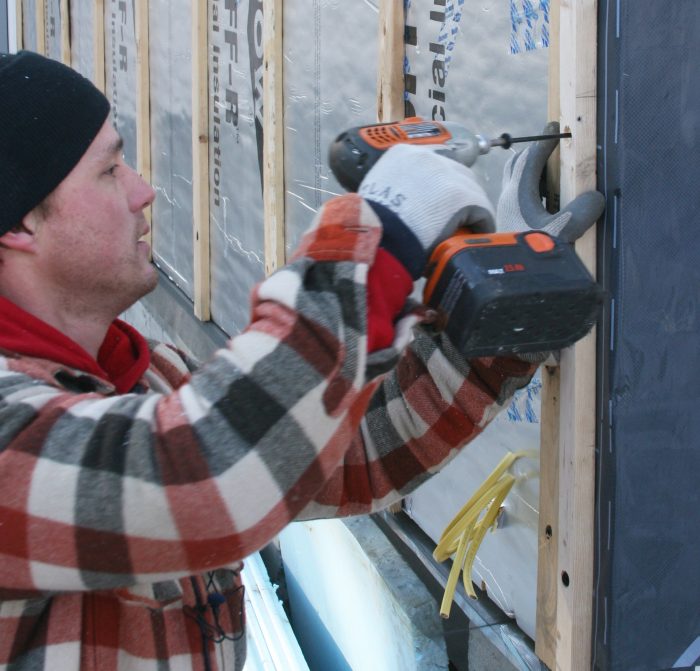
Installing a continuous layer of rigid insulation on the exterior side of wall sheathing or roof sheathing reduces thermal bridging through framing members and improves building airtightness. GBA has lots of articles explaining why exterior insulation makes sense and how builders can install it.
Although this construction method has been used in New England for at least four decades, there are many regions of the country where contractors still aren’t familiar with exterior insulation. That’s why so many frustrated homeowners post questions on our Q&A pages along the lines of, “Why can’t I find a contractor who is willing to install a continuous layer of exterior insulation?”
Those of us who help answer these questions often feel like Bill Murray in Groundhog Day. Here’s a sample of the type of questions I’m talking about:
Weekly Newsletter
Get building science and energy efficiency advice, plus special offers, in your inbox.
This article is only available to GBA Prime Members
Sign up for a free trial and get instant access to this article as well as GBA’s complete library of premium articles and construction details.
Start Free TrialAlready a member? Log in
57 Comments
This is going to be very helpful for a lot of folks.
I would only add that contractors who avoid this kind of work are perhaps more rational than one might think. Margins are tight, learning on the job can be very expensive, and complex jobs can lead to unhappy clients if things aren’t carefully managed.
So a client seeking this kind of work will probably need to go out of the way to allay the reasonable concerns of the contractor, whose business depends on avoiding risk and uncertainty. That means more trust on both sides than is probably typical.
Norm,
I agree with you completely. You wrote, "I would only add that contractors who avoid this kind of work are perhaps more rational than one might think. Margins are tight, learning on the job can be very expensive, and complex jobs can lead to unhappy clients if things aren’t carefully managed."
In my 2019 article on this same topic, this is what I wrote on the issue: "Most builders are rational professionals who are operating an inherently risky business. These days, residential construction is booming in many parts of the U.S. Builders are busy. Moreover, there is a shortage of skilled labor right now, so even builders who want to expand find it hard to hire new workers. If a builder is making a good profit by building conventional homes — homes that aren’t particularly airtight or well insulated — that builder has few incentives to work with a client who wants something different. It’s entirely rational for a builder to avoid clients who say, 'I want you to use a new technique that I read about on the internet.' For most builders, a client like you is nothing but trouble."
I think the widespread adoption of exterior foam in Central Canada was aided by the foam typically being only 1" thick, which meant very little disruption of conventional practices for installing siding, detailing penetrations, etc. There is a huge difference between what is necessary to install 1" and 3" thicknesses.
I've been devouring GBA and BSC articles because I've decided to be my own contractor (and designer) for our next house for this very reason (and I can afford to), even though I have no prior building experience. But I'm worried about the ability to find subs that will be willing to try something new (to them) like double-stud framing or dense-pack wood fiber insulation. I have a very low expectation of finding a HVAC tech who has even heard of "mean radiant temperature".
