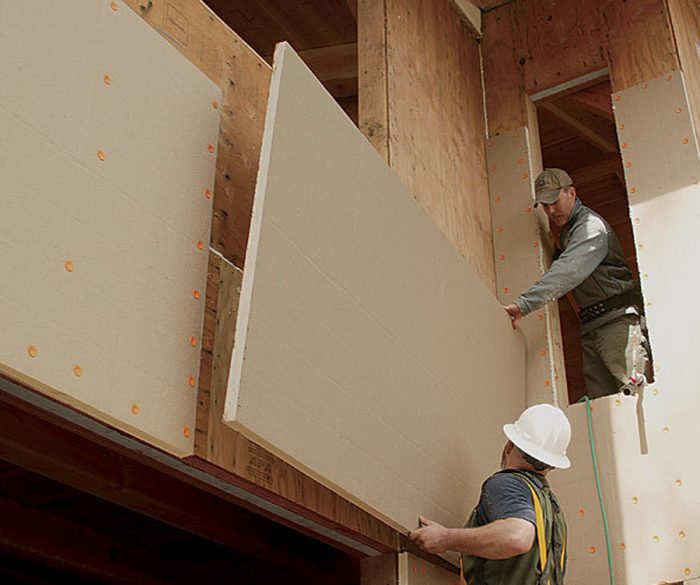
When I built my house about forty years ago, I installed a continuous layer of expanded polystyrene (EPS) on the exterior of the wall sheathing. Back in the 1980s, many builders questioned the wisdom of this type of rigid foam installation, expressing the opinion that the foam would trap moisture in the wall.
Even 40 years ago, however, building scientists knew that a continuous layer of exterior rigid foam helped protect the wall sheathing, as long as the foam was thick enough. Exterior rigid foam keeps wall sheathing warm during the winter, and warm sheathing stays dry.
In the decades following my decision to use exterior rigid foam, researchers have accumulated more and more evidence that exterior rigid foam works. That’s why I was recently surprised to read a dire prediction about foam-sheathed walls from GBA blogger Ben Bogie.
Ben Bogie is a skilled builder who works in Connecticut. He’s the type of builder who pays attention to building science and Passive House construction techniques, and he’s a frequent contributor to GBA’s BS + Beer Show. Here’s how Bogie answered a question from GBA editor Kiley Jacques in a recent interview published on GBA:
Kiley Jacques: Are there products and/or aspects of assemblies you want to see retired for good?
Ben Bogie: Yes, exterior foam insulation and PVC plastics. My concern with rigid foam—aside from the global warming potential—is the fact that, inevitably, over the life of a building, there is going to be a water intrusion event. If you put a vapor-impermeable layer over the outside of a building, it can only dry to the interior, where there is the lowest drying potential. With exterior rigid foam, we are setting the building up for the possibility that it can’t dry out, which means it could…
Weekly Newsletter
Get building science and energy efficiency advice, plus special offers, in your inbox.
This article is only available to GBA Prime Members
Sign up for a free trial and get instant access to this article as well as GBA’s complete library of premium articles and construction details.
Start Free TrialAlready a member? Log in
39 Comments
Martin,
Rain-screens initially seemed like a useful climate specific response to the problems encountered primarily in marine zones like the PNW and coastal New England. In the absence of envelope problems in other climates they didn't appear to be worth the extra effort.
Some decades on do you have a feel for where the line is best placed? Is it only hot dry climates where they don't make sense, or would you still confine their use to regions where walls experience long periods of wetting?
Malcolm,
That's a tough question to answer. Every builder is willing to accept a different level of risk. Some builders (evidently including Ben Bogie) worry about sheathing rot -- and that type of builder will certainly sleep better if their walls include a rainscreen gap.
I'm curious about any possible adverse impacts from rainscreen installations in areas prone to wildfires. Has any research been done on this?
I always refer to GBA.
The findings in Japan are as follows.
