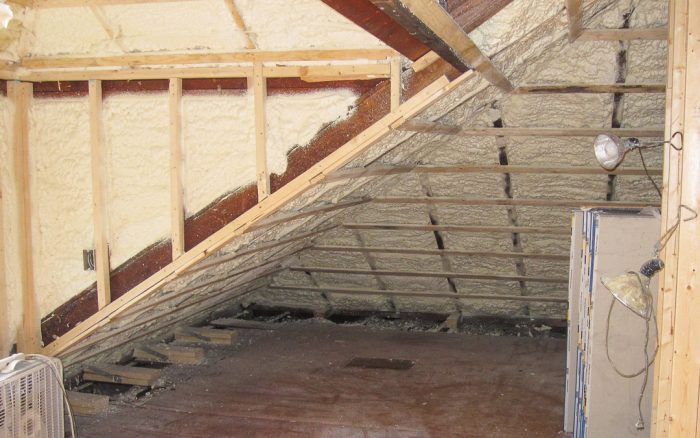
A GBA reader named 88Clayton is insulating the attic in his house with spray foam and has run into a problem: the level of insulation recommended by contractors is at odds with what the building inspector wants.
“I’m on the southern edge of [Climate Zone] 4,” 88Clayton writes in a Q&A post. “My spray foam contractor recommended R-20 of open cell. That’s what is currently sprayed on my roof deck. The code inspector came by today and is insisting on R-38, as if it [were] a conventional vented attic with loose blown fibers.”
With an air leakage rate of 1.7 ach50, the house is tight when compared with typical construction. Even so, the R-20 recommendation 88Clayton got from all four foam contractors is well below code required insulation levels for his climate zone (R-49 in the International Residential Code) and less than what he has in the walls of his house—R-25.
“It’s a bit strange to have walls that are better insulated than [the] roof,” he says. “Where is the realistic point of diminishing returns? I know the encapsulation itself has benefits that go beyond just raw R value, even though the inspector doesn’t quite get this, but perhaps I do need more foam thickness before the diminishing returns kick in.”
That’s where we begin this Q&A Spotlight.
It’s closed-cell foam you really want
When foam is sprayed directly on the underside of the roof deck, it should be closed-cell, not open-cell, writes Zephyr7. “Open-cell has moisture issues here!” he writes.
Open-cell foam is an effective air barrier, but it’s vapor permeable. Closed-cell foam is both an air barrier and a vapor barrier, so moisture is not able to migrate through the foam and collect in the roof sheathing.
“I’ve…
Weekly Newsletter
Get building science and energy efficiency advice, plus special offers, in your inbox.
This article is only available to GBA Prime Members
Sign up for a free trial and get instant access to this article as well as GBA’s complete library of premium articles and construction details.
Start Free TrialAlready a member? Log in
14 Comments
It's disappointing that after 15 yrs of being in the marketplace SPF continues to suffer from application related problems and continued cost pressures from less expensive competing products.
Regarding the supply of conditioned air at 50cfm per 1000 sq ft to the attic, that seems to be for a central air duct, which operates only when the a/c or heat is running. Given that a/c and heat don't run much here in the southern end of Zone 2A in the late fall, winter and early spring, it seems like continuous venting from the conditioned space into the attic would be preferable. Is there a reason why less-frequent-but-drier air directly from a duct would be preferable?
Alternatively, does it make sense to use a small fan (20-40 cfm), perhaps humidity/temperature controlled, to vent attic air to the outside and suck in conditioned air from the living space when the humidity or temp gets too high in the attic?
Humidity issues tend to be worst in winter and summer. In winter, warm/humid air inside the house can condense against cold(er) sheathing and other exterior surfaces, causing mold and rot. In summer, the very hot and humid outside air can condense if it reaches cold(er) interior surfaces chilled by the A/C system. In spring and fall, most US locations have relatively moderate humidity, and the lack of large differences between indoor and outdoor temperatures tends to limit the risk of condensation within building cavities. So, conditioning the attic when the air handler operates is a pretty good approximation of dehumidifying during only the highest-risk times of year.
