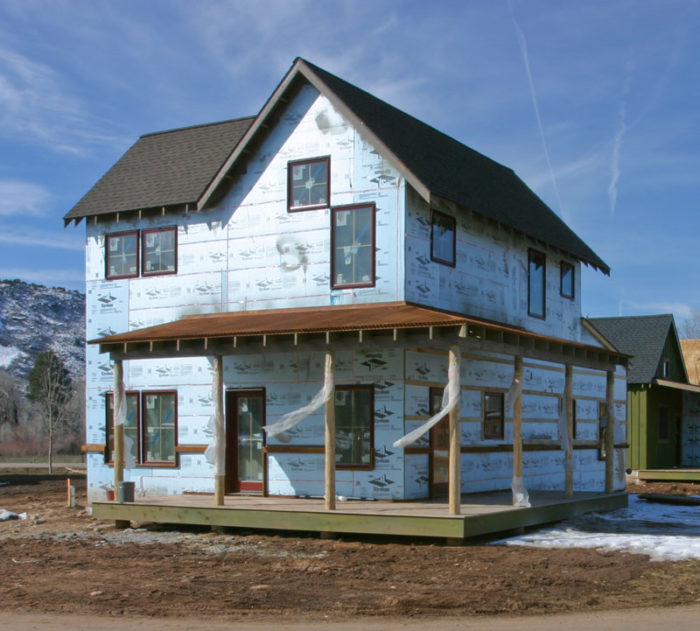
Image Credit: Daniel Morrison
Many builders add one or more layers of rigid foam insulation to the outside of a house to lower heat losses. Rigid insulation has an R-value of up to 6.5 per inch, but it also can be an effective vapor retarder.
Ed Welch touched off an extended discussion in the Green Building Advisor’s Q&A section when he asked whether the foam would trap moisture inside walls, creating mold as well as the potential for structural decay.
His concerns seem well placed. In a cold climate during the heating season, moisture vapor inside a building is driven outward into exterior walls. When it reaches a surface that’s below the dew point, the vapor condenses into a liquid. That surface is typically the back side of the exterior sheathing.
Rigid foam board, especially foil-faced polyisocyanurate, creates a vapor-impermeable barrier, so the wall would have limited drying potential. Even more permeable types of insulation, such as expanded polystyrene, are vapor barriers when the installation is thick enough.
No one argues this point of view more forcefully than Robert Riversong of Vermont, who has been building high-performance houses for many years. Riversong notes the exterior skin of a house should be at least five times as vapor-permeable as the interior. Yet 2 in. of extruded polystyrene insulation — the amount it would take to keep sheathing above the dew point in a cold climate — create an effective vapor retarder.
Further, Riversong argues that long-term studies have shown foam-clad walls have no way of drying out in the event of even minor rain penetration. He suggests there are better ways of increasing R-values and reducing thermal bridging, such as double-framed walls or using foam board on the interior.
He also favors cellulose insulation and other natural materials over petrochemical plastics because they are more…
Weekly Newsletter
Get building science and energy efficiency advice, plus special offers, in your inbox.
This article is only available to GBA Prime Members
Sign up for a free trial and get instant access to this article as well as GBA’s complete library of premium articles and construction details.
Start Free TrialAlready a member? Log in
110 Comments
Exterior foam issues...
Your last statement is the key to it all. You can have almost any building system, whether Persist, Remote, Larsen, SIPs, ICF or stick frame, in any climate zone and as long as is designed, detailed, planned and executed correctly. You should not have problems with moisture and/or mold as long as your humidity and ventilation are controled as part of the overall system of the house. Many builders prove it every day around the country. Thank God for Building Democracy.
wufi
we ran wufi models for seattle w/ a rear ventilated rainscreen over 'outsulation' and there were no moisture issues in the wall assembly.
when that assembly was moved to anchorage, moisture build-up in the wall was greater than seattle, but still very minimal and shows to dry out.
retrofits vs. new construction
Scott,
Thank you for this excellent summary of the related issues of thermal and hygrothermal performance including the subtle differences in viewpoint from the people whose opinions we all follow closely.
The principles for low risk, high performing wall assembles, for new construction at least, seems to have been firmly established for all climate regions.
I work in a cold climate more frequently with retrofits then new construction where the opportunities to add insulation to the thermal envelope are typically from the outside in tandem with re-cladding the home. Properly detailing the walls according to the principles outlined above can quickly become cost prohibitive if we need to remove insulation from the stud cavity and remove an interior vapor barrier (which for my jurisdiction may be in violation of code).
I'd like to see a discussion focused on the challenges posed by retrofits per era of construction and per climate region.
Market penetration of exterior foam sheathed walls
A representative of a major building material company shared some independent research he commissioned regarding the numbers of builders using rigid foam on exterior walls. Custom, spec and small scale home builders had the lowest use of rigid foam on exterior walls at between 5% and 10%. Production builder use is in the 10% to 15% range. And generally when production builders incorporated rigid foam, it was part of a division-wide practice implementation.
While I think as Scott notes, more builders (and renovators doing exterior work) are incorporating rigid foam, it's still not a widespread practice. It will be interesting to see how fast and deep the move to incorporating rigid foam is over the next 5 years.
documented cases?
Does anyone have any actual documentation (photos, moisture meter readings) of water problems caused by continuous exterior rigid foam insulation--not including the well-documented issues with faulty EIFS installations--that they could post, along with their hypothesis regarding the cause of the problem?
Outsulation
I have been thinking for years about how to add insulation on the OUTSIDE of stone walls of my house here in SW France. What problems can I anticipate that are different to those for standard housing in the US & Canada please? It is so easy to add insulation outside of thick and uninsulated stone and occasional cement block that is coated with standard crepis skin. There is no insulation in the tiled floor and only standard fibre-glass in the roof. But ..?
Response to Richard Bill
Richard,
Many European contractors are experienced at adding exterior foam insulation to existing masonry buildings. These systems usually employ synthetic stucco (EIFS).
Instead of installing rigid foam to the exterior masonry, it's also possible to install metal or wood studs, hanging from the roof overhang or attached (with standoffs) to the masonry. Then closed-cell spray polyurethane foam can be installed against the exterior of the masonry and between the studs.
It's very hard to retrofit insulation under an existing slab-on-grade floor. However, it's certainly possible to retrofit vertical rigid foam board at the perimeter of the slab. The foam should extend below grade.
Outsulation
Foam below grade creates space tor termites, does it not?
Response to NewHammer
New Hammer,
Whether or not below-grade foam creates problems with termites depends on your climate. Where I live, in northern Vermont, there are no termites, so foam is routinely used to insulate the exterior of foundations. In other regions of the country, codes limit the use of exterior foundation foam.
Richard Bill is writing from southwest France. I don't know if southwest France has a termite problem.
Termites
Yes. We do have a termite problem in the region; considerable, together with other cellulouse eating insects. Something else to think about, even on a stone building but with oak and other older wood interior and roof beams.
Thanks.
Rigid board on interior?
Riversong suggests using foam board on the interior. I've got a case now where we won't be changing the siding, but are down to the 2x4 studs. Would interior foamboard be the way to go? Portland Oregon area.
Rigid foam on INTERIOR?
I too would be highly interested in this technique. I am in the process of desiging a new home with rainscreen walls, wet blown cellulose and air tight drywall (no poly). In order to eliminate or greatly reduce thermal bridging I am contemplating INTERIOR foam board over the studs.
A variation would be to install strips of foam board over the studs and have the insulation contractor blow wet cellulose flush with these strips. This option would alieviate concerns about covering the entire interior surface with a low perm membrane.
Vancouver Canada.
What about a house wrap over the foam board?
Just curious why no mention of using a house wrap over the foam board was not considered. Wouldn't a permeable house wrap help the wall system dry out and prevent moisture issues?
Specialist architecture engineer
It's a very important report. I live in Riyadh City. I notice in many building that architects use outdoor or exterior wallpapers with special textures. I think by experience that's a weak solution. It's better to use natural building materials -- texture like stones or marble -- or eco green products in painting or any new facade building materials in new technologies world.
Interior foam
My only concern with interior foam sheathing is that the entire wall cavity would potentially cool to a dew point, thus making condensation a larger problem than with outside foam sheathing, no? I understand Mr Riversong recommends a much higher permeance to the outside, but with a well exceuted and sealed exterior foam, is there really a concern if the proper thickness is correctly installed and the interior humidity levels are adequately controlled in the winter months?
