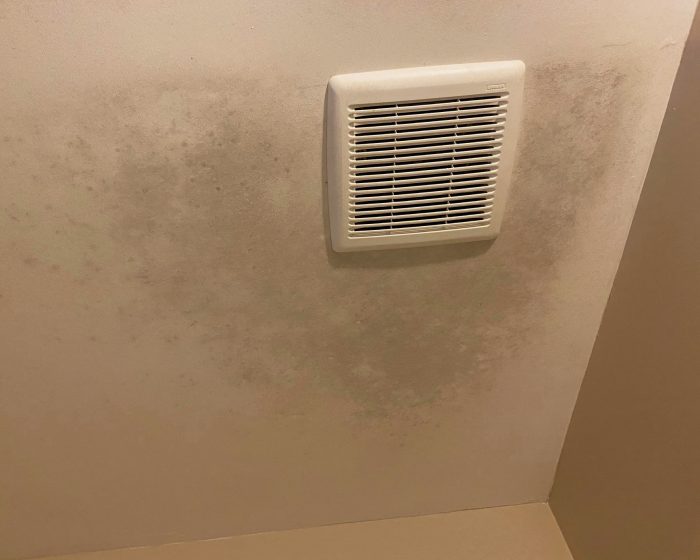
When well-meaning contractors make energy-efficiency improvements on an existing house, energy bills should go down. That’s good. But sometimes, even when energy bills go down, the indoor conditions or comfort get worse. For example, tightening up a building can lower indoor air quality—especially if the contractor doesn’t understand the need for a good mechanical ventilation system. Another example: energy-efficiency improvements can reduce air conditioner run time. While this lowers energy bills, it can also raise indoor humidity levels, leading to mold.
In other words, you can’t fiddle with the leg bone without affecting the knee bone. Contractors have to adopt “the house is a system” thinking to avoid these kinds of problems.
High indoor humidity can lead to mold problems
Ideally, a home’s indoor relative humidity won’t rise above 60% during the summer. That’s the goal—but not always the reality.
Kohta Ueno, an engineer and principal at Building Science Corporation, has been studying the causes of high indoor humidity for many years. (Back in 2013, I reported on his research on the topic in a GBA article called “All About Dehumidifiers.”) Ueno was one of three authors (the other two were Joe Lstiburek and Armin Rudd) of a groundbreaking 2002 study of homes in Houston that had high indoor humidity. As it turns out, the problems described by Ueno in 2002 aren’t limited to Houston—they also occur in many East Coast locations with hot, humid summers. Anecdotally, these problems are reported to occur more frequently in recently built energy-efficient homes than in older homes.
This past summer, I attended the Building Science Summer Camp in Westford, Massachusetts. During a meal break at the conference, I met a mold remediation contractor from Texas who told me that his business was booming. “The buildings with high…
Weekly Newsletter
Get building science and energy efficiency advice, plus special offers, in your inbox.
This article is only available to GBA Prime Members
Sign up for a free trial and get instant access to this article as well as GBA’s complete library of premium articles and construction details.
Start Free TrialAlready a member? Log in
7 Comments
I haven't heard or thought about the affect of SEER ratings on humidity. I would love to see more thoughts or evidence about spec'ing less efficient equipment to help with dehumidification.
Dill Bill,
See this article: "Climate-Specific Air Conditioners."
In that article, I quoted HVAC engineer John Proctor. Here's what I wrote:
Proctor believes that the SEER test is flawed. “There are three tests used to determine SEER,” Proctor told me. “One is a steady-state test at 50% relative humidity. The other two tests are performed with a 82 degree outdoor temperature and an 80 degree return-air temperature, with an extremely low indoor humidity level, so that there is absolutely no moisture build-up on the coil. These conditions are never found in the field — these conditions are dryer even than conditions in Saudi Arabia. So to improve a unit’s SEER rating, manufacturers have learned to run the fan for 90 seconds after the compressor goes off, because the coil is still cool. But because the test assumes there is no moisture on the coil, they can’t take advantage of any evaporative cooling. If you install this type of unit in Florida, with the fan running for 90 seconds after the compressor goes off, you end up putting the water back into the house, which is a bad idea. And in a dry climate, the fan isn’t running long enough. So the compromise design isn’t right for anyone.”
Dill Bill,
You might also want to read this article: "Window-Mounted Air Conditioners Save Energy."
In that article, I also quoted John Proctor. Here's what I wrote:
Some critics have noted that air conditioner manufacturers design equipment to achieve a high score on the laboratory SEER test, even when some of the engineering solutions used to achieve high test scores result in poor performance or efficiency in the field. For more information on perceived flaws in the SEER standard and SEER testing protocols, see SEER Ratings Challenged.
John Proctor, the president of Proctor Engineering Group in San Rafael, California, has performed useful research into possible flaws in the SEER rating method. Proctor (with co-author Gabriel Cohn) has publshed a paper on the topic: Two-Stage High Efficiency Air Conditioners: Laboratory Ratings vs. Residential Installation Performance. Proctor and Cohn wrote, “The increased installation of high Seasonal Energy Efficiency Ratio (SEER) air conditioners along with utility program rebates for these units prompted a study of the measured performance of these systems. This project assessed the performance of these systems in the climate zones found in the mid-Atlantic region of the U.S. … The data were analyzed to assess the relationship between laboratory testing and real world performance. This study found causes for concern including: actual seasonal energy efficiency ratios between 59% and 84% of the rated SEERs, constant fan operation substantially degrading seasonal efficiencies and reducing dehumidification, latent loads that exceed Manual J estimates, and sensible loads substantially lower than Manual J estimates.”
Thanks Martin. Another rabbit hole for me.
Too bad this article doesn't give any actual numbers, I'd be very curious to see what kinds of RH numbers (along with temperatures) are causing problems.
DC,
Good question. I have emailed Kohta Ueno, asking him to respond; I hope he will be able to do so.
One way that researchers quantify these problems is with monitoring equipment that logs "percentage of hours above 60% RH" for indoor air. In the 2002 study in Houston, unimproved houses that logged 5% of hours above 60% RH did not exhibit problems. The problematic houses (those with ductwork moved to the interior of the home, improved insulation, and upgraded glazing) had 23% of hours above 60% RH. At that level of indoor RH, problems were noticeable.
In most of these investigations, there was not a good or consistent data source. Typically, the property managers went in to problem units once in a while, and did "spot" measurements of temperature and relative humidity. From what I recall (rather than going through a decade of reports), I believe they often reported 80% to 90% RHs in problem units in summer. Of course, there are plenty of caveats--this was probably consumer-level meters, which are known to be poorly calibrated, especially in RH.
One exception was a Houston investigation, where the management team installed data loggers--see data below, which is a "box and whisker" graph of temperature and RH. The "box" shows first/third quartile of data, the line and X show median and mean, and the dots show outliers (https://www.excel-easy.com/examples/box-whisker-plot.html). Some problem units were 75-85% and 68-77% RH.
Log in or become a member to post a comment.
Sign up Log in