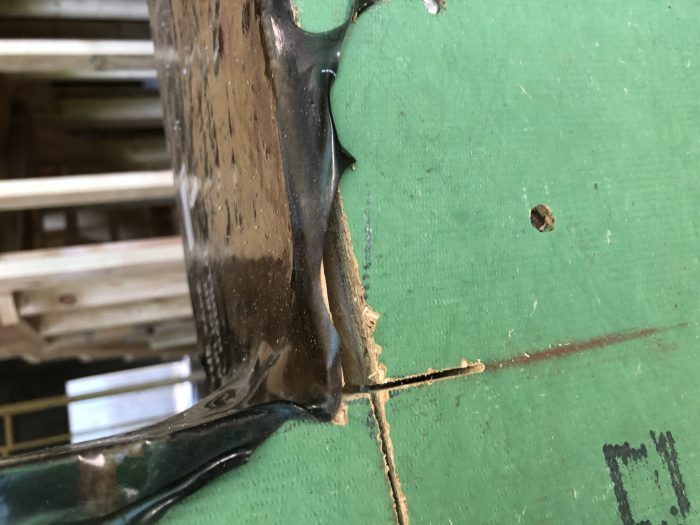
The Zip System R-sheathing that 88Clayton has chosen for his house is structural OSB sheathing with a water- and air-resistive coating applied to one side and a continuous layer of insulation applied to the other. When installed with Zip Tape, the sheathing provides the WRB for the walls and becomes an integral part of the house’s air barrier and thermal envelope.
But when most of the nails attaching the sheathing to the house have been overdriven, some disappearing into the layer of foam insulation bonded to the back of the sheathing, Clayton wonders just how effective any of this is going to be.
“The framers building my house severely over-drove 90% of my sheathing nails on the Zip-R,” Clayton says in a Q&A post. “It’s into the foam in many cases. Thousands of nails. Not to mention, their tape job is horrendous, with improper lapping.”
What to do next? Clayton isn’t sure whether it’s feasible to tape over every single one of the nail holes. Should he cover the ZIP sheathing with a layer of housewrap? Or, is there some other way of fixing this mess?
That’s where we start this Q&A Spotlight.
Consider a liquid-applied flashing
Spenceday suggests that Clayton consider using Liquid Flash, a liquid-applied alternative to ZIP Tape made by Huber, the same company that manufactures Zip sheathing.
“It may sound daunting,” he says, “but Liquid Flash may be an option here. It would be faster than taping to dab each hole with Liquid Flash and a putty knife. Same for fixing problematic tape joints or fish mouthing.”
Like Malcolm Taylor and other GBA readers, Spenceday raises another issue: if the nails are that badly overdriven, has the shear strength of the sheathing been compromised? What are the structural…
Weekly Newsletter
Get building science and energy efficiency advice, plus special offers, in your inbox.
This article is only available to GBA Prime Members
Sign up for a free trial and get instant access to this article as well as GBA’s complete library of premium articles and construction details.
Start Free TrialAlready a member? Log in
25 Comments
In general, most Builders today are “Cell Phone Builders”; many have Superintendents, and have no need to be on jobsites or get out of their air conditioned Ford 350. The lack of education is the norm in the industry. Many states (including TX) do not require a license, nor minimum education requirements. When I teach classes, my first question is - how many of you own a code book? - Usually is 1 out of 30-40 builders. Most classes I teach are attended by the same 30-40 builders, out of hundreds of available Builders in most metro areas, and it’s worse in rural areas. Every week I hear “I’ve been doing it this way for thirty years and you ain’t teaching me squat”… my usual answer is, you been doing it wrong for thirty years!
Most Builders or Homeowners hire draftsmen that charge a dollar per square foot for plans without full details or specifications, and it’s up to the trades to figure out how to build the house and know the codes, which almost always, they don’t.
Cities do not provide sufficient budgets to educate Building officials to the latest codes and even less for building science. Code enforcement is delegated to third party inspectors, and many of them pass their inspections to keep the account; as two HERS raters and verifiers here in Dallas told me awhile back “If I flunk my inspections, I may lose my job or account, and at the end of the day, we have to feed our families”. Many rural areas do not even have code enforcement.
Few Homeowners will study and research for good Designers or Architects and Builders who have good education and experience with good building practices, and they believe since the Builder is the “Professional”, he most know everything. The reality is a sad state of our industry!
It's Monday morning- is it time to pet the peeves yet? :-)
This article sports multiple instances of "sheer" in place of the intended "shear". While homonyms, they are not synonyms.
I have no experience with Zip-R. Is there something about it that makes it inherently more difficult to nail properly?
No. It takes someone spending one extra second to think about what they are doing and maybe an inline air regulator so the guy nailing the sheathing can dial his pressure down from the guy facing nailing LVL's.
This is a huge problem with framers. My town's building department started doing sheathing inspections about a year ago specifically because all of the issues listed in this article and how common they were. We've seen framers have to rip off sheathing panels that were so over nailed they were useless for shear strength. I wont even get into negative effects on air tightness causing numerous failed blower door tests and costly retrofits.
Lucky that the homeowner caught this one. Most houses are unchecked by building inspectors, homeowners, general contractors before the siding contractor shows up and hides in all.
Monkeying around on site this morning with my homemade panel (a scrap of plywood and foam), it's a bit trickier than putting sheathing directly over framing because of the different densities the nail travels though. Still nothing you can't adjust for, but I can see why this problem would occur a lot more frequently with Zip-R than regular sheathing.
IMHO, not as long as you follow manufacturer's instructions to the "T", which is seldom done; storing sheathing clean or cleaning sheathing before taping. following nailing patterns, proper taping and rolling tape.