In general, rain screen is a cause of fire spread.
However, there was an example where phenolic foam insulation was used for the exterior and melted during a fire to seal the gap and prevent the spread of fire.
I'm not sure about the effect of a rainscreen, but it sure seems like mineral wool would be a better choice for the external insualation than foam in those areas.
[Response to Comment #17]
Antonio,
Here are links to three relevant GBA articles or discussions:
"How to Vent a Rainscreen"
"Can a rainscreen become a chimney for fire?"
"Fire-resistant rainscreen system"
We've built over 400 homes in Washington state without rainscreens. The key for us in our very specific area is to manage liquid water with gutters and downspouts and to shed rainwater properly, including proper flashing. I don't believe in the "every window leaks" or "all claddings leak" expressions. The world of absolutes is generally wrong. We have low enthalpy most of the year, our weather comes generally from the north rather than from the south. I'm not saying whether one should or should not build with a ventilated rain screen. I just think one should evaluate their macro (weather) conditions, site specific conditions, and the building specific conditions (not all walls in the same home should be designed with a one-size-fits-all mindset).
PioneerBuilders,
I agree. The first time I ever heard of a rain-screen was forty years ago when John Patkau used one on the two sides of his house in West Vancouver that saw the most wind and rain. the difference in how well the walls on my own house perform varies wildly by their orientation and exposure.
That said, given the the chances are pretty slim that the walls of each house in the PNW will be built with both that level of thought, an good execution of the important details, ai think a blanket requirement for rain-screens makes sense.
With all due respect to Ben Bogie (who is awesome) I agree with you Martin. In addition to your data based arguments, I believe that there is a flaw in logic here. One could also say:
"I don't think we should build air tight homes because of the fact that, inevitably, over the life of a building, there is going to be a ventilation failure, and then moisture, mold, and health problems."
Both are legitimate concerns, but we can't build high performing homes and hedge for major failures at the same time. Getting details right and planning for maintenance and inspection over time is just the way things have to go now.
Andy,
I agree, although I don't think it makes sense to design building assemblies so that if they experience some reasonable level of deterioration over time that they become risky - something like a wall that relied on maintaining a very high level of air-tightness for its longevity.
My reluctance to trust foam comes from its vulnerability to insect infestations, especially now that it seems to be more common to use it in load-bearing situations. Mike Smith (c0-inventor of the Mooney wall) only uses borate treated foams, but I haven't been able to access them up here in Canada.
Andy,
I don't really disagree with Ben Bogie over the idea that we have to make buildings that are robust enough to tolerate a little bit of builder sloppiness. But his conclusion is exactly backwards: if you are worried about the possibility of flashing errors, you should be building walls with a continuous layer of exterior rigid foam -- precisely because such walls will be less likely to have rotten sheathing than walls without exterior rigid foam.
Hey Martin,
I appreciate that my comments have spurred this conversation. First off, you'll get absolutely no argument from me on the physics. It's research I'm familiar with and am far from smart enough to find substantial fault with.
The core of my concern is touched on in your second to last paragraph "If by “installations that are not being detailed well” Bogie is talking about walls with gross flashing errors, then I agree with him" Historically i think that builders who were progressive enough to be early adopters of exterior foam insulation were likely paying attention to water management details. But... even on my own early projects (2010 and with much input gleaned from GBA) I look back with some degree of concern. The details and execution were sound, but the stick and peel products could have been better. I've only learned this through hands on experience.
Over the past few years I've been increasingly called on to act in a teaching capacity at various trade shows, events, clinics, etc. More often than not these sessions have to deal with water management (I'm not sure how I ended being considered an "expert" in this area but it is certainly one of the things I obsess over). Through the experience of being put in front of large groups of trades people, high performance and not, I've come to realize that the general understanding of basic flashing and water management is pretty abysmal across the industry.
