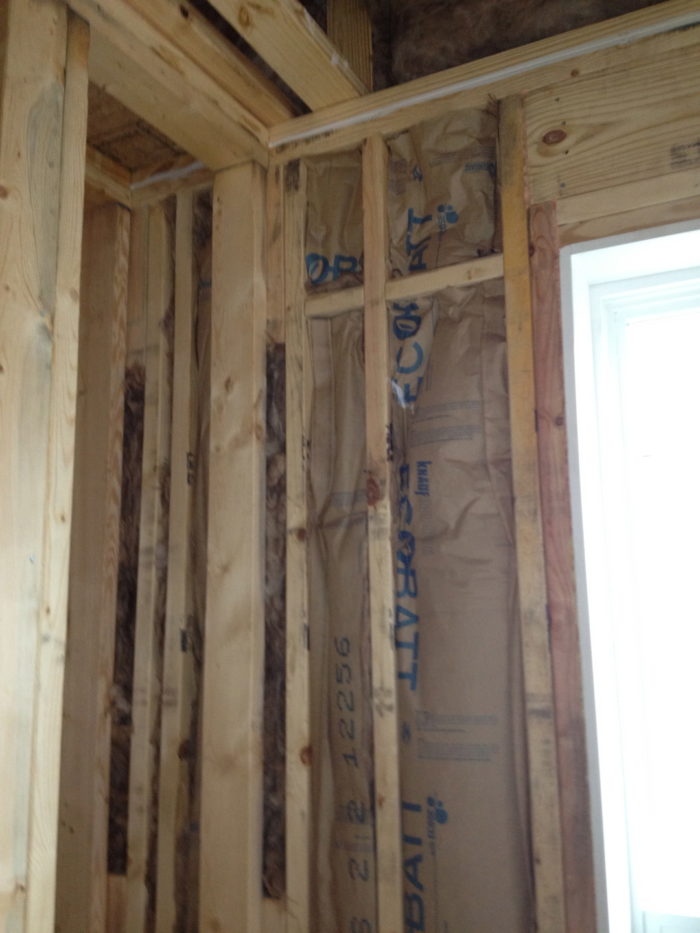
Image Credit: All photos by Carl Seville
Image Credit: All photos by Carl Seville The building inspector passed this installation with no air barrier behind the modular tub/shower unit even though it didn't meet the Georgia energy code requirement Another missing air barrier, also missed by the building inspector. An effort was made to install the required air barrier, but this rather large gap in the material makes it fairly useless. Although I prefer unfaced batts, even they can be installed poorly
I recently performed the pre-drywall inspection on a small home seeking LEED certification. The local building inspector had visited and approved the batts for covering up.
When I arrived, I immediately noticed that the kraft-paper-faced batts were installed, as is typical, at about a Grade III level, with significant gaps and compressions. (For more information on the definition of a Grade III installation, see Installing Fiberglass Right.) And because the facing was stapled to the studs, I couldn’t do a thorough inspection for proper trimming around wires and pipes without causing major damage.
I’ve come to the conclusion that in most cases, unfaced friction-fit batts are a better solution. They don’t have the gaps where tabs are stapled and can be pulled out for inspections without ripping the facing.
I don’t think I can count the number of times I have warned my clients about using batt insulation. I can explain the problems with installation, get eye-to-eye contact with their installing contractor who tells me that they can do Grade I work, but so far, in every case, the result is inferior work.
My guess is that the subcontractor doesn’t know, or care, about high-quality insulation, and even if they do, the need for it is never communicated to the field crews.
Most installers want to do a good job
Most workers on the job site are happy to learn how to install batts correctly. On a large multifamily building I certified under the National Green Building Standard several years ago, I worked closely with the field crews, showing them what a Grade I installation looked like. The result was consistently high-quality work, until they switched crews and we had to start all over.
Interestingly, it was the field crew, rather than the supervisors, who understood the process and worked hard to make things right. With the luxury of a long-running, multi-unit project, they could take the necessary time and develop a process for quality work.