I rather specify taped regular plwd/osb + taped outsulation with staggered seams + a 3D WRB for the same price of ZipR, giving me a better chance to possible overcome same installation failures and have no/less moisture problems, plus I believe that the rigid foam needs to be on the outside.
Armando,
Temperamentally I feel much the same way. Keep the structure as a discrete thing. Don't compromise it for energy efficiency by substituting materials, or using techniques like Advanced Framing. Then add the layers you need to meet your performance goals.
On my house, the framing crew was the one subcontractor that was willing to learn something new and do things right. We had a meeting ahead of time between me, the general contractor, and the lead framer to go over the detail drawings. That gave him a chance to ask questions and express concerns. They taped the sheathing seams, installed the rigid foam, detailed the WRB, installed the windows, and installed the siding as drawn. They complained that the taping was tedious, but did it.
The insulation and HVAC contractors weren't so cooperative. I didn't ask the plumbers or electricians to do anything very out of the ordinary.
This is the second article I've read on this site (the first was about window installers doing an incredibly poor job of installing windows) where the crew has ruined the entire job, either through ignorance or carelessness.
If the homeowner is posting questions on this site (and therefor must be reading articles on this site) then they must care about house construction. So why not be on site when the crews are going to be doing the work? Watch them install the first ZIP sheathing panel (or the window) and if they do it wrong have them change it. Why wait until the entire job is done and then cry "Oh, NO!"?
If you know more than the crew, and want it done a particular way (or just according to the manufacturers specs) then you should be on site to make sure that it's done correctly.
Frequently, the ability to pay to have a house build goes with having a job of your own.
Why not make them strip it off, and do it again correctly?
agreed.....that might be an expensive lesson for the builder, but how else are they going to learn if they don't read and comply with manufacturer's instructions.
As the homes, the materials we use to build them, and the systems we put into them get more and more complicated (or just different from what we are used to), and as builders, architects and other professionals tackle their first high-performance projects, there's a need for education. And it's not just the designer or builder who needs to understand both the why and how of the process. That info has to trickle down to everyone involved.
I've visited a lot of high-performance homes during my time at FHB and one of the things that always amazed me was how well-versed the homeowners were in the design, materials, process, and science of their projects. That seems like a sign that someone, likely the architect or builder, did their job really well. Another commonality among many of these projects were meetings with the architect, builder, and all of the subs before construction started and/or at crucial times during construction. Everyone has to buy into the project, or they can respectfully back out.
In fact we published an article on this idea a while back, which may be helpful:
https://www.greenbuildingadvisor.com/article/a-better-approach-to-design-build
Overdriven fasteners may be related to nail gun use, but I'd bet the severity of the overdrive is increased due to the foam backing.
With wood-to-wood contact between typical sheathing & framing, the framing will absorb some of the compression of the sheathing wood fibers and halt the nail at a certain depth. But the foam backing probably does not do this and therefore allows the overdrive to go much farther in, potentially weakening the connection a lot more.
David,
The difficulty is also increased by the margin by which the compressor is set to cycle. If it is too large the gun might be driven by air between say 85 and 110psi. The structural engineer I use hates owner-builds because they typically use small portable compressors, and tasks like nailing off sheathing produce waves of over and under driven nails.
Malcom, I believe it. When I've done my own work I usually set the gun to leave the nail a little proud and then true them up by hand. Takes more time though...
In the Seattle area, shear nailing inspections are so routine for every jurisdiction that only the newbies screw it up. My framer is paranoid about failing inspections so he has the crew set the margin of error of the guns to slightly underdrive the nails rather than risk overdriving, and then the next day I hear him banging on the exterior with a hammer to finish any proud nail heads.
These guys have been working for me for 10 years and I know all their idiosyncrasies. Another builder called them morons. I replied, "They may be morons, but they're MY morons." I can predict everything they do. I know exactly when to intervene. If they refuse to attach rigid roam I just wait 2 weeks till they're short of cash and they're happy to bring extra ladders and helpers and git 'er done!
The secret is to thoroughly understand the weakness of your subs. A first time builder doesn't have this luxury. I know each guy of my technical trade subs. If there's a new employee I watch his work like a hawk because I know he's still learning, even if the company itself is 25 years old.
Without independent supervision the sky is the limit for mistakes. Some mistakes are so grotesque it's tempting to every metal object in your tool belt at the clown.
Just remember that if there are 3 possible interpretations of a given operation, there's only a 33% chance your workers will perform it the way you think it should be done.
@ Stephen - "...if there are three possible interpretations, there's only a 33% chance they'd do it the way you think it should be..."
You, sir, are an optimist. Personally, my experience says the chances are less than 10%...
LOL!! Very true, Andrew. The optimist says 33% the realist says 10% and the pessimist says 3%
"The secret is to thoroughly understand the weakness of your subs."
Haha! Could have been written by Machiavelli.
Seems to me the foam between the framing and OSB will lower the shear value regardless of whether the nails are properly driven.
It does, but Huber provides nailing schedules to compensate depending on the required shear loading.
I'm curious to know how close Huber advises spacing. A professor of civil engineering once told me he gets nervous when nail spacing is closer than 4" OC.
Charles,
A link to the nailing schedule: https://www.huberwood.com/assets/pdfs/ZIP-R-Sheathing-Installation-Guide.pdf
We are in a high seismic zone here on Vancouver Island, and our engineers routinely call for nailing 2", 3" and 4" oc for shear walls.
I've seen callouts for that kind of spacing, but at what point do you split the stud? The professor must have had a reason for concern. In the field of the panel and at the plates you can stagger the nails, but usually not at the vertical edges.
Log in or become a member to post a comment.
Sign up Log in