TJI stud bays vs double stud wall

I would like to hear from the community comparing and contrasting the use of 12″ TJI studs to a 12″ double stud wall (not staggered). Assume (for the sake of this discussion) that the TJI studs will pass code in your locale. My main questions are as follows:
Is the thermal bridging from the OSB web significant when compared to a double stud wall?
Does the gap between 2×4’s create a difficult insulating scheme compared to individual cavities when using dense-pack cellulose?
Would using TJI studs provide more simplicity/speed when framing than double stud walls?
What is the lumber usage comparison between the two, does one use significantly less wood?
Any other thoughts, concerns, or difficulties for either system would be highly appreciated.
Thank you
Dylan
Mountainous 4A with some high wind zones
GBA Detail Library
A collection of one thousand construction details organized by climate and house part
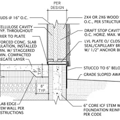
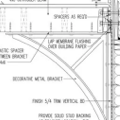
Replies
Dylan,
Having built many double-stud houses but none with TJI walls, I can only guess.
TJIs would likely save labor but cost more in materials, so it's not clear where the cost comparison would end up. I can imagine it being quite difficult to tip up a 12" TJI wall, where double walls are typically raised separately and involve conventional building practices.
The OSB web should not be a significant thermal bridge and the whole-wall R-value will likely be very similar. But I don't trust OSB as a durable material and would never use it for sheathing, roof decking or subflooring. It also has higher embodied energy as well as phenol-formaldehyde resins.
If you know the techniques, I find it's easier dense-packing an open double wall than isolated stud cavities, as I can install a lot of material from one spot. Also, a double wall allows wiring and mechanicals to be installed with no drilling - TJI's would require extensive drilling in isolated locations so as not to weaken them structurally (though this is less of an issue in a vertical orientation).
It's been done with TJI's, but it's done a lot more often with double studs, and I've found that a Riversong Truss wall is easier, less costly, more resource-efficient and more energy efficient than any other such deep-wall system.
Differences in framing are greatest at the openings and corners. Double frame wall details I imagine are a little easier.
Based on the concurrent 'thermal bridge' thread in the Q&A this is an interesting comparison. I would expect the TJI wall to have a slighter higher whole wall R-value (less insulation displaced) but have a worse thermal performance because of the thermal bridging. Significantly less? Likely not, but I'd be interested to see it modeled.
As RRiversong points out OSB is more prone to moisture damage. I also try to avoid it for the applications he notes.
Initially OSB was considered a resource efficient material because it utilized scrap wood. Demand is high enough now the OSB manufactures do use virgin wood, likely rapidly grown plantation trees.
In terms of appropriate resource use its best to source from local, sustainable forestry practices even if it means using a little more wood. Engineered wood is manufactured by large corporations that often represent less sustainable forestry management.
Here is a case study of a house built with TJI walls - https://www.greenbuildingadvisor.com/homes/first-us-passive-house-shows-energy-efficiency-can-be-affordable
An important caveat is that if you walk into the local lumberyard you will find that they won't sell you TJI's to be studs. They say that they might be too "floppy" because they aren't designed for compression loads.
It shouldn't be that hard to find an independent engineer to stamp their use as studs, though. Katrin may have had to do just that. But the TJI manufacturer's engineers typically won't do it.
BTW a new company is supposedly ramping up production of foam sandwich boards that are the same strength and dimensions of 2x6's. I can't recall their name, but they are in Boulder, CO IIRC
Thanks guys for your answers. I have been considering a dbl stud wall for the house I'd like to build, but wanted to get other's responses to using TJIs.
Robert I like your Riversong Truss wall, but for some reason I cannot wrap my head around the necessary details to have the trusses envelope the rim joist when platform framed and resting on a basement wall (maybe I'm just tired).
When the non-load bearing wall is on the interior it makes sense to me, but when I move the load bearing wall to the interior it is just to the inside of the basement wall. Do you have to move to a 12" basement wall as well, or can the bearing wall not be located directly over the basement wall. My years as a framer tell me that is just wrong, but from an engineering perspective perhaps it doesn't matter. If you could provide any links to appropriate construction details I would greatly appreciate it.
Thanks
Dylan,
There are many ways to do this. If you're insulating an 8" foundation on the outside with 2" of foam board, then the inner wall is partly over the foundation and the outer framing will cover the exterior foam. You can support the exterior framing on an extended PT plywood subsill.
