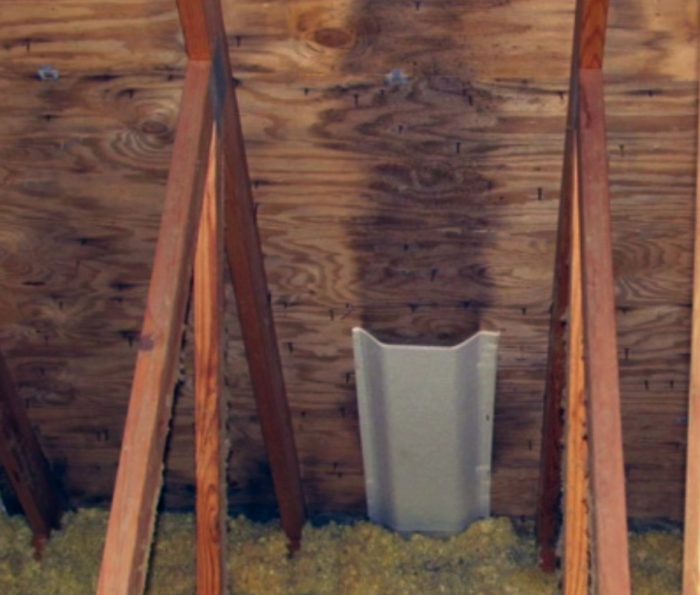
Increasingly, homeowners in the Pacific Northwest are noticing mold on the underside of their roof sheathing. This phenomenon occurs in vented attics, and is more common in new homes than old homes. One puzzling aspect of the phenomenon is that the mold is found in well-built homes that comply with all relevant building codes. In other words, most of the homes with this problem have ceilings that are fairly airtight; they have adequate levels of insulation on the attic floor; and they have adequate levels of ventilation at the soffits and ridge. So what’s going on?
A variety of factors contribute to this problem, including recent changes in construction practices and the region’s damp climate. The most surprising factor may be the role of night sky radiation—a phenomenon which can cool roof sheathing to a temperature lower than the air temperature. In most cases, increasing the rate of attic ventilation—for example, by enlarging the soffit vents—doesn’t help; in fact, the greater the ventilation rate, the worse the mold.
Roof leaks? Inadequate ventilation? Indoor air? No, no, and no.
Researchers from RDH Building Science, a consulting company in Vancouver, BC, have investigated cases of sheathing mold in vented attics and have conducted field research on the issue. In a 2019 report published by the BC Housing Research Centre, “Asphalt Shingle Sloped Roofing Research Study,” the RDH researchers noted, “Moisture problems in sloped wood-frame attic roof assemblies are often attributed to rain water ingress, inadequate ventilation of the attic space, and air leakage condensation from interior spaces or ductwork. However, detailed investigation and testing of many of these attics has found that these factors cannot wholly account for the observed problems. … These roofs are generally constructed to meet current building code and third-party roofing warranty requirements.”
In…
Weekly Newsletter
Get building science and energy efficiency advice, plus special offers, in your inbox.
This article is only available to GBA Prime Members
Sign up for a free trial and get instant access to this article as well as GBA’s complete library of premium articles and construction details.
Start Free TrialAlready a member? Log in
18 Comments
Has the 'thermal mass' of a shingled roof assembly changed appreciably over the years? And if so, could that lesser heat capacity possibly allow radiative cooling to drop the sheathing temperature to dew point more quickly?
I'm thinking along the lines of the felt, shingle thickness, sheathing thickness/denisty, etc. I suspect this would be 'noise' rather than an actual cause, but just brainstorming.
Along the same lines, I wonder if any differences would be observed in cellulose filled attics vs fiberglass... cellulose 'storing' a bit of the days heat and radiating back to the sheathing at night?
Tyler,
You wrote, "I suspect this [and differences in thermal mass of the roof assembly] would be 'noise' rather than an actual cause." I would agree.
Nor do I think that there would be any significant difference in sheathing mold when comparing attics with cellulose to attics with fiberglass.
Thanks Martin. I'm indebted to both BSC and RDH for this type of research - and to you for synthesizing it into something we can use. Good news, bad news - it's always comforting to know where you are and what's going on.
