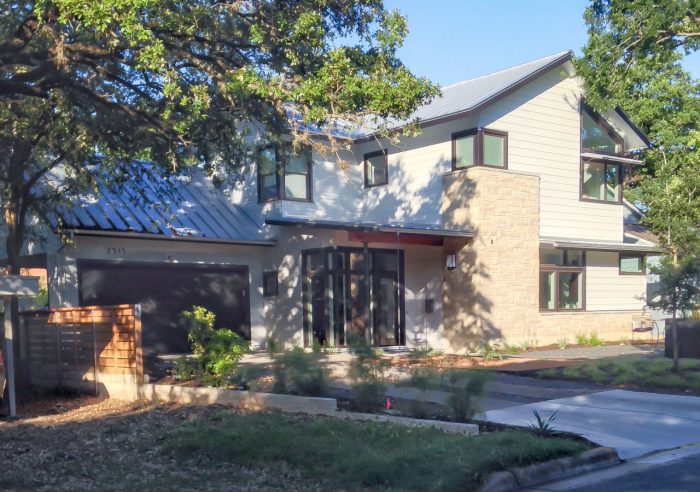
If you are interested in high-performance building for hot and humid climates, you probably have heard of Austin, Texas-based architect Peter Pfeiffer. Pfeiffer is an environmentalist, a building scientist, and an AIA fellow recognized for “his achievements in mainstreaming green building in America over the past three decades.” He’s been recognized by the National Association of Home Builders for his advocacy of green building and by Fine Homebuilding magazine for designing “The Greenest Home in America” in 2003. He was involved in the development of the U.S. Green Building Council’s LEED for Homes program, has helped manufacturers develop innovative building materials including radiant barrier sheathing, has long been involved with Austin Energy’s green building program, and is a member of the city’s “Zero Energy Capable Homes Task Force.” A regular speaker at architecture and building conferences across the country, Peter is outspoken, opinionated, and sometimes controversial.
If you are interested in residential architecture and spend some time in Austin, you’ll soon be able to spot a Barley/Pfeiffer home. Barley/Pfeiffer Architecture is the firm Pfeiffer started with his partner Alan Barley in 1987. From the beginning, their intention was to build homes that conserve energy and water, maximize passive cooling strategies in their hot and humid climate, and offer owners healthy and comfortable indoor living. Barley/Pfeiffer homes are commonly sided with a combination of metal, fiber-cement lap siding, and native-stone veneer. They have metal roofing, deep roof overhangs, awnings, and other shading devices, which are all part of their distinctive style. Barley/Pfeiffer homes are not necessarily modest in size, though they are not shy about explaining to clients that their lifestyle is just as important as the performance of their home when it comes to environmental impact.
Weekly Newsletter
Get building science and energy efficiency advice, plus special offers, in your inbox.
This article is only available to GBA Prime Members
Sign up for a free trial and get instant access to this article as well as GBA’s complete library of premium articles and construction details.
Start Free TrialAlready a member? Log in
21 Comments
The portions of the article about overhangs and the window designs were interesting. However, I think that the square footage of houses should be factored more into the conversation about efficiency. 2450 SF is a large house for two people, and the increased efficiency gains that are created by design and materials seem minimized in such a large house. Given that many of the builders who are leading the way in reduced energy use, improving indoor air quality and moisture control, are custom home builders, square footage and the size of houses in general seems to be conveniently omitted.
I agree with you Sarah. Unfortunately, many homeowners are willing to shell out a lot of money for a lot of gizmos and materials to make their homes "green," but few are willing to live in a smaller home. Until or unless that shift happens, architect and builders like Peter and many of the folks who hang around GBA, will have to do their best to make those homes as durable, healthy, and efficient as possible, and hopefully continue to nudge clients towards smarter and smaller plans, little by little.
Most thoughtful designers and builders probably have a tipping point - a line they won't go beyond where the client's wishes conflict too strongly with their principles. But before that point it seems reasonable to assume if you don't do the work someone else will, and perhaps your involvement can in some way mitigate the project's shortcomings. If I sat around waiting for the perfect clients - well I'd end up doing a lot of sitting around.
Sarah, I hear your point. But we also have to acknowledge the successes where we can get them. Consider this - many of these clients come into our office wanting to build larger homes, and we are happy in that we are able to show them how 2500 SF, through probing project programming and careful design, can live as well as the 3500 - 4000 SF they originally had in mind. Take your successes where you can get them; the world is not perfect.
While I agree that we should not make our homes too large, square footage is not the best way to judge the sustainability of a house. A very complex small house can use as many resources to build as a larger carefully planned one. Also, as homes get bigger, the ratio of interior volume (essentially air) to the envelope area (floors, walls, roof) changes, so when you build larger homes there is more air than envelope. I am not advocating building bigger (I lived in an 800 SF house for 13 years), but there are times and places when the right size is larger. And a well designed and built large house will use significantly less energy and water than a poorly done small one. My 2646 SF house is much smaller than any new homes being built in my neighborhood, and although there are only 2 of us, we both have home offices, and we use pretty much every part if it almost daily.
