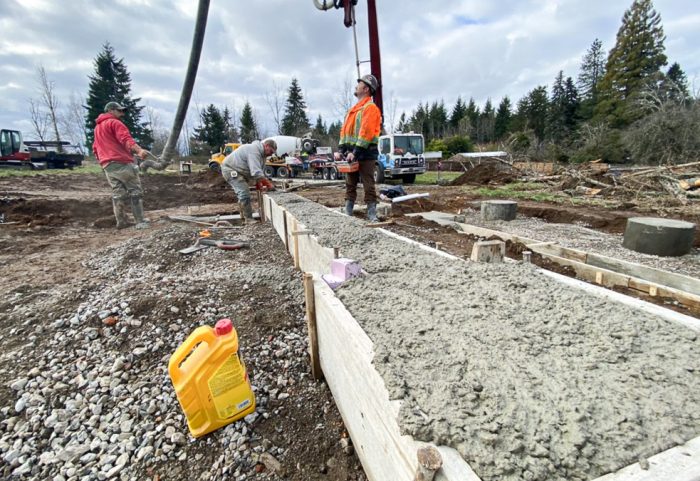
For a house under construction in Damascus, Oregon, Birdsmouth Design-Build opted for a concrete-free slab-on-grade, an innovative detail the company had used in the past to reduce embodied carbon. Then the company went a step further by ordering slag concrete for those parts of the building where using concrete was unavoidable.
The 2300-sq.-ft. house and 800-sq.-ft. garage each had a slab-on-grade foundation. In the house, layers of gravel, insulation, and plywood take the place of a conventional concrete slab. In the garage, that kind of substitution wasn’t possible, but swapping slag concrete for standard-mix concrete will significantly reduce the carbon content of the concrete. Slag concrete also went into footings, stem walls, and outdoor flatwork.
Concrete is a major greenhouse gas contributor, due mostly to the high carbon emissions associated with Portland cement, the binder that holds coarse and fine aggregates together. An estimated 8% of global greenhouse gas emissions can be traced to concrete. In slag mixes, 50% of the Portland cement can replaced with slag, a granulated industrial byproduct produced in an iron blast furnace (even higher amounts of slag are possible). It’s one of several supplemental cementing materials, or SCMs, available to designers and ready-mix plants.
Birdsmouth Project Manager Jessica Canales said the company is always on the lookout for ways to decrease the carbon footprint of the houses they build. Concrete-free slabs, which Birdsmouth founder Josh Salinger details in this Fine Homebuilding article, are a big help. But concrete could not be eliminated completely, and for components that had to be made from concrete switching to a slag mix was another step in the right direction. When the company found that its local ready-mix plant, Wilsonville Concrete, could supply slag cement they decided to give it a try.
Birdsmouth’s efforts coincide with interest from the Oregon Department of Environmental Quality in lowering the carbon impact of public works projects and spreading the word about the potential in residential work. The department had conducted some case studies that compared the performance and workability of slag concrete with conventional blends for several projects in the city of Portland. The department’s interest spilled over to the residential arena, and to the Birdsmouth house under construction in Damascus. A case study on that project is upcoming.
Batch plant sells lot of slag concrete
Frank King, sales manager at Wilsonville Concrete, says the company has been offering slag concrete for about eight years, and that as much as 90% of the ready-mix that Wilsonville sells has at least some slag cement in it.
“My goal is to send almost every load out with some portion of slag cement in it,” he said in a telephone call. Why? “The environment, number one. Number two, it’s great for concrete. It’s kind of like a Hamburger Helper. It just makes the concrete better.”
Just how much slag is added to the cement depends on how the concrete will be used. Flatwork and slabs typically get a 20% slag mix, a point at which most installers would not be able to tell the difference between it and a 100% Portland cement mix. For footings and foundations, where forms don’t have to be stripped immediately and finishing requirements are less, King usually suggests a 50% slag blend.
Slag concrete takes longer to set, so finishing can be slower. On a large commercial job, such as a warehouse floor, finishers normally might wait a couple of hours before tackling the surface with a power trowel. With a slag blend, they might have to wait for eight or 10 hours before the surface can handle the trowel—and that extra time eats into profit margins. (Most residential jobs, however, are not power-troweled, so finishers are not required to wait as long.)
Slag concrete also is slower to come to full strength, King said. At 28 days, the standard benchmark for a strength test, the slag concrete lags behind conventional Portland cement blends, but by 56-90 days, the strength of slag concrete actually exceeds that of a conventional blend.
Using slag cement instead of Portland cement typically does not affect the cost of the ready-mix, King said. However, when the slag content reaches 50% to 60%, the batch plant might recommend adding accelerators, and those extra admixtures can push the cost up.