Single-family homes, particularly one-off models, don’t offer the same opportunities. I arrive when they are itching to start hanging drywall and rarely willing to pull out some or all of the insulation unless absolutely necessary.
Inspectors aren’t helping
Even worse than the poor quality insulation on the LEED home were the missing air barriers. Neither the builder nor the inspector were aware of the current energy code requirement for rigid air barriers at all tubs, chases, soffits, and stairs on exterior walls.
The house passed and was ready for drywall with these noticeable code violations. Since they are required for certification, the builder installed spray foam and rigid barriers to correct the problems. What frightens me is that the inspectors simply don’t know the code well enough to enforce it.
I also perform code required blower-door and duct-leakage testing for code compliance on homes that are not being certified. I am not in a position of authority to enforce any other energy code requirements other than the testing, but in almost all cases, I see major violations in missing air barriers and poorly sealed ducts.
In re-reading my 2010 post on outlawing batt insulation, I am coming to the realization that not enough has changed, and I don’t expect to see much progress in the near future.
Weekly Newsletter
Get building science and energy efficiency advice, plus special offers, in your inbox.
24 Comments
Seeking LEED certification...really?
Carl,
Your comments about the batt installation are spot on. No arguement there. But I find it interesting that this house "was ready for coverup" as you state with what appears to be minimal air sealing as well. You pointed out the obvious lack of air barriers, but what about the lack of visible sealants? Nothing around header seams, multi stud seams, tees etc. Can't tell if the exterior wall top plate is "gasketed" or whether its simply caulk in the seam between the double plate. No visible top plate treatment on top plate of interior wall. Appears to be lots of extra lumber as well.
So, its more than just shoddy batt applications, its still about understanding the systematic approach....from the creation of the plan, through the builder, through the subcontractor and as you state, through the inspector. The weakest link in that chain, no matter where it is will always result in a less than desirable, or even intended result.
Even worse...
Even worse is in the South and SW, where many of the good Raters and Verifiers I’ve talked to said that they’ve lost builder clients to their competition who give a “passing” grade to substandard job performance by builders and subcontractors. I know RESNET and BPI are aware of the issue, but I’m not sure they’ve done much to stop it.
Philosophical question
Carl:
If batt insulation were introduced as a new product today, do you think it would even be allowed into the code?
What if its on fire?
The lack of a taking little time learning how to do it right for a 50+ year house is maddening, but the lead picture is also pretty scary to me. Isn't that oil covered paper "vapor retarder" on the batt an excellent fire chase? I can only shutter to think if a small fire started in the wall, say, oh in the electrical box.
Good points, all
Chris - there is caulk at some of the framing joints, but no gaskets at top plates. Since this house is seeking LEED certification, it only needs to meet ESTAR version 2 criteria. LEED won't require ESTAR 3 requirements until the next version (or possibly an interim energy efficiency upgrade this year). Most of the extra framing is due to the fact that the house was panelized. There were other issues with the panel manufacturer - they forgot to build a chase for HVAC and the energy heel in the trusses, further degrading the home performance.
MIke - I don't know enough about the code approval process to give you an answer, but it really troubles me that a product is so consistently installed so poorly that it doesn't perform as advertised and the fact that it also has to be combined with another product (air barriers) to work properly. The blame really lies with the industry and code enforcement - people aren't trained to do it right, the dollar rules so the lowest price gets the job, and few building officials enforce the energy code, letting people get away with substandard work. And finally, consumers don't know enough to ask for quality installations.
Andrew - They did seal all the chases so no kraft paper was left exposed.
Kraft work
From my awesomely vague recollection of code where I live the insulation kraft paper needs to be in direct contact with a fire resistant surface to reduce flame spread inside the wall cavity, same with blue and pink polystyrene. Is this not the case?
Money
It's all about the money isn't it?
Untrained crews, rushing jobs, bribing dishonest inspectors or just refusing to use the honest and knowledgable ones.
NYC enacted a nearly draconian energy code, requiring inspections and photographic documentation, only to turn inspection over to untrained lowest wage worker approve anything firms (and mind you, the same "inspection" firms that routinely faked concrete inspections - a life safety issue, pretty sure faking energy inspections won't faze them a sec.).