Fascinating stuff, thanks for including a hot humid article :)
I'm intrigued by the "no dehu" argument, as it goes against others advice (e.g. Risinger). I'd love to know what the metric for air quality they use to argue for open windows vs dehumidification. We've found the dehu to be wonderful in the shoulder seasons (dewpoint of 75 at 70 degrees is fairly common, but we don't have no fancy thermal syphon in our one story house ;)
Certainly opening windows for cross flow is great for VoCs smells and Oxygen, but given that the house is going to be closed for 6 months for AC (and 2/3 for winter) so you are going to have to manage those separately anyway. The trouble I see is that once you get a bunch of humid air in the house, it's hard to get it out other than running the AC, which then super chills the air (without a dehu).
Also I'd love to know what they do with directly west facing windows, impossible to shade with overhangs (probably pick a site and design that avoids them, I'm guessing!).
Thanks for the comment James. I will follow up with Peter with some questions and post the replies in a couple weeks.
James, your questions are good ones, and ones we have be playing with for a few decades as we advise our clients and builders here and around North America. Firstly, we expend lots of effort to educate our clients about being responsible for the indoor air quality of their homes: air-out new furniture, carpeting and padding, etc before bringing them into the home; watch what you use as cleaning agents; use a front-loading washer; always use your bath exhaust system (via a timer switch) and your kitchen exhaust (even when just boiling water) - and open your darn windows and doors once in a while. Take responsibility for your own health and well-being!
Regarding "no de-humidificaiton" - you may have missed my point on that. Firstly, we build the house (as explained in the article a bit) to minimize the infiltration of humid outside air, and the molds and pollen that come with it. From 1981 - 84 I was involved in the development of the early computer-based analysis programs (in grad school at UT - M Arch in Energy Studies) and later with passive-solar pioneering architect LM "Mac" Holder) to see that venting attics hurt a home's energy performance and IAQ more than helped it.
We have done multiple field studies and experiments on this over the past 35 years to hone our recommendations and have developed things like our "ventilated radiant barrier roof system" coupled with a tightly-sealed attic. (Mentioned briefly in the article but too much to go into here right now.) Matt Risinger, among other builders throughout America, now regularly employs many of these systems we developed.
However, before introducing our various system to the public and builders like Matt, we first employed them in buildings and homes we own and operate - and monitored their performance with temperature and humidity sensors - as well as experienced their performance characteristics personally ourselves by living and working in the homes and buildings employing them. Oakridge Labs has tested at least one of them (see attachment), and endorsed it; as did the Florida Solar Energy Center as far as back in the early 90's (when we were developing Kool Ply, which then became LP Tech Shield radiant barrier roof decking). So we have put a ton of time, research, money and field testing of the systems we employ in our homes to create, among other things, passive humidity and radiation barriers. (We have always believed strongly in testing our innovations and systems before yacking about them.)
Then, to further help with comfort, health and de-humidificaiton - we closely size the a/c units so they do a pretty decent job of de-humidifying and filtering the air due to longer run times and colder condensing coils. (From what you say, it sounds like you may have an over-sized AC system in your home, or slightly warm coils in the air-handler.) We use humidity sensors to see that we typically can keep the RH at-or- below 45% this way. On other homes, especially those where the clients entertain a lot (lots of latent load), or where the home will be left empty for multiple weeks a year (producing a need to keep humidity in check), we DO specify a separate de-humidification and ventilation system. (I have come to respect the Ultra Aire line of products for this.)
However, normally we try to employ the KISS principle when it comes to specifying systems and things in our clients' homes. 35 years and hundreds of custom homes (many clients of which we remain in close touch with) have proven to us that, in the end, folks simply don't care to maintain their homes anymore than they have to, so we avoid equipment complexity whenever possible and mostly rely on thoughtful project programming, design and building-science execution - rather than "Green by Gizmo" (a goofy catch phrase I started using over the past two decades...) Thanks for your interest!
Is there ever a compelling reason to use spray foam in a new house?
Stephen,
I can't think of one in our climate, and it does seem like it comes up here on GBA as the best solution to solve what were essentially design errors, but I don't know the first thing about hot, humid climates, so maybe this is the one region where it makes sense?
Yes! An unbeatable way to limit air, and much vapor infiltration; and to help create a passive humidity barrier that avoids making for cold condensing surfaces within the structure. I have found that, if applied carefully utilizing the better products with a lower Global Warming potential, SPF has become a game-changer in the industry since it was first introduced in the 1950's and widely so in the 1990's.
I'm going to disagree with my friend Peter here and say that you can very effectively seal a new home from heat/cold/air/vapor without spray foam. My own house was designed and built on the premise - you can read about the entire process in my column here, starting with this post: https://www.greenbuildingadvisor.com/article/the-third-times-the-charm.
I set out to design a house that didn't need spray foam and I believe I have succeeded. Keeping ductwork out of the attic is the first step to avoiding spray foam. In my case I used ductless HVAC, but I have consulted with clients who put ductwork in open web ceiling trusses and insulated on top of decking installed on the top of the trusses as I did in my house. It's not a standard design but it works.