Given how difficult it's been for me to work out the complexities of building science and all kinds of trade-offs between different ways to build, I completely understand why an experienced builder would not be willing to do something unfamiliar, even if the client is eager to take on the risks.
rob_montroy,
"even if the client is eager to take on the risks."
There is the rub. Being eager to take on the risk, doesn't often translate into indemnifying the builder against liability if things go wrong.
My money is on it being MUCH harder to do this as a self designer/builder since you still have the downside of non-traditional methods, but also the massive complication of being a totally inexperienced designer and builder.
Before you spend too much time on drawing plans I'd try getting connected to subs via word of mouth so they'll at least hear you out before telling you no.
Good luck with your project though!
Rob,
I'm doing much the same thing, though I've already broken ground. I'm a few months into my build and what really made it possible is finding a couple of carpenters to help. They are young, willing to learn and I'm able to give them 6 months of full time work. I'm also working full time on it with them, so we are learning these techniques together.
Adam
I'll chime in from Alabama -
It's worse than you let on. Not only do other contractors know little about their trade, finding materials is an even larger nightmare. It's a lack of resources / capability double whammy.
Insulation contractors that don't know about exterior insulation. Insulation dealers who have 'foam board' but look at you with a blank stare when you ask for "Polyiso" "The other foam" or "For the love man, here's a product number, let me show it to you on your own computer".
I've had similar instances when trying to source mineral wool, flashings, waterproofing materials, etc. It's all special order, once you find someone who is even willing to look it up in their catalog for you.
I've had a few good experiences though - whitecap seems to come through on most occasions. A few electrical suppliers have popped up that know what a wago is. The Birmingham office of service partners is good. The builders 1st source has been good.
It just takes a long planning time to do anything that's not baseline.
There's a third aspect of this too - the northern Alabama area is growing at a blistering pace. There's such a demand for houses that they're being cranked out in the standard configuration faster (brick / cheapest house wrap / 7/16" osb / 2x4 / R11 / Drywall) than they can break ground. There's no incentive to improve, train, or do anything different than what they're doing now. It's only going to be through regulation that any situation in the southeast improves.
Our exterior insulation roof project has been a disaster. I wanted 7" of continuous rigid foam insulation over original board sheathing, then new plywood sheathing, and finally metal roof. I pressed my GC to make sure his roofer had the chops for this job. I even spec'd flat horizontal 2x4s 16" apart over original sheathing so roofers would have easy target for screws instead of trying to hit 2" wide vertical rafters. I got the typical "yeah, yeah, we can do that" from the roofer, who then proceeded without telling us, to build a knee wall on the ridge that filled with water, got under the Grace and leaked into the attic. Eventually had to terminate the roofer, find another team that has been undoing all of the original mistakes, including ordering wrong length metal panels because hadn't taken into account longer roof run with additional insulation height. We're now a year behind schedule and still not done. I think a big part of the problem was the original roofer just didn't listen, didn't really focus on the plans I drew up, and didn't provide adequate oversight and monitoring of his team doing the work.
"build a knee wall on the ridge that filled with water"
OK I gotta ask, what the heck is a knee wall on a ridge and what was it for?
It's been a rainy season here, and it's definitely making me appreciate assemblies that don't require a lot of weather protection time.
Stolzberg wrote about it here: https://www.greenbuildingadvisor.com/question/what-next-with-roof-mess.
So what do we take from all these problems? My feeling is there isn't much point in simply complaining about the present state of construction knowledge of high performance assemblies, or appetite of builders to do new things. It doesn't lead anywhere useful.
What you specify should reflect as closely as possible the available products and usual practice in your area. Any upgrades should stay within the skill set of those doing the work. If not you assume the risk that you won't find anyone to do the work, or that that work will be done incorrectly.
That doesn't mean you can't end up with a high performance envelope. Rather that the route you get there might not include the details you have become enamored with from the ratified world of builders featured here on GBA.
Malcolm,
You wrote, "My feeling is there isn't much point in simply complaining about the present state of construction knowledge of high performance assemblies, or appetite of builders to do new things. It doesn't lead anywhere useful."
I agree. That's why I tried to come up with a few suggestions for homeowners.
As you know, GBA tries to provide science-based advice to builders and homeowners, to make it easier to achieve good results when working on a residential construction project. We're not just here to complain.