Response to B Mac
B Mac,
Adding a permeable housewrap on top of exterior foam insulation will not improve a wall's drying ability. The reduction in the wall's drying ability is due to the low permeance of the foam layer. Adding a higher permeance layer on top of the foam has no effect on the permeance of the foam below the housewrap.
Foam, details, Lstiburek, and dew point
There is no argument that there can and probably will be problems with exterior foam if the details are not right, but that is not a persuasive reason not to use this highly effective strategy.
Look at it this way: you can fall in love, get married, and have children. There are a whole lot of details in that process that can can cause problems, but that doesn't mean that people shouldn't fall in love, get married, and have kids.
It's a good rule of thumb to follow Lstiburek's recommendations. He's the first to tell you so, of course, but the kicker is that he's usually right. I wish my financial advisor was half as reliable.
The wall only has to dry to one side. I'd worry a whole lot more about vinyl wallpaper than about exterior foam.
Finally, if you want local help and support, track down your Dow rep. They have a lot of excellent information on this assembly.
Leave the exterior foam's
Leave the exterior foam's seams untaped in conjunction with a permeable housewrap. This allows you to breathe through the seams as well as get the advantages of having a permeable membrane. I've heard multiple building scientist say they like this method with the wrap under the foam so you can flash/detail the windows/doors properly.
Another disadvantage of the exterior foam is that you are completely reliant on tapes and flashing that is not technically properly shingled vs the traditional method of flashing below the WRB wrap and directly against the sheathing; ASTM D2112 flashing method I do believe. This should cause concern.
basic prinicples
My experience brings 2 major principles to follow and then almost any wall system will work in any climate. 1 - Keep the vapour barrier on the warm side of the insulation. Note- your building may shift so if you are using your spray foam insulation as a vapour barrier - you may want a back up when it cracks. 2 - Use an "air" barrier on the exterior of the insulation - not another vapour barrier like house wrap (not all house wraps -but do your research....) Walls need to breath!
Response to Anonymous
Dear Anonymous,
Your rule, "Keep the vapor barrier on the warm side of the insulation," is a poor one.
First of all, vapor barriers like polyethylene have largely been replaced by vapor retarders like kraft paper or paint.
Second, even if I follow your rule and install poly on the interior side of my insulation (assuming the work is performed in January) -- what happens in July? Surprise! My poly is now on the cold side of the insulation. Once inward solar vapor drive begins sending exterior moisture into my wall cavity, I suddenly realize that my poly is soaking wet.
It's a simple rule, but it is wrong. There's no substitute for a full understanding of the thermal and moisture performance of any suggested wall assembly. Your simple rule won't work.
Anonymous didn't say anything about poly.
Using your argument, no using foam (or anything that acts as a vapor barrier) any where unless foam is the only barrier, all the way through. Are you saying no foam? If so, why do you suggest foam? Most foam is effectively a vapor barrier.
vapor barrier
Has anyone used or seen research on the working longevity of the "Membrain" product?
Foam strips on studs
John's idea from June 28th suggested attaching foam strips on the outside of the wall framing before the sheathing goes on. I would think this would lessen thermal bridging by creating a thermal break where the studs touch the sheathing and give more space for cellulose in the cavity plus allow the wall to breathe normally. I decided to abandon the exterior foam idea on our new house after getting sticker shock on the cost of the foam and the labor. I had read the Robust Walls article and calculated that we would need 1 1/2" of XPS foam to prevent 98% of condensation. Now, I wonder how this "strip" method would work and if it could be a more affordable method?
Would I have trouble with condensation around the foam? Will I not be able to keep the dew point from settling in the walls and therefore between the studs / foam / sheathing where I could get rot? what about using EPS foam which is able to "breathe" and therefore dry with the wall assembly when it does encounter condensation?
Thanks John - I think it's a great idea but I want to get more opinions before I do it!
correction
I stand corrected -- John asked about interior foam -- but I want to know what others think about the same principle but on the EXTERIOR side of the stud walls?
Laura T be careful
Putting foam on the exterior of the studs prior to sheathing may mean that you do not properly brace your walls, as it will be difficult to provide adequate lateral bracing as required by code, unless you employ another method of bracing.
"outsulation" complexity
The theory seems great however some Issues to consider with outsulation:
a) The location of door and window openings with in the wall assembly are tyipically in line with the structural wall (ie studs). This can create diagonal thermal bridging issues and extensive flashing compexity.
b) Supporting exterior finishes on the outside surface of the insulation can be problematic.
c) Relying on the walls to dry from the inside by reducing or removing the vapour barrier, is highly problematic because wall finishes vary with their individual vapour resitance capacity. These finishes vary through out the life of the building and are beyond the control of the building designers. i.e. paint vs vapour barrier paint, Wall tile etc.. If we are relying on the wall to dry from the inside, at some point in the life of the building these walls may not opperate as designed simply because a tenant may - unknowingly - paint the walls with a vapour resistant paint of decide to tile a wall.
Outsulation
We have completed a seniors care facility in Ucluelet, British Columbia, Canada that uses this system of outsulation. The additional coats were justified because of the cold, rainy and highly humid coastal enviroment. The project was compeleted in 2005 and is so far working well, however it is controlled in terms of the internal wall finishes.
Response to Nathan
Nathan,
Your concern that an occupant's decision to paint the interior of a wall with vapor-retarding paint may lead to wall failure is misguided.
Building scientists recommend the use of vapor-retarding paint precisely because it is forgiving. It satisfies ignorant building inspectors without unduly limiting a wall's ability to dry to the interior.
One interior finish that you didn't mention -- vinyl wallpaper -- is a much more serious problem than vapor-retarding paint. Hundreds of hotels in the U.S., especially in southern states, have mold-factory walls due to two factors: vinyl wallpaper and air conditioning. This problem can be extremely expensive to remedy, because of the extent of the required demolition.
Outsulation - comment reply
Martin,
Yes - good comment regarding VP paint - VP paint perhaps is not a good example to isllustrate the point. In our Ucluelet project we infact used vapour barrier primer. Your vinly wall paper example is better.
Cavity insulation causing problems.....
As the first comment advised, I think we all need to remember the "house as a system" approach. Various building systems will work correctly in various climates, as long as someone is educated in building science. And, unfortunately, there are very few, if any, silver bullets that can be applied universally. And we need to stay very aware of relative humidity, dew points, and ventilation as we tighten homes, increase insulation levels, reduce thermal bridging, etc.
Scott, one question I have relates to this statement:
"Ironically, the use of insulation in wall cavities along with rigid foam on the building exterior can actually increase the risk of condensation if the wall system is improperly designed. The reason is that cavity insulation slows the flow of heat outward and has the effect of keeping the back side of exterior sheathing cooler, thereby making condensation more likely."
Makes sense and I have heard Martin mention it as well. But how can we calculate these wall thicknesses? Depth of stud cavities related to thickness of exterior outsulation, etc. I've just started utilizing the WUFI software from the Oak Ridge National Laboratory to analyze interior moisture potential, dew points, etc Maybe that is the best method?? Has anyone had much experience with that software? I wonder if Building Science Corporation has tested it and recommends it.
At the ACI conference recently, I asked John Straub about the PERSIST method (I'm still looking for that damn silver bullet!), and its application to various climates. He explained that in extreme climates (I assume, very cold and humid), PERSIST wall assemblies may be advised, but in more moderate climates, he did not know why you would give up the added insulation.....add sprayed cellulose to a 2X6, and you get an additional R-14. Systems and thicknesses of outsulation and insulation all change with latitudes and longitudes. Is WUFI the software silver bullet that will help me sleep better at night?
Response to Ed
Ed,
There are various methods available to help ease your mind when specifying rigid foam sheathing over insulated cavity walls.
Your first resource should probably be Table N1102.5.1 in the 2007 Supplement to the International Residential Code (IRC). The table provides prescriptive advice; it lists minimum foam thickness for insulated 2x4 walls and 2x6 walls in a variety of climates.
A version of the table can be found here:
http://www.buildingscience.com/documents/guides-and-manuals/irc-faqs/irc-faq-insulating-sheathing-vapor-retarder-requirements/
You may also be interested in a calculation method promoted by Joe Lstiburek and reported by Ted Cushman in his article, "Robust Walls":
http://www.coastalcontractor.net/pdf/2006/0611/0611robu.pdf
Finally, there's nothing wrong with using good old WUFI.
Great...Now What?
I am in the middle of an exterior renovation and my architect spec'd 3/4" rigid foam insulation on the exterior of my house. The house was built in the 1850's and has major gaps in the board sheathing. I was on board with the exterior insulation and had my windows built out to accept the 3/4 foil faced board.