This comes at an opportune time for me as I'm just starting to re-roof my house after 25 years, and am happy to have confirmation of what I thought was going on with roofs here. The plywood sheathing on my two symmetrical shed dormers situated on the north and south sides show differing levels of discolouration, but no structural or even surface damage.
Because the moisture problems appear to be entirely limited to the sheathing and not the surrounding structural elements, one solution I've done for years has been to specify metal roofs on purlins or skip-sheathing. This seems to completely eliminate the problem, and has the added advantage of allowing some horizontal ventilation. However with changes to the seismic codes here, roof sheathing is now required as part of the structural diaphragm, so that solution is off the table for most of the coastal PNW.
I'd like to share an interesting observation on this subject. Last year I've framed my house on Orcas island, but had to postpone construction until this spring. The house was left in the dry-in state with metal roof installed, windows and liquid applied WRB. The slab wasn't completely dry yet, there were quite a few dark/wet spots on it and I was worried that all that moisture would cause mold growth on the inside. When I got back to continue construction this spring, to my surprise all the sheathing inside the house was mold free, including roof plywood in the attic. However, the plywood roofing over the front porch area was all covered with mold. No mold on the framing that supports that plywood though. So, it looks like cold roof effect mostly affects the sheathing itself, but the lumber under it is relatively safe from it. I am still puzzled though why the well ventilated outside part of the sheathing got so much mold and no mold at all on the inside of the attic.
Vlad,
I've found a certain amount of what seems like capriciousness in where mold occurs on roof sheathing here too. Taking into account all the factors Martin laid out, it still seems difficult to see why it gets established in one spot but not the surrounding area.
I have found though that on unheated outbuildings, exterior overhangs seem more prone to mold than the roof sheathing that continues into the structure.
Vlad,
Q. "I am still puzzled though why the well ventilated outside part of the sheathing got so much mold and no mold at all on the inside of the attic."
Q. Here's one possible explanation: Remember that I noted in my article that increasing the size of ventilation openings can make mold worse? In the attic, the amount of available moisture is limited by the size of the openings in the soffit vents and ridge vent. The sheathing above the porch is exposed to the outside air, and therefore the amount of available moisture is more.
Martin,
Wouldn't the easy solution be to install conditioned attics and never let the moisture get in there to begin with?
Andy Homoly
Andy,
That's what I wrote in my article: "One foolproof way to avoid this type of mold is to build houses with unvented conditioned attics." If you missed that part of the article, it's the next to the last sentence.
A timely article as we are experiencing mold on our attic sheathing in our Portland. OR home. It was built in 1978 and when we bought it a couple of years ago the roofing was replaced as part of the sale agreement along with a couple sheets of roof sheathing, additional round (3") soffit vents put in and mold mitigation.
After reading a couple articles on this site I decided our access into our attic (in the hallway) was definitely leaky, basically drywall just sitting on a frame so not very airtight. When I stuck my head up there to replace the hatch cover I find mold all along the north side but not over the north side of the garage which is uninsulated. I also find the venting to the bathroom fan laying on the floor of the attic. We also discovered that there are no ventilation baffles and the insulation was covering all the soffit vents. Sigh. Why did I stick my head up there :) We should have checked everything sooner but when we moved into the house my husband was actively fighting stage 4 cancer so we had other things occupying our energy.
So here we are today. We have mushroom vents (on north side only), no ridge vent , no gable vent and the soffit vents are either a screen or the small louvered vents on the 2 x 4 blocking. We have pulled all the insulation back from the soffit vents and put in a new attic hatch with rubber gasket and clamps to keep it tight against the frame. I know we need to put baffles in and I have watched Mike G 's video on making your own but its pretty tight in there with only 2 x 4 blocking between the trusses. The foam and plastic baffles seem pretty wimpy. The current blown in fiberglass insulation is also woefully inadequate barely covering the trusses so that will need to be dealt with as well.
I wish the home inspector had pointed this all out but one thing he said to me was the insulation looked compacted and pressed down "like an animal had been up there". Of course now I know better.
