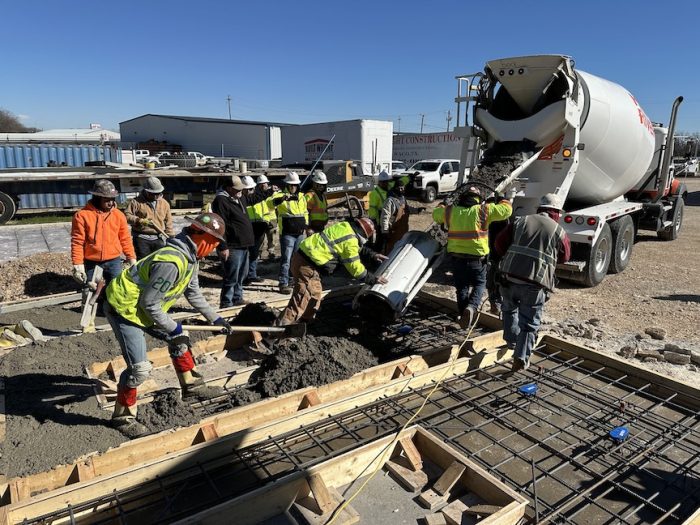
What is the greatest thing since sliced bread? If you think about this cliché, it’s actually setting a low bar. The first automated bread-slicing machine wasn’t introduced until 1928. Prior to that, for approximately the duration of human civilization, innovation and variation on breadmaking was vast. Wheat was first domesticated over 9000 years ago in the Fertile Crescent. Ancient Iberians were the first people to use ale yeast, or barm, as a leavening agent, circa 6000 BCE. And around 1000 BCE, the Mayans perfected nixtamalization, the process of taking something of little nutritional value (corn) and transforming it into a source nourishment (masa harina). These are noteworthy moments. Industrial slicing, on the other hand, was indicative of an era when softer “modern” loaves became the norm, owing to milling and production that removed essential nutrients from the end product, but also gave it a longer shelf life. Sliced bread… yay.
There is no equivalent cliché for concrete, but maybe there should be, only something that does justice to the standard bearer in question. Something like, _____ is the greatest thing since Ancient Roman concrete. (Okay, it doesn’t exactly ring.) One option to fill in the blank is Ultra-High Performance Concrete (UHPC), which infuses high-strength steel fibers into its mix design. Another option is so-called green concrete, which substitutes upcycled waste materials like blast furnace slag and fly ash for high carbon-emitting Portland cement; or even suitable concrete alternatives that span millennia, from strawbales to hempcrete.
But what if the standard mix design of a traditional concrete—approximately 70% aggregate (e.g., rock and sand), 15% cementitious material, and 15% water—could remain nearly the same, unadulterated, while being rendered cheaper, stronger, and cleaner?
Green concrete = low-cement concrete
In Waco, Texas, the city’s Independent School District (ISD) is constructing a new elementary school (Kendrick Elementary, which broke ground on March 28) using internally cured concrete, a solution that uses nano-modified cement (NMC) admixtures to disperse moisture evenly when the internal humidity of the concrete begins to drop. This results in greater hydration for the cement and yields a more durable concrete. The low-carbon part is due to the fact that there is simply less cement in the mix design—up to 30% less!—and no supplementary cementitious materials (SCMs) like slag or fly ash to make up the difference. Increasing SCMs in the mix presents “a complex material change which sets the stage for bad concrete,” according to Chris Bennett, owner of Bennett Build, a consultancy focused on sustainable concrete solutions.
“The cement doesn’t care if you’re adding some secret ingredients,” says Bennett. “If you are a better steward of the hydration cycle, meaning if you’re activating more of your cement, then you’re going to need less of it.” Given his trade, Bennett hasn’t completely soured on the use of fly ash or other admixtures that can reduce the concrete’s embodied emissions, but he stresses the caveats. Longer curing times is one; responsible sourcing and proper handling of certain toxic byproducts are others. But what he finds most troubling is the premium that is now associated with certain green solutions. “Ready-mix suppliers are enjoying amazing prices on fly ash and slag, which traditionally they have not. There’s a scarcity of SCMs because they’re now thought of as integral to low-carbon concrete.” He cites developers that have increased their budgets up to 30% to be considered sustainable. “But in actuality, cement is very expensive. So, if you’re reducing the cement, the cost for low-carbon concrete mixes should be going down!”
Bennett was part of the Waco ISD project team, along with Brightworks Sustainability, architecture firm O’Connell Robertson, and structural engineer Structures that sold the school district on this approach, first by leaning on its associated cost savings, then following up with the carbon savings. Both are appealing, obviously, which only left the most important consideration: how will it perform?
Ryan Stoltz, an associate principal with Structures, acknowledges some of the downsides associated with green solutions. “Sometimes it’s worth it,” he says. “You get some attention for being sustainable and it doesn’t compromise too much. Maybe you don’t need the product quite as strong, or having delayed strength is okay. But this kind of nano-modified cement that we’re using is taking a basic mix, not adding anything scary, making the hydration process more optimized, and achieving high early strength with some chemical admixture. At the end of the day, you’re just reducing the cement. That’s very attractive in a way I hadn’t seen in other green solutions. You take what’s there and make it better and more efficient.”
