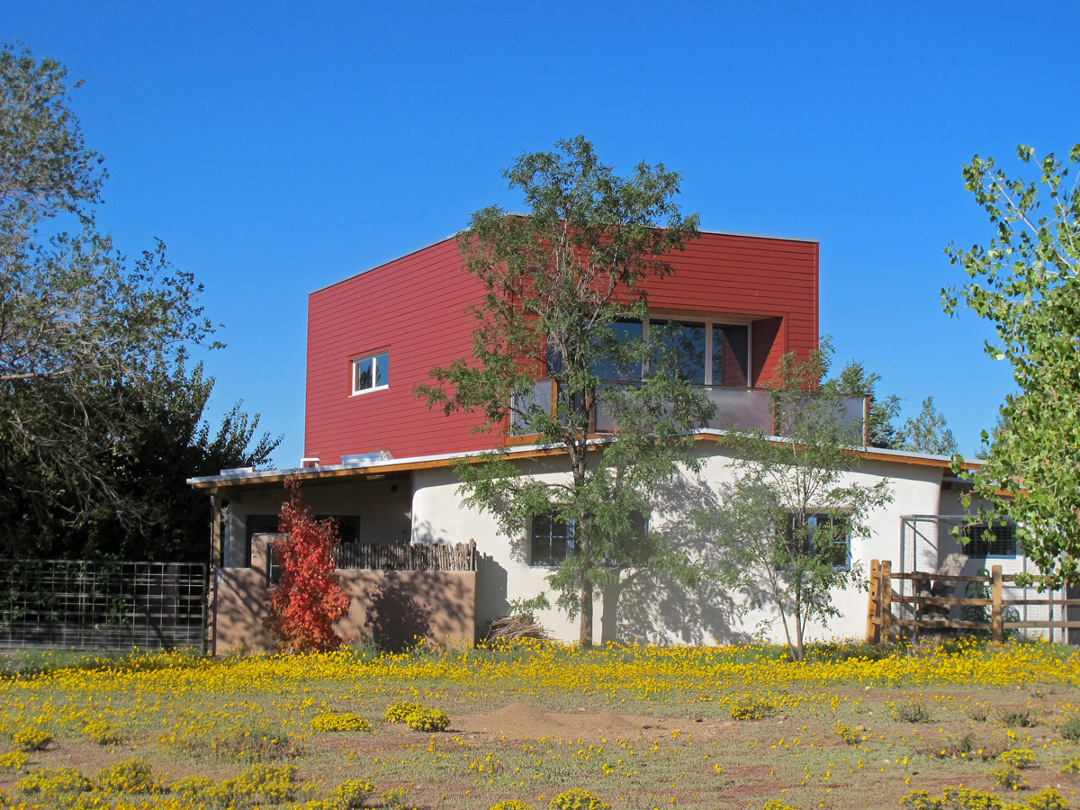
Image Credit: Michael Grant
Image Credit: Michael Grant West view approaching the front door
Image Credit: Michael Grant Entry door to addition showing James Hardie clapboard siding
Image Credit: Michael Grant The outdoor living Portal is at the edge of a public park
Image Credit: Michael Grant The outdoor living Portal, showing the Sunroom just to the left
Image Credit: Michael Grant View from the Guest Studio to the back yard, with Breezeway at the far right
Image Credit: Michael Grant The Entry Foyer showing stairs to the new Master Suite
Image Credit: Michael Grant Sunroom, with recycled Storefront windows on the left and lithocrome black concrete floor
Image Credit: Michael Grant Dining/Living space, showing exposed original beams and a new steel post that supports the second floor
Image Credit: Michael Grant Stairway viewed from Master Suite
Image Credit: Michael Grant Meditation deck suspended over stairway, with small access passage from master bath on the right
Image Credit: Michael Grant Master suite with site-built trusses, bamboo flooring, exposed glu-lam beam on lower right, and chase for center roof drain at upper left
Image Credit: Michael Grant Guest studio: ceiling rafters are only decorative, with TJI's running perpendicular and lengthwise above
Image Credit: Michael Grant Master bath with plywood countertops, Japanese soaking tub, passage to meditation deck at rear, and walk-in shower on left
Image Credit: Michael Grant Studio bath is only 7ft x 3.5ft wide, so a corner toilet makes it all work out
Image Credit: Michael Grant Studio bath: the center-pivot shower door saves critical inches and opens against the sink
Image Credit: Michael Grant The outdoor shower showing exposed copper shower-head assembly attached to garden hose bibs with a manual drain valve at the bottom
Image Credit: Michael Grant A laundry hoist drying rack suspends from individual pulley's in the ceiling; in our dry climate, wet laundry also helps humidify the room
Image Credit: Michael Grant Computer modeling sketch overview of the project
Image Credit: Michael Grant Floor plans show the original adobe footprint (in brown) and the new areas (in blue), along side the upstairs master suite
Image Credit: Michael Grant Cross sections show how the TJI upstairs floor were placed over the original roof, providing a useful crawlspace for ducts and wires
Image Credit: Michael Grant Construction of the entry foyer; this steel post will stand outside the new entry door, and the large glu-lam beam is visible from inside the master suite
Image Credit: Michael Grant Site-built trusses are being laid out upstairs; the steel frame required a crane to lower both posts through the existing roof
Image Credit: Michael Grant The upstairs is sheathed with CDX prior to rigid XPS insulation and the lower adobe walls have been insulated with polyurethane spray foam
Image Credit: Michael Grant A rooftop Oskar Porter as red cladding is being applied over house wrap over blue rigid XPS (the black roofing felt is residual from an earlier application)
Image Credit: Michael Grant
This addition has a tight envelope, thick insulation, a heat-recovery ventilator, and a roof that harvests rainwater
Michael Grant has been building, renovating, and designing high performance homes in Santa Fe, New Mexico, for almost two decades.