It's hard enough to get typical installs detailed somewhat "well", I have a hard time stomaching that as the codes push for the use of continuous insulation, (sure it can be materials other than foam and in other locations but we both know that the broad percentage will likely be XPS or poly-iso) that these details are going to be executed well.
They can't flash to a flat surface and we're expecting them to make turns or use products that really stick?
And I don't mean to cast such a pallor across the industry but it's what I see on an almost daily basis. I think we're starting to do better but it's hard to say that's not just a projection of the silo I exist in.
Another concern I have is over the IRC guiding cold climates to use 20 + 5, but that's a conversation for another time...
Back to work for me, for now.
"Another concern I have is over the IRC guiding cold climates to use 20 + 5, but that's a conversation for another time..."
Ben put his finger on it here--the biggest issues with foam tend to happen when foam is installed too thin for a given climate, especially when paired with an interior layer of polyethylene which is still common practice and advocated by building officials in cold climates. This leaves sheathing that can still see condensation, but with little to no drying potential to the interior or exterior. It makes me cringe when I see builders install a layer of 3/4" foil faced polyiso when I can reasonably guess that they're using interior polyethylene here in the Minneapolis area. That's not a robust wall. Yet it works...until it doesn't. One flashing error--a missing roof edge kickout or missing head flash end dams-- gets ugly, if not right away then over time.
The concern is understandable, but not particularly well founded. There are millions of houses in Canada built with 2x6 R(xx) + R5 insulation and a 6 mil polyethylene vapor barrier on the interior. If it were super risky there would be thousands of failures and class action lawsuits.
That said, Canadian builders are more meticulous about air-sealing the vapor barrier than their US tract-home counterparts. I've never even seen "vapour hats" for sealing behind electrical boxes to the poly sheeting at box stores in the US, but it's a stock item everywhere in Canada:
https://guides.co/g/insulation-manual-installing-vapour-and-air-barrier/128855
Of course plenty of people (DIYers and pros alike) are fully capable of screwing up those details too.
https://guides.co/g/insulation-manual-installing-vapour-and-air-barrier/128855
See also:
https://www.greenbuildingadvisor.com/article/rethinking-the-rules-on-minimum-foam-thickness
Building walls with no exterior foam and no RAINSCREEN is a bigger risk to the sheathing than the apparent moisture trap of R5 foam + 6 mil polyethylene. Exterior foam dramatically reduces the impact of EXTERIOR moisture drives (rainscreens do too). Exterior bulk water incursions are more likely to become a problem for the sheathing than minor air leakage through faults in an imperfectly sealed interior side vapor barrier. How many houses have been built with imperfectly sealed interiors without a rainscreen? Are those houses all failing?
With sloppy construction anything can fail, but the true risk of R20 + R5 c.i. in a zone 6 or 7 climate just isn't very high despite the moisture trap.
Dana,
Part of that may be because in Canada the poly is included in the insulation inspection needed for any house that has pulled a building permit. Although not as accurate as a blow door test, poly has the advantage of lending itself to visual inspection the way other air barriers don't.
Dana,
Exactly I have seen 100's of homes in my area zone 6 built with 2x6 R21 with R 5 foam. I have taken many of these homes apart, remodeling, additions, etc. and have seen no evidence of sheathing deterioration. There just is any problems. I have seen rot issues when there is a gross flashing error, but I have seen plenty of walls without foam with rot issues too.
Exterior rigid insulation offers many benefits, I think the most important though is that it allows non "savy" builders a way to install additional R value in a cost effective, simple manor. Slap it on, tape it carefully, follow a couple best practice methods...."presto" better wall assembly.
"If it were super risky there would be thousands of failures and class action lawsuits."
That's not necessarily true. The concern I'm highlighting relates to the decreased ability to handle incidental bulk water intrusion, so in the event of failures the wall design would be deemed at most a contributing factor and not the immediate cause. A leak is a leak.
I'm not as concerned with its vapor profile or seasonal drives for reasons you noted. It's quite common in cold climates at this point. I stand by my assertion it's not a robust wall, particularly the thin foil faced variety that excludes rainscreen strapping.