There are ways and means to enforce code, without much effort.
Use the professionals who are licensed and can be sued out of business for ignoring code.
Don't believe in professionals, and many are rubbish....
Then require the GC and or owner to post an energy bond.
Then simple thermal imaging / blower door test / energy audit of utility bills after the fact will tell the tale.
If the building fails, pull the contractors / owners bond as a fine, and revoke the certificate of occupancy until it's fixed.
It'll never happen though, as the real estate industry isn't going to let professionals, code, standards, quality and anything else that gets in the way of a fast buck.
by the way
Batt is the only really fire safe consumer accessible insulation, and given the increasing poverty in America, DIY is the only way most have to insulate.
I'm one of them.
and
I agree, unfaced friction fit batts make it LOTS easier to do the job right, and you're more likely to get a quality SEPERATE air / vapor barrier (depending). I do both, friction fit and barrier, it's recognition that 1. Humans make mistakes (or your QA may not pick up a crews bad work) and 2. Nothing lasts forever / is made perfect. You need redundency if you are serious about quality and not having problems biting you in the butt in 10 yrs.
Follow up on batt application quality
To: Carl Seville, Martin Holladay, Allison Bailles et al:
Gentlemen,
As an employee of Knauf Insulation, an international manufacturer of insulation products and insulating systems, I would like to commend your efforts and the work that you do for The Green Building Advisor. Many of us at Knauf Insulation are frequent visitors to the site and on an occasional basis, chime in to the conversations. Our interest was historically driven by insulation topics, but as we continue to focus more and more on building science and system solutions, a broader spectrum of your topics become more applicable to our business and our challenges.
In Carl’s most recent blog, he once again references his disappointment with the installed quality of fiberglass insulation batts. In the photo accompanying the blog, the product shown is manufactured by Knauf Insulation.
In the past, when such photos have appeared, some manufacturers have taken exception in any manner of ways, including letters from their legal representation. Knauf Insulation, on the other hand, chooses to respond differently.
There is no question that many types of construction products suffer from poor application techniques, with fiberglass batts being significantly referenced many times and on many fronts. However, there is also no question that fiberglass batts still represent the vast majority of insulation products used in the construction industry today. Having said that, Knauf Insulation sees these issues as directly related and is interested in raising the bar on the application of our products.
As a worldwide leader in the manufacturing of various insulation products, we are of course interested in the ultimate performance of our products. We are heavily invested in the newest manufacturing technology and dedicated to the production of insulation materials in the most sustainable manner possible. Knauf Insulation has led the industry in converting to bio-based binder technologies and currently leads the industry in POST CUNSUMER recycled glasscontent with a certified percentage of 58%.
While research, processes and technology are all important, Knauf Insulation recognizes that installed quality is equally as important to the ultimate performance of our finished products. In that regard, we are reaching out to you for your assistance.
We wish to extend an open invitation for any or all of you to join us for an open conversation at our corporate headquarters in Shelbyville, Indiana relative to the quality application of insulation products. Rather than sit idly by and hope that insulation contractors and inspectors do a better job of installing and inspecting, Knauf Insulation prefers to take a proactive approach and is interested in working with those such as yourselves who have been vocal with regards to poor workmanship, uninformed or poorly informed inspectors, the plusses and minuses of varying insulation products and or systems, and how those directly relate to the system performance of a structure.
The pulpits that each of you occupies has created for you strong voices in this ever challenging and continuously changing segment of the construction industry. Knauf Insulation hears what you are saying. We are confident that there are solutions that can and will include professionally installed fiberglass insulation products in a manner that results in the desired performance being achieved. So please consider joining us. Your contributions would be significant to our planning as we work hard at maximizing the investments that we have made in our company, our products and our customers in a manner that supports our company byline: Its Time To Save Energy!
I look forward to hearing from you and discussing this significant issue with you. We have some flexibility in our calendar and could very likely work around your existing schedules.