My wife Julia and I stumbled upon this dumpy little adobe home in Santa Fe, NM, which was for rent back in 2003. I thought the place had hidden charm; she was skeptical. After all, it still had double-hung single pane windows that dust could blow through, a smelly gas wall heater, and no insulation to speak of.
Yet there was that wide-plank flooring in the kitchen, and it bordered a park, with our Sangre de Christo mountains beyond. The 14-inch thick adobe walls and rubble foundation dated back to the 1930s, and the house had beautiful 4×6 ceiling beams we later unveiled by removing the drywall. And, well … we needed a place to park while we looked for our “real” home.
A couple of years after we started renting the house, after shivering through the winters and sweating through the baking summers, we actually bought the place. This would be the one. We would remodel, and we would go all the way.
Honest renovation
As a continuing student of design, I was learning a new 3D CAD program, and thus of course I modeled our 1,150-square-foot rectangular adobe into the computer and began to play with design options.
Standing on the roof made the mountain views irresistible, convincing us that we would have to build upwards. A friend of mine, also an architect, suggested the radical idea of juxtaposing a modern addition against the traditional home, and that philosophically this would be the only honest renovation we could make. Since Santa Fe was already teeming with “faux adobes” (meaning framed walls trying to look like true adobe walls), I ran with the idea.
Selling such unconventional ideas to our neighborhood would prove a bit more of a challenge, but going door-to-door to discuss our intentions in person offered a wonderful opportunity to connect with folks and win votes. And our neighbors surprised us. I was floored when most of them grew genuinely excited about Julia’s idea to use the color red for our exterior cladding. And so red was exactly what we used.
The result was a true marriage between old and new, and the various eccentricities that emerge from a home that has sheltered generations of people, our animals, and our collective quirks over the years. Julia and I both feel that living in a modern-traditional hybrid brings us the best of both worlds.
Engineering the view and solar performance
Our new addition gives our house an entry foyer together with stairs leading to our master bedroom suite above. Our entire addition is skewed 20º off the home below to orient our view straight towards Lake Peak, the highest nipple eastward on the ridge line of our Sangres.
Skewing the orientation allowed us both to define opposing styles and to offer a resolution to problems with the floor plan intersections. The second-floor load bears not on the weathered adobes, but on three strategically placed steel columns, a couple of steel I-beams and wood glulam beams, all of which I had engineered for just $1,500.
The sunroom works as a solar collector
To the south we added a sunroom with panoramic storefront windows. I had made a dumb mistake earlier; I first installed the storefront windows in our bedroom upstairs before I knew better. The windows produced condensation in winter and made us overcook in summer — all because I had placed more importance on my idea of “sexy” over what actually worked.
The windows made more sense in the downstairs sunroom, where we also installed a temperature-activated fan that harvests warm air from the ceiling and delivers it to my home office on the north side of the house via a 6-inch duct. The fan is automated to activate only when two conditions are met: the office is below 68ºF and the sunroom is above 78ºF. This was made possible by a Johnson Control A419 thermostat with a remote probe to the office, and some special wiring from my electrician.
Adjacent to the sunroom, a secondary mechanical room was added to house a future solar hot water tank for the solar collectors we will soon mount on the shed roof of the sunroom. The solar hot water tank will then preheat water for our high-efficiency combo boiler in the primary mechanical room.
Detached guest studio with outdoor shower
Outside, across our tiny yard, we built a diminutive studio, complete with a cedar sauna and an outdoor shower. Various friends and family have put their names on it. While less efficient from a thermal standpoint, there’s something sweet and delicious about guest quarters that are detached from the main home. Rather than build a new mechanical room for the studio, we extended a deep 4-foot trench with superinsulated water lines from the main mechanical room, with separate loops for DHW and radiant floor heat. The studio has its own thermostat that we set to 50ºF when unoccupied.
There’s nothing like taking an outdoor shower, but there was one hurdle to solve. I couldn’t find a frost-proof shower valve for this application, so my plumber and I did some creative plumbing (see photo). We used two regular garden hose bibs for the hot/cold lines, safely buried in the insulated wall of the bathroom on the opposite side. Our custom exposed copper shower head assembly then screwed onto the hose bibs, and includes a manual release valve at the very bottom. In winter, this must be manually opened after each shower to drain the exposed assembly against freezing.