I differ with Pfeiffer on a few points to be sure, but the best thing he said (and it's going to stick with me) is "if you can air condition above the dew point, you are doing yourself a favor". I think I'll adopt this as a design criteria, comfort above the dew point.
We just had a 78F dew point he in Michigan yesterday, which is about as bad as it gets here and that happens to be the temp we keep our house at. With a VRF heat pump and a dehu in the basement it keeps the RH at or below 50% and it's comfortable. Most homes around here have oversized ACs and maintain 70F to 72F and often only about 65% RH. Pfeiffer's statement makes it even more clear to me how problematic this is, it's honestly not as comfortable and also asking for more moisture related problems.
It is my opinion that open cell spray foam is essential in the attic in building a house in a hot, humid climate. It allows the ductwork to be brought into a semi-conditioned space. I would like to know more about the details on the flash and fill in the walls. My advice is to never use closed cell foam in a wood structure in hot, humid areas. You noted that the wall assembly often becomes a steam iron and this steam will for the most part be trapped from entering the house by the closed cell foam and it will eventually rot the wood exterior sheathing. Why wouldn't you just use open cell foam in the entire wall cavity? You said the wall R value in the wall cavities is R11? How is that achieved with flash and fill in a 2 x 6 wall? In most hot and humid areas where I see flash and fill or flash and batt used most installers install less than 1/2" of closed cell foam and then do a horrible installation on top of it.
>"It is my opinion that open cell spray foam is essential in the attic in building a house in a hot, humid climate. "
It's cheaper, greener, and more moisture-resilient to go with rigid foam board above the roof deck, which keeps all the structural wood inside the thermal & moisture boundary of the house. Spray foam on the underside of the roof deck is often the path of least resistance in retrofits, but less than optimal, and completely unnecessary in new construction.
An IRC 2018 code-min roof in zone 2 & 3 would be U0.030 (which is R33 "whole assembly", including the R-values of the roofing, nailer decks, structural roof, ceiling gypsum, and interior & exterior air films.) That can be met with as little as 5" of rigid polyiso above the roof deck. If that's too thick 2-3" above the roof deck with 5-6" of damp sprayed cellulose on the underside of the roof deck gets you there.
>"...the wall assembly often becomes a steam iron and this steam will for the most part be trapped from entering the house by the closed cell foam and it will eventually rot the wood exterior sheathing."
Not necessarily- rainscreened well vented cladding can fix 99.9% of those issues. But the described assembly was:
"R-5 continuous exterior insulation on the walls and another R-11 in the wall cavities, which is easy to achieve with 2×6 framing. ".
The continuous R5 would also protect the sheathing from exterior moisture drives if done with rigid foam.
Still the cost (financial & environmental) of closed cell foam as well as the lower performance due to the shorter path through the thermally bridging framing ( https://www.finehomebuilding.com/2017/07/10/closed-cell-foam-studs-waste ) makes a full cavity fill of open cell preferable.
But open cell foam is still not NEARLY as green as doing it with rock wool, fiberglass or cellulose. A continuous R5-R6 foil faced polyiso and R20 cellulose in the wall cavities would be cheaper, higher performance, and by far greener than anything that used spray foam in the cavities. The cellulose adds ample additional hygric buffering to protect the structural wood, and even a measurable thermal mass benefit.
Dana,
How many houses have you built or worked on in Zone 3?
Dana, you bring up many items worth discussing, but I have to sign off for now. Maybe we can catch up off-line ([email protected]). You, or someone, also asked how many homes we have done in Climate Zone 3. Answer - a good number (400 - 500) in climate zones 1 through 5 over 35 years. Lots of good lessons learned along the way...
Perhaps the single biggest lesson we have learned is this -
Houses without AMPLE overhangs are less comfortable and have MANY more problems over the years; the owners tend to get rid of them pre-maturely because of that. So things like rain-screens, moisture and humidity problems (including the "steam iron effect") all become background noise if the home or structure is simply designed to be relatively well-shaded and to shed the elements naturally - by design. Design fads come and go, but comfort and durability remain important to most folks.
Todd, my view on things you mention is to first create a robust humidity barrier to keep the humidity out of the house, and to utilize closed-cell SPF to eliminate cold-condensing surfaces within the wall structure so nothing gets moist (1" - 2" spray foam coupled with cellulose or rockwool). In this way, we play it safe from a mold, mildew and rot perspective - and achieve more like a weighted R-19 in our wall systems (although R-13 is plenty good enough in our climate zone 2). Hope this helps.
What do you consider a robust humidity barrier? I don't understand why you would ever put closed cell foam that is a vapor barrier inside a wall or roof assembly in Zone 2 or 3?
“It’s a sealed attic with a vented, radiant-barrier roof. It’s a good system,”
Am I correct that the attic is "air open" to the interior of the house, possibly with a small supply duct from the AC ?
Michael, if the home has a well-sealed attic coupled with a ventilated roof system of one sort or another, and the roofing underlayment is vapor permeable (30# felt) - we have not seen any need to even partially condition the attic w a small supply duct.
Log in or become a member to post a comment.
Sign up Log in