[Response to Comment #6 by Ben Bogie]
Ben,
You wrote, "Through the experience of being put in front of large groups of trades people, high performance and not, I've come to realize that the general understanding of basic flashing and water management is pretty abysmal across the industry."
You and I probably agree that good flashing and water management practices are important for all types of houses, whether or not the house has continuous exterior rigid foam. If knowledge of these practices is abysmal -- and I suspect you're right that it is -- then that is the problem that you and I both agree needs to be addressed. In your original interview with Kiley, I wish you had stated your concern the same way -- a concern about the abysmal state of builder knowledge of water management principles and flashing techniques -- rather than as a concern that houses with exterior rigid foam will have problems.
You’d have to get the transcript of our conversation, my memory is good but not that good, but I generally air that grievance in the light of flashing concerns.
Damn editors...
Just kidding!
Omg, I had a job a few years ago, where the house had been completed renovated a few years earlier. There were five locations, where the flashing directed water into walls. The backprimed clapboards looked okay, but the sheathing and studs were rotted out. 70k later everything is fine.
No foam, plenty of rot. This job was an exception, most serious rot I have encountered in 35 years has been condensation related.
Jay,
Your $70,000 repair job sounds like many of the disasters described in my article, "All About Wall Rot."
And, as I'm sure you know, disasters in the second category -- condensation-related rot -- are far less likely to occur in homes with a continuous layer of exterior rigid foam than in homes without such a layer.
The 20 + 5 comment Ben made is the main concern I have with exterior foam products. Minnesota amended that portion of the code and does not require any exterior insulation in climate zone 7. The typical wall assembly in my market is drywall, 6 mil poly, 2 x 6 framing, R-21 fiberglass batt, OSB, WRB and siding. I seldom see a rain screen. Though the 20 + 5 assembly can work in a cold climate, in my opinion, it's higher risk in many instances. I've included a WUFI analysis I received for the above assembly, the only difference in the WUFI over the common assembly in my market is dense packed cellulose is substituted for the fiberglass and a rain screen was included in the modeling. The modeling also included a structure with moderate air leaks. Use the 20 + 5 assembly in a tight home and it works, add more exterior insulation or add a more vapor open exterior insulation and it works, at least according to WUFI.
Randy,
For my most recent perspective on the 20+5 issue, see "Rethinking the Rules on Minimum Foam Thickness."
For my perspective on WUFI simulations, see "WUFI is Driving Me Crazy."
Thank you both Martin and Ben. It's good to know that exterior rigid foam is not inherently risky to buildings.
One possible foam-based building risk I have greater concern about is the use of high density spray foam on basement rim joists in older houses. Encasing the warm side of a solid timber in foam makes the beam colder in the winter and also prevents drying to the inside. I haven't seen any reports of failures attributable to this though. Any thoughts? Are we going to have a rash of sill replacements in 30 years?
Norman,
I address your questions in the last four paragraphs of my article, "Insulating Rim Joists."
Look for the paragraphs with the heading, "What about homes that lack a capillary break under the mudsill?"
Interesting, thanks for the reference Martin.
I came to this article somewhat skeptical. I find the article quite convincing, though with some small reservations. The "warm sheathing is dry sheathing" idea makes total sense, the main reason I find this article compelling.
However as #4 suggests, well detailed rain screens may have a great deal to do with the results. And a large improvement may be had with simply doing an effective rainscreen.
My initial skepticism comes from memories of the problems that occurred with SIPS in cold climates. Interior, warm/moist air would migrate between the panel joints and saturate the inner faces of the outer sheathing, leading to rot at panel joints. I'm sure you all remember that. The solution was simple, tape the interior panel joints. Place the air barrier on the warm face.
