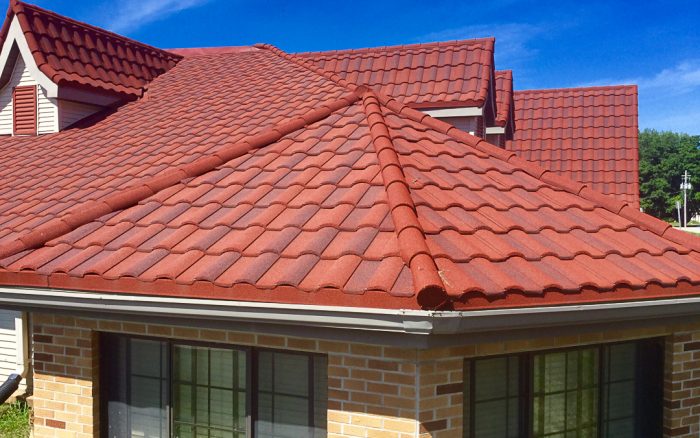
Metal roofing has a long history in the U.S. but until 20 years ago it was a bit player in residential construction with just a 3.6% share of the reroofing market. That number has roughly quadrupled since then, according to an industry trade group, as metal claims an increasingly larger slice of the pie.
What happened? Product offerings are more extensive than the simple corrugated panels that have long been used on barns and sheds. Metal roofing is available in a range of styles — from several kinds of standing seam to a variety of stamped metal shingles that look like slate, clay tile, and even asphalt. Paint and stone coatings are more sophisticated and more durable, giving roofing a very long service life while appealing to homeowners with a variety of aesthetic preferences.
The industry also is working harder to win over consumers who once thought that metal roofing was too hot, too heavy, noisy, or prone to rust, says Dick Bus, president of ATAS International and head of the Metal Roofing Alliance. “Those myths are gone, and people want to reroof with something that has some permanence to it,” he said. “Metal roofing that’s properly installed can last upwards of 50 to 60 years or more.”
Metal roofing may never catch up to asphalt in the residential arena simply because of cost. Light gauge, through-fastened panels might be competitive with asphalt on a simple roof shape, but the industry acknowledges that a standing seam or metal shingle roof can be two or three times the initial cost of asphalt. Still, manufacturers think they can continue expanding on the strength of other attributes: long-term performance, recyclability, high fire resistance, and low maintenance.
Start with the base metal
Steel and aluminum are the two most common and least expensive metals used for residential…
Weekly Newsletter
Get building science and energy efficiency advice, plus special offers, in your inbox.
This article is only available to GBA Prime Members
Sign up for a free trial and get instant access to this article as well as GBA’s complete library of premium articles and construction details.
Start Free TrialAlready a member? Log in
25 Comments
Couple of negatives about metal roofs not discussed, first is snow slide in northern climates. Snow tends to come off these roofs in large chunks, damage can result to decks and other surfaces below the roof line. Second is expansion and contraction of steel. I've seen some through-fastened panel's screws back out of the panel which will create a leak and possibly lessen the uplift needed to blow the roof off. I believe this happens because of the expansion and contraction of the panel working on the screws. Steel can be a great choice, I usually try to convince a customer to move to standing seam or shingle style.
Thanks for the comments Randy.
Have you ever tried the brakes that can be installed to prevent the snow sliding off the roof?
Also, I wonder if the fastener issue in an install failure. It seems to me that installers would have figured out the expansion and contraction issue by now, if that is in fact what is causing the screws to back out.
Maybe another GBA member has some experience with that.
Brian,
I have experienced the same problems with exposed fastener roofs. My (non-exhaustive) list of things that would cause them to back-out would be:
- The expansion and contraction of much larger panels than used on snap-lock roofs - which also either use clips or slots to mitigate the problem.
- If one fastener loosens it allows uplift movement which can loosen adjacent ones. Again not a factor with hidden fastener panels.
- Freeze-thaws of moisture around the gasketted head.