Mold mitigation is big business here in the PNW but you cannot get any concrete information on what they use. Apparently its top secret. Everybody I have talked to that has had mold mitigation has had it done when they went to sell their home. When I ask if it worked and what did the company use they always say I don't know it smelled like bleach and then I moved. I did go up there and see if I could scrub the mold off in a small area and it does come off. What do mold mitigation companies use? Moldicide, fungicide, biocide, bleach, eco friendly non toxic pseudo gas??? Some paint the sheathing after treatment either opaque or not, some run tests ( don't need one I can see the mold) It's very frustrating.
Anyway, any advice on mold mitigation would be appreciated.
Karen
Karen,
I don't recommend mold mitigation for attics. What I recommend is addressing moisture issues, if any. (You mentioned two: a bath exhaust fan venting directly to the attic, and an attic hatch without weatherstripping. It seems that you have fixed both problems, which is good.) For more information, see "Common Sense On Mold."
Concerning attic ventilation: As my article notes, improving attic ventilation in the Pacific Northwest can make mold problems worse.
I guess we just have to choose our poisons. The roofs I have observed as having mold growth from what seems to be ventilation air and night sky cooling, haven't had any damage. The more common problem I see is still inadequate ventilation in the presence of some air-leaks from below. Those ones almost always come with some rot in the sheathing.
Thanks Martin,
I did read that article. I believe it was a combination of inadequate insulation, insulation blocking the vents, crappy hatch and the bath fan venting created the perfect storm. Of course if we ever try to sell our house the mold will stop the sale in its tracks.
What do you think about the baffles? I like the super baffle but I'm not sure how to retrofit them and the ones at the big box stores seem super flimsy although I can find durovent online. If I just concentrated on the north side I'd only have to do about 15 of them but it is so tight (4" at the soffit end). Is there any code issues with using rigid foam for baffles? I could fashion them out of 1/4" plywood. My window of opportunity is getting short as once summer hits it will be pretty miserable in the attic.
The existing insulation is blown in fiberglass. Does it matter if we add cellulose over fiberglass or should we stick with fiberglass? I know I need to do air sealing and luckily I only have 1 recessed light to deal with along with a soffit above the kitchen.
Karen,
For information on installing insulation baffles near the eaves of a roof, see these four articles:
"All About Attic Venting"
"Site-Built Ventilation Baffles for Roofs"
"Sliding Insulation Between Rafters From Above"
"Insulating Tight Spaces at the Eaves"
Only you can decide if you are able to work in the tight space you describe.
Q. "Is there any code issues with using rigid foam for baffles?"
A. No, as long as you maintain the code-mandated minimum vent channel height of 1 inch.
Q. "The existing insulation is blown-in fiberglass. Does it matter if we add cellulose over fiberglass or should we stick with fiberglass?"
A. Either material will work, although blowing a layer of cellulose above the existing fiberglass would be better, because the cellulose would reduce air leakage and the possibility of convective looping.
Thank you, Martin. We have been building the PNW for over 40 years with vented roof assemblies and no attic mold (who knows, roughly 400 plus homes). We build pretty high performance homes, but I wanted to share a variable that I haven't seen touched on much. We typically build in South Kitsap/North Mason counties. If you look at a map, we're east of the Olympic Mountains. We do get a lot of rain/overcast days, but Washington state has a lot of microclimates. My thought is that labeling the PNW as a blanket location is completely understandable, but I think it is also important to understand the climate/topography where one is specifically building. There are the broad patterns of rain and wind, but then the annual shifting jet stream and mountains can also play a role. Then there's the specific site - sometimes our homes are treed, sometimes they aren't. Sometimes they're sloped, sometimes they aren't. Sometimes they're exposed to the coast (generally, facing West), sometimes not. In any case, with the 2018 WSEC, it looks like we'll be shifting to hot roofs, but I figured I'd share my two cents.
PB,
Good point. GBA published a blog recently of a builder in Selah, Washington, which is a desert climate. Even in the area I build on Vancouver Island, a half hour will bring you to areas of completely different climatic conditions.
Pioneer,
Like Malcolm, I'd like to say that I appreciate your point. Thanks.
Would an inch of rigid insulation on top of the sheathing keep the sheathing above the dew point?
What about 1" rigid foam on the underside of the sheathing--sealed to the trusses at the edges with spray foam?
Log in or become a member to post a comment.
Sign up Log in