That said, I also consider myself an advocate for better practices; I'm one small voice advocating for change. I'm thinking of regulatory changes, educational changes, and changes in construction practices. To move the needle in the right direction, it's sometimes necessary to explain not only what works, but also what aspects of our current practice are broken. The hope is that we are all moving to a better future.
Martin,
The blog is a great comprehensive resource for those considering whether and how to use exterior insulation. I'm not saying you or others shouldn't identify the problems, rather that people contemplating a build should pick their battles.
My comment was in part inspired by a trend I have seen here on GBA for posters to assume that because something makes good sense from a building science perspective it is a) worth incorporating into their projects, and b) meets their building code.
Especially for first time builders, just getting any house finished is a major accomplishment, fraught with difficulties. Adding the layers of complexity that they see done fairly effortlessly by people like Ben Bogie is fine as long as they go in with their eyes open, and aren't surprised when things don't work out.
The blogs following builds on GBA that have most impressed me over the years were the ones that adopted fairly conventional but well performing assemblies, that also got finished without drama or incident. Stephen Sheehy's house comes to mind. If the intention is to end up with a well build house without ending your marriage, that's the approach I'd suggest. I don't think specifying thick exterior foam on walls or roofs is for now anyway in that category.
A lot of this just comes down to norms (whether via mandate or just local practice). I have gathered from you Malcolm that rainscreens are mandated in your region and so everyone is doing them and it's just part of the work/material flow.
I do think some regions are more familiar with exterior foam than others, which changes how alien the task is.
In other words, while some of the resistance does come from the inherent difficulty of the task, I think it really boils down to expectations and norms. So one question we might ask is, should we somehow push exterior foam (or generally exterior insulation) more towards a norm.
maine_tyler,
"rainscreens are mandated in your region and so everyone is doing them and it's just part of the work/material flow."
And its own separate building inspection during construction, which goes a long way to establishing good practices for any new requirement.
I suppose the main point of my post was that a potential homeowner or builder who wants to try many of the techniques mentioned on this site, such as a normal rainscreen with exterior insulation, needs to plan for spending extra time with material acquisition, and performing interviews with potential subs or contractors to make sure they're up to the work - in a region where it may not be common.
It's definitely possible, just not out of the gate as it's presented here. If your research consisted solely of GBA, you might be inclined to believe that every product is available in your region, and every contractor there knows how to implement these details well. Then only to be met with the real world of none of it working out and disrupting timelines for both materials and training for the trades, if you're willing to be the first guinea pig.
Kyle,
The other side of this discussion is I'm very grateful to those innovators who do push things forward, and take on that added complexity, so we all benefit later. Things like concrete-free slabs, which may make a lot of sense, and become a widespread practice down the road. But I wouldn't attempt one here for love or money.
I work in Kitsap County, outside of Seattle. In October, the new Washington State energy codes are scheduled kick in. The new (prescriptive) code requires walls to have either continuous wall insulation (likely 1” or 2” of rigid foam) or a U-factor of 0.056 or less. Either way, it seems like it will be a rough transition for homebuilders, many of whom are not experienced with exterior insulation. (This may be less of a problem in Seattle, where experienced “green builders” are more common. They are harder to find outside of the city.) That assumes that local jurisdictions bother to enforce the energy code; I expect there will be a lot of pushback once builders catch on to the new requirements. Until now, most folks have gotten away with a simple 2x6 wall with R-21 fiberglass batts. In reality, these walls probably have an effective U-factor of 0.08–0.09 due to thermal bridging and less-than-flawless insulation and airsealing. So, the new requirements will be a big wake-up call. It will be interesting to see how this plays out.
I'd like to return to and highlight a comment Martin makes in his closing paragraph: "If you’re worried about climate change, you may want to skip the idea of exterior rigid foam."
My remodeling firm, Byggmeister, used to advocate strongly for adding exterior insulation to walls and roofs as part of our projects. We no longer do that for three reasons. First, exterior retrofits are extremely expensive. Second, given the urgency of the climate crisis and the breakneck speed with which we need to decarbonize, we can't afford to emit much if any carbon now to save carbon later. Finally in order to have any chance of meeting our climate reduction goals, we need to prioritize electrification.
What we do on more of our projects now is we air seal and insulate as best we can can within the existing shell and then get the home off of fossil fuels. For folks with unlimited budgets who can afford the exterior retrofit as well as the whole house heat pump conversion, go for it — just make sure you use a carbon storing exterior insulation like wood fiberboard.