Now I am in a panic. Minnesota has major temperature fluctuations and this house is super drafty. We took all of the old siding off and replaced the windows. The foundation has been repaired.
Should I move forward with the 3/4" rigid insulation? I get a different answer from every architect I talk to.....help!
The goal is to lower my heat bill and make the house comfortable, NOT ruin the house or have mold issues.
Doug
Doug, don't panic
Doug,
Don't panic. Exterior foam is a good idea. However, your architect probably hasn't spec'd enough of it.
Minnesota has two climate zones -- Zone 6 and Zone 7. To avoid condensation problems in your wall, your foam sheathing should have a minimum R-value of:
R-7.5 for a 2x4 wall or R-11.25 for a 2x6 wall in Zone 6; or
R-10 for a 2x4 wall or R-15 for a 2x6 wall in Zone 7.
You should have a discussion with your architect and refer to Table N1102.5.1 in the 2007 Supplement to the International Residential Code (IRC).
Ideally, you'll install thicker foam. However, the fact remains that even if you stick with the thin foam, it doesn't mean your wall will turn to oatmeal. You'll just need to be a little more careful about your indoor humidity levels in winter. If you keep your indoor humidity level low, you should be okay. Refer to WUFI for more information.
My goodness. Perhaps the spec was fine. Look, the dew point moves depending on temperature. On cold days it is deeper in the wall, regardless the exterior covering, foam or plywood. On slightly less cold days it is more to the outside, perhaps at the interior of the sheathing, with or without foam. Maximum foam will keep it in the foam (or perhaps the exterior sliding at certain temps, thus a vented drain plain.
But, "You'll just need to be a little more careful about your indoor humidity levels in winter" absolves you from the whole issue? If it was simply that simple why all the fuss?
3/4" rigid foam
Doug,
Having been in that same place, I'm with Martin. 3/4" is a bad thickness of exterior foam for your climate. It's thick enough to stop the moisture movement through the sheathing that has been successfully keeping the sheathing dry for all these years, but not thick enough to prevent condensation on that sheathing on your cold days once that moisture movement stops.
Go thicker would be my recommendation. Once you are headed towards exterior foam there is a minimal cost difference in going thicker, your labor cost won't change much at all.
3/4" Foam
Okay....I talked to my architect and he said 3/4" foil is fine if I install 15# felt under the rigid foam. Is this good advise?
All of my windows are built out 3/4". How can I go thicker and not make the windows look silly? I hope that question makes sense. I'm worried about the details....
This house has been such a stressful project. My roofer messed up the roof and took off with our money (we took him to court an won), found a foundation "issue." and fixed that. Tore off all of the siding and hired an architect. I showed my architect a Fine Homebuilder article about exterior insulation and we rolled with it. Now I'm 2 days from sealing up the house and run across this information....
I want to do this project once and do it right. It looks like I am in for a change order of sorts. I'm not sure my contractor or architect have the knowledge to pull this off correctly. Again....everyone has conflicting information.
My city building inspector has never seen exterior insulation and told me 3/4" "should be a huge improvement." and to "let him know how it goes." Funny....the city has no clue wither.
Thanks for your help.
Doug
"It's okay if there is asphalt felt underneath"?
Doug,
Either you misunderstood your architect, or your architect misunderstood you, or your architect is ignorant.
Asphalt felt provides virtutally no R-value. I'm not sure of your climate zone or your framing thickness, but you need between R-7.5 and R-15 of foam. Moreover, R-7.5 will work only if your house is in southern Minnesota and your walls are framed with 2x4s.
It's possible that your architect is ignorant about the building science issues surrounding foam sheathing.
As I said before, you won't be the first person who has broken the minimum R-value guidelines for foam sheathing. If you end up with thin foam, be sure to maintain a low indoor relative humidity during the winter. No humidifers!
Thanks, Martin....
.....for the links. Very helpful.
Felt Under Foam
Martin-
Thank you for the information. I did not misunderstand my architect in regards to the tar paper or rosin paper installed under the foam. My architect instructed me to have 15# felt under the foam in case moisture did form and the paper would help keep the sheathing dry.
I am just a homeowner and I hired an architect because they are the professionals. Seems like my architect needs to learn more about exterior insulation. I showed him this blog and he basically told me that the subject was over thought.
Needless to say, I am trying to get more foam on the exterior, but I am stalled by the fact my windows are built out to accommodate 3/4" foam. The fun begins...
I guess I could just stick with the 3/4" foam and keep the humidity levels low, but that seems like a silly compromise since I have a house with the entire exterior siding removed. My architect has lost all interest in this subject and he has been paid in full, so I'm on my own.
Thanks for all of the help.
Doug
"The paper would help keep the sheathing dry"
Doug,
The source of the problematic moisture is the interior of the home. If you install asphalt felt under the foam, that's where the condensation will form -- on the back side of the asphalt felt. The condensation will put the existing sheathing at risk. Although installing asphalt felt is a good idea, it does nothing to address your potential condensation problem.
I know this is history now, but this poor fellow was being driven nuts. The relatively few times that the dew point is going to be exactly on the back of the foam or tarpaper is not any more often than it was on the inside or outside of existing sheathing of many existing homes, old and new.
Exterior foam
I am also planning a large scale renovation/addition to my currently uninsulated 1951 cottage/ranch house. All of the existing siding and sheathing will be removed and I am planning on re-sheathing walls with OSB/plywood covered with a WRB with 3" of polyiso over that with vertical strapping installed for siding. I was thinking of using closed cell spray foam on the interior side, but after reading the above, I'm concerned that the sheathing will not be alble to dry either way. I don't know if this is such a problem if there is no water penetration, but I realize that there is no such thing as a waterproof wall. Would using cellulose on the interior be prefereable? I live in Richmond, VA- pretty hot and humid in the summer (use AC for probably 2-3 months) and can get cold in the winter, but not for long periods.
Response to Josh
Josh,
Sandwiching OSB between two layers of vapor-impermeable insulation (polyisocyanurate and closed-cell spray polyurethane foam) is a bad idea.
It would be safer to install a vapor-permeable insulation (for example, cellulose or open-cell spray polyurethane foam) between the studs.
“[Deleted]”
Pierre,
1) Isn't that exactly what Josh proposed? " 3" of polyiso over that with vertical strapping installed for siding. I was thinking of using closed cell spray foam on the interior side".
2) You do know this discussion is almost ten yers old?
How about old fashioned wall assembly?
We are undergoing a renovation on our 1930 arts and crafts style home in Ottawa Canada. We have taken apart the entire second storey and are installing a shed dormer on one side of the house. The new section and the old section will be built out to a 2x6 wall thickness, and the combination of diagonal walls (the old slope with knee walls), the new section and the roof insulation will all require different strategies.
For the vertical walls:
The current plan was to use a traditional wall system of 6mil poly on the inside (diligently caulked, taped and sealed at every point), R22 Roxul (mineral fiber I believe) batts between the 2x6's, 5/8 plywood sheathing (or 1x12 shiplap boards on existing walls), Typar wrap (air barrier), and a cement fiber siding product (or brick on the existing walls).
For the diagonal walls:
This is a challenge because I want this area to bring up ventilation from the soffit up into the roof and there are currently only 2x6 rafters. I plan to add the 'raft-r-mate' foam vents up against the roof surface from the soffit area, up to and extending into the attic area. I would then either add spray foam insulation, or friction fit Roxul batts into the 24" cavity and then the 6mil poly on the inside. Could build out the cavity by adding some 2x2's on top of the existing rafters, this would allow me to get close to R40. The roof is directly on top of this area, and will have a 'peel and stick' membrane and steel shingles added on top (Decra type).
For the Roof:
The idea was to have the standard 'builder' type system, 6 mil poly on the inside, and blown cellulose (up to R50 if possible) on top. The attic will be fairly shallow and I am a bit concerned that air swirling from the ventilation will redistribute the cellulose. Not sure even if that is a problem that anyone has heard of before (if not, good!).
I haven't contracted out any of this work yet, however the windows I have ordered will prevent me from adding any insulation on the outside of the house. I would however like to hear some comments or feedback on the proposed strategy to see what some of you knowledgeable folks have to say about this.can
Having took Building Science in school, (from Straube as someone mentioned earlier), I do have some basic understanding of the science and engineering behind this. I can estimate here that there will be some condensation happening in the wall cavity (in the Roxul batts), however drying could occur to the outside for the vertical walls, and the overall R value would be sufficient for the purpose and 2-3 times better than before (some walls were not insulated!).
