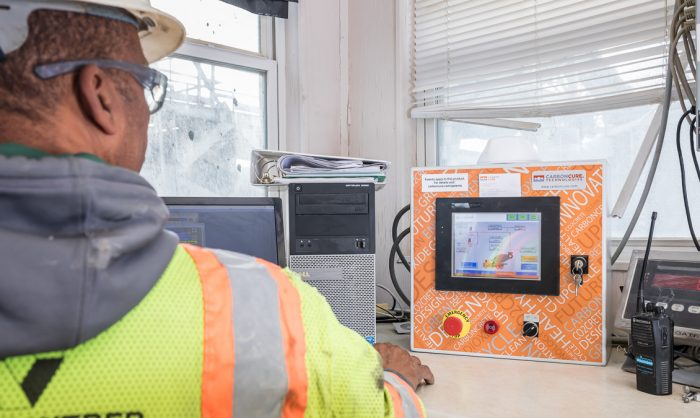
Lawmakers in two northeastern states are considering changes to state bidding rules that would encourage the use of concrete with less embodied carbon than standard mixes.
In New York, both houses of the legislature have approved a measure that would require the Office of General Services to set guidelines for the procurement of concrete with lower embodied carbon for state contracts. Contractors would have to follow the guidelines and certify that their work and the concrete they use are in compliance.
New Jersey lawmakers are considering a bill that would establish a discount rate for contractors using low-carbon concrete when they submit bids for state work. The bidding advantage, based on the global warming potential (GWP) values for the concrete, could be as much as 8% of the total cost of the job. The bill is not expected to make much progress until later in the year. Amendments are considered likely.
Concrete is a major contributor to global carbon emissions. According to an article on the New York legislation posted at Construction Dive, cement, the binder in concrete, is responsible for as much as 7% of total global emissions. Overall, the United Nations Environment Program says the built environment, including the construction industry, accounts for more than 38% of all energy-related carbon emissions.
More than 10 billion tons of concrete are produced annually, the New York Senate Bill S542A says. “To bring the concrete and cement sectors in line with the targets agreed upon in the Paris Agreement, annual emissions must fall by 16% by 2030,” the introduction to the measure reads. “However, current trajectories project that demand for both materials could increase by as much as 23% by 2050. Under this business-as-usual scenario, production escalation on this scale will release extraordinary levels of CO2 during the next three pivotal decades.”
But, the legislation notes, concrete has a “unique potential” to store and mineralize carbon permanently, and it ultimately could become a net-carbon sink rather than a net-carbon source.
Reducing concrete’s carbon footprint
Builders and specifiers have a number of options for ordering low-carbon concrete from the country’s roughly 5500 local ready mix plants.
According to U.S. Concrete, a Texas-based firm that provides aggregates and ready-mix concrete through affiliates around the country, producing 1 ton of cement typically releases 1 ton of carbon into the atmosphere. Reducing the amount of cement in concrete by replacing it with other materials (called supplementary cementitious materials, or SCMs) is one way of cutting concrete’s greenhouse gas emissions.
One of those materials is fly ash, a mineral residue produced by coal-burning power plants. Fly ash can replace as much as 50% of the portland cement in concrete, reducing carbon emissions but also improving the working characteristics of the concrete. Concrete made with fly ash shrinks less than conventional concrete and is easier to pump. Slag, a byproduct of blast furnaces that smelt ore, is another substitute that can replace as much as 50% of the cement in concrete for structural and paving work and as much as 80% of the cement in mass concrete structures, the company notes at its website.
Because slag cement takes almost 90% less energy to make than portland cement, the amount of embodied energy in a cubic yard of concrete can be cut by as much as 48% when using a slag cement substitute, the company says.
The Portland Cement Association, an industry trade group, says manufacturers also have developed portland-limestone cement, a blend with higher limestone content, that performs the same as standard blends but reduces carbon content by 10%.
Another approach was pioneered by CarbonCure, a Canadian firm founded in 2012, which developed a process for injecting carbon dioxide (CO2) gas into ready-mix concrete at the batch plant. The technology is used at more than 300 concrete plants globally, according to the company. Collectively, the plants have supplied nearly 10 million cubic yards of concrete to date. The process also can be used to make concrete block.
