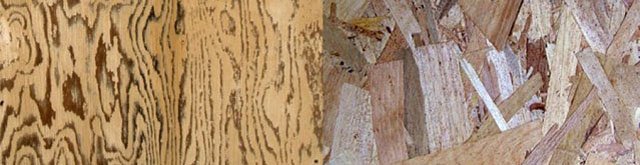
Although skeptical builders avoided oriented strand board (OSB) when it was first introduced commercially in the 1980s, today it dominates the U.S. sheathing market, far outstripping plywood with about 64% of sales. Improved resins, better water-resistance, and especially lower costs have helped make OSB the first choice for many builders even though plywood production can be counted in the billions of square feet annually.
From a structural standpoint, OSB and plywood share many performance characteristics and can be used interchangeably in a given application. Both are engineered wood products. “The amount of wood and the equipment to process them is a little different but it’s still the same basic concept,” says Dr. Joseph Loferski, a professor in Virginia Tech’s Department of Sustainable Biomaterials. “You’re going to take a tree, chop it into smaller pieces, put glue on it, and glue it back together. That’s basically the process.”
In comparing these two panel products, many of the fundamentals haven’t changed much since Sean Groom took a deep dive in this article for Fine Homebuilding magazine back in 2005. Yet the question of which one is better still pops up, especially as the dynamics of building assemblies change. Tighter building enclosures and more insulation have made builders more sensitive to the nuances of moisture management and air control. Those focused on sustainable design are starting to ask questions about embodied carbon—a topic that wasn’t on the radar a decade and a half ago.
Water-resistance is still a factor
How these panel products react to water was, and is, a key difference. Plywood is a sandwich of thin plies of wood, with grain direction alternating 90 degrees from one ply to the next. OSB is a mat of wood strands compressed under pressure and heat into a…
Weekly Newsletter
Get building science and energy efficiency advice, plus special offers, in your inbox.
This article is only available to GBA Prime Members
Sign up for a free trial and get instant access to this article as well as GBA’s complete library of premium articles and construction details.
Start Free TrialAlready a member? Log in
15 Comments
The link for Fine Homebuilding magazine didn't work for me.
Its also worth noting that the small Huber study on the airtightness of the OSB was done to ACH75 -ACH300, and the Code requirement for airtightness is in ACH50. Kind of a dubious "marketing" study if you ask me. Its a shame, that comparing apples to oranges get so much interest.
For what is worth, many of us use OSB in our building assemblies, paying special interest in sealing details to achieve consistent low numbers, from .6ACH50 to 1ACH50.
Armando,
I fixed the link. Thanks for letting us know.
Hey Armando--I don't know if the FHB article had a units error, but the GBA writeup uses the correct units--50 to 300 Pa (not ACH 50), which is the kind of pressures you need to get a measurable signal out of something like OSB.
"Initially, the study was designed to measure the air permeance of three types of sheathing: 15/32-in. plywood, 7/16-in. OSB, and 7/16-in. Zip. Phase 1 of the project was to measure permeance and find out what effect wetting and drying cycles would have on them. They used a standard testing method (ASTM E2178) to check air-leakage rates under pressures that ranged from 25 to 300 Pascals (Pa).
What constitutes an air barrier? For purposes of this study, RDH used a standard criteria of 0.02 liters per second per square meter at 75 Pascals of pressure (lps/m2). If a material allows more air than that to get through, it’s not effective as an air barrier."
@Kohta – I do know that the ASTM test need to be conducted in a controlled environment at 75 Pascals, but real world is another thing, as the code requires testing at 50 Pascals. Not only is that, but to showboat tests at 300 Pascals about fun or shock and awe, its another thing. In real world, 300 Pascals maybe during a hurricane or tornado situations.
Even though OSB is NOT sold as an air barrier, IMO, with a good sealing detailing, it works really well, and many of us have proved that on the field for many years. What I opposed to is the exploitation of “marketing” tests to sell products. I suppose those companies think we all have “stupid” or “sucker” written on our foreheads. Just read some of the comments on the original blog.
Awhile back, I went to a field trip where they show an air leakage test done on a house. They actually created two plastic covered areas, similar to the picture bellow, one with tape on the OSB seams and one without. I recall that to get the plastic to bubble up like the picture, the ACH had to be ramped up really high, never seen in real conditions.
Armando, as we've discussed before, I have seen with my own eyes a new house with commodity OSB as the air barrier where we could not get below 1.0 ACH50 due to air leakage through the OSB. We switched to ZIP sheathing and routinely tested at or below 0.4 ACH50, using the same details. I know it's not a common issue, and 1.0 ACH50 isn't bad, but air really can leak through commodity OSB. Apparently it's likely related to the aspen wood chips used in northern states vs. the SYP chips used in southern states.
Let’s be careful not to see the forest for the trees. The Code does NOT require testing of a product or specific material. It does require testing for the Building Thermal Envelope... at 50 Pascals.
N1102.4(R402.4)Air leakage - The building thermal envelope shall be constructed to limit air leakage in accordance with… See N1102.4.1.2(R402.4.1.2)Testing.
No, but many of us use sheathing as the primary air control layer so it's relevant information. That's not to say that OSB is a bad material or should not be used, just that if you are trying to use it as your primary air barrier, there is a chance you won't be happy with the results.
"Asked whether using OSB is any riskier than using plywood in a higher-performance wall assembly, Kohta Ueno, a senior associate at Building Science Corp., said it’s easy to generalize."
Based on the subsequent quote, I think there's a "not" missing from the end of that sentence.
Great article, Scott. If you run a BEES analysis between OSB and plywood, the environmental impact of OSB is significantly greater than plywood. BEES, or Building for Environmental and Economic Sustainability, a software developed by NIST to evaluate the environmental impact of comparable building materials, takes broader criteria than carbon.
Fernando, that is interesting.
My first reaction would have been that OSB is easier on the environment, compared to plywood. Both use adhesives, but osb can salvage more wood per logs of varying quality, right? With fewer plywood quality logs becoming available each year (large assumption on my part), does the comparison really matter if plywood becomes limited in availability?
Curious to hear more,
Thanks!
I have no personal opinion and had the same intuition as you. My comment is based on a LCA of the two under the broad NIST criteria, which takes into account multiple impacts. If you see the article I linked, you may an explanation. I don't recall how much detail I got into--sorry, 65 yo.
Kyle, what I have heard from industry pros is that while in theory OSB plants can use slash and other low-grade material, there is not a system for trucking slash from the forest--the system is set up to move logs, so that's what gets used at the plant. I can't confirm that's the case but it makes sense.
There was a very interesting FHB webinar yesterday with a presenter from Trus Joist. He told us that Weyerhaeuser uses brand-spanking new harvested trees for all their products, and they won't use scraps from other places because they didn't know how those scraps were treated in previous applications or plants, and that any process to "clean" them would change the composition of the wood for their products.
Most excellent, Dudes! 😆
Locked in pricing for three projects. Ply was same price as the cheapest OSB... so Ply it is.
A life cycle analysis represents the best means to compare materials or products for relative environmental impacts. Using NIST's BEES program, I have compared the two, and OSB has a much higher environmental impact than plywood. In these things, intuition can lead to wrong conclusions. See https://www.greenbuildingadvisor.com/article/choosing-sustainable-building-materials
Log in or become a member to post a comment.
Sign up Log in