Thanks, Rachel. Byggmeister continues to be a thought leader in the green building world. I appreciate your firm's approach.
>"then get the home off of fossil fuels"
>unlimited budgets...can afford...the whole house heat pump conversion"
If the whole house heat pump conversion is the unlimited budget, Cadillac version, how do you get a home off fossil fuels on the cheap?
>"we can't afford to emit much if any carbon now to save carbon later"
>"we need to prioritize electrification."
What do we think electrification of the energy economy is? It's an intensive process of building out immense new infrastructure of renewables and an updated grid to deliver/store said electricity, plus a major shift in infrastructure for vehicles. I'm not saying I'm against it, but I'm curious if the dismissal of exterior insulation retrofits as too carbon intensive and the embracing of electrification as not being the same is based on a comparative analysis backed by data?
Maine Tyler,
You misquoted Rachel White. She did not write that "the whole house heat pump conversion is the unlimited budget, Cadillac version." She wrote, "For folks with unlimited budgets who can afford the exterior retrofit as well as the whole house heat pump conversion, go for it."
In other words, the "Cadillac version" -- your words, not hers -- is exterior insulation plus heat pump conversion.
OK I might have misunderstood. So she's advocating for whole house heat pump conversions. The rest of my question stands.
I guess I'm just a little concerned with the notion that our way out is full on electrification without pushing the bounds on efficieny. I'm not convinced there's been a real data driven analysis behind that idea when looking at long term goals. Obviously it's too complicated to present such arguments in GBA article comments, but I'd be happy to even just hear that they're out there (the analyses) and well researched.
There's also a big difference between retrofitting exterior insulation and adding it to new projects.
Comparing the embodied carbon of things like exterior insulation to the carbon saved is pretty straightforward, if not perfectly accurate; carbon payback for foam insulation could be several decades, which is not helpful if a primary goal is reducing the climate impact of our homes. You can do the same with the cost for the labor to install exterior insulation; how does that compare to putting the same money into other carbon-reducing measures such as installing PV. Ideally we would all have more efficient homes using carbon-neutral materials, but those materials are expensive.
Michael,
What you say is reasonable at face value, but this gets very complicated fast when we start looking at how we are actually going to electrify the economy.
I'm not really up in arms about people pushing back against extreme insulating measures do to its diminishing returns, but I do question certain assumptions and feel that the embodied carbon side of the equation seems to get largely ignored when it comes to electrifying the economy. It feels like we are adding a variable to only one side of the equation.
"given the urgency of the climate crisis and the breakneck speed with which we need to decarbonize, we can't afford to emit much if any carbon now to save carbon later."
THIS is the mentality that scares me a bit. I do beleive ignoring the future is how we got into this mess. Of course if the science strongly suggests that we have a larger carbon budget later than now, that's worth heeding, but I'm not convinced that's what the science exactly says and i worry it a misunderstanding of our predicament. Of course I really dont know.
Anyways, perhaps my questioning is a bit unfair, but I like to think we scrutinize one another for the better, so that all of our collective assumptions are challenged.
Maine Tyler,
I think Martin addressed the first question. So I'll try to address your second question.
You're right, of course, that building out the infrastructure to support an electrified economy is carbon intensive. And there is reason to be concerned (or to at least ask the question) about the impact of decisions to invest a bit less in load reduction of existing homes and a bit more in electrification.
Perhaps the most cogent critique I have heard of Byggmeister's current approach to residential retrofits — which is to air seal and insulate as best as we can within the existing shell and then to electrify — is that if we don't dramatically reduce the loads of existing homes the surge in power demand may require utilities to fire up dirty power plants on the coldest days of the year. Could this result in more emissions than the upfront emissions associated with exterior retrofits?
I don't know if anyone really knows the answer to this and other trade-off questions, which are super complex. What I do know is that Byggmeister's experience of pushing deep energy retrofits for more than a decade — and completing only a handful — has led us to believe DERs are a niche and costly approach to reducing residential carbon emissions. And if those DERs rely on foam insulation, then they are also counterproductive, as Mike Maines notes.