I'm dealing with these problems right now. The roof of our local community hall had an exposed fastener roof installed in the late 1980s. Most of the gasketted screws have loosened over time to the p0int where they leak - not enough to cause water to drip into the attic, but en0ugh to gradually rot the wood they are driven into. What do you do? Larger diameter screws work in a few cases, but for the rest you need to find sound backing and somehow patch several hundred of the old holes.
To me exposed and hidden fastener roofs are quite different animals. I'd consider using high-end shingles before I'd go with exposed-fastener metal panels.
Thanks for sharing Malcolm. I've not heard about this problem before.
https://www.greenbuildingadvisor.com/question/exposed-fastener-metal-roof-vs-standing-seam
I maintain a roof with snow load, the exposed fasteners jack up every single winter.
Great overview. The only thing I'd add is that it's worth considering what type of roofing you are thinking of using at the design stage. Because most trim on metal roofs is at the plane of the ribs, not flat the way it is with asphalt shingles, small changes in the design can make the roof much easier to detail and build. For instance, if the entry gable in the first illustration (image 1 0f 10) continued all the way the the eaves, it would eliminate a time consuming and potentially problematic transition.
Great Article!
Anybody have any advice for preventing "oil-canning" on standing seam roofs?
Also, Per the section on designer preferences, I'm curious how much embodied energy there is in steel roofs compared to asphalt shingles? ( I suspect copper and Aluminum have enormous amount of embodied energy?)
Rick,
Oil-canning can be minimized by a few things:
- Select panels with slight ribs in their profile (like these: https://www.westform.com/products.php?s1=commercial&s2=prolok_12_16 )
- Minimize the p0ints of attachment to the plywood sheathing except for those through slots on the panels.
- You can also add mesh or gasket underlayments which limit it.
- Remember that oil-canning is a purely aesthetic problem, and don't worry about it.
The question 0f embodied energy is complicated by metal being re-cyclable in the way most other roofing isn't.
Hi Rick and Malcolm.
I recently interviewed an architect who had used steel roofing and siding on his home (I'll be publishing some of the interview and the house in coming weeks). He commented that the steel does in fact have high embodied energy, but as you pointed out Malcolm, it is recyclable. He saw the durability of the roofing and siding and potential for reuse as a worthwhile trade off to the embodied energy.
Our installer placed a 1/2 Neoprene rope/gasketing down the center (vertically) of each 22" standing seam metal panel. This gives the panel a slight upward bow in the center, not noticable but all but eliminated oil canning. He also claimed it would help with expansion and contraction. Can't even tell this hump exists where the panel is crimped along the bottom drip edge. I do thing he stopped it maybe a foot short of the drip. A few years later our roof still looks great with noticably less 'oil-canning' than other installs in the area. He tacked that gasketing material at the top a bottom with a standard roofing nail at the center of where the next panel would lay before installing it parallel to the seam of the roof. They did a phenomenal job installing so I'm sure there are other factors at play here but that was one that I immediately noticed.
Malcolm, Brian, Jesse-
Excellent info! Thank you!
Great article. Thanks
What gets me is pro snap standing seam costs twice as much as AG steel, just because it was formed in a different machine.
Thanks for this information. I'm building soon and roof selection is on my to do list.
Are Solar PV arrays more difficult to install on metal roofing? I assume there are methods to seal rail mounts at roofing penetrations, but do the penetrations themselves initiate localized rust or corrosion?
Jim,
One of the advantages of metal roofing profiles with raised ribs is many solar mounts can be attached by clips without requiring any penetrations in the roof. Neither clips or holes in the panels should cause rust or corrosion.
An example: https://www.solarelectricsupply.com/solar-panel-mounts/roof-mounts/snapnrack/series-500-standing-seam-metal-system
I'm putting screw down Galvalume over 10" thick SIPs on a "hot roof". What should I use
for the underlayment between the metal and the OSB surface of the roof panels?
Foard Panel recommends just #30 felt for metal roofs directly installed (hot) on their SIP roof panels. Check out their “Siding and Roofing System Recommendations” guide for details: https://foardpanel.com/technical-notes
I’m about to put a standing seam metal roof on my Foard SIP roof, and was considering using Cedar Breather between the felt and metal panels, but never found a roofer who had done it before, nor could I figure out how to vent the metal roof eaves (I used cor-a-vent for the siding). And even the Cedar Breather instructions don’t have clear guides on how to vent the eaves or gable edges in a metal install (they have lots of detail for cedar shakes). So in the end, I’m going with just felt, per the manufacturer guidelines.