Regards,
Todd
Response to Todd
Todd,
The problem with an old-fashioned wall assembly is that you get old-fashioned performance.
Mineral-wool batts in a 2x6 wall give you a whole-wall R-value of about R-14 or so (after taking into consideration thermal bridging through the studs). That's not much. You should be aiming for R-40.
In Ottawa, you can probably get away with interior poly -- but the interior poly can be risky if your home is ever air conditioned. I would skip the poly and use vapor-retarder paint.
If your sections of insulated roof are framed with 2x6s, and if you include a ventilation channel, you have very little room for insulation. Roxul batts definitely won't work there. At the very least, these sections need closed-cell spray polyurethane foam. Or else you need to build down your framing to thicken your roof. If you're a student of John Straube, you should be aiming for R-60.
Interior Foam Board over steel studs?
I am currently building a house out of steel studs. The house is located in western Sonoma County, California. Because of the steel studs and thermal bridging, we are being required to add a R-4 1" foam board to the exterior of the house. Two problems I have is 1. Windows are ordered and the 1" was not taken into account. and 2. we are doing a traditional 7/8" stucco and the stucco contractors around here won't do the job if the 1" foam board is used because of possible sagging problems with the weight of the stucco.
So I have decided to go with Tuff-R (DOW) in the 5/8" thickness that would give a R-4.1 value on the interior between the steel studs and 5/8" drywall.
Is this a good idea? Or am I asking for mold/moisture problems?
Response to Erik
Erik,
From your description of your plan, I don't see any reason why you will have moisture problems in your walls. However, your house will have energy-use problems.
Thermal bridging through steel studs is such a serious problem that any cavity insulation is virtually worthless. All you are going to end up with is 5/8-inch insulation for your walls. That's nuts.
You probably have a mild climate, but I don't think you should build a steel-stud house with less than 4 inches of rigid foam. If you can't find a stucco contractor to stucco your house, choose a different siding!
And by the way, it's easy for finish carpenters to install jamb extensions on your windows (or to use drywall returns to your windows on the interior of your house).
I can't imagine that your proposed wall meets California's Title 24 requirements.
Response to Martin
First off Martin, thank you for such a quick response!
The house is in climate zone 2. When the energy calcs were originally done, they were based on 2x6 steel studs at 16 o.c. with 1/2" drywall. The specific requirements for the 2x6 walls was R-19 plus R-4 continuous insulation. So at this point we would meet the requirements of Title 24.
But I am kind of torn on what to do now. We will be doing exterior sheathing on the house next weekend, so obviously I've waited too long to start dealing with this. I need to satisfy Title 24, but I don't want to spend money on something that won't make a difference!!
Response to Erik
Erik,
Trust me -- thick exterior foam over steel studs will definitely "make a difference." Try to find a way to include 2 or 4 inches of exterior rigid foam. You won't regret it.
foam behind Hardie board
The above discussion raises a question for me. My circa 1947 house has 2x4 stud walls with blown-in cellulose in the walls. When the cellulose was being blown it started cracking the old brittle sheet rock, and the installers "turned down" their machine, so I expect that the cellulose is not packed tightly and may not completely fill the cavities. I badly need new siding, and am leaning toward Hardie plank. Am I correct in thinking that the simplest way to avoid moisture problems is to wrap the old wood plank sheathing with Tyvek, and to install the siding directly over the Tyvek, with NO fan-fold or foam insulation? With a hip roof, and very narrow venting soffits, I am not interested to add more thickness to my walls.
Response to Gary H
Gary H,
The simplest way to avoid moisture problems in your walls is to do a superb job of flashing and to install a rainscreen air gap between your siding and your WRB (Tyvek in your case). The cause of most moisture problems in walls is wind-driven rain that saturates the sheathing.
Foam on Dormers
I am going to be replacing the windows on 2 dormers. I live in far north central Minnesota where temps in winter frequently hit -40. The house was built in the 1940's with no attention to thermal performance. The dormer is built with 2x4's with little to no cavity insulation. I was planning on adding 4 inches of PIR insulation around the dormer vertical walls and fill the areas above the ceiling with cellulose insulation.
I wanted to make sure my plan was sound. I obviously would be required to extend the roof of the dormer out further past the added 4" of insulation. What is the detailing though where the dormer wall meets the main roof deck? Do I cut the insulation to be flush with the roof deck then use regular metal roof flashing
like you normally would?
It also seems a bit tricky with the batten boards that would be required with 4" of insulation on the dormer. I assume one of the batten boards would need to be placed parallel to the roof deck angle and the roof flashing would be behind that batten board?
I included a link to the picture of the dormers I am talking about.
http://dl.dropbox.com/u/6913865/HouseFront.jpg
Response to David B.
David,
I'm not sure what you mean by PIR insulation, but I'm going to assume you are talking about polyisocyanurate.
You'll need to strip the dormer cheeks (the walls) down to the wall sheathing, and you'll need to strip your roofing down to the roof sheathing in the vicinity of the dormer. You need to install your rigid foam with attention to air sealing. The perimeter of the rigid foam needs to be caulked before it is installed; it should extend down to the roof sheathing. The gap between the roof sheathing and the new wall foam should be caulked.
Foam seams should be taped with housewrap tape.
I would install peel-and-stick membrane between the new wall foam and the roof sheathing. Then I would install my vertical strapping to create a rainscreen. I would install step flashing when re-shingling the roof (repairing the roof), with the step flashing butting up to the outside of the vertical strapping. (I know, there could be water behind the step flashing. But trust me, it'll be fine. That's where you want the step flashing to go. And the peel-and-stick will handle wind-driven rain that gets past your siding.)
Thanks for the detailed
Thanks for the detailed response. The PIR acronym was used in the Robust Walls article linked to from here. Any suggestion on how to handle the knee-wall and/or roof-deck? There is ZERO insulation on areas behind the knee wall. I don't want to use any fiberglass insulation and prefer the rigid foam and cellulose. The worst part is they tried to create some ventilation on the underside of the roof deck behind the knee-wall so there is a massive chimney effect in the winter.
Response to David B.
David B.,
It's always hard to make renovation recommendations without a site visit.
If you have an uninsulated cold attic behind a kneewall, the best insulation strategy is to relocate the insulation so that it follows the roofline, bringing the behind-the-kneewall area within the home's conditioned envelope. Rigid foam insulation is, indeed, far preferable to fiberglass batts.
If you insulate below the roof deck without ventilation, be sure to use an insulation that is not air-permeable; options include spray polyurethane foam or rigid foam. Make all seams as airtight as possible.
Remember, it's always possible to install rigid foam insulation on top of the existing roof sheathing. Of course, that means you'll need to re-roof the house.
Future siding replacement
This site and comments have been extremely informative. I have a future house project where I would like to replace the wood siding on my house. In the process I was thinking of adding a layer of rigid foam under the new siding not only for the R-value but also to help with air infiltration. I live in Livingston, MT where the fall, spring, and winter winds can be 30-40mph for several days. The walls are 2X6 with foil faced fiberglass batts with tongue-and-groove wood plank interior finish. I have been concerned about wall condensation if I add the exterior foam. A couple of other well-known building site people have told me that I would not have a problem putting on 1" of exterior foam, but the info at this site indicates I should have at least 2". What are your thoughts?
more info
i just found some notes from a couple of months ago that indicate that I should use a product called Foamular which has a perm rating of 1.1 instead of a product like ProPink which has a perm rating of 0.23 (there is a plastic film appllied to the surface of ProPink whereas Foamular does not). I would be very interested in hearing thoughts regarding this information especially in context of my future house project as described in my previous post.
Response to Kirk
Kirk,
The thicker foam will lessen chances of condensation by warming your sheathing and your wall cavities. With exterior rigid foam, thicker is better than thin.
hi
I would think this would lessen thermal bridging by creating a thermal break where the studs touch the sheathing and give more space for cellulose in the cavity plus allow the wall to breathe normally.
Rigid foam on INTERIOR?
Any follow up on my June 28th comment?
I don't see how adding a 1 or 1.5" XPS on the interior would increase the chance of condensation issues. How is that any different than a 2x6 or 2x8 wall filled with cellulose?
Anyway I would really appreciate any comments or ideas.
John
Interior rigid foam
John,
Interior rigid foam works fine; I've used the technique several times myself. The main disadvantage is that it fails to address rim joists and partition intersections — areas that are addressed well by exterior foam.