Thanks for sharing those thoughts Rachel. As I alluded to earlier, my questioning may have been a bit unfair, especially in that I think the equation is different for retrofits vs new construction, of which you work only on the former. I agree that DERs are niche and probably not the best general path forward, especially if they are not timed with other house work that needed to happen anyways (siding replacement, etc.)
But as far as using exterior insulation in general (as discussed by Martin in the article) I'm less convinced omitting exterior insulation from our options is justified by arguing that the upfront carbon cost is simply too high. We do need to cut emissions now, but also set ourselves up for success in operating a truly low carbon economy in the future. Because frankly, we're no where close to being able to do that right now and omitting exterior insulation (and like mentalities) doesn't seem like the most important tap to start screwing shut.
I am excited about the upcoming release of Timber HP wood fiber products as an option for exterior insulation over foam though. I DO think we should be thinking about upfront carbon in builds.
maine_tyler,
I agree. If forgoing exterior insulation now isn't a big enough contributor to carbon emissions to make any immediate or useful difference, then it may well make sense to build the way you want houses to look in the future.
https://www.theguardian.com/world/2023/may/09/mind-boggling-methane-emissions-from-turkmenistan-revealed
The arguments in favor of using insulation with high levels of embodied carbon when there are low-carbon equivalents available is similar to the argument whether we should be addressing climate change ("trying to save the planet") on an individual basis or if we should be designing defensively, making our homes more resilient in the face of increasing climate instability. I believe we can do both, but when it seems like we have to choose one, I'm not sure which is the right choice.
Michael,
There are a lot of people who have thought more deeply that I can about this, but it seems to me that what is unique about carbon emissions are that they are solely a collective problem. If you leave your plastic waste up a logging road (as people do here) and justify it by saying that it is dwarfed by the waste island in the Pacific, or on some Third World beaches, you are still affecting your local area. But the carbon footprint of a project only contributes to the global problem.
So moral concerns aside, it alters the equation. Practically that equation seems to me to be entirely dependent on whether the carbon significantly affects the total emissions - and leads me to the quandary as to whether is makes any sense to take any actions that realistically will have negligible or no effect?
Malcolm, I think it's a different situation than depositing plastic waste on public land. I live on a fairly busy road and deal with my share of littering as well. We should all reduce our "pollution" as much as reasonably possible. That's the morally right thing to do. But as climate change progresses--we're seeing multiple 80-90+°F days with 70+°F dewpoints in Maine this summer--that's Louisiana or Miami territory, after seeing -20°F just a few months ago--should my contribution to the collective problem overshadow my ability to keep my house and family safe and reasonably comfortable? We need to do everything we can, but without global cooperation and widespread government-driven changes, we aren't going to get where we need to be, and climate change is going to just get more wild.
Maine Tyler,
Q. "How do you get a home off fossil fuels on the cheap?"
A. I don't think that anyone claimed that it's possible to "get a home off fossil fuels on the cheap." My own approach is to wait for a fossil-fuel burning appliance to need replacement (everything breaks eventually), and to substitute an electric appliance when it's time to buy your next appliance. This takes a little planning and forethought -- for example, by making the necessary changes in electrical wiring before the appliances conk out -- so it won't necessarily be "cheap." But it's less expensive than doing everything all at once.
Remember, too, that the Inflation Reduction Act (IRA) and (in some states) incentives from state governments and local utilities provide rebates for some types of rewiring costs and appliance purchases.
So, if you're not using exterior insulation, do you build new houses with standard 2x6 framing and fiberglass batts in the stud bays?
Tom_K
It depends on where you are. In many climate zones that would be an improvement on what is presently done. In others you can get higher R-value assemblies in a variety of ways - Mooney walls, 2"x8" framing, double walls - without using foam board.
Thanks, question was for Byggmeister, but currently in IECC zone 8. Plenty of exterior insulation options that aren't foam. Wondering why they wouldn't recommend it for me.
Hi Tom, I'm a colleague of Rachel's at Byggmeister and just to clarify our work is exclusively on existing homes. That said many of our colleagues who do new homes are often proponents of double stud walls with dense packed cellulose and rain screens, which seems like a great option to me. We wouldn't advocate for 2x6 with FGB in new construction down here and definitely not up in zone 8.
In all seriousness. If you are handy, and can get the necessary equipment on site, how hard is it to do the exterior insulation yourself? From all of the videos I've seen there isn't much to really learn is there?