Sincerely,
Christopher P. Brown
Director of training and field support
Knauf Insulation North America
[email protected]
Cell: 317-402-1501
Office: 317-421-8473
Response to Chrisopher Brown
Christopher,
Thanks for the invitation. I'm not sure that I can make it to Indiana, but I'd be happy to speak with you by phone or communicate by e-mail. As you can imagine, I have ideas and suggestions.
I'm glad to hear that Knauf is willing to work with journalists and bloggers like us, rather than threatening us with legal action. It's a good step in the right direction.
Thanks, Christopher
For engaging in the conversation in a civil, rather than a defensive manner. I don't think that I can make the trip to Indiana either, but I am very interested in having a discussion about how we can make the situation better. I don't blame batt insulation manufacturers any more than contractors, installers, and inspectors, and even consumers unwilling to pay for quality work - everyone plays a role in poor installation quality. I am not sure that there is a manageable solution to this problem. It will take a major shift in perception in the marketplace - people need to understand that they must pay for quality work. It is certainly possible to install batts well, it's just that too much work goes to the lowest bidder with little in the way of standards or quality control. Insulators are often paid by the quantity they install with little oversight. Builders don't know or care if the quality is good, inspectors don't require quality work, and consumers aren't savvy enough to do much about it.
One thing that manufacturers might consider is to educate consumers, builders, and inspectors to help raise the quality of the work. In my experience, you often need to create demand for a product or service - something that takes time and money. A strong marketing campaign for proper building insulation may help transform the marketplace towards better performing buildings. Then again, I may just be naive.
Some ideas for Knauf
Christopher,
As you know, that status quo isn't working. The vast majority of fiberglass batt jobs are a disaster and are an embarrassment to the industry. These installations don't provide the R-value that customers expect and deserve.
If Knauf is willing to step up to the plate and acknowledge that the status quo isn't working, that would be great. We can't move forward without making a clean break with the past.
Here are some suggestions -- ideas to get you thinking.
1. Many industries sell construction products that are difficult to install. There is a standard solution to this problem: require that the product can only be installed by trained, certified installers. These certified installers would need to be trained at your factory. If installers fail to follow best practices, they would lose their certification.
2. Another approach: stop selling batts, because they are so difficult to install. Instead, focus on blown-in fiberglass.
3. If you want to continue selling batts, change the packaging. Every package should have a warning in huge letters: "This product will not work unless it is installed in direct contact with an air barrier with carefully sealed seams. The integrity of the air barrier should be verified with a blower door."
4. Start a national advertising campaign that frankly admits that current practices aren't working. Make a public pledge to start fresh with a new approach. Here's the slogan: "Two air barriers, no voids, no compression - or fiberglass batts won't work."
Those are just some off-the-cuff ideas to get the ball rolling.
Blaming the product for bad installation
Carl,
You said: "I don't blame batt insulation manufacturers any more than contractors, installers, and inspectors, and even consumers unwilling to pay for quality work - everyone plays a role in poor installation quality."
Why blame fiberglass batt manufacturers at all? The deficiency is with the installers. There are plenty of jobs that have to be done right. Certified welding, ship piloting, and running locomotives come to mind as examples. All of the necessary elements of specification and inspection of insulation are in place, so there is no reason for the problem.
We have recently had discussions about spray foam in which it was acknowledged that a defective installation is quite possible and potentially highly problematic. However, I have never heard these installation pitfalls blamed on the product. Has anybody ever called for banning spray foam because it can be installed with defects?
Response to Ron Keagle
Ron,
You wrote, "All of the necessary elements of specification and inspection of insulation are in place, so there is no reason for the problem."
I feel that I should answer like Galileo, who, when ordered by the Pope to recant his statement that the earth orbits the sun -- and is not fixed as the Church maintained -- recanted, but then muttered under his breath, “Eppur si muove” (But it still moves).
"All of the necessary elements of specification and inspection of insulation are in place, so there is no reason for the problem." Yet we still have a problem.