You also raise a question about condensation dangers from thin exterior foam. So, why is thin foam riskier than thick foam? Mainly because thin foam reduces the ability of the exterior sheathing (OSB or plywood) to dry to the exterior, but it isn't thick enough to prevent condensation during the winter. The idea is to install thick foam, thereby warming up the sheathing to the point where condensation never occurs.
You raise the question, "What about a 2x6 or 2x8 wall filled with cellulose? Won't that wall have cold sheathing?" The answer is, it will. Condensation or frost formation is certainly possible on the cold OSB sheathing on such a wall. The main reason that these walls don't usually fail is that they dry to the exterior when the sun hits them or when the weather warms up in the spring. Thin exterior foam limits drying to the exterior, though, and can tip these walls into failure.
Thick walls insulated with fiberglass or cellulose are risky. These days, John Straube is warning builders of double 2x4 walls (usually 12 inches thick) filled with cellulose to avoid OSB, which is the riskiest sheathing material because it is rather impermeable and prone to rotting. He'd prefer to see plywood or fiberboard sheathing on such a wall. And don't forget the rainscreen air gap, which helps encourage drying when the sheathing gets wet.
Interior rigid foam
Martin
Thank you for taking the time to respond with a well thought out reply. I just have a few more questions and clarifications.
I am in Vancouver Canada and our winters are very wet but only infrequently go much below freezing. In the winter it rains here six days a week for six months. Summers on the other hand are very dry and very warm to hot. It only gets hot enough to consider air conditioning for about one week typically.
I am designing my own home and plan to general contract it and/or do much of the work myself. I am interested in all I can do to improve the energy efficiency and comfort using cheap labour (myself!). To that end ripping 1.5" XPS on a table saw and nailing it to the interior side of the studs is a reasonable proposition to me. As I can do this when ever I please after the shell is erected it removes this task from the schedule critical path.
I realize this is not as effective at reducing thermal bridging as applying XPS to the exterior, however I am willing to take a slight hit on thermal bridging if it means avoiding "leaky condo" syndrome. I really don't want to impede exterior drying. (I'd be using ADA rather than poly vapour barrier as well.)
It would seem the critical point with exterior XPS is the thickness. Too thin and you get sheathing condensation. Too thick and you blow your budget (I don't need 4" of XPS here in Vancouver.) So in my situation interior application makes more sense.
The strip method would allow the wet blown cellulose contractor to install like 5" if 1.5" XPS strips over 2x4's. Cellulose does not impede moisture movement so drying to the interior is maximized.
That was my poorly explained point about "what about a 2x6 pr 2x8 wall filled with cellulose?" The point I was trying to make is how is that different, condensation wise, than 2x4 with interior XPS (for a similar total insulation value). I realize the drying potential is vastly different.
In our climate rainscreen is a must.
I will be using 1/2" plywood sheathing because it is more vapour permeable than OSB glue-board.
If you have any examples of STRIP INTERIOR XPS jobs please direct me to them!
Thank you again
John
Response to John
John,
I think your plan will work fine. Be sure your damp-spray cellulose is dry before you close up your walls.
Moisture dilemma
Not too long ago, we gutted all the plaster and lath from our house. I was then told it was code to put poly on insides of exterior walls, so I did.
We also cut little holes in the poly to glue sheetrock to walls. There also was probably a few small areas missed.
The walls are 2x4. This is also a balloon-framed house with R-13 fiberglass in the cavities. I have recently installed 1-inch Owens Corning styrofoam to the exterior.
I now plan to install vinyl siding to this wonderful home. Will this sweet wall combo be doomed to failure?
Thanks so much in advance.
Response to Jason
Jason,
You didn't tell me where you live or what your climate is.
Whenever a house has exterior rigid foam, it's best to omit interior polyethylene or vinyl wallpaper. So your wall design is not ideal. It's also unclear whether your exterior foam insulation is thick enough to avoid condensation problems. (That depends on your climate. If you are in Zone 6 or any colder zone, your foam sheathing really isn't thick enough.)
All of that said, your wall is not doomed to failure. There's not much you can do about it now except to keep your indoor relative humidity low. Whatever you do, don't install a humidifier!
more info
I, unfortunately, live in a very cold climate - the beautiful state of Minnesota. I live in the southwest corner of the state. Last year it got down to -25 F in winter. What do you think I should do?
Response to Jason's second post
Jason,
According to Table N1102.5.1 in the 2007 Supplement to the International Residential Code, the minimum R-value for exterior foam on 2x4 walls in your climate (Zone 6) is R-7.5. You chose to install R-5 foam, which is less than required by the code. Thin exterior foam can leave your sheathing cold enough to allow condensation.
If you haven't installed your siding yet, you could consider doubling up your exterior foam. If you go this route, you should stagger the seams in both directions. But doubling up your exterior foam will require adjustments to your exterior window trim.
Just because your foam is too thin and you have inappropriate interior poly doesn't mean your wall will rot. If you leave your wall the way it is now, the most important thing you can do is keep your interior relative humidity low during the winter. They may require you to run your bathroom exhaust fan for longer than usual.
3rd and hopefully final question
Since the house is balloon-framed and the stud cavities go all the way to the attic, won't moisture be able to vent this way? What would we put on to get to a r-value of 7.5? Could we use 1/4" fan-fold? In your opinion - since you are quite knowledgeable - what should I do? what would you do? Thanks for all of your help!
Response to Jason's third post
Jason,
1. You never want to encourage air movement through stud cavities. The idea is to make stud cavities as airtight as possible. (In fact, the Energy Star Homes program requires wall insulation to be enclosed on all six sides by an air barrier.)
If you encourage air flow up your stud cavities, warm interior air will be drawn into the bottom of the stud cavities, and the moisture in that air will condense on the first cold surface it encounters -- either the interior face of your wall sheathing or exposed framing members in your attic. That would quickly lead to mold and rot.
So, for heaven's sake, find a way to install an air barrier at the top of your balloon-framed stud cavities. (I suggest you use spray polyurethane foam. Get a Handi-Pack kit at your local lumberyard.)
2. You can increase the R-value of your R-5 sheathing to R-7.5 by adding a 1/2-inch layer of XPS. No, 1/4-inch fanfold isn't thick enough.
3. What should you do? That's up to you. I don't know what your budget is, or your appetite for risk. If you can afford to do the work, I would certainly recommend beefing up the thickness of your exterior foam. I probably wouldn't bother to try to remove the interior poly, though -- too late for that. If I were you, I would buy a hygrometer and install it indoors. Make sure your indoor relative humidity stays below 30% in the winter.
Exterior Insulation with brick and stone over it.
I will be building a new home with 2" x 6" studs and a 10" thick foundation walls, in Ontario Canada. I am considering exterior insulation rather than traditional interior insulation with an interior vapour barrier. What issues and challenges do I need to be aware of if I use 4" of exterior insulation? I have seen your video showing the installation, but it was with siding rather than with brick/stone.
Is it possible to get a schematic drawing drawing that I can present to my architect and builder. Exterior insulation is not common at all in Ontario.
Brick veneer over exterior foam insulation
Anonymous,
The GBA Web site has a library full of construction details, including details showing brick veneer over exterior foam insulation. Here is the detail you are looking for:
https://www.greenbuildingadvisor.com/cad/detail/wall-section-brick-veneer-1-12-rigid-insulation
If you're a GBA member, all you have to do is click the link. If you're not yet a member, sign up!
rigid insulation and moisture
We a building a new house in northern Alberta where it can get up to 34'C in the summer and down to -50"C in the winter. Of course we want a reasonably, cost effective house. The plan is 2 x 6 walls with "pink fiber" insulation, 6m poly on the inside. Outside would be house wrap on 7/16 sheating then 1 1/2" rigid insulation covered by vinyl siding. My builder has just informed me about possible moisture that can be trapped in the wall. This moisture may get in there during construction, as already in the building material, or may get in during the odd extreme storm.
We add a lot of moisture in our house in this climate in the winter to maintain the inside at about 35%. So I think I need to keep the inside poly.
We have already all the material including 8" windows and doors so staggered 2x4 wall is not a good obtion.
What can I do to reduce the risk of moisure being trap in the wall? Is there rigid insulation that is designed to "breath" more than others? Put the housewrap on top of rigid? Not tape the rigid joints to allow to "breath"?
Comments and advise would be well appreciated.