An exhaust-only solution can work if the house is not super tight and not already depressurized by other exhaust fans. There is an additional cost in energy to condition the air that leaks in to replace the exhausted air. If going this route, exhaust air from the very top of the attic space.
There are various dehumidification options in 5.1.5. I'm sure they aren't exactly equivalent in effectiveness or energy use.
https://basc.pnnl.gov/code-compliance/controlling-moisture-unvented-attics-code-compliance-brief
Just want to point out that the use of the phrase "the code" implies one uniform code across localities. This is not the case as the version of the IECC in effect across the country varies from locality to locality.
At GBA "the code" usually means current IECC. Now whether states and localities wish to adopt the current code is of course up to them.
I somewhat disagree. "The Code" for most of us is whatever version of the IRC has been adopted locally. That governs all aspects of residential construction, including energy efficiency. The IECC is a broader code that governs both residential and commercial construction. The residential aspects of the IECC are embedded in the IRC, and the IRC folks work hard to synchronize the two. The IECC is sometimes a bit more flexible if designers with to use it, and the IRC allows for that as well. Still, the IRC is the top level "code" for most of us.
Of course, local exceptions and delays in adoption make everything more difficult. In NJ, we are on a sort-of 5 year cycle of code adoptions, which is totally out of synch with the I-code people's 3-year cycle. And we take exception to lots of good work from the I-code people because, of course, our politicians know far more than them.
Well ya, but I was thinking within the sphere of GBA articles that current IRC/IECC code is almost always part of the context absent more detailed information. Especially in a Q&A scenario.
When I reference the code here, I'm referencing the current 2018 International Residential Code (IRC), which as Peter pointed out is the current home building code book from the International Code Council and includes the most recent International Energy Conservation Codes where applicable to residential construction. I believe that Martin has always leaned on the most recent IRC for his reference too.
To Peter's point, this is a challenge for home building journalists. When we published content in FHB, from an architect or builder in one area, the work may or may not have agreed with the local codes in any given reader's jurisdiction. We got a lot of mail about that.
Readers were often appalled with what they saw in the magazine. If we published a horizontal deck railing, which codes in many areas do not allow, we'd be sure to get some feedback from upset readers. I can remember the subject line of one email that read, "Railings of Death."
We were always happy to get and publish reader feedback on safety issues, but the fact was often that the architects and builders were building within the law of the building codes that applied to their projects.
Railings of Death have just been approved in our latest code revisions. Canny investors in BC are lining up to buy shares in funeral homes.
You are talking about the roof decking on the other side of the insulation. So if the outside air is in the 90s the roof deck is probably 140°. What about the thermal bridging?
There is a product called aero barrier that could be used to get a similar air seal and then use dense pack to get the r value and eliminate the bridging.
Spray foam is so expensive that the benefits are oversold and substandard r values used. Then there is the fact the every job is a science experiment. Mix part a and part b at the proper ratios at the proper temps and apply at the proper thickness. I have smelled spray foam that has had a lingering order.
Here in Northern Ontario, the R-value varies depending on whether it's a roof with attic space (R-60) or without attic space (nom. R-31)
Looking at this from another angle: does it make monetary sense to spray foam all cavities? For the Ohio weatherization program, we’ve adopted the option of using rigid insulation (polystyrene) for spaces between joists, with spray foam only used as filler for leftover gaps. It’s used primarily in bandboard and basement/crawlspace applications (attics typically get blown with cellulose), but the reduction in expensive spray foam usually makes up for the increased labor cost. Just curious if anyone does this in attics.
As an aside, in my past architectural life I was intimately familiar with railings of death. Next to politics, religion and OSU/Michigan rivalries, there were few other topics that caused such gnashing of teeth and rending of garments.
I wonder what this foam will look like in a year once it's covered in drywall... I bet the foam will de-laminate as time marches on and wood works it's magic.
Did anyone do a blower door test to see if and where this foam leaks air before it gets covered?
Log in or become a member to post a comment.
Sign up Log in