Product vs Installation
Ron - The manufacturers do have some culpability in the problem with poor installation. While there are problems with spray foam, most manufacturers require their distributors to be trained and certified before they can install their products. Batt manufacturers could do a better job explaining proper installation than they do. I like Martin's idea of big warnings on packages, sort of like the required warnings on cigarettes. Batts do have installation instructions, but they tend to be hidden away and not emphasized. As I said in my response to the Knauf rep, a serious marketing effort to explain the value of proper installation to the industry as well as consumers would begin to create the demand for proper installation. We have a long way to go, but we have to start somewhere
The problem
Martin,
When I say the necessary elements of specification and inspection are in place, I only mean they are in place, so there should be no problem of inadequate quality due to a lack of oversight. But there is indeed a problem due to a lack of enforcement of specification and inspection. I certainly agree that there is a problem with installation. I have seen my share of bad batt installation. But my point obviously is that the problem is not the fault of the product.
Response to Ron Keagle
Ron,
Like Carl, I believe there is plenty of blame to go around.
The manufacturers are at fault for skimping on installer training, doing a poor job of package labeling, and for turning a blind eye to job-site problems. This attitude may have served them in the past, but they are currently suffering blowback. Fiberglass batts have a terrible reputation, and that isn't good for the manufacturers.
Insulation contractors are under competitive pressure, and I have sympathy for their dilemma. Nevertheless, the vast majority of insulation contractors don't follow manufacturers' recommendations when installing fiberglass batts -- and insulation contractors are to blame for this dismal situation.
General contractors are to blame when they sub out insulation work to the low bidder, and when they don't insist on top-quality work.
Most building owners don't understand these issues, but they should. They are to blame for their ignorance. If they are going to hire a builder or an insulation contractor, they need to study up on the pitfalls of insulation work and should insist on quality work.
Building inspectors are to blame when they don't enforce the code, which requires all building materials to be installed according to manufacturers' instructions.
Journalists are to blame too -- I'm one of them, and I cringe at the work of my colleagues. It took me 30 seconds to find this web site -- http://www.ehow.com/how_13050_install-fiberglass-insulation.html -- where some so-called journalist recommends, "Stuff scraps of insulation in any open areas where heat loss may occur."
Blame all around!
So why should insulation manufacturers care? They're just one cog in the wheel, right? Here's why: Carl Seville visits job sites, and he reports, accurately, that most fiberglass batt jobs are sloppy. If he wanted, he could name names. There's Bob the insulation contractor, and Fred the GC, and Mary the homeowner, and George the building inspector. So what? Even if all of them learned their lessons, and turned over a new leaf or got out of the business or were put in jail, the problem is bigger than all of them.
At the end of the day, Knauf should care. Their name is on the batts, and their name shows up in Carl's photos. And if the entire industry has a black eye, the manufacturers need to wake up and smell the coffee.
batt Insulation
At some point the General Contractor/Builder has to take responsibility. Pointing to the installer and inspectors sounds like a deflection of accountability. As builders, it's our job to teach (assuming we know) how to do things correctly. If the supervisory people responsible for this home were on site and engaged with the workers, this problem wouldn't exist. If it's not done poorly, it's time to look in the mirror and take responsibility. Batts are as good or better than blown products, when installed correctly, which is not rocket science. Poor installations are causing inappropriate knee jerk reactions, thus questioning if batts are okay. Poor management is responsible for poor workmanship, once that concept is accepted, the work will be better. Thirty five years building, but still showing guys how to instll batts, that's okay, because the end result is a good job, and that's what we need.
Fixing the problem
Martin,
I agree that if everyone is having so much trouble with batts that it is giving them a bad reputation, then it would behoove the industry to provide the best installation training possible. I do not know how much they do provide, or whether or not they are providing enough. Maybe the batt manufactures can tell us whether they think their installation message needs to be clearer in order to fix the black eye they are getting from bad installations. It would be an interesting question to ask them.
I would like to see the problem get fixed, and it does not seem like it would be hard to do. With the right training, understanding, and technique, there is no reason why a batt job should have any defect whatsoever. Once the manufacturer gets the instructions out to the installers, and the installers do the job correctly, that should put an end to bad batt installations. It seems doable to me.