Mixed_beans,
- That's true of just about any construction task - laying hardwood flooring, tiling, finishing concrete slabs, wiring your electrical panel, running an excavator. It all appears DIY friendly until it isn't. Skilled trades typically have a lot of experience and many have served apprenticeships. Pretty well everything looks simple on Youtube. My experience is that exterior insulation becomes exponentially more difficult as the thickness increases, both installing the insulation itself, and adapting the details necessary for penetrations and cladding.
The cost of any construction assembly or equipment needs to be assessed with the labour component included. That's the only useful way to compare them with the alternatives. Exterior insulation costs what it does because it involves adding one or two layers which cover the entirely of the outside of the structure, with all that entails.
I was thinking 6 inches of Rockwool Comfoboard which I know isn't light. I hear you when you say it looks easy on YouTube. Took me a little time to get used to using a chainsaw and excavator mostly efficiently.
Mixed_Beans,
Sorry - I thought you were talking about the viability of people doing it in general, not you specifically.
Sure you can install the insulation. 6" of rockwool is about as difficult as you can get though. It will be hard to hit the studs, and to keep the strapping co-planar. Detailing bucks for openings, and blocking for penetrations will need a lot of thought, but it's doable with a bit of patience.
My apologies. You are right. I guess I let my future home build find its way into the conversation.
Mixed_beans,
Not at all, the confusion was mine. As I said, it's doable, but at the extreme end of the spectrum of difficulty for exterior insulation. If it were me I would choose a wall assembly where most of the insulation was in the cavities, and had just enough outside to keep the sheathing warm.
Thanks for the feedback. Hoping I am not derailing the conversation much on this. In your opinion what does that look like on the border of climate zones 5 and 6?
Mixed Beans,
If you are in Zone 5, consider insulated 2x6 framing with a continuous exterior layer of R-7.5 (or higher) insulation. More information here: "Calculating the Minimum Thickness of Rigid Foam Sheathing."
It's not super "hard" from the standpoint of being conceptually difficult, though it is a fair bit of "hard work." If you can follow an assembly that's already been somewhat proven / tested, the conceptual part gets even easier -- like using only an inch or two of exterior foam where it's short enough to fasten the siding through the foam to the structure. When you start getting into thicker foams layers, there's a bit more engineering required in terms of how to attach siding. There's also details to work out, like what to do around windows, at the top and bottom of walls, etc, but there's a fair number of resources around to figure this stuff out -- the trick seems to be deciding what's best for your situation, as there's few "standard" ways to do things and a lot of semi-experimental ideas that people have had.
Overall, if you're semi-handy, have some willing helpers, and don't mind (a) spending a bunch of time thinking through details and (b) doing a bunch of mostly physical labor, it's very doable.
I'm up for the labor. Can't be any more difficult than felling, bucking and logging trees on an acre of property. At least I hope not. I'm thinking up to 6 inches of Rockwool Comfoboard on a two story, up here in New England, will get me about where I need to be.
Thanks for the great article and resources. Does anyone have a good wall detail for stucco over continuous rigid insulation? I'm in IECC climate zone 3, Los Angeles, CA and currently have 2x4 walls sheathed in 7/16" zip. New nail fin windows will be installed against the zip, and I'd like to add 2" of rigid insulation, then finish in stucco. I've seen Matt Risinger's Roxul-sponsored stucco over rockwool comfortboard that's the closest I've found but not sure if thats the best approach. Any help appreciated, thank you! - Curtis
User 749,
I suggest that you read this article: "To Install Stucco Right, Include an Air Gap."
The article includes the following advice: "If you’re installing stucco over foam, here’s how to create a ventilated rainscreen gap: (a) Install 1×3 or 1×4 vertical strapping on top of the foam, screwed through the foam into the studs; (b) Fasten paper-backed metal lath to the strapping, and proceed with a standard installation of three-coat stucco."
The article also notes, "For further information on the use of paper-backed metal lath over furring strips, see the statement by Kohta Ueno, quoted in a comment on this Q&A thread: “Stucco over exterior rigid foam – yea or nay?” "
Thanks, Martin! I'd saved the first article but hadn't read the second that was really helpful. So if I did Zip/WRB-> rigid foam or roxul comfortboard->vertical strapping ->paper-backed metal lath -> stucco, would I also need a small air gap/rainscreen between the Zip and rigid insulation or just go straight over the sheathing?