John
It seems to me that
Response to John
John,
In your case I would recommend that you don't use interior poly (because of the rigid foam sheathing). Instead, use MemBrain.
exterior foam insulation
Hello all
I am planning to build a house near Ottawa, Canada and this discussion thread is a godsent ,as I was getting pretty confused about all the seemingly conficting information on wall insulation. I want to have both above average insulation values and above average shear wall strength. After having digested this thread and other ideas, I am planning the following wall structure: siding + 1 " air space (furring strips)+tyvek+OSB or Plywood sheeting (later preferred) +2x6 studs+ 2 inches expanded polysterene board cut to fit inside the stud space+spray foam at the junction of the foam board and the studs to plug any gaps+ 3.5 inches stone wool insulation+ 1" expanded polysterene covering the wall on the inside + membrain or aluminium foil+ 2 inch air space ( 2 x1" furring strips) + gyprock. This should provide about R 29 insulation with about 32% of the isulation value between the inside face of the 2" polysterene board and the outside of the wall. Thus there should not be condensation on the 2" polysterene inside face. The dew point should be inside the 2" polysterene. Note that the 2 inch interior airspace is not so much for insulation value as a way to keep the stud space airtight . There will be no openings in the 1" polysterene board closing the stud space from the inside. Electrical wire and boxes will fit inside the 2" airspace. While not a cheap solution , providing my own labor for insulation work should make it affordable. Note also that the 2" polysterene will be cut with the special hot knives used for ISP panels, so this step should be manageable. I do not pretend that this solution is universal, but I think it should work in Canada , zone 6 or 7 especially since we are required by code to have a vapor barrier on the inside. If anybody sees a flaw in this design , your comments will be deeply appreciated.
Response to Eric M
Eric M,
You're making a "foam sandwich," which is not ideal. Nevertheless you'll probably be okay.
If you do a careful job with the 1-inch EPS covering the interior side of the studs, you don't really need the strips of foam between the studs, which is your fussiest detail.
One more point: be sure that you have a plan to address thermal bridging and air leakage at the rim joists.
interior foam insulation
Martin
Thank you for your input. It is greatly appreciated. I may be unduly concerned about having condensation on the inside face of the sheeting. This concern came from the conflicting opinions about the sheeting preventing the wall from drying adequately to the outside ( less so for plywood than OSB). If this condensation potential is not an issue , I guess I could skip the foam inserts and simply fill the wall stud entirely with rockwool . I would still use a spray foam such as Owen Corning's ( made for that purpose) , to seal the junction between sheeting and studs. Thus my inside wall cavity would be as airtight as I can make it with no hole penetration from the inside andf, if I am not mistaken, the foam on the inside would take care of the stud heat bridge problem.
Response to Eric M's second post
Eric M,
In my first response, I tried to give advice about your planned assembly. But you are really approaching things differently from most builders.
By far the best place to put rigid foam is on the exterior of your wall. That way the foam:
1. addresses thermal bridging, including thermal bridging through rim joists;
2. greatly reduces the chance of condensation on the interior side of the wall sheathing.
Other locations for rigid foam insulation -- including the two options you mention -- can work, but they are more expensive, more fussy, and less effective than the preferred location -- outside of the sheathing.
Foam over brick and CMUs
I have brick exterior with about a 1/2" air gap and then a 4" CMU (concrete masonry unit) wall on the inside plastered and painted. I want to add foam to the exterior. None of the articles or comments mention putting foam over brick walls. Got some advice? Will there be similar moisture problems? The house is in Boulder, Colorado with coldest month average temperatures of 35, 33, and 36 degrees F.
Response to Walter
Walter,
It's possible, but the details are tricky.
1. Adding rigid foam and new siding to the exterior of your home raise structural issues, since attaching everything to the existing brick veneer may be inadequate from a structural perspective. It might be easier to widen your footings, bring a new foundation up to grade, and install a new exterior stud wall, and then install closed-cell spray polyurethane foam between the bricks and the new studs, and between the new studs.
2. You have to do a good job detailing transitions; you want your thermal barrier to be continuous and your air barrier to be continuous. These details are particularly tricky at the bottom of the wall and the top of the wall.
3. You'll need to come up with a careful flashing plan for your windows and doors -- or else install new windows and doors, pulled out to the new location in plane with the insulation. That's expensive but possible.
Old House Refurb, insulation/siding issues
Martin,
I appreciate the discussion, thanks.
I am a mechanical engineering student and doing a complete refurbish (bad combination I know) on my 1890's 4-square. The problem is that during the refurbish process I am removing and replacing sections of damaged 'plank' sheathing including several studs here and there. It is difficult to obtain a somewhat planar surface with the cupping and rough cut plank sheathing and replaced sections (1/8" variations are common) . I had thought about using that nearly worthless foldout foam to assist in having a relatively smoother surface for vinyl siding, but am fairly concerned about the vapor trap issue.
So the question becomes, do you agree with my assessment that its not an advisable solution, or am I being the typical 'over thought' engineer on this one? Do I really need to worry about the 1/8" depth variance at the many vertical and hz seams and if so what are cheap solutions?
Of course if I had money I would employ the several inches of exterior foam, corporate sponsors anyone?
Thanks for any input.
Response to Chester
Chester,
Without knowing your climate, it's hard to know how exterior foam will affect your home's performance.
A good vinyl siding installer is very familiar with the problem you describe. While fan-fold foam can help smooth out minor irregularities, some houses require more shimming than others. If your existing sheathing is very wavy, the best solution is to install vertical strapping, 16" or 24" on center, over your existing sheathing, and to shim the strapping as necessary to achieve a co-planar surface.
Once you're familiar with the issues you're struggling with, you can drive around your neighborhood and look at existing vinyl siding jobs. You'll be able to tell the difference between the jobs installed by a skilled installer who strove for a planar surface and those installed by an unskilled installer who followed the existing wavy surface.
Old House
Sorry about that, I am in-between Lincoln and Omaha NE.
designing a retrofit/refurb system?
Scott,
thanks for a great discussion and summary of the issues surrounding this topic. It's exactly the issue I'm trying to resolve right now. We're replacing roofing, siding, and windows in our 1987 home in northern VT, where the winters are long, deep, and cold, and the summers can have week-long bouts of high heat and humidity too.
I live in a house w/2x6 studs, 4 to 6 inch blown or fiberglass insulation in all walls, plywood sheathing and 3/4" shiplap cedar siding. The overall R value is approximately R-19 (minimum to meet homeowner's bylaws in original construction back in 1986). The interior walls are sheetrock w/latex paint in most rooms. Unless it's counterintuitive, the cedar siding will be removed and replaced w/vinyl siding.
But, I'm caught between builders who swear on their reputation that housewrap under the vinyl siding, or under foam board insulation and vinyl siding, will cause moisture retention and mold in the sheathing and wall insulation, and the efficiency experts who claim that housewrap and foamboard (both w/taped seams) are no-brainers (and that builders who disagree aren't to be trusted).
I assume vinyl siding won't completely prevent water from reaching the sheathing. Housewrap under vinyl siding could breath, and could provide drainage from properly flashed windows and doors, but would also get cold and could allow condensation to form on the side facing the sheathing it's meant to protect.
The shiplap cedar being replaced only allows 3/4" (the projecting distance of the clapboard vinyl siding). If we add foamboard under the vinyl (and over the wrap) we'll have to change the depth of the jambs for the windows. We could pay the extra costs for siding w/pre-affixed foam, but the R-value of those seems to be low for the added cost.
I'd really appreciate any suggestions or recommendations on how to best add the siding while keeping the overall R-value high and simultaneously reducing the risks of moisture, mold and rot in the sheathing. What is the best practice in designing a refurbishment or retrofit as a "system"?
(Incidentally, the same issue arises w/the use of various underlayments between sheathing and architectural shingles)
Thanks in advance!
Matt
Response to Matt Bovee
Matt,
The cheapest way to proceed is with housewrap or asphalt felt covered with vinyl siding. However, that approach won't improve the thermal performance of your wall.
If you want reduced air leakage and higher R-value, you will have to pay for it. The easiest way to add R-value to your wall is to add a layer of rigid foam between your existing wall sheathing and your new siding.
If these ideas are new to you, I suggest you read the following articles:
Roofing and Siding Jobs Are Energy-Retrofit Opportunities
How to Install Rigid Foam Sheathing
Calculating the Minimum Thickness of Rigid Foam Sheathing
Installing Mineral Wool Insulation Over Exterior Wall Sheathing
Follow up re:designing a retrofit/refurb system?
Martin,
thanks very much for the fast reply. I'll definitely read all those references you supplied.
The thermal performance of the existing walls is quite good at present.