This system can be done either with a truss wall or with a double wall system in which the inner wall bears the floor assembly and the outer wall bears the roof. The best approach depends on your design.
If you haven't yet poured the foundation, then the ThermoMass system, with up to 4" of XPS centered in the concrete wall, creates a 12" thick foundation with 4" of concrete on each side of the foam. This is perfect for a double wall frame and offers almost the same dynamic thermal mass advantage as exterior insulated concrete without exposing the foam board to UV, insects or mechanical damage.
That foundation allows the inner wall to bear the upper floor while the outer sheathed wall bears the roof load. I just had a house I designed built like this for a client in VT.
Hi Robert,
Thanks for the section views. I appreciate your approach and your distrust of OSB. I feel similarly. One question always comes to mind when I see double stud wall designs and I am hoping for your opinion. Do you worry about condensation on the inside of the cold plywood sheathing? Also, do you try to establish a vapor retarding or air retarding layer at the interior, at the drywall for instance?
I have read too many pieces by the Building Science Corp folks not to wonder about think walls and cold exterior sheathing. I know Mark Rosenbaum builds houses with double stud walls and seems to feel they work fine. I have also seen some closer to where I am located (in the pacific northwest) where 2" of rigid insulation was added to the exterior. What is your approach to moisture and air when you use double stud walls?
I mean, "about thick walls..."
Thanks Robert, for the detail drawings. I am in very early planning stages, don't even have the land yet. I've been designing my house for a number of years now and have several different floor plans for different possible site topographies and solar orientations. Now that we are (hopefully) with in a year or two at most I am am making decisions about the various system choices. So that once we have purchased land I can begin drawing detailed plans in earnest.
I intended to build as much of the house as my skills and knowledge allow, i.e. I will contract the grading, excavation, basement walls, plumbing and electrical. I want to do much of the work myself; 1 because that has always been a goal in my life and 2 in order to reduce costs as much as possible. Concerning the foundation walls I haven't obtained any preliminary estimates in order to decide if a ThermoMass, Superior Wall, or other poured wall would be more cost effective than contracting a traditional block wall and then I build the insulated interior wall.
By the way my first choice for a wall system was a modified post and beam frame with straw-bale infill. However I find it unlikely that I could obtain a construction loan for that system. Permitting wouldn't have been too big a a struggle here in Asheville, NC considering there have been other projects in the area that have been constructed.
J Chestnut,
When I've set up two identical width clear walls (11 1/4" to match TJI depth):
TJI wall (24 on center) = R-40
Double stud 2x4 wall (16 on center) = R-37.1
Spam filter won't let me post detailed breakdown of walls, but they're both cellulose dense packed.
Christopher,
Every well-insulated house requires an air barrier and a vapor retarder. I use the Air-Tight-Drywall system with vapor retarder primer. Every new house also requires mechanical ventilation to control humidity and air quality.
With controlled indoor humidity, a vapor retarder, an interior air barrier assembly, and dense-pack cellulose insulation which inhibits air flow and easily stores, buffers and redistributes moisture, and an exterior "skin" that can breathe, moisture accumulation in the sheathing layer is not a problem.
I prefer sawn lumber sheathing over plywood, since it breathes better, and #15 felt WRB over housewrap since it also transpires moisture better. And I always use wooden siding with a solid-color latex stain for durability and breatheability.
Moisture accumulation in the sheathing, particularly the all-too-common OSB, is a problem only if the sheathing is warm enough to generate mold or decay organism growth. The "warm sheathing" approach maintains perfect biological growth conditions if the sheathing should ever get wet. Cold and wet is not a problem - only warm and wet.
Dylan,
A block foundation is not as durable as a well-designed concrete foundation. You'll probably find that material costs are roughly the same for ThermoMass or block with interior insulation. If your basement will be living space, then you can't do better than ThermoMass. I'm not impressed with Superior Walls (with their steel framing and caulked joints) and the shipping of such heavy materials is not very green. I recently discovered ThermoMass and, if a full foundation is necessary, I think it's unbeatable for strength, water sealing, insect proofing, thermal mass - and it's perfect in the 4"/4"/4" configuration for a 12" thick wall.
Thanks again to everyone who weighed in on my questions, and also for all other input.