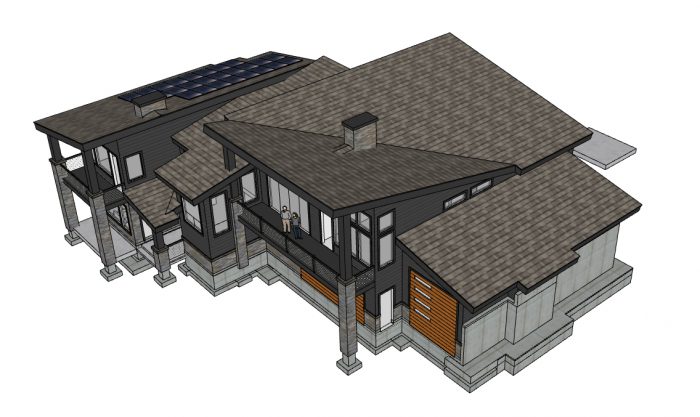
Mapping out the roof assembly for a new house in Climate Zone 6B, Steve Mackay has settled on long I-joists insulated with a mix of closed-cell spray polyurethane foam and blown-in fiberglass. He doesn’t plan on venting the roof, and he wants to be certain his design will be problem free.
Here’s what it looks like: 14-inch I-joists with 5 inches of closed-cell foam sprayed on the underside of the roof desk. The balance of the insulation will be fiberglass (Mackay wants to use the BIBS system) with no interior vapor barrier. In all, he gets R-67 in the roof cavity, with R34 coming from the foam, and R-33 from the fiberglass.
Mackay has read an article on the topic by GBA’s Martin Holladay, and he’s confident the assembly will work. With an inside design temperature of 68°F and an outside design temperature of 22°F (an average of the three coldest months of the year) and a relative humidity of 35%, the inside surface of the spray foam will be about 45°F. That’s well above the dew point of the air and safe from the threat of condensation.
“I’m very confident this will work well,” he writes in a Q&A post. “However, the ccSPF [closed-cell spray polyurethane foam] is expensive and the insulation contractor suggested using 2 inches of ccSPF under the roof deck and then using ocSPF [open-cell spray polyurethane foam] to get the R-value I’m looking for.”
The assembly would be cheaper than Mackay’s original plan. But does this change his calculations on where the first condensing surface is? And with the change, does the risk of condensation inside the assembly go up?
That’s where we start this Q&A Spotlight.
Weekly Newsletter
Get building science and energy efficiency advice, plus special offers, in your inbox.
This article is only available to GBA Prime Members
Sign up for a free trial and get instant access to this article as well as GBA’s complete library of premium articles and construction details.
Start Free TrialAlready a member? Log in
24 Comments
> recent building codes only allow unvented roof assemblies for pitches 3:12 and greater (IRC 2015 Section R806.5.2.7).
This is a mis-interpretation of the code. Read all of R806.5 carefully.
Figure 6 describes open cell spray foam as air permeable. It's not and so code doesn't require R value ratios. In some climates it requires a vapor barrier.
Hey Jon,
I believe that you are right.
The IRC R806.5.2.7 says:
"In Climate Zones 1,2, and 3 air-permeable insulation installed in unvented attics shall meet the following requirements:
...
The roof slope shall be greater than or equal to 3:12 (vertical/horizontal)"
So it is not a sweeping limitation on roof pitch for unvented attics, it is specific to air-permeable insulation. Is that your understanding?
>"So it is not a sweeping limitation on roof pitch for unvented attics, it is specific to air-permeable insulation. Is that your understanding?"
That's how I would interpret it. (But what do I know? Not much- go ahead and ask my wife! :-) )
hint: why do you think it says "In Climate Zones 1,2, and 3...."?
Jon,
Of course, in those climate zones. I was hoping you would clarify why you first commented that the reference was a misinterpretation. I think we have gotten to the bottom of it.
I was hoping that someone would disprove my theory that 3 out of 4 people (probably including inspectors) can't interpret a screen full of code. But OK - the originally quoted code doesn't apply to Steve because:
1) there is no R806.5.2.7 in the 2015 IRC code
2) he isn't in climate zones 1,2,3
3) most importantly, R806.5.5 makes all of 2018 R806.5.5.2 optional. Nothing in it is generally required of a roof - it's a misinterpretation to claim it justifies anything (eg, slope) that doesn't involve vapor diffusion ports (which Steve isn't considering).