Research was key in finding the right supplier and blend
At the start of her research, Canales assumed it would not be much of a challenge to find a slag mix for the Damascus project.
“I was feeling like I should be able to go online and find a mix design with slag to give to any of our suppliers,” she said in a telephone call. “But what I learned is that it’s not as simple as following a recipe. The quality of ingredients plays a big role in the product that you get.”
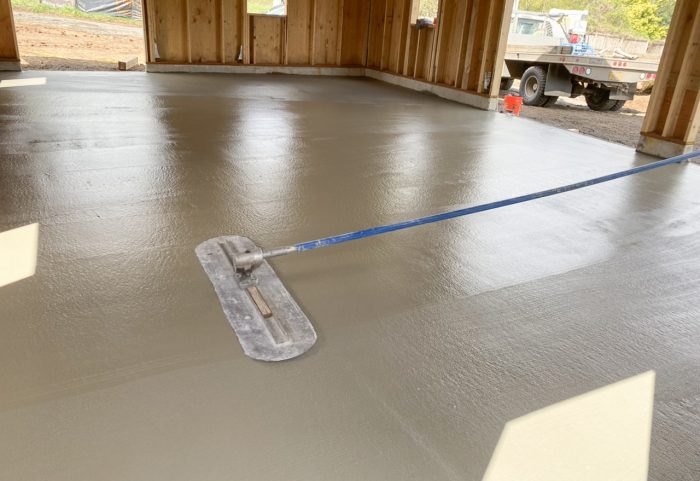
With advice from King at Wilsonville, the concrete mixes used at the house in Damascus were tailored for specific locations. The more slag the mix contained, the harder it was to finish smoothly, Canales said. The concrete set up faster, so installers had to work quickly, but the concrete also took longer to cure, and trowels and other finishing tools tended to drag over mixes with a higher slag content.
Footings and stem walls—which won’t be visible when the house is complete—got a 50% air-entrained slag mix. The garage floor slab as well as flatwork that was to serve as a base for pavers got a 30% slag mix, making for a slightly better finish surface.
Temperature also had an impact. The concrete in Damascus was poured in February and March when temperatures were above freezing but still cold. Concrete mixed with slag cement tends to cure more slowly even on warm days, and low temperatures slowed the process even further. As a result, forms could not be stripped as quickly.
Canales estimates that between labor and materials using slag concrete increased costs by about 5%.
“It definitely was challenging,” she said. “It would be an option for projects when we would do a pour in the summertime. That’s ideal. Doing pours in the winter with higher slag content is probably not recommended.”
How likely Birdsmouth is to use slag concrete in the future is still an open question. Having gone through the process once, Canales said, the firm is at least in a better position to communicate the challenges they encountered to their concrete installers who might be reluctant to bid on a job with too many unknowns.
Another factor, Canales said, is how slag concrete would do as a finish floor. Although the garage floor slab was troweled smooth, it was not ground and polished as an interior concrete slab might be. The company isn’t ready for a wholesale adoption of slag mixes just yet but appears open to using the blends in the future.
Project focus of a new case study
Jordan Palmeri, scientist and senior policy analyst for the state’s Department of Environmental Quality Built Environment Program, is at work on a case study about the Damascus project, part of an effort to spread the word about low-carbon concrete mixes and their potential to reduce embodied carbon in both public works projects and residential building.
When the case study is ready, it will be posted here.
Case studies about the use of slag cement in sidewalks have already been published, and Palmeri will wrap up this report when final strength test results are available. The Portland public works trials tested slag mixes of up to 50%, comparing their performance to 100% Portland cement blends. Results were encouraging. For example, the report on one sidewalk test said in part:
“Overall, the low–carbon mixes met the city’s concrete performance specifications, were well received by the concrete finishers, were cost–neutral or less expensive, and are performing well in the post–project visual inspections—all while reducing the carbon footprint of an average sidewalk ramp by 23–34%. The main difference between the 100% cement and lower–carbon mixes was the [duration of time for] strength gain, although all mixes achieved the specified compressive strength of 3000 psi by day 14–well ahead of the 28–day specification.”
New requirements for concrete used in Portland city projects start at the beginning of 2023.
The use of slag cement has not been as typical in residential work as it has on bigger jobs, Palmeri said, because most residential builders are using smaller concrete producers, and smaller ready-mix companies are not as likely to have a second silo for storing slag cement. Even so, slag cement has been readily available in the Pacific Northwest, sometimes at a lower cost than Portland cement.
“From a producer’s perspective, they will deliver any mix you ask for,” he said in a telephone interview. “They’ve had low-carbon mixes available for a really long time. They just need to be asked for them.”