Also, I've seen details on how to vent top and bottom with other cladding systems but how would you do it with stucco?
Would it make sense to try and include foil-faced insulation/a radiant barrier in a wall system like this in my climate zone 3? It sounds like in most cases they're not worth doing. Thanks, Curtis
User 794,
Q. "If I did Zip / WRB / rigid foam or Roxul Comfortboard / vertical strapping / paper-backed metal lath / stucco, would I also need a small air gap/rainscreen between the Zip and rigid insulation?"
A. No.
Q. "I've seen details on how to vent top and bottom with other cladding systems, but how would you do it with stucco?"
A. The details would be similar, but in my opinion the upper vent is optional.
Q. "Would it make sense to try and include foil-faced insulation/a radiant barrier in a wall system like this in my climate zone 3?"
A. If you choose to install rigid insulation with a foil facing, that will work fine, as long as you follow the ratio rules for the ratio between the continuous exterior insulation and the fluffy insulation between the studs. A separate radiant barrier makes no sense, in my opinion.
Thanks, Martin - is this detail getting close? I'm still not sure what to do with the vent at the top since we have exposed rafters and don't have a soffit. I know you mentioned it was optional and if I can't find a solution will probably plan on not having it.
I saw a Joe Lstiburek detail in his hot-dry/mixed-dry book that shows the wall air gap between the rigid foam and sheathing instead of between the stucco and rigid foam (included that detail attached as well) - which do you prefer?
The wall will also be sticking out quite a bit further than the foundation, I was planning originally to add rigid foam there too but have since decided against it after hearing about bug and rodent problems/recommendations to put foundation insulation on the inside.
Thanks,
Curtis
Curtis,
The drainage gap belongs between the stucco and the rigid foam. As I noted in Comment #50, : "If you’re installing stucco over foam, here’s how to create a ventilated rainscreen gap: (a) Install 1×3 or 1×4 vertical strapping on top of [that is, on the exterior side of] the foam, screwed through the foam into the studs; (b) Fasten paper-backed metal lath to the strapping, and proceed with a standard installation of three-coat stucco."
Thanks, Martin I started getting confused looking back through my notes. Anything you would do differently from this detail for climate zone 3b for the wall or roof? Wall air gap would be created by the 1x3 vertical strapping with paper-backed metal lath fastened to strapping.
Curtis
Clients looking to build high performance should be seeking out high performance builders. We do exist.
The issue of contractors not being interested in high performance building methods goes well beyond just exterior insulation. (I've worked with SIPs for 30 years and often I am the only builder a client has met who has done so). ERVs, air sealing, blower door testing, high performance windows all are still outside the average builder's skill set.
Exterior insulation is an excellent way to fix some of the issues with stick building. But clients interested in high performance can consider alternatives if exterior insulation becomes a stumbling block. (SIPs, ICF, Pre-cast concrete are some of my favorite options).
I live in a 1920s 1-1/2 story in the PNW that has a finished attic that we use all the time for hanging out. When we moved in, I knew nothing. And I'm beginning to think the inspector knew only a fraction more than I did ... but I digress. The original owners finished the space by stuffing pink fiberglass between the 2x6 rafter cavities and sheetrocking over it all. Not long after we moved in, we realized it was "raining" from the can lights due to excessive condensation and it eventually became apparent that the vents in the roof were just tacked on. I subsequently learned all about vented and unvented roof assemblies and was appalled at the information "provided" to me by our inspector. I've since become obsessed with reading all about building science (but still maintain that REDUCING, REUSING, and REINVENTING before building/buying something new) but completely discouraged that so many contractors don't even know what I'm talking about when I mention building science. We are now up against a moisture/mold issue in our attic and it seems we have to either sacrifice all of the headroom that makes our attic mostly usable so we can properly insulate (and vent) from the interior, or just bypass all the cost of maintaining a finished attic and eliminate it from our building envelope, as trying to source a contractor who even knows about exterior insulation above the roof deck let alone the possibility of using recycled rigid foam has proved completely fruitless. (Actually, one company did but they only work on large commercial projects.) It really feels like such a shame to lose our attic but I just can't wrap my head around putting in the work to remediate the mold situation lurking behind the sheetrock and not actually meeting energy standards which the previous owners blatantly bypassed. Sigh.
Log in or become a member to post a comment.
Sign up Log in