Weatherization details
To weatherize the existing adobe home, we had to blow 2 to 3 inches of spray foam over all of the existing stucco, and then re-stucco. We built a new framed roof above the existing roof, to beef up the roof insulation and expose the old 4×8 rafters to the living space below. And we replaced all of the single-pane windows, of course, with a mix of Serious U-0.16 windows and decent Pozzi wood-clad U-0.28 windows.
All of the new walls were framed with 2×6 studs with dense-packed cellulose. After the walls were sheathed, an additional 2-inch layer of XPS foam was installed to raise the dew point temperature of the sheathing.
After tightening up the home with spray foam, closing off the old crawl space vents, and blower-door testing, we added an Ultimate Air heat-recovery ventilator (HRV). Because our home tested positive for radon, the HRV would kill three birds with one stone: supply fresh air, retain our heat in the winter, and mitigate the radon by dilution and negative pressure by exhausting from the crawl space. We were relieved that subsequent radon tests have tested negative.
Roof design for water harvesting
Our master suite roof is supported by custom-engineered, site-built, top-mount trusses that slope to the middle. Thus we have a center roof drain to avoid canales and to capture all rainfall in a 4-inch pipe leading to a 1,700-gallon cistern. (Please note that this approach does introduce a large pipe straight through the thermal envelope of the home, contributing to heat loads; such a pipe should be extremely well insulated.)
Water is stored in a buried orange-ribbed Infiltrator tank. It confounds me to this day that other tank brands require a minimum water volume percentage of, say, 25%. Why collect water you cannot use?
A Grundfos pump in a 3-foot round culvert well-house delivers harvested rainwater through a drip irrigation system to our plants and vegetables. A hydrant delivers high-pressure rain water for those special summer gardening moments. And I ran a barely buried garden hose to the cistern for manual refilling with city water during our dry summer months.
Weekly Newsletter
Get building science and energy efficiency advice, plus special offers, in your inbox.
Lessons Learned
Like many designers and builders, I have suffered my own slow growth curve and mistakes around building balanced homes: homes that optimize energy performance, spacial function, and artistic form.
My most recent passion is Germany’s Passivhaus approach, for which I should become a certified designer by next month. My current favorite wall system is a thermal-bridge-free, airtight, high-performance wall consisting of a two-by wood-framed structural inner wall that bears on a raft slab, sheathed to be airtight, and including TJI studs resembling Larsen trusses. The entire wall assembly is then insulated from both sides.
Our home doesn’t have this gorgeous wall system, because I didn’t know about it when we remodeled, which leaves my home, much like me, with room for improvement. But I guess this is also pretty much where I am happy to be.
General Specs and Team
Location: | Santa Fe, NM |
---|---|
Bedrooms: | 3 |
Bathrooms: | 3 |
Living Space: | 2400 |
Cost: | 250 |
Additional Notes: | Completed August 2010 - Excellence in Green Remodeling from Hacienda's Parade Of Homes (2010) - Best Design from Hacienda's Parade Of Homes (2010) - Exemplary Site Utilization from the New Mexico Green Building Council (2010) |
Architect/Designer/Builder: Michael Percy Grant, Percy Home Design, LLC Structural Engineer: David Grabiel, QPEC
Construction
Roof Type 1: R-49 (torch-down roof over 7" polyiso rigid, unvented)
Roof Type 2: R-56 (standing-seam metal over 2" polyiso over 12" TJI w/ cellulose, unvented)
Walls Existing: R-10 to R-15 (plaster/stucco over 2-3" polyurethane spray foam over 14" earth adobe)
Walls New: R-29 (James Hardie clapboard siding over 2" XPS over 2x6 @ 24 o.c. w/ cellulose)
Floors, existing: 8" inaccessible & uninsulated dirt crawl space, old vents sealed up, exhausted by HRV
Floors, new: R-10 (Concrete slab over 2" XPS throughout, isolated from stem walls for thermal break)
Windows: Serious 725 series windows w/ suspended film glazing (U-0.16) and Pozzi wood-clad windows (U-0.28)
Energy
Boiler: Laars Endurance unit for DHW and space heat combined
Heaters: Myson hot water radiant wall heaters
AC: None needed
Energy Specs
Passive solar: 250-sf sunroom oriented 16º east of south
5" black slab fully isolated from soil and stem wall by 3" rigid XPS
12" cellulose ceiling plus 1.5" polyiso for R-52 roof
Water Efficiency
Laundry hoist: Rack that hoists to the ceiling on pulleys to dry clothes; also humidifies our room in our dry climate (see photo)
Rainwater cistern: 1,750-gallon buried tank collecting from 1,500 sf of roof, distributed by a Grundfos pump to drip irrigation
Graywater: Two graywater lines from half of kitchen sink and from master tub, with 3-way diverter valves to feed either landscaping or city sewer in winter
Indoor Air Quality
Whole-house mechanical ventilation: Ultimate Air RecoupAerator HRV runs full time (HRV both provides fresh air and exhausts radon from dirt crawl space)
0 Comments
Log in or create an account to post a comment.
Sign up Log in