Applying exterior rigid foam insulation is rather like making a SIP on site. With the air barrier typically on the OUTER face, we have the possibility of interior moist air migrating between insulation panel joints and condensing in the small gaps between insulation panels, thus wetting sheathing at these locations. In this circumstance I would consider taping the exterior faces of the sheathing joints before applying exterior insulation, thus moving the air barrier to the inner (warm) face of the exterior insulation.
We're seeing a big move in construction to move the insulation to the exterior, which also complicates door/window installations, makes them more labor intensive, which adds cost. And the increased number of components and complexity adds more chances for mistakes.
As I mentioned, applying exterior insulation is almost like building a SIP onsite. Given the current push to move insulation to the outer face, I'm really thinking we need to be building much more with SIPS. They eliminate a lot of the complexity/complications and site labor/cost that the exterior insulation approaches are causing.
My 2 cents.
Antonio,
The problems caused by air leakage through SIP seams -- especially in cold climates -- are significant. Using SIPs can be risky, unless the SIP installer is extremely meticulous when installing interior seam tape.
But the performance of a continuous layer of rigid foam installed on the exterior side of wall sheathing differs from the performance of SIPs, because the rigid foam seams almost never align with the sheathing seams. We don't have to speculate about this issue, because scientists have studied these homes, and have collected and shared their data and conclusions for decades.
Martin, thanks for the reply.
As a designer the bulk of my work is for stock plans (sold online) that can potentially be built anywhere in the USA. So I'm always trying to find the solutions that have the best chance of working in all climate zones, and can be built by relatively inexperienced, or at least no better than average contractors. Obviously it's a challenge.
Your work has helped me so much over the years and I just wanted to take this opportunity to say thanks.
Antonio,
You're welcome. One more point about the difference between SIP construction and the installation of a continuous layer of exterior rigid foam: with SIPs, the OSB layer that rots is always the exterior layer of OSB -- that is, the cold layer -- not the interior (warm) layer of OSB. With continuous exterior rigid foam, there (generally) is no exterior layer of sheathing -- so there is no cold sheathing to rot.
FWIW, I have inspected hundreds of houses built with EIFS over the years, primarily in NJ zone 4. Most of them had structural decay for all of the reasons that EIFS has had problems. But we could absolutely correlate the degree of damage with the thickness of the foam. When we saw more than 2" of exterior insulation as part of the EIFS package, we would generally see little or no moisture damage, regardless of the installation details. The thicker foam just made for a far more durable assembly even when the builders messed up the other details. OTOH, we saw many cement stucco installations with really good details and no exterior insulation that were soaking wet in winter from condensation on the back side of the sheathing. After that, it's a race against time: is the wall going to dry faster than it warms up enough for mold to start growing? I'd hedge my bets and use thick exterior insulation.
Peter,
Thanks for your comments. Wood-framed homes with either EIFS cladding or cement-based stucco cladding are special cases. Houses with these two types of cladding are particularly susceptible to sheathing rot if bad flashing practices lead to water entry.
The historical problems with EIFS have been extensively covered in technical journals, and the EIFS industry has responded by restricting installation of EIFS to certified and trained installers, and by instituting new details that manage water entry better than the old face-sealed systems.
For an overview of problems with conventional stucco, see my article, "To Install Stucco Right, Include an Air Gap."
Note that my article on stucco-clad houses documented extensive failures in stucco-clad homes -- none of which had exterior rigid foam.
Great discussion Martin; thanks. I've utilized mostly double stud walls for simpicity, but I prefer exterior insulation as it keeps the entire wall warmer. My main objection with polyiso is the GWF, so I'm looking forward to using local New England wood insulation panels from GOlab. I used a lot of SIPS 30-40 years ago and worry about the roofs deteriorating, but I've never seen wall panel joint failures - they seem to hold up fine.
Bob,
I wrote a long report on SIP homes in Juneau, Alaska with rotting walls; the report was published in the September 2003 issue of Energy Design Update. Those problems were caused by high interior moisture levels, a lack of ventilation, a particularly difficult climate -- and, most importantly, by the installers' failure to use tape at the interior of the SIP seams.