If anyone has more detail on a proven Cedar Breather install on SIP panels with SS metal roof, I’d love to hear it, as I still have a few weeks before my roof gets installed...
bentkibler,
There has been a lot of discussion recently on GBA around the usefulness off small gaps under metal roofs like the ones created by products like Cedar Breather. I'll leave you to come to your own conclusions, but my feeling is the gap is not an effective way to dissipate moisture, and may cause more moisture to accumulate than if the roofing was applied directly to the sheathing. I also have the same problems you do with imagining how to effectively detail the gap at the eaves so that it integrates with the drip-edge while still being open for ventilation.
My suggestion would be to either apply the roofing directly to the sheathing, or strap with 2"x lumber and create ventilation channels.
Rather than rely on the SIPs manufacturer to recommend an underlayment, I'd check what the roofing supplier requires. There are synthetic underlayments specifically designed for metal roofs. Felt can be problematic, as when it gets too hot it melts, adheres to the metal above, and then tears.
Thanks Malcolm! I'm inclined to agree with you, that an air gap directly under the metal might cause more condensation than it helps mitigate. Englert also recommends just 30# felt: https://www.englertinc.com/images/stories/documents/panels/1300InstallationGuide.pdf But of course, that recommendation assumes a normal vented plywood assembly, not OSB and SIPs.
FWIW, both my architect and timber framer suggested the ultimate venting solution is to just build a cold plywood deck over the SIP panels. If I were doing it again, that's probably the best choice, and the incremental framing cost is little more than a rounding error in the total cost of the metal roof.
At the top you mention "The industry also is working harder .... too hot, too heavy, noisy" but don't actually address the noise issue in the article. The noise of a metal vs an asphalt shingle roof is my main concern. And noise of standing seam vs metal shingles. Thanks for the article!
Good summary article. However, it did not address the wonderfully low emmissivity of a galvalume roof on the UNDERSIDE. If installed on discontinuous angled wood lathing, this makes for one heck of what I call a "shading umbrella" roof because the underside acts much like a radiation barrier, and the discontinuous angled lathing lets it vent out. In this way, you can have a vented radiant barrier roof system atop a sealed attic - best of both worlds, particularly in the south where air-conditioning is used a lot. See the GBA article we contributed to a month or two ago entitled "Designing for a Hot, Humid City"
Peter,
In the blog you link to https://www.greenbuildingadvisor.com/article/designing-homes-for-a-hot-humid-city there was some suggestions in the comments that the roof system you advocate using is perhaps not the most efficient for the climate. You replied that a response deserved more time than you had right then. I'd be interested in you revisiting that discussion to understand more about the various alternatives.
I just got the latest Fine Home Building magazine in the mail, and this article is the cover story. Why do I need the magazine if everything is already on GBA months in advance?
While there is some overlap, there is a lot of stuff on Fine Homebuilding that's not on GBA & conversely.
The aesthetics of the printed page also differ quite a bit from glowing screen, and it works even when the power is out (but you knew that...)
There was some hail damage to my 19-year-old asphalt-shingled roof last summer and insurance has agreed to pay for a replacement. I am considering a standing-seam metal roof, with the idea of thin-film solar panels affixed in between the seams sometime in the future. I am in the process of getting bids for the roof and have a couple of questions:
1. Almost all the contractors are proposing roofing over the existing asphalt-shingles because of the extra cost involved with a tear-down of the shingles. Could this present problems in the present or the future? Could the asphalt rot before the metal roof is due for replacement decades from now?
2. If I opt for striated panels to minimize oil-canning issues, could this create problems affixing the peel-and-stick thin-film solar panels? Anyone has experience affixing peel-and-stick thin-film solar panels to a striated standing-seam metal roof?
Thanks in advance.
Log in or become a member to post a comment.
Sign up Log in