Part of what baffles/concerns me is how to also minimize condensation between the new vinyl siding and the surface immediately beneath it (either siding or the plywood sheathing, depending on the final choice made). How does one create a drainage plain such that the material under the new vinyl siding is protected from exterior water AND also minimize the chance of condensation on the back of the siding as warm humid air migrates from the inside during the winter months?
Also, if we opt for a rigid foam layer between the sheathing and new siding, what are the pros and cons of the different types w/respect to drainage and winter condensation? I've read that foil-backed Polyisocyanurate will yield the best R value (w/good stability) for a given thickness. In a cold climate should the foil side be towards the exterior or the interior?
Apologies if all these questions are obvious or answered in the links you provided. I've been swamped w/both the volume of info on the topics and the contradictory opinions. It seems to be far from a simple (pardon the pun) "cut and dried" issue.
Thanks again!
Matt
Response to Matt Bovee
Matt,
Q. "Part of what baffles/concerns me is how to also minimize condensation between the new vinyl siding and the surface immediately beneath it (either siding or the plywood sheathing, depending on the final choice made)."
A. If you are concerned about condensation on cold sheathing, then you want to warm up your wall cavity with a layer of exterior rigid foam. The foam insulates the wall cavity, keeping the sheathing warm all winter (above the dew point). You can't have condensation as long as the material is above the dew point.
Don't worry about the vinyl siding. If vinyl siding had condensation on the back -- and I don't know why it would -- the moisture would dry quickly because the back side of vinyl siding is well ventilated.
Read the articles, and all of these issues will (I hope) become clear.
Follow-up: pros and cons of added insulation
Martin,
Thanks again for your suggestions. I've read all the suggested materials, and much much more.
It sounds like the main issue w/using, say, felt over the existing siding and vinyl siding over that would be how flat the new siding could be applied. Moisture that formed could dry when conditions changed to permit it. There is the issue of removal/reinstallation of the current siding as windows are replaced (another big part of the job). There's also the issue of felt causing staining at the weep hole points. But I can discuss these things w/the builder. That's one cost effective option.
I'd also like to improve the insulating factor of the walls and provide a flatter surface for the mounting of the vinyl siding. However, most of what I've read suggests that foam board insulation would be a low permeance water resistive barrier, and replacing the existing siding with 3/4" foam board would probably cause moisture to form on the back side of the foam board during the winter months. Is there a way to install rigid foam insulation over felt so that it allows the structure underneath to "breath" better, or does one of the rigid foam board types have a better permeance? For example, if felt was properly lapped on the sheathing, and untaped 3/4" insulating foam board applied over that, then the vinyl siding applied, do you think this would provide a sufficient WRB and yet also permit good drying?
All this of course assumes proper flashing of the roof and windows...
Matt
Response to Matt Bovee
Matt,
Q. "However, most of what I've read suggests that foam board insulation would be a low permeance water resistive barrier."
A. Maybe you have read that elsewhere. However, I advise builders NOT to use rigid foam as a WRB. I think it's better to use asphalt felt or plastic housewrap as a WRB.
Q. "Replacing the existing siding with 3/4-inch foam board would probably cause moisture to form on the back side of the foam board during the winter months."
A. Right. That's why my article advise the use of thicker foam in a cold climate like yours.
Q. "Is there a way to install rigid foam insulation over felt so that it allows the structure underneath to breathe better?"
A. Walls insulated with a layer of exterior rigid foam are designed to dry to the interior, not the exterior. To be sure this happens, don't install any interior polyethylene.
Q. "Does one of the rigid foam board types have a better permeance?"
A. Yes. The permeance of different foam types varies. EPS = highest permeance, and foil-faced polyiso = lowest permeance. However, the differences in permeance aren't enough to matter, so use any foam you want. More information here: Rigid Foam Insulation.
Q. "If felt was properly lapped on the sheathing, and untaped 3/4" insulating foam board applied over that, then the vinyl siding applied, do you think this would provide a sufficient WRB and yet also permit good drying?"
A. The asphalt felt is a perfectly acceptable WRB, but you can't use thin (3/4-inch) rigid foam in your climate because thin foam won't keep your wall sheathing warm enough to avoid condensation and moisture accumulation problems. I must (for the second or third time) urge you to read my article that explains all about this issue: Calculating the Minimum Thickness of Rigid Foam Sheathing.
Response to Martin re: my many insulation questions
Martin,
thanks for the lightning fast reply. I did read your article, more than once.
What I still don't grasp is why the combination of plywood, overlayed w/felt, then untaped 3/4" foam board, and finally vinyl siding wouldn't allow moisture that forms beneath the foam board to escape/dry as conditions changed. An article by Building Science Corp lists EPS and XPS at permeance levels equal or greater than 1 (which I've read is the same as dry plywood). Is the issue that the foam board is also not very absorbtive, and so despite the permeance levels moisture (not vapor) would be trapped, even if the boards were not taped? If so, wouldn't the same problem occur with simply housewrap such as Tyvek, since it is extremely good at trapping moisure (in or out) even though it is highly vapor permeable?
Apologies if this comes across as if I'm not reading whay you've suggested or that I'm simply dense. It's just that this appears to be a Catch-22 unless I am willing to slap 2" of insulation around the house, reverse the direction for drying from the original construction, and accept extra deep jambs for all 25+ windows being replaced.
Matt
Response to Matt Bovee
Matt,
Plywood has variable permeance. As it gets wet, it gets more permeable. In that sense, it is a "smart" vapor retarder. Once it's wet, it wants to dry out.
EPS is dumb. The permeance of 1 inch of EPS is about 2 perms, and it doesn't change when it gets wet. Computer simulations and experience show that when you install 3/4 inch of EPS on your Vermont walls, you lower the permeance of your sheathing enough to that the sheathing can't dry out, but you don't raise the temperature of your wall enough to prevent the moisture accumulation from happening in the first place.
The rule with foam is "go thick or don't go there." Thin foam is risky and counterproductive.
You say that any plan to "slap 2 inches of insulation" on your walls is a Catch-22. I see it differently. It's not a Catch-22; it's the appropriate specification.
You seem to be rebelling against my explanations, so there may be no stopping you. Write again in 10 years and tell me how everything works out.
Candian living above zone 7A
We live in a ridiculous part of the world (Manitoba, Canada). This winter we had temps down to -40 degrees Celsius, with wind chills that went to -50 (extreme) creating desert like conditions. In the summer we get up to +40 degrees Celsius, creating tropical like conditions. We are about to start building a Timber Frame building, 2 stories, with the second floor opening to the great room. My contractor wants us to start on the inside with drywall, then poly vapour barrier, then 2 inch rigid foam, then 2x6 walls with pink batting (I'm interested in Roxul rather than pink batting), then OSB, outside sheathing and our log siding. No one in our area understands why this would be any better than the conventional way of rigid foam on the outside, but our contractor says that he often has to deal with moisture problems on houses done in the conventional manner. He swears that using his method, he has never had to go back and deal with moisture issues. We have issues occasionally with the power going off for a day or two, both in summer and winter. We will be heating with an electric furnace, as well as a wood stove during the spring and fall.
Would it be better to go with this 'inside out' method, considering the extreme temperature changes and moisture during the season? Or do folks find the conventional method of having the rigid foam on the outside better for moisture control and R value regardless of location? I can't seem to get a definitive response from anyone.
Thanks for your time!
Response to Liberty Des Roches-Dueck
Liberty,
Many homes in cold climates have successfully included rigid foam on the interior of walls. There are two disadvantages, however, to this approach compared to installing rigid foam on the exterior of your walls:
1. The "cold sheathing" problem. To read more about this issue, see How Risky Is Cold OSB Wall Sheathing?
2. It's hard to properly insulate rim joists and partition intersections with interior rigid foam. If you install your rigid foam on the exterior side of your wall sheathing, rim joists and partition intersections are well insulated, and air leaks are reduced.
For more information on these issues, I suggest that you read the following two articles:
How to Install Rigid Foam Sheathing
Calculating the Minimum Thickness of Rigid Foam Sheathing
Hard to do without the interior poly
The installation of exterior foam board has become increasingly popular in cold Canadian climates. Myself and many builders understand the risks involved in proceeding with such a system. To achieve the proper thickness of foam in our climate (considering our minimum code for wall assembly is R24) is cumbersome and expensive.
With R24 fiberglass insulation in the cavity, you would need R24 rigid foam on the exterior of the sheathing to barely bring you to the dew point of the mean average winter temperature (R30 if you don't have an appetite for risk). That's 5" of foam board. That comes at a heavy cost.