Carbon dioxide is provided by industrial gas suppliers in liquid form to ready mix plants. When it’s injected into a batch of concrete the carbon dioixde becomes a mineral that increases the strength of the concrete and reduces the amount of cement that must be used. Each cubic yard of concrete made with the process saves 25 lb. of CO2, the company says. Construction of a single high-rise building could avoid 1.5 million lb. of carbon emissions. CarbonCure claims that concrete delivered to a job site comes with minimal, if any, cost differential. A map at the company’s website shows where producers are located.
CarbonBuilt, a group at the University of California, Los Angeles, developed technology in which calcium hydroxide replaces some of the cement used in concrete block along with an SCM such as fly ash. After concrete is formed, it’s cured with waste CO2 in a process the company calls “Reversa.” In demonstration projects, the technology was used to make 10,000 concrete blocks with CO2 taken directly from a coal power plant in Wyoming and, later, from coal and natural gas power plants in Alabama.
CarbonBuilt and CarbonCure were winners of the $20 million Carbon XPrize competition.
What the concrete industry says about carbon
The concrete industry is working to reduce embodied carbon in concrete in a number of ways, says Gregg Lewis, executive vice president of the National Ready Mix Concrete Association. Through its Build with Strength program, the organization promotes what it says are the environmental advantages of using concrete. While critics advocate using more mass timber and less concrete and steel, the ready mix industry says concrete has “one of the lowest carbon footprints of any building material on a per-unit weight basis.”
“There’s been a tremendous amount of innovation around mix designs, particularly as it relates to embodied carbon in concrete,” Lewis said in a telephone call. The National Ready Mix Concrete Association says its goal is to reduce concrete carbon emissions by 50% in 2030. In the meantime, the trade group lists the advantages of using concrete in buildings: high strength, long life, high fire resistance, and, Lewis adds, advantages of thermal mass, and low rates of air leakage, which can lower emissions that result from the heating and cooling of buildings, i.e. operational carbon.
“When talking about operational carbon, you’re not going to get a better performing structure than with ready-mix concrete and that’s been born out over and over again in all different kinds of buildings,” Lewis said. “The importance of pursuing reduced embodied carbon makes a lot of sense as a logical next step in addressing overall carbon impacts.”
The association is neutral on the legislation in New Jersey and New York, in part, because it represents members on both sides of the argument. Another route toward lowering embodied carbon with cement substitutes is a wider use of performance-based specifications that would allow specifiers to order concrete made with SCMs as long as it performed as well as standard mixes that rely completely on cement. Currently, some specs have a minimum cement requirement.
“If you look at SCMs and admixtures, then you’re getting somewhere right off the bat,” Lewis said. “Part of this is education that needs to happen with architects. If architects generally had a better understanding of performance-based specifications, they could embrace that and drive performance at the same time as they’re reducing embodied carbon in the concrete they’re specifying. But in too many cases, folks reuse the same specifications from project to project to project, and there’s very little effort made and very little understanding of the opportunities inherent in a performance-based specification to dramatically drive down that embodied carbon.”
Finally, Lewis points to emerging research suggesting that carbon can absorb atmospheric carbon over its lifetime, reducing the embodied carbon attributed to making it in the first place. One study that Lewis flagged suggested that “carbonation” of cement products represents “a substantial carbon sink that is not currently considered in emission inventories.”
“If you’ve got your mix design and you’re innovating properly, then chemically you will lock that atmospheric carbon into the concrete both through the mix design and the process of recarbonization, where that exposed concrete continues to absorb carbon over the life time of the building,” Lewis said. “This is something where research is only in its nascent stage but the indications are extremely good that concrete should be viewed as a place to store carbon.”
Scott Gibson is a contributing writer at Green Building Advisor and Fine Homebuilding magazine.
Weekly Newsletter
Get building science and energy efficiency advice, plus special offers, in your inbox.
One Comment
Frankenconcrete in and of itself is little but an overly hard, nonporous, moisture trap that cracks with disturbing regularity. Of course, it's the absurd levels of heat required to clink the stuff at the root of the rot (we'll leave the violent levels of activity required to move the stuff about the earth aside for now). Traditional concrete demands lower heating levels in the processing stage.
Through fiat debt "money" acrobatics, frankencrete maintains its market position on a daily basis in much of the fiat debt note world—which basically is everywhere for the moment. When honored by enough people, these fiat debt notes drive adoption of awesomely violent methods and materials—as we see daily.
Log in or create an account to post a comment.
Sign up Log in