Concrete finishers who aren’t familiar with slag cement might need a little coaching the first time in how differently a slag mix might behave, particularly in cold weather where setting times are slower. The use of accelerators in the mix, and something as mundane and unpredictable as a traffic delay that throws delivery time off, can make an introduction to slag cement less than perfect.
“I wouldn’t overplay the barriers in this case study,” he said of the Damascus project. “Literally, it’s the first time these folks have ever worked with a low-carbon mix.”
Palmeri says slag cement has a lot of potential for reducing the carbon impact of buildings—particularly when used in foundations.
“There’s very little risk,” he said of that application. “You don’t need high early strength, and there are no special finishing requirements. Foundations should be a go-to and then you should feather up your SCM content in your flatwork mixes as your finishers get used to it. When it’s really cold weather, your challenges with working with these kinds of mixes are going to be magnified. Just as really cold weather affects concrete in general.”
Ultimately, Palermi would like to see low-carbon concrete mixes become the default on residential projects and built into buying guidelines for state work. Given the long distance origins of slag and the gradual decline of fly ash availability, he’d also like to see a wider acceptance of other SCMs, such as ground-glass pozzolan.
Where to find slag concrete
The Slag Cement Association (SCA), a trade group for the industry, says slag cement is available in “various U.S. regions and states,” and it maintains a searchable database at its website to help builders find a supplier.
Drew Burns, the association’s executive director, said in a telephone call that slag cement may be harder to get in some rural areas where it has not typically been used. Nationally, growth over the last five years has been brisk, he said, with double-digit year-over-year increases in shipments in the last three years. Most of it, however, has been used on big infrastructure projects where durability and environmental sustainability have been driving concerns.
The domestic supply of slag has declined as the number of iron and steel mills has dropped, he said, but logistical pipelines for importing the material have been created. U.S. supplies can come from either Asia or Europe as well as domestic steel mills.
Although Burns did not have statistics on exactly how much of the U.S. slag supply goes to residential work, there’s no question that it’s a young market.
“It is a new material and historically our industry has been using ordinary Portland cement as their primary ingredient,” he said. “When you switch to a new material there are caveats or differences to curing and finishing practices that a lot of residential contractors aren’t necessarily privy to compared to larger contracts that are working on infrastructure projects or highway projects.”
At the National Ready Mixed Concrete Association (NRMCA), Colin Lobo, executive vice president and head of the engineering division, said another reason may be cost. Fly ash has been cheaper than Portland cement in the past, while the cost of slag was about the same. That gave the low-carbon edge to fly ash blends, not slag mixes. That situation, however, could be changing as the availability of fly ash declines along with the number of coal-burning power plants.
Burns said there are resources at both the SCA and the NRMCA to help contractors and ready-mix plant operators to learn more about slag cement, and get off on the right foot should they decide to begin using it.
Changes in building codes and public policy also could help make slag and other SCMs more appealing, if not required outright, Palmeri said, including a greater reliance on Environmental Product Declarations (EPDs) in choosing the most appropriate building materials.
“There’s an urgency in climate change . . . ” Palmeri said. “We’re trying to develop policy that would require this. We have procurement policies in the city of Portland that say we’re only going to buy products with EPDs and that the carbon footprint of those products needs to be X. We just developed those at the state level for [Department of Transportation] purchases of concrete, asphalt and steel. We’re hoping that policies for public procurement of materials with EPDs and setting carbon limits makes its way into the private market as well.”
For residential concrete finishers and builders, it may just be a case of learning more about the benefits of slag cement, and then getting the right advice about using it. Palmeri recalled a conversation he had with a progressive builder, one who was “always thinking about the next thing.”
“Once we talked through this concrete work he asked me, ‘Why is this not just the default on projects?'” Palmeri said. “‘Why do we have to order this special when it’s something they already have? And I thought it was the most brilliant question.”
Scott Gibson is a contributing writer at GBA and Fine Homebuilding magazine.
Weekly Newsletter
Get building science and energy efficiency advice, plus special offers, in your inbox.
13 Comments
State departments of transportation have decades of experience with fly ash and slag in concrete roads and bridges. Roman engineers used volcanic ash in concrete to great advantage in antiquity. A google search will yield a large body of research, mostly positive.
Interesting. I am always amazed at how high quality the different blends of Roman concrete and cements were. Of course, most of Southern Italy does not have constant freeze thaw cycles. But still, to stand in a building like the Pantheon, with a 2000 year old concrete dome, is amazing........
This is great. It is essential that we begin to reduce the carbon footprint of concrete production and use.
