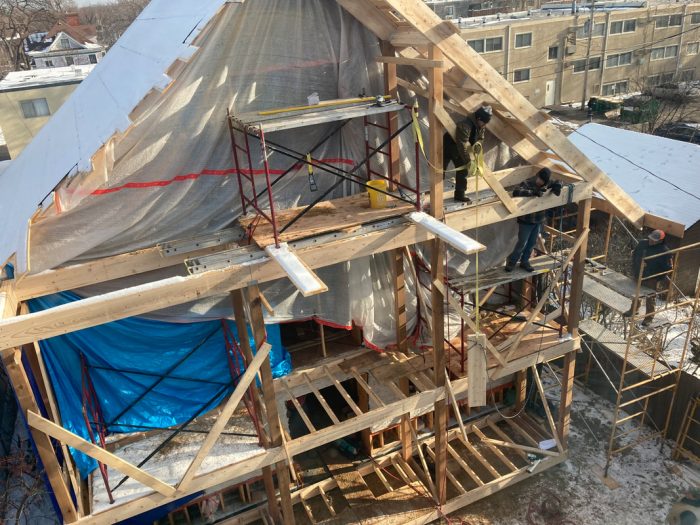
The most intuitive building systems are usually those that draw on hundreds of years of precedent. A slew of older but time-tested building techniques are in redux, albeit with some innovative twists, from mass timber to plant-based concrete alternatives to earth-based compounds. We can insulate whole buildings with fungus; we can create whole neighborhoods that act as carbon sinks. Anything new is old, only perhaps a bit more streamlined. This is certainly the case with strawbale homes.
In the Uptown area of Minneapolis, Minnesota, married couple Katie Jones and Peter Schmitt are nearing completion on their new 1,450-square foot, two-story home that has been insulated using nearly 600 individual strawbales and coated in three viscous layers of plaster, both inside and out. The striking home, designed in the style of carriage house-meets-Austrian ski chalet, begins as a traditional post-and-beam structure that is tucked away in the back end of the lot. Fronting the lot is an 1893-built three-story Victorian, also owned by Jones and Schmitt, where they currently occupy the third floor and lease the other two. Following a full-scale renovation of the nineteenth-century home, which included exterior asbestos abatement, air-tight insulation, solar panels, a heat pump conversion, and near total electrification, the couple became inspired to construct their own detached home that met the highest standards for energy efficiency and carbon reduction, both operational and embodied. In short, they wanted a Passive House.
Jones cites the importance of maintaining a light footprint and “being able to generate more energy than this house uses annually.” The home’s metal seam roof, which features dramatic three-foot long eaves (generous overhangs are essential for moisture mitigation in strawbale homes), will feature a diversified solar array comprised of Heliene bi-facial modules and repurposed Solar World mono-facial modules salvaged from the their property’s old garage. Collectively,…
Weekly Newsletter
Get building science and energy efficiency advice, plus special offers, in your inbox.
This article is only available to GBA Prime Members
Sign up for a free trial and get instant access to this article as well as GBA’s complete library of premium articles and construction details.
Start Free TrialAlready a member? Log in
6 Comments
Interesting project. While I don't think straw bale construction is going to take over the market anytime soon, it's nice to see examples of it being used. I have a few questions:
What are 1x10 roof trusses?
In the building section, what is the gap at the top of wall?
Straw bale buildings in a cold climate should dry to the exterior--are there any concerns or was anything special done at the stone (or fake stone?) cladding?
What is the foundation system?
Are they including hygrothermal monitors in the walls?
For what it's worth, it's wheat straw, not wheat-based straw.
Michael,
I've been in a couple of straw bale buildings and really like their feel. One thing I notice in write ups about them, which they share with rammed earth and Cobb dwellings, is that invariably a large part of the labour involved was supplied by either volunteers, or students of an alternate construction program. The economics of building with them seem to rely on that free labour, and it seems to me to be a big reason they don't even make the cross over into becoming a more mainstream construction method.
Hi Malcolm,
While there was overwhelming support from neighbors and local architects, students, etc. to participate in the community build portions, calling it "free labour" is a misnomer. Those who took shifts stacking bales or plastering first had to be trained on site by the owners (who in turn invested a lot of their time), then those volunteers performed small portions of the home. Most of the plastering was performed by a professional team at https://mcclellanexteriors.com, and the owners Katie and Peter shouldered most of the strawbale stacking and securing.
All that said, point taken about this not entering the mainstream anytime soon.
"Trusses" was a typo... meant to say rafters. Has since been fixed.
The gaps aren't actually there. The bales extend all the way up to the roof assembly. I believe the gaps are there in the elevation to illustrate that the eaves and the portion of the roof that extends over the 2nd-fl balcony are separate from the home's thermal envelope.
Nothing special was applied to the exterior plaster or (real) stone ... the only condition was the plaster had to be applied over a duration when the temp didn't go below freezing for 72 hours, which in Minnesota means summer months only.
Foundation is slab on grade, with radon protection layer below the slab.
There are 10 moisture monitors embedded in the walls. Moisture rates gradually dropped once the plaster fully cured and dried. The owners indicate that current readings range from 6% - 16%, which is well within the acceptable range to avoid mold.
Justin,
The roof is framed with trusses not rafters, except for the timber-frame overhangs. You can't use 1"x lumber for framing members.
I think Michael's question about the stone base was related to stone being a reservoir cladding, which will move moisture into the wall behind. Having no separation between it and the straw sounds problematic.
What is "an intuitive envelope"? How does it differ from others?
Thanks Justin. Reviewing the images, I see that Malcolm is right--the roof is framed with trusses, not rafters. To get R-70 with cellulose they must be at least 18" deep, or more if they also have ventilation (which they should, as cellulose is air-permeable) unless the roof is vented above the roof sheathing.
The stone worries me, as it is relatively impervious and will slow the wall drying to the exterior when it's cold out, but permeable enough to absorb water which will be drawn inward at times when air conditioning is running. But it's not very high so maybe the straw bales can still dry easily enough.
It's great to hear they they embedded moisture monitors and that the values seem low enough to be safe.
Log in or become a member to post a comment.
Sign up Log in