To clarify: R806 allows any slope, vented or unvented.
https://codes.iccsafe.org/content/IRC2015/chapter-8-roof-ceiling-construction
https://codes.iccsafe.org/content/IRC2018/chapter-8-roof-ceiling-construction
I hope you are installing larger than average gutters at the end of that valley so that all that water doesn't wash down your lower roof in one spot and damage the shingles. As to that lower roof, can you extend the roof line so that it's straight across (at the same level as the bumpout eave) so that your gutters can be in a straight line? That will help get rid of the rain water faster.
The original design intent of the home was to have no gutters and no roof tape. I called out exactly your point to my architect and builder very early on in one of the first design iterations, both claimed this is normal practice and to trust them that it won’t be an issue.
What I will likely do is ride out one winter watching these issues and seeing if I should put up gutters or heat tape.
The whole house design and build process has been very disappointing. It is very difficult to get good advice from the professionals I’ve hired which is why I spend so much time on this forum.
Steve
Steve,
Only peripherally connected to your main question, but I'd work really hard to get rid of the post that pokes through your roof next to the balcony. It is a both potential leak and looks odd.
At this stage it's too late for that. Everything is constructed except for the roof overhang over the deck.
California has very different code when it comes to this. Ca residential building code r806 and specifically table r806.5 states that for example climate zones 3 through 15 only require air impermeable insulation of r5.... I'd be curious to understand why these codes are so different...
Ca uses a different climate zone numbering scheme. R5 is the same requirement as zone 3 above.
When this was discussed on the forum, I though it was a problematic roof. Now seeing the renderings, it is even worse. I really want to know what the architect designing it was thinking. There is no need to design in all questionable details that at best will be hard to do well. They are expensive, finicky and could have been designed out.
So we are in snow country, lets go with low slope with a valley.
That is not enough, lets shingle it, cause you know low slope plus shingles plus snow build up, what can go wrong?
Of course that is not enough lets stick a chimney in the middle of the valley. WTF?
Best make sure that chimney is flashed like on a flat roof with the peel and stick carried up high enough under the brick for expected snow height.
EDIT:
I don't think overall this the designers fault, it is an issue with how the system is set up.
The architect wants to make the most attractive design to please the client.
The interaction is mostly about aesthetics, "of course we can put the fireplace in the middle of the roof" and "nothing like a nice geometric roof to make the house look modern".
Contractor will always want to build what is proposed, asking for changes to simplify build only causes more delays and less labour. Any time there is a "detail" the contractor know he is looking at minimum $10k to do it. So lots of details are great!
I really don't know how it could be done better. You can have a great looking house, that is easy to build and energy efficient.
Unfortunately there is no financial incentive for any of the people involved to focus on "easy to build and energy efficient".
Hey Akos, don't candy coat it for us- tell us what you REALLY think! :-)
(A chimney in a valley really IS precious, I have to admit...)
Akos,
You know this is my first ever house build and at nearly 50 years old it's probably my last one. I thought I was doing my best picking professionals and interviewed several architects and builders talked to builders about architects, talked to architects about builders and talked to their clients. I interviewed 5 architects and 7 builders. You make the best decisions you can, decide on people that you can work well with and you trust, then have to rely on their expertise.
Unfortunately my experience with my engineer and architect has not been great. So far my builder is doing okay. As an engineer I caught dozens of mistakes in both deliverables. However there were many things I missed. This roof valley and the dripping onto the garage roof was one item I was told not to worry about.
I didn't recognize the issue of the chimney in the valley until your post. It is possible I can make the chimney smaller to give more clearance to the valley. Perhaps offset the flue in the chimney to provide more clearance.
I'm glad of this board and input like yours because it gives me a chance to think of solutions during the construction rather than after I have years of leaks. So for that I thank you.
Steve
Steve,
I don't think there is an easy answer. It sounds like you did all you can. The designer did do a nice job, the outside looks great. Consistent style, nicely balanced massing. It is just some of these details. Just because they can be built, it doesn't mean they should.
For your chimney, looks like you won't be able to see if from ground level. Swapping out the brick to a metal chimney will be less problematic and significantly cheaper. If you can find one with taller flashing collars, there will be less chance of leaks in case of ice dams.
The metal chimney should also have a smaller footprint so you can get a bit of extra space from the valley.
> ride out one winter watching these issues and seeing if I should put up gutters or heat tape.
A reasonable plan, but there are some advantages to putting heat mat under the shingles (which is better done now). Energy use can be very low.
I agree with adopting as many flat roof techniques as possible. And maybe 100% coverage with ice and water shield?