The other problem we face (at least in my area) is that interior polyethylene is required by code.
So my question; is it worth going doing the exterior foam road when without it, your osb is likely to dry out properly should it condense or have water penetrate from the exterior?
Looking at my post it appears
Looking at my post it appears as though a builder would be better off putting all the insulation on the outside of the osb and leave the cavities empty (I have read the PERSIST blogs). Poly would still be required. How would this perform?
Response to Shawn Currie (Comments #90 and #91)
Shawn,
There is no single answer to your question. In most cases, however, a 12-inch-thick double stud wall insulated with cellulose will be less expensive than a PERSIST or REMOTE wall with 5 inches of rigid foam. If you build a double-stud wall, I recommend the use of plywood sheathing rather than OSB sheathing, and I also recommend the inclusion of a ventilated rainscreen gap.
Plenty of cold-climate builders in Alaska have used the PERSIST or REMOTE approach, however, with very good results.
For more information on REMOTE and PERSIST, see:
Getting Insulation Out of Your Walls and Ceilings
REMOTE: A Manual
Hello Everyone,
In reading
Hello Everyone,
In reading this article and the comments I'm still left a little perplexed as to beat approach my situation. Looking for bet practise advice here....
Here goes; I live in Ottawa Ontario, temperate swings from minus 30's to plus 30's. House built in 1983 by Minto, good bones to the house. 2x6 exterior walls with 5/8" sheathing. I'm refitting exterior of house. Removing the old aluminum siding. Original thoughts are tyvek envelope the entire house and tape all seams as appropriate, then a layer of inch and half rigid insulation, all joins taped and sealed to top and bottom plates; strapping over top of that to take my new siding. I was lead to believe that IsoFoil inch and half thick is my best option. However reading these comments and article, am I still okay to go as I've just described?
Thoughts and comments?
Thank you folks
Response to Sheldon Bussey
Sheldon,
Ottawa is in Climate Zone 6. Here is a link to a map that shows the climate zones of Canada: Climate Zone Map for Canada.
Your plan to install 1.5 inch of polyisocyanurate won't work in your climate zone. For more information (including an explanation of why your rigid foam layer has to be thicker), see this article: Calculating the Minimum Thickness of Rigid Foam Sheathing.
The performance of polyiso insulation is degraded by cold temperatures, as that article explains. In your climate zone, it's best to assume that polyiso has an R-value of R-4.5 per inch.
If you want to install exterior rigid foam on 2x6 walls in your climate zone, the rigid foam layer needs to have a minimum R-value of R-11.25. So the minimum thickness of your polyiso layer is 2.5 inches.
Thank you Martin.....
So, if I only add 1.5" I'm wasting $$ because I don't reach that R value, but am I also increasing my risk of condensation and potential for rot?
This rigid layer will be added over top of the tyvek and the 5/8" plywood sheathing already in place.
Building out all my window and door trim 2.5" would be a nightmare, but is the benefit in bulking up my insulation worth it?
Iguess what I'm really asking is; In adding any rigid to my exterior am I gaining any benefit? or increasing risk?
Thank you again
Response to Sheldon Bussey
Sheldon,
Adding thin rigid foam to the exterior of your walls is riskier than adding thick rigid foam, because thin rigid foam reduces the wall's ability to dry to the exterior, without making the existing wall sheathing warm enough to prevent moisture accumulation.
Q. "If I only add 1.5 inch I'm wasting $$ because I don't reach that R-value, but am I also increasing my risk of condensation and potential for rot?"
A. Yes.
Q. "This rigid layer will be added over top of the Tyvek and the 5/8-inch plywood sheathing already in place. Building out all my window and door trim 2.5 inches would be a nightmare, but is the benefit in bulking up my insulation worth it?"
A. Determining whether it is "worth it" is a tough call. The answer to the question depends on many variables, including your assumptions about future fuel cost increases and how many years you expect to live in your house before moving. If you want to perform the calculations, you'll need to use energy modeling software to determine your annual energy savings. For more information on how these calculations are made, see this article: Payback Calculations for Energy-Efficiency Improvements.
Q. "I guess what I'm really asking is: In adding any rigid to my exterior am I gaining any benefit? or increasing risk?"
A. If you add 2.5 inches of rigid foam, you are definitely gaining a benefit. If you add 1.5 inch of rigid foam, you are increasing risk.
HRV helpful here?
Hello all,
I'm currently building a small home in Vermont (I'm the homeowner, not the builder) and we're using 2x6 walls with fiberglass, plywood sheathing, housewrap, and 2" of continuous foam, followed by vinyl siding. There will be no class I or II vapor retarder on the inside. (Just normal painted drywall, allowing the wall to dry to the inside.)
Originally, we were going to use polyiso in order to meet the R11.25 prescription for zone 6 exterior insulation over 2x6 walls. However, I then read about how polyiso's performance suffers in colder temperatures, and XPS' performance can actually increase. I read that polyiso's R value can fall to 4.5 per inch, and XPS' R value can increase to 5.5 per inch.
So, we are going to use XPS instead of polyiso. If I'm reading the various articles about cold weather performance of the various foam types correctly, that should get us R 11 for the XPS foam in colder temps. That falls just .25 short of the prescribed 11.25 value. My sense is that that small difference will not be significant factor when all the other variables are considered.
One such variable which Martin has mentioned several times in the comments on this article is the indoor humidity level. If we can keep the indoor humidity low, we shouldn't have moisture problems even if we don't quite meet the R 11.25 value in our exterior foam layer.
So my question is whether or not an HRV would help with keeping indoor humidity low enough. We are going to install an HRV in the house, exhausting from the bathrooms and laundry room, and supplying to the two bedrooms.
Martin or others, do you have any thoughts on this approach?
Thank you for any input!
-Ross
Response to Ross Carlson
Ross,
Q. "My question is whether or not an HRV would help with keeping indoor humidity low enough. We are going to install an HRV in the house, exhausting from the bathrooms and laundry room, and supplying to the two bedrooms."
A. Yes, operation of an HRV during the winter tends to lower the indoor relative humidity (RH). If you want, you can buy a hygrometer to keep track of the indoor RH, and adjust the number of minutes per hour that your HRV is set to run so that the indoor RH meets your needs. About 30% RH is a good goal during the winter in Vermont.
Re: HRV helpful here?
Thanks for the very quick response, Martin! Would you agree that we should be okay with 2" of XPS on a 2x6 wall as long as we keep the RH at a reasonable level?
Response to Ross Carlson
Ross,
I think that 2 inches of XPS will work under the circumstances you describe. That said, there are two drawbacks to your plan:
1. If you house is sold, the future owners may not be as conscientious as you about maintaining a low indoor RH during the winter. Thicker foam will make the house more resilient.
2. Green builders try to avoid the use of XPS, because it is manufactured with a blowing agent that has a high global warming potential. In your case, the best solution would be to install 3 inches of EPS. For more information on this issue, see Choosing Rigid Foam.
Thanks again Martin. We're
Thanks again Martin. We're far enough along in the build that we're essentially committed to no more than 2 inches of foam, so I don't think the 3" of EPS is an option for us at this point without some significant (and costly) course correction. I should have asked these questions a few months ago. :)
Best options in 2 inches
If you decide you can't exceed 2 inches, I would recommend either:
1. Graphite infused EPS foam, usually sold under the brand name Neopor. That gets the R-value up closer to that of XPS and avoids the two problems with XPS, which are a. the extremely high climate impact of the blowing agent used to make the foam, and b. the R-value decays over time eventually (perhaps after 50 years) reaching the same value as EPS.
or
2. Mineral wool board (Roxul brand) which can be installed pretty much he same was as foam board, but is vapor open, so you don't need to follow any minimum R-value rules.
Impact of an unheated interior in Winter
Hello,
Our proposed holiday property new build is considering exterior rigid foam (zone 4c). However, it will be unheated and unoccupied for long periods in Winter, what impact, if any, does that have on the wall assembly?
Response to Quinn Sievewright
Quinn,
The brief answer is "none."
The longer answer is that whenever a property is left unheated for months over the winter, there is a small chance that musty odors or mold may develop. This can happen whenever warm humid weather follows a spell of cold weather. Owners of summer homes have known about this phenomenon for decades, and it has nothing to do with whether or not the wall has a layer of rigid foam.
The solution is to air out the home in the spring, and to clean up any mold on indoor surfaces. Don't worry about it.
-- Martin Holladay
Response to Martin
Thanks Martin!
Log in or become a member to post a comment.
Sign up Log in