal bridging than if they were one solid stud, the numbers suggest that thermal bridging in itself has only a small effect on clear-wall R-value, and a double stud wall of any thickness may perform slightly better than a wall of the same thickness with solid studs all the way through more because there's less overall volume of wood and more of insulation than because of a reduction in thermal bridging.
According to CN, staggering the studs only improves the R-value of the assembly in a 7-inch, R-23.8 wall by R-1. The improvement in R-value for an 8-inch wall with aligned studs over a 7-inch wall with the studs touching is R-4, but 3.6 of that 4 is due to an extra inch of cellulose, only 0.4 apparently due to interrupting the thermal bridging. Going to a 9-inch wall improves the R-value by another 3.7, 3.6 of which is, presumably, cellulose and 0.1 of which is more interruption of thermal bridging.
A double-stud wall still makes sense, as for a given overall wall thickness, having a space between two walls uses less wood and thus contains more insulation, stopping thermal bridging may improve R-value by as much as R-1, it uses less expensive (smaller) lumber, it may provide an easy path for wiring without having to drill through studs, and it may provide a nicely unpenetrated surface for an air barrier inside the wall, but the study you've cited certainly calls into question the importance of thermal bridging in its literal sense of providing an uninterrupted pathway for heat transfer. I would be fascinated to read what some of the experts on GBA think of the accuracy and implications of the CN numbers.
As Malcolm noted, the main purpose of the foam strips is to eliminate empty space where convection might occur.
You're quite right about the extra half inch. I hadn't really thought about it, as I was mostly envisioning tilting up each of the walls on its own bottom plate, but I did think there might be some benefit I hadn't thought of in having them share a plate even though separating the plates might offer a (small) thermal advantage.
I am not an expert on this but I looked into building with similar thoughts and issues and I created a spreadsheet to calculate the whole wall R-Value of various options.
Your 2x4 + 1" foam + 2x3 has a whole R-Value of approximately 23.3 depending upon the % of wall area covered by studs. It has some significant cost and complexity advantage over 2" foamboard on the outside since 2" 4x8 foam panels are about $25 and strips of 1-2" strips of 1" foamboard will be almost nominal cost in comparison to 4x8 sheets, of course the R-value is a bit lower (by about 2.)
You might consider simply using 2x4 walls + 1" R5 or R6 foamboard strips + furring on the inside as another option - this creates walls close to a standard 2x6 wall size and allows you to use Roxul's 5.5" R-23 insualtion. Where I live the R-15 roxul is $43 while the R-23 Roxul for 2x6 walls is only $45 so you would cut your insulation cost by more than 1/2 (considering saved labor as well.) Plus you can use standard extended window and door jambs (is that an oxymoron??) etc. saving even more on labor and materials. Again, the downside is the R-Value change, the whole R-value for this option is only R-19.22 but that is a still a great improvement over 2x6 walls with R-19 fiberglass batts (~13.5) and is likely the most bang for your buck and effort. Fine Homebuilding has an article on this method called "Breaking the Thermal Bridge" where a builder uses the method on top of 2x6 walls. The article says it makes R-30 walls (it doesn't), but either way it shows how to frame windows and corners as well as interior stud portions so its very useful for a DIY'er.
While whole wall values of 23 and 19 aren't amazing compared to the passive house stuff the cost benefit is very good compared to some alternatives particularly when considering the diminishing returns of adding R-value.
Again I am not a building engineer and just started looking into to this so be gentle with comments if my calcs are off :0)
Thank you, Michael. I would be greatly interested if you would attach a copy of your spreadsheet or, if that 's not feasible, describe how it works enough that I might replicate it. The article you cited is for FH members only, but it's an interesting idea. Here, the R-15 Roxul is around $0.88psf, and the R-23 is around 1.28.
I found an R-value calculator at http://www.ekotrope.com/products/r-value-calculator/ that estimates the R-value of my 2x3 + 2x4 wall at R-23, but it doesn't provide for a double wall or the resulting reduction of thermal bridging.
I have attached my spreadsheet. I basically copy the first section and change the values to get the next wall type.
It only does two types of walls - typical walls with some sort of stud section + cavity insulation and then walls that add another layer of foam board on top. Basically for each section you put in the R-value of that section and the % wall coverage. For the final layer of foam it assumes it is covering 100%. For double walls or studs sandwiching foam board you need to pre-calc the R (which is nothing more than adding the R-value of all the components). There are a bunch if wall types already entered 2x6 + 2" foam is the highest but also the most expensive. I should add in costs to calculate cost/R value.
That calculator you linked to would work if you could set the R-value of the stud area, which you kind of can by changing the thickness of the wood, but you would have to use a thickness that results in R-value equivalent to your double wall or 2x4+insulation+2x3 section.
Essentially the studs are in series with another kind of insulation so you add up the total R-Value to get the R-Value of the stud section. If the studs are literally in line then the R-value is something like R-Value of stud + R-Value of Insulation in between + stud. Thermal bridging is really a misnomer, or a term to highlight that fact that if in parallel a section with a low R-value has a much higher effect than the section with a high R value. Its like two water pipes next to each other one 1" and one 1/4" - no matter how much you reduce the 1/4" pipe the 1" pipe will still have the most effect on waterflow. So to take into effect that thermal bridging effect really means to just correctly calculate the whole R-value.
So if a stud has an r-value of about 1.5 per inch then your stud area has and r-value of (3.5+2.5)*1.5 + 5 (for the poliviso), = 11.88 and the equivalent depth of stud to get that R-value would be 11.88/1.2 = 9.75 " stud. So I entered that into the calcuator referenced above to get an R-value of 23.9. I am not exactly sure what value it uses internally for the R-value of wood so it may be off by a bit but my calculate comes to 23.3 so they are pretty close to each other.
Thank you, Michael, for the explanation and attachment.