"Dana Dorsett suggests that he include a 1 1/2-inch air gap under the sheathing then install 12 1/2 inches of half-pound open-cell foam."
Is that thickness allowable/possible? I ask because I seem to recall other articles either here on GBA or elsewhere which say that there is a technical limitation to the applied thickness of spray foam, whether open cell or closed. I don't remember the whys and wherefores, and don't really have time to search for that info, but I am curious if I remember correctly.
Traditionally most open cell foam need to be applied in lifts of no more than ~6" at a time, (and usually not less than ~3" to guarantee it hit's the right temperature range for the water/steam blowing agent) with a cooling/curing period between lifts to avoid quality problems, or even potential self-ignition while curing.
But there are no technical barriers to hitting 12.5" total depth if staying within the manufacturer's specifications on maximum depth per pass. Doing it in more than one lift results in a lumpier, less even surface, but that's par for the course for anything more than 6", if installed per the manufacturer's instructions.
Vendors keep tinkering with the chemistry, and some products now claim no upper limit per pass eg:
https://www.demilec.com/documents/Tech-Library/Sealection-500/Sealection-500-Product-Application-Guide.pdf
See p.2 where it states:
"Always spray perpendicular to the surface in a minimum 3” lift. There is no maximum thickness due to physical properties, so Sealection 500 can be sprayed as thick as possible in a single pass without signs of blow-off from the reacting mass. Thin foam layers often results in poor physical properties, and poor chemical reaction due to low exothermic heat generated from the chemical reaction, which is needed to create proper cell formation.
If touch-ups or subsequent passes are needed to achieve the prescribed thickness, allow the foam lifts to cool and release any steam generated during the spraying process. Wait at least 2-5 minutes before successive foam lifts are applied. Small blisters may form on the surface of the foam if this recommendation isn’t followed."
So whatever product is selected read the instructions carefully, and make sure the installer is up on any limitations per pass. You don't want to star (or even take a bit role) in this movie:
https://www.greenbuildingadvisor.com/article/three-massachusetts-home-fires-linked-to-spray-foam-installation
Peter Yost edit and note: I have edited my starting comment above at the end of the blog regarding venting, low-pitch roofs, and the building code. This is because I got it wrong and "Jon R" in his comments got it right, including his assessment of the percentage of building professionals (including me!) who can't correctly read and interpret a full screen of code language.
Stay tuned for a GBA blog on the topic of code language, code development process, and building science coming soon! I think I will run a draft by Jon R before publishing...thanks Jon R for your work within the GBA community.
Peter gets the "cool guy" award. And credit for bringing up some kind of review process to improve GBA . Perhaps the software could facilitate this in some way (private comments?) I wouldn't mind if this spotlight article were edited and all comments about R806 were deleted - that's arguably the right thing to do to make GBA a clear and concise library of information.
Start taking these plans to roofer
from the IKO website:
local building code requirements, as some shingles may have a minimum slope recommendation higher than 2:12. As well, a slope of 4:12 is most commonly considered the lowest slope for “standard shingle installations”. Most manufacturer and industry recommendations require, or at the very least recommend, special underlayment or other considerations on roofs between 2:12 and 4:12.
That valley, that chimney, that post through the roof, on a 2 1/2 pitch, yow.
I live next to an A frame, shingles missing, never leaks a drop
My house is 3 1/2 and 2 and leaked like a sieve for 40 years before I bought it.
I predict heartache and frustration in 5 years if incredible attention to detail is not spent on that roof.
An average roofer will fail
So basically you want he guy who says this roof is going to leak and doesn't want to do it.....
and what is with the weird detail at the bottom of the big valley?
or at the top for that matter?
and does that piece of intermediate roof go flat in the middle? That is going to be fun to detail
And what is with the varying overhangs? looks like zero a the top of the roof with the solar, varying on the sides...
shrug, maybe it is a look.....
Here in northern Michigan we have not gotten into "unvented" roofs much. The few we have specified as of late, we are now using Hunter's Cool Vent product which allows for both a insulated roof outboard of the sheathing and a vented roof assembly. Seems to solve all of the insulation, air and vapor concerns about getting the system "just right". If you haven't, you may want to look into it. And slope relative to shingles? Yeah, with 160 inches plus average snowfall, we don't specify shingles on slopes less than 4/12. Regardless on any residence we do up here, the roof gets full coverage ice and water shield underlayment for additional protection.
https://www.hunterpanels.com/polyiso-roof-products/cool-vent
Log in or become a member to post a comment.
Sign up Log in