The report, titled "Problems With Juneau’s SIP Walls," is too long to quote in full. Suffice it to say that I interviewed several builders who had repaired homes with rotting SIP walls. The wall rot followed the same pattern as the roof rot -- it started at the seams, with rot first showing up at the exterior OSB layer, parallel to a seam.
Here are the opening paragraphs of my article:
"The epidemic of rot plaguing structural insulated panels (SIPs) in Juneau, Alaska, has been widely described as a roof problem (see EDU, October 2001 and December 2001). However, several Juneau builders and construction consultants report that some of the homes with rotting SIP roofs also have rotting SIP walls.
"In 2001, the Structural Insulated Panel Association (SIPA) hired Joseph Lstiburek, a principal at the Building Science Corporation, to investigate Juneau’s rotting SIPs, most of which were installed between 1995 and 1998. Lstiburek’s report (posted on the Web at https://web.archive.org/web/20040426005400/https://www.sips.org/technical/juneau_report.html), titled “The SIPA Report on the Juneau, Alaska Roof Issue,” makes no mention of rotting wall panels. But John Cooper, a Juneau engineer who has been hired by homeowners to investigate SIP problems, has discovered that many SIP homes have wall rot. “The wall failures look just about like the roof failures, and the failure mechanism is about the same as for the roofs,” says Cooper. “The wall rot shows at the seams; most of them are running a fair length of the wall.”
"Roof rot is more obvious than wall rot, so it is understandable that Juneau’s SIP problems were first noticed by roofers. Daniel Ulery, vice president of Four Eagles
Construction in Juneau, has repaired several buildings with rotting SIPs. “On roofs, you can tell where you’ve got decay, because the deck will be spongy when you
step on it,” says Ulery. “But with walls, the decay is sometimes hidden.” "
Thanks Martin; I stand corrected. I have some experience with rotten roofs and get the occasional call from someone with that problem, and it's very discouraging that it continues to happen for the same reasons. We know the issue, but better installation methods still don't seem to be standard, or demanded by the manufacturers.
Great Article! If warm sheathing dries quicker, would sheathing products with integrated insulation to the interior side of the sheathing be problematic (even if taped properly)? If so, could these product theoretically be installed backwards (likely voiding the warranty) to solve the cold sheathing issue?
Jimmy,
Sheathing with integrated insulation that was installed backwards would be indistinguishable from a practical p0int of view from sheathing with the insulation installed in the exterior afterwards. So if the rules of the amount needed to keep the sheathing dry were observed it would work. Unfortunately however the problem of doing it isn't just a matter of voiding the warranty, there is no way to secure the sheathing through its (now) outer foam layer.
Generally speaking, the integrated insulation/wood structural panel includes the water resistive barrier. By flipping the panel around, we would negate that component of the wsp (wood structural panel) design. We use Huber Zip a lot and are doing a current project with zip r. This is because it is a wsp (resist seismic loads, maybe wind if that's the higher load in your area), wrb (liquid water resistive barrier), and ci (continuous insulation) all in one (this is a labor productivity thing - if you flipped the panel, all things being equal, you'd have to install another wrb (and that would make the wall even more vapor closed)). The insulation is not on the "correct" side as far as condensation is concerned (I might suggest that wa (water activity is more important, but that's a topic for another day)). So we install a combination of vented cladding and rainscreen (specifically, using rainslicker by Benjamin Obdyke). Essentially, I want drying potential to both sides of the exterior sheathing (we use a class 3 vapor retarder at the interior). (This is a record number of parentheses on GBA, ha!!)
Malcom & PioneerBuilders,
Thank you for your thoughtful response(s)! All great points. I appreciate having a community forum like this to poke holes in my wacky ideas.
PioneerBuilders, that sounds like a great wall assembly!
Log in or become a member to post a comment.
Sign up Log in