While the use of slag is great for roads and infrastructure, I would raise two points of caution. First, there is no reason why, in many cases, residential buildings can't be 100% concrete free. Thousands of houses on the East Coast have been built on treated wood pilings driven into the ground without footings (the bearing capacity is set by the friction resistance of the piles-typically at 15,000 lbs. or more). These houses have lasted decades, including through big storms/tidal surges. While many of these houses have slabs poured for parking cars, this is not necessary-gravel works just fine. So first and foremost we should think about how to reduce the use of concrete and cement products in residential building.
Second, scientists must do very careful testing of slag concrete to make sure that over the short and long term, chemicals or heavy metals harmful to humans or the environment do not leach out (or even off gas) in the manufacturing process and then once installed. I presume slag, like fly ash, can contain some nasty stuff so it is important that the manufacturing process is environmentally compliant and, once the concrete cures in place, these materials stay put and do not end up causing issues for the environment or the inhabitants.
Not all slag is created equal. Good point.
I'm interested in concrete-free garage floor options. Gravel on dirt is one option, but I wonder about moisture from the ground coming up into the building. You can add a vapor barrier layer under the gravel, but then I wonder whether drips from wet cars parking will collect on top of it. I think there is probably a simple solution that works well but I'm not sure exactly what it is. The code requirement that it be non-combustable rules out a lot of options, including a lot of commercial products sold for over-layers on garage floors.
There's an old driveway style that is concrete runners with grass between them. I see that it's being revived as a way to reduce storm water runoff. But I don't see a way to apply that to a garage floor, with the requirement that the floor be non-combustable. Maybe the solution is a car port instead of a garage?
Soil cement?
Apparently it’s been done. You still need some Portland cement and the right kind of soil but seems like it could work.
Is anyone on the forum familiar with this application?
I may be wrong but soil cement seems like all it does is substitute poorer aggregate for that usually used in concrete. You mix the cement with soil, which as well as the typical sand and larger aggregate, can contain clay and other components found on the site, and then rely on compaction to improve strength. If you want the same PSI as regular concrete, you would need a higher cement ratio than typical concrete, not less.
It that sense it's a lot like the rammed earth construction used in walls. The benefit from a carbon reduction standpoint must be the substitution of imported aggregate for that you can find on site. Used in a garage where the depth is shallow and that experiences p0int loads, it doesn't seem like it would hold up very well.
Typical mixes use roughly half as much cement but they are not as strong as concrete.Strength would depend upon the precision of the mix, the type of soils, the moisture content of the soils and the ability to achieve sufficient compaction.
It is by no means a slapdash process but could produce a somewhat cheaper slab with half the cement.
There are possible issues with brittleness and cracking in all but the best jobs.
I am only personally familiar with large scale infrastructure applications. For me, the question is if it can work for auxiliary residential applications like driveways, patios and garage floors.
A carport with gravel instead of a garage is certainly the simple solution.
I wonder if you could convince your local building department that a mass timber solution is fire safe even if it is technically combustible. This would probably require either a very lax jurisdiction or the sort of testing that is not feasible on a residential project. It makes me think of the wood alley in Chicago: https://en.wikipedia.org/wiki/Wooden_Alley This may not be reasonable or worth the effort for a variety of reasons, but could theoretically be possible
The house I grew up in was on a hill sloping down from the street. Our carport had a wood floor. This wouldn't meet today's codes for noncombustible materials, but it seemed to hold up relatively reasonably otherwise. I was a kid though, so I may not have been fully aware of any maintenance annoyances.
Yes, a carport with a gravel floor is likely a good plan. There's a giant oak tree right next to the driveway, so one of the challenges is keeping the squirrels from stashing acorns in vehicles. It could have wire mesh walls to keep the rodents out, but then the challenge is to keep it from looking like a zoo cage.
On the other hand, for an EV, an enclosed and insulated garage means less energy spent in the winter keeping the battery warm, so maybe that makes up for the carbon emissions of the slab?
I also wonder about covering a wood floor with galvanized steel sheets. How thick would the metal need to be to satisfy the code requirement for non-combustible? I don't think the requirement is clearly defined. Or maybe galvanized steel sheets as a robust and non-combustible vapor barrier over hard-pack gravel or rammed earth, with nothing combustible in the assembly. You can use a lot of steel and still have less CO2 impact than an 4" concrete slab--I calculate 0.6" thick steel would make it about equal, so 1/8" steel would have 1/5 the carbon impact of concrete, or 1/16" steel 1/10 the impact.
Charlie,
Carl Seville did a really nice carport at his place with storage built into the walls.
Thanks Malcolm. I think that is the best-looking carport I have ever seen. A good inspiration.
Charlie,
It's nice enough that it doubles as outdoor covered living space - which a a great idea.
Log in or create an account to post a comment.
Sign up Log in