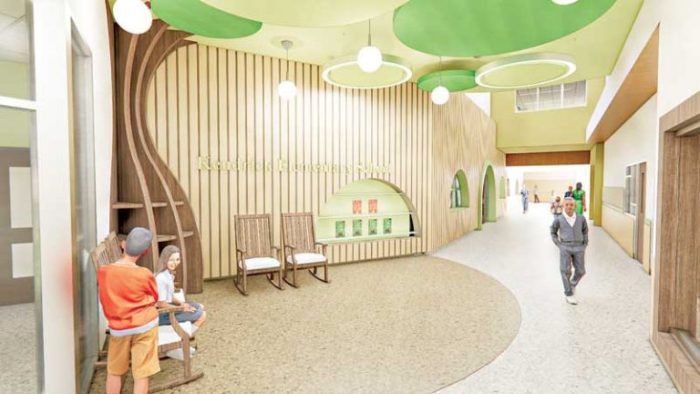
Why Waco ISD matters
Bennett estimates the costs savings for the school district to be in the low seven figures, which of course is critical for a publicly funded project. And because it is a public project, all the data and analyses related to performance and break tests are publicly available, as is the mix design, something that Brightworks’ principal Chris Forney compares to “baking gluten free.” He concedes that it will take time for larger developers to get on board, much like convincing clients on the importance of energy modeling, building commissioning, and conducting life-cycle assessments—all things that still have their detractors but were practically unheard of 20 years ago.
In that spirit, Forney cautiously calls this milestone “a dip of our toe in the pool,” and professes knowledge that this approach could be even more low carbon. “We could not get the ready-mix company to make the reductions that we know are possible. There’s evidence of that in the break tests for a 4000 psi mix,” he says. (4000 psi mixes typically require 28 days of curing.) “They were getting breaks that were significantly higher because we were getting such better utilization out of the cement in the concrete. So that tells us we can and should be pulling out more cement.”
The behavioral performance of low-carbon concrete will likely always be something that people question, regardless of its constituent ingredients. After all, the elemental design of standard concrete has remained unquestioned for a long, long time, and convincing contractors (and clients) to accept “a new math,” according to Kristina Abrams, an architect with O’Connell Robertson, will require “education and patience” and, above all, a “nurturing” approach.
For Waco ISD, the pre-bid process took an unconventional approach. In order to submit a bid, qualified contractors in the state of Texas who expressed interest in the project were required to undergo a free training and certification process, and ultimately demonstrate a proficiency in building with a prescriptive mix design. Last October, Waco ISD hosted a mandatory, two-day pre-bid mockup for potential bidders for the mixing, placement, finishing, and polishing of three 20′ x 20′, 4-inch thick slabs. For such a pour, standard mix designs would require 560 lbs. of cement; this test pour used just 430 lbs. and achieved compressive strength, or 28-day break results, well in excess of 10,000 psi.
Provided each team’s test slab achieved a minimum Mohs hardness score of 7 (equal to quartz) at the end of day one, the polishing phase commenced at 9am on day two. Those in attendance who performed successful pours of the internally cured concrete with NMC admixture became certified with the admixture manufacturer. Indeed, nurturing demands patience, on the part of the student and the teacher.
“This nano-modified cement is a huge innovation,” Abrams says. “Owners of publicly funded projects are not currently willing to pay a premium for low carbon concrete.You have to start with cost, and [this innovation] cannot be more expensive” to be effective and gain traction in the market. “There’s a huge responsibility put on our industry, as architects, to acknowledge that there’s an opportunity for carbon reduction that very few people are digging into.”
_______________________________________________________________________
Justin R. Wolf is a Maine-based writer who covers green building trends and energy policy.
Weekly Newsletter
Get building science and energy efficiency advice, plus special offers, in your inbox.
4 Comments
That's an exciting development! Another advantage of reducing the amount of Portland cement is reducing the risk of cracks--most people don't realize that the "stronger" the mix--i.e., the more cement in the mix--improves compression resistance but also makes the concrete more brittle and prone to shrinkage cracks.
I learned about water content at an early age; my dad had been the site engineer for placing many miles of concrete interstate highway here in Maine in the 1960s, and he proudly pointed out that his sections of highway hadn't cracked in 40 years. (Some portions had been out-sourced to private engineers who saved money, and ended up with concrete that had to be replaced after 20 years.) My dad's sections had very low water content and had to be mechanically placed, vs. manually screeding slabs the way we typically do on residential projects. The concrete is still there today, though now capped with asphalt. Just yesterday my wife asked why a certain section of interstate had a lot of potholes; that was the section that was just asphalt, without a concrete layer.
He also used low-water mix on the large walkout basement addition at the house where I grew up; zero cracks or water infiltration. He attributed it to slow, damp-curing, which I always recommend, though builders rarely follow because standard practice is to pull the forms and "dry" the concrete as quickly as possible. But damp-curing allows for better hydration and a tougher result.
"4000 psi mixes typically require 28 days of curing." Isn't 28 days required by definition?
No, 28 days is used mainly out of habit. You can also do 7-day (or 3-day, or 14-day, or any number that you want). Conventional mixes usually gain about 2/3 of their strength after 7 days and 99% after 28 days, but site conditions and non-standard mixes will vary.
Charles,
I've used high fly-ash concrete that had a 50+ day cure. As Michael said, concrete has a high initial increase in strength, so there aren't many circumstances when the length of the total cure matters much. In house construction concrete usually gets damaged in the first few days by stripping the forms or back-filling too soon.
Log in or create an account to post a comment.
Sign up Log in