Installation education
Carl,
It would certainly be in the interest of the fiberglass industry to detail the installation technique. Beyond that, you would still need to control the installation so that it conforms to proper practice. The reasons for bad installation of figerglass are varied. It would be worthwhile to deeply explore what goes wrong and why.
From the Design community
From the Design community, I stopped specking and using batt insulation over 15 years a go, period. Same goes for flex ducts, HVAC systems in unconditioned attic, wood burning fireplaces w/o doors, just to name a few as I’ve chosen to maintain good standards throughout. Most of my colleagues have sold their soul just to get the job; but not any different than the insulation Manufacturers, Builders, Retailers, Installers, Inspectors or Raters and Verifiers.
The easy answer...
... is to hire Rick Chitwood (who knows very well how to properly install fiberglass batts) to create a video detailing the process in different circumstances. Don't let anybody who buys batts leave the hardware store without a copy. Make it available in DVD and electronic formats so it's simple to share with the crew. Sponsor competitions for the best insulation job. Winner gets a free trip to Indiana. Problem solved!
Response to Larry Weingarten
Larry,
You wrote, "Sponsor competitions for the best insulation job. Winner gets a free trip to Indiana."
Good idea -- but the competition already exists. It is sponsored by Johns Manville, a Knauf competitor. I don't have all of the results, but here are some recent winners:
In 2007, the winner was Salvador Herrera.
In 2008, the winner was Ray Blackwater.
In 2009, the winner was Miguel Martinez.
And the prize is $10,000, which is much better than a trip to Indiana.
Solutions
Guys and Gals,
The problem is not about 'Blame'! Trying to decide who gets the black eye is a game and self defeating. We have a wonderful opportunity from Knauf for implementing some solutions.
Keep our eye on the ball - a solution!
I believe manufacturers are in the drivers seat! They have an ongoing concern about properly installing their product. If it keeps getting a bad wrap, people stop using it. So there is a vested interest in a solution that works and is effective.
Advertisements like a guy and his kids hauling a few batts upstairs and unrolling them. Using words like safe, etc - don't cut it. The ad is saying buy what you can afford and put it in. Save money, obtain comfort and safety.
Certified Installers, on site QA, Training are all a part of the solution. $10K prizes are a pipe dream and a marketing solution with a fixed price.
How about Training and certification of installers. Then offering a rebate for 'on site Third Party Verification to Grade I' ? Make the rebate in cash, or product or a future credit for material. Or a combination. Do not forget to include recognition as part of the Rebate.
You could deem some builders, contractors as trained or mostly trained. For example BPI and RESNET Energy Smart certified contractors.
Use the program to improve houses, Knauf has a great product for sealing top plates. Tie some of the rebate into that product. The manufacturer's ultimate goal is not just to stay in business, it is also to increase business.
Reality Check
Videos? Certified Installers? Competitions? How about a website or a diagram or an instruction guide or a youTube video? COME ON PEOPLE!!! You are talking about a product that is widely used, available everywhere, and used by an entire industry that is largely unregulated, unlicensed, and uneducated (in the formal sense). Moreover it is full of part time participants and DIYers.
I don't know what the solution is. If Knauf puts 'danger' labels on its product alone, then folks won't understand that the other batt products pose the same danger. If Knuaf aggressively runs an education campaign on the dangers of using batt insulation they will come under attack from their peers and it will hurt the sale of their product.
Knauff could try a warranty policy that guarantees performance if installed properly with limited results. Perhaps Knauff could partner with big box retailers like the Home Depot and Lowes and lumber yards to educate the public on the importance of proper installation of batt insulation. In my ideal world, you wouldn't be allowed to buy a window or a roll of batt insulation without a license and that license would require demonstrated proficiency at the installation and operation of that product. But as long as the teachers union continues to lobby against licensing and education for contractors, that isn't going to happen.
I'd love to hang out with the Knauf folks and talk about solutions. In fact, I'll even extend an invitation for them to send someone out to WinterCAMP this year to talk with some of the brighter minds about how they could improve their impact on the building community.
Log in or create an account